Transforming the Way Izumi Techno Works with CADDi Drawer
Before
Searching for drawings was time-consuming, and creating estimates took a long time. Verifying drawings while out of the office required a significant amount of time, slowing down communication.
After
Drawings, including similar ones, can now be found immediately, reducing the time required for estimates. Drawings can be easily verified even when out of the office.
Searching for Drawings is Time-Consuming, and Verification Outside the Office is Difficult
Founded in 1966, Izumi Techno is a specialized manufacturer of anodizing, a process that imparts durability to aluminum. With customers in various industries, including precision machinery, semiconductor equipment, automotive, and medical devices, the company has consistently received high acclaim. As a technology-driven company, Izumi Techno has accumulated a track record of achievements, and its independently developed surface treatment and functional anodizing technologies are now recognized as industry-leading. Many manufacturers have designated Izumi Techno as a certified factory, making it an indispensable presence in the anodizing industry.
At Izumi Techno, the sales management department has been responsible for creating estimates. The sales management is divided into external staff, who visit customers directly, and internal staff, who create estimates based on information from the external staff. On average, about 100 estimates are created daily, and a few staff members handle these estimates. When creating estimates, they search for past drawings with similar shapes and refer to the prices at that time. The drawings were digitized and divided into folders. To search for a drawing, they open the folders and look through them, but there are no indications of similar cases when an order is placed. The only way to search is to rely on the staff’s memory or narrow down by drawing name or period and view everything. Searching takes at least 10 minutes, which is highly inefficient.
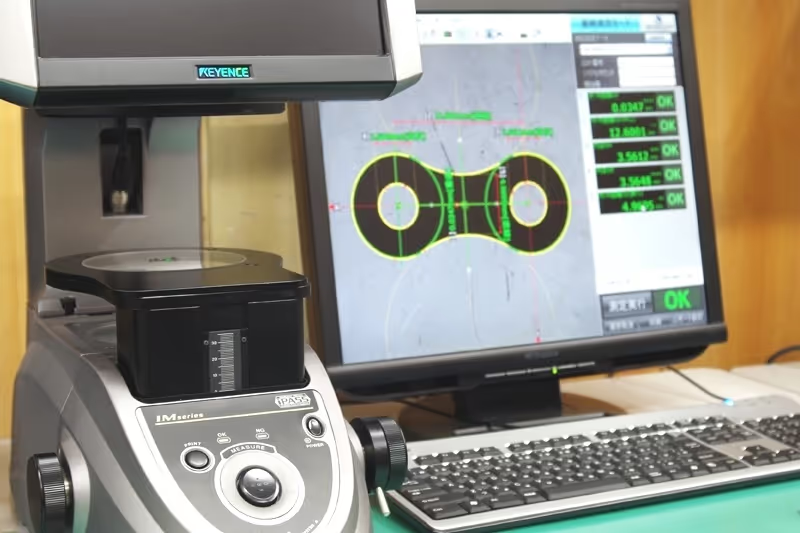
Moreover, when external staff need to confirm drawings during meetings with customers or when they need to contact internal staff to verify detailed information, they must access the drawings from outside the company. Since the drawing data is stored on the company’s internal server, they must access it from outside while ensuring security. In addition to the time required to search for drawings, they also need time to authenticate the company’s internal security before accessing the data, making the process even more inefficient.
Izumi Techno had been using various software to streamline operations. Although they had built their own systems, they faced challenges in drawing management and were always looking for tools to improve the situation.
Intuitive Realization from the Demo! Smooth Implementation and Significant Operational Improvements, Including Reduced Overtime
Izumi Techno has hundreds of customers and handles a vast number of drawings. Introducing a new system that can efficiently handle drawing data was an urgent task for improving operational efficiency, and the company was gathering information from various sources. However, they struggled to find a system that met their expectations. They were almost resigned to the idea that they would have to build everything in-house.
At that time, Koh, the General Manager of the Business Administration Division, saw a demo of the drawing data utilization cloud, CADDi Drawer, at an exhibition he attended. After watching the system in action and receiving an explanation, he intuitively felt that this could solve their challenges.
“I felt that uploading drawings and associated data would be easy. The versatility is also very high. The ability to find similar drawings was extremely helpful.”
“With some systems, when you register a piece of information, you need to perform multiple tasks to link it. With CADDi Drawer, the linking process is very smooth.”
“To be honest, this was the first time I decided to implement a system without much hesitation.”
Koh immediately decided to implement CADDi Drawer and began using it in sales management. He describes the effects after implementation:
“Previously, even just accessing the server where the drawings were stored took 5-10 minutes. Then, searching for the drawings took another 5-10 minutes. Now, we can find them in 1-2 minutes.”
“By finding similar drawings, the time required for creating estimates has decreased. As a result, it has also reduced overtime. Another change is that drawings can be easily viewed outside the office, thanks to the cloud. Although there were some uncertainties at the beginning of the implementation, whenever we had any issues, they were promptly addressed. We can use the system without any stress and smoothly. They also sincerely accept and respond to our requests, which is incredibly helpful.”
By implementing CADDi Drawer, Izumi Techno has transformed the workflow of sales management and achieved significant results.
Refining the Usage of CADDi Drawer and Expanding it to Business Partners
In the future, Izumi Techno plans to improve the efficiency of operations that are still processed in an analog manner and is considering utilizing CADDi Drawer in other departments.
For example, they are exploring whether using it in the manufacturing department can reduce defects.
They can confirm data on past defects, so if they are manufacturing the same or similar item, they can prevent the same defect by checking the data in advance.
This enables them to be cautious and avoid the same defects in new products.
Regarding Izumi Techno’s future prospects, they prioritize refining the usage of CADDi Drawer to align with their internal operations rather than exploring new ways to use it. There are primary and secondary subcontracting positions, and Izumi Techno holds the secondary subcontracting position in relation to the primary subcontractors who perform the processing.
Since they provide niche surface treatments, they have hundreds of customers. They envision that if the companies interacting with Izumi Techno also implement CADDi Drawer, it could lead to even greater efficiency. It may be difficult now, but if realized, the efficiency of exchanging drawing data, which is currently done via email, could be significantly improved.
While utilizing CADDi Drawer and advancing operational efficiency, Izumi Techno aims to continuously improve and enhance its ability to swiftly respond to the diverse needs of each customer, striving to become the “one and only” and “number one” company in the surface treatment field. In the process, the utilization of CADDi Drawer will not only improve their own operations but also expand to their business partners, transforming the way they work.
They aim to achieve not just efficiency but a true digital transformation of their operations.
Ready to see CADDi Drawer in action? Get a personalized demo.
Take this case study on-the-go
.png)