Driving World-Leading Manufacturing through "One SUBARU"
Before
Inquiries regarding drawing information to the design department often took a week or more for a response due to heavy workloads.
After
Inquiries became unnecessary, enabling the search and collection of information directly, resulting in the elimination of approximately several hundred hours/month of non-productive work.
Responding to the Greatest Transformation in the Automotive Industry in 100 Years: The Urgent Need for Increased Productivity
The automotive industry is currently experiencing a once-in-a-century transformation, driven by the convergence of the CASE (Connected, Autonomous/Automated, Shared, Electric) paradigm. This period demands not only product innovation but also a reformation of manufacturing processes. In response, SUBARU Corporation has announced a new management strategy, focusing on the "One SUBARU" initiative. This strategy emphasizes returning to a flexible and agile organizational culture, closely integrating manufacturing, development, and the supply chain to enhance productivity.
{{download}}
Within this context, the Cost Innovation Promotion Department was established to address cost-related challenges and formulate strategies across the organization. SUBARU aims to be at the forefront of "Manufacturing Innovation" and "Value Creation" under its new management system. One significant goal in "Manufacturing Innovation" is to halve the number of processes, components, and steps involved in production, starting with the reduction of non-productive work.
The existing system at SUBARU required specific information such as part numbers or design notification numbers to search for drawings. This often necessitated inquiries to the busy design department, with responses taking up to one or two weeks, causing delays in operations. Even within the design department, finding drawings was challenging for those working in different areas or with less experience.
Achieving Hundreds of Hours per Month in Non-Productive Work Reduction by Visualizing and Utilizing Drawing Data Across Departments
SUBARU sought ways to leverage its accumulated drawing assets to reduce non-productive tasks. The company identified CADDi Drawer, a cloud-based drawing data management tool, as a potential solution.
"I have about 20 years of experience in design," says Kei Matsumura, First Section, EP Planning, Cost Innovation Promotion Department. "In the design work, searching for drawings took up a significant amount of time. Sometimes, this was acknowledged as part of our performance, but I always felt that if I had more time, I could engage in work that added more value. When I learned about CADDi Drawer from an executive introduction, it immediately resonated with me, and I became an advocate for its adoption."
"When I learned about CADDi Drawer, it immediately resonated with me, and I became an advocate for its adoption" - Kei Matsumura, Cost Innovation Promotion Department
Following the introduction of CADDi Drawer, SUBARU succeeded in reducing the time spent on drawing searches and inquiries across the company by approximately several hundred hours per month. As its use expands across departments, this reduction in time is expected to multiply.
Ido, from the Cost Innovation Promotion Department, further elaborates on the benefits of CADDi Drawer:
"Many data management solutions focus on merely accumulating information, but CADDi Drawer allows us to analyze and utilize the data within the same system. For example, when comparing two similar drawings with different costs, we can use past data to investigate what factors contribute to cost variations from a technical perspective. Previously, when we wanted to learn more about the content of a drawing, we had to rely on inquiries to the designers, but now CADDi Drawer has become an indispensable tool that bridges the gap between creators and users, and between the past and the future."
Promoting "One SUBARU" with Company-Wide Use of CADDi Drawer to Achieve World-Leading Manufacturing
The introduction of CADDi Drawer has also contributed to talent development. Previously, individuals working in different design areas or with less experience needed to be guided to specific drawing numbers to search for the right documents. Now, they can search for drawings by product name or material using keywords, making it easier to find the information they need without the need for inquiries.
"Before, if you didn’t know the drawing number, you couldn’t search for a drawing. Even if you wanted to inquire, you’d first need to figure out who to ask. Now, even without the drawing number, you can search by part name. For example, typing 'bumper' will immediately bring up the relevant drawing, making information much more accessible. The amount of information that can be referenced for decision-making has increased dramatically since CADDi Drawer was introduced. Moreover, the cycle of researching and obtaining information by oneself enhances learning, and those using CADDi Drawer are undoubtedly becoming more skilled. The new value creation, evolution in creativity, and the impact on human resource development are immeasurable. Moving forward, I hope CADDi Drawer will further energize communication, serving as a starting point for projects from planning through after-sales, involving the entire supply chain. Our goal is to create an environment where everyone uses it."
"The amount of information that can be referenced for decision-making has increased dramatically since CADDi Drawer was introduced." - Kei Matsumura, Cost Innovation Promotion Department
The Cost Innovation Promotion Department is now actively disseminating information about CADDi Drawer throughout the company. This has sparked widespread interest, and the number of proactive users is steadily increasing. These key users are driving the broader adoption of the tool.
Otani, another member of the Cost Innovation Promotion Department, shares insights on the current usage:
"When we talk to users, they tell us they can’t imagine working without CADDi Drawer anymore. Those who understand its value are using it proactively. By expanding its use to more departments, we believe we can transform the old structure and achieve the highly productive work style we envision."
"Our colleagues who use CADDi Drawer tell us they can't imagine working without it anymore." - Yuji Otani, Cost Innovation Promotion Department
SUBARU’s "One SUBARU" initiative aims to standardize CADDi Drawer across the company. They envision a future where CADDi Drawer is the first tool employees turn to, not only in design and manufacturing departments but also in subsidiaries, overseas affiliates, and suppliers. Through this comprehensive adoption, SUBARU strives to achieve world-leading manufacturing under its new management system.
Ready to see CADDi Drawer in action? Get a personalized demo.
Take this case study on-the-go
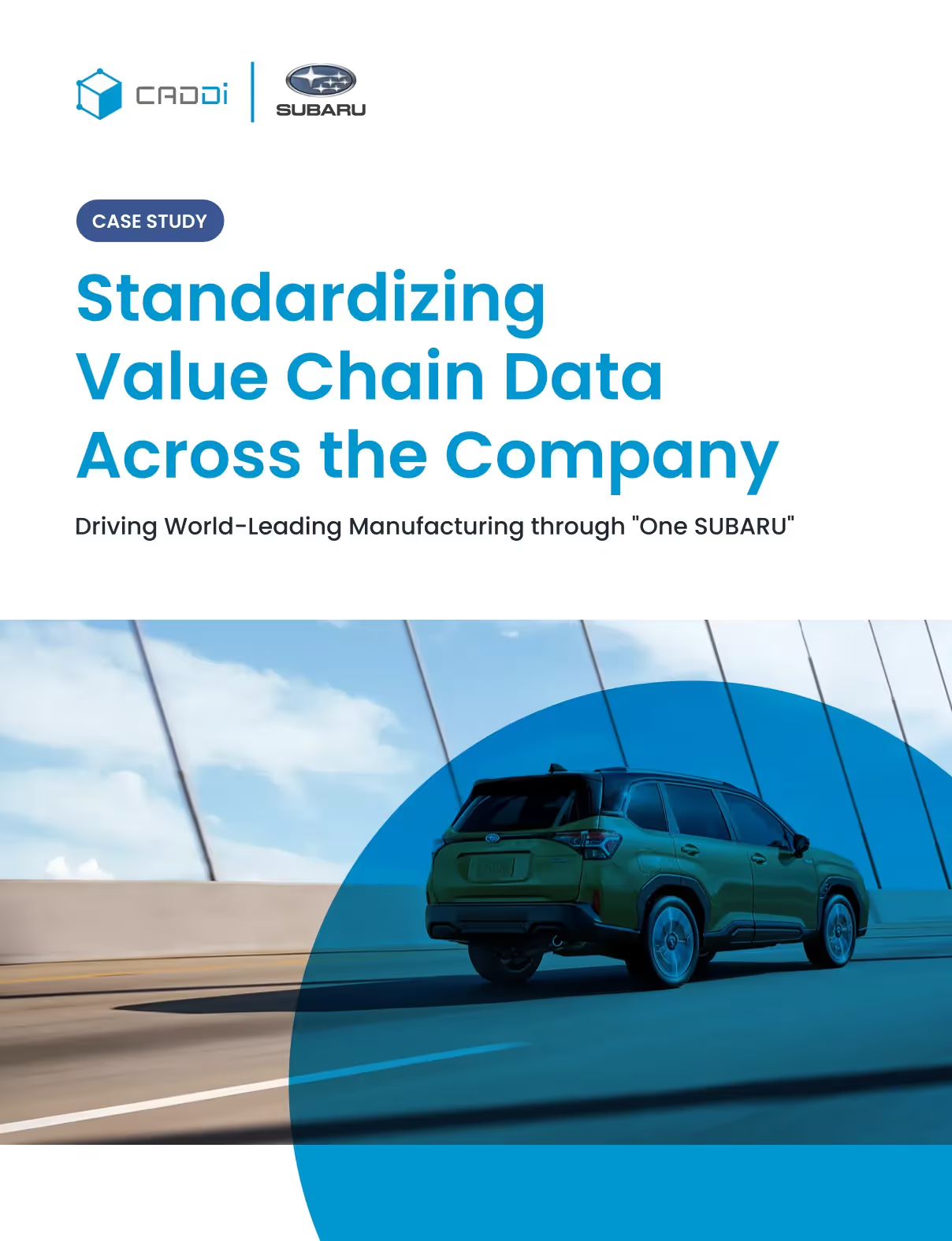