Procurement Performance Assessment - What it is and how to do one
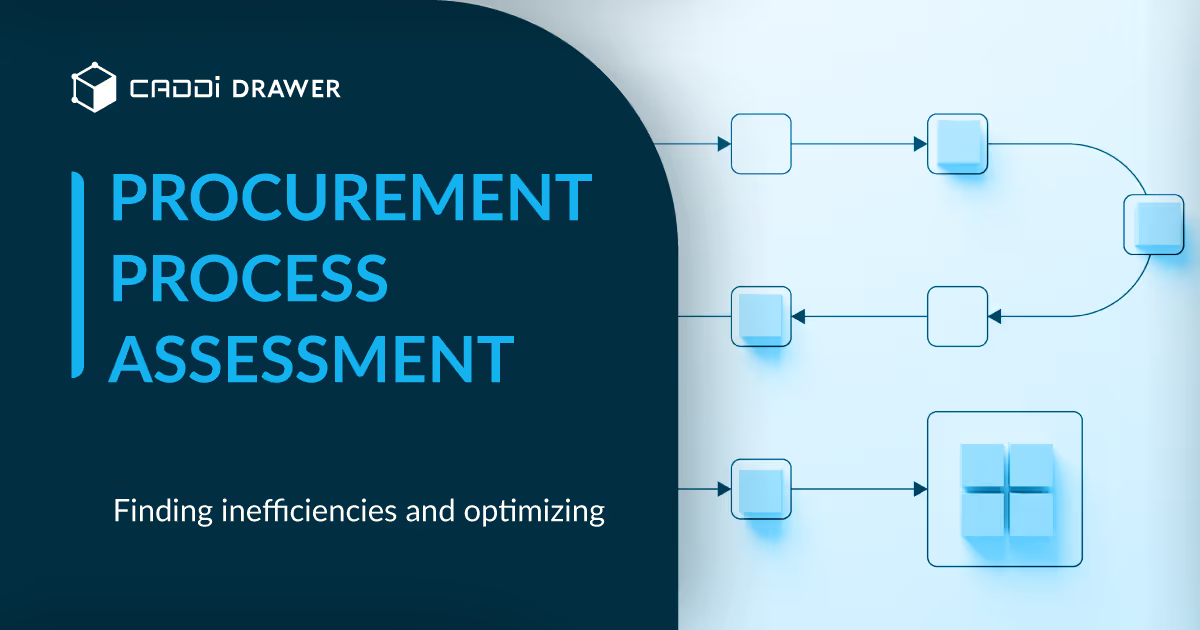
Table of Contents
A procurement performance assessment is a process where you analyze and track the effectiveness, speed, and financial performance of your procurement activities. It involves breaking down procurement to individual deals and suppliers, looking at the costs, quality data, and timelines for each of them. Then you roll this granular data up to see overall trends in procurement performance.
How do you do a Procurement Performance Assessment?
A helpful procurement performance assessment is a major undertaking that will require cooperation across multiple parties. Don’t expect to breeze through this; instead, devote the time to get the most out of what you learn.
Each company will have their own stumbling blocks and opportunities when completing their assessment. Generally speaking, though, these are the subtasks you need to complete:
1. Ensure your systems can produce the data you need
This preliminary task can be the most difficult. You need to make sure that your enterprise resource planning (ERP) software is producing and storing the data of what parts are procured on each deal. You want to know costs, quantities, suppliers, the dates of transactions, and more. You also want to track data about those parts once you’ve started using them, using your product lifecycle management (PLM) software. Data about quality, failure rate, and use duration should be stored for each part.
The challenging thing is making sure there’s a connection between the order data of a part and the failure data of the same part in operation. Most software setups will have a disconnect. Using a system of insight, like CADDi, can make these connections more consistent and intuitive. This is necessary in order to make accurate judgments in your procurement performance assessment.
2. Determine the most critical KPIs for your procurement process
You should go into your procurement performance assessment with specific goals in mind. Base these goals on where your process needs to achieve better performance. Do you need to decrease the time that each procurement cycle takes? Do you need to save more money on each deal?
Once you have some sense of what you’re trying to achieve, determine the metrics that would reflect success in these categories. Some examples of KPIs for procurement processes include:
- Average spend on each deal
- Average failure rate/year on each part
- Average cycle length between orders being initiated and receiving the parts
- Number of suppliers used in an average month
- Contract compliance rate
There are many more specific KPIs that may be required for specific goals. You may also want to focus on only certain types of deals, or certain suppliers.
Once you have some KPIs you want to focus on, start collecting the baseline data of your system at its current state.
Keep an open mind as you collect this data. You’re likely to notice metrics that are underperforming that you didn’t expect as you start to turn over rocks. You might need to reevaluate your priorities once you get a more accurate picture of your current performance.
3. Investigate causes of procurement performance inefficiencies
Once you understand where improvements are necessary, start investigating the causes of those inefficiencies. For example, if cycles are taking too long, look at where time is added during procurement. Is it in looking up past deals for related parts? Is it in putting out the RFQ to suppliers? Is it in approving a quote?
Your system might not be granular enough at first to capture all of these sub-stages of cycles. Tracking this data may involve the cooperation and coordination of many different teams. Use a few specific examples and track them as they go through the steps.
It’s important to note that this will require extra work for your procurement team and others. Don’t dump this on them as “additional work”, but allocate time and resources for it. Set your expectations for other work accordingly. Think of this as investment in your long-term process. It will be worth it.
4. Attempt fixes and track results
This seems like it would be the most difficult step, but sometimes your procurement performance assessment can reveal some surprisingly simple solutions. You may realize that some layer of approvals adds no value but consistently takes a long time. You may uncover old manual steps in processes that can be automated easily with modern technology.
Other issues will require more sophisticated features. A common stumbling block in procurement is accessing old data. If investigating past deals for a given part, procurement teams typically need to look up specific order or part numbers. This leads to a lot of endless scrolling through databases or cross-referencing dozens of tables. Cutting-edge solutions do exist, however. CADDi can trivialize these searches by using drawing-based connections to give you all relevant historical data without requiring any specific knowledge.
Once you’ve implemented some changes, continue tracking your KPIs to ensure improvements. You may not immediately see the results you expect. Remember that process changes always have learning curves, so be patient as people become accustomed. It’s also possible that you misattributed an inefficiency. This isn’t anything to be ashamed of. Procurement is a complicated process where many things are interconnected. Reassess your hypotheses with the knowledge you’ve gained from your first attempt. Eventually all your roadblocks can be ironed out.
5. Prepare your next procurement performance assessment
The procurement performance assessment isn’t a “one and done” process. It should be something repeated on a regular basis. Even if all your initial goals are achieved, new improvements are always possible. Embrace a continuous improvement mentality and keep finding areas to improve.
How to get a step up with CADDi Drawer
CADDi Drawer represents a significant leap forward in the continuous improvement initiatives within the manufacturing sector, particularly in the realms of procurement and drawing management.
Streamline activities in the procurement and manufacturing process
The following features enable you to streamline the time-consuming tasks of data collection and organization in procurement and manufacturing operations.
- Cost data, supplier information, spec documents and manufacturing work instructions link automatically to each drawing and can also be exported together.
- By using keyword searches combined with similarity searches, the time spent searching for drawings and data in procurement tasks can be reduced.
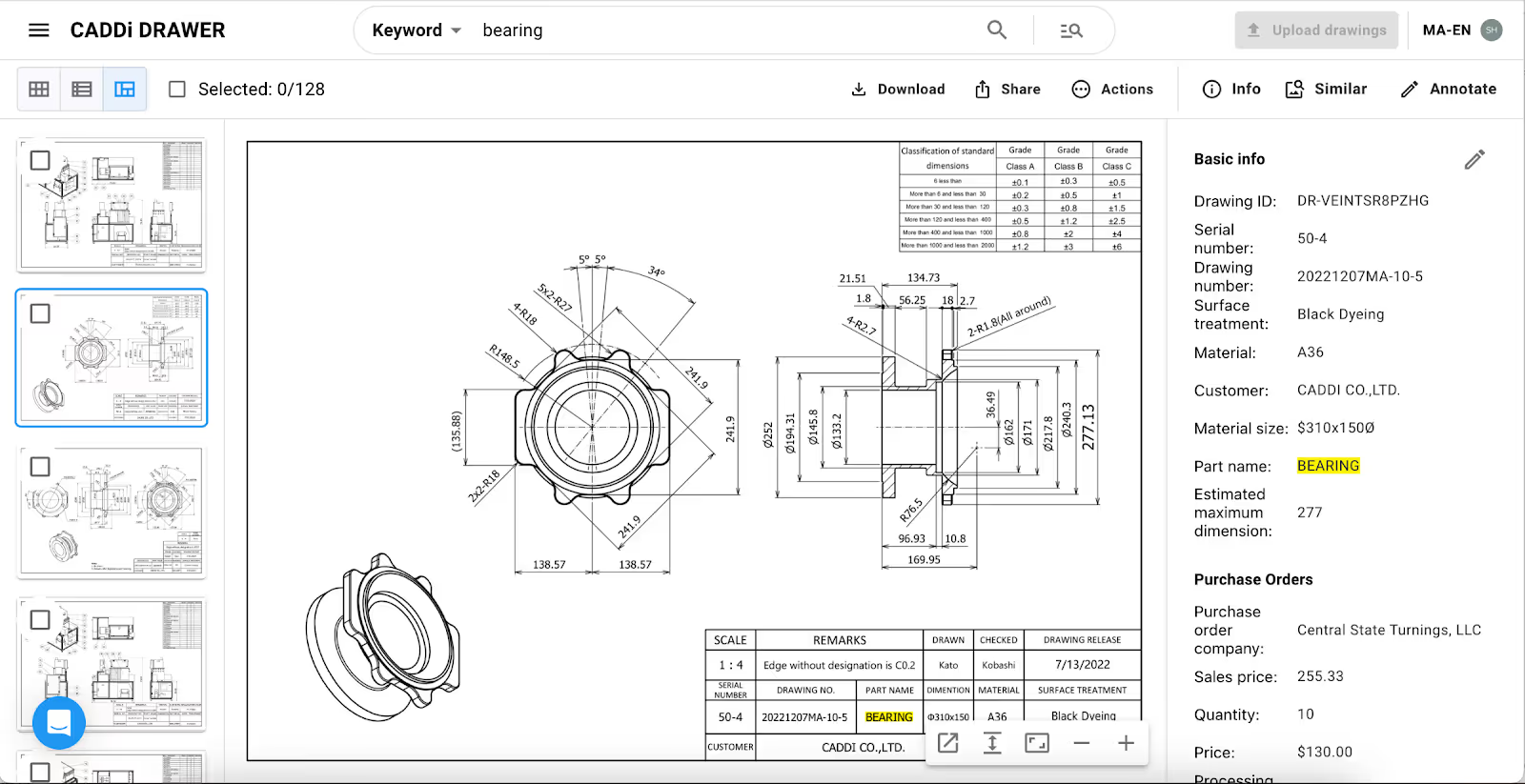
One of the key aspects of CADDi Drawer that supports continuous improvement is its collaborative capabilities. In manufacturing, the ability to quickly share and review designs and specifications can significantly speed up the iteration process. CADDi Drawer allows for seamless collaboration among teams, regardless of their physical location, fostering an environment where feedback is rapidly integrated, and improvements are continuously implemented. This feature is crucial for manufacturers aiming to refine their processes and products steadily over time, as it ensures that all stakeholders can contribute to the enhancement of quality and efficiency.
A procurement performance assessment is a process where you analyze and track the effectiveness, speed, and financial performance of your procurement activities. It involves breaking down procurement to individual deals and suppliers, looking at the costs, quality data, and timelines for each of them. Then you roll this granular data up to see overall trends in procurement performance.
How do you do a Procurement Performance Assessment?
A helpful procurement performance assessment is a major undertaking that will require cooperation across multiple parties. Don’t expect to breeze through this; instead, devote the time to get the most out of what you learn.
Each company will have their own stumbling blocks and opportunities when completing their assessment. Generally speaking, though, these are the subtasks you need to complete:
1. Ensure your systems can produce the data you need
This preliminary task can be the most difficult. You need to make sure that your enterprise resource planning (ERP) software is producing and storing the data of what parts are procured on each deal. You want to know costs, quantities, suppliers, the dates of transactions, and more. You also want to track data about those parts once you’ve started using them, using your product lifecycle management (PLM) software. Data about quality, failure rate, and use duration should be stored for each part.
The challenging thing is making sure there’s a connection between the order data of a part and the failure data of the same part in operation. Most software setups will have a disconnect. Using a system of insight, like CADDi, can make these connections more consistent and intuitive. This is necessary in order to make accurate judgments in your procurement performance assessment.
2. Determine the most critical KPIs for your procurement process
You should go into your procurement performance assessment with specific goals in mind. Base these goals on where your process needs to achieve better performance. Do you need to decrease the time that each procurement cycle takes? Do you need to save more money on each deal?
Once you have some sense of what you’re trying to achieve, determine the metrics that would reflect success in these categories. Some examples of KPIs for procurement processes include:
- Average spend on each deal
- Average failure rate/year on each part
- Average cycle length between orders being initiated and receiving the parts
- Number of suppliers used in an average month
- Contract compliance rate
There are many more specific KPIs that may be required for specific goals. You may also want to focus on only certain types of deals, or certain suppliers.
Once you have some KPIs you want to focus on, start collecting the baseline data of your system at its current state.
Keep an open mind as you collect this data. You’re likely to notice metrics that are underperforming that you didn’t expect as you start to turn over rocks. You might need to reevaluate your priorities once you get a more accurate picture of your current performance.
3. Investigate causes of procurement performance inefficiencies
Once you understand where improvements are necessary, start investigating the causes of those inefficiencies. For example, if cycles are taking too long, look at where time is added during procurement. Is it in looking up past deals for related parts? Is it in putting out the RFQ to suppliers? Is it in approving a quote?
Your system might not be granular enough at first to capture all of these sub-stages of cycles. Tracking this data may involve the cooperation and coordination of many different teams. Use a few specific examples and track them as they go through the steps.
It’s important to note that this will require extra work for your procurement team and others. Don’t dump this on them as “additional work”, but allocate time and resources for it. Set your expectations for other work accordingly. Think of this as investment in your long-term process. It will be worth it.
4. Attempt fixes and track results
This seems like it would be the most difficult step, but sometimes your procurement performance assessment can reveal some surprisingly simple solutions. You may realize that some layer of approvals adds no value but consistently takes a long time. You may uncover old manual steps in processes that can be automated easily with modern technology.
Other issues will require more sophisticated features. A common stumbling block in procurement is accessing old data. If investigating past deals for a given part, procurement teams typically need to look up specific order or part numbers. This leads to a lot of endless scrolling through databases or cross-referencing dozens of tables. Cutting-edge solutions do exist, however. CADDi can trivialize these searches by using drawing-based connections to give you all relevant historical data without requiring any specific knowledge.
Once you’ve implemented some changes, continue tracking your KPIs to ensure improvements. You may not immediately see the results you expect. Remember that process changes always have learning curves, so be patient as people become accustomed. It’s also possible that you misattributed an inefficiency. This isn’t anything to be ashamed of. Procurement is a complicated process where many things are interconnected. Reassess your hypotheses with the knowledge you’ve gained from your first attempt. Eventually all your roadblocks can be ironed out.
5. Prepare your next procurement performance assessment
The procurement performance assessment isn’t a “one and done” process. It should be something repeated on a regular basis. Even if all your initial goals are achieved, new improvements are always possible. Embrace a continuous improvement mentality and keep finding areas to improve.
How to get a step up with CADDi Drawer
CADDi Drawer represents a significant leap forward in the continuous improvement initiatives within the manufacturing sector, particularly in the realms of procurement and drawing management.
Streamline activities in the procurement and manufacturing process
The following features enable you to streamline the time-consuming tasks of data collection and organization in procurement and manufacturing operations.
- Cost data, supplier information, spec documents and manufacturing work instructions link automatically to each drawing and can also be exported together.
- By using keyword searches combined with similarity searches, the time spent searching for drawings and data in procurement tasks can be reduced.
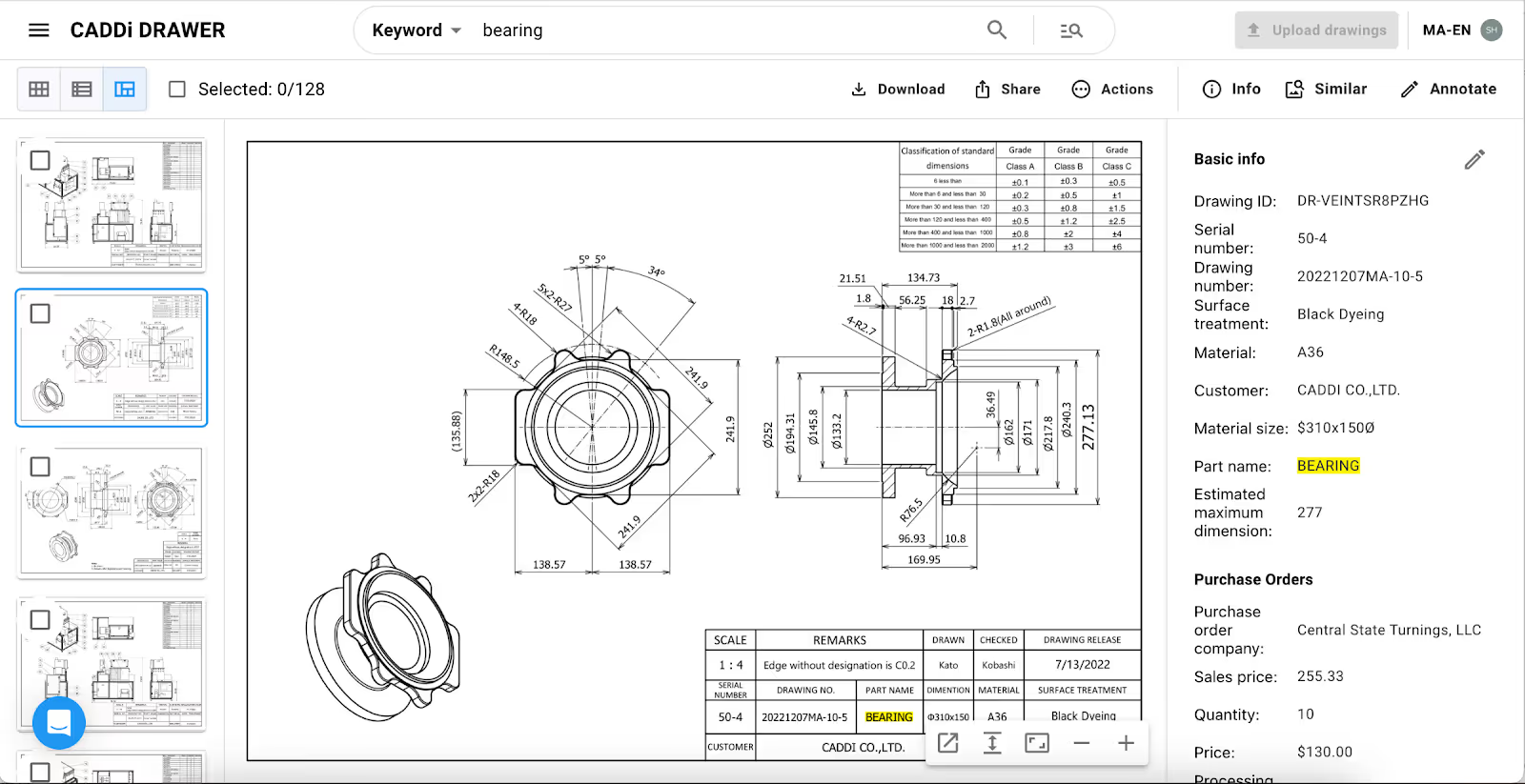
One of the key aspects of CADDi Drawer that supports continuous improvement is its collaborative capabilities. In manufacturing, the ability to quickly share and review designs and specifications can significantly speed up the iteration process. CADDi Drawer allows for seamless collaboration among teams, regardless of their physical location, fostering an environment where feedback is rapidly integrated, and improvements are continuously implemented. This feature is crucial for manufacturers aiming to refine their processes and products steadily over time, as it ensures that all stakeholders can contribute to the enhancement of quality and efficiency.
Ready to see CADDi Drawer in action? Get a personalized demo.
Subscribe to our Blog!
Related Resources
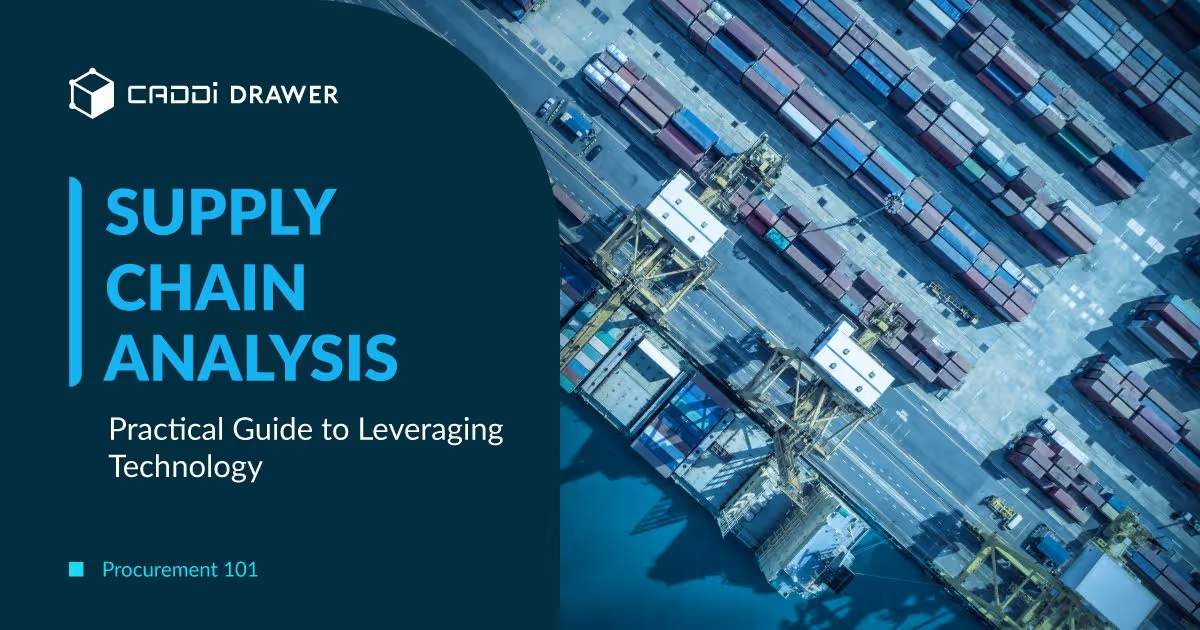
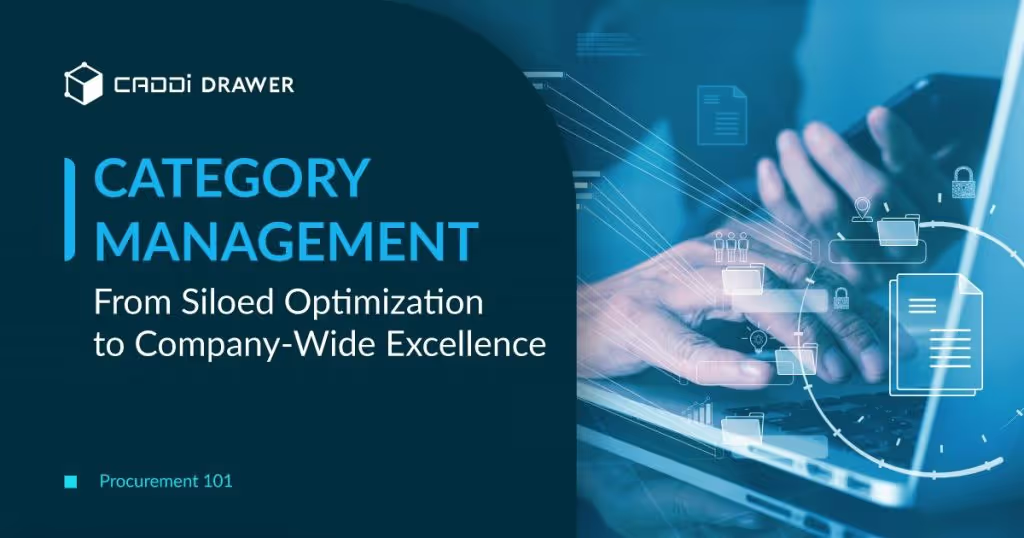

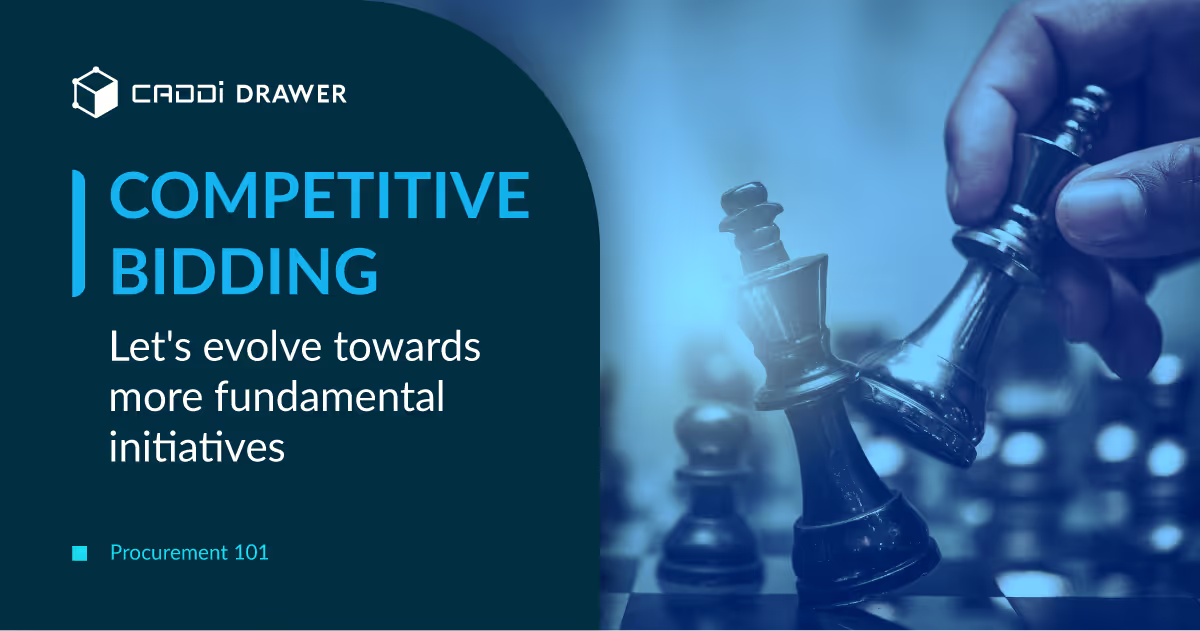
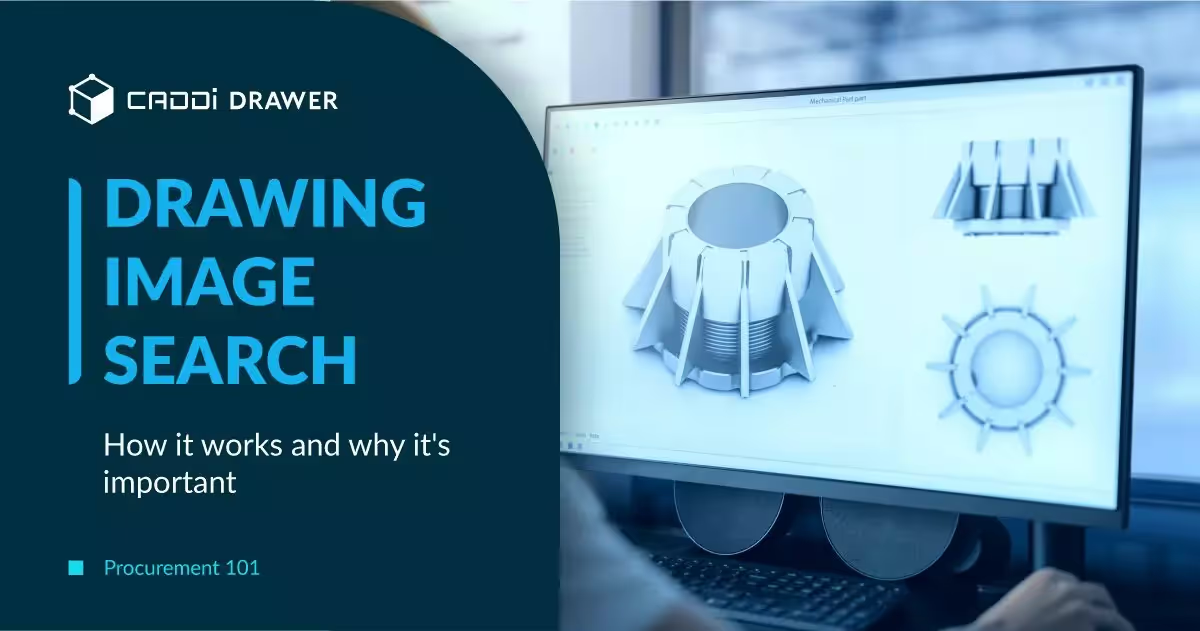
