Procurement 101: Advanced Planning and Scheduling (APS) – How it works
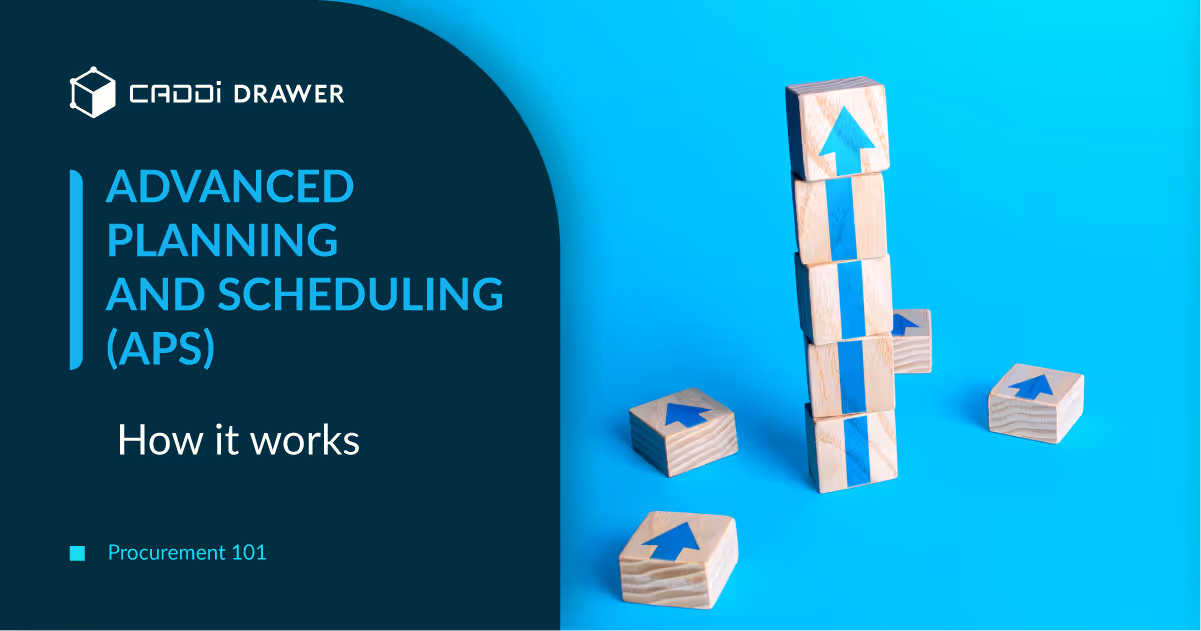
Table of Contents
Facing challenges in aligning your production capabilities with rapidly changing market demands? Advanced Planning and Scheduling (APS) systems are transforming manufacturing efficiency, enabling companies to reduce lead times by 20% and inventory costs by 15%, while improving order fulfillment accuracy by 10%.
Dive into how APS leverages real-time data and advanced algorithms to streamline operations, ensuring procurement managers not only meet but exceed industry benchmarks.
The Essence of APS in Modern Manufacturing
APS solutions are much more than mere scheduling tools; they are the central nervous system of modern manufacturing plants. These systems use sophisticated algorithms to forecast demand, plan production, and manage inventory, offering a panoramic view of the manufacturing process from raw materials to finished products.
Unlike their predecessors, APS systems consider various constraints like machine capacity, workforce availability, and supply chain logistics, ensuring a seamless and efficient production flow.
- Dynamic Planning for Real-Time Efficiency: APS allows for the dynamic adjustment of schedules, taking into account real-time data and changes in demand, supply, and production capacity. This agility is invaluable in today’s fast-paced market, where delays can mean lost opportunities.
- From Gantt Charts to Advanced Algorithms: While traditional planning methods like Gantt charts lay the groundwork, APS systems build upon this by incorporating complex algorithms that consider multiple factors simultaneously. This results in more accurate and efficient production schedules, minimizing bottlenecks and enhancing productivity.
Bridging the Gap: APS and Industry 4.0
The synergy between APS and Industry 4.0 technologies is a match made in manufacturing heaven. As factories become smarter and more interconnected, the role of APS systems becomes increasingly critical. They not only facilitate efficient production planning but also enable the integration of cyber-physical systems, IoT devices, and big data analytics into the manufacturing process. This integration is pivotal for achieving the high levels of automation and efficiency envisioned by Industry 4.0.
- Enhancing Supply Chain Resilience: In the wake of global disruptions like the COVID-19 pandemic, APS systems have proven to be indispensable tools for maintaining and enhancing supply chain resilience. By allowing for rapid reconfiguration of production schedules and resources, manufacturers can respond swiftly to changes in demand and supply chain disruptions.
- Optimization Across the Board: The advanced optimization engines within APS systems enable manufacturers to make informed decisions that balance demand with production capacity, reduce lead times, and minimize costs. This optimization extends beyond the factory floor, impacting the entire supply chain and ultimately contributing to a more sustainable manufacturing ecosystem.
Unlocking Efficiency: How APS Works
APS systems are the unsung heroes behind the curtains of the manufacturing world, transforming raw data into streamlined production schedules. Unlike the traditional methods that often fall short in the dynamic manufacturing environment, APS leverages advanced algorithms and optimization engines. These powerful tools consider a plethora of factors, from resource availability to machine breakdowns, ensuring that production goals are met with maximum efficiency.
- Dynamic Adjustment: APS empowers planners to adjust schedules in real-time, responding promptly to unforeseen changes.
- Optimization: By minimizing bottlenecks and enhancing resource utilization, APS significantly boosts productivity.
The sophistication of APS tools, including those from industry leaders like DELMIA and Siemens, transforms productivity by enabling forward-looking planning and fostering collaboration across departments.
Evolving Trends and Future Directions
The landscape of APS is ever-evolving, with technological advancements steering the way toward more agile and intelligent manufacturing processes. The shift towards cloud-based solutions and integration with ERP systems marks a significant trend, catering to the need for flexibility and scalability in manufacturing operations.
- Cloud Deployment: The transition to the cloud offers a more scalable and flexible approach to APS, accommodating the dynamic nature of manufacturing demands.
- No-touch Transactions: Automating the order placement process minimizes human intervention, streamlining the manufacturing process even further.
The future of APS is bright, with an emphasis on machine learning and automation to further refine scheduling processes, making them more efficient and less reliant on human intervention.
The Strategic Imperative of APS
Implementing APS is not just about upgrading technology; it’s a strategic decision that influences the very core of manufacturing excellence. APS acts as a bridge between operational efficiency and strategic business outcomes, offering:
- Agile Manufacturing: APS enables manufacturers to be more responsive to market changes and customer demands.
- Cost Reduction: By optimizing production schedules, companies can significantly reduce operational costs, including labor and wastage.
- Enhanced Customer Satisfaction: The ability to meet delivery deadlines reliably improves customer trust and loyalty.
In a nutshell, APS is a critical component in the quest for manufacturing excellence, aligning production capabilities with business objectives to navigate the complexities of today’s market demands.
Real-World Impact: Case Studies and Results
Embracing Innovation: A Success Story
Consider the case of a leading automotive manufacturer that turned to APS to streamline their complex production lines. By integrating APS with their existing ERP systems, they achieved a 20% reduction in lead times and a 15% decrease in inventory costs, demonstrating the potent benefits of advanced scheduling and planning.
Manufacturing Resilience: Overcoming Challenges
Another example is a global consumer goods company facing supply chain disruptions. Through APS, they could dynamically adjust production schedules, accommodating sudden changes in demand and supply. This adaptability led to a 10% improvement in order fulfillment accuracy and a significant boost in customer satisfaction levels.
How CADDi Drawer Can Help
CADDi Drawer, a cutting-edge digital platform designed for the manufacturing and procurement sectors, directly addresses the pressing challenges in data management within APS. Its capabilities can provide an innovative solution to many of the hurdles discussed earlier, particularly those related to data inconsistency, fragmentation, and the lack of a centralized system for data sharing and analysis.
Streamline activities in the procurement process
The following features enable you to streamline the time-consuming tasks of data collection and organization in procurement operations.
- Price data and supplier information can be automatically linked to each drawing and can also be exported together.
- By using keyword searches combined with similarity searches, the time spent searching for drawings and data in procurement tasks can be reduced.
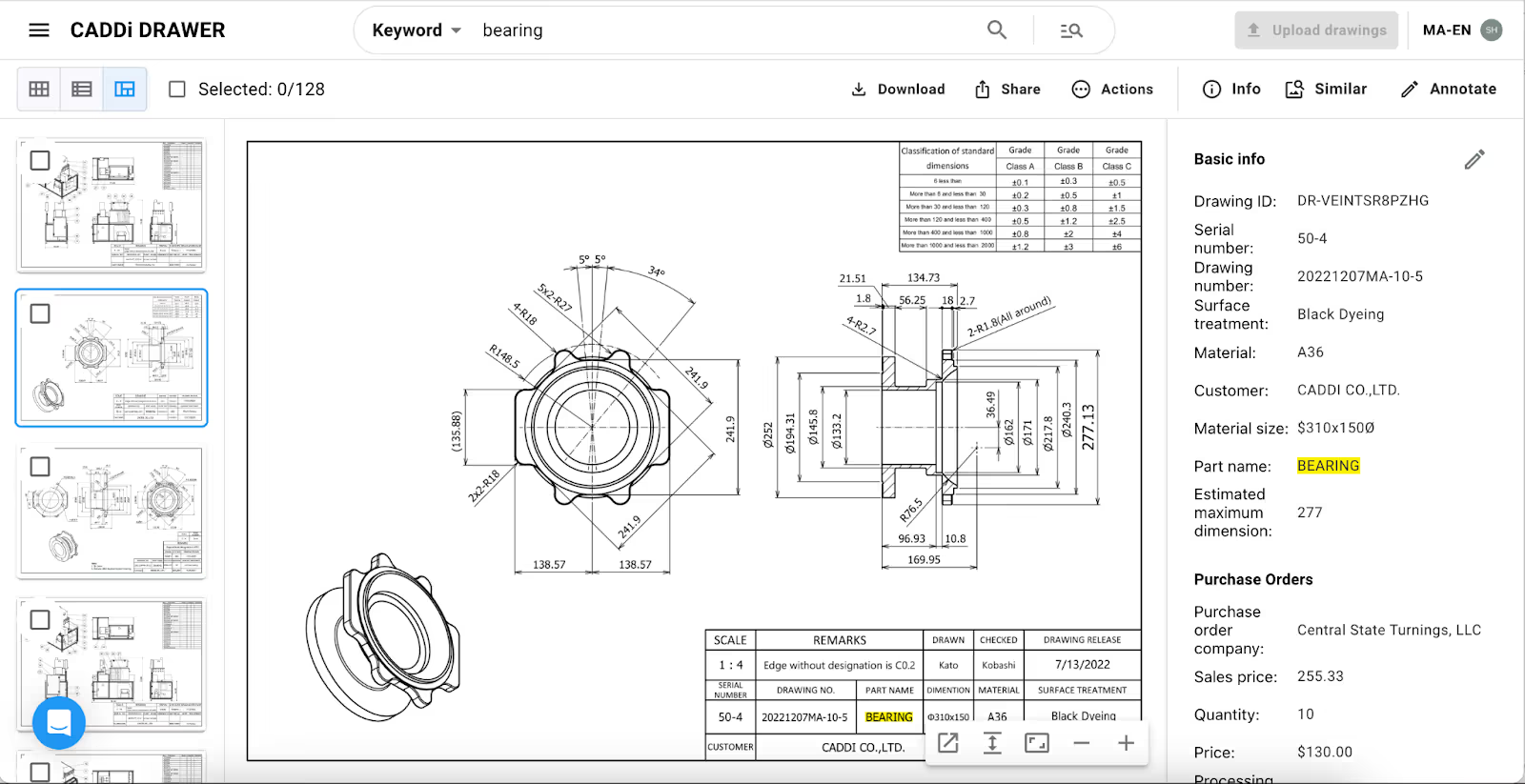
Enhancing Collaboration and Standardization
Collaboration and standardization across the supply chain are crucial for overcoming visibility challenges. CADDi Drawer fosters collaboration by enabling easy sharing and access to data among all supply chain participants. This collaborative environment ensures that everyone is on the same page, enhancing coordination and efficiency. Additionally, the platform supports data standardization, which is vital for integrating data from diverse sources and ensuring that it is comparable and actionable.
CADDi Drawer serves as a System of Insights (SoI), designed to leverage data primarily managed and stored by Systems of Records (SoR), like those represented by ERPs. Utilizing data stored in SoRs and data extracted and structured from drawings by CADDi Drawer, it supports procurement intelligence processes, including analyses and data processing for supplier selection and management, RFQ creation, and quote evaluations.
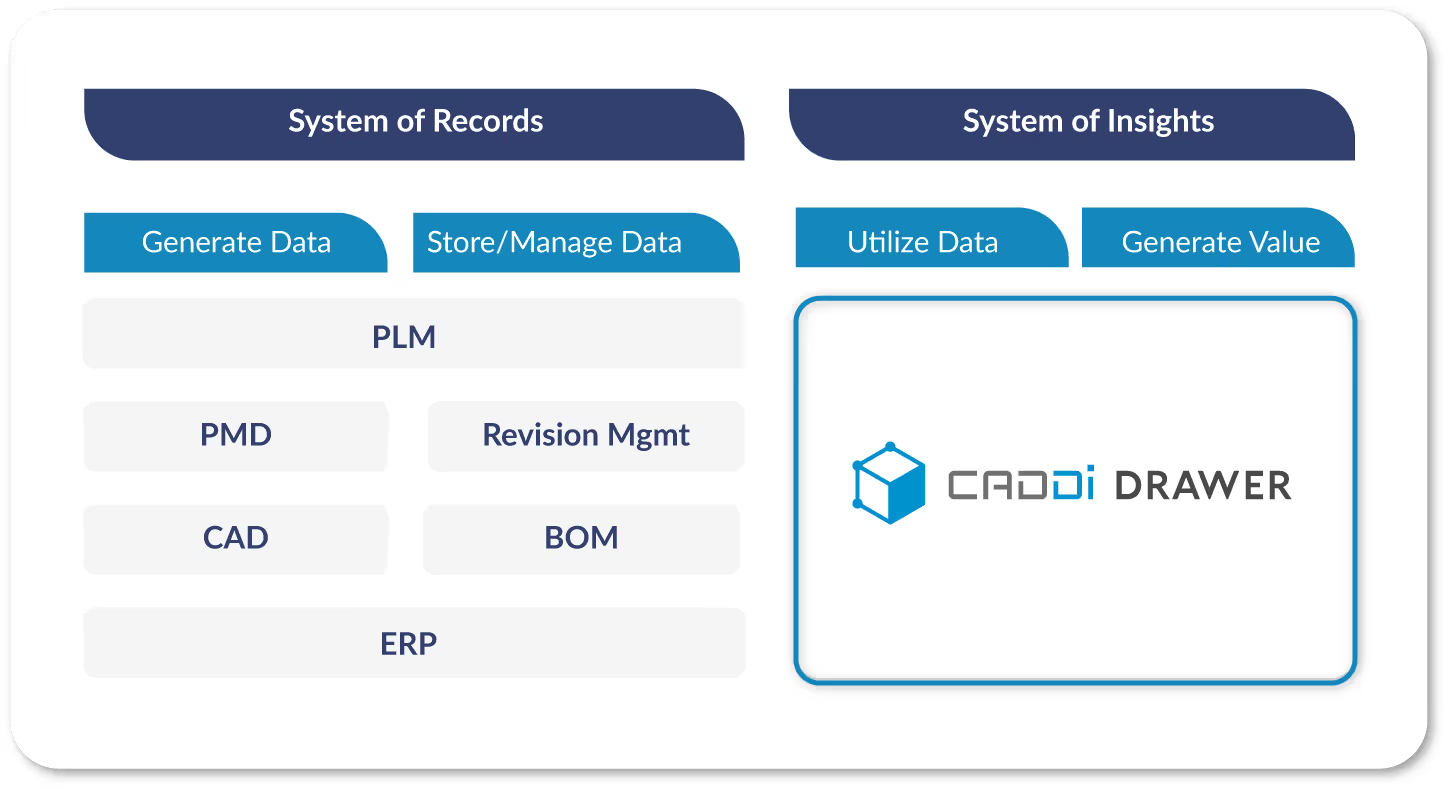
Facing challenges in aligning your production capabilities with rapidly changing market demands? Advanced Planning and Scheduling (APS) systems are transforming manufacturing efficiency, enabling companies to reduce lead times by 20% and inventory costs by 15%, while improving order fulfillment accuracy by 10%.
Dive into how APS leverages real-time data and advanced algorithms to streamline operations, ensuring procurement managers not only meet but exceed industry benchmarks.
The Essence of APS in Modern Manufacturing
APS solutions are much more than mere scheduling tools; they are the central nervous system of modern manufacturing plants. These systems use sophisticated algorithms to forecast demand, plan production, and manage inventory, offering a panoramic view of the manufacturing process from raw materials to finished products.
Unlike their predecessors, APS systems consider various constraints like machine capacity, workforce availability, and supply chain logistics, ensuring a seamless and efficient production flow.
- Dynamic Planning for Real-Time Efficiency: APS allows for the dynamic adjustment of schedules, taking into account real-time data and changes in demand, supply, and production capacity. This agility is invaluable in today’s fast-paced market, where delays can mean lost opportunities.
- From Gantt Charts to Advanced Algorithms: While traditional planning methods like Gantt charts lay the groundwork, APS systems build upon this by incorporating complex algorithms that consider multiple factors simultaneously. This results in more accurate and efficient production schedules, minimizing bottlenecks and enhancing productivity.
Bridging the Gap: APS and Industry 4.0
The synergy between APS and Industry 4.0 technologies is a match made in manufacturing heaven. As factories become smarter and more interconnected, the role of APS systems becomes increasingly critical. They not only facilitate efficient production planning but also enable the integration of cyber-physical systems, IoT devices, and big data analytics into the manufacturing process. This integration is pivotal for achieving the high levels of automation and efficiency envisioned by Industry 4.0.
- Enhancing Supply Chain Resilience: In the wake of global disruptions like the COVID-19 pandemic, APS systems have proven to be indispensable tools for maintaining and enhancing supply chain resilience. By allowing for rapid reconfiguration of production schedules and resources, manufacturers can respond swiftly to changes in demand and supply chain disruptions.
- Optimization Across the Board: The advanced optimization engines within APS systems enable manufacturers to make informed decisions that balance demand with production capacity, reduce lead times, and minimize costs. This optimization extends beyond the factory floor, impacting the entire supply chain and ultimately contributing to a more sustainable manufacturing ecosystem.
Unlocking Efficiency: How APS Works
APS systems are the unsung heroes behind the curtains of the manufacturing world, transforming raw data into streamlined production schedules. Unlike the traditional methods that often fall short in the dynamic manufacturing environment, APS leverages advanced algorithms and optimization engines. These powerful tools consider a plethora of factors, from resource availability to machine breakdowns, ensuring that production goals are met with maximum efficiency.
- Dynamic Adjustment: APS empowers planners to adjust schedules in real-time, responding promptly to unforeseen changes.
- Optimization: By minimizing bottlenecks and enhancing resource utilization, APS significantly boosts productivity.
The sophistication of APS tools, including those from industry leaders like DELMIA and Siemens, transforms productivity by enabling forward-looking planning and fostering collaboration across departments.
Evolving Trends and Future Directions
The landscape of APS is ever-evolving, with technological advancements steering the way toward more agile and intelligent manufacturing processes. The shift towards cloud-based solutions and integration with ERP systems marks a significant trend, catering to the need for flexibility and scalability in manufacturing operations.
- Cloud Deployment: The transition to the cloud offers a more scalable and flexible approach to APS, accommodating the dynamic nature of manufacturing demands.
- No-touch Transactions: Automating the order placement process minimizes human intervention, streamlining the manufacturing process even further.
The future of APS is bright, with an emphasis on machine learning and automation to further refine scheduling processes, making them more efficient and less reliant on human intervention.
The Strategic Imperative of APS
Implementing APS is not just about upgrading technology; it’s a strategic decision that influences the very core of manufacturing excellence. APS acts as a bridge between operational efficiency and strategic business outcomes, offering:
- Agile Manufacturing: APS enables manufacturers to be more responsive to market changes and customer demands.
- Cost Reduction: By optimizing production schedules, companies can significantly reduce operational costs, including labor and wastage.
- Enhanced Customer Satisfaction: The ability to meet delivery deadlines reliably improves customer trust and loyalty.
In a nutshell, APS is a critical component in the quest for manufacturing excellence, aligning production capabilities with business objectives to navigate the complexities of today’s market demands.
Real-World Impact: Case Studies and Results
Embracing Innovation: A Success Story
Consider the case of a leading automotive manufacturer that turned to APS to streamline their complex production lines. By integrating APS with their existing ERP systems, they achieved a 20% reduction in lead times and a 15% decrease in inventory costs, demonstrating the potent benefits of advanced scheduling and planning.
Manufacturing Resilience: Overcoming Challenges
Another example is a global consumer goods company facing supply chain disruptions. Through APS, they could dynamically adjust production schedules, accommodating sudden changes in demand and supply. This adaptability led to a 10% improvement in order fulfillment accuracy and a significant boost in customer satisfaction levels.
How CADDi Drawer Can Help
CADDi Drawer, a cutting-edge digital platform designed for the manufacturing and procurement sectors, directly addresses the pressing challenges in data management within APS. Its capabilities can provide an innovative solution to many of the hurdles discussed earlier, particularly those related to data inconsistency, fragmentation, and the lack of a centralized system for data sharing and analysis.
Streamline activities in the procurement process
The following features enable you to streamline the time-consuming tasks of data collection and organization in procurement operations.
- Price data and supplier information can be automatically linked to each drawing and can also be exported together.
- By using keyword searches combined with similarity searches, the time spent searching for drawings and data in procurement tasks can be reduced.
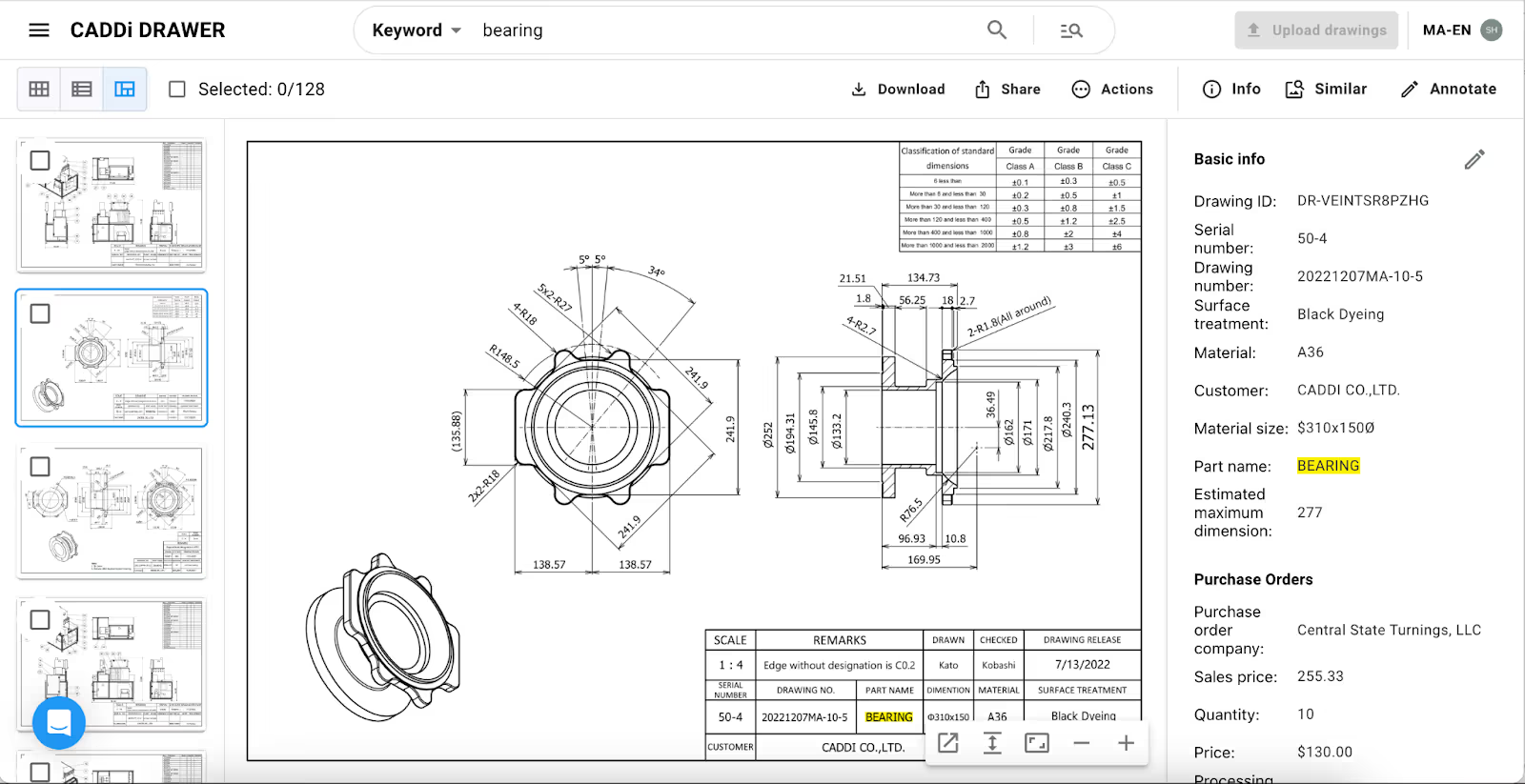
Enhancing Collaboration and Standardization
Collaboration and standardization across the supply chain are crucial for overcoming visibility challenges. CADDi Drawer fosters collaboration by enabling easy sharing and access to data among all supply chain participants. This collaborative environment ensures that everyone is on the same page, enhancing coordination and efficiency. Additionally, the platform supports data standardization, which is vital for integrating data from diverse sources and ensuring that it is comparable and actionable.
CADDi Drawer serves as a System of Insights (SoI), designed to leverage data primarily managed and stored by Systems of Records (SoR), like those represented by ERPs. Utilizing data stored in SoRs and data extracted and structured from drawings by CADDi Drawer, it supports procurement intelligence processes, including analyses and data processing for supplier selection and management, RFQ creation, and quote evaluations.
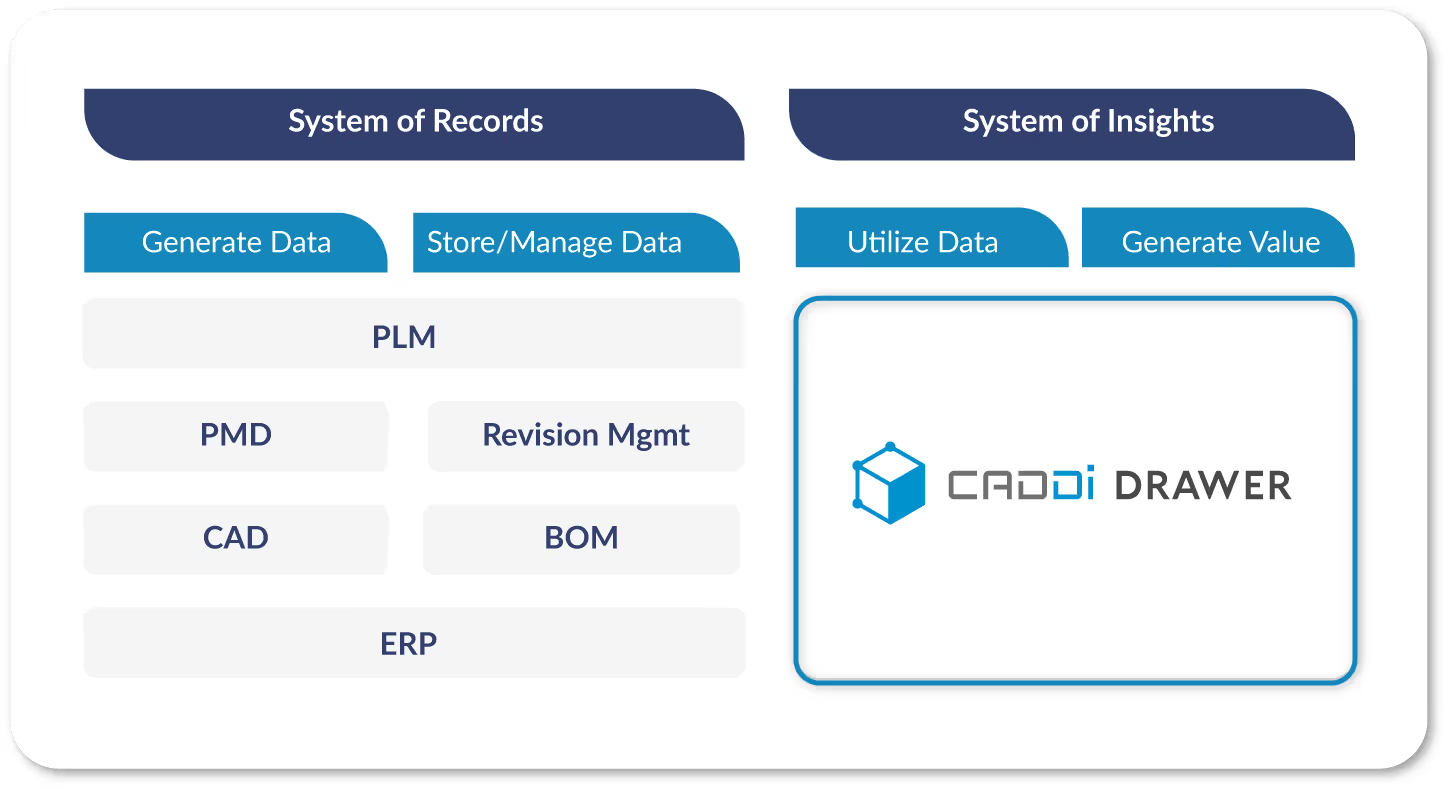
Ready to see CADDi Drawer in action? Get a personalized demo.
Subscribe to our Blog!
Related Resources
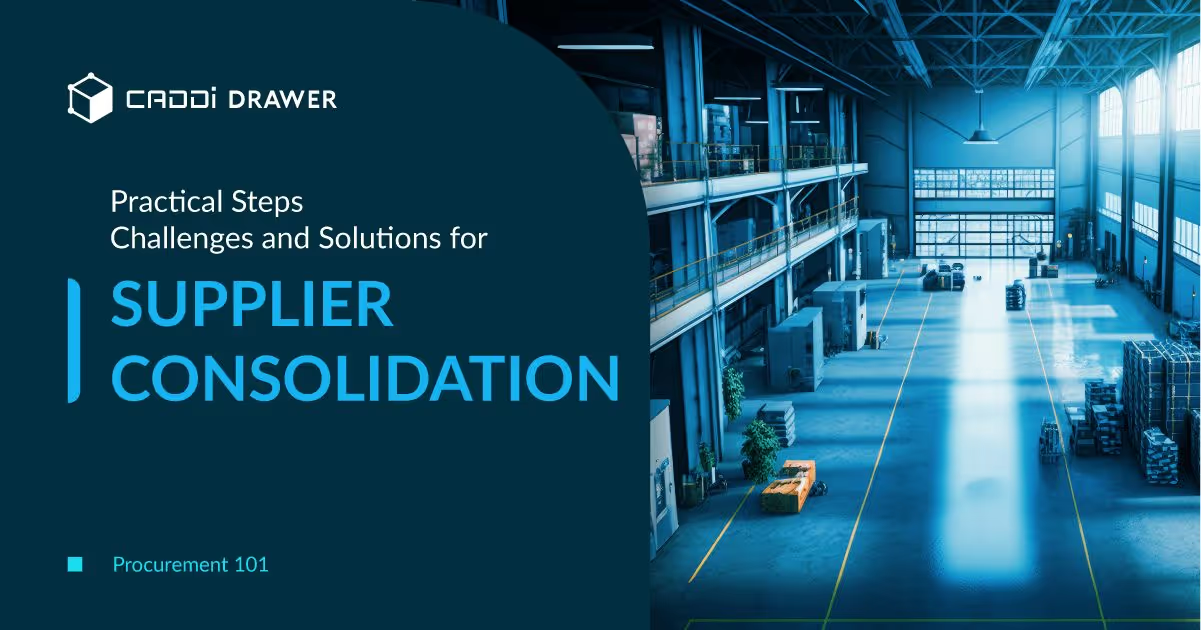
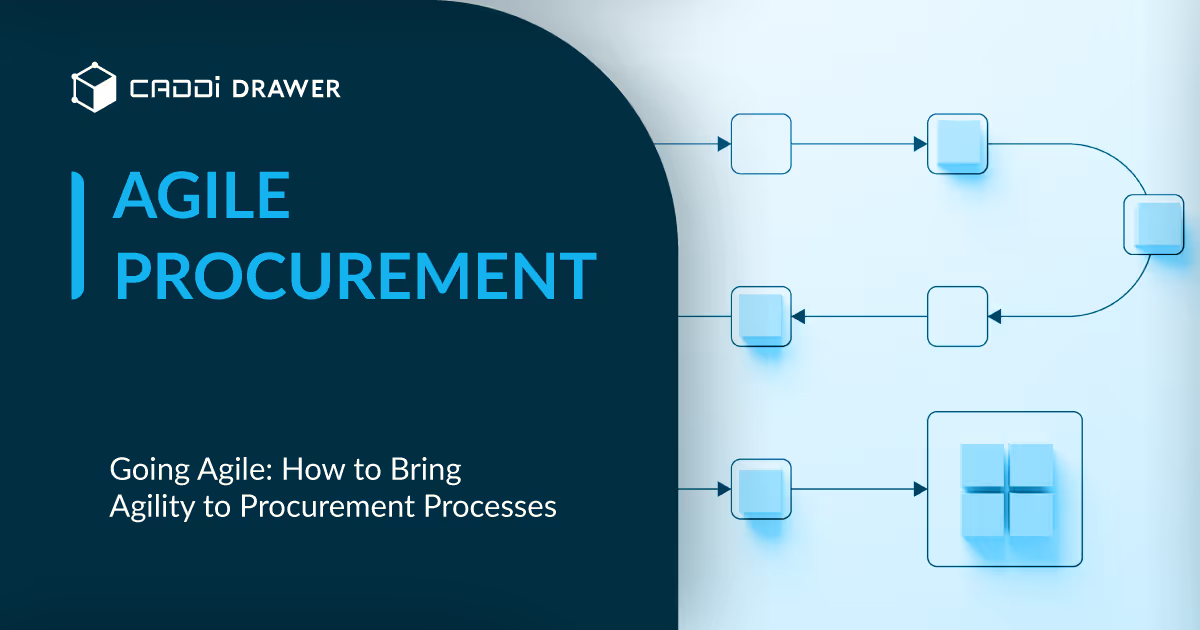
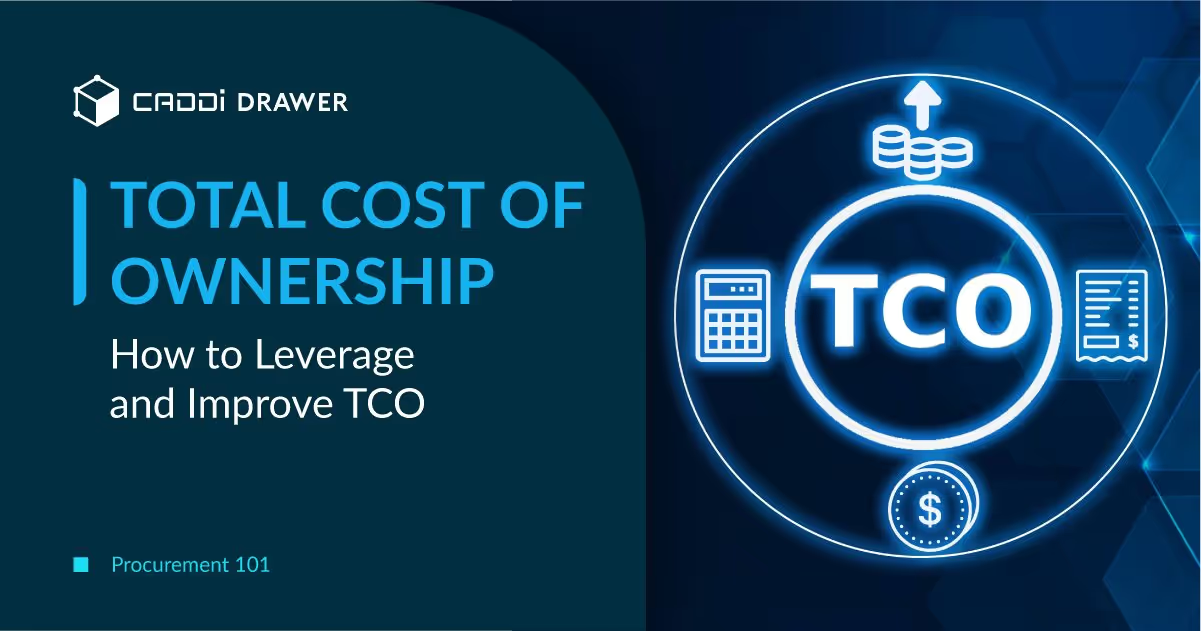
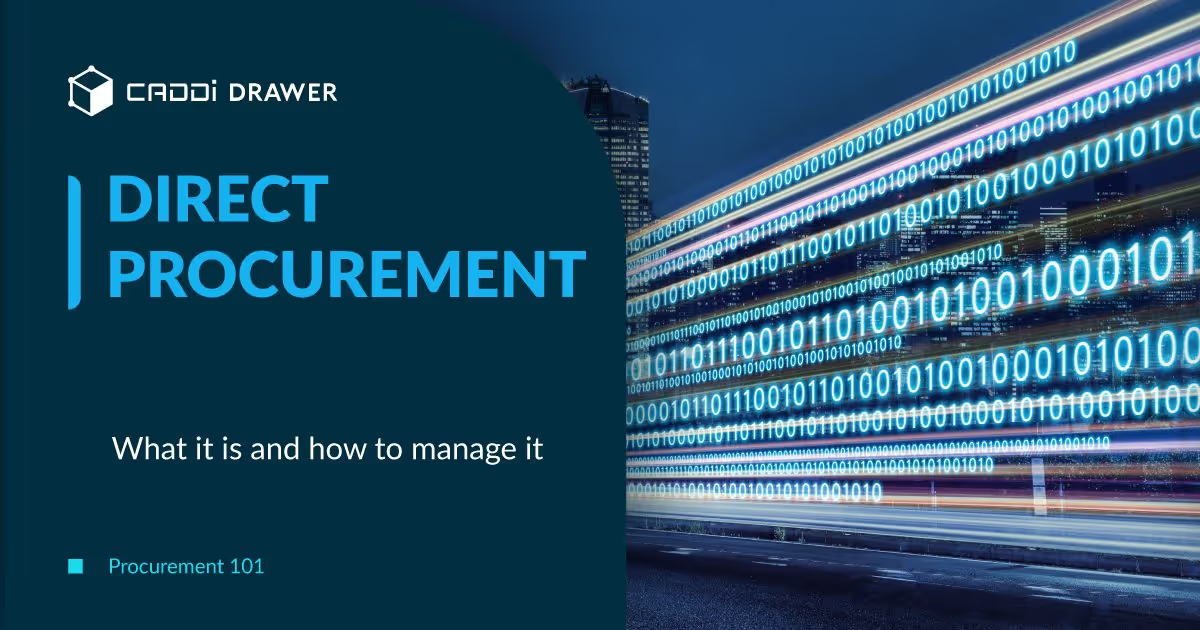

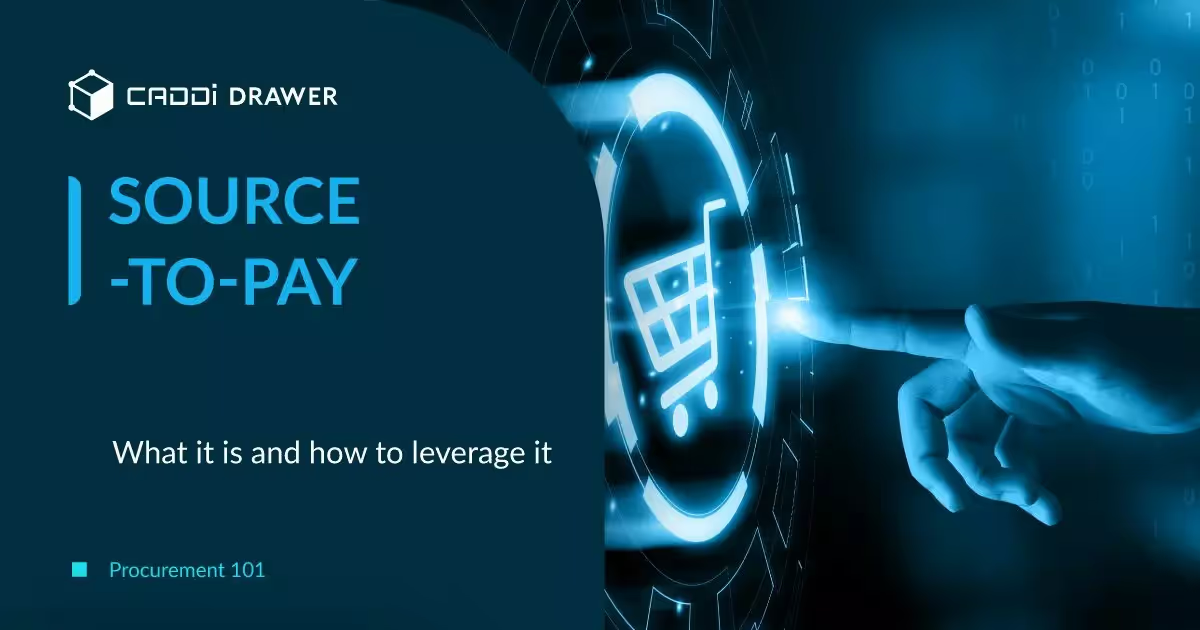