From Good to Great: Elevating Your Processes with Continuous Improvement in Manufacturing
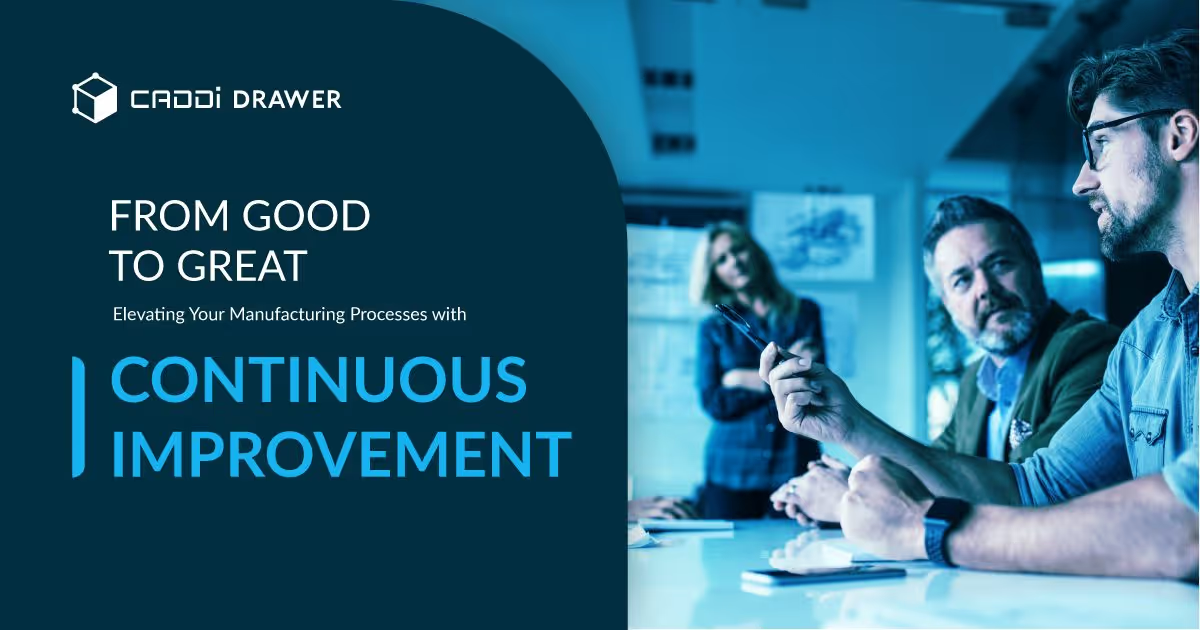
Table of Contents
Continuous improvement in manufacturing, deeply rooted in the philosophy of Kaizen, focuses on making small, incremental changes that cumulatively lead to significant improvements in efficiency, waste reduction, and profitability. Adopting a continuous improvement mindset is crucial for staying competitive in an ever-evolving market landscape, where customer expectations rise and technological advancements continuously reshape production methodologies.
The Philosophy of Continuous Improvement
At the heart of continuous improvement in manufacturing is the Japanese concept of Kaizen. Kaizen is all about small, consistent changes that lead to major improvements in standardized work over time. This philosophy not only focuses on manufacturing processes but extends to all areas of the business, encouraging a culture where every employee is actively seeking ways to improve their work.
Another foundational element is lean manufacturing, a systematic method for waste minimization without sacrificing productivity. Lean principles are deeply intertwined with continuous improvement, emphasizing efficiency, waste reduction, and the value of understanding customer needs to deliver high-quality products efficiently.
These philosophies underpin a variety of strategies aimed at fostering an environment of ongoing progress and development. By embracing these philosophies, manufacturers set the stage for implementing more structured continuous improvement strategies, which we will explore in the next sections.
Strategies for Continuous Improvement in Manufacturing
Total Quality Management (TQM)
TQM is a holistic approach that focuses on long-term success through customer satisfaction. In a TQM effort, all members of an organization participate in improving processes, products, services, and the culture in which they work. The benefits of TQM include improved quality of products and services, higher employee morale, and reduced costs through the elimination of waste and inefficiency.
However, challenges can arise from the extensive cultural shift required, the need for long-term commitment, and the potential for initial implementation costs to be high. This is why an organization and its members must fully commit to Total Quality Management implementation.
Six Sigma
Six Sigma is a data-driven approach aimed at reducing defects and improving quality. By applying statistical methods to identify and eliminate causes of errors, Six Sigma focuses on achieving near-perfection in manufacturing output. The benefits include significant reductions in process variability, improved product quality, increased customer satisfaction, and cost savings.
Nevertheless, the challenges include the need for specialized training, potential resistance to change, and the requirement for a significant investment of time and resources to implement effectively.
5S System
The 5S System, originating from five Japanese terms starting with ‘S’ (Seiri, Seiton, Seiso, Seiketsu, and Shitsuke, or Sort, Set in Order, Shne, Standardize, and Sustain), focuses on workplace organization and standardization. The principles encourage a clean, organized, and efficient workspace that improves productivity and safety. Benefits of the 5S System include a more organized workplace, reduced waste, improved safety, and increased efficiency. However, there are challenges in implementation, including maintaining consistency and commitment from all employees and the initial time investment needed to implement the system fully.
PDCA Cycle (Plan-Do-Check-Act)
The PDCA Cycle is a four-step model for carrying out change. This iterative process involves planning the change (Plan), implementing the change (Do), observing the results (Check), and institutionalizing the change if successful (Act). The PDCA Cycle promotes continuous improvement by facilitating a systematic approach to problem-solving and process improvements.
Benefits include the ability to quickly adapt to changes, continuous feedback for improvements, and enhanced problem-solving capabilities. The challenges, however, may include the potential for complacency in the ‘Act’ phase and the need for ongoing management support and employee engagement.
Integrating Technology for Continuous Improvement in Manufacturing
In the modern manufacturing landscape, technology plays a pivotal role in driving continuous improvement. Enterprise Resource Planning (ERP) systems streamline operations, providing real-time data used to make informed decisions, improve processes, and reduce costs. Additionally, the Internet of Things (IoT) and Artificial Intelligence technologies offer unprecedented opportunities for optimizing manufacturing operations.
These technologies can predict maintenance needs, automate quality control, and enhance operational efficiency. The challenge lies in the investment required, both in terms of finances and the need to train employees, but the potential benefits for efficiency and competitiveness are immense.
Case Study: Successful Continuous Improvement in Manufacturing Example
One of the most notable examples of successful continuous improvement in manufacturing is Toyota’s implementation of the Toyota Production System (TPS). By integrating lean manufacturing principles and the Kaizen approach, Toyota significantly reduced waste and improved productivity. This system not only enhanced their operational efficiency but also became a model for continuous improvement globally.
The key to their success was committing to a culture of continuous improvement, where every employee is empowered to contribute to process enhancements.
How to get a step up with CADDi Drawer
CADDi Drawer represents a significant leap forward in the continuous improvement initiatives within the manufacturing sector, particularly in the realms of procurement and drawing management.
Streamline activities in the procurement and manufacturing process
The following features enable you to streamline the time-consuming tasks of data collection and organization in procurement and manufacturing operations.
- Cost data, supplier information, spec documents and manufacturing work instructions link automatically to each drawing and can also be exported together.
- By using keyword searches combined with similarity searches, the time spent searching for drawings and data in procurement tasks can be reduced.
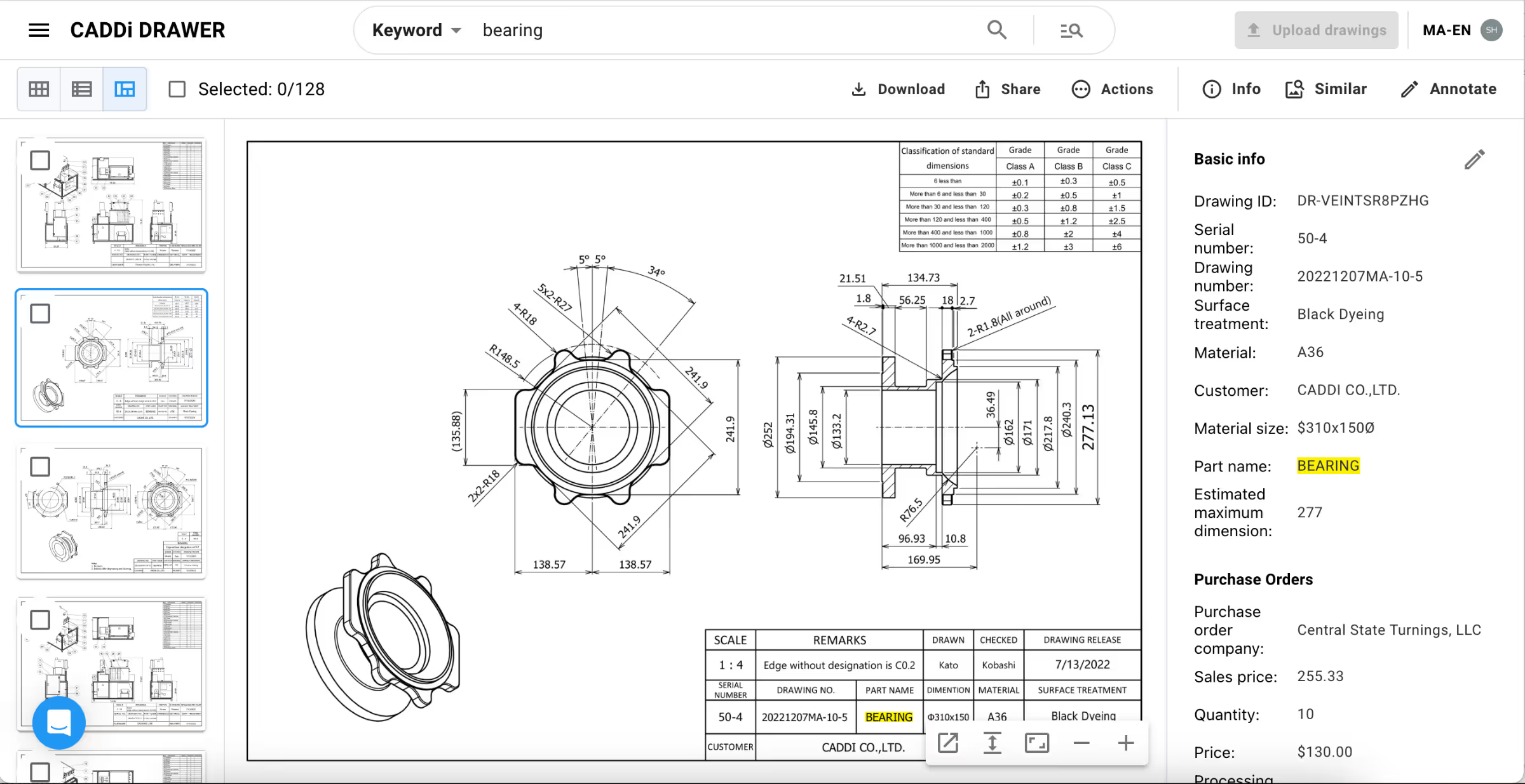
One of the key aspects of CADDi Drawer that supports continuous improvement is its collaborative capabilities. In manufacturing, the ability to quickly share and review designs and specifications can significantly speed up the iteration process. CADDi Drawer allows for seamless collaboration among teams, regardless of their physical location, fostering an environment where feedback is rapidly integrated, and improvements are continuously implemented. This feature is crucial for manufacturers aiming to refine their processes and products steadily over time, as it ensures that all stakeholders can contribute to the enhancement of quality and efficiency.
Continuous improvement in manufacturing, deeply rooted in the philosophy of Kaizen, focuses on making small, incremental changes that cumulatively lead to significant improvements in efficiency, waste reduction, and profitability. Adopting a continuous improvement mindset is crucial for staying competitive in an ever-evolving market landscape, where customer expectations rise and technological advancements continuously reshape production methodologies.
The Philosophy of Continuous Improvement
At the heart of continuous improvement in manufacturing is the Japanese concept of Kaizen. Kaizen is all about small, consistent changes that lead to major improvements in standardized work over time. This philosophy not only focuses on manufacturing processes but extends to all areas of the business, encouraging a culture where every employee is actively seeking ways to improve their work.
Another foundational element is lean manufacturing, a systematic method for waste minimization without sacrificing productivity. Lean principles are deeply intertwined with continuous improvement, emphasizing efficiency, waste reduction, and the value of understanding customer needs to deliver high-quality products efficiently.
These philosophies underpin a variety of strategies aimed at fostering an environment of ongoing progress and development. By embracing these philosophies, manufacturers set the stage for implementing more structured continuous improvement strategies, which we will explore in the next sections.
Strategies for Continuous Improvement in Manufacturing
Total Quality Management (TQM)
TQM is a holistic approach that focuses on long-term success through customer satisfaction. In a TQM effort, all members of an organization participate in improving processes, products, services, and the culture in which they work. The benefits of TQM include improved quality of products and services, higher employee morale, and reduced costs through the elimination of waste and inefficiency.
However, challenges can arise from the extensive cultural shift required, the need for long-term commitment, and the potential for initial implementation costs to be high. This is why an organization and its members must fully commit to Total Quality Management implementation.
Six Sigma
Six Sigma is a data-driven approach aimed at reducing defects and improving quality. By applying statistical methods to identify and eliminate causes of errors, Six Sigma focuses on achieving near-perfection in manufacturing output. The benefits include significant reductions in process variability, improved product quality, increased customer satisfaction, and cost savings.
Nevertheless, the challenges include the need for specialized training, potential resistance to change, and the requirement for a significant investment of time and resources to implement effectively.
5S System
The 5S System, originating from five Japanese terms starting with ‘S’ (Seiri, Seiton, Seiso, Seiketsu, and Shitsuke, or Sort, Set in Order, Shne, Standardize, and Sustain), focuses on workplace organization and standardization. The principles encourage a clean, organized, and efficient workspace that improves productivity and safety. Benefits of the 5S System include a more organized workplace, reduced waste, improved safety, and increased efficiency. However, there are challenges in implementation, including maintaining consistency and commitment from all employees and the initial time investment needed to implement the system fully.
PDCA Cycle (Plan-Do-Check-Act)
The PDCA Cycle is a four-step model for carrying out change. This iterative process involves planning the change (Plan), implementing the change (Do), observing the results (Check), and institutionalizing the change if successful (Act). The PDCA Cycle promotes continuous improvement by facilitating a systematic approach to problem-solving and process improvements.
Benefits include the ability to quickly adapt to changes, continuous feedback for improvements, and enhanced problem-solving capabilities. The challenges, however, may include the potential for complacency in the ‘Act’ phase and the need for ongoing management support and employee engagement.
Integrating Technology for Continuous Improvement in Manufacturing
In the modern manufacturing landscape, technology plays a pivotal role in driving continuous improvement. Enterprise Resource Planning (ERP) systems streamline operations, providing real-time data used to make informed decisions, improve processes, and reduce costs. Additionally, the Internet of Things (IoT) and Artificial Intelligence technologies offer unprecedented opportunities for optimizing manufacturing operations.
These technologies can predict maintenance needs, automate quality control, and enhance operational efficiency. The challenge lies in the investment required, both in terms of finances and the need to train employees, but the potential benefits for efficiency and competitiveness are immense.
Case Study: Successful Continuous Improvement in Manufacturing Example
One of the most notable examples of successful continuous improvement in manufacturing is Toyota’s implementation of the Toyota Production System (TPS). By integrating lean manufacturing principles and the Kaizen approach, Toyota significantly reduced waste and improved productivity. This system not only enhanced their operational efficiency but also became a model for continuous improvement globally.
The key to their success was committing to a culture of continuous improvement, where every employee is empowered to contribute to process enhancements.
How to get a step up with CADDi Drawer
CADDi Drawer represents a significant leap forward in the continuous improvement initiatives within the manufacturing sector, particularly in the realms of procurement and drawing management.
Streamline activities in the procurement and manufacturing process
The following features enable you to streamline the time-consuming tasks of data collection and organization in procurement and manufacturing operations.
- Cost data, supplier information, spec documents and manufacturing work instructions link automatically to each drawing and can also be exported together.
- By using keyword searches combined with similarity searches, the time spent searching for drawings and data in procurement tasks can be reduced.
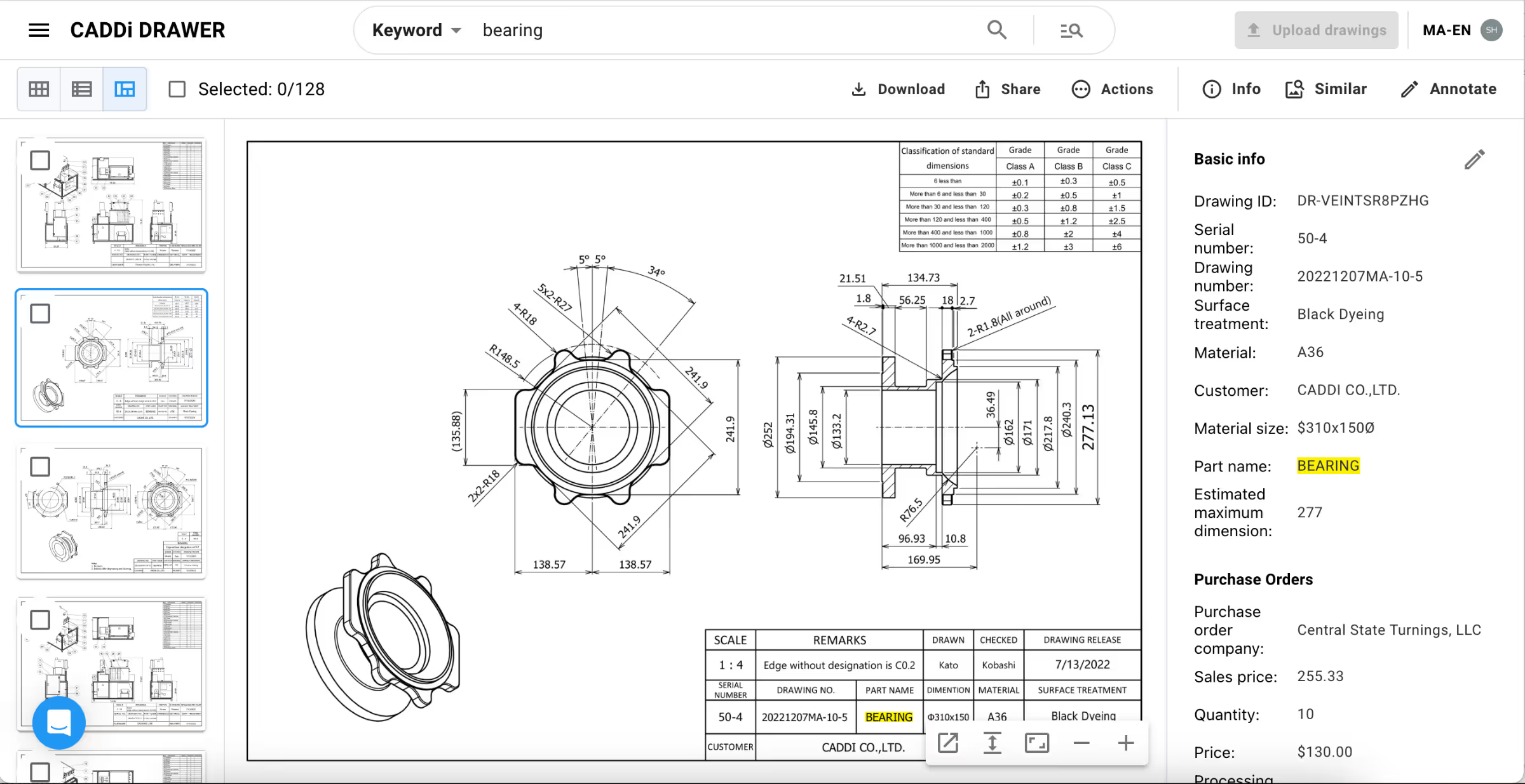
One of the key aspects of CADDi Drawer that supports continuous improvement is its collaborative capabilities. In manufacturing, the ability to quickly share and review designs and specifications can significantly speed up the iteration process. CADDi Drawer allows for seamless collaboration among teams, regardless of their physical location, fostering an environment where feedback is rapidly integrated, and improvements are continuously implemented. This feature is crucial for manufacturers aiming to refine their processes and products steadily over time, as it ensures that all stakeholders can contribute to the enhancement of quality and efficiency.
Ready to see CADDi Drawer in action? Get a personalized demo.
Subscribe to our Blog!
Related Resources
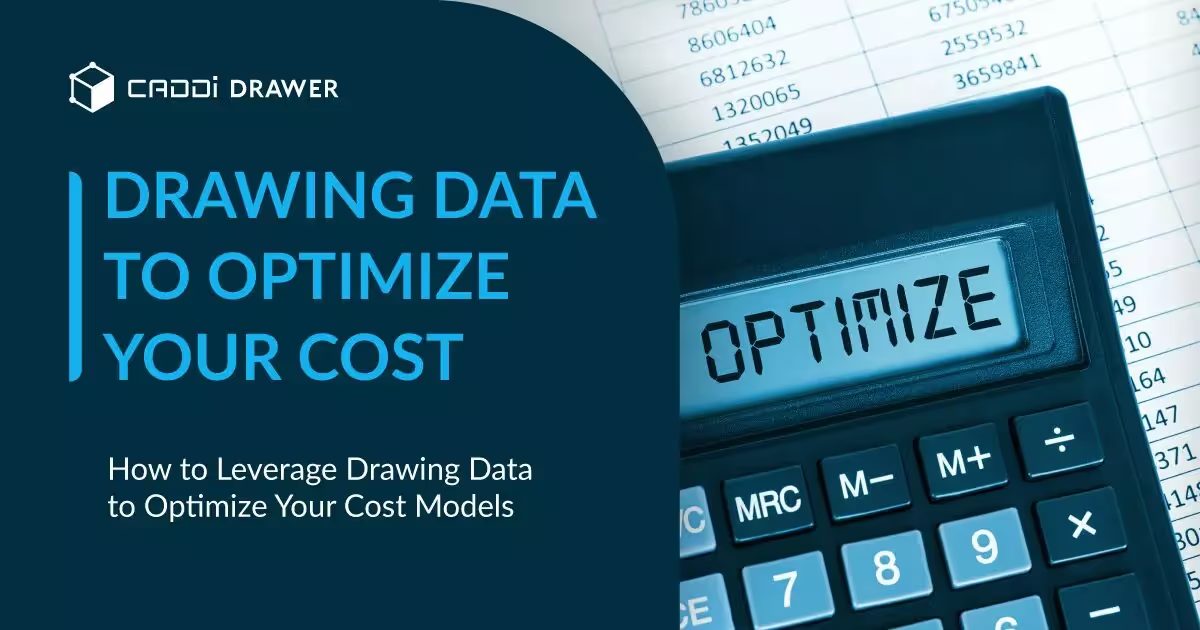
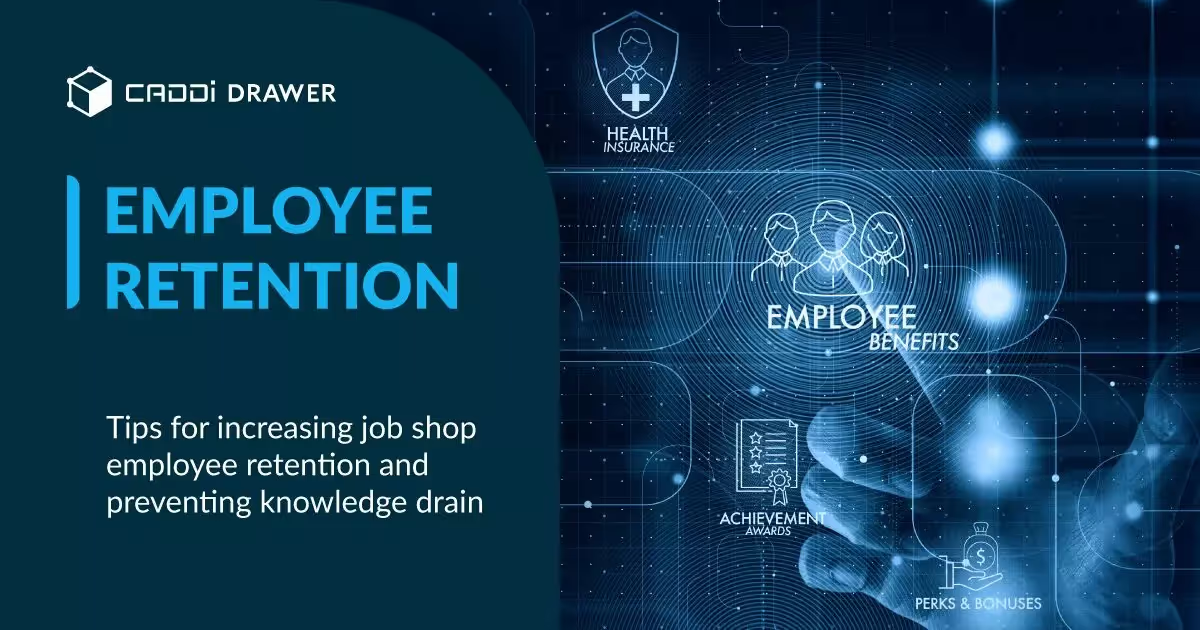
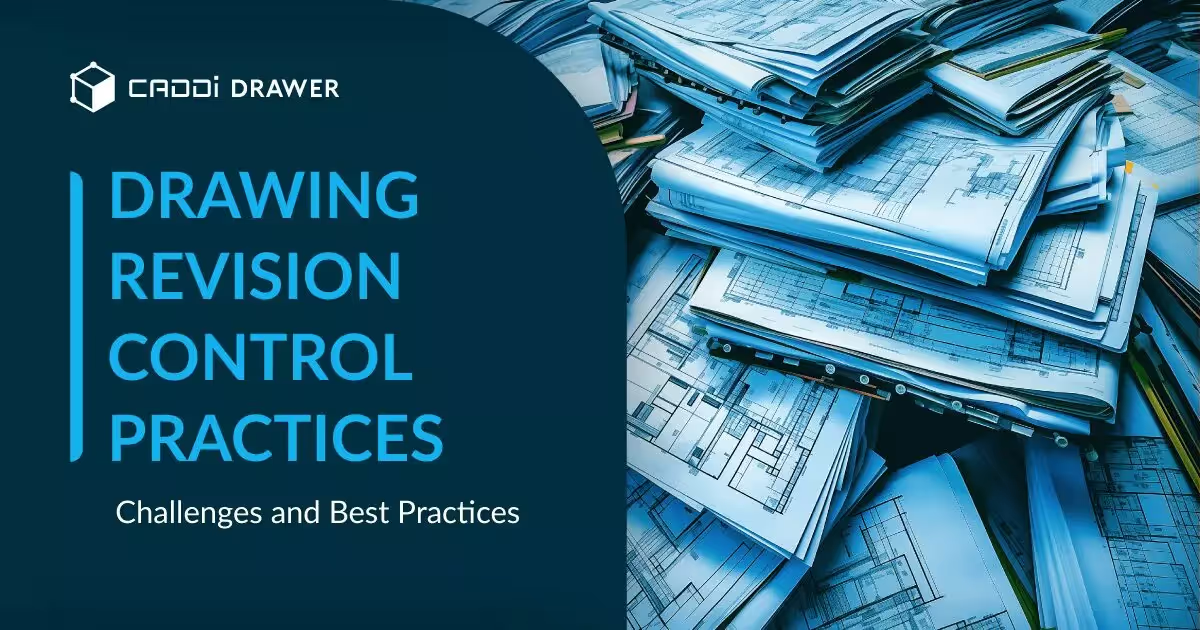
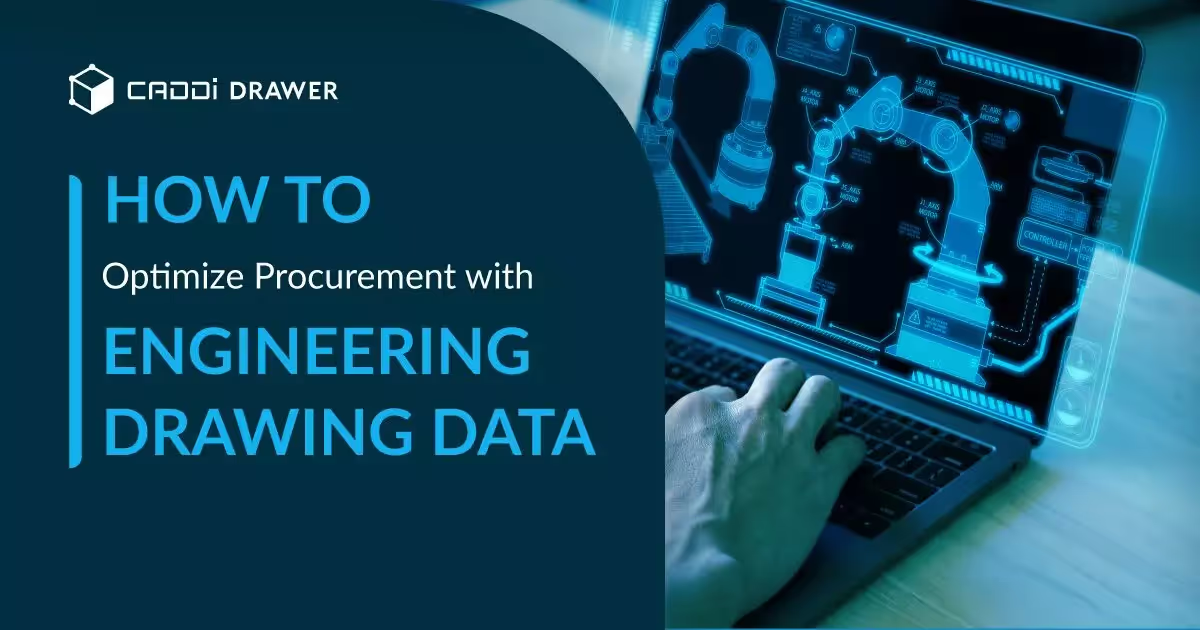
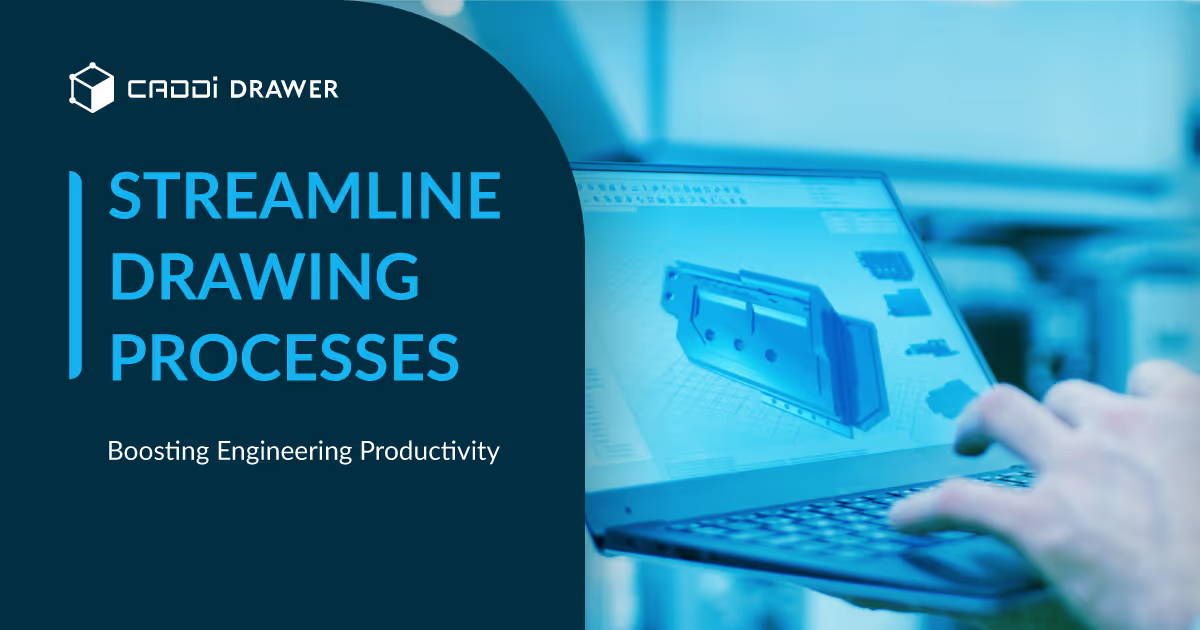
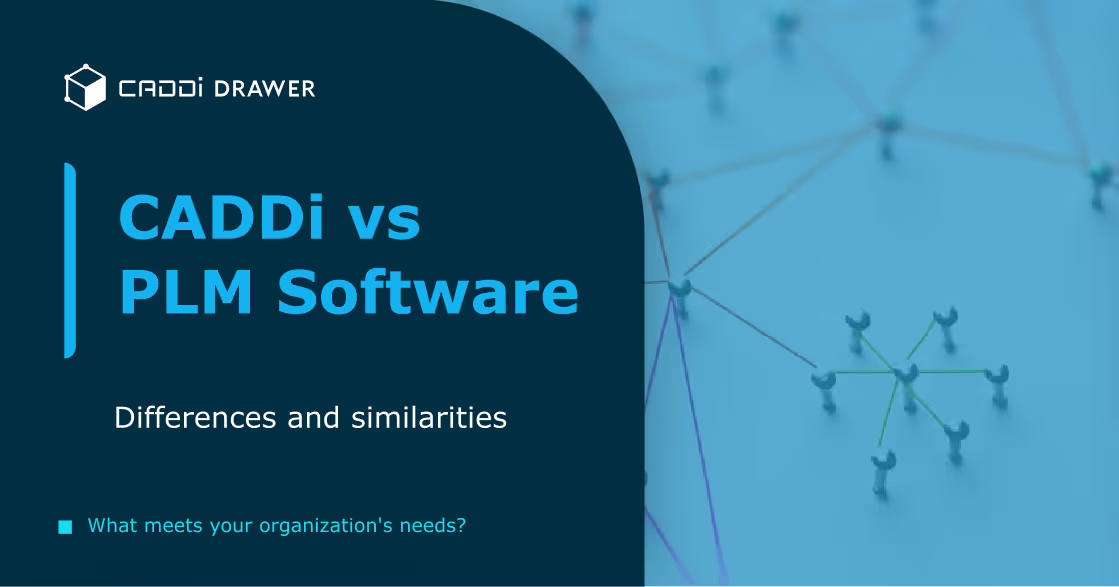