Unlocking Rapid Search Capabilities for Improved Productivity
Before
Engineers and procurement staff want to refer to past drawings when designing and procuring, but searching for drawings based on memory is time-consuming. This inefficiency cuts into the time for core tasks.
After
Similar drawings from the past can be found immediately, significantly reducing work hours. There is anticipation that drawing data can be transformed into an asset and used as a common communication tool.
Searching for Drawings Consumes Time, Reducing Time for Core Tasks
Sugino Machine is an industrial machinery manufacturer that develops, designs, manufactures, and sells equipment and technologies such as ultra-high pressure water jet cutting machines, parts cleaning machines, and small machining centers. Inheriting the founding spirit of “think for ourselves, make for ourselves, and sell and service for ourselves,” the company has been developing technologies for over 80 years, offering six “ultra-technologies” of “cutting, machining, washing, polishing, crushing, and solving.” Sugino Machine has contributed to the development of diverse industries worldwide and has received high acclaim.
At Sugino Machine, there is a high occurrence of custom designs that modify standard products to meet customer requirements. During the design process, designers strive to find and utilize past drawings of parts with the same or similar shapes as much as possible. Creating new drawings not only increases design work hours but also generates additional work in other departments, such as drawing registration and processing method evaluation, leading to increased costs.
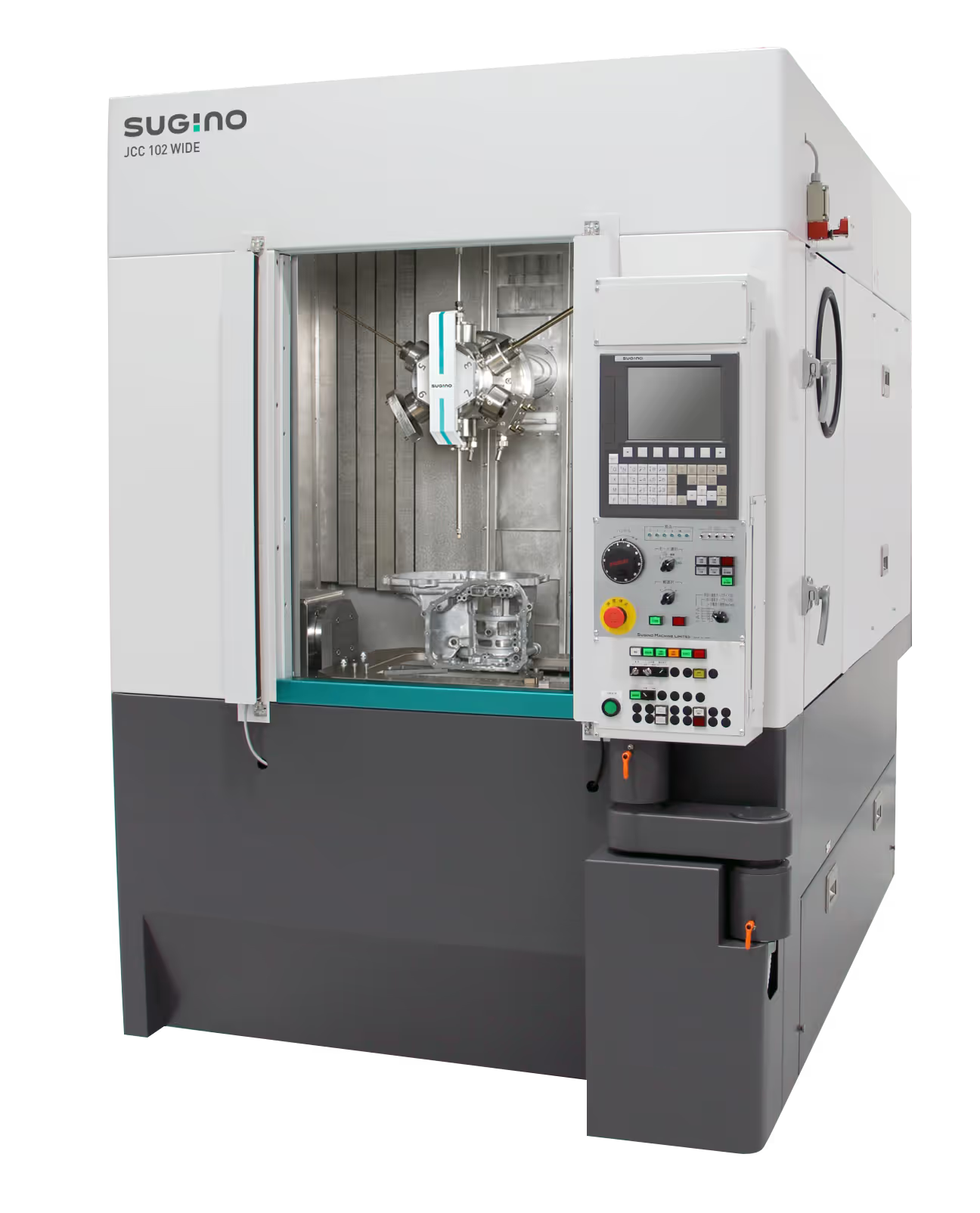
Even for new development projects, designers search for past drawings and use them as is if they find the same parts, or refer to how similar parts were designed. In the procurement department, it is crucial to procure at the optimal quantity, price, and timing, so they search for past drawing data to confirm procurement history and proceed with their work.
However, since drawings are managed in PDF format or on paper, the only way to find them is to rely on each person’s memory or predict based on the part name, which takes a huge amount of time to search for past records.
Although a drawing management system is in place, it is used to manage drawing versions and the relationships between parts depicted in drawings, such as which parts are attached to which drawings. It is difficult to search for parts with similar shapes or search based on the text written in the drawings, making it challenging to find similar drawings from the past. The time that should be spent on core tasks is being consumed by searching for drawings.
Thorough Support from Customer Success Becomes a Decisive Factor in Implementation
Sugino Machine, facing the challenge of “low searchability of drawing data,” learned about the drawing data utilization cloud, CADDi Drawer, while exploring solutions. By implementing CADDi Drawer, it becomes possible to display search results as a list using keywords, part numbers, or images in about 2 seconds. Considering it optimal for improving drawing search speed and reducing work hours, Sugino Machine began considering and decided to implement the system.
Yasu from the Precision Machinery Division describes the implementation process:
“Both the decision to implement and the start of operation were quick. The speedy support from the customer success team was excellent. They frequently visited us, conducted interviews, and provided lectures.”
“They devised various ways to use the system, and whenever we had questions, we received answers promptly.”
“When we made requests for specific features, they were fulfilled in a relatively short period. The most challenging part of starting something new is getting it to take root. This speedy response was a significant factor in our decision to implement the system.”
Within about three weeks of implementation and the start of operation, Sugino Machine completed the registration of tens of thousands of drawings, enabling immediate searching and viewing of similar drawings. The accuracy of drawing searches has also improved by using functions such as multi-condition searches. In some cases, a 50% reduction in work hours has been achieved compared to before implementation.
Tak from the Precision Machinery Division describes the effects and expectations after implementation:
“The most important thing in establishing a system is understanding. To varying degrees, people have a status quo bias, and they will resist if a system, no matter how wonderful, is forced upon them. From now on, I believe visible effects will emerge, whether in work hours or costs. Of course, educational activities are also necessary, but when one department seems to be doing well lately, and it turns out that CADDi Drawer is one of the reasons, it should naturally lead to increased usage.”
“In the procurement department and among designers, there are often cases where designers spend time on non-design tasks without even realizing it. With CADDi Drawer, they may suddenly find that their work is finished earlier than usual, creating time that can be used for other purposes.”
“In this way, we were able to break free from the vicious cycle of ‘it’s faster to draw a new one than to search for a drawing.'”
“I hope this will lead to the development of new technologies or other advancements.”
Transforming Drawings into a Common Communication Tool with CADDi Drawer to Drive Innovation
Sugino Machine is also considering further utilization of CADDi Drawer. First, they plan to expand and establish usage in the initial implementation departments, and eventually consider expanding to other departments. By doing so, they hope to use drawings as a common communication tool and promote information sharing between departments.
“When there are many types of products, the number of design departments also increases. However, we have not quite reached the point of sharing drawings between departments. On the other hand, there is only one procurement department. Drawings come from different departments, and there may actually be something similar. If we can easily search for similar drawings and view past records, we can identify the most cost-effective options. I expect CADDi Drawer to lead to such realizations.”
“We are considering transforming drawings into a common communication tool and connecting them across the organization wich CADDi Drawer.”
“We can now view drawings across the company, and I hope this will trigger innovation.”
Sugino Machine not only improves operational efficiency with CADDi Drawer but also transforms drawing data into an asset to drive change and continue contributing to the development of diverse industries worldwide.
Ready to see CADDi Drawer in action? Get a personalized demo.
Take this case study on-the-go
.png)