Parts Proliferation: The Junk Drawer of Manufacturing Chaos
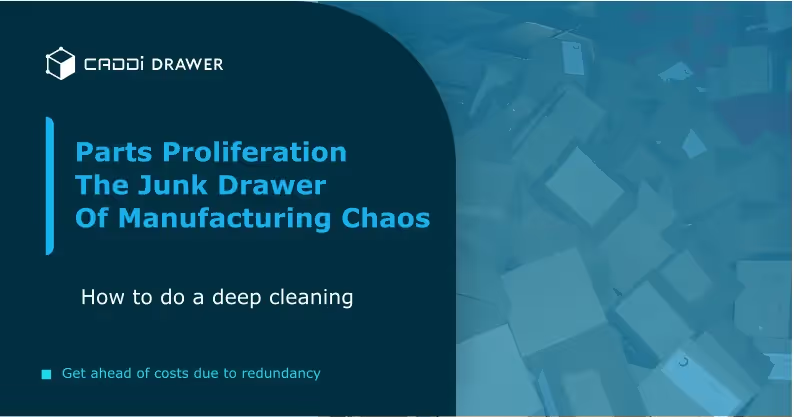
Table of Contents
The Problem of Parts Proliferation: How We Got Here and Why It’s Costing You Big
Let’s be honest—manufacturing isn’t exactly the land of sunshine and rainbows when it comes to efficiency. For decades, organizations have been hoarding parts like old cars behind your uncle’s house, adding more and more SKUs to an already bloated inventory with the enthusiasm of finding a good deal on an auction lot. But unlike that 97 Camry, most of these parts are far from valuable.
Welcome to the world of parts proliferation, where every slightly modified widget gets a unique ID, design engineers reinvent the wheel daily, and procurement teams are drowning in a sea of interchangeable bolts, brackets, and bushings. It’s messy, expensive, and completely avoidable. Yet here we are.
What is Parts Proliferation?
Parts proliferation refers to the excessive creation and accumulation of parts in a company's inventory, often resulting in hundreds (or thousands) of redundant, duplicate, or near-duplicate components. It’s like having five remotes for your TV—each does basically the same thing, but you can’t find the one you actually need when it matters.
The Ugly Truth: The Financial Cost of Parts Proliferation
Let’s get to the cold, hard numbers, because nothing speaks louder than the bottom line:
- Inventory Costs: Each redundant part adds an average of $4,500 to $7,500 annually in inventory carrying costs, including storage, handling, and obsolescence.
- Procurement Inefficiencies: Overlapping and redundant parts mean your procurement team is spending unnecessary time and money sourcing and managing duplicate parts from multiple suppliers.
- Engineering Time: Redesigning or specifying new parts instead of reusing existing ones can consume up to 30% of an engineer’s work hours, translating into thousands of hours in lost productivity.
- Lifecycle Costs: Proliferated parts means new procedures for each part, complicating maintenance and repair operations which often results in excess downtime and spare part overstock. That doesn’t even touch on how the costs can vary greatly as some of those parts start to go EOL
- Lost Negotiation Leverage: Consolidating part numbers allows for better volume discounts. Failing to do so costs manufacturers an estimated 10-15% premium on procurement.
A Deloitte report estimates that up to 60% of part numbers in a typical manufacturing database are duplicates or obsolete. Multiply these inefficiencies across product lifecycles, and you’re staring at millions of dollars in lost value.
How Did We Get Here? A Snarky Retrospective
Let’s take a quick trip down memory lane to examine the ingenious (read: disastrous) ways manufacturers created this problem:
- The Heroic Engineer Syndrome
Engineers love designing. What they don’t love? Digging through poorly indexed databases to find an existing part. Why reuse a part when you can flex your CAD muscles and create a shiny new one? It’s faster (for them), and they aren’t the ones maintaining the database. - Siloed Teams
Design, procurement, and manufacturing teams might as well exist in parallel universes. Communication is often so bad that one team doesn’t even realize a perfectly good part exists because another team buried it in an email attachment three years ago. - "Just In Case" Stockpiling
Somewhere along the way, someone decided it was a good idea to keep a few extra options on hand—just in case. Fast forward a decade, and now you’re paying to store 17 versions of the same flange. - ERP as the Junk Drawer
Enterprise Resource Planning (ERP) systems are supposed to streamline operations. Instead, they’ve become the digital equivalent of a junk drawer, stuffed with redundant part numbers – we all know no one has time to clean up that mess. - Lack of Accountability
Everyone assumes managing parts inventory is someone else’s job. Spoiler alert: It’s no one’s job until the CFO sees the bill.
The Downstream Fallout: Why You Should Care
Sure, parts proliferation is a costly and time consuming hassle for procurement, but the real kicker comes when the ripple effects hit your bottom line:
- Product Development Delays: Engineers waste valuable time searching for parts or designing duplicates. That’s time better spent on innovation. And every release delay delays the next release even more.
- Missed Revenue Opportunities: Products delayed to market due to part availability or confusion mean lost sales and a competitive disadvantage.
- Operational Inefficiency: Maintenance crews and assembly lines face headaches when trying to source the correct part among duplicates, leading to unnecessary downtime. Plus, frustrated workers are workers looking for other jobs—do you have the time to rehire?
- Customer Dissatisfaction: Using slightly different parts in the same product line leads to inconsistencies in quality, frustrating your customers.
The Real Solution: CADDi’s AI Data Platform
Let’s stop pretending that the answer to parts proliferation is more spreadsheets or stern memos to engineering. CADDi’s AI-Driven Data Platform offers a game-changing solution:
- Holistic Data Integration
CADDi doesn’t just catalog your parts; it intelligently links drawings, purchase orders, quotations, defect reports, work instructions, and CAM data. It’s like a deep spring clean for your manufacturing operations—decluttering and organizing everything you need. - AI-Powered Search
Using machine learning, CADDi enables engineers, procurement specialists, and operations teams to quickly retrieve drawings and all related assets. Instead of digging through endless folders, you’ll get what you need in seconds. - Historical Data Reuse
The platform makes it easy to identify and reuse existing parts, reducing redundancies and cutting unnecessary costs. That’s not just efficiency; it’s profitability. - Collaborative Insights
CADDi breaks down silos by providing a shared platform where design, procurement, and manufacturing teams can align. No more “we didn’t know we already had that” moments. - Tailored Recommendations
The platform suggests consolidation opportunities and highlights cost-saving options, helping you negotiate better supplier terms and reduce your parts inventory.
The ROI of Cleaning Up the Mess
Manufacturers who’ve tackled parts proliferation with CADDi have seen dramatic results:
- 30% Reduction in Inventory Costs: Consolidating redundant parts frees up valuable resources.
- 90% Faster Engineering Search Time: Engineers spend less time searching and more time innovating.
- 20% Procurement Savings: Negotiating better supplier terms becomes possible with streamlined parts lists.
- Improved Product Quality: Consistent part usage means fewer defects and better customer satisfaction.
Interactive Tour: See CADDi in Action
Ready to stop hemorrhaging money and start optimizing your operations? Take an interactive tour of CADDi’s Smart Manufacturing Platform and see how we can declutter your parts inventory, slash costs, and transform your business.
It’s time to deep clean your inventory, save millions, and finally put an end to the chaos of parts proliferation. Don’t wait for another quarterly financial report to remind you how costly this problem really is. Dive in and make your parts inventory work for you—not against you.
The Problem of Parts Proliferation: How We Got Here and Why It’s Costing You Big
Let’s be honest—manufacturing isn’t exactly the land of sunshine and rainbows when it comes to efficiency. For decades, organizations have been hoarding parts like old cars behind your uncle’s house, adding more and more SKUs to an already bloated inventory with the enthusiasm of finding a good deal on an auction lot. But unlike that 97 Camry, most of these parts are far from valuable.
Welcome to the world of parts proliferation, where every slightly modified widget gets a unique ID, design engineers reinvent the wheel daily, and procurement teams are drowning in a sea of interchangeable bolts, brackets, and bushings. It’s messy, expensive, and completely avoidable. Yet here we are.
What is Parts Proliferation?
Parts proliferation refers to the excessive creation and accumulation of parts in a company's inventory, often resulting in hundreds (or thousands) of redundant, duplicate, or near-duplicate components. It’s like having five remotes for your TV—each does basically the same thing, but you can’t find the one you actually need when it matters.
The Ugly Truth: The Financial Cost of Parts Proliferation
Let’s get to the cold, hard numbers, because nothing speaks louder than the bottom line:
- Inventory Costs: Each redundant part adds an average of $4,500 to $7,500 annually in inventory carrying costs, including storage, handling, and obsolescence.
- Procurement Inefficiencies: Overlapping and redundant parts mean your procurement team is spending unnecessary time and money sourcing and managing duplicate parts from multiple suppliers.
- Engineering Time: Redesigning or specifying new parts instead of reusing existing ones can consume up to 30% of an engineer’s work hours, translating into thousands of hours in lost productivity.
- Lifecycle Costs: Proliferated parts means new procedures for each part, complicating maintenance and repair operations which often results in excess downtime and spare part overstock. That doesn’t even touch on how the costs can vary greatly as some of those parts start to go EOL
- Lost Negotiation Leverage: Consolidating part numbers allows for better volume discounts. Failing to do so costs manufacturers an estimated 10-15% premium on procurement.
A Deloitte report estimates that up to 60% of part numbers in a typical manufacturing database are duplicates or obsolete. Multiply these inefficiencies across product lifecycles, and you’re staring at millions of dollars in lost value.
How Did We Get Here? A Snarky Retrospective
Let’s take a quick trip down memory lane to examine the ingenious (read: disastrous) ways manufacturers created this problem:
- The Heroic Engineer Syndrome
Engineers love designing. What they don’t love? Digging through poorly indexed databases to find an existing part. Why reuse a part when you can flex your CAD muscles and create a shiny new one? It’s faster (for them), and they aren’t the ones maintaining the database. - Siloed Teams
Design, procurement, and manufacturing teams might as well exist in parallel universes. Communication is often so bad that one team doesn’t even realize a perfectly good part exists because another team buried it in an email attachment three years ago. - "Just In Case" Stockpiling
Somewhere along the way, someone decided it was a good idea to keep a few extra options on hand—just in case. Fast forward a decade, and now you’re paying to store 17 versions of the same flange. - ERP as the Junk Drawer
Enterprise Resource Planning (ERP) systems are supposed to streamline operations. Instead, they’ve become the digital equivalent of a junk drawer, stuffed with redundant part numbers – we all know no one has time to clean up that mess. - Lack of Accountability
Everyone assumes managing parts inventory is someone else’s job. Spoiler alert: It’s no one’s job until the CFO sees the bill.
The Downstream Fallout: Why You Should Care
Sure, parts proliferation is a costly and time consuming hassle for procurement, but the real kicker comes when the ripple effects hit your bottom line:
- Product Development Delays: Engineers waste valuable time searching for parts or designing duplicates. That’s time better spent on innovation. And every release delay delays the next release even more.
- Missed Revenue Opportunities: Products delayed to market due to part availability or confusion mean lost sales and a competitive disadvantage.
- Operational Inefficiency: Maintenance crews and assembly lines face headaches when trying to source the correct part among duplicates, leading to unnecessary downtime. Plus, frustrated workers are workers looking for other jobs—do you have the time to rehire?
- Customer Dissatisfaction: Using slightly different parts in the same product line leads to inconsistencies in quality, frustrating your customers.
The Real Solution: CADDi’s AI Data Platform
Let’s stop pretending that the answer to parts proliferation is more spreadsheets or stern memos to engineering. CADDi’s AI-Driven Data Platform offers a game-changing solution:
- Holistic Data Integration
CADDi doesn’t just catalog your parts; it intelligently links drawings, purchase orders, quotations, defect reports, work instructions, and CAM data. It’s like a deep spring clean for your manufacturing operations—decluttering and organizing everything you need. - AI-Powered Search
Using machine learning, CADDi enables engineers, procurement specialists, and operations teams to quickly retrieve drawings and all related assets. Instead of digging through endless folders, you’ll get what you need in seconds. - Historical Data Reuse
The platform makes it easy to identify and reuse existing parts, reducing redundancies and cutting unnecessary costs. That’s not just efficiency; it’s profitability. - Collaborative Insights
CADDi breaks down silos by providing a shared platform where design, procurement, and manufacturing teams can align. No more “we didn’t know we already had that” moments. - Tailored Recommendations
The platform suggests consolidation opportunities and highlights cost-saving options, helping you negotiate better supplier terms and reduce your parts inventory.
The ROI of Cleaning Up the Mess
Manufacturers who’ve tackled parts proliferation with CADDi have seen dramatic results:
- 30% Reduction in Inventory Costs: Consolidating redundant parts frees up valuable resources.
- 90% Faster Engineering Search Time: Engineers spend less time searching and more time innovating.
- 20% Procurement Savings: Negotiating better supplier terms becomes possible with streamlined parts lists.
- Improved Product Quality: Consistent part usage means fewer defects and better customer satisfaction.
Interactive Tour: See CADDi in Action
Ready to stop hemorrhaging money and start optimizing your operations? Take an interactive tour of CADDi’s Smart Manufacturing Platform and see how we can declutter your parts inventory, slash costs, and transform your business.
It’s time to deep clean your inventory, save millions, and finally put an end to the chaos of parts proliferation. Don’t wait for another quarterly financial report to remind you how costly this problem really is. Dive in and make your parts inventory work for you—not against you.