Procurement 101: Total Cost of Ownership (TCO) – How to Leverage and Improve it
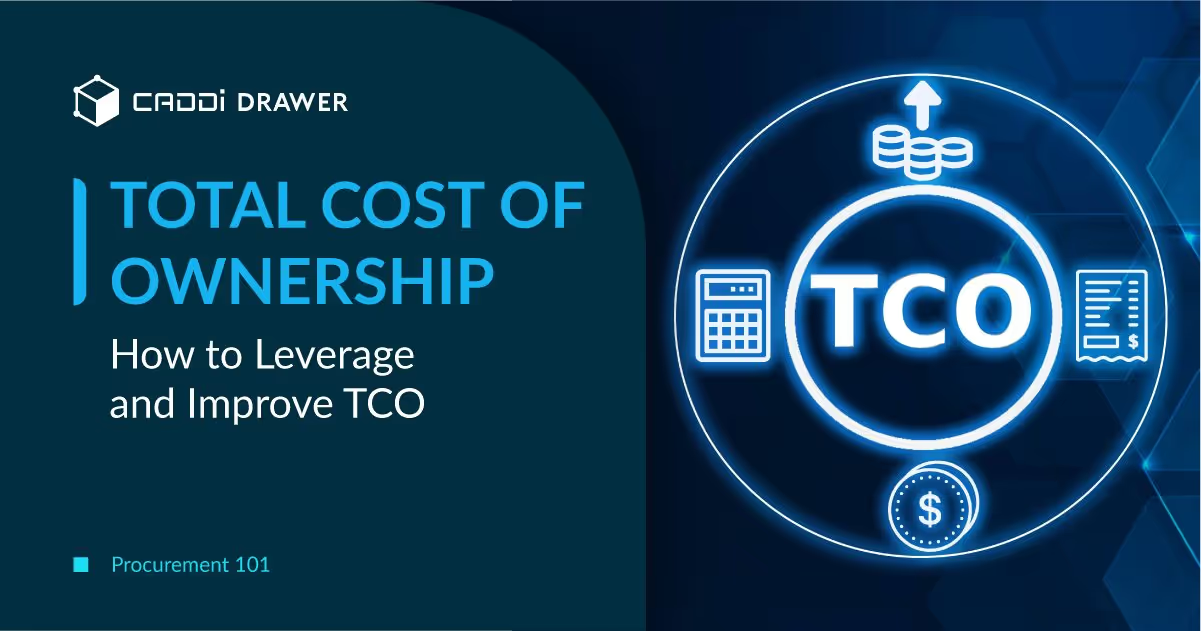
Table of Contents
Total Cost of Ownership (TCO) is often used as an important metric at the time of IT system implementation, but it’s not limited to that; it should always be kept in mind in the context of procurement and supply chain management in the manufacturing industry as well. Below, we will discuss the method of calculating TCO, how to utilize this metric, and what approaches are available for improvement.
Understanding Total Cost of Ownership
TCO encapsulates every penny spent on an asset from acquisition to disposal, including hidden costs that might not be apparent at the outset. This methodology is particularly pivotal in industries where procurement and manufacturing decisions significantly impact the bottom line.
For instance, in the IT sector, where upgrading systems or investing in new technology can have far-reaching financial implications, TCO plays a crucial role. A study by Gartner highlighted the importance of TCO in IT investments, noting that companies often underestimate the long-term costs associated with new technology, including maintenance, support, and downtime.
But TCO’s relevance isn’t confined to IT. In manufacturing, considering TCO extends far beyond the initial price of individual components. It encompasses a wide range of factors that can significantly impact a company’s bottom line, from assembly efficiency, logistics cost, warehousing labor and occupancy costs, and management costs. The traditional view of TCO focuses on direct and indirect costs of procuring a product, but for a comprehensive understanding, one must look at the costs incurred throughout the supply chain. Also, the decision to purchase new equipment involves considering not just the purchase price, but also operational and maintenance expenses over the equipment’s life.
A report by the Manufacturing Institute on the automotive industry illustrated how a deeper understanding of TCO can lead to substantial savings. The report revealed that by focusing on TCO, some manufacturers were able to reduce their total ownership costs by up to 25%, thanks to more informed procurement strategies and a focus on lifecycle costs rather than upfront expenses alone.
How to Calculate TCO
The calculation of TCO might seem daunting, but it boils down to a simple formula: Initial cost + Maintenance cost – Residual value = TCO. This formula serves as a starting point for a deeper analysis, which includes evaluating energy costs, maintenance fees, and other expenses over the asset’s lifespan. It’s a method that demands both precision and foresight, requiring managers to forecast future costs and savings accurately.
Initial Cost
This is the upfront purchase price of the asset, which often represents a fraction of the total cost incurred over its lifespan. Despite being a significant factor, the initial cost is just the tip of the iceberg in the overall financial analysis of an asset.
Maintenance Cost
These are the costs associated with keeping the asset in optimal working condition. Regular maintenance activities can include cleaning, inspecting, lubricating, adjusting, and repairing the asset. This ensures the asset operates efficiently and extends its useful life, but it also represents a significant portion of the TCO. Unexpected breakdowns can lead to additional maintenance costs not initially accounted for.
Residual Value
At the end of its useful life, an asset may still hold some value, which can be recovered through resale or salvage. This value is subtracted from the overall cost to provide a more accurate picture of the net expense related to owning and operating the asset over its lifetime. The residual value is influenced by factors such as the asset’s condition at the end of its use, market demand, and the presence of a secondary market.
Key Factors in TCO Calculation
The devil is in the details, and when it comes to TCO, the details matter—a lot. Key components of TCO analysis include acquisition costs (purchase price and related expenses), operating costs (energy use, routine maintenance), and personnel costs (training, support staff). But TCO doesn’t stop there. It also considers less tangible, though no less critical, factors such as downtime, opportunity cost, and even the cost of disposing of the asset at the end of its useful life.
A compelling case study from the manufacturing sector underscores the impact of these factors. An analysis of two competing high-efficiency industrial pumps showed that while Equipment A had a lower initial cost, Equipment B offered a lower TCO due to its superior energy efficiency and lower maintenance requirements. Over a ten-year period, Equipment B’s total ownership costs were 20% lower than Equipment A’s, illustrating the importance of looking beyond the sticker price.
Through these lenses, the calculation and application of TCO emerge not just as financial tasks, but as strategic imperatives that can shape the future of procurement and manufacturing decisions.
Leveraging TCO in Procurement and Sourcing Activities
The strategic leverage of TCO in procurement and sourcing transcends traditional cost analysis, morphing into a tool for gaining competitive advantage and fostering supplier relationships.
A prime example of this strategy in action is seen within the electronics manufacturing sector. Companies like Intel and Samsung have harnessed TCO evaluations to streamline their supply chains, identifying not just cost savings but also opportunities for enhancing supplier collaboration. By focusing on the TCO, these firms have been able to negotiate better terms with suppliers, ensuring that they receive the best possible value for their investments.
Research conducted by the Supply Chain Management Review indicates that companies employing TCO-based procurement strategies can achieve up to 30% cost savings in their sourcing activities over a three-year period.
Approaches to Improve TCO
Improving Total Cost of Ownership (TCO) requires a multifaceted approach, focusing on reducing costs not just at the point of purchase but throughout the asset’s lifecycle. Here are specific strategies to analyze and improve TCO effectively:
Lifecycle Cost Analysis
Begin with a comprehensive analysis of the asset’s lifecycle costs, including acquisition, operation, maintenance, and disposal costs. This will help identify significant cost drivers and areas where savings can be achieved.
Vendor Negotiation and Selection
Carefully select vendors based on not only the initial purchase price but also their support, warranty, and maintenance offerings. Negotiate terms that favor lower long-term costs, such as extended warranties or inclusive maintenance contracts.
Preventive Maintenance
Implementing a robust preventive maintenance program can significantly reduce unexpected breakdowns and extend the asset’s useful life. Regular maintenance ensures that equipment operates efficiently, thus lowering operating costs.
Energy Efficiency
For assets that consume energy, opting for energy-efficient models can substantially lower operating costs. Although these may have a higher initial cost, the long-term savings on energy bills can improve the TCO.
Training and Usage
Proper training for personnel on the correct use and maintenance of assets can reduce wear and tear, extend the asset’s life, and decrease the likelihood of costly downtime and repairs.
Technology Upgrades and Retrofitting
Investing in technology upgrades or retrofitting older equipment can improve efficiency and productivity, reducing operational costs over time. Analyze the cost-benefit of upgrades versus purchasing new equipment.
Resale Value Maximization
Consider the asset’s potential resale value at the end of its useful life. Maintaining assets in good condition and choosing brands and models with higher resale value can reduce the net cost of ownership.
Total Cost Modeling
Use total cost modeling tools to simulate different scenarios and their impact on TCO. This can help in making informed decisions about asset purchases, maintenance strategies, and retirement plans.
Supplier Partnerships
Develop long-term partnerships with suppliers to secure better pricing, service levels, and access to innovations that can reduce TCO. Suppliers can often provide valuable insights into optimizing the use and maintenance of their products.
Continuous Improvement
Adopt a continuous improvement mindset towards TCO reduction. Regularly review TCO components for new savings opportunities and adjust strategies as necessary to adapt to changing conditions and technologies.
How CADDi Drawer Can Help Analyzing and Improving TCO
CADDi Drawer’s contribution to improving TCO is multifaceted. By providing a centralized platform for managing procurement data and drawing information, it significantly reduces the time and effort required to source materials and negotiate with suppliers. This centralized approach not only streamlines procurement processes but also offers insights into spending patterns, enabling procurement managers to make data-driven decisions that align with their TCO reduction goals.
Assetization of Drawing Data
By leveraging CADDi Drawer, it is possible to automatically extract unstructured data from drawings and digitize and store it as structured data. In this way, information that would otherwise be buried in image files or media as drawings can be treated as an asset that can be utilized across the procurement department.
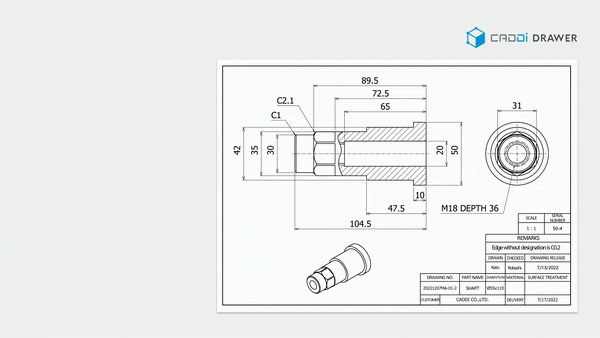
Streamline activities in the procurement process
The following features enable you to streamline the time-consuming tasks of data collection and organization in procurement operations.
- Price data and supplier information can be automatically linked to each drawing and can also be exported together.
- By using keyword searches combined with similarity searches, the time spent searching for drawings and data in procurement tasks can be reduced.
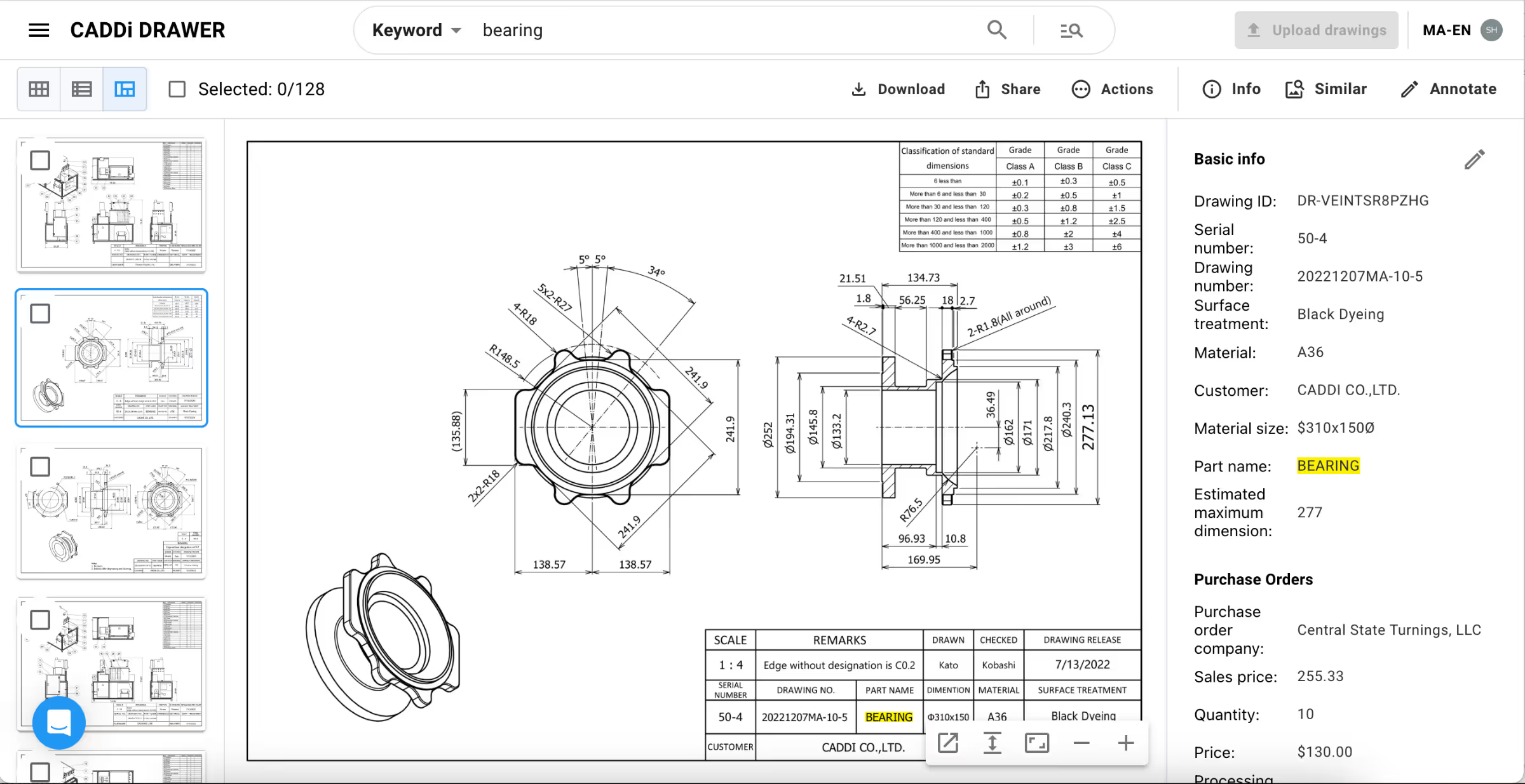
Total Cost of Ownership (TCO) is often used as an important metric at the time of IT system implementation, but it’s not limited to that; it should always be kept in mind in the context of procurement and supply chain management in the manufacturing industry as well. Below, we will discuss the method of calculating TCO, how to utilize this metric, and what approaches are available for improvement.
Understanding Total Cost of Ownership
TCO encapsulates every penny spent on an asset from acquisition to disposal, including hidden costs that might not be apparent at the outset. This methodology is particularly pivotal in industries where procurement and manufacturing decisions significantly impact the bottom line.
For instance, in the IT sector, where upgrading systems or investing in new technology can have far-reaching financial implications, TCO plays a crucial role. A study by Gartner highlighted the importance of TCO in IT investments, noting that companies often underestimate the long-term costs associated with new technology, including maintenance, support, and downtime.
But TCO’s relevance isn’t confined to IT. In manufacturing, considering TCO extends far beyond the initial price of individual components. It encompasses a wide range of factors that can significantly impact a company’s bottom line, from assembly efficiency, logistics cost, warehousing labor and occupancy costs, and management costs. The traditional view of TCO focuses on direct and indirect costs of procuring a product, but for a comprehensive understanding, one must look at the costs incurred throughout the supply chain. Also, the decision to purchase new equipment involves considering not just the purchase price, but also operational and maintenance expenses over the equipment’s life.
A report by the Manufacturing Institute on the automotive industry illustrated how a deeper understanding of TCO can lead to substantial savings. The report revealed that by focusing on TCO, some manufacturers were able to reduce their total ownership costs by up to 25%, thanks to more informed procurement strategies and a focus on lifecycle costs rather than upfront expenses alone.
How to Calculate TCO
The calculation of TCO might seem daunting, but it boils down to a simple formula: Initial cost + Maintenance cost – Residual value = TCO. This formula serves as a starting point for a deeper analysis, which includes evaluating energy costs, maintenance fees, and other expenses over the asset’s lifespan. It’s a method that demands both precision and foresight, requiring managers to forecast future costs and savings accurately.
Initial Cost
This is the upfront purchase price of the asset, which often represents a fraction of the total cost incurred over its lifespan. Despite being a significant factor, the initial cost is just the tip of the iceberg in the overall financial analysis of an asset.
Maintenance Cost
These are the costs associated with keeping the asset in optimal working condition. Regular maintenance activities can include cleaning, inspecting, lubricating, adjusting, and repairing the asset. This ensures the asset operates efficiently and extends its useful life, but it also represents a significant portion of the TCO. Unexpected breakdowns can lead to additional maintenance costs not initially accounted for.
Residual Value
At the end of its useful life, an asset may still hold some value, which can be recovered through resale or salvage. This value is subtracted from the overall cost to provide a more accurate picture of the net expense related to owning and operating the asset over its lifetime. The residual value is influenced by factors such as the asset’s condition at the end of its use, market demand, and the presence of a secondary market.
Key Factors in TCO Calculation
The devil is in the details, and when it comes to TCO, the details matter—a lot. Key components of TCO analysis include acquisition costs (purchase price and related expenses), operating costs (energy use, routine maintenance), and personnel costs (training, support staff). But TCO doesn’t stop there. It also considers less tangible, though no less critical, factors such as downtime, opportunity cost, and even the cost of disposing of the asset at the end of its useful life.
A compelling case study from the manufacturing sector underscores the impact of these factors. An analysis of two competing high-efficiency industrial pumps showed that while Equipment A had a lower initial cost, Equipment B offered a lower TCO due to its superior energy efficiency and lower maintenance requirements. Over a ten-year period, Equipment B’s total ownership costs were 20% lower than Equipment A’s, illustrating the importance of looking beyond the sticker price.
Through these lenses, the calculation and application of TCO emerge not just as financial tasks, but as strategic imperatives that can shape the future of procurement and manufacturing decisions.
Leveraging TCO in Procurement and Sourcing Activities
The strategic leverage of TCO in procurement and sourcing transcends traditional cost analysis, morphing into a tool for gaining competitive advantage and fostering supplier relationships.
A prime example of this strategy in action is seen within the electronics manufacturing sector. Companies like Intel and Samsung have harnessed TCO evaluations to streamline their supply chains, identifying not just cost savings but also opportunities for enhancing supplier collaboration. By focusing on the TCO, these firms have been able to negotiate better terms with suppliers, ensuring that they receive the best possible value for their investments.
Research conducted by the Supply Chain Management Review indicates that companies employing TCO-based procurement strategies can achieve up to 30% cost savings in their sourcing activities over a three-year period.
Approaches to Improve TCO
Improving Total Cost of Ownership (TCO) requires a multifaceted approach, focusing on reducing costs not just at the point of purchase but throughout the asset’s lifecycle. Here are specific strategies to analyze and improve TCO effectively:
Lifecycle Cost Analysis
Begin with a comprehensive analysis of the asset’s lifecycle costs, including acquisition, operation, maintenance, and disposal costs. This will help identify significant cost drivers and areas where savings can be achieved.
Vendor Negotiation and Selection
Carefully select vendors based on not only the initial purchase price but also their support, warranty, and maintenance offerings. Negotiate terms that favor lower long-term costs, such as extended warranties or inclusive maintenance contracts.
Preventive Maintenance
Implementing a robust preventive maintenance program can significantly reduce unexpected breakdowns and extend the asset’s useful life. Regular maintenance ensures that equipment operates efficiently, thus lowering operating costs.
Energy Efficiency
For assets that consume energy, opting for energy-efficient models can substantially lower operating costs. Although these may have a higher initial cost, the long-term savings on energy bills can improve the TCO.
Training and Usage
Proper training for personnel on the correct use and maintenance of assets can reduce wear and tear, extend the asset’s life, and decrease the likelihood of costly downtime and repairs.
Technology Upgrades and Retrofitting
Investing in technology upgrades or retrofitting older equipment can improve efficiency and productivity, reducing operational costs over time. Analyze the cost-benefit of upgrades versus purchasing new equipment.
Resale Value Maximization
Consider the asset’s potential resale value at the end of its useful life. Maintaining assets in good condition and choosing brands and models with higher resale value can reduce the net cost of ownership.
Total Cost Modeling
Use total cost modeling tools to simulate different scenarios and their impact on TCO. This can help in making informed decisions about asset purchases, maintenance strategies, and retirement plans.
Supplier Partnerships
Develop long-term partnerships with suppliers to secure better pricing, service levels, and access to innovations that can reduce TCO. Suppliers can often provide valuable insights into optimizing the use and maintenance of their products.
Continuous Improvement
Adopt a continuous improvement mindset towards TCO reduction. Regularly review TCO components for new savings opportunities and adjust strategies as necessary to adapt to changing conditions and technologies.
How CADDi Drawer Can Help Analyzing and Improving TCO
CADDi Drawer’s contribution to improving TCO is multifaceted. By providing a centralized platform for managing procurement data and drawing information, it significantly reduces the time and effort required to source materials and negotiate with suppliers. This centralized approach not only streamlines procurement processes but also offers insights into spending patterns, enabling procurement managers to make data-driven decisions that align with their TCO reduction goals.
Assetization of Drawing Data
By leveraging CADDi Drawer, it is possible to automatically extract unstructured data from drawings and digitize and store it as structured data. In this way, information that would otherwise be buried in image files or media as drawings can be treated as an asset that can be utilized across the procurement department.
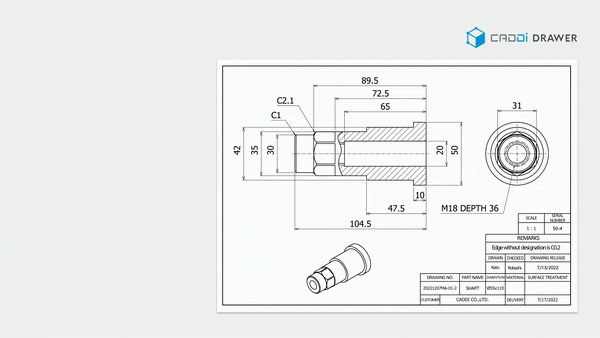
Streamline activities in the procurement process
The following features enable you to streamline the time-consuming tasks of data collection and organization in procurement operations.
- Price data and supplier information can be automatically linked to each drawing and can also be exported together.
- By using keyword searches combined with similarity searches, the time spent searching for drawings and data in procurement tasks can be reduced.
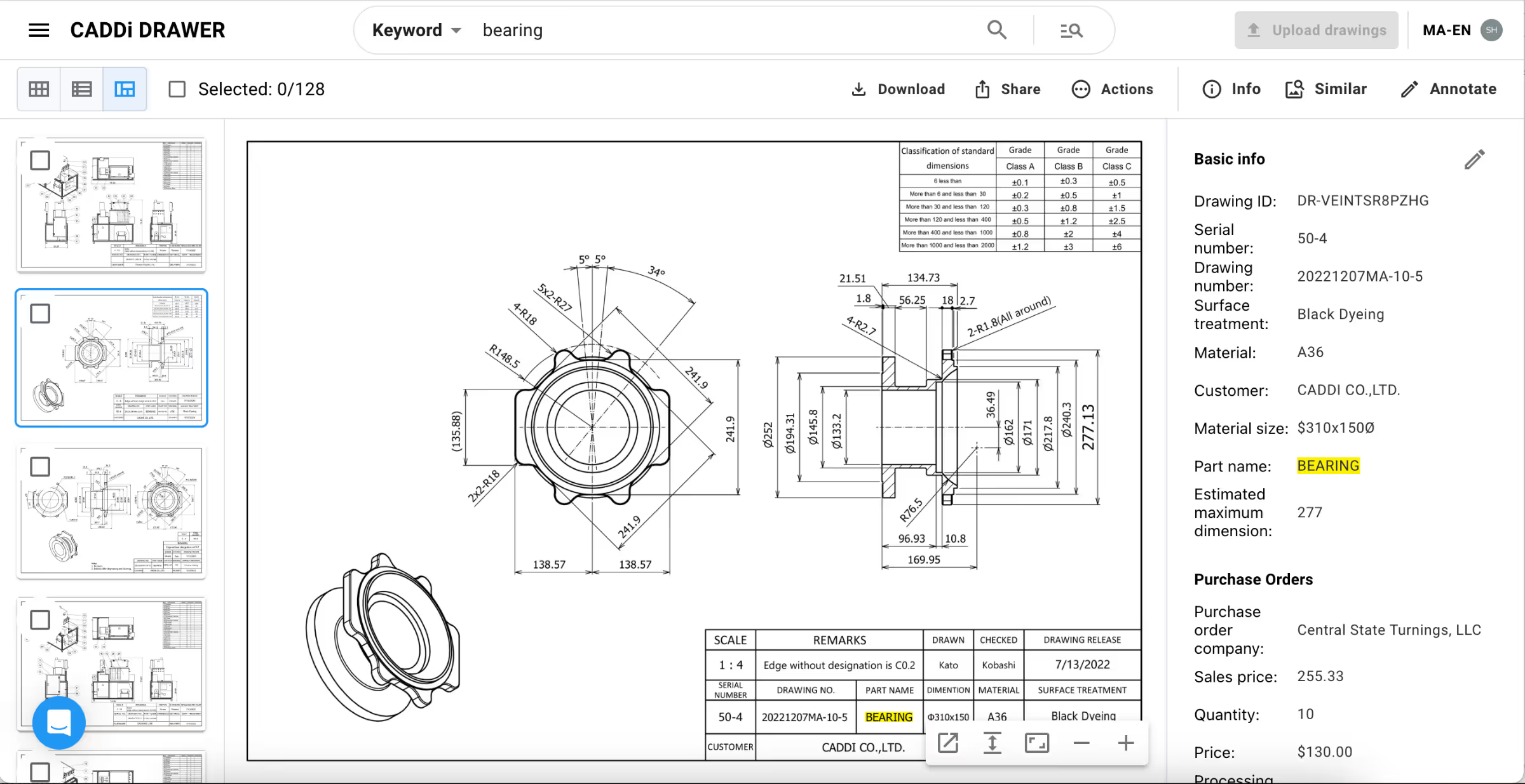
Ready to see CADDi Drawer in action? Get a personalized demo.
Subscribe to our Blog!
Related Resources
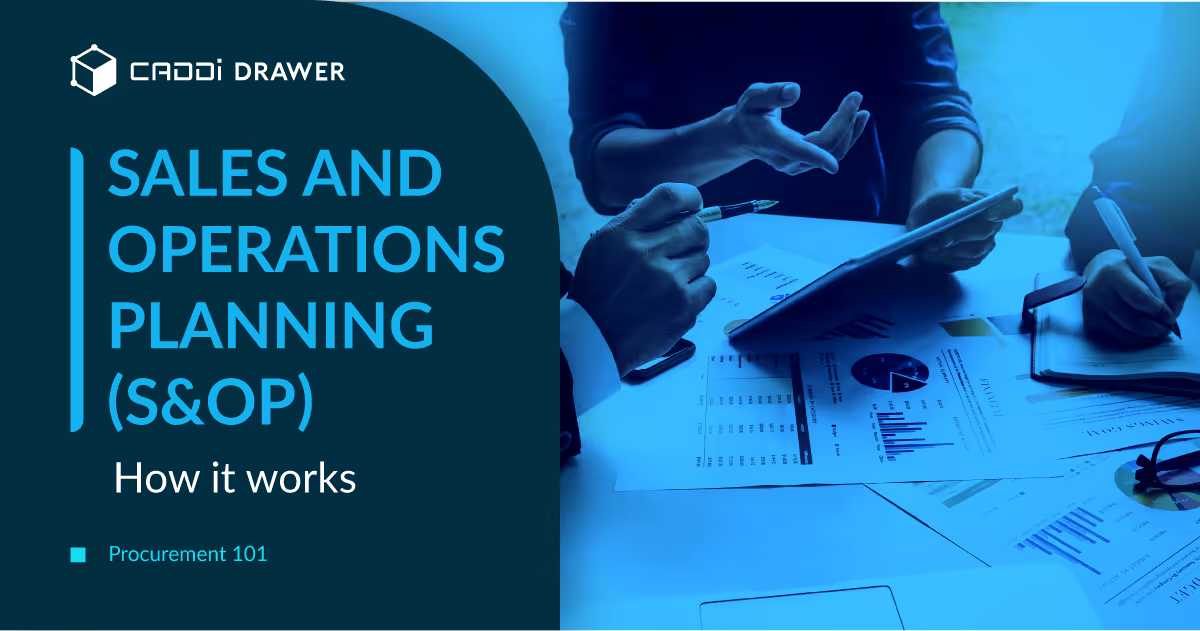
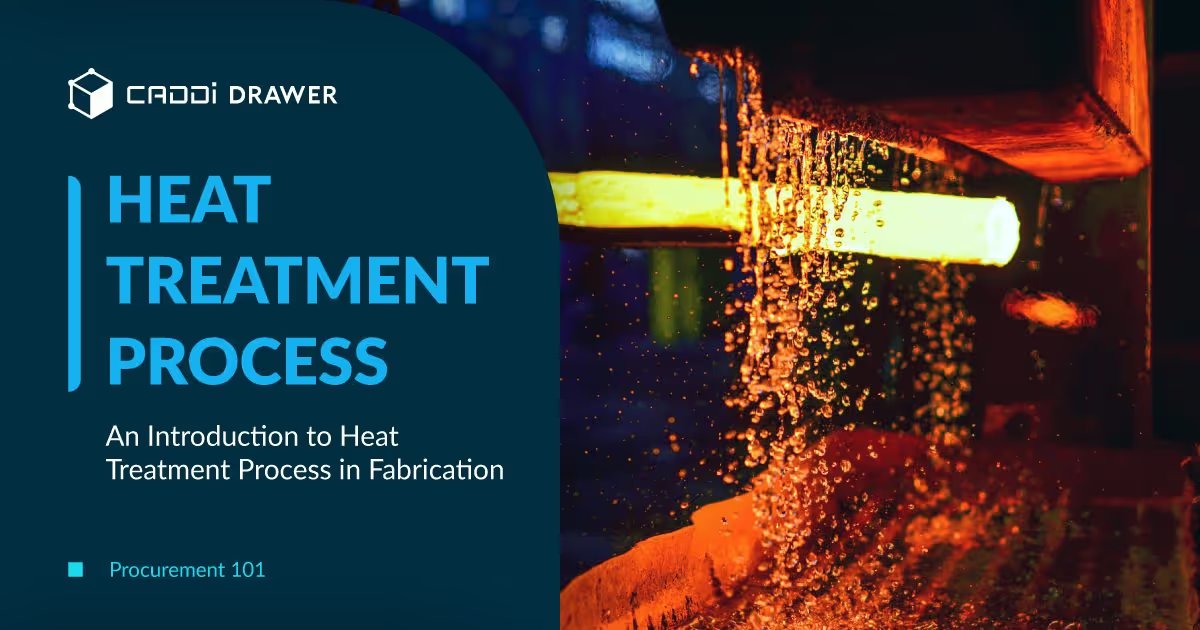

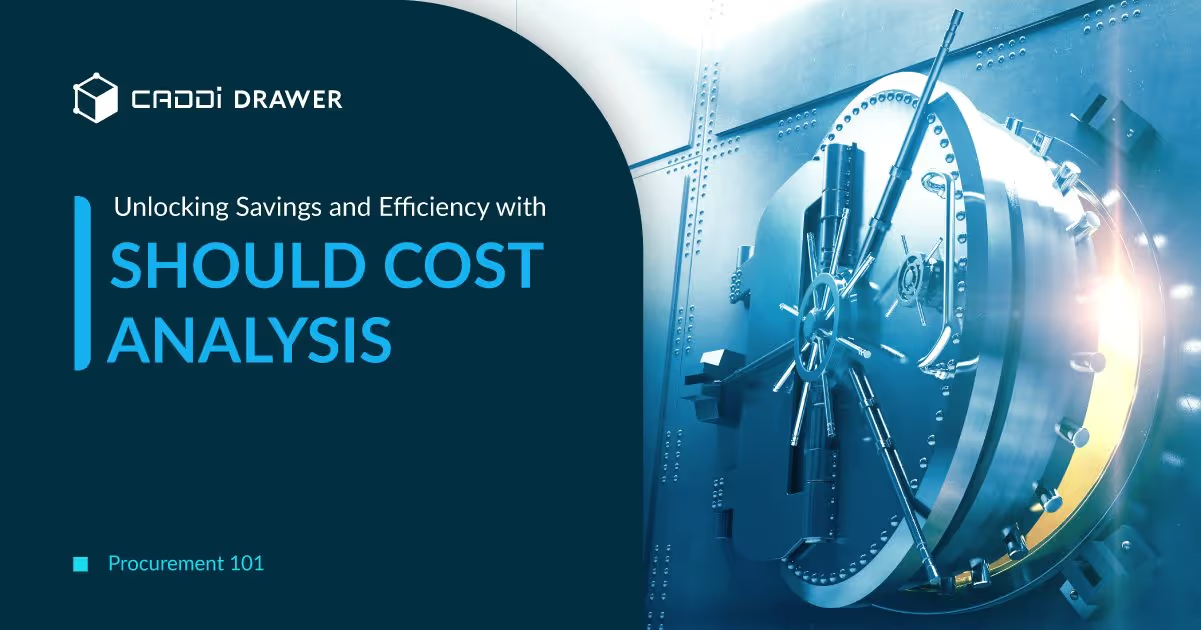
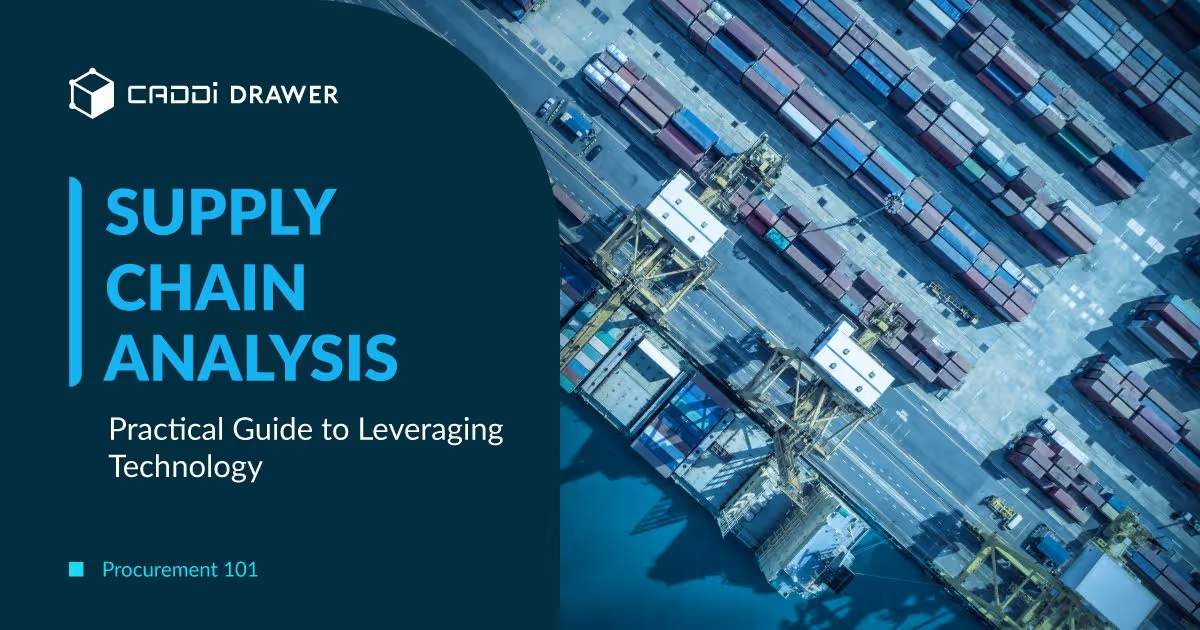
