Why Surface Treatment Matters in Custom Metal Fabrication
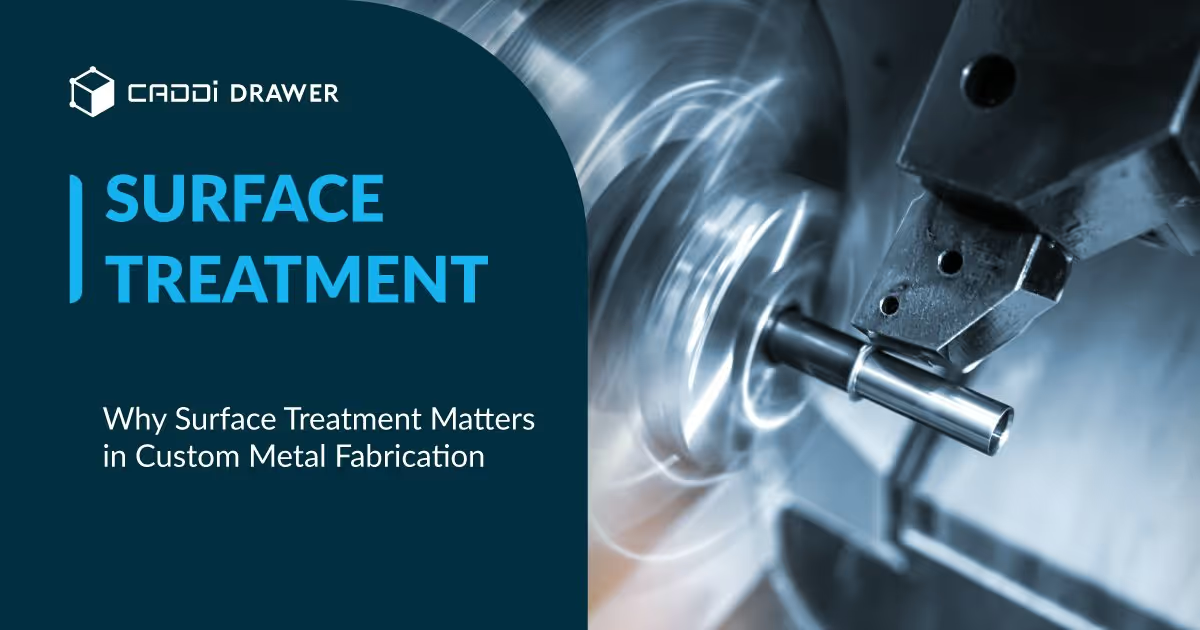
Table of Contents
Introduction
In the world of custom metal fabrication, surface treatment plays a critical role in determining the quality, performance, and longevity of the finished product. From aerospace and automotive to medical and industrial applications, the demands placed on metal parts are becoming increasingly stringent, and achieving these requirements all starts with the surface.
The surface of a metal part is where many of the critical properties that determine its performance and durability are established. That’s why surface treatment is so important – it’s the process of modifying and enhancing the surface to meet specific requirements and improve overall quality and reliability.
However, surface treatment is not a one-size-fits-all process. There are a wide range of options available, each with its own advantages, limitations, and applications, as described in another article about metal finishing. The choice depends on factors such as the base material, end-use environment, and specific performance requirements of the part.
To further complicate matters, many manufacturers and custom metal fabricators choose to outsource their surface treatment processes to specialized providers. While this can offer benefits like access to advanced equipment and expertise, it also introduces new challenges and risks that must be carefully managed to ensure consistent quality.
In this article, we will explore the critical role of surface treatment in custom metal fabrication and discuss the key challenges and best practices for ensuring high-quality, reliable results.
Challenges in assuring quality of surface treatment of metal parts
Achieving the perfect finish is no easy feat, especially when outsourcing the process to third-party providers. Surface treatment is a complex process with numerous variables and potential failure modes that can impact the quality and consistency of the finished parts.
The complexities of outsourcing
Outsourcing surface treatment can offer many benefits, such as access to specialized expertise, advanced equipment, and cost savings. However, it also introduces a new set of challenges and potential failure modes that can compromise the quality and consistency of the finished parts.
Common issues that can arise when outsourcing surface treatment include:
- Miscommunication of specifications and requirements leading to non-conforming parts
- Lack of process control and variability in the surface treatment parameters
- Extended lead times and reduced flexibility to accommodate changes or rush orders
- Limited visibility and difficulty in identifying and resolving quality issues quickly
- Potential risk of intellectual property loss or compromise, particularly for sensitive applications
To mitigate these risks, it’s crucial to select a surface treatment partner with a proven track record of quality, reliability, and expertise in the specific processes and applications required. However, even with a carefully vetted partner, outsourcing adds an extra layer of complexity that requires robust quality control measures and close collaboration.
The multitude of variables and failure modes
Surface treatment encompasses a wide range of processes, each with its own set of critical variables and potential failure modes. From pre-treatment steps like cleaning and masking to the actual coating or plating processes and post-treatment operations, there are numerous factors that can impact the quality and performance of the finished parts.
For example, in the case of electroplating, common failures can include:
- Poor adhesion and delamination of the plating due to improper cleaning or surface preparation
- Uneven plating thickness and coverage due to incorrect current density or part orientation
- Rough or pitted surface finish due to contamination or incorrect additive levels in the plating bath
- Hydrogen embrittlement leading to reduced ductility and premature failure, particularly in high-strength steel parts
Similarly, in powder coating, common issues can include:
- Orange peel or textured surface finish due to incorrect powder application or curing parameters
- Pinholing or outgassing defects due to improper pretreatment or contamination on the part surface
- Color variations or inconsistency due to changes in the powder composition or application process
- Reduced corrosion resistance or coating durability due to insufficient film thickness or cure
The human factor
In addition to the technical complexities of surface treatment, the human factor plays a critical role in ensuring consistent quality. The success of the process ultimately depends on the skill, knowledge, and attention to detail of the operators, technicians, and quality control personnel involved.
In outsourcing arrangements, the lack of direct control over the personnel performing the surface treatment can introduce additional risks. Common issues can include:
- Insufficient training or lack of experience with the specific processes or applications required
- High turnover or frequent changes in personnel leading to inconsistency in the process
- Lack of accountability or ownership for quality due to diffused responsibility across multiple organizations
- Cultural or language barriers that can hinder effective communication and problem-solving
Selecting the right surface treatment partner
When it comes to outsourcing surface treatment, choosing the right partner is critical. Just as you wouldn’t trust your precision aerospace components to a general machine shop, you shouldn’t trust your metal parts to just any surface treatment provider.
But with so many options out there, how can you separate the true experts from the rest? How can you find a partner that will deliver the quality, consistency, and reliability you need to succeed in today’s competitive market?
Understand your specific requirements
The first step in selecting a surface treatment partner is to have a clear understanding of your own unique requirements. This goes beyond just knowing whether you need plating, anodizing, or coating – it means diving into the details of your specific application.
Consider factors like:
- The base material and geometry of your parts
- The environmental conditions the parts will be exposed to
- Any regulatory or industry standards that must be met
- Specific performance requirements for corrosion resistance, wear resistance, conductivity, etc.
The more specific you can be about your needs, the better equipped you’ll be to find a partner that can meet them. It’s like choosing a surgeon – you wouldn’t just look for a general practitioner, you’d want a specialist with experience in your specific procedure.
Evaluate technical expertise and capabilities
Once you have a clear idea of what you need, it’s time to start evaluating potential partners based on their technical expertise and capabilities. Look for providers that have:
- Proven experience with your specific type of surface treatment and base material
- State-of-the-art equipment and facilities that are properly maintained and calibrated
- Rigorous quality control processes, including ISO certifications and regular audits
- A team of skilled technicians and engineers with ongoing training and development
Don’t hesitate to ask for detailed information about their processes, equipment, and personnel. A true expert will be happy to share their knowledge and demonstrate their capabilities.
Establish clear specifications and expectations
Once you’ve selected a surface treatment partner, it’s essential to establish clear specifications and expectations upfront. This includes:
- Detailed drawings and 3D models of your parts
- Specific requirements for coating thickness, hardness, adhesion, appearance, etc.
- Acceptance criteria and inspection methods
- Packaging and shipping requirements
- Timeline and delivery expectations
Be as detailed and specific as possible, and make sure that everyone is on the same page before the project begins. This will help avoid misunderstandings and ensure that your parts meet your exact specifications.
Implement robust quality control measures
To ensure consistent quality and catch potential issues early, it’s important to implement robust quality control measures throughout the surface treatment process. This can include:
- Regular in-process inspections and testing
- Final inspection and acceptance testing
- Detailed documentation and traceability
- Corrective action procedures for any non-conformances
Work with your surface treatment partner to develop a comprehensive quality control plan that meets your specific needs and requirements. And don’t hesitate to conduct your own audits and inspections to verify that the plan is being followed.
Foster a culture of continuous improvement
Finally, remember that selecting a surface treatment partner is not a one-time event – it’s an ongoing relationship that requires continuous improvement and collaboration. Encourage open communication, share feedback and ideas, and work together to identify opportunities for optimization and innovation.
By fostering a culture of continuous improvement, you can not only ensure consistent quality and reliability, but also drive down costs, improve efficiency, and stay ahead of the competition.
The bottom line
Outsourcing surface treatment can be a complex and challenging process, but by following these best practices and partnering with a true expert, you can achieve the high-quality results your business demands. Remember, your surface treatment is only as good as the partner you choose – so choose wisely, communicate clearly, and never stop striving for perfection.
Introduction
In the world of custom metal fabrication, surface treatment plays a critical role in determining the quality, performance, and longevity of the finished product. From aerospace and automotive to medical and industrial applications, the demands placed on metal parts are becoming increasingly stringent, and achieving these requirements all starts with the surface.
The surface of a metal part is where many of the critical properties that determine its performance and durability are established. That’s why surface treatment is so important – it’s the process of modifying and enhancing the surface to meet specific requirements and improve overall quality and reliability.
However, surface treatment is not a one-size-fits-all process. There are a wide range of options available, each with its own advantages, limitations, and applications, as described in another article about metal finishing. The choice depends on factors such as the base material, end-use environment, and specific performance requirements of the part.
To further complicate matters, many manufacturers and custom metal fabricators choose to outsource their surface treatment processes to specialized providers. While this can offer benefits like access to advanced equipment and expertise, it also introduces new challenges and risks that must be carefully managed to ensure consistent quality.
In this article, we will explore the critical role of surface treatment in custom metal fabrication and discuss the key challenges and best practices for ensuring high-quality, reliable results.
Challenges in assuring quality of surface treatment of metal parts
Achieving the perfect finish is no easy feat, especially when outsourcing the process to third-party providers. Surface treatment is a complex process with numerous variables and potential failure modes that can impact the quality and consistency of the finished parts.
The complexities of outsourcing
Outsourcing surface treatment can offer many benefits, such as access to specialized expertise, advanced equipment, and cost savings. However, it also introduces a new set of challenges and potential failure modes that can compromise the quality and consistency of the finished parts.
Common issues that can arise when outsourcing surface treatment include:
- Miscommunication of specifications and requirements leading to non-conforming parts
- Lack of process control and variability in the surface treatment parameters
- Extended lead times and reduced flexibility to accommodate changes or rush orders
- Limited visibility and difficulty in identifying and resolving quality issues quickly
- Potential risk of intellectual property loss or compromise, particularly for sensitive applications
To mitigate these risks, it’s crucial to select a surface treatment partner with a proven track record of quality, reliability, and expertise in the specific processes and applications required. However, even with a carefully vetted partner, outsourcing adds an extra layer of complexity that requires robust quality control measures and close collaboration.
The multitude of variables and failure modes
Surface treatment encompasses a wide range of processes, each with its own set of critical variables and potential failure modes. From pre-treatment steps like cleaning and masking to the actual coating or plating processes and post-treatment operations, there are numerous factors that can impact the quality and performance of the finished parts.
For example, in the case of electroplating, common failures can include:
- Poor adhesion and delamination of the plating due to improper cleaning or surface preparation
- Uneven plating thickness and coverage due to incorrect current density or part orientation
- Rough or pitted surface finish due to contamination or incorrect additive levels in the plating bath
- Hydrogen embrittlement leading to reduced ductility and premature failure, particularly in high-strength steel parts
Similarly, in powder coating, common issues can include:
- Orange peel or textured surface finish due to incorrect powder application or curing parameters
- Pinholing or outgassing defects due to improper pretreatment or contamination on the part surface
- Color variations or inconsistency due to changes in the powder composition or application process
- Reduced corrosion resistance or coating durability due to insufficient film thickness or cure
The human factor
In addition to the technical complexities of surface treatment, the human factor plays a critical role in ensuring consistent quality. The success of the process ultimately depends on the skill, knowledge, and attention to detail of the operators, technicians, and quality control personnel involved.
In outsourcing arrangements, the lack of direct control over the personnel performing the surface treatment can introduce additional risks. Common issues can include:
- Insufficient training or lack of experience with the specific processes or applications required
- High turnover or frequent changes in personnel leading to inconsistency in the process
- Lack of accountability or ownership for quality due to diffused responsibility across multiple organizations
- Cultural or language barriers that can hinder effective communication and problem-solving
Selecting the right surface treatment partner
When it comes to outsourcing surface treatment, choosing the right partner is critical. Just as you wouldn’t trust your precision aerospace components to a general machine shop, you shouldn’t trust your metal parts to just any surface treatment provider.
But with so many options out there, how can you separate the true experts from the rest? How can you find a partner that will deliver the quality, consistency, and reliability you need to succeed in today’s competitive market?
Understand your specific requirements
The first step in selecting a surface treatment partner is to have a clear understanding of your own unique requirements. This goes beyond just knowing whether you need plating, anodizing, or coating – it means diving into the details of your specific application.
Consider factors like:
- The base material and geometry of your parts
- The environmental conditions the parts will be exposed to
- Any regulatory or industry standards that must be met
- Specific performance requirements for corrosion resistance, wear resistance, conductivity, etc.
The more specific you can be about your needs, the better equipped you’ll be to find a partner that can meet them. It’s like choosing a surgeon – you wouldn’t just look for a general practitioner, you’d want a specialist with experience in your specific procedure.
Evaluate technical expertise and capabilities
Once you have a clear idea of what you need, it’s time to start evaluating potential partners based on their technical expertise and capabilities. Look for providers that have:
- Proven experience with your specific type of surface treatment and base material
- State-of-the-art equipment and facilities that are properly maintained and calibrated
- Rigorous quality control processes, including ISO certifications and regular audits
- A team of skilled technicians and engineers with ongoing training and development
Don’t hesitate to ask for detailed information about their processes, equipment, and personnel. A true expert will be happy to share their knowledge and demonstrate their capabilities.
Establish clear specifications and expectations
Once you’ve selected a surface treatment partner, it’s essential to establish clear specifications and expectations upfront. This includes:
- Detailed drawings and 3D models of your parts
- Specific requirements for coating thickness, hardness, adhesion, appearance, etc.
- Acceptance criteria and inspection methods
- Packaging and shipping requirements
- Timeline and delivery expectations
Be as detailed and specific as possible, and make sure that everyone is on the same page before the project begins. This will help avoid misunderstandings and ensure that your parts meet your exact specifications.
Implement robust quality control measures
To ensure consistent quality and catch potential issues early, it’s important to implement robust quality control measures throughout the surface treatment process. This can include:
- Regular in-process inspections and testing
- Final inspection and acceptance testing
- Detailed documentation and traceability
- Corrective action procedures for any non-conformances
Work with your surface treatment partner to develop a comprehensive quality control plan that meets your specific needs and requirements. And don’t hesitate to conduct your own audits and inspections to verify that the plan is being followed.
Foster a culture of continuous improvement
Finally, remember that selecting a surface treatment partner is not a one-time event – it’s an ongoing relationship that requires continuous improvement and collaboration. Encourage open communication, share feedback and ideas, and work together to identify opportunities for optimization and innovation.
By fostering a culture of continuous improvement, you can not only ensure consistent quality and reliability, but also drive down costs, improve efficiency, and stay ahead of the competition.
The bottom line
Outsourcing surface treatment can be a complex and challenging process, but by following these best practices and partnering with a true expert, you can achieve the high-quality results your business demands. Remember, your surface treatment is only as good as the partner you choose – so choose wisely, communicate clearly, and never stop striving for perfection.
Ready to see CADDi Drawer in action? Get a personalized demo.
Subscribe to our Blog!
Related Resources
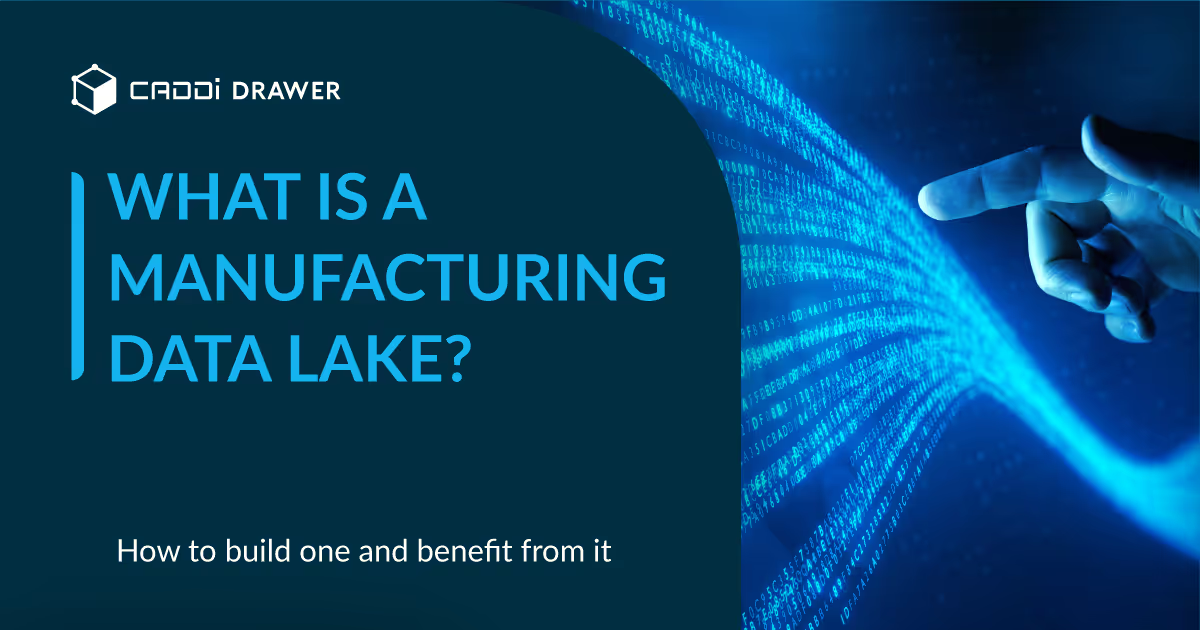
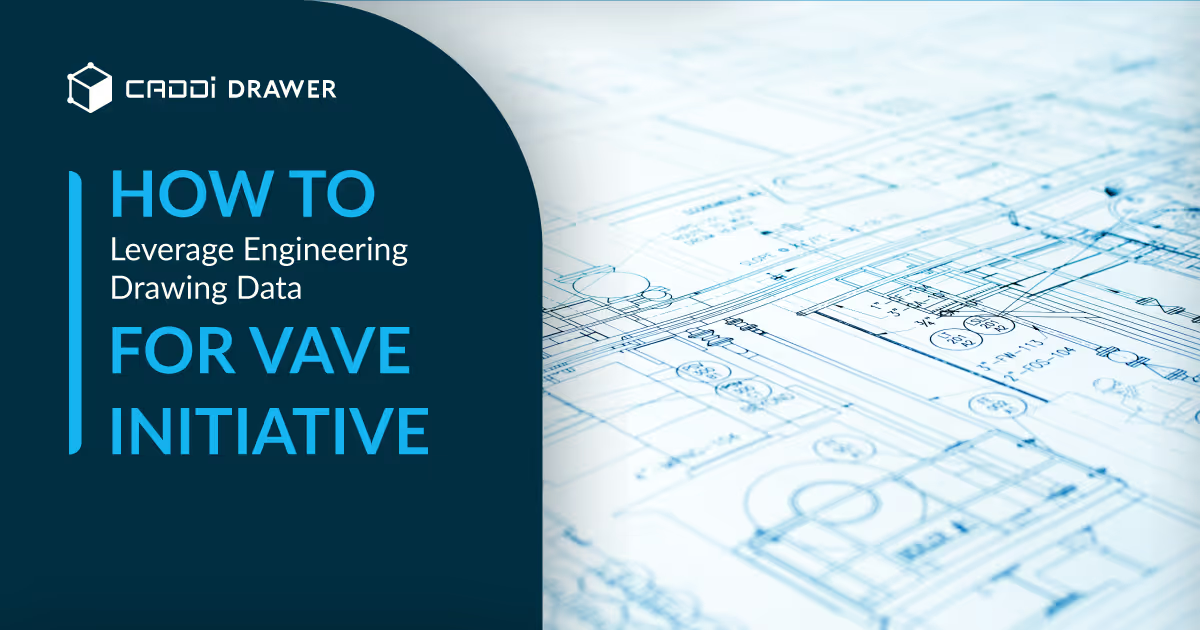
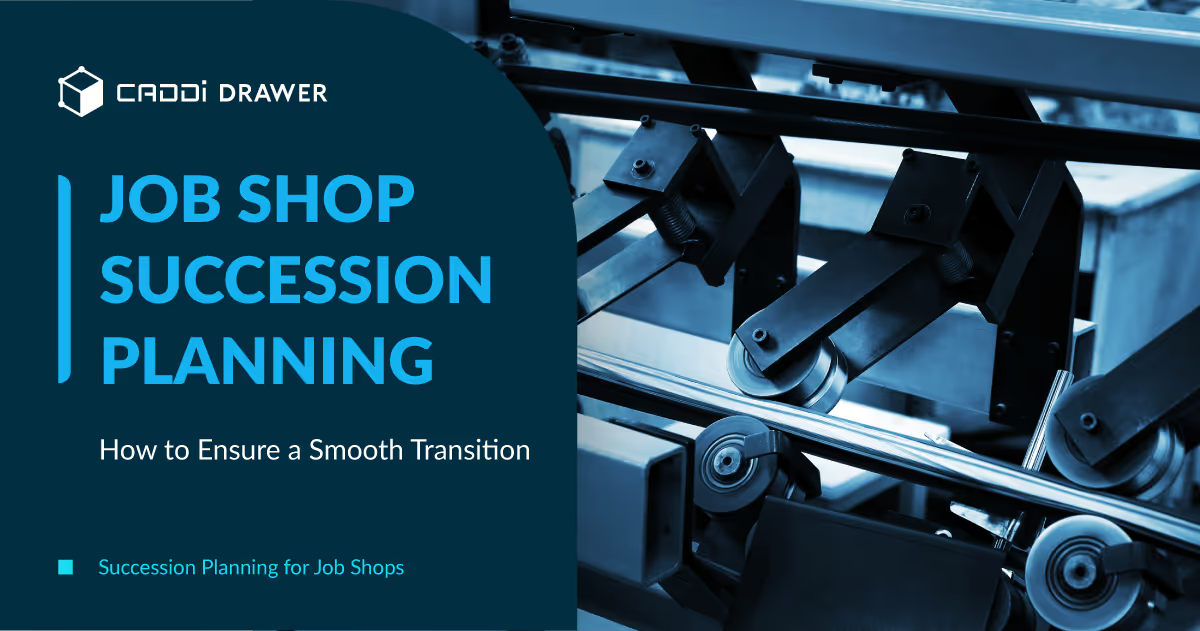
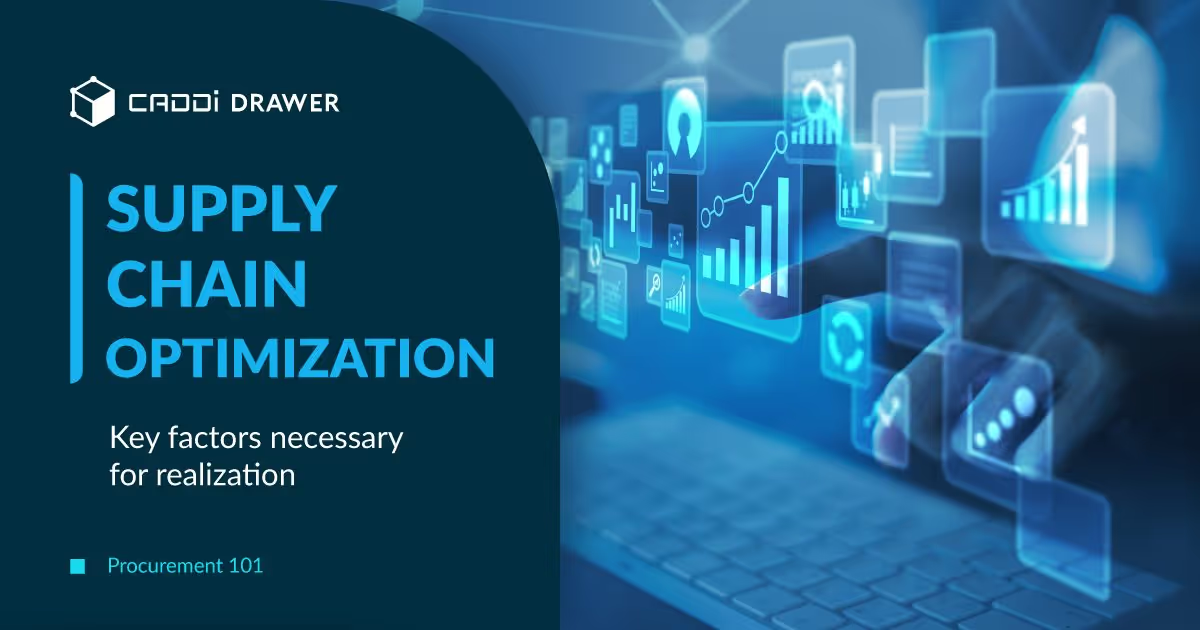
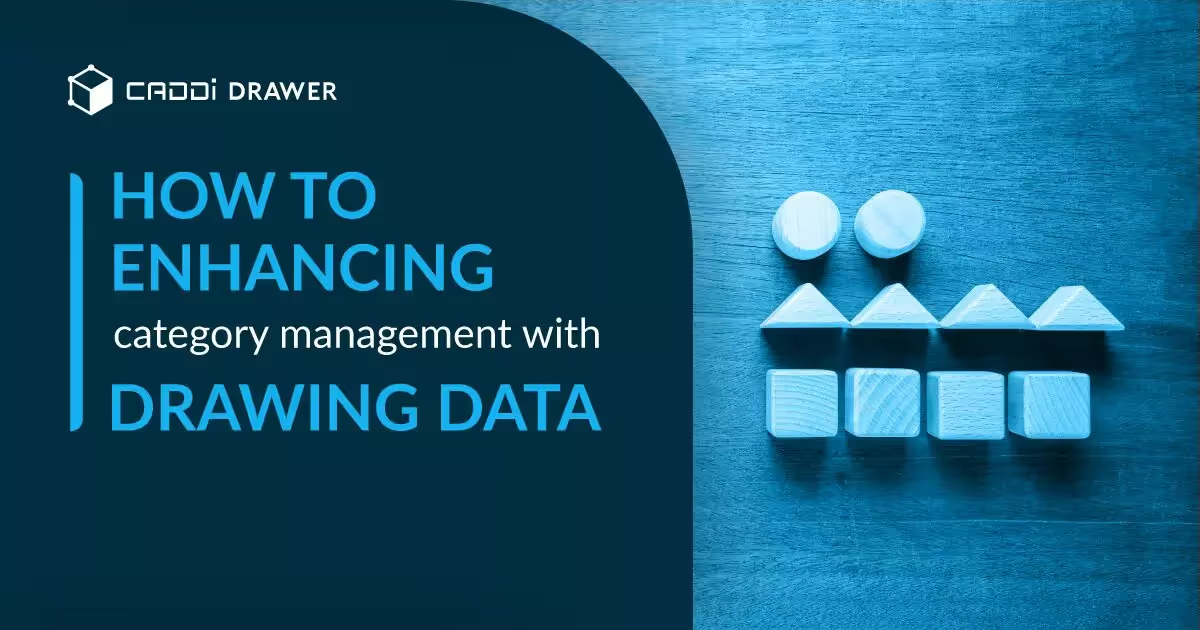
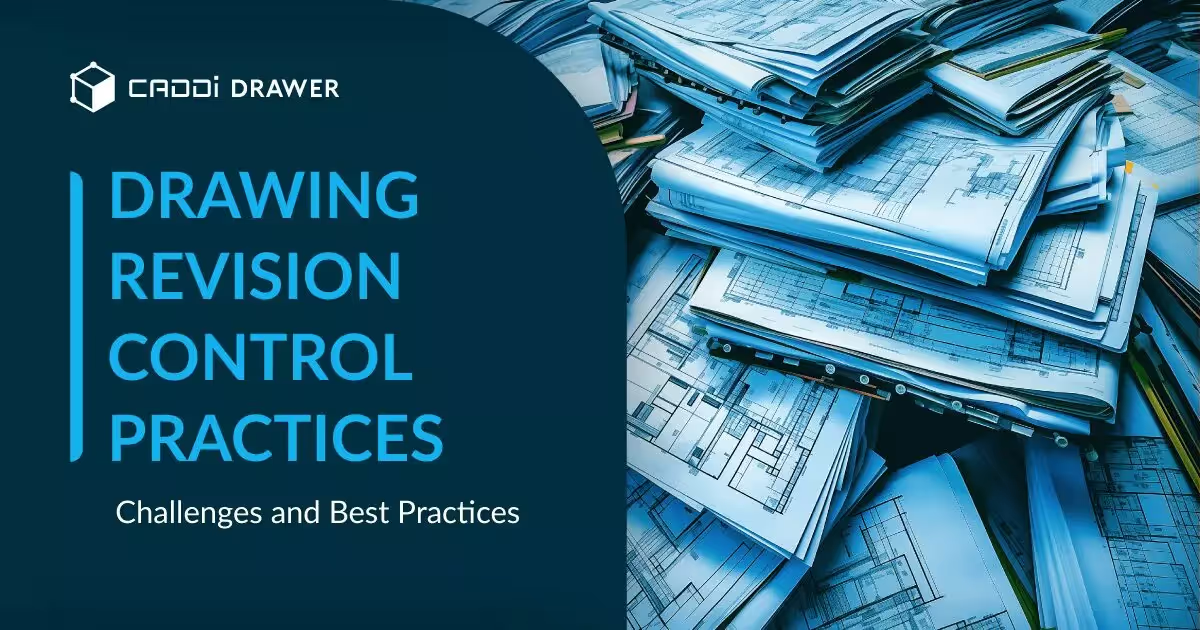