Procurement 101: An Introduction to Heat Treatment Process in Fabrication
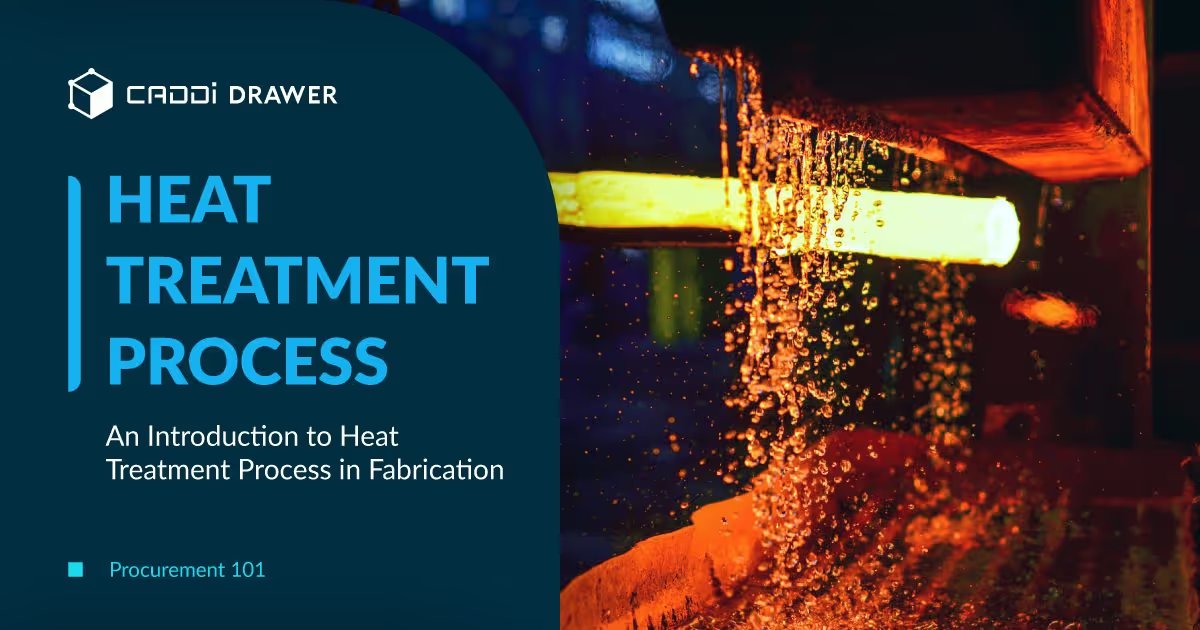
Table of Contents
What is Heat Treatment?
Heat treatment is a controlled process used to alter the microstructure of metals and alloys in order to change their physical and mechanical properties. The main purposes of heat treatment are to increase hardness, strength, ductility, and toughness as well as to relieve internal stresses and refine the structure. Heat treatment involves heating the metal to a specified temperature, holding it at that temperature for a set time, and then cooling it at a controlled rate.
Some of the common heat treatment processes used in custom fabrication workshops include:
- Annealing – Heating to and holding at a suitable temperature and then cooling slowly. This results in reduced hardness and increased ductility.
- Normalizing – Heating to and holding at a suitable temperature above critical, followed by air cooling. This refines the grain structure.
- Hardening – Heating to a suitable temperature above critical, followed by rapid cooling or quenching. This increases hardness significantly.
- Tempering – Reheating hardened steel to a temperature below critical to reduce brittleness and hardness. This increases ductility and toughness.
- Case hardening – Diffusion of carbon or nitrogen into the metal surface, forming a hard wear-resistant outer case with a tough ductile core.
Proper heat treatment allows the fabrication shop to tailor the properties of metals to meet the design and engineering requirements of custom parts and products. In the following sections, we will explain each technique in detail, step by step.
Annealing
Annealing is a heat treatment process used to alter the physical and sometimes chemical properties of a material. Annealing involves heating the metal to a specified temperature, holding it at that temperature for a set time, then cooling it back to room temperature.
The process softens the metal, making it more ductile and less hard, improving its machinability and responsiveness to cold working processes like rolling, forging, or bending. Annealing also relieves internal stresses that can build up in the metal during casting, welding, or machining.
There are several types of annealing processes:
- Full anneal – Heating to above the upper critical temperature, soaking, then cooling slowly. Produces a coarse pearlite structure.
- Process anneal – Heating to a temperature below critical, soaking, then cooling. Done between stages of cold working.
- Stress relief anneal – Heating to a relatively low temperature, soaking, then cooling. Reduces residual stresses only.
Key applications and benefits of annealing include:
- Softening metal for improved machinability and formability
- Relieving internal stresses to prevent cracking or distortion
- Refining the grain structure for more uniform properties
- Enhancing ductility to prevent failure under stress
- Facilitating diffusion of elements to alter alloy composition
- Preparing metal for cold working processes like metal forming
Proper annealing improves the workability and machinability of metals for manufacturing while optimizing their strength and durability for the intended application.
Normalizing
Normalizing is a heat treatment process used in custom fabrication to improve the ductility and modify the microstructure of steels and metal alloys. It involves heating the metal above its upper critical temperature, usually 30-50°C above, and allowing it to cool in air. This process produces a finer grain structure compared to annealing, where the metal is cooled slowly.
The benefits of normalizing include:
- Improved ductility and machinability
- Relief of internal stresses
- Refined and uniform grain structure
- Preparation for subsequent hardening
- Softening of metal for further processing
Normalizing is commonly used when machining has extensively deformed the microstructure and properties of a metal. It softens the metal, relieves internal stresses, and improves machinability and ductility. Normalizing is also used before hardening to refine the grain structure and prepare the metal for the phase transformations that occur during quenching. Overall, normalizing is an essential heat treatment process in custom fabrication when properties like ductility, machinability, and structural uniformity need to be optimized.
Hardening
Hardening is a heat treatment process that increases the hardness and strength of metals and alloys by heating above a critical temperature and then quickly cooling or ‘quenching’. The rapid cooling does not allow time for the metallic crystals to reform in their normal arrangement. Instead, the atoms are “frozen” in a chaotic state, resulting in a much harder metal.
The most common hardening process is quenching, where the hot metal is plunged into a liquid bath such as oil or water for rapid cooling. Other methods include air cooling, where the hot metal is cooled quickly by exposure to normal air temperature, and cryogenic treatment, where the metal is frozen by immersion in liquid nitrogen.
The benefits of hardening metals and alloys include:
- Increased hardness and strength
- Improved wear resistance
- Enhanced machining qualities
- Greater dimensional stability
- Higher elasticity
Hardening is commonly used for tool steels and alloy steels to give them the strength and hardness needed for cutting, pressing, extruding etc. It is an essential heat treatment process in fabrication when properties like wear resistance, fatigue strength and yield strength need to be optimized.
Tempering
Tempering is a secondary heat treatment process applied after the primary hardening process of quenching. It involves heating the metal to a temperature below the crucial temperature and then cooling.
The main purposes of tempering are:
- Relieve internal stresses induced by the hardening treatment of quenching. Quenching can leave residual stresses in the metal that can lead to distortion or cracking. Tempering helps relieve these stresses.
- Improve ductility and toughness. Quenching makes the metal very hard and brittle. Tempering makes the metal slightly softer while retaining most of the hardness, improving ductility and toughness. This reduces brittleness.
- Improve machinability. The increased hardness from quenching can make the metal more difficult to machine. Tempering softens it slightly to allow easier machining.
- Stabilize dimensions. Tempering reduces distortion and shrinkage from quenching by relieving internal stresses. This helps stabilize the dimensions.
- Reduce hardness. In some cases tempering is used just to reduce the hardness to a desired level.
The main difference between quenching and tempering is that quenching rapidly cools the hot metal to harden it, while tempering reheats the metal to controlled temperatures below the critical point to impart desired properties. Quenching makes the metal hard and brittle, tempering makes it more ductile and tough.
Case Hardening
Case hardening is a heat treatment process that hardens the surface layer of a metal while keeping the core soft and tough. It involves heating the metal component to a high temperature and then cooling the surface rapidly to harden it. The core remains unaffected by the treatment.
There are several types of case hardening processes:
- Carburizing – The metal is heated and exposed to a carbon-rich gas that diffuses carbon into the surface. This increases the carbon content and hardness at the surface.
- Nitriding – The surface is heated and exposed to ammonia gas which diffuses nitrogen into the surface layer. This creates hard nitride compounds.
- Flame hardening – An oxyacetylene torch is used to rapidly heat the metal surface which is then quenched to harden it. The core remains soft.
- Induction hardening – The surface is rapidly heated using induction coils then quenched. This selectively hardens the surface layer.
Case hardening is commonly used on gears, shafts, bearings, valves, and other components that require a hard wear-resistant surface and a tough shock-absorbing core. The gradient hardness improves fatigue life. Case hardening processes allow selective surface hardening without affecting the properties of the core metal.
Precipitation Hardening
Precipitation hardening, also known as age hardening, is a heat treatment process that increases the yield strength of malleable materials including aluminum, magnesium, steel, titanium, and some nickel based alloys. This process involves the formation of uniformly dispersed precipitates in the crystalline structure of the metal that hinder dislocation movement and thereby increase hardness and strength.
The process involves three main steps:
- Solution heat treatment – The material is heated to a sufficiently high temperature to enable precipitate forming elements to enter into solid solution. This produces a single phase supersaturated solid solution.
- Quenching – The material is rapidly cooled to form a supersaturated solid solution by preventing diffusion and precipitation of phases. This produces a soft but ductile metastable state.
- Aging – The material is heated to an intermediate temperature. This enables diffusion of atoms and leads to controlled precipitation of finely dispersed particles. These coherent precipitates interact with dislocations and impede their movement, thereby strengthening the material.
Compared to normal hardening which relies on rapid quenching, precipitation hardening allows for a more uniform distribution of finely dispersed precipitates. This provides better mechanical properties and avoids distortion and cracking. The process can also be used selectively on parts of a component, unlike other bulk hardening techniques. Precipitation hardening is widely used to strengthen nonferrous metals and alloys.
Process Selection
When selecting a heat treatment process for custom fabricated parts, there are several factors to consider:
- Metal Alloy – The alloy composition will determine which heat treatment processes are suitable. Some alloys respond favorably to hardening and tempering while others are more suited for annealing. The alloying elements like carbon, chromium, nickel etc. will influence the microstructure and properties.
- Desired Properties – The mechanical properties needed for the application will guide selection. If high hardness and strength are needed, hardening and tempering would be selected. If ductility and toughness are important, annealing may be preferable.
- Part Geometry – The size and shape of the part can determine which process will provide the most uniform results. Some processes like carburizing may be restricted based on part geometry.
- Equipment Availability – The heat treating facilities and equipment available will dictate the feasible processes. Custom fabricators should assess capabilities in-house versus outsourcing.
- Cost – The heat treatment selected should balance performance needs with costs. Simpler methods like annealing may be more economical for some applications.
By evaluating the alloy, properties needed, part geometry, capabilities, and budget, custom fabricators can determine the optimal heat treatment process for their specific application. The process chosen has a crucial impact on the microstructure and ultimate service performance. Careful selection and quality control is needed to achieve the desired characteristics.
Quality Control
Quality control is a critical part of any heat treatment process. Proper process controls and testing ensures the heat treatment achieves the desired material properties.
Importance of Process Controls and Standards
- Using standardized procedures is vital for repeatable, reliable results. This includes following established protocols for heating rates, soak times, quench media, etc.
- Process monitoring with automated data collection provides traceability. Devices like thermocouples record temperature profiles throughout the cycle.
- Heat treatment standards published by organizations like ASTM International, SAE International, AWS, and others provide essential guidelines. Facilities should maintain proper calibration of all equipment.
- Certifications like ISO 9001 help improve quality systems. Staff training and qualifications are also important for reducing variability.
Methods for Testing Effectiveness
- Hardness tests like Rockwell, Brinell and Vickers evaluate if the hardness level meets specifications. Portable testers allow for testing directly on parts.
- Tensile testing confirms strength and ductility requirements are achieved. This requires machining specimens and using universal test machines.
- Nondestructive tests like zyglo dye penetrant testing check for cracks or discontinuities caused by heat treating.
- Microstructural analysis through optical or electron microscopy validates microstructure formed. This ensures phase transformations completed properly.
- Dimensional checks verify part size was not significantly altered during heating and quenching. This includes using calibrated instruments like micrometers.
With rigorous process control and testing, manufacturers can reliably heat treat components that meet all mechanical property and quality standards. Proper quality control is key for safety-critical applications.
Conclusion
Heat treatment is crucial in custom metal fabrication, as it can significantly enhance the properties and performance of metal parts and components. This article covered the major heat treatment methods: annealing, normalizing, hardening, tempering, case hardening, and precipitation hardening. Each process serves a specific purpose, from softening to strengthening the metal.
Choosing the right heat treatment requires understanding the desired properties in the final part and precise control of heating and cooling conditions. When done correctly, heat treatment enables fabricators to deliver high-quality components that meet or exceed customer expectations.
What is Heat Treatment?
Heat treatment is a controlled process used to alter the microstructure of metals and alloys in order to change their physical and mechanical properties. The main purposes of heat treatment are to increase hardness, strength, ductility, and toughness as well as to relieve internal stresses and refine the structure. Heat treatment involves heating the metal to a specified temperature, holding it at that temperature for a set time, and then cooling it at a controlled rate.
Some of the common heat treatment processes used in custom fabrication workshops include:
- Annealing – Heating to and holding at a suitable temperature and then cooling slowly. This results in reduced hardness and increased ductility.
- Normalizing – Heating to and holding at a suitable temperature above critical, followed by air cooling. This refines the grain structure.
- Hardening – Heating to a suitable temperature above critical, followed by rapid cooling or quenching. This increases hardness significantly.
- Tempering – Reheating hardened steel to a temperature below critical to reduce brittleness and hardness. This increases ductility and toughness.
- Case hardening – Diffusion of carbon or nitrogen into the metal surface, forming a hard wear-resistant outer case with a tough ductile core.
Proper heat treatment allows the fabrication shop to tailor the properties of metals to meet the design and engineering requirements of custom parts and products. In the following sections, we will explain each technique in detail, step by step.
Annealing
Annealing is a heat treatment process used to alter the physical and sometimes chemical properties of a material. Annealing involves heating the metal to a specified temperature, holding it at that temperature for a set time, then cooling it back to room temperature.
The process softens the metal, making it more ductile and less hard, improving its machinability and responsiveness to cold working processes like rolling, forging, or bending. Annealing also relieves internal stresses that can build up in the metal during casting, welding, or machining.
There are several types of annealing processes:
- Full anneal – Heating to above the upper critical temperature, soaking, then cooling slowly. Produces a coarse pearlite structure.
- Process anneal – Heating to a temperature below critical, soaking, then cooling. Done between stages of cold working.
- Stress relief anneal – Heating to a relatively low temperature, soaking, then cooling. Reduces residual stresses only.
Key applications and benefits of annealing include:
- Softening metal for improved machinability and formability
- Relieving internal stresses to prevent cracking or distortion
- Refining the grain structure for more uniform properties
- Enhancing ductility to prevent failure under stress
- Facilitating diffusion of elements to alter alloy composition
- Preparing metal for cold working processes like metal forming
Proper annealing improves the workability and machinability of metals for manufacturing while optimizing their strength and durability for the intended application.
Normalizing
Normalizing is a heat treatment process used in custom fabrication to improve the ductility and modify the microstructure of steels and metal alloys. It involves heating the metal above its upper critical temperature, usually 30-50°C above, and allowing it to cool in air. This process produces a finer grain structure compared to annealing, where the metal is cooled slowly.
The benefits of normalizing include:
- Improved ductility and machinability
- Relief of internal stresses
- Refined and uniform grain structure
- Preparation for subsequent hardening
- Softening of metal for further processing
Normalizing is commonly used when machining has extensively deformed the microstructure and properties of a metal. It softens the metal, relieves internal stresses, and improves machinability and ductility. Normalizing is also used before hardening to refine the grain structure and prepare the metal for the phase transformations that occur during quenching. Overall, normalizing is an essential heat treatment process in custom fabrication when properties like ductility, machinability, and structural uniformity need to be optimized.
Hardening
Hardening is a heat treatment process that increases the hardness and strength of metals and alloys by heating above a critical temperature and then quickly cooling or ‘quenching’. The rapid cooling does not allow time for the metallic crystals to reform in their normal arrangement. Instead, the atoms are “frozen” in a chaotic state, resulting in a much harder metal.
The most common hardening process is quenching, where the hot metal is plunged into a liquid bath such as oil or water for rapid cooling. Other methods include air cooling, where the hot metal is cooled quickly by exposure to normal air temperature, and cryogenic treatment, where the metal is frozen by immersion in liquid nitrogen.
The benefits of hardening metals and alloys include:
- Increased hardness and strength
- Improved wear resistance
- Enhanced machining qualities
- Greater dimensional stability
- Higher elasticity
Hardening is commonly used for tool steels and alloy steels to give them the strength and hardness needed for cutting, pressing, extruding etc. It is an essential heat treatment process in fabrication when properties like wear resistance, fatigue strength and yield strength need to be optimized.
Tempering
Tempering is a secondary heat treatment process applied after the primary hardening process of quenching. It involves heating the metal to a temperature below the crucial temperature and then cooling.
The main purposes of tempering are:
- Relieve internal stresses induced by the hardening treatment of quenching. Quenching can leave residual stresses in the metal that can lead to distortion or cracking. Tempering helps relieve these stresses.
- Improve ductility and toughness. Quenching makes the metal very hard and brittle. Tempering makes the metal slightly softer while retaining most of the hardness, improving ductility and toughness. This reduces brittleness.
- Improve machinability. The increased hardness from quenching can make the metal more difficult to machine. Tempering softens it slightly to allow easier machining.
- Stabilize dimensions. Tempering reduces distortion and shrinkage from quenching by relieving internal stresses. This helps stabilize the dimensions.
- Reduce hardness. In some cases tempering is used just to reduce the hardness to a desired level.
The main difference between quenching and tempering is that quenching rapidly cools the hot metal to harden it, while tempering reheats the metal to controlled temperatures below the critical point to impart desired properties. Quenching makes the metal hard and brittle, tempering makes it more ductile and tough.
Case Hardening
Case hardening is a heat treatment process that hardens the surface layer of a metal while keeping the core soft and tough. It involves heating the metal component to a high temperature and then cooling the surface rapidly to harden it. The core remains unaffected by the treatment.
There are several types of case hardening processes:
- Carburizing – The metal is heated and exposed to a carbon-rich gas that diffuses carbon into the surface. This increases the carbon content and hardness at the surface.
- Nitriding – The surface is heated and exposed to ammonia gas which diffuses nitrogen into the surface layer. This creates hard nitride compounds.
- Flame hardening – An oxyacetylene torch is used to rapidly heat the metal surface which is then quenched to harden it. The core remains soft.
- Induction hardening – The surface is rapidly heated using induction coils then quenched. This selectively hardens the surface layer.
Case hardening is commonly used on gears, shafts, bearings, valves, and other components that require a hard wear-resistant surface and a tough shock-absorbing core. The gradient hardness improves fatigue life. Case hardening processes allow selective surface hardening without affecting the properties of the core metal.
Precipitation Hardening
Precipitation hardening, also known as age hardening, is a heat treatment process that increases the yield strength of malleable materials including aluminum, magnesium, steel, titanium, and some nickel based alloys. This process involves the formation of uniformly dispersed precipitates in the crystalline structure of the metal that hinder dislocation movement and thereby increase hardness and strength.
The process involves three main steps:
- Solution heat treatment – The material is heated to a sufficiently high temperature to enable precipitate forming elements to enter into solid solution. This produces a single phase supersaturated solid solution.
- Quenching – The material is rapidly cooled to form a supersaturated solid solution by preventing diffusion and precipitation of phases. This produces a soft but ductile metastable state.
- Aging – The material is heated to an intermediate temperature. This enables diffusion of atoms and leads to controlled precipitation of finely dispersed particles. These coherent precipitates interact with dislocations and impede their movement, thereby strengthening the material.
Compared to normal hardening which relies on rapid quenching, precipitation hardening allows for a more uniform distribution of finely dispersed precipitates. This provides better mechanical properties and avoids distortion and cracking. The process can also be used selectively on parts of a component, unlike other bulk hardening techniques. Precipitation hardening is widely used to strengthen nonferrous metals and alloys.
Process Selection
When selecting a heat treatment process for custom fabricated parts, there are several factors to consider:
- Metal Alloy – The alloy composition will determine which heat treatment processes are suitable. Some alloys respond favorably to hardening and tempering while others are more suited for annealing. The alloying elements like carbon, chromium, nickel etc. will influence the microstructure and properties.
- Desired Properties – The mechanical properties needed for the application will guide selection. If high hardness and strength are needed, hardening and tempering would be selected. If ductility and toughness are important, annealing may be preferable.
- Part Geometry – The size and shape of the part can determine which process will provide the most uniform results. Some processes like carburizing may be restricted based on part geometry.
- Equipment Availability – The heat treating facilities and equipment available will dictate the feasible processes. Custom fabricators should assess capabilities in-house versus outsourcing.
- Cost – The heat treatment selected should balance performance needs with costs. Simpler methods like annealing may be more economical for some applications.
By evaluating the alloy, properties needed, part geometry, capabilities, and budget, custom fabricators can determine the optimal heat treatment process for their specific application. The process chosen has a crucial impact on the microstructure and ultimate service performance. Careful selection and quality control is needed to achieve the desired characteristics.
Quality Control
Quality control is a critical part of any heat treatment process. Proper process controls and testing ensures the heat treatment achieves the desired material properties.
Importance of Process Controls and Standards
- Using standardized procedures is vital for repeatable, reliable results. This includes following established protocols for heating rates, soak times, quench media, etc.
- Process monitoring with automated data collection provides traceability. Devices like thermocouples record temperature profiles throughout the cycle.
- Heat treatment standards published by organizations like ASTM International, SAE International, AWS, and others provide essential guidelines. Facilities should maintain proper calibration of all equipment.
- Certifications like ISO 9001 help improve quality systems. Staff training and qualifications are also important for reducing variability.
Methods for Testing Effectiveness
- Hardness tests like Rockwell, Brinell and Vickers evaluate if the hardness level meets specifications. Portable testers allow for testing directly on parts.
- Tensile testing confirms strength and ductility requirements are achieved. This requires machining specimens and using universal test machines.
- Nondestructive tests like zyglo dye penetrant testing check for cracks or discontinuities caused by heat treating.
- Microstructural analysis through optical or electron microscopy validates microstructure formed. This ensures phase transformations completed properly.
- Dimensional checks verify part size was not significantly altered during heating and quenching. This includes using calibrated instruments like micrometers.
With rigorous process control and testing, manufacturers can reliably heat treat components that meet all mechanical property and quality standards. Proper quality control is key for safety-critical applications.
Conclusion
Heat treatment is crucial in custom metal fabrication, as it can significantly enhance the properties and performance of metal parts and components. This article covered the major heat treatment methods: annealing, normalizing, hardening, tempering, case hardening, and precipitation hardening. Each process serves a specific purpose, from softening to strengthening the metal.
Choosing the right heat treatment requires understanding the desired properties in the final part and precise control of heating and cooling conditions. When done correctly, heat treatment enables fabricators to deliver high-quality components that meet or exceed customer expectations.
Ready to see CADDi Drawer in action? Get a personalized demo.
Subscribe to our Blog!
Related Resources


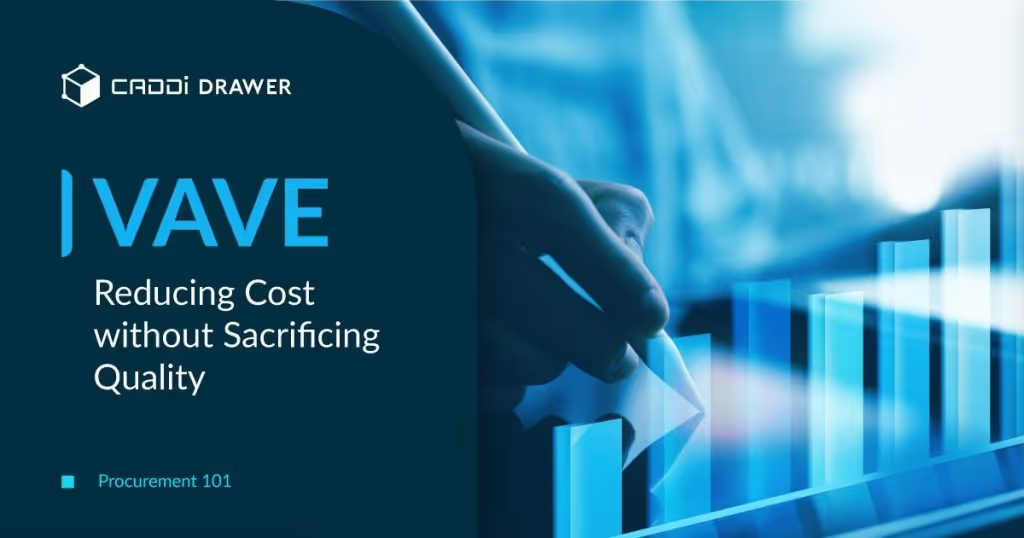

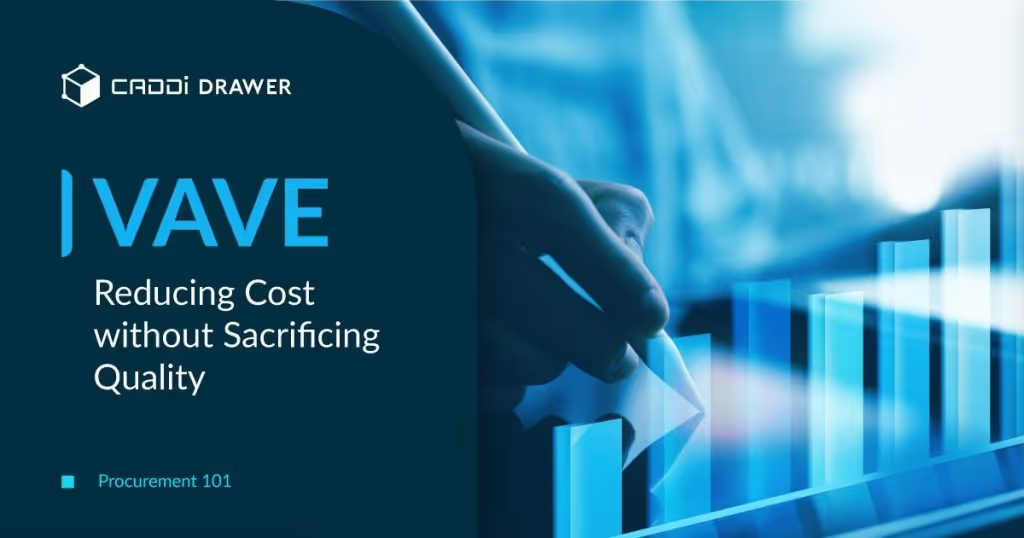
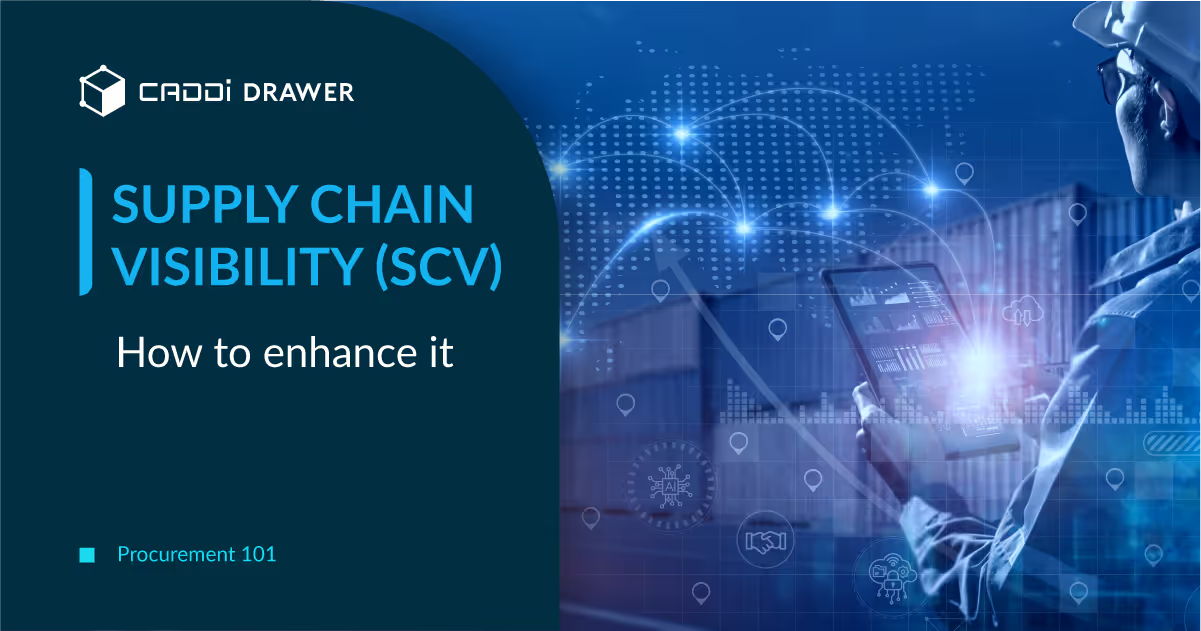