How to Optimize Procurement Workflows with Drawing Management
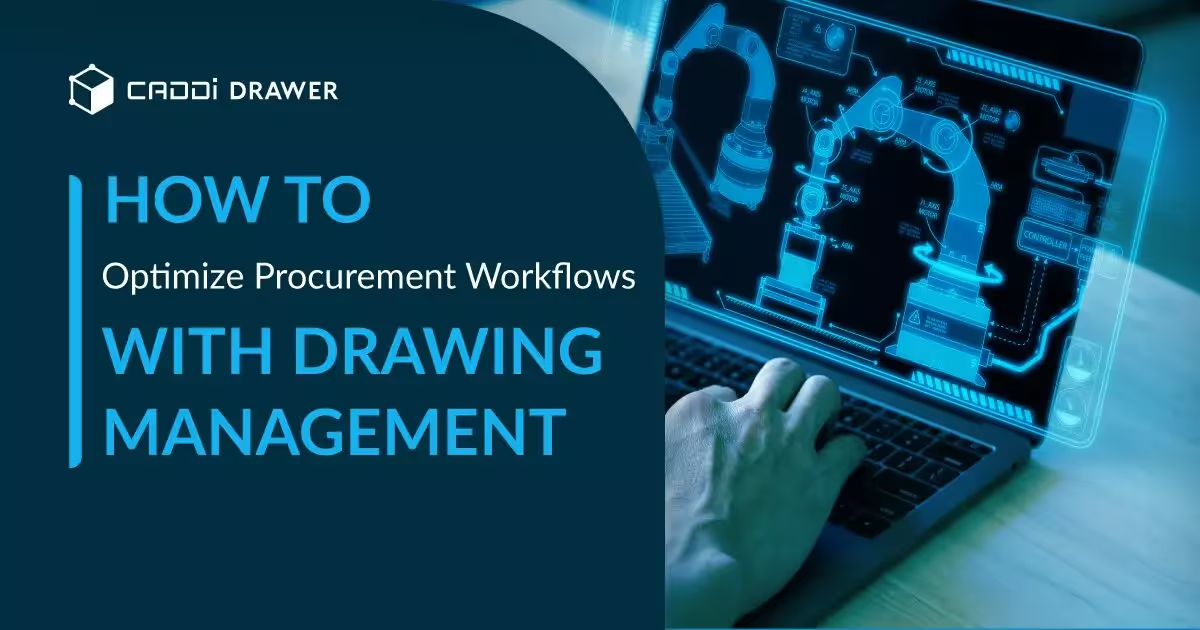
Table of Contents
Why Drawing Management in Procurement is Important
Procurement workflows involve managing the full lifecycle of obtaining goods and services for an organization, from identifying needs to sourcing suppliers to final delivery. A key part of many procurement workflows is managing technical drawings and documentation that provide specifications for the items being procured.
However, drawing management can pose challenges in procurement. Industrial manufacturing and mass-production engineering projects often involve thousands of drawings in multiple formats and versions. Tracking drawing revisions, ensuring stakeholders have the latest versions, and linking drawings to purchase orders and contracts becomes very difficult without a centralized system. Poor drawing management leads to mistakes, delays, and cost overruns.
Optimizing drawing management for procurement provides major benefits. Digital drawing management systems with version control, workflows, and integrations with procurement systems enable real-time access to current drawings across the supply chain.
This improves procurement accuracy, compliance, and efficiency. Suppliers can always construct items to the right specifications. Drawing-related disputes and delays are reduced. Overall, optimized drawing management streamlines procurement operations, reduces risks, and provides significant time and cost savings.
Current State of Drawing Management in Procurement
In many organizations today, drawing management in procurement workflows is still a highly manual process. Teams often rely on paper-based or file sharing systems to manage and share drawings across stakeholders. This creates several inefficiencies:
- Drawing files are stored in multiple locations – shared drives, email, local folders, printouts, etc. This makes it difficult to find the latest versions and collaborate effectively.
- There is no central repository or system of record for drawings. Without a single source of truth, errors and mismatches can occur.
- Sharing and accessing drawings involves emailing files back and forth or printing copies. This is time consuming, prone to version control issues, and makes it hard to track who has the latest drawings.
- There is often minimal security, audit trails, or access controls for drawings containing proprietary information.
- Drawings frequently get lost or damaged when relying on paper copies.
According to McKinsey, nearly 70% of engineering time is spent searching for data instead of doing value-added work. Manual drawing management is a major contributor to these inefficiencies. Industry research suggests teams can waste up to 30 minutes per drawing when managing them manually. For a major capital project with thousands of drawings, the time wasted can quickly add up to thousands of hours and lead to substantial delays.
Best Practices for Optimized Drawing Management
Digital drawing management offers significant advantages over traditional paper-based workflows. By leveraging automation and collaboration tools, procurement teams can streamline processes and boost productivity.
Transition to Digital Workflows
- Eliminate paper blueprints and drawings by maintaining digital master copies in cloud storage or a PLM system. This enables universal access and eliminates printing costs.
- Standardize file naming conventions and organize digital drawings in a structured manner for easy search and retrieval.
- Implement digital workflows for drawing revisions, approvals, and distribution to replace paper transmittals. This accelerates cycle times.
- Equip field teams with mobile devices for accessing the latest drawings electronically in real-time vs carrying bulky printouts.
Automate with PLM Systems
- Integrate drawing management with product data in a PLM system for a single source of truth across the product lifecycle.
- Automate processes such as transmittals, change orders, approvals, revisions etc to eliminate manual steps.
- Ensure tight integration between drawings and BOMs, specifications, quality documents etc for traceability.
- Leverage reporting dashboards for visibility into drawing status, revisions, approvals and other KPIs.
Enable Collaboration via Cloud Platforms
- Maintain drawings in a cloud-based platform for universal access across global teams and external partners/suppliers.
- Allow multi-user editing with built-in workflows to collaborate on drawings in real-time while maintaining version control.
- Facilitate communication and feedback via markups, annotations and discussions linked to drawings.
- Restrict access via role-based permissions to ensure security and confidentiality of sensitive drawings.
Key Benefits of Optimized Drawing Management
Optimizing drawing management in procurement workflows can deliver several key benefits:
- Faster procurement cycles – With a centralized drawing management system, procurement teams can quickly locate the latest approved drawings and documents needed for purchasing components, materials, and services. This eliminates delays from chasing down correct revisions.
- Lower costs – Reduced time spent searching for drawings cuts procurement costs. Well-organized documentation also minimizes expenses from purchasing obsolete or incorrect items.
- Improved quality control – Access to verified, up-to-date drawings enables procurement to order parts and materials that precisely match specifications. This results in fewer quality issues or change orders.
- Better visibility and tracking – A drawing management system provides real-time visibility into document status, revision history, approvals, and more. This level of tracking and auditability is critical for regulated industries.
Optimized drawing management connects procurement and engineering data flows, enabling procurement to keep up with fast-paced design changes. This integration and efficiency drives measurable improvements across key performance metrics.
How CADDi Drawer Optimizes Procurement Workflows
CADDi Drawer offers powerful capabilities to transform drawing management and procurement processes. By leveraging AI and machine learning, Drawer automates the extraction of data from drawings, enables intelligent search across historical drawings, and connects drawing information with quotations and supply chain data. This empowers procurement teams to capitalize on past drawings and quotations to elevate revenue and cut costs.
Key features of CADDi Drawer include:
- Auto Scanning of PDF Drawings: Drawer automatically extracts all data from drawings, including dimensions, text, and shapes. It can even convert handwritten drawings to be searchable and comparable. This digitization of drawings enables procurement to easily locate and utilize drawing information.
- Connecting Quotations and Supply Chain Data: Drawer allows uploading CSV files to connect all relevant information to the associated drawings, such as cost, quantity, supplier details, sales price, cost breakdowns, and more. This integration with ERP data, CAM/CAD systems, quality reports, and spec sheets provides a holistic view for procurement decision-making.
- Intelligent Search: Users can search entire historical drawing archives using any keyword, including material, size, designer name, part name, etc. Drawer’s patented similarity search identifies shapes to find similar drawings, even from handwritten drawings created decades ago. The image search capability allows uploading a photo or sketch to find the most similar drawings in the database.
- Revision Comparison: Drawer makes it simple to see the differences between similar drawings or revisions with a single click. This helps procurement understand changes and their potential impact.
- Data Export: All drawing information, along with associated supplier data, prices, tags, and more can be easily exported to a CSV file. This allows further analysis and integration with other procurement systems and processes.
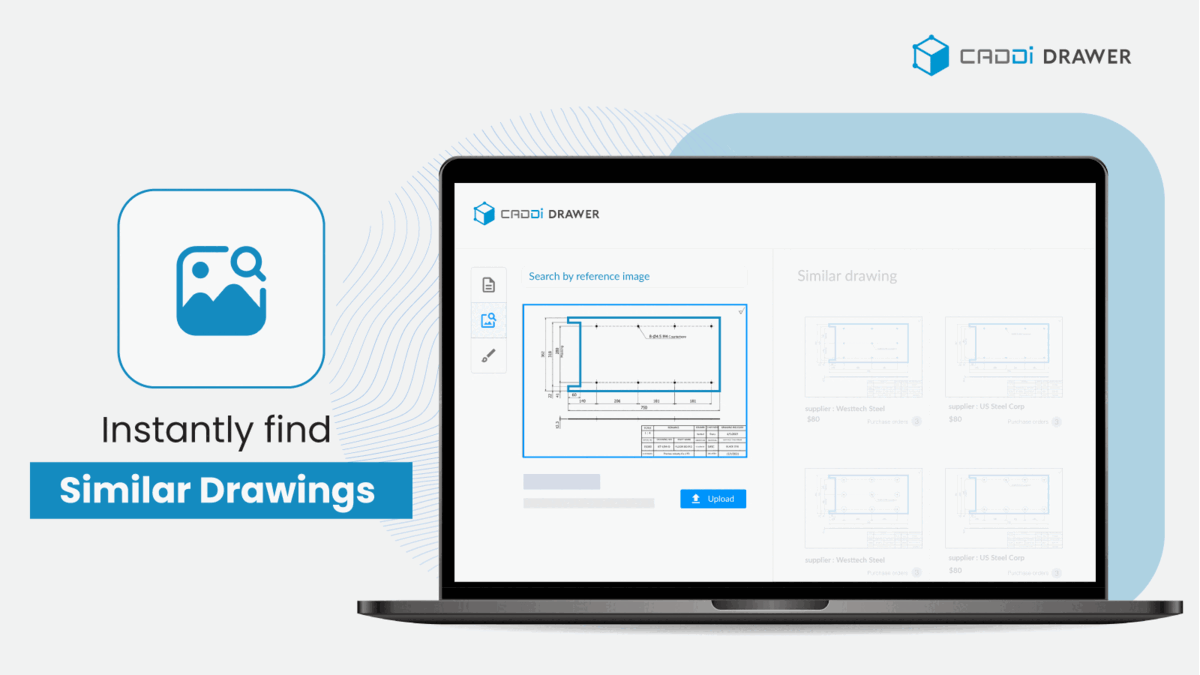
CADDi Drawer enables several key use cases for transforming procurement:
- Strategic Sourcing: With similarity search and connected cost data, procurement can identify the best suppliers and negotiate prices based on historical data. Inconsistent prices for similar parts are highlighted for review.
- Supplier Consolidation: By identifying similar drawings sourced from multiple suppliers, Drawer enables consolidating volumes to preferred suppliers. This is especially powerful for rationalizing suppliers across different subsidiaries and ERP systems.
- Value Analysis and Engineering: Drawer helps uncover cases where small design differences result in large cost discrepancies. This powers VAVE initiatives to optimize designs for cost savings.
In summary, CADDi Drawer’s intelligent drawing management empowers procurement teams with in-depth insights to reduce costs, streamline processes, and make more strategic decisions. By integrating drawing data with the overall procurement workflow, Drawer helps transform procurement from a transactional function to a value-generating strategic partner.
Why Drawing Management in Procurement is Important
Procurement workflows involve managing the full lifecycle of obtaining goods and services for an organization, from identifying needs to sourcing suppliers to final delivery. A key part of many procurement workflows is managing technical drawings and documentation that provide specifications for the items being procured.
However, drawing management can pose challenges in procurement. Industrial manufacturing and mass-production engineering projects often involve thousands of drawings in multiple formats and versions. Tracking drawing revisions, ensuring stakeholders have the latest versions, and linking drawings to purchase orders and contracts becomes very difficult without a centralized system. Poor drawing management leads to mistakes, delays, and cost overruns.
Optimizing drawing management for procurement provides major benefits. Digital drawing management systems with version control, workflows, and integrations with procurement systems enable real-time access to current drawings across the supply chain.
This improves procurement accuracy, compliance, and efficiency. Suppliers can always construct items to the right specifications. Drawing-related disputes and delays are reduced. Overall, optimized drawing management streamlines procurement operations, reduces risks, and provides significant time and cost savings.
Current State of Drawing Management in Procurement
In many organizations today, drawing management in procurement workflows is still a highly manual process. Teams often rely on paper-based or file sharing systems to manage and share drawings across stakeholders. This creates several inefficiencies:
- Drawing files are stored in multiple locations – shared drives, email, local folders, printouts, etc. This makes it difficult to find the latest versions and collaborate effectively.
- There is no central repository or system of record for drawings. Without a single source of truth, errors and mismatches can occur.
- Sharing and accessing drawings involves emailing files back and forth or printing copies. This is time consuming, prone to version control issues, and makes it hard to track who has the latest drawings.
- There is often minimal security, audit trails, or access controls for drawings containing proprietary information.
- Drawings frequently get lost or damaged when relying on paper copies.
According to McKinsey, nearly 70% of engineering time is spent searching for data instead of doing value-added work. Manual drawing management is a major contributor to these inefficiencies. Industry research suggests teams can waste up to 30 minutes per drawing when managing them manually. For a major capital project with thousands of drawings, the time wasted can quickly add up to thousands of hours and lead to substantial delays.
Best Practices for Optimized Drawing Management
Digital drawing management offers significant advantages over traditional paper-based workflows. By leveraging automation and collaboration tools, procurement teams can streamline processes and boost productivity.
Transition to Digital Workflows
- Eliminate paper blueprints and drawings by maintaining digital master copies in cloud storage or a PLM system. This enables universal access and eliminates printing costs.
- Standardize file naming conventions and organize digital drawings in a structured manner for easy search and retrieval.
- Implement digital workflows for drawing revisions, approvals, and distribution to replace paper transmittals. This accelerates cycle times.
- Equip field teams with mobile devices for accessing the latest drawings electronically in real-time vs carrying bulky printouts.
Automate with PLM Systems
- Integrate drawing management with product data in a PLM system for a single source of truth across the product lifecycle.
- Automate processes such as transmittals, change orders, approvals, revisions etc to eliminate manual steps.
- Ensure tight integration between drawings and BOMs, specifications, quality documents etc for traceability.
- Leverage reporting dashboards for visibility into drawing status, revisions, approvals and other KPIs.
Enable Collaboration via Cloud Platforms
- Maintain drawings in a cloud-based platform for universal access across global teams and external partners/suppliers.
- Allow multi-user editing with built-in workflows to collaborate on drawings in real-time while maintaining version control.
- Facilitate communication and feedback via markups, annotations and discussions linked to drawings.
- Restrict access via role-based permissions to ensure security and confidentiality of sensitive drawings.
Key Benefits of Optimized Drawing Management
Optimizing drawing management in procurement workflows can deliver several key benefits:
- Faster procurement cycles – With a centralized drawing management system, procurement teams can quickly locate the latest approved drawings and documents needed for purchasing components, materials, and services. This eliminates delays from chasing down correct revisions.
- Lower costs – Reduced time spent searching for drawings cuts procurement costs. Well-organized documentation also minimizes expenses from purchasing obsolete or incorrect items.
- Improved quality control – Access to verified, up-to-date drawings enables procurement to order parts and materials that precisely match specifications. This results in fewer quality issues or change orders.
- Better visibility and tracking – A drawing management system provides real-time visibility into document status, revision history, approvals, and more. This level of tracking and auditability is critical for regulated industries.
Optimized drawing management connects procurement and engineering data flows, enabling procurement to keep up with fast-paced design changes. This integration and efficiency drives measurable improvements across key performance metrics.
How CADDi Drawer Optimizes Procurement Workflows
CADDi Drawer offers powerful capabilities to transform drawing management and procurement processes. By leveraging AI and machine learning, Drawer automates the extraction of data from drawings, enables intelligent search across historical drawings, and connects drawing information with quotations and supply chain data. This empowers procurement teams to capitalize on past drawings and quotations to elevate revenue and cut costs.
Key features of CADDi Drawer include:
- Auto Scanning of PDF Drawings: Drawer automatically extracts all data from drawings, including dimensions, text, and shapes. It can even convert handwritten drawings to be searchable and comparable. This digitization of drawings enables procurement to easily locate and utilize drawing information.
- Connecting Quotations and Supply Chain Data: Drawer allows uploading CSV files to connect all relevant information to the associated drawings, such as cost, quantity, supplier details, sales price, cost breakdowns, and more. This integration with ERP data, CAM/CAD systems, quality reports, and spec sheets provides a holistic view for procurement decision-making.
- Intelligent Search: Users can search entire historical drawing archives using any keyword, including material, size, designer name, part name, etc. Drawer’s patented similarity search identifies shapes to find similar drawings, even from handwritten drawings created decades ago. The image search capability allows uploading a photo or sketch to find the most similar drawings in the database.
- Revision Comparison: Drawer makes it simple to see the differences between similar drawings or revisions with a single click. This helps procurement understand changes and their potential impact.
- Data Export: All drawing information, along with associated supplier data, prices, tags, and more can be easily exported to a CSV file. This allows further analysis and integration with other procurement systems and processes.
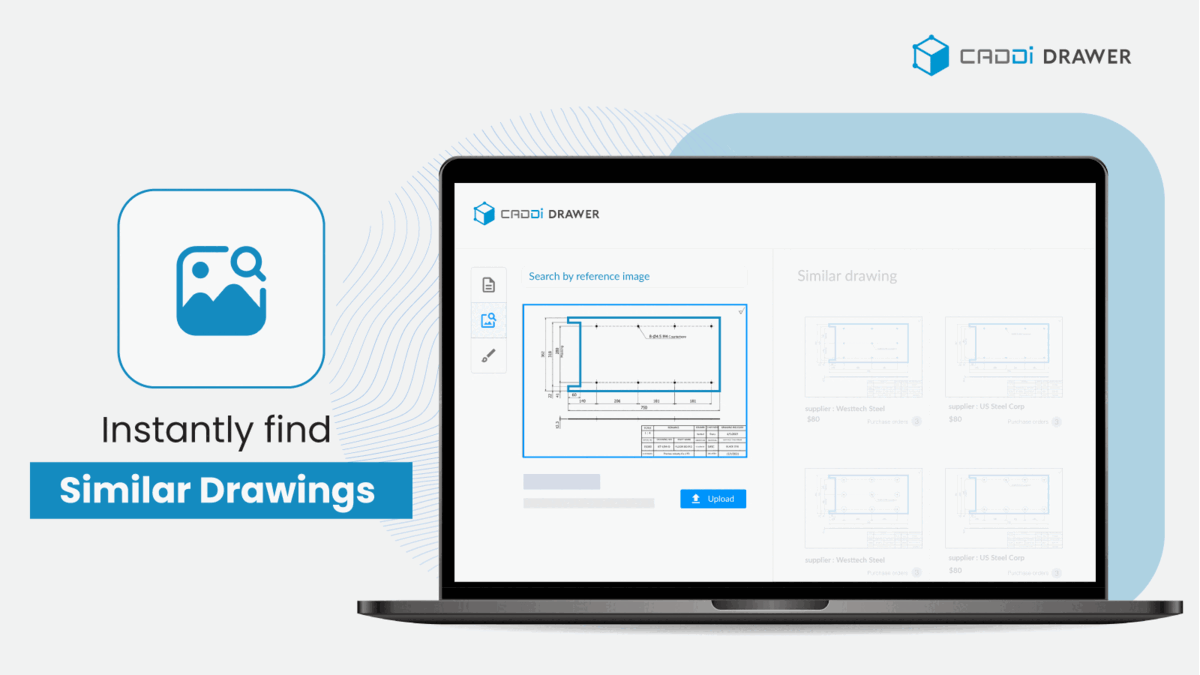
CADDi Drawer enables several key use cases for transforming procurement:
- Strategic Sourcing: With similarity search and connected cost data, procurement can identify the best suppliers and negotiate prices based on historical data. Inconsistent prices for similar parts are highlighted for review.
- Supplier Consolidation: By identifying similar drawings sourced from multiple suppliers, Drawer enables consolidating volumes to preferred suppliers. This is especially powerful for rationalizing suppliers across different subsidiaries and ERP systems.
- Value Analysis and Engineering: Drawer helps uncover cases where small design differences result in large cost discrepancies. This powers VAVE initiatives to optimize designs for cost savings.
In summary, CADDi Drawer’s intelligent drawing management empowers procurement teams with in-depth insights to reduce costs, streamline processes, and make more strategic decisions. By integrating drawing data with the overall procurement workflow, Drawer helps transform procurement from a transactional function to a value-generating strategic partner.
Ready to see CADDi Drawer in action? Get a personalized demo.
Subscribe to our Blog!
Related Resources
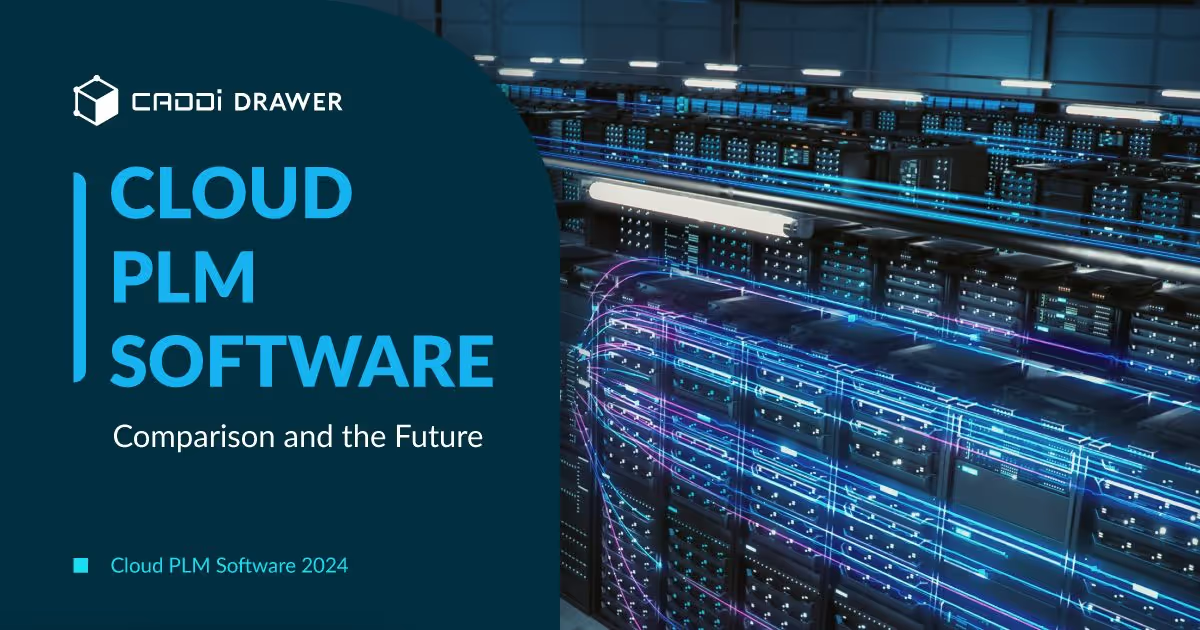
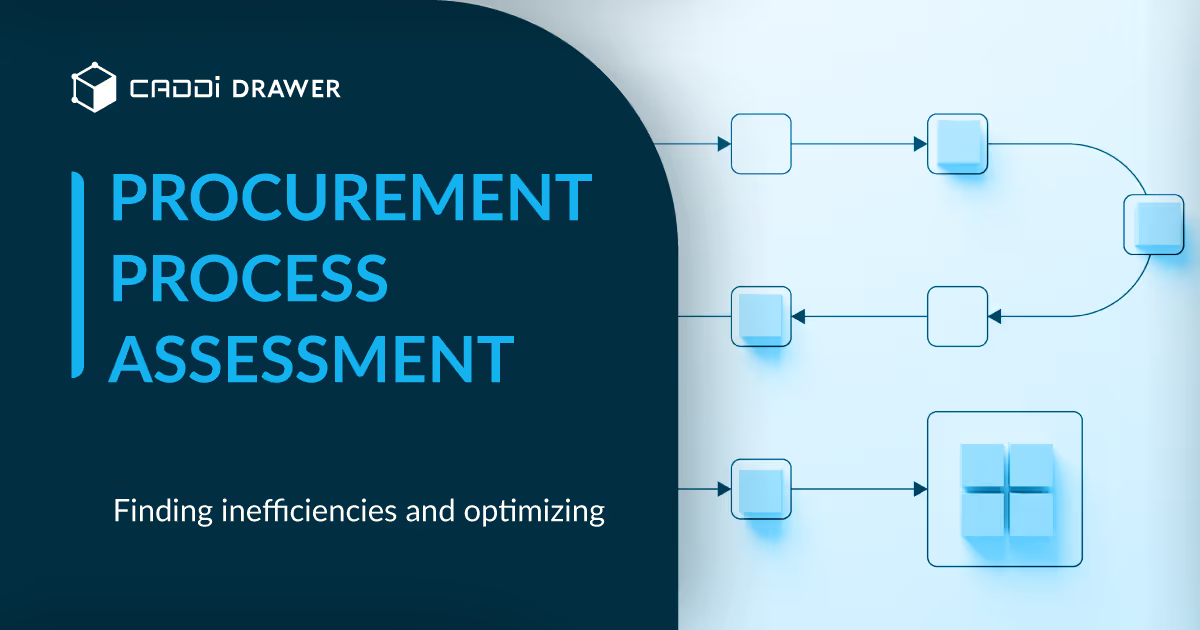
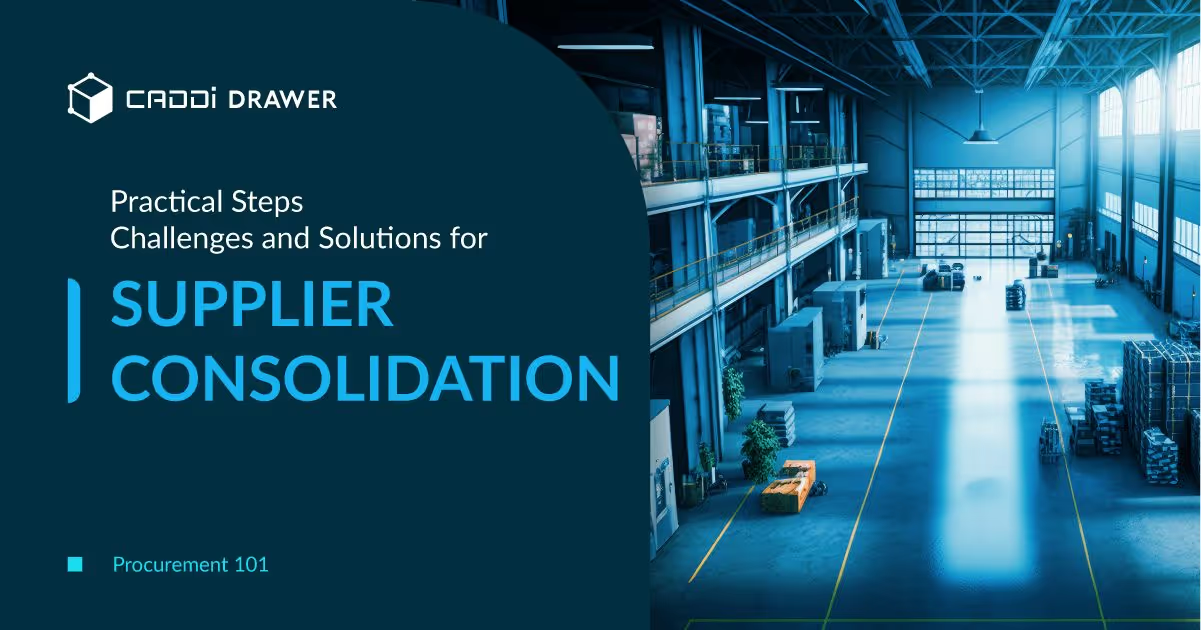
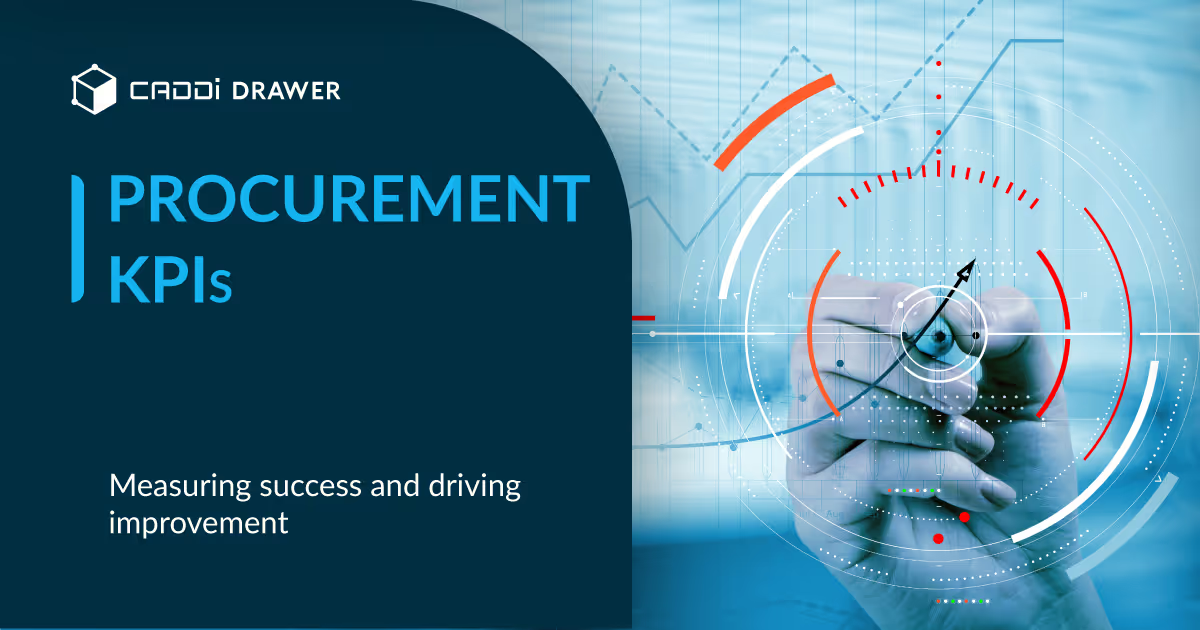
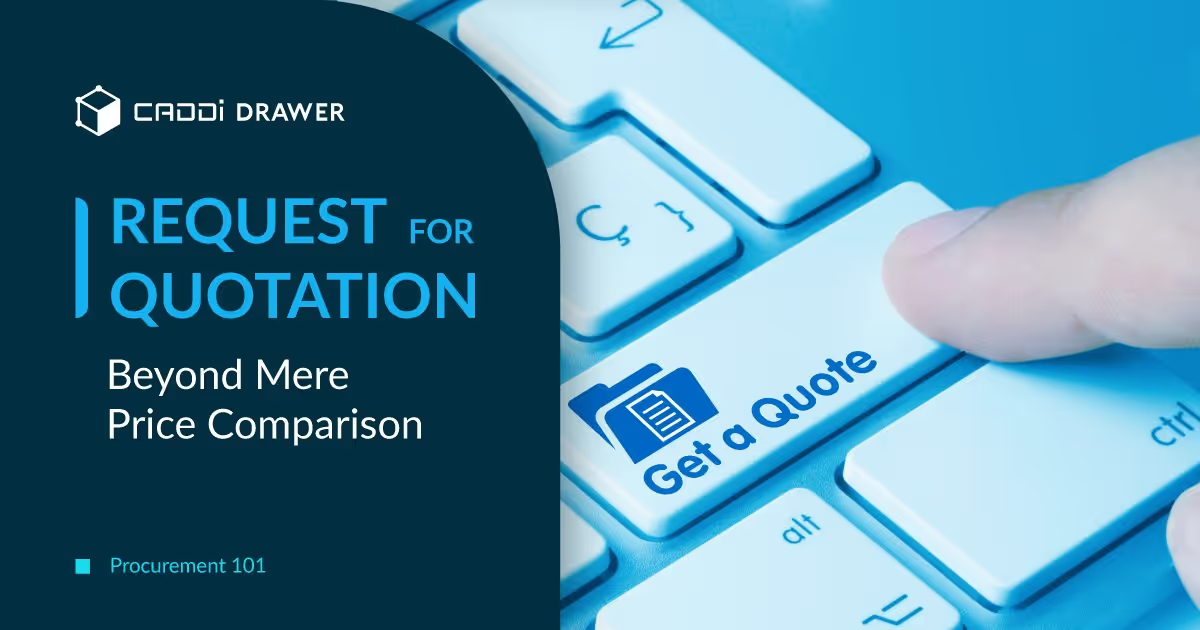
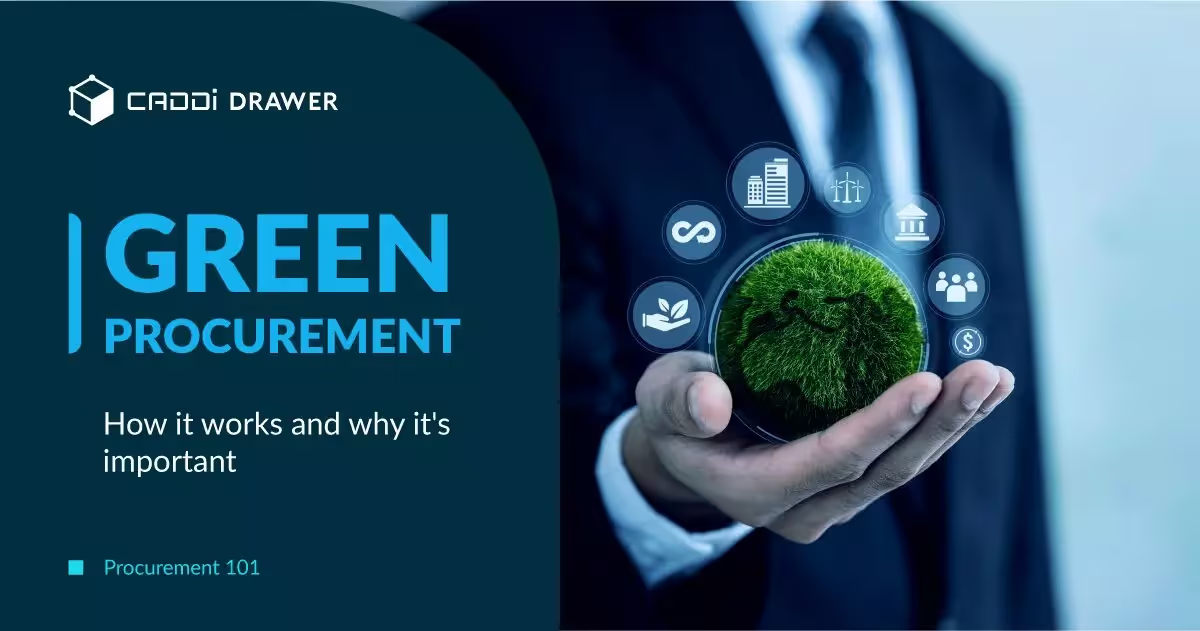