Update on digital twins and more for digital manufacturing
New digital approaches leveraging cloud simulations and other advanced analytics are helping manufacturers optimize production lines and end products.
At the forefront of digital transformation (DX) initiatives is digital manufacturing. Leveraging an integrated computer-based approaches for design, simulation, testing, and production, the use of digital manufacturing could double over the next two years to become a $767B market before 2027. In fact, digital manufacturing is part of a larger trend towards digitization for efficiency and increased ability to customize products.
Common permutations include sensor-based IoT functions, cloud-connected computer-aided design (CAD) and engineering (CAE), and digital twins. Artificial intelligence and machine learning are seeing rapid adoption as well — especially to predict the ramifications of manufacturing process changes and automate decisionmaking.
Common applications include those in smart factories, additive manufacturing, and operations specializing in custom and on-demand manufacturing. Circular-economy initiatives also benefit from digital-manufacturing approaches for the way in which the latter maximizes resource efficiencies.
We recently asked several industry experts about these digital-manufacturing variations and applications. Here’s what those experts had to say.
MEET THE EXPERTS
Arvind Rangarajan | Global head of software and data • HP Personalization and 3D Printing
Jacques Lemire | Director — motors and motion business unit • Designatronics SDP/SI
Jessie Frazelle | Cofounder and CEO • Zoo Corp.
Karthikeyan (Karthikk) Munirathinam | Director of digitalization • Schaeffler Americas
Michal Wierzchowski | VP of operations • Jabil
Ori Yudilevich | CTO • MaterialsZone
Robert Luchars | Executive VP • ECM PCB Stator Technology
Yoshi Umeno | Industry manager — global medical and robotics • Kollmorgen
Yushiro Kato | Co-founder and CEO • CADDi
Describe how data travels through one digital-manufacturing operation.
Yudilevich: MaterialsZone facilitates seamless materials data management across organizations — standardizing, normalizing, and securely storing information in a cloud-based platform accessible from anywhere. This collaborative environment supports the entire data lifecycle and makes it ready for slicing-and-dicing, querying, visualization, analysis, and AI-based predictions.
In additive manufacturing, material selection and printing configuration parameters strongly influence the quality of the end product and its suitability as defined by regulatory and sustainability constraints. MaterialsZone addresses these challenges by offering unique AI predictive capabilities supported by an explainable AI dashboard that uses the SHAP values technique. These tools empower the engineer by yielding deep insights into otherwise inaccessible multi-parameter spaces.
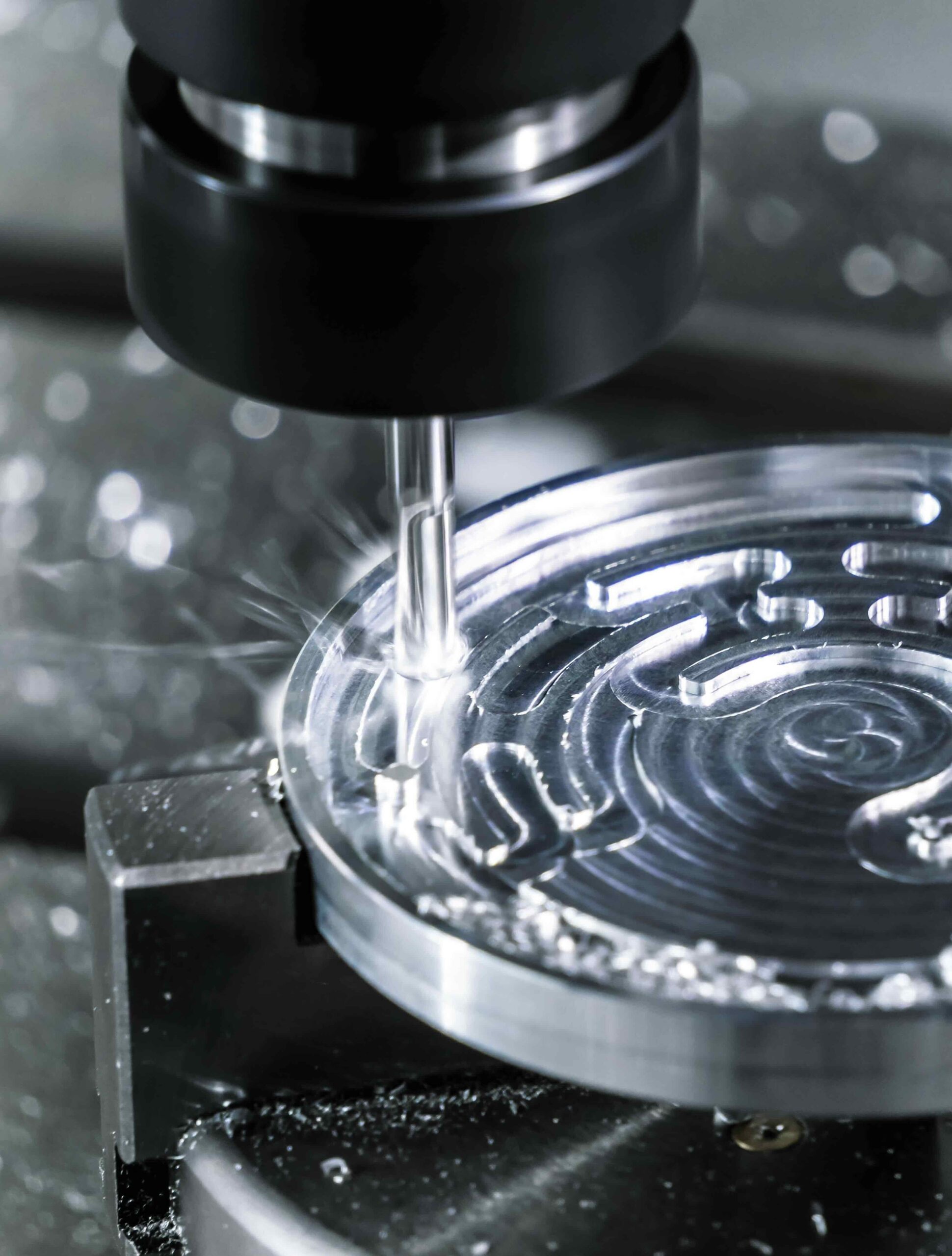
What technologies of yours are spurring innovation in digital manufacturing?
Kato: CADDi Drawer, designed to support DX in the manufacturing industry, is a unique AI-enabled search platform that centralizes drawings in one platform regardless of format with proprietary image-analysis algorithms (with a patent pending). Through high-precision similarity searches on the most important digital asset in manufacturing, drawings, it enables cost reduction in design, procurement, and production departments.
CADDi Drawer is not merely a drawing management tool; it serves as a powerful knowledge retention solution. In procurement, essential data is often scattered across decentralized databases and the minds of employees, resulting in a significant knowledge drain when employees leave. Using AI-enabled shape recognition, CADDi Drawer centralizes drawings and cross-references them with purchase histories, effectively preserving crucial knowledge and reducing the time it takes to search for drawings by up to 80%.
Wierzchowski: We’re enhancing our overall ecosystem by integrating manufacturing-related functions within the shop floor control system. This integration is facilitated by the adoption of a low-code programming language, which enables us to efficiently scale and increase our adaptability to meet the unique needs of our end users. The success of this modernization stems from the business process management system we established four years ago, which catalyzed the adoption of Jabil’s enterprise process standards.
We’re also advancing our enterprise capabilities in the fields of computer vision, knowledge and language processing, and analytics and intelligence. The Jabil strategy for rapid industrialization and deployment of technologies leverages a modular architecture composed of various technologies. These can be combined to fulfill precise customer needs. As a result, we’re cultivating new capabilities to analyze data; address failures in realtime; and anticipate as well as prevent potential failures before they occur.
Any new offerings leveraging AI?
Kato: CADDi is addressing critical issues in the manufacturing industry, offering innovative solutions for procurement and data management, including CADDi Drawer — a SaaS solution that turns drawing libraries into searchable assets for manufacturers. By allowing easy and precise searches for drawings (critical digital in manufacturing) CADDi Drawer helps manufacturing companies save costs in their design, procurement, and production departments.
As a global manufacturing solutions provider servicing 600-plus supply chain partners fabricating custom metal partners, CADDi realized a pain point every customer seemed to have — accessing past drawings was an absolute nightmare. So, the team developed a proprietary image analysis algorithm to help clients digitize and search for drawings much faster and more accurately than any other platform in the marketplace. CADDi uses AI to streamline and digitize the procurement process.
Realizing the impact of this solution, the team launched CADDi Drawer as a SaaS to help manufacturers procure parts for less by reducing pricing inconsistencies and fabricators win more deals by semi-automating their quotations. CADDi Drawer reduces drawing search time by 80% and overall procurement costs by 30%.
What makes CADDi unique in the industry is that is designed with the manufacturing industry and its needs top of mind. If you imagine AI as a child that continues to learn, CADDi’s AI has been born and raised in manufacturing. It doesn’t go off on tangents in other disciplines. It simply knows manufacturing in and out.
Lemire: Our machining centers (and Industry 4.0 implementation of intelligent digital technologies in our manufacturing and industrial processes) are key to satisfying future gear demand for robotics applications. Soon, we’ll be collecting data via next-generation computing for a large digital database to allow AI modeling of errors in backlash.
For us, AI is also key to supporting predictive maintenance and reducing manufacturing costs. Motion control is evolving to integrate AI learning and predictive models. Electromechanical systems are now more integrated with the IoT. Supporting the robotics industry, carefully documenting the characteristics and unique DNA of next-generation motors and gearmotors will allow for better performance and predictive maintenance.
Can the importance of cloud computing be overstated?
Rangarajan: A significant portion of HP’s 3D printers are connected to the cloud, where data is securely managed to yield valuable insights for end users. The HP 3D center offers a centralized view of fleet activity by providing realtime production data from the cloud.
For customer support, telemetry data is used. HP’s 3D Process Development and Digital Sintering solutions provide end users access to a full suite of process parameter settings for experimenting and developing processes to scale. By leveraging orchestrated workflows and scalable cloud computing, software can run cost effectively, eliminating the need for substantial end-user infrastructure investments.
Additionally, HP recognizes that in today’s factory environment, there’s a need to interface into MES and ERP systems. Our automated application programming facilitates integration so partners and third-party ISVs can tap into new markets by enhancing the value of their products and offering end-to-end solutions. This integration also enables remote job submission and realtime status monitoring. Plus, a secure cloud-based solution with robust API gives users a way to start developing and scaling additive solutions with new software capabilities delivered every few months.
Luchars: PrintStator is a cloud-based CAD/CAM software to print stators for coreless axial-flux electric motors. PrintStator’s SaaS features let any innovator become an electric-motor designer and producer. From the cloud-based interface, PrintStator users can enter precise performance and dimensional specifications to create custom electric motors for consumer electronics, HVAC, e-mobility, medical, robotics, and aerospace applications.
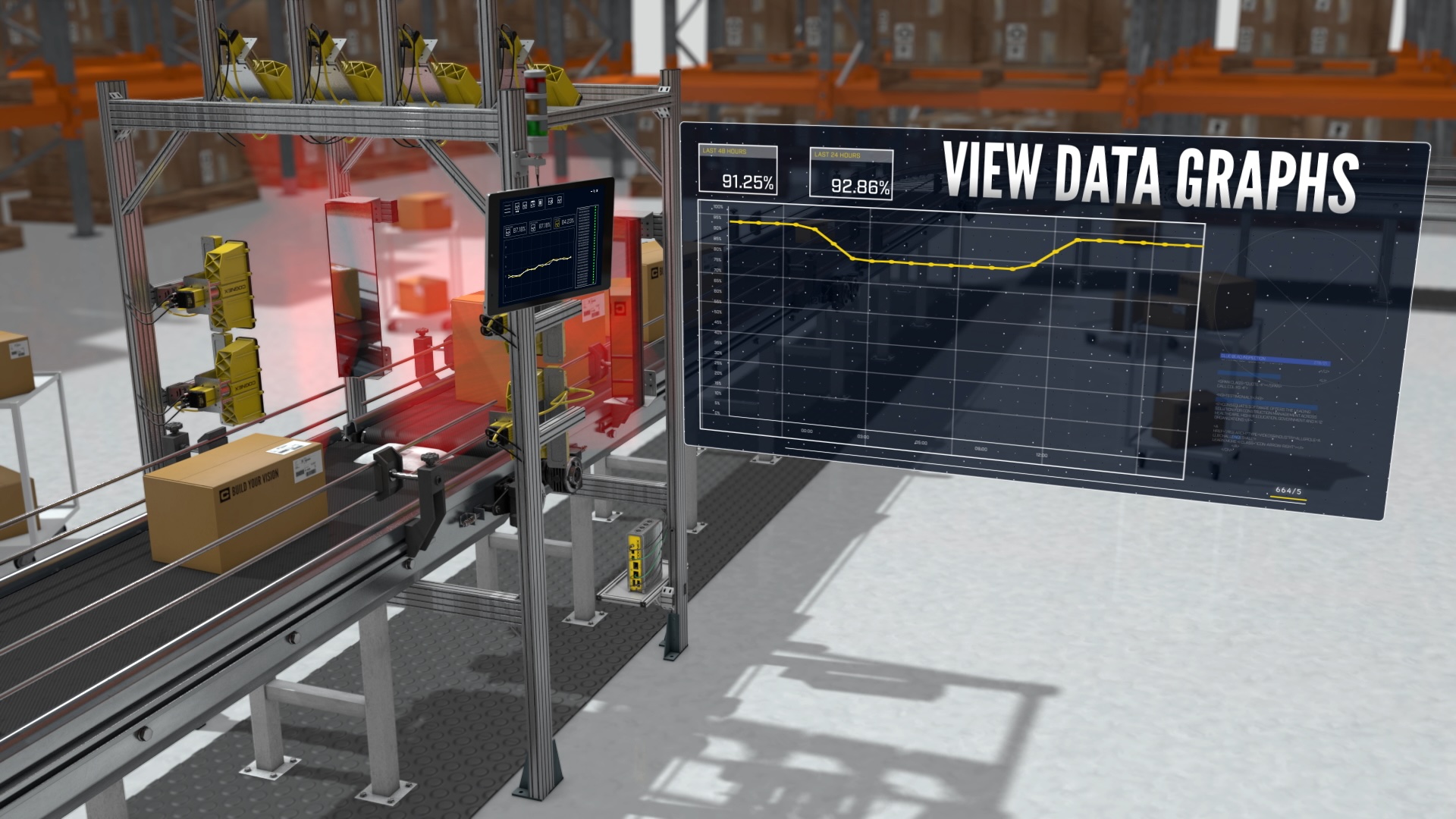
Describe some recent use of digital twins or digitization.
Wierzchowski: By creating a detailed digital replica of our sites, we’ve enhanced our overall asset use, minimized excess inventory, and improved the flexibility of transferring machines across manufacturing sites.
Rangarajan: The next step in the evolution of 3D printing will be the implementation of digital twins — a virtual replica of 3D printers and their operations. Every serial number has its unique live model that represents the machine state. These digital twins are created leveraging physics models of the underlying process as well as telemetry data supported by AI and ML techniques. Digital twins support the creation of continuous, automated, and efficient 3D-printer operations via adjustment and optimization of build and print parameters. This in turn maximizes uptime and reduces variability across machines and within a given build. Digital twins also contribute to efficient and scalable systems for high production.
As more processes along the production lifecycle become automatized, manufacturing capabilities will expand beyond the constraints of labor costs — extending production into night and weekend shifts so costly to manufacturers. With lower total cost of ownership (TCO) for 3D-printing technologies, access can expand to new verticals and prompt a new wave of manufacturing marked by lights-out factories.
Wierzchowski: We initially implemented digital-twin technology at Jabil for the design of complex automated stations. This technology has since advanced to encompass factory-floor design to give us high-performing production lines, streamlined material flow, and reduced manufacturing costs. The comprehensive view of the manufacturing floor provided by digital twins has also facilitated timely maintenance scheduling so crucial for maintaining uninterrupted production.
Kato: Over the past year, AI has been increasingly utilized in optimizing machine and circuit designs, with innovative applications like CADDi Drawer standing out. CADDi Drawer represents a significant advancement in this field by digitizing historical drawings, which includes both design elements and documented quality issues encountered during manufacturing. This comprehensive digital archive enables engineers to learn from past experiences, focusing on innovation rather than reiteration.
The AI in CADDi Drawer goes beyond mere digitization. It analyzes various aspects of the drawings, such as the shapes of parts, to identify similarities in designs. This capability allows for the standardization of parts where feasible, which in turn enhances production efficiency and cost-effectiveness. By standardizing parts based on historical data and design similarities, organizations can streamline their manufacturing processes, reduce costs, and improve overall product quality.
In essence, tools like CADDi Drawer embody a shift in design philosophy, leveraging AI to convert historical data into actionable insights. This approach helps in avoiding repetitive issues, fostering innovation, and cost of production of machine and circuit design.
Munirathinam: As our world becomes increasingly connected, realtime guidance and AI-powered predictions have become essential for Schaeffler and its end users. Functioning as virtual information constructs describing a physical product or system, digital twins create a comprehensive view of Schaeffler products along the entire value chain — from the supplier to the end customer. This holistic view optimizes internal processes and helps Schaeffler offer superior service to machine builders and end users. By providing functional parameters in a machine-readable format, Schaeffler products seamlessly integrate with end users’ production processes, and digital twins even provide relevant data beyond the physical product.
Digital twins come in various formats at Schaeffler and include the Service Twin for simulating product performance in the field; the Design Twin for digital 3D CAD designs and simulation tools; and the Process Twin for simulating factory floor processes and machinery. These insights can be used to optimize a product’s performance over its lifecycle through data provisioning, root-cause analysis, feedback loops, virtual sensors, cloud simulation, analytics, and quality prediction.
What about the special case of additive manufacturing?
Lemire: 3D printing helps us quickly deliver prototypes and functional mockups. The range of 3D-printable materials continues to expand for more product-design and development flexibility.
Rangarajan: Emerging text-to-3D, text-to-CAD, and AI-based landmark-detection and geometry-morphing solutions will help simplify design processes — so even more engineers can bring breakthrough applications to life. These technologies are also helping to optimize and scale production for lower TCO of 3D printing machines. Additionally, emerging generative-AI solutions such as LLM are helping increase production efficiency and speed.
As 3D-printing technology and artificial intelligence continue to grow in lockstep, the additive-manufacturing community will uncover new and exciting ways to help end users develop applications more quickly and easily than ever before in a new era marked by digitized manufacturing.
Umeno: Kollmorgen provides motion control to 3D printing for housing and commercial construction applications in the U.S., Europe, India, and China. Our solutions offer several advantages for the efficient and precise printing of large-scale structures. Kollmorgen AKM servomotors offer high torque density and withstand the demanding loads and difficult environments encountered in construction. Our AKD-series drives maintain accuracy and repeatability (and synchronization of print heads or extruder nozzles) to ensure consistent layer deposition during the printing of structures having exacting dimensional tolerances.
Our motion-control components are built for reliability when subject to the harsh environments of construction sites. Sealed motors and corrosion-resistant materials enhance their longevity in outdoor applications. Plus, our motors and drives enable faster printing speeds; this reduces printing times and increases productivity for construction companies.
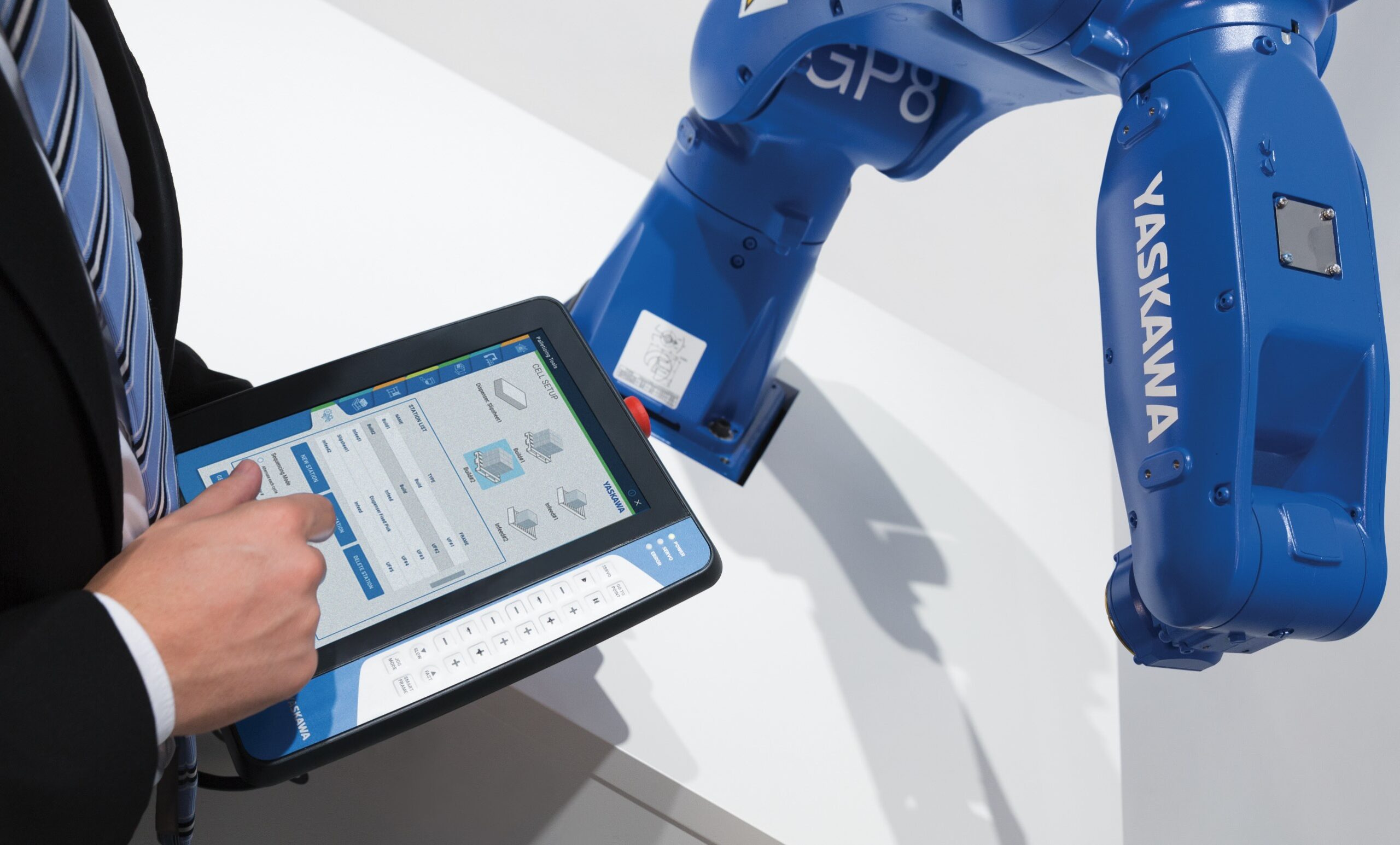
Yaskawa Cockpit collects data from all local devices and stores that data in a local database for access and analysis. The software platform visualizes the status, health, and performance of the connected devices.
Luchars: In January 2024, ECM launched the design-to-manufacture Motor CAD platform PrintStator as a public SaaS offering. Within minutes, the platform turns user specifications into PCB Stator motors. Those PCB design files can then be immediately printed anywhere worldwide. ECM’s PCB Stators replace the bulky copper windings in traditional motors with an ultra-thin disc. The motors are up to 70% lighter than conventional options while requiring just 20% of the raw materials — and maintaining around 95% efficiencies.
Frazelle: Zoo’s KittyCAD Design API and underlying geometry engine leverages GPUs running in the cloud to render models and compute geometric operations. All of Zoo’s APIs are dynamically scaling cloud infrastructure that can handle large amounts of load. Its machine-learning API ML-ephant leverages cloud computing for training models (Text-to-CAD) based on a large set of production CAD-file data. -Zoo’s Text-to-CAD interface is built on our ML-ephant Machine Learning API and has already gained a lot of traction.
Text-to-CAD lets engineers generate models to import into any CAD program. We saw 13,000 CAD files generated by end users the day of this product’s launch and high usage has continued. The model is continually improving to address user feedback and add training data for specific features.
Traditional CAD engines can use GPUs for rendering but not for the mathematical operations. Zoo’s CAD engine leverages a GPU for computing mathematical operations — making it much faster than incumbents. What’s more, Zoo’s modeling app utilizes our KittyCAD Design API and geometry engine; the app is an open-source hardware-design interface that lets engineers generate CAD models, both by editing code and with point-and-click actions. This is a first-of-its-kind user experience for mechanical engineering.
Yudilevich: MaterialsZone’s platform offers an end-to-end materials informatics solution for Lean R&D processes — to streamline these processes for all stakeholders. By leveraging MaterialsZone, organizations can seamlessly integrate comprehensive internal and external insights and a blend of simulated and experimental data through intelligent analysis. This yields materials-innovation breakthroughs much faster than conventional methods.