Achieving long-abandoned cost reductions
Before
Information on similar products and past purchase history was siloed, leading to slow data retrieval. Veteran and less experienced employees assessed projects differently, leading to discrepancies and errors.
After
Team members can quickly search for similar products and past purchase history. Standardized workflows help every team member work more efficiently, no matter their experience level. With similarity search, team members can validate costs, spot unusual pricing, and speed up the approval process.
Kawasaki Heavy Industries, Ltd. is a comprehensive engineering manufacturer engaged in a wide range of businesses, including ships and railway vehicles, motorcycles, industrial plants, precision machinery, and robots. The Robot Division has set a goal of quadrupling its current sales by 2030.
A significant roadblock to achieving this goal was productivity per employee. In the Robot Division, the Procurement Department in particular had issues with price estimates and workflows of procured parts differing depending on the buyer in charge. CADDi was introduced to solve this situation. After a two-week trial in July 2023, it was officially introduced in December of the same year.
We discussed the impact CADDi has had on the Robot Division with three Kawasaki employees:
Ono Takushi, Executive, Procurement Department
Sakai Koichi, Department Manager, Procurement
Hayashi Kazuki, Project Leader, Procurement
Utilizing CADDi to achieve business efficiency
In the past, the company's procurement department had been creating and using a database in Excel that could estimate reasonable costs by inputting information from drawings. However, the database had to be updated manually, and it had various problems, such as being slow to operate due to the large amount of data it handled.
By introducing CADDi, it became possible to quickly search for similar drawings, reducing the time to find a particular part by 4.4 minutes per case. This represents a reduction of more than $20,000 in labor costs per year.
Furthermore, the Procurement Department conducted cost analysis using CADDi, which resulted in the discovery of many cost reduction opportunities.
Turning dormant data into a valuable easy-to-access asset with CADDi
Within the three months since the introduction of CADDi, over 90% of the Procurement Department adopted the product for weekly if not daily use. CADDi's many quality-of-life features and ease of use made it an obvious fit in the procurement team's workflows.
Project leader Hayashi Kazuki calls out CADDi's Viewer feature as an example of CADDi's ease of use. Before, to find a particular drawing, they had to manually open each one, one at a time, and check if it was correct. CADDi's ability to bring up every relevant drawing at once alongside the pricing data, while highlighting differences between them, made this task go from hundreds of clicks to just one.
"With CADDi, you can view multiple drawings at a glance, so you can see when, to which supplier, and for how much an order was placed."
- Hayashi Kazuki, Project Leader
Another quality-of-life feature called out by Mr. Kazuki is the ability to search multiple part numbers simultaneously. Their requests for quotes usually came in with a long list of part numbers that they used to have to search for one at a time. Again, a time-consuming, tedious task was turned into a quick and simple one-click solution. These time saves may not seem significant at first, but given how many times these tasks are repeated in a day, optimizing them quickly becomes extremely valuable.
With CADDi, data becomes a true asset: something that could be easily accessed and analyzed to inform decisions.
"With the introduction of CADDi, we have not only been able to manage and store data, but we have also been able to use it to create new value."
- Hayashi Kazuki, Project Leader
Aiming to improve productivity across the entire company
The Procurement Department is expected to be able to increase its work efficiency by more than 5% in just three months with CADDi. In the future, the company plans to expand CADDi Drawer to other departments as well, aiming to improve productivity across the entire company.
We wanted to see why CADDi's usage across the Procurement Department soared in such a short time, so we asked Project Leader Hayashi Kazuki, his superior Ono, and Procurement Department Manager Sakai Koichi about their efforts after the introduction.
How CADDi drove adoption through user research and clear communication
When introducing the system, each department first set a goal and explained how CADDi would be used to reach it. After that, an explanatory meeting was held for the entire department. Instead of simply telling employees how to use the system, each employee was interviewed individually about their work. Based on the work flow and labor cost breakdown that was identified, more detailed usage and benefits of using the system were explained.
The utilization rate of CADDi gradually increased, but the productivity gap between those who used the system and those who did not began to widen. As a result, Mr. Hayashi held use case sharing sessions to appeal to employees with low utilization rates. By providing support, the utilization rate gradually increased up to 90%.
"Once they've become adept at using it to a certain extent, they start saying it's easy to use and convenient, and they start to use it more and more. So we made sure to communicate thoroughly with them until they got to that point."
- Hayashi Kazuki, Project Leader
CADDi's contribution to the development of junior employees
Mr. Hayashi was selected to lead the CADDi initiative. Hayashi has always been highly praised for his work attitude and results, but Ono says that since he was put in charge of the CADDi project, his work performance has improved even further.
Through the promotion of CADDi, Mr. Hayashi has been able to increase his collaboration with other departments and the project has allowed him to consider business problems from a higher perspective.
The growth opportunities for Mr. Hayashi continue to develop. Mr. Takushi notes that the results of business improvements using CADDi are regularly reported at meetings attended by the heads of each division, and in the future Mr. Hayashi will be tasked with promoting CADDi Drawer at this meeting across divisions.
Promoting CADDi across divisions to achieve "Group Vision 2030"
CADDi customer success meets with the Kawasaki team once per week to check progress and formulate future strategies to further improve productivity gains.
"Right after the implementation, I had many meetings with Aritomo from CADDi Customer Success. The response was quick, and I was able to get the materials and information I needed quickly, which was very helpful."
Hayashi Kazuki, Project Leader
The company has set a "Group Vision 2030" that aims to quadruple sales over the next six years. To that end, the Procurement Department is working to improve work efficiency. By using CADDi, the path to efficiency has gradually become clear, but there are still many challenges to overcome. "No matter how good a system is, it won't produce results unless it is widely adopted. It is important to have a common goal in order to increase utilization rates," says Ono.
Kawasaki Heavy Industries, Ltd. will continue to use CADDi to improve business efficiency across the company.
Ready to see CADDi Drawer in action? Get a personalized demo.
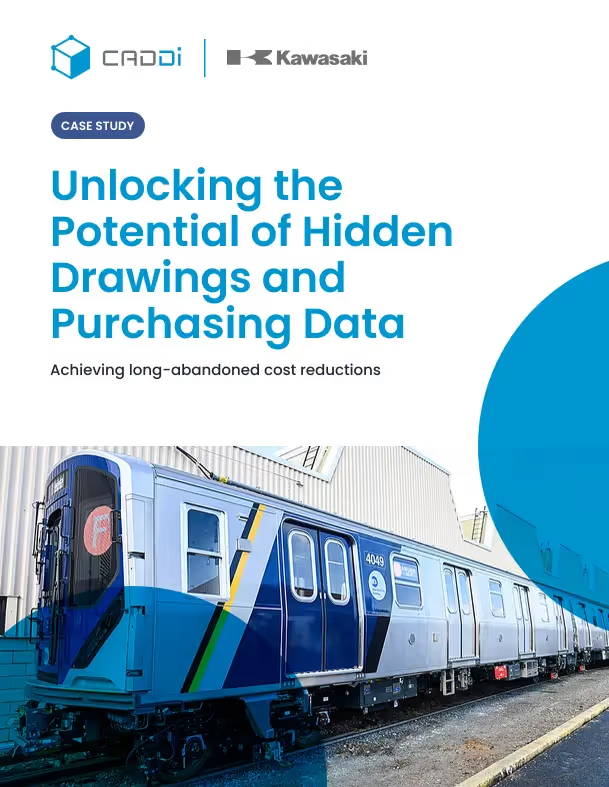