How to Leverage Drawing Data to Optimize Your Cost Models
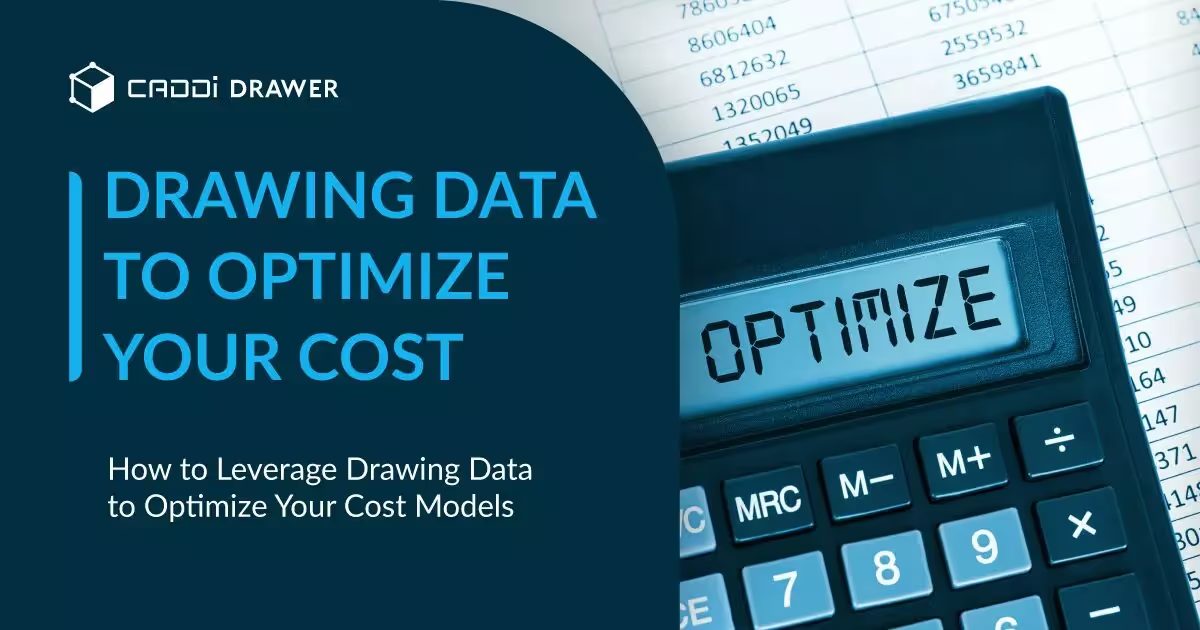
Table of Contents
Introduction to Cost Modeling
Cost modeling is the process of estimating and predicting the total costs associated with designing, developing, and manufacturing a product. It is a crucial step in product development and engineering, allowing companies to evaluate the financial viability of a potential new product before investing significant resources into bringing it to market.
In manufacturing and engineering, accurate cost modeling provides many benefits. It helps companies determine if a proposed product will be profitable to produce based on projected revenues and expenses. Cost modeling enables comparison of design alternatives, materials, and manufacturing methods to find the most cost-effective option. It also aids in setting the appropriate pricing for a product and identifying opportunities to reduce costs through design changes or process improvements.
Overall, cost modeling provides vital information for making informed business decisions about product development, budgeting, and resource allocation. As products become more complex, with thousands of parts and long global supply chains, detailed and reliable cost modeling is increasingly critical for companies to remain competitive.
Now let’s examine how drawing data can be utilized for effective cost modeling in product development.
Using Drawing Data for Cost Modeling
Engineering drawings contain a wealth of data that is extremely valuable for developing accurate cost estimates and models. The drawings specify all the key physical details and parameters of the product or system being modeled, including:
- Dimensions – The drawings provide detailed measurements of all components, assemblies, and systems. This allows accurate material quantities to be calculated.
- Materials – The materials for each part are defined on the drawings. This provides the essential input for determining material costs.
- Finishes – Surface finishes such as coatings and polishing, are specified on drawings. This impacts processing and labor costs.
- Tolerances – The dimensional tolerances and geometric tolerances provide manufacturing requirements. Tighter tolerances require more operations and expense.
- Assembly relationships – The drawings illustrate how components fit and operate together. This reveals complexity and assembly costs.
Since the drawings contain comprehensive details for manufacturing the product, they serve as the central source of truth for generating cost estimates. Rather than relying on assumptions or generic data, cost models can be built around the unique specifications contained in the engineering drawings. This allows very accurate and tailored estimates to be developed.
By leveraging the detailed data in the drawings, estimators can account for the precise materials, features, operations and processes needed to produce the product. This minimizes guesswork and provides greater confidence in cost projections. Overall, treating drawings as a vital information source enables superior cost modeling and estimating.
Challenges and Limitations
Extracting data from drawings for cost modeling presents several key challenges:
- Difficulty extracting data automatically: Unlike 3D models, 2D drawings are raster images that make automated data extraction difficult. There is no underlying parametric data to pull from. Complex image recognition and processing is required.
- Variability in drawing styles/standards: Drawings can vary greatly in visual style, layout, notation, dimensions etc. This makes it hard to apply automated techniques reliably across different drawing sets. There is no universal standard that all drawings conform to.
- Keeping drawings and models in sync: Even when data can be extracted from drawings, keeping it synced with 3D models is an ongoing challenge. Drawings and models diverge as they are edited, requiring constant cross-checking and updates to ensure consistency.
Overcoming these limitations requires advanced computer vision techniques, standardized drawing frameworks, and tight version control between 2D and 3D data sets. Cost estimators must carefully evaluate and clean drawing data before usage in models.
Best Practices
Standardizing drawing practices company-wide is critical for creating accurate cost models. All teams should follow consistent conventions for dimensions, notes, layers, and other drawing elements. This makes data extraction and cost estimation more seamless.
Cross-functional collaboration is also key. Engineers, designers, estimators, and project managers should align on modeling needs and drawing standards. With input from multiple disciplines, drawings can capture the right details for costing. Teams should review drawings together before major project milestones.
Automating data extraction from drawings is essential for efficient modeling. Manual data entry is time-consuming and error-prone. New technologies like AI and machine learning can automatically pull dimensions, materials, and other attributes from drawings. This speeds up model creation while minimizing mistakes. As automation improves, companies should invest in tools to enhance drawing-based cost modeling.
Future Outlook
Cost modeling using drawing data has promising developments on the horizon. There are three key areas where we expect to see improvements:
Improving Interoperability Between CAD and Cost Modeling Software
Currently, transferring data between CAD and cost modeling software can be cumbersome. Often it involves exporting drawing data to a neutral format like IFC or CSV, then importing it into the cost modeling software. Better integration between the two types of tools would streamline data transfer and reduce effort. We may see CAD and cost modeling vendors partner to offer tighter connections between their offerings.
However, it’s important to note that the drawing data that can be output from 3D CAD has limitations. Tolerances, metal finishes, and various other data necessary for accurate cost modeling are often not included in the 3D models. In many cases, this detailed information still needs to be gleaned from traditional 2D drawings.
Until 3D CAD tools evolve to comprehensively capture all the manufacturing specs in the model itself, combining 3D CAD output with data from 2D drawings will remain a practical necessity for precise cost estimation. Improving the link between 3D CAD and 2D drawings within CAD software could help streamline this hybrid data gathering approach in the near term.
AI to Automate Data Extraction from Drawings
Extracting cost-relevant data like areas, counts, and materials from drawings is currently a manual process. Emerging AI techniques like computer vision could automate recognizing building elements in drawings and extracting the key data. This would eliminate tedious manual work and reduce errors.
Real-Time Updating of Cost Models
Today, cost models are static snapshots. When the building design changes, cost models must be manually updated. In the future, dynamic links between CAD and cost tools could allow real-time updating of cost models. As soon as a change is made in the CAD software, the cost model is automatically refreshed. This would enable greater agility and confidence in decision making.
Leveraging CADDi Drawer for Drawing-Based Cost Modeling and Benchmarking
CADDi Drawer offers a powerful solution for companies looking to improve their cost modeling with drawing data. By automating data extraction from drawings and connecting this information with existing supply chain data, CADDi Drawer enables a more efficient and accurate approach to cost estimation.
One of the key features of CADDi Drawer is its ability to automatically scan and extract data from PDF drawings, including dimensions, text, and shapes. This eliminates the time-consuming manual process of gathering data from drawings for cost modeling. Even handwritten drawings can be made searchable and comparable, allowing companies to leverage their entire historical drawing archive.
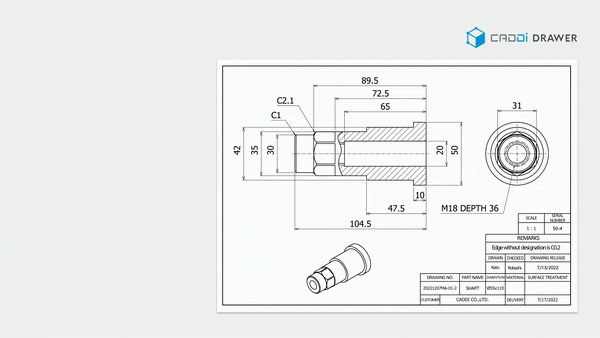
In addition to extracting drawing data, CADDi Drawer allows users to easily connect estimation/quotation and other supply chain data to the associated drawings. This can include cost, quantity, supplier information, sales price, cost breakdowns, and more. By uploading CSV files or integrating with ERP, CAM, CAD, and other systems, all relevant information is linked to the drawings, providing a comprehensive view for cost modeling.
CADDi Drawer’s powerful search capabilities further enhance the cost modeling process. Users can search their entire drawing archive using keywords, including material, size, designer’s name, part name, and notes. The platform’s patented similarity search technology can identify similar drawings based on the shape of each part, even for handwritten drawings from decades ago. This allows cost estimators to quickly find relevant historical data for benchmarking and cost comparison.
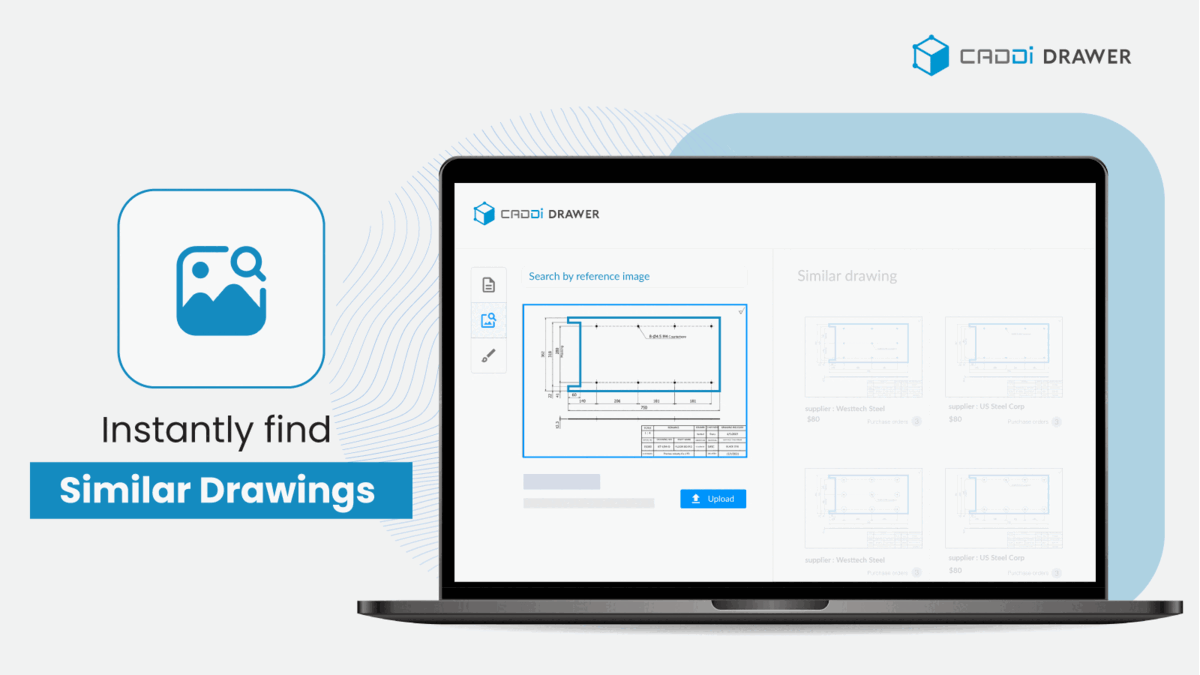
For even greater convenience, CADDi Drawer offers an image search feature that allows users to upload a photo of a sketch or drawing and find the most similar drawings in their archive.
When comparing similar drawings or revisions, CADDi Drawer makes it easy to identify differences with just one click. This streamlines the process of evaluating design changes and their impact on costs.
Finally, CADDi Drawer allows users to download all drawing information, along with associated supplier data, prices, tags, and more, to a CSV file with a single click. This facilitates further analysis and integration with cost modeling tools.
Furthermore, the article below also explains benchmarking using CADDi Drawer as an alternative means of cost analysis, so please be sure to refer to it.
Introduction to Cost Modeling
Cost modeling is the process of estimating and predicting the total costs associated with designing, developing, and manufacturing a product. It is a crucial step in product development and engineering, allowing companies to evaluate the financial viability of a potential new product before investing significant resources into bringing it to market.
In manufacturing and engineering, accurate cost modeling provides many benefits. It helps companies determine if a proposed product will be profitable to produce based on projected revenues and expenses. Cost modeling enables comparison of design alternatives, materials, and manufacturing methods to find the most cost-effective option. It also aids in setting the appropriate pricing for a product and identifying opportunities to reduce costs through design changes or process improvements.
Overall, cost modeling provides vital information for making informed business decisions about product development, budgeting, and resource allocation. As products become more complex, with thousands of parts and long global supply chains, detailed and reliable cost modeling is increasingly critical for companies to remain competitive.
Now let’s examine how drawing data can be utilized for effective cost modeling in product development.
Using Drawing Data for Cost Modeling
Engineering drawings contain a wealth of data that is extremely valuable for developing accurate cost estimates and models. The drawings specify all the key physical details and parameters of the product or system being modeled, including:
- Dimensions – The drawings provide detailed measurements of all components, assemblies, and systems. This allows accurate material quantities to be calculated.
- Materials – The materials for each part are defined on the drawings. This provides the essential input for determining material costs.
- Finishes – Surface finishes such as coatings and polishing, are specified on drawings. This impacts processing and labor costs.
- Tolerances – The dimensional tolerances and geometric tolerances provide manufacturing requirements. Tighter tolerances require more operations and expense.
- Assembly relationships – The drawings illustrate how components fit and operate together. This reveals complexity and assembly costs.
Since the drawings contain comprehensive details for manufacturing the product, they serve as the central source of truth for generating cost estimates. Rather than relying on assumptions or generic data, cost models can be built around the unique specifications contained in the engineering drawings. This allows very accurate and tailored estimates to be developed.
By leveraging the detailed data in the drawings, estimators can account for the precise materials, features, operations and processes needed to produce the product. This minimizes guesswork and provides greater confidence in cost projections. Overall, treating drawings as a vital information source enables superior cost modeling and estimating.
Challenges and Limitations
Extracting data from drawings for cost modeling presents several key challenges:
- Difficulty extracting data automatically: Unlike 3D models, 2D drawings are raster images that make automated data extraction difficult. There is no underlying parametric data to pull from. Complex image recognition and processing is required.
- Variability in drawing styles/standards: Drawings can vary greatly in visual style, layout, notation, dimensions etc. This makes it hard to apply automated techniques reliably across different drawing sets. There is no universal standard that all drawings conform to.
- Keeping drawings and models in sync: Even when data can be extracted from drawings, keeping it synced with 3D models is an ongoing challenge. Drawings and models diverge as they are edited, requiring constant cross-checking and updates to ensure consistency.
Overcoming these limitations requires advanced computer vision techniques, standardized drawing frameworks, and tight version control between 2D and 3D data sets. Cost estimators must carefully evaluate and clean drawing data before usage in models.
Best Practices
Standardizing drawing practices company-wide is critical for creating accurate cost models. All teams should follow consistent conventions for dimensions, notes, layers, and other drawing elements. This makes data extraction and cost estimation more seamless.
Cross-functional collaboration is also key. Engineers, designers, estimators, and project managers should align on modeling needs and drawing standards. With input from multiple disciplines, drawings can capture the right details for costing. Teams should review drawings together before major project milestones.
Automating data extraction from drawings is essential for efficient modeling. Manual data entry is time-consuming and error-prone. New technologies like AI and machine learning can automatically pull dimensions, materials, and other attributes from drawings. This speeds up model creation while minimizing mistakes. As automation improves, companies should invest in tools to enhance drawing-based cost modeling.
Future Outlook
Cost modeling using drawing data has promising developments on the horizon. There are three key areas where we expect to see improvements:
Improving Interoperability Between CAD and Cost Modeling Software
Currently, transferring data between CAD and cost modeling software can be cumbersome. Often it involves exporting drawing data to a neutral format like IFC or CSV, then importing it into the cost modeling software. Better integration between the two types of tools would streamline data transfer and reduce effort. We may see CAD and cost modeling vendors partner to offer tighter connections between their offerings.
However, it’s important to note that the drawing data that can be output from 3D CAD has limitations. Tolerances, metal finishes, and various other data necessary for accurate cost modeling are often not included in the 3D models. In many cases, this detailed information still needs to be gleaned from traditional 2D drawings.
Until 3D CAD tools evolve to comprehensively capture all the manufacturing specs in the model itself, combining 3D CAD output with data from 2D drawings will remain a practical necessity for precise cost estimation. Improving the link between 3D CAD and 2D drawings within CAD software could help streamline this hybrid data gathering approach in the near term.
AI to Automate Data Extraction from Drawings
Extracting cost-relevant data like areas, counts, and materials from drawings is currently a manual process. Emerging AI techniques like computer vision could automate recognizing building elements in drawings and extracting the key data. This would eliminate tedious manual work and reduce errors.
Real-Time Updating of Cost Models
Today, cost models are static snapshots. When the building design changes, cost models must be manually updated. In the future, dynamic links between CAD and cost tools could allow real-time updating of cost models. As soon as a change is made in the CAD software, the cost model is automatically refreshed. This would enable greater agility and confidence in decision making.
Leveraging CADDi Drawer for Drawing-Based Cost Modeling and Benchmarking
CADDi Drawer offers a powerful solution for companies looking to improve their cost modeling with drawing data. By automating data extraction from drawings and connecting this information with existing supply chain data, CADDi Drawer enables a more efficient and accurate approach to cost estimation.
One of the key features of CADDi Drawer is its ability to automatically scan and extract data from PDF drawings, including dimensions, text, and shapes. This eliminates the time-consuming manual process of gathering data from drawings for cost modeling. Even handwritten drawings can be made searchable and comparable, allowing companies to leverage their entire historical drawing archive.
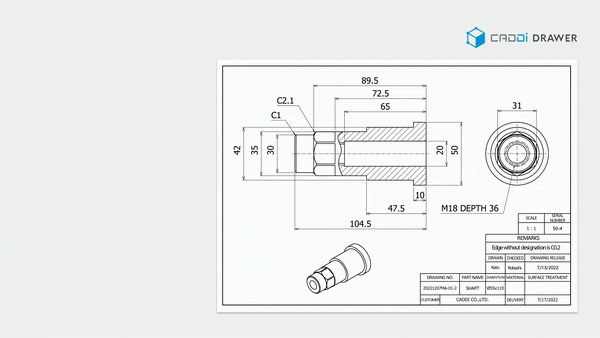
In addition to extracting drawing data, CADDi Drawer allows users to easily connect estimation/quotation and other supply chain data to the associated drawings. This can include cost, quantity, supplier information, sales price, cost breakdowns, and more. By uploading CSV files or integrating with ERP, CAM, CAD, and other systems, all relevant information is linked to the drawings, providing a comprehensive view for cost modeling.
CADDi Drawer’s powerful search capabilities further enhance the cost modeling process. Users can search their entire drawing archive using keywords, including material, size, designer’s name, part name, and notes. The platform’s patented similarity search technology can identify similar drawings based on the shape of each part, even for handwritten drawings from decades ago. This allows cost estimators to quickly find relevant historical data for benchmarking and cost comparison.
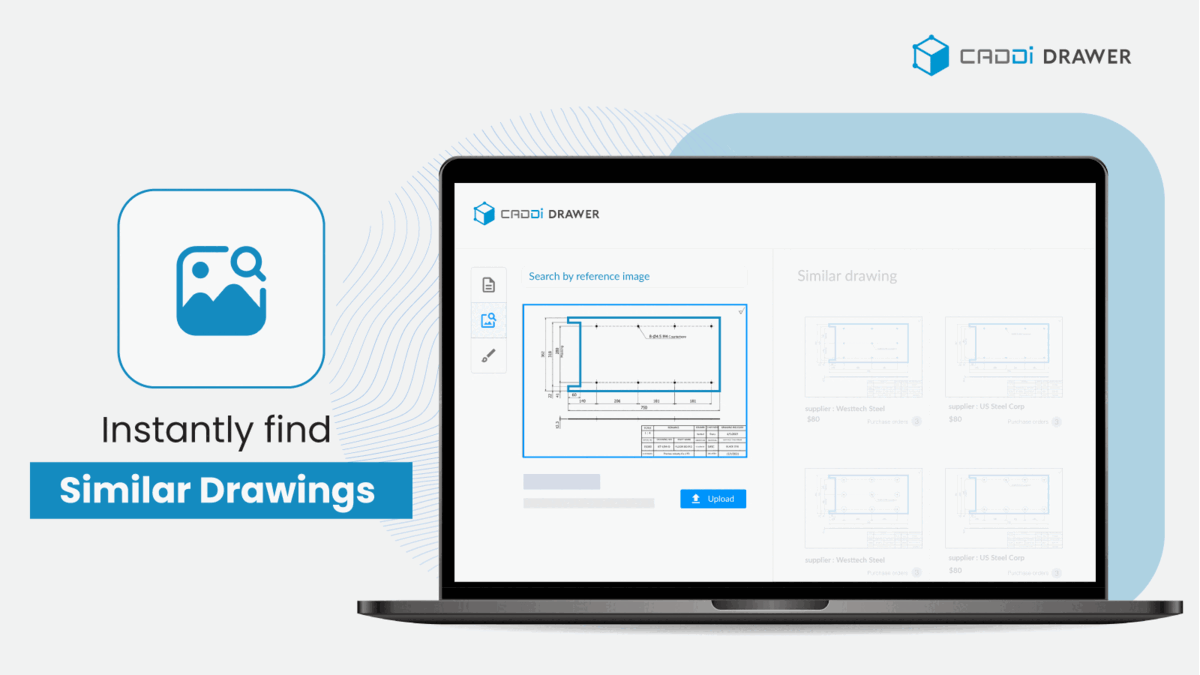
For even greater convenience, CADDi Drawer offers an image search feature that allows users to upload a photo of a sketch or drawing and find the most similar drawings in their archive.
When comparing similar drawings or revisions, CADDi Drawer makes it easy to identify differences with just one click. This streamlines the process of evaluating design changes and their impact on costs.
Finally, CADDi Drawer allows users to download all drawing information, along with associated supplier data, prices, tags, and more, to a CSV file with a single click. This facilitates further analysis and integration with cost modeling tools.
Furthermore, the article below also explains benchmarking using CADDi Drawer as an alternative means of cost analysis, so please be sure to refer to it.
Ready to see CADDi Drawer in action? Get a personalized demo.
Subscribe to our Blog!
Related Resources
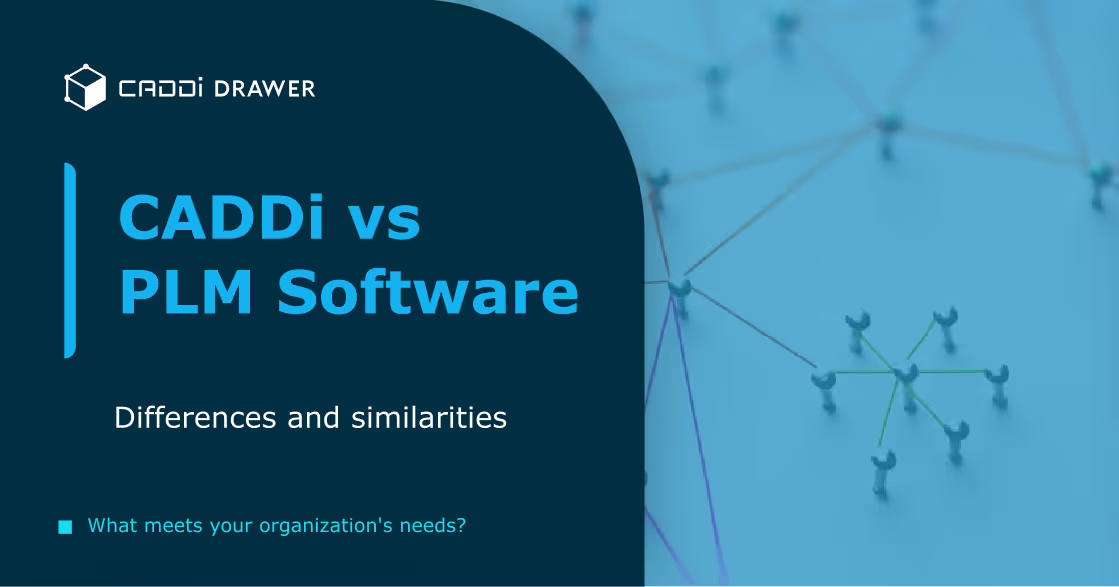

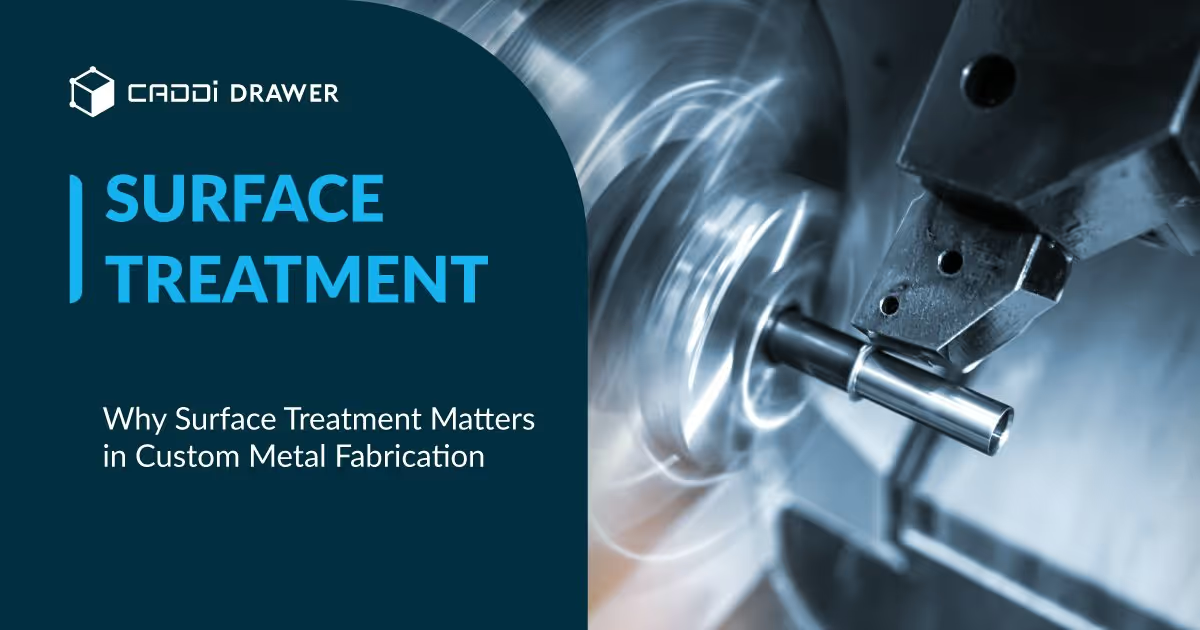
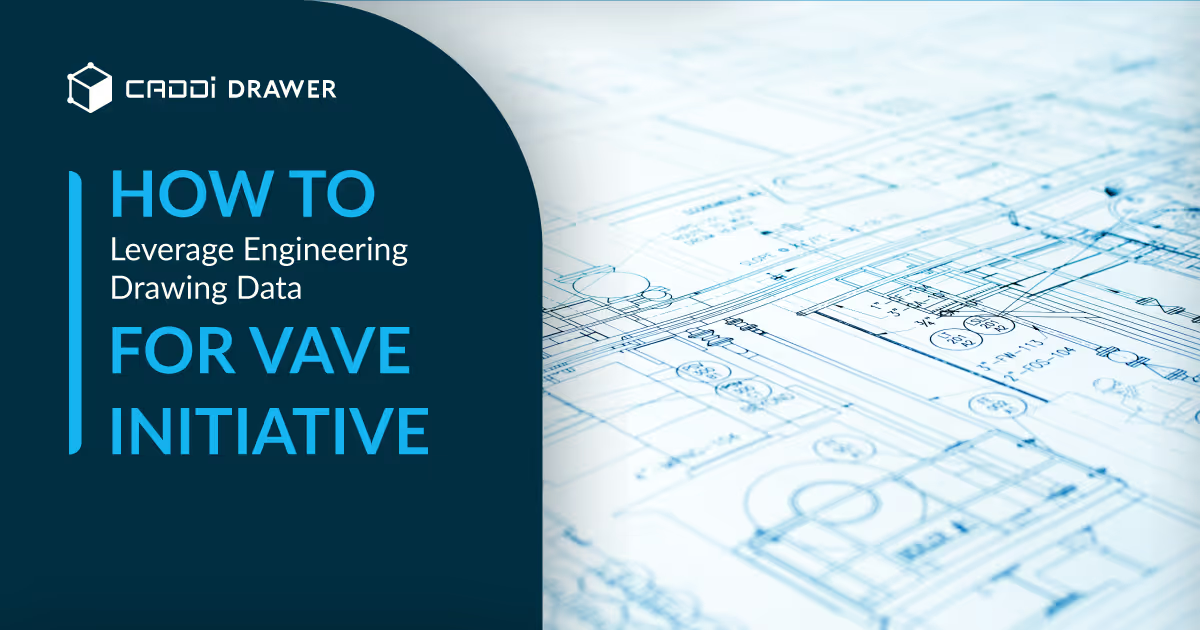
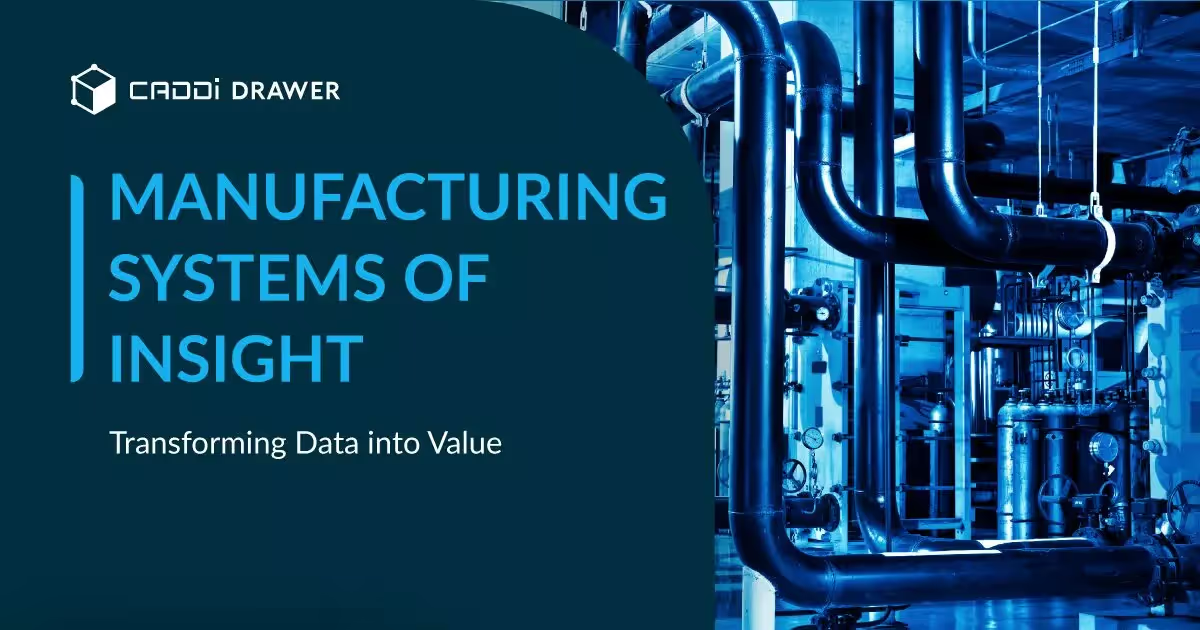
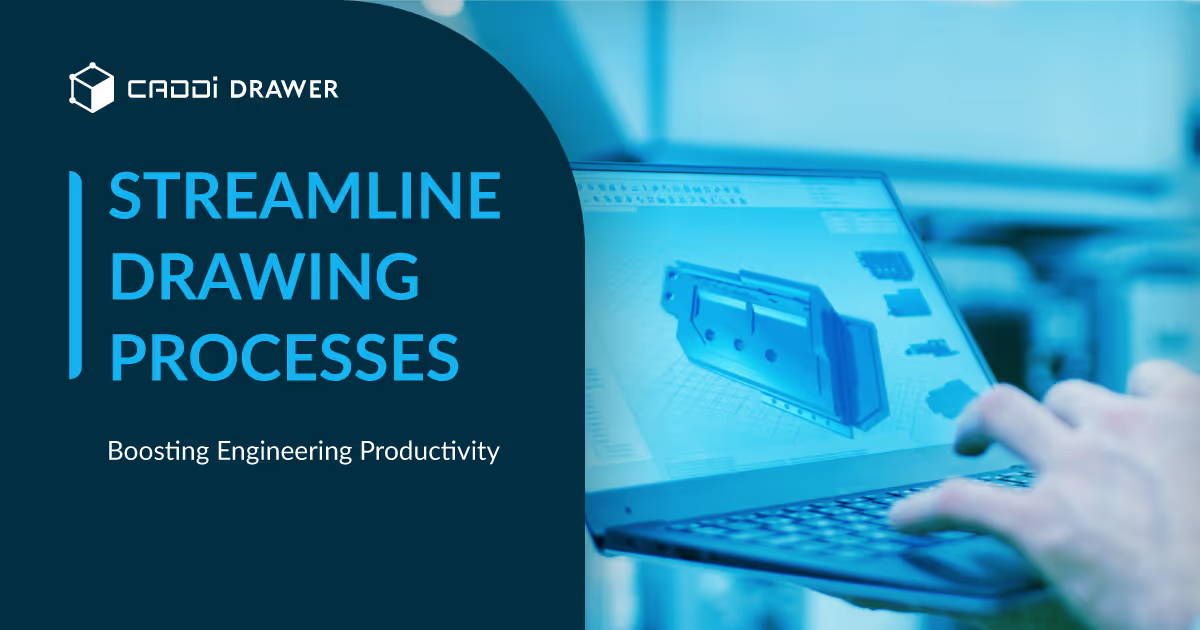