Cloud PLM Software 2024 – Comparison and the future
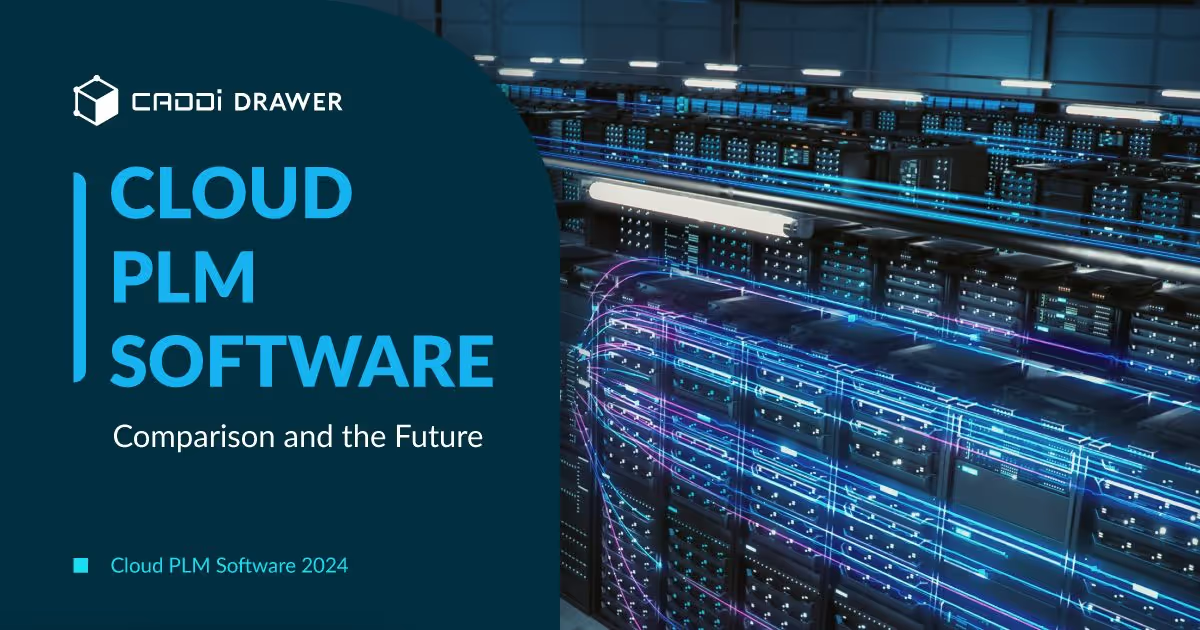
Table of Contents
In the article “Procurement 101: Common Failures in Cloud PLM Implementation and How to Avoid Them,” we discussed how to lead cloud PLM implementations to success. Following that, this article presents a list of the major cloud PLM systems and their features as of 2024. It is our hope that this will serve as a useful reference for vendor selection.
Major Cloud PLM Systems List
1. Autodesk Fusion Lifecycle
Core Features: Offers comprehensive project management tools, robust product data management functionalities, quality management systems, and enhanced collaboration tools. It’s designed to streamline product development processes from concept to retirement, ensuring that all stakeholders have access to the latest information.
- Company Size: Medium to large enterprises
- Industry: Manufacturing, engineering, and design
Pros: Features an intuitive interface that simplifies the complexities of PLM. Strong integration capabilities with other Autodesk products enhance workflow continuity. Its robust data management functionalities ensure that product data is accurate, accessible, and secure.
Cons: The platform can be costly for small businesses, making it a significant investment. Additionally, the wide range of features and functionalities may present a steep learning curve for new users unfamiliar with PLM systems.
2. PTC Windchill
Core Features: This platform excels in Bill of Materials (BOM) management, document control, change management, and quality management. It’s designed to facilitate seamless product development and lifecycle management for businesses of all sizes.
- Company Size: Large organizations
- Industry: Aerospace, automotive, electronics, and industrial machinery
Pros: PTC Windchill is renowned for its comprehensive PLM tools and exceptional integration with CAD systems. The platform is highly scalable, making it ideal for large organizations looking to manage complex product life cycles efficiently.
Cons: New users may find the setup process complex and time-consuming. The user interface, while functional, could benefit from enhancements to improve navigation and user experience.
3. Siemens Teamcenter
Core Features: Teamcenter provides robust BOM management, document management, workflow management, and product configuration tools. It’s built to accommodate the needs of enterprises requiring high levels of customization and integration.
- Company Size: Large enterprises
- Industry: Automotive, aerospace, defense, and electronics
Pros: The platform is highly customizable and scalable, with a strong global support and service network. It offers extensive integration capabilities, making it a versatile choice for companies with complex product development needs.
Cons: The cost can be prohibitive for smaller businesses, and the feature complexity requires comprehensive training for users to fully leverage the system’s capabilities.
4. Arena Solutions
Core Features: Arena Solutions specializes in BOM management, change management, quality management systems, and supply chain collaboration. It’s aimed at companies managing complex electronic designs and requiring tight integration across departments.
- Company Size: Small to medium-sized businesses (SMBs), suitable for startups
- Industry: High-tech, electronics, medical devices, and consumer goods
Pros: The software is user-friendly and provides excellent support for managing complex electronic designs. It also offers solid customer support, ensuring that users can effectively utilize its features.
Cons: Some users may find integration with external systems challenging, and the platform’s customization options are somewhat limited compared to other PLM systems.
5. SAP PLM
Core Features: SAP PLM encompasses portfolio and project management, product development, compliance management, and enterprise asset management. It’s designed to support end-to-end business processes within the SAP ecosystem.
- Company Size: Large enterprises
- Industry: All industries, particularly those already using SAP ERP
Pros: The system is well-integrated within the SAP ecosystem, offering robust functionality and supporting comprehensive business processes. It’s ideal for businesses looking for a holistic approach to PLM.
Cons: The platform’s complexity can be daunting for smaller teams, and the overall cost of implementation and operation may be high.
6. Dassault Systèmes ENOVIA
Core Features: ENOVIA stands out with its 3D design and simulation capabilities, BOM management, change management, and real-time collaboration tools. It supports the development of complex products and fosters sustainable innovation.
- Company Size: Medium to large enterprises
- Industry: Aerospace, defense, automotive, and industrial equipment
Pros: The platform offers strong analytics capabilities and is particularly suited for industries dealing with complex products. Its focus on sustainable innovation is also a key differentiator.
Cons: Significant training may be required to fully utilize the platform, and integrating with non-Dassault systems can present challenges.
7. Infor PLM
Core Features: Infor PLM offers product design, development, and launch management tools, alongside supplier relationship management and quality management features. It’s tailored for industry-specific needs and integrates well with Infor’s ERP systems.
- Company Size: Medium to large enterprises
- Industry: Fashion, food and beverage, and industrial manufacturing
Pros: The platform’s industry-specific solutions and flexible architecture make it a strong choice for businesses looking for a tailored PLM experience. It also boasts good integration capabilities with Infor’s ERP systems.
Cons: Some users may find the platform’s customization options complex, and the user interface less intuitive than competitors.
8. Aras Innovator
Core Features: Aras Innovator provides BOM management, quality planning, product engineering, and project management tools. It’s designed for businesses requiring a high degree of customization and flexibility in their PLM system.
- Company Size: Medium to large organizations
- Industry: Aerospace and defense, automotive, and industrial manufacturing
Pros: The platform is highly flexible and customizable, offering a subscription model that includes all updates and upgrades. Its strong community support is a valuable resource for users.
Cons: The system can be resource-intensive to maintain, and the customization process may require a steep learning curve.
9. Propel
Core Features: Propel offers product information management, quality management, and customer feedback integration. It’s designed for high-tech and consumer goods industries, emphasizing ease of use and integration with customer feedback to inform product development.
- Company Size: Small to medium-sized businesses
- Industry: High-tech, consumer goods, and medical devices
Pros: Propel is distinguished by its user-friendly interface and exceptional integration with Salesforce, making it an ideal choice for businesses already using Salesforce platforms. It excels in industries like high-tech and consumer goods by facilitating rapid innovation and product iteration based on customer feedback.
Cons: While Propel is highly effective for managing standard product lifecycle processes, companies dealing with more complex manufacturing processes or those requiring in-depth technical functionalities might find it lacking in some advanced features found in more specialized PLM systems.
10. Oracle Agile PLM
Core Features: Oracle Agile PLM provides a comprehensive suite of tools for product collaboration, quality management, portfolio management, and product governance. It’s built to secure and manage product information throughout the entire lifecycle, from concept to retirement.
- Company Size: Medium to large enterprises
- Industry: High-tech, industrial manufacturing, and life sciences
Pros: One of the main advantages of Oracle Agile PLM is its strong data security features, ensuring that sensitive product information is kept secure. It also offers a comprehensive suite of features for managing all aspects of product lifecycle management and integrates well with other Oracle products, making it a good choice for businesses already invested in the Oracle ecosystem.
Cons: The user interface of Oracle Agile PLM can feel somewhat outdated compared to more modern systems, potentially impacting user adoption and productivity. Additionally, the system may require significant customization to meet specific business needs, which can increase the time and cost of implementation.
11. Upchain
Core Features: Upchain specializes in BOM management, document management, workflow management, and CAD integration. It’s designed to be accessible and user-friendly, catering particularly to small and medium-sized businesses that need a straightforward PLM solution without the complexity of larger systems.
- Company Size: Small to medium-sized businesses
- Industry: Manufacturing, engineering, and design
Pros: Upchain’s ease of use is a major benefit, allowing teams to get up and running quickly with minimal training. It’s also praised for its flexible pricing model, which makes PLM technology accessible to smaller businesses that might be priced out of other solutions. Additionally, its CAD integration capabilities facilitate seamless design and engineering processes.
Cons: While Upchain is a strong contender for small to medium-sized businesses, larger organizations or those with more complex PLM requirements might find its featureset limited. The platform may lack some of the advanced functionalities and customization options provided by more comprehensive PLM systems, potentially necessitating additional tools or systems to fill these gaps.
The future of cloud PLM systems
As businesses continue to seek more efficient, scalable, and collaborative ways to manage product life cycles, cloud PLM solutions are expected to adapt and innovate in several key areas:
Enhanced Collaboration and Accessibility
Future cloud PLM platforms will further break down silos between departments and external partners, fostering real-time collaboration across the entire product lifecycle. Enhanced accessibility features will ensure that team members, regardless of their location, can access critical product data and contribute to the product development process. This is particularly important as remote work and distributed teams become more prevalent in the global economy.
Customization and Flexibility
As companies operate in increasingly dynamic markets, the ability to customize and adapt PLM systems quickly will become crucial. Cloud PLM providers will likely offer more flexible, modular solutions that can be tailored to specific industry needs or integrated with other business systems (such as ERP, CRM, and SCM). This flexibility will enable businesses to respond more rapidly to market changes, regulatory requirements, and new opportunities.
Subscription-Based Models and Scalability
The trend towards subscription-based pricing models is expected to continue, making PLM solutions more accessible to businesses of all sizes. Cloud PLM platforms will offer scalable solutions that can grow with a company, allowing for the addition of users, increased data storage, and enhanced functionalities without significant upfront investments.
Integration of IoT with PLM
The integration of IoT with PLM is becoming increasingly important, enabling real-time monitoring and control of the manufacturing process. This integration allows for the collection of vast amounts of data from smart devices and machinery, which can be analyzed to optimize manufacturing processes, predict maintenance needs, and enhance product quality. The future of cloud PLM will see deeper integration with IoT, facilitating a more connected, efficient, and responsive manufacturing environment.
Digital Thread and Digital Twins
The Digital Thread concept refers to the creation of a comprehensive, integrated view of a product’s data throughout its lifecycle, from design to manufacturing to service. This seamless flow of data enables stakeholders to access, share, and analyze product information in real time, making it possible to trace the product’s evolution and make informed decisions.
Similarly, Digital Twins use data collected from the physical world to create virtual simulations. These simulations can predict failures, simulate performance under various conditions, and improve product designs. The future cloud PLM systems will leverage Digital Twins and Digital Threads to provide insights that drive innovation and efficiency.
How CADDi Drawer Can Enhances Leveraging Data in Cloud PLM Systems
While cloud PLM systems offer various advantages, in engineering, procurement and manufacturing activities, it’s not feasible to complete tasks with only the data within the PLM. It becomes necessary to analyze and make decisions in engineering chain management and supply chain management by combining various types of information such as drawing data (design information) and supplier data.
Therefore, in addition to Systems of Records (SoR), which mainly manage and store structured data, there is a need for Systems of Insights (SoI). These systems extract data from SoRs for procurement intelligence processes such as analysis and handling data processing. One such SoI is introduced below: CADDi Drawer.
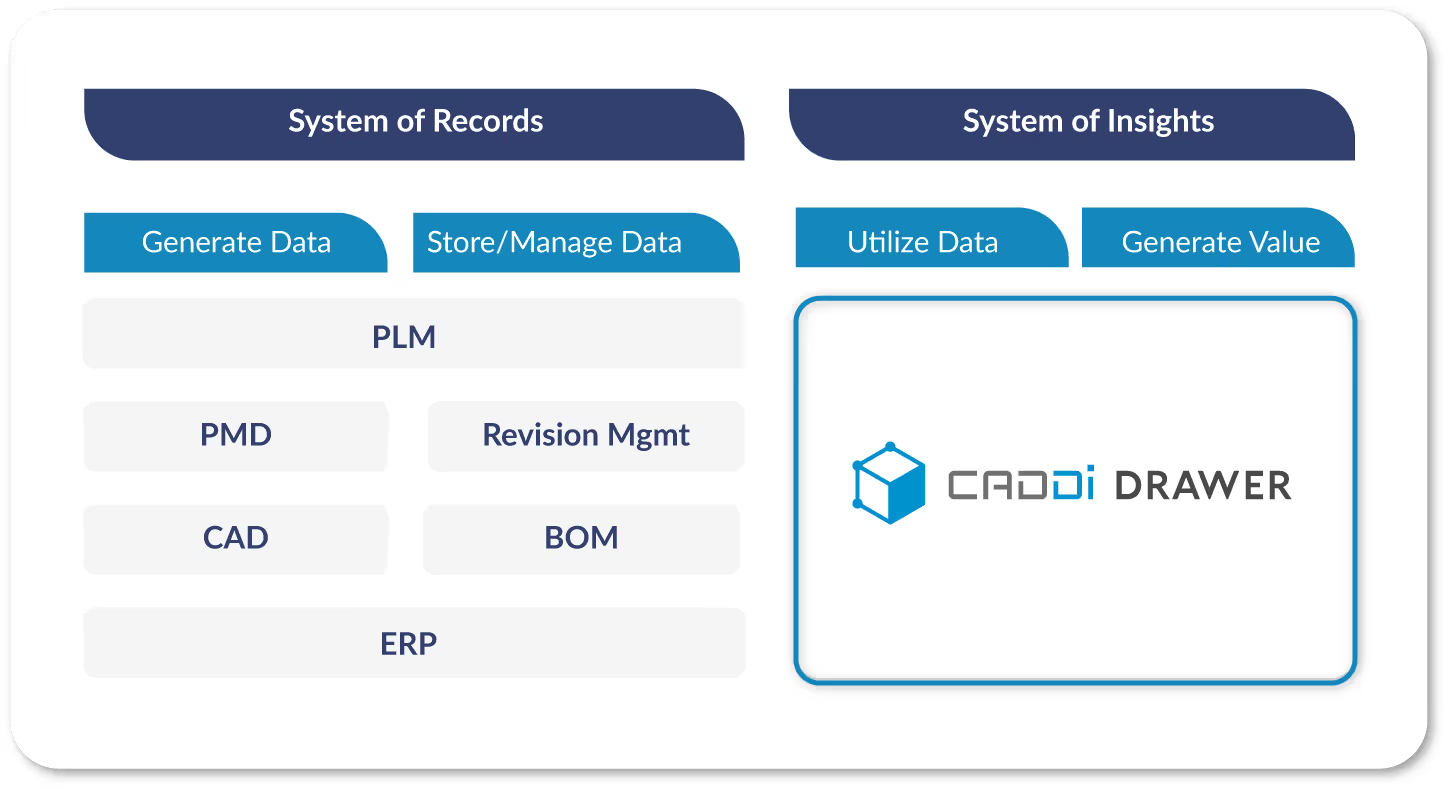
It has the unique capability to automatically convert unstructured data on drawings into structured data, making it accessible and analyzable alongside traditional structured data sources. This capability allows CADDi Drawer to offer comprehensive insights that were previously unattainable.
.avif)
By turning drawings and other unstructured data into structured formats, CADDi Drawer enables procurement teams to perform deep analytics on a wider array of data points and significantly streamline procurement activities such as supplier selection. This capability opens up a multitude of opportunities for insights, from identifying non-obvious cost drivers in the supply chain to uncovering efficiencies in product specifications or procurement processes.
In the article “Procurement 101: Common Failures in Cloud PLM Implementation and How to Avoid Them,” we discussed how to lead cloud PLM implementations to success. Following that, this article presents a list of the major cloud PLM systems and their features as of 2024. It is our hope that this will serve as a useful reference for vendor selection.
Major Cloud PLM Systems List
1. Autodesk Fusion Lifecycle
Core Features: Offers comprehensive project management tools, robust product data management functionalities, quality management systems, and enhanced collaboration tools. It’s designed to streamline product development processes from concept to retirement, ensuring that all stakeholders have access to the latest information.
- Company Size: Medium to large enterprises
- Industry: Manufacturing, engineering, and design
Pros: Features an intuitive interface that simplifies the complexities of PLM. Strong integration capabilities with other Autodesk products enhance workflow continuity. Its robust data management functionalities ensure that product data is accurate, accessible, and secure.
Cons: The platform can be costly for small businesses, making it a significant investment. Additionally, the wide range of features and functionalities may present a steep learning curve for new users unfamiliar with PLM systems.
2. PTC Windchill
Core Features: This platform excels in Bill of Materials (BOM) management, document control, change management, and quality management. It’s designed to facilitate seamless product development and lifecycle management for businesses of all sizes.
- Company Size: Large organizations
- Industry: Aerospace, automotive, electronics, and industrial machinery
Pros: PTC Windchill is renowned for its comprehensive PLM tools and exceptional integration with CAD systems. The platform is highly scalable, making it ideal for large organizations looking to manage complex product life cycles efficiently.
Cons: New users may find the setup process complex and time-consuming. The user interface, while functional, could benefit from enhancements to improve navigation and user experience.
3. Siemens Teamcenter
Core Features: Teamcenter provides robust BOM management, document management, workflow management, and product configuration tools. It’s built to accommodate the needs of enterprises requiring high levels of customization and integration.
- Company Size: Large enterprises
- Industry: Automotive, aerospace, defense, and electronics
Pros: The platform is highly customizable and scalable, with a strong global support and service network. It offers extensive integration capabilities, making it a versatile choice for companies with complex product development needs.
Cons: The cost can be prohibitive for smaller businesses, and the feature complexity requires comprehensive training for users to fully leverage the system’s capabilities.
4. Arena Solutions
Core Features: Arena Solutions specializes in BOM management, change management, quality management systems, and supply chain collaboration. It’s aimed at companies managing complex electronic designs and requiring tight integration across departments.
- Company Size: Small to medium-sized businesses (SMBs), suitable for startups
- Industry: High-tech, electronics, medical devices, and consumer goods
Pros: The software is user-friendly and provides excellent support for managing complex electronic designs. It also offers solid customer support, ensuring that users can effectively utilize its features.
Cons: Some users may find integration with external systems challenging, and the platform’s customization options are somewhat limited compared to other PLM systems.
5. SAP PLM
Core Features: SAP PLM encompasses portfolio and project management, product development, compliance management, and enterprise asset management. It’s designed to support end-to-end business processes within the SAP ecosystem.
- Company Size: Large enterprises
- Industry: All industries, particularly those already using SAP ERP
Pros: The system is well-integrated within the SAP ecosystem, offering robust functionality and supporting comprehensive business processes. It’s ideal for businesses looking for a holistic approach to PLM.
Cons: The platform’s complexity can be daunting for smaller teams, and the overall cost of implementation and operation may be high.
6. Dassault Systèmes ENOVIA
Core Features: ENOVIA stands out with its 3D design and simulation capabilities, BOM management, change management, and real-time collaboration tools. It supports the development of complex products and fosters sustainable innovation.
- Company Size: Medium to large enterprises
- Industry: Aerospace, defense, automotive, and industrial equipment
Pros: The platform offers strong analytics capabilities and is particularly suited for industries dealing with complex products. Its focus on sustainable innovation is also a key differentiator.
Cons: Significant training may be required to fully utilize the platform, and integrating with non-Dassault systems can present challenges.
7. Infor PLM
Core Features: Infor PLM offers product design, development, and launch management tools, alongside supplier relationship management and quality management features. It’s tailored for industry-specific needs and integrates well with Infor’s ERP systems.
- Company Size: Medium to large enterprises
- Industry: Fashion, food and beverage, and industrial manufacturing
Pros: The platform’s industry-specific solutions and flexible architecture make it a strong choice for businesses looking for a tailored PLM experience. It also boasts good integration capabilities with Infor’s ERP systems.
Cons: Some users may find the platform’s customization options complex, and the user interface less intuitive than competitors.
8. Aras Innovator
Core Features: Aras Innovator provides BOM management, quality planning, product engineering, and project management tools. It’s designed for businesses requiring a high degree of customization and flexibility in their PLM system.
- Company Size: Medium to large organizations
- Industry: Aerospace and defense, automotive, and industrial manufacturing
Pros: The platform is highly flexible and customizable, offering a subscription model that includes all updates and upgrades. Its strong community support is a valuable resource for users.
Cons: The system can be resource-intensive to maintain, and the customization process may require a steep learning curve.
9. Propel
Core Features: Propel offers product information management, quality management, and customer feedback integration. It’s designed for high-tech and consumer goods industries, emphasizing ease of use and integration with customer feedback to inform product development.
- Company Size: Small to medium-sized businesses
- Industry: High-tech, consumer goods, and medical devices
Pros: Propel is distinguished by its user-friendly interface and exceptional integration with Salesforce, making it an ideal choice for businesses already using Salesforce platforms. It excels in industries like high-tech and consumer goods by facilitating rapid innovation and product iteration based on customer feedback.
Cons: While Propel is highly effective for managing standard product lifecycle processes, companies dealing with more complex manufacturing processes or those requiring in-depth technical functionalities might find it lacking in some advanced features found in more specialized PLM systems.
10. Oracle Agile PLM
Core Features: Oracle Agile PLM provides a comprehensive suite of tools for product collaboration, quality management, portfolio management, and product governance. It’s built to secure and manage product information throughout the entire lifecycle, from concept to retirement.
- Company Size: Medium to large enterprises
- Industry: High-tech, industrial manufacturing, and life sciences
Pros: One of the main advantages of Oracle Agile PLM is its strong data security features, ensuring that sensitive product information is kept secure. It also offers a comprehensive suite of features for managing all aspects of product lifecycle management and integrates well with other Oracle products, making it a good choice for businesses already invested in the Oracle ecosystem.
Cons: The user interface of Oracle Agile PLM can feel somewhat outdated compared to more modern systems, potentially impacting user adoption and productivity. Additionally, the system may require significant customization to meet specific business needs, which can increase the time and cost of implementation.
11. Upchain
Core Features: Upchain specializes in BOM management, document management, workflow management, and CAD integration. It’s designed to be accessible and user-friendly, catering particularly to small and medium-sized businesses that need a straightforward PLM solution without the complexity of larger systems.
- Company Size: Small to medium-sized businesses
- Industry: Manufacturing, engineering, and design
Pros: Upchain’s ease of use is a major benefit, allowing teams to get up and running quickly with minimal training. It’s also praised for its flexible pricing model, which makes PLM technology accessible to smaller businesses that might be priced out of other solutions. Additionally, its CAD integration capabilities facilitate seamless design and engineering processes.
Cons: While Upchain is a strong contender for small to medium-sized businesses, larger organizations or those with more complex PLM requirements might find its featureset limited. The platform may lack some of the advanced functionalities and customization options provided by more comprehensive PLM systems, potentially necessitating additional tools or systems to fill these gaps.
The future of cloud PLM systems
As businesses continue to seek more efficient, scalable, and collaborative ways to manage product life cycles, cloud PLM solutions are expected to adapt and innovate in several key areas:
Enhanced Collaboration and Accessibility
Future cloud PLM platforms will further break down silos between departments and external partners, fostering real-time collaboration across the entire product lifecycle. Enhanced accessibility features will ensure that team members, regardless of their location, can access critical product data and contribute to the product development process. This is particularly important as remote work and distributed teams become more prevalent in the global economy.
Customization and Flexibility
As companies operate in increasingly dynamic markets, the ability to customize and adapt PLM systems quickly will become crucial. Cloud PLM providers will likely offer more flexible, modular solutions that can be tailored to specific industry needs or integrated with other business systems (such as ERP, CRM, and SCM). This flexibility will enable businesses to respond more rapidly to market changes, regulatory requirements, and new opportunities.
Subscription-Based Models and Scalability
The trend towards subscription-based pricing models is expected to continue, making PLM solutions more accessible to businesses of all sizes. Cloud PLM platforms will offer scalable solutions that can grow with a company, allowing for the addition of users, increased data storage, and enhanced functionalities without significant upfront investments.
Integration of IoT with PLM
The integration of IoT with PLM is becoming increasingly important, enabling real-time monitoring and control of the manufacturing process. This integration allows for the collection of vast amounts of data from smart devices and machinery, which can be analyzed to optimize manufacturing processes, predict maintenance needs, and enhance product quality. The future of cloud PLM will see deeper integration with IoT, facilitating a more connected, efficient, and responsive manufacturing environment.
Digital Thread and Digital Twins
The Digital Thread concept refers to the creation of a comprehensive, integrated view of a product’s data throughout its lifecycle, from design to manufacturing to service. This seamless flow of data enables stakeholders to access, share, and analyze product information in real time, making it possible to trace the product’s evolution and make informed decisions.
Similarly, Digital Twins use data collected from the physical world to create virtual simulations. These simulations can predict failures, simulate performance under various conditions, and improve product designs. The future cloud PLM systems will leverage Digital Twins and Digital Threads to provide insights that drive innovation and efficiency.
How CADDi Drawer Can Enhances Leveraging Data in Cloud PLM Systems
While cloud PLM systems offer various advantages, in engineering, procurement and manufacturing activities, it’s not feasible to complete tasks with only the data within the PLM. It becomes necessary to analyze and make decisions in engineering chain management and supply chain management by combining various types of information such as drawing data (design information) and supplier data.
Therefore, in addition to Systems of Records (SoR), which mainly manage and store structured data, there is a need for Systems of Insights (SoI). These systems extract data from SoRs for procurement intelligence processes such as analysis and handling data processing. One such SoI is introduced below: CADDi Drawer.
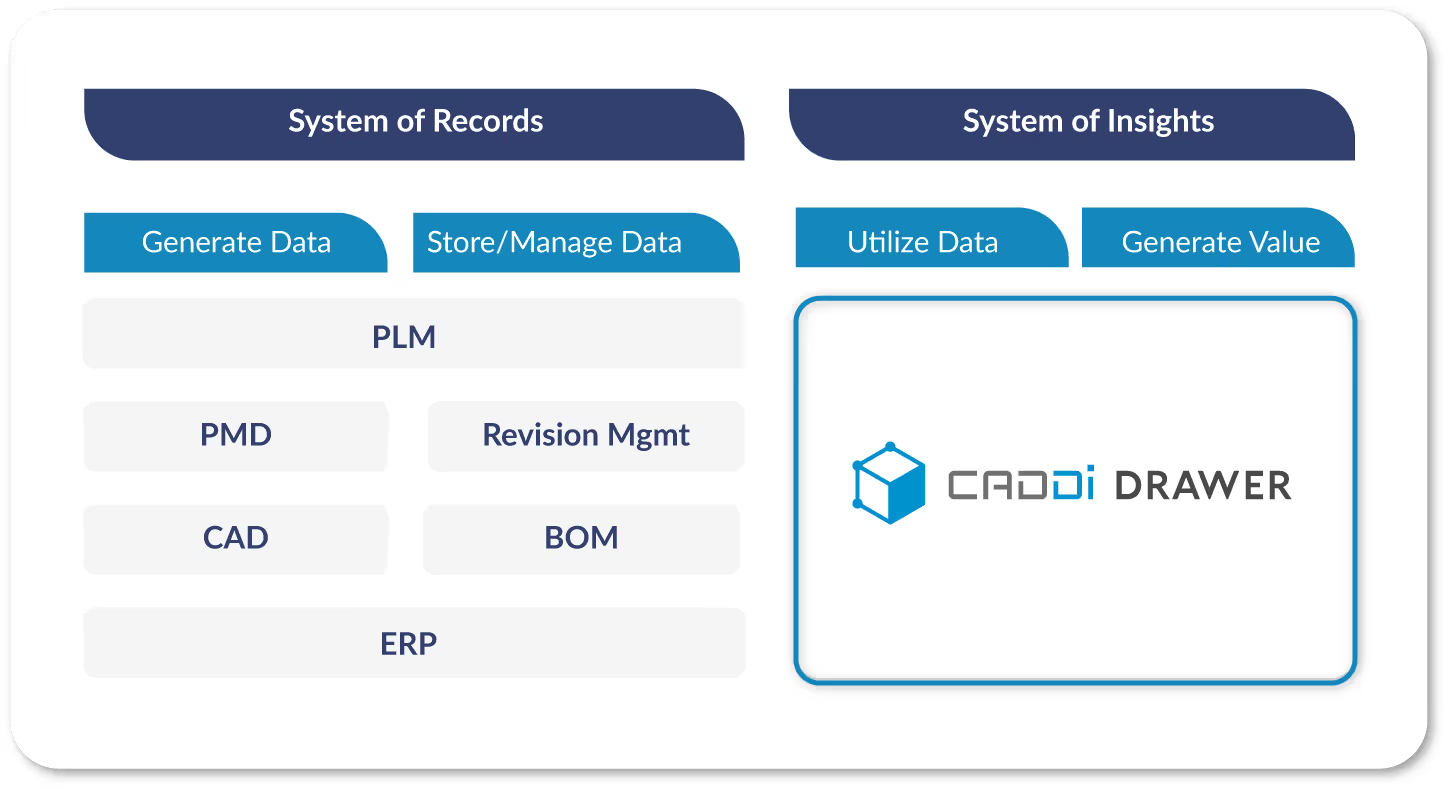
It has the unique capability to automatically convert unstructured data on drawings into structured data, making it accessible and analyzable alongside traditional structured data sources. This capability allows CADDi Drawer to offer comprehensive insights that were previously unattainable.
.avif)
By turning drawings and other unstructured data into structured formats, CADDi Drawer enables procurement teams to perform deep analytics on a wider array of data points and significantly streamline procurement activities such as supplier selection. This capability opens up a multitude of opportunities for insights, from identifying non-obvious cost drivers in the supply chain to uncovering efficiencies in product specifications or procurement processes.
Ready to see CADDi Drawer in action? Get a personalized demo.
Subscribe to our Blog!
Related Resources
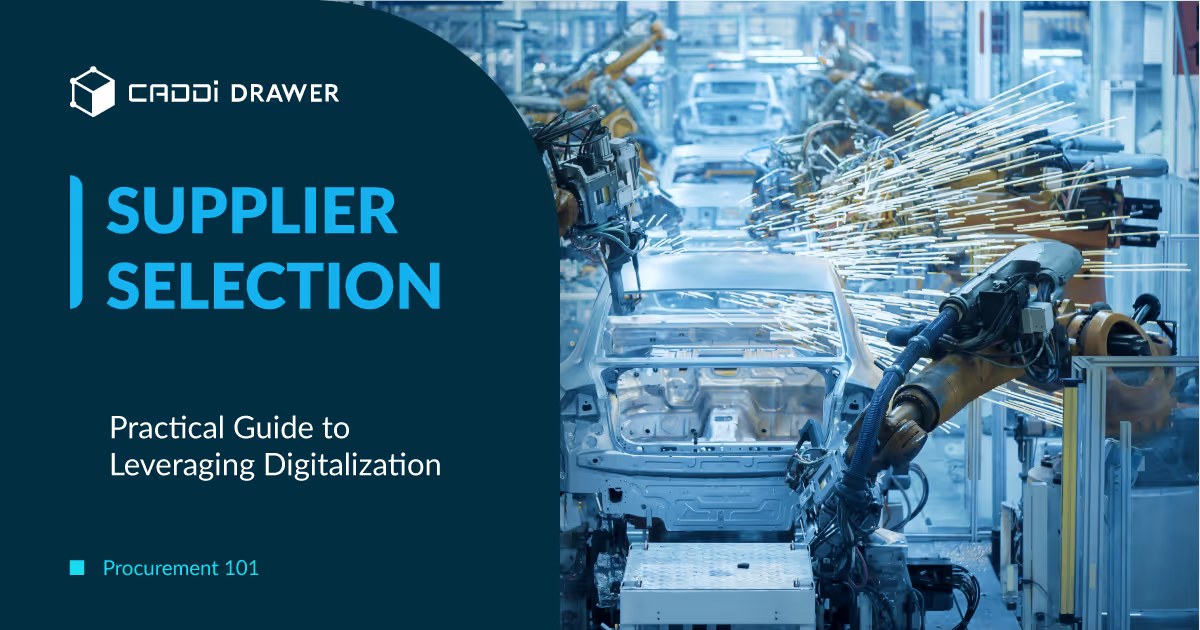

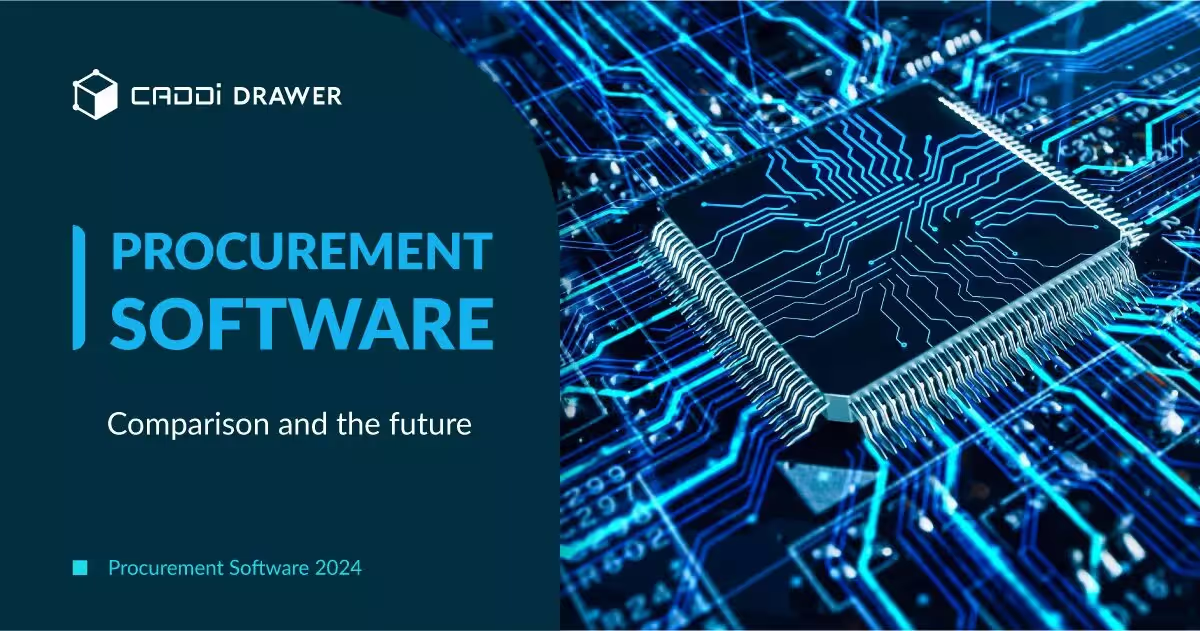
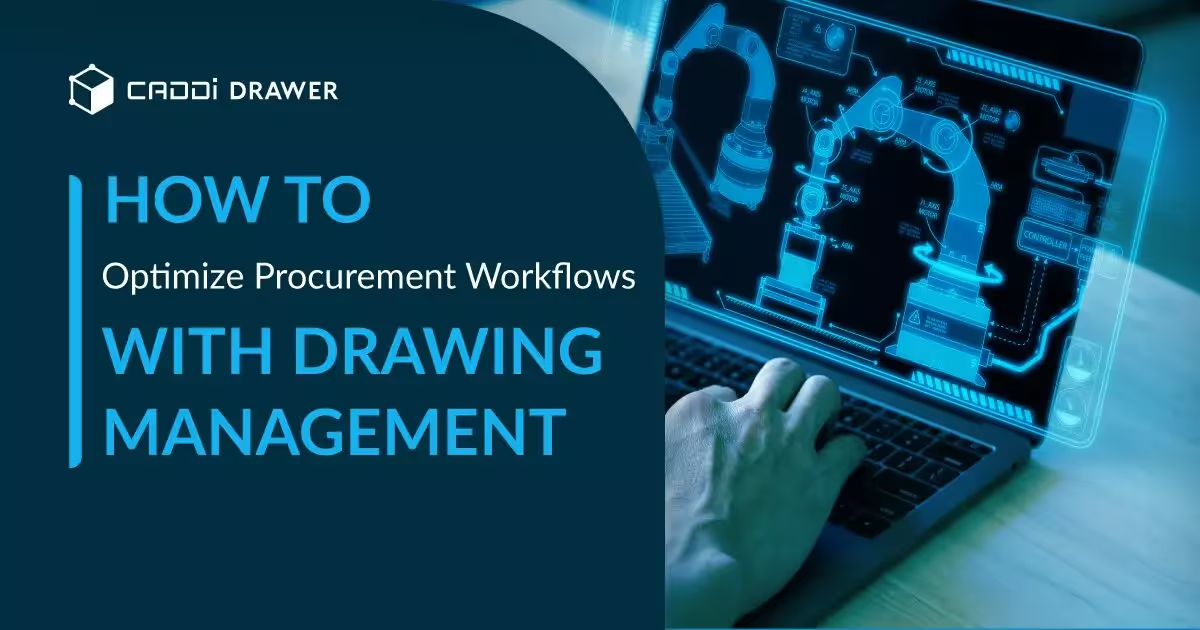
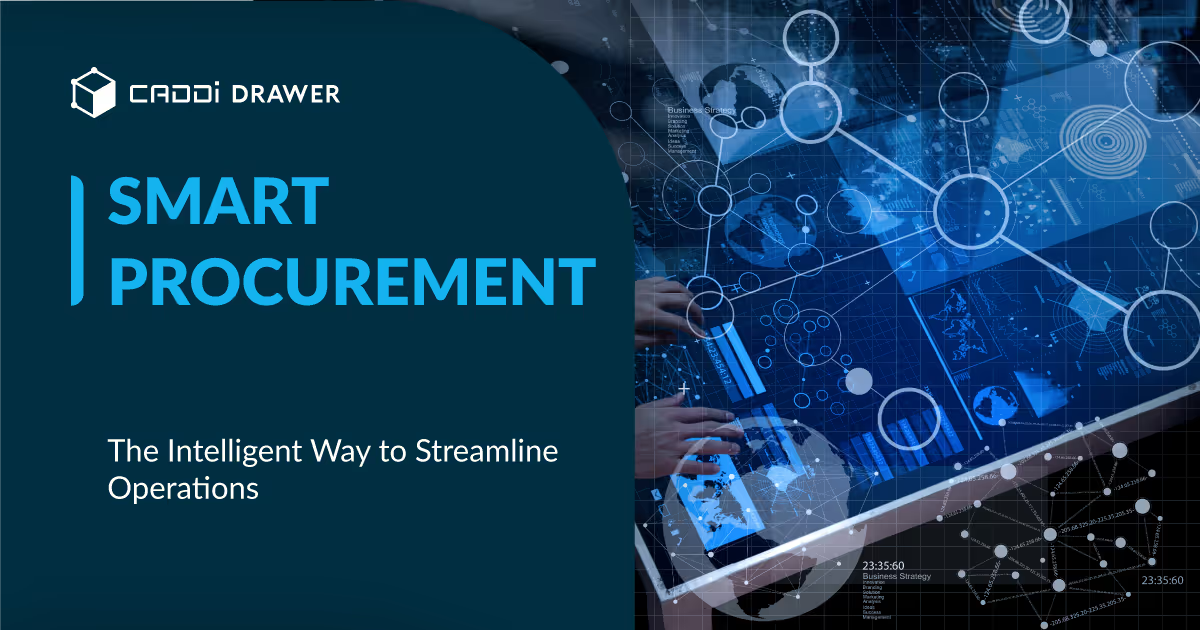
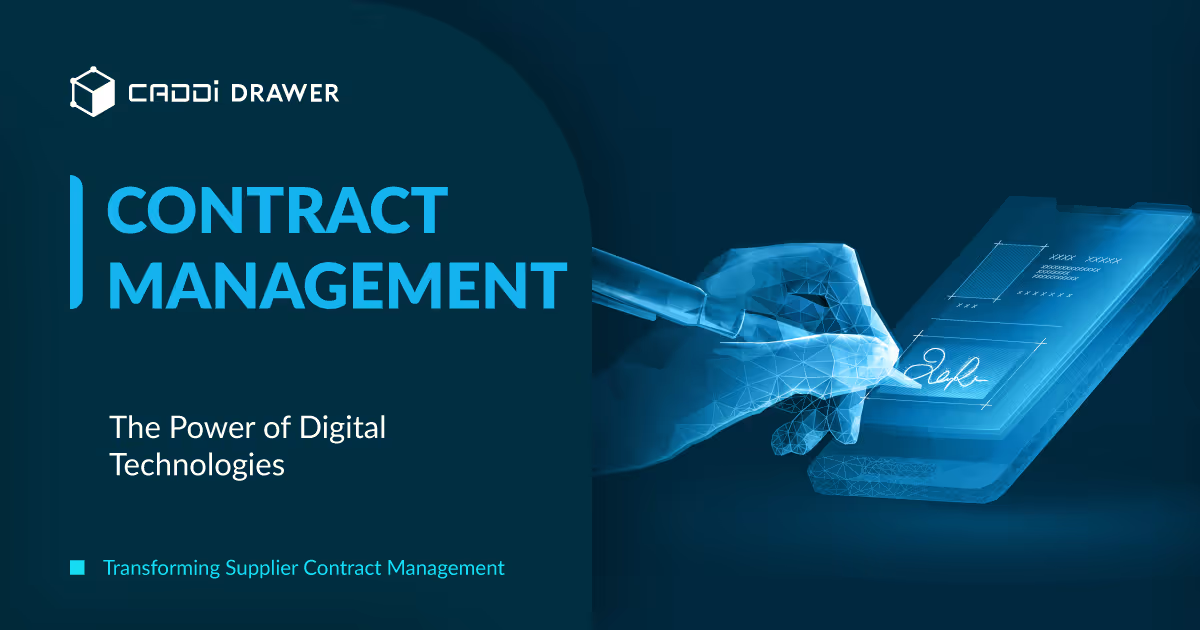