Procurement 101: Supply Chain Optimization – Key factors necessary for realization
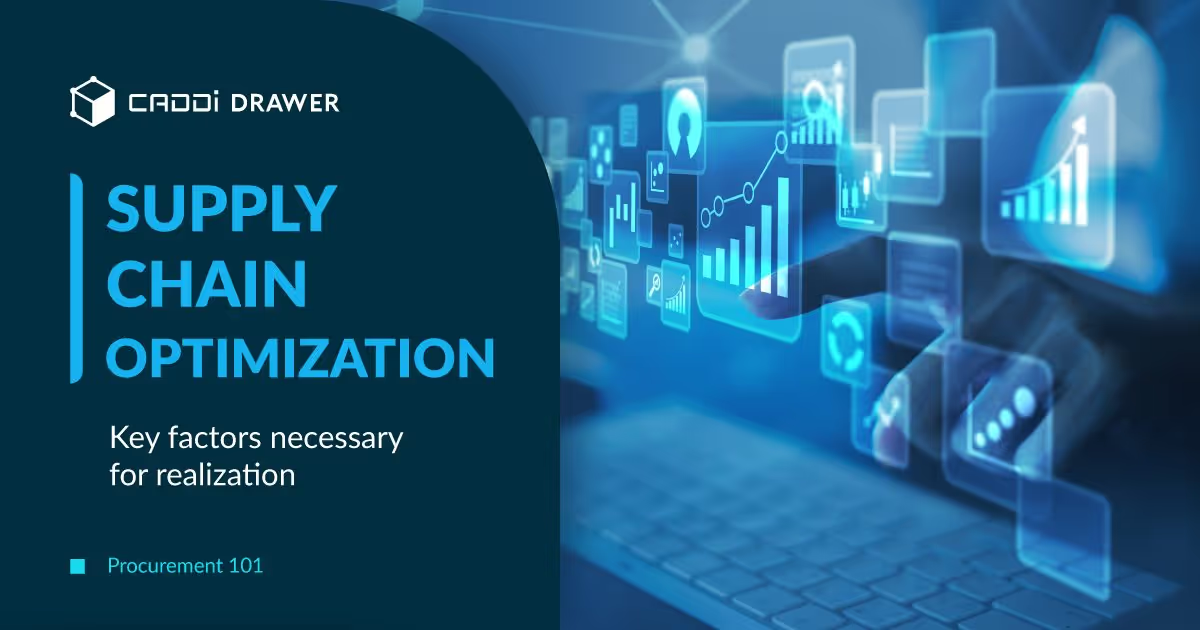
Table of Contents
It’s a common assumption that the intricate dance of supply chain management is solely the realm of algorithms and data analytics. However, the real game changer in manufacturing efficiency lies not just in the numbers but in the strategic harmonization of technology, planning, and human insight.
Are you grappling with inventory excesses or shortages, skyrocketing operational costs, or logistical inefficiencies?
This article unfolds the blueprint for transforming these challenges into opportunities for growth, showcasing the pivotal role of AI-driven solutions and the power of data in optimizing supply chains for a competitive edge.
Understanding Supply Chain Optimization
Supply chain optimization in the manufacturing and distribution context is about crafting a seamless, efficient pathway from raw materials to end-users. This process spans various industries, including retail, industrial products, and consumer packaged goods, each with its unique challenges and solutions. The ultimate goal is to ensure that products are delivered in the right quantities, to the right places, at the right time, minimizing costs while maximizing customer satisfaction.
Supply chain optimization isn’t just a single strategy but a collection of practices designed to improve various facets of the supply chain. These include:
- Cost Optimization: Strategies like just-in-time manufacturing, factory automation, and energy consumption reduction not only streamline production processes but also significantly cut down on waste and operational costs.
- Inventory Optimization: Balancing inventory levels to meet demand without incurring excess storage costs or risk running out of stock is critical. This involves manufacturing products in precise amounts and rationalizing inventory levels to minimize costs and waste.
- Network Optimization: Identifying the best locations for factories, warehouses, and distribution centers to control costs and enhance reliability is crucial. This also involves assessing suppliers and their capacity to handle supply and demand fluctuations.
Key Techniques for Optimization
The journey toward optimization begins with a detailed plan that includes several stages: design, planning, and execution. Here’s how these stages unfold:
- Design Stage: Decisions about the physical locations of factories, warehouses, and distribution centers are made. This phase determines the foundation of an efficient supply chain.
- Planning Stage: Production plans are developed, considering product storage costs and transportation availability to ensure timely production.
- Execution Stage: This stage aligns order management, inventory, and transportation logistics to deliver products efficiently and cost-effectively.
Real-world examples underscore the impact of these techniques. For instance, a leading consumer goods company implemented inventory optimization strategies, reducing their storage costs by 15% and improving order fulfillment speed by 20%. Another example is a global manufacturing firm that adopted network optimization, resulting in a 10% reduction in transportation costs and a 5% improvement in delivery times.
Strategic Approaches and Solutions
Embracing strategic approaches and innovative solutions is paramount for optimizing the supply chain in the manufacturing sector. These strategies are not just theoretical; they are grounded in real-world applications that demonstrate significant improvements in efficiency, cost reduction, and customer satisfaction.
Forecasting Demand and Safety Stock: The foundation of an efficient supply chain lies in the ability to forecast demand accurately. This involves using statistical methods like Standard Deviation and Mean Absolute Deviation to calculate safety stock levels, ensuring that companies can manage unpredictability effectively.
Production Planning: Creating a supply-chain manufacturing and distribution plan to meet forecasted demand at the lowest cost is crucial. This includes decisions on daily manufacturing volumes, warehouse restocking, and transportation modes.
Granular Forecasting with AI: The advent of AI and machine learning has enabled a new breed of supply-chain-optimization solutions. These solutions offer granular forecasting at levels such as per article per customer per day, significantly enhancing inventory management and distribution efficiency.
Outsourcing Non-Core Activities: Outsourcing procurement, logistics, or customer service can lead to significant improvements in focus and efficiency.
Enhancing Supplier-Retailer Communication: Transparent communication between suppliers and retailers ensures timely fulfillment of demand and avoids confusion.
Adopting Centralized Management Software: Integrating different facets of a business through centralized management software enables cohesive operation, making data accessible across departments.
Case Studies of Supply Chain Optimization
Increased Supply Chain Throughput and Reduced Costs
According to McKinsey, companies adopting optimization tools and processes in manufacturing industries have seen supply chain throughput increase by 10 to 15 percent in the short term without changing assets or overall configurations. Furthermore, these optimizations can reduce costs by 5 to 10 percent and CO2 emissions by 10 to 15 percent, thereby increasing operational flexibility and resilience toward disruptions. This is achieved through best practices such as improving information flows, elevating customer centricity, and bridging the gap between long-term planning and day-to-day operations.
Diversification of Manufacturing Locations for Resilience
A US-based electronics manufacturer faced challenges due to overreliance on materials and manufacturing in Asia, exacerbated by the COVID-19 pandemic and geopolitical instability. By engaging with EY for supply chain modeling and optimization, the company diversified its manufacturing locations, reducing long-term supply chain risk. This strategic move, facilitated by a comprehensive analysis and an integrated digital model, led to the selection of a new manufacturing site in North America, ultimately reducing excess product inventory by 27%.
Implementing Technology for Advanced Optimization
In today’s digital age, leveraging technology is non-negotiable for achieving advanced supply chain optimization. Modern technologies such as AI and machine learning enable predictive demand planning, inventory management, and supply chain visibility, ensuring more informed decision-making and efficient operations.
Data plays a pivotal role in refining supply chain operations. Modern solutions leverage granular data analysis to forecast demand accurately, optimize inventory levels, and ensure timely distribution. This data-centric approach not only improves operational efficiency but also significantly reduces costs and enhances customer satisfaction.
Here are some best practices of leveraging technology.
Predictive Demand Planning: The application of AI and machine learning for predictive demand planning exemplifies technology’s pivotal role. A specific case is Amazon’s anticipatory shipping model, which uses big data analytics to predict customer purchases before orders are placed. By analyzing previous purchase history, product searches, and even the time spent on each page, Amazon pre-positions goods in warehouses closer to potential buyers, drastically reducing delivery times and enhancing customer satisfaction.
Inventory Management: In inventory management, IoT devices and RFID tags offer real-time tracking of goods, significantly improving inventory accuracy and reducing the risk of stockouts or overstocking. For instance, Zara utilizes RFID technology to track items from manufacturing through to sale, enabling precise inventory levels and rapid restocking of popular items, which is critical for their fast-fashion business model.
Supply Chain Visibility: Enhanced supply chain visibility is another critical advantage. Maersk and IBM’s collaboration on TradeLens, a blockchain-enabled shipping solution, illustrates how technology can provide transparency across the supply chain. By digitizing the supply chain process from end to end, TradeLens allows all participants, including shippers, shipping lines, and customs authorities, to access real-time data, reducing delays and improving the efficiency of global trade.
Granular Data Analysis: The utilization of granular data analysis for forecasting demand accurately is revolutionizing supply chain operations. For example, Coca-Cola leverages big data to analyze sales across different regions and adjust its supply chain operations accordingly. This enables the beverage giant to optimize its inventory levels based on regional preferences and seasonal demand, ensuring that popular products are always available while minimizing waste and storage costs.
Cost Reduction and Customer Satisfaction: The data-centric approach also plays a crucial role in reducing costs and enhancing customer satisfaction. UPS’s ORION (On-Road Integrated Optimization and Navigation) system uses advanced algorithms to determine the most efficient delivery routes, considering traffic, weather conditions, and the delivery commitments of millions of packages. This not only reduces fuel consumption and emissions but also ensures timely deliveries, directly impacting customer satisfaction positively.
How CADDi Drawer can assist Supply Chain Optimization
At CADDi, we recognize the intricacies involved in transforming procurement processes. Our range of solutions and services is tailored to assist manufacturers at every stage of their transformation journey. From strategic sourcing to risk management, our platform empowers manufacturers to enhance their procurement processes.
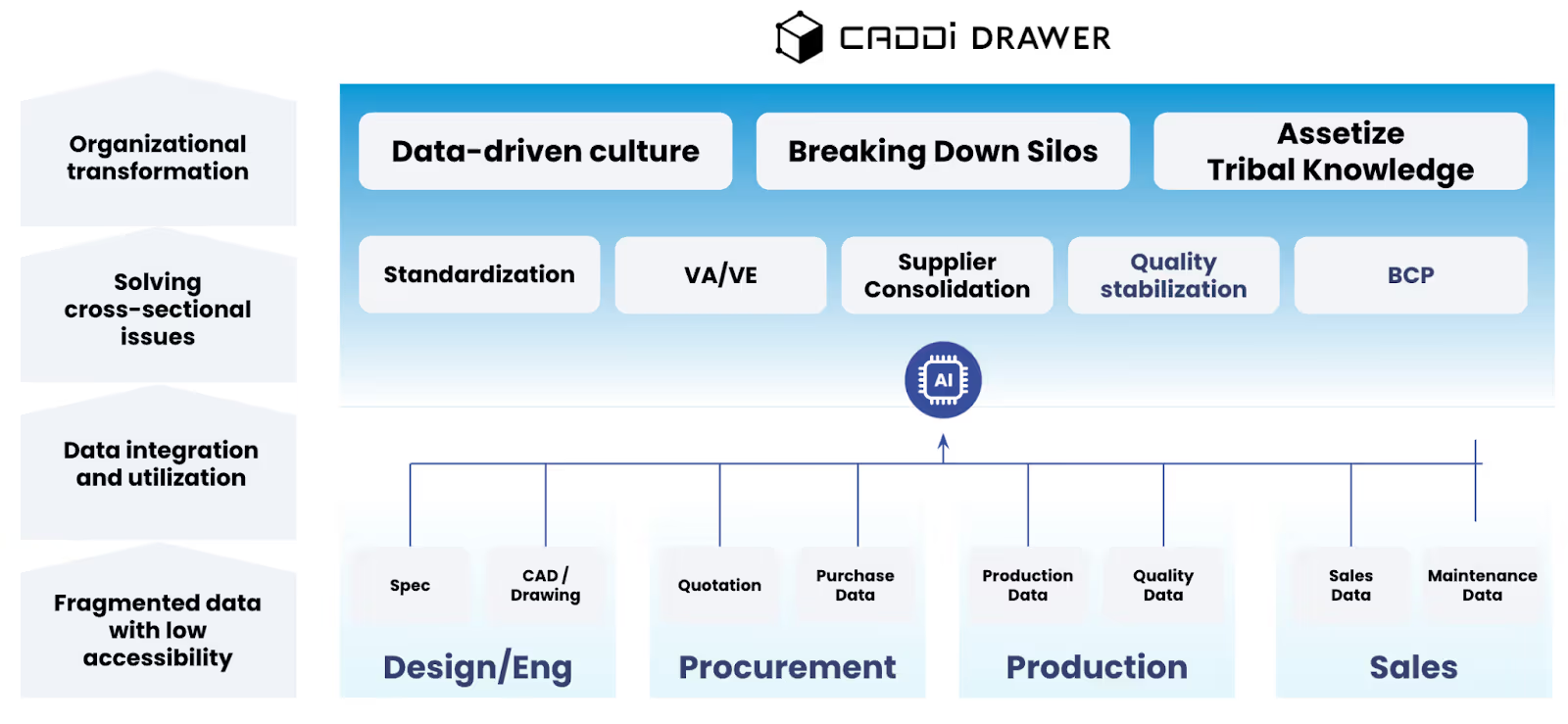
Consolidate scattered data into a centralized location
By simply uploading CSV files, you can consolidate all pertinent information related to associated drawings: costs, quantities, supplier details, sales prices, breakdowns, and more. CADDi Drawer seamlessly integrates ERP data, CAM, CAD, quality defect reports, and spec sheets automatically. Leveraging our proprietary OCR-based AI technology, CADDi Drawer effortlessly extracts and digitizes non-structural data, such as legacy drawings in static scanned PDF files containing handwritten text.
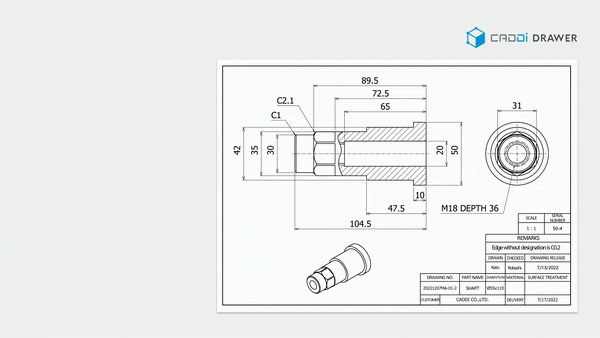
Utilize AI-driven intelligence for supply chain data analysis
Utilizing CADDi’s patented technology, each part’s shape is identified to locate “like parts” across historical drawings, with relevant supply chain data (e.g., cost, quality, manufacturing notes, specs) automatically linked to each drawing. This provides enhanced visibility into dormant drawings within your file storage and enables actionable insights to drive cross-functional initiatives such as design standardization, VAVE, and supplier consolidation.
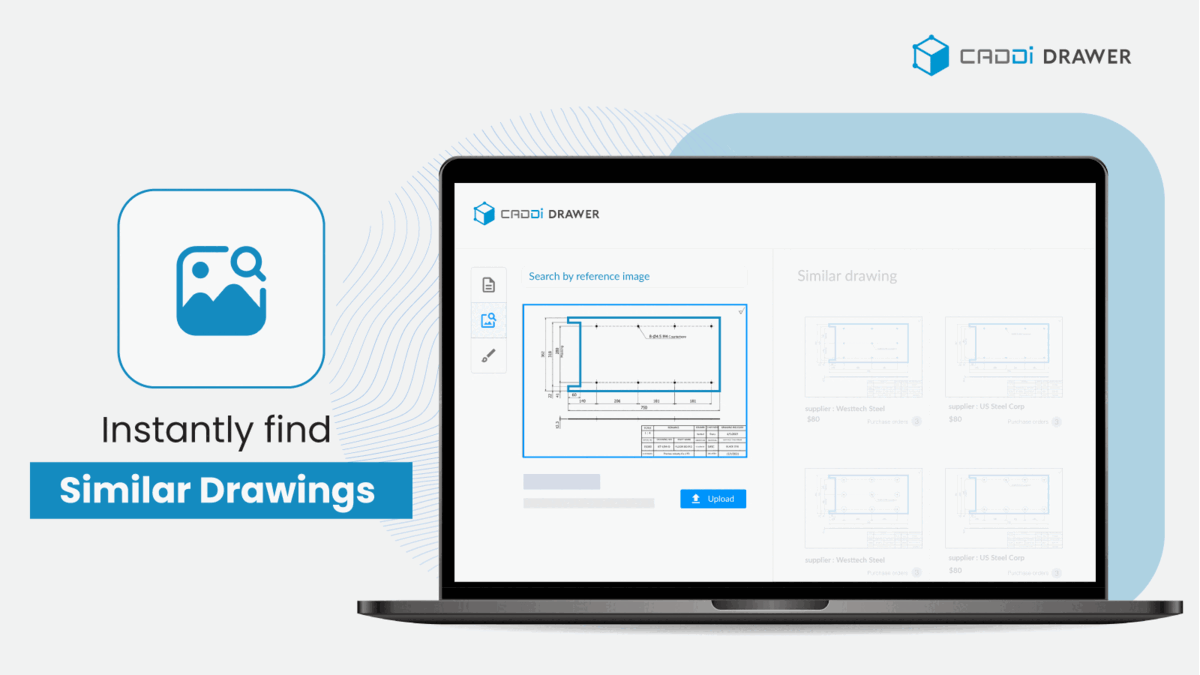
Streamline document management and compliance efforts
Navigating various regulations and standards changes can be challenging and time-consuming. CADDi Drawer enables efficient searching through numerous drawings and specifications, previously identified manually, to verify their compliance status. The system digitizes information from 2D drawings, including supplier names and material details, and integrates this with procurement data and specifications. Leveraging this data, users can conduct keyword searches to identify drawings containing specific substances, along with supplier names, facilitating collaboration with suppliers on corrective measures to ensure compliance with regulations.
It’s a common assumption that the intricate dance of supply chain management is solely the realm of algorithms and data analytics. However, the real game changer in manufacturing efficiency lies not just in the numbers but in the strategic harmonization of technology, planning, and human insight.
Are you grappling with inventory excesses or shortages, skyrocketing operational costs, or logistical inefficiencies?
This article unfolds the blueprint for transforming these challenges into opportunities for growth, showcasing the pivotal role of AI-driven solutions and the power of data in optimizing supply chains for a competitive edge.
Understanding Supply Chain Optimization
Supply chain optimization in the manufacturing and distribution context is about crafting a seamless, efficient pathway from raw materials to end-users. This process spans various industries, including retail, industrial products, and consumer packaged goods, each with its unique challenges and solutions. The ultimate goal is to ensure that products are delivered in the right quantities, to the right places, at the right time, minimizing costs while maximizing customer satisfaction.
Supply chain optimization isn’t just a single strategy but a collection of practices designed to improve various facets of the supply chain. These include:
- Cost Optimization: Strategies like just-in-time manufacturing, factory automation, and energy consumption reduction not only streamline production processes but also significantly cut down on waste and operational costs.
- Inventory Optimization: Balancing inventory levels to meet demand without incurring excess storage costs or risk running out of stock is critical. This involves manufacturing products in precise amounts and rationalizing inventory levels to minimize costs and waste.
- Network Optimization: Identifying the best locations for factories, warehouses, and distribution centers to control costs and enhance reliability is crucial. This also involves assessing suppliers and their capacity to handle supply and demand fluctuations.
Key Techniques for Optimization
The journey toward optimization begins with a detailed plan that includes several stages: design, planning, and execution. Here’s how these stages unfold:
- Design Stage: Decisions about the physical locations of factories, warehouses, and distribution centers are made. This phase determines the foundation of an efficient supply chain.
- Planning Stage: Production plans are developed, considering product storage costs and transportation availability to ensure timely production.
- Execution Stage: This stage aligns order management, inventory, and transportation logistics to deliver products efficiently and cost-effectively.
Real-world examples underscore the impact of these techniques. For instance, a leading consumer goods company implemented inventory optimization strategies, reducing their storage costs by 15% and improving order fulfillment speed by 20%. Another example is a global manufacturing firm that adopted network optimization, resulting in a 10% reduction in transportation costs and a 5% improvement in delivery times.
Strategic Approaches and Solutions
Embracing strategic approaches and innovative solutions is paramount for optimizing the supply chain in the manufacturing sector. These strategies are not just theoretical; they are grounded in real-world applications that demonstrate significant improvements in efficiency, cost reduction, and customer satisfaction.
Forecasting Demand and Safety Stock: The foundation of an efficient supply chain lies in the ability to forecast demand accurately. This involves using statistical methods like Standard Deviation and Mean Absolute Deviation to calculate safety stock levels, ensuring that companies can manage unpredictability effectively.
Production Planning: Creating a supply-chain manufacturing and distribution plan to meet forecasted demand at the lowest cost is crucial. This includes decisions on daily manufacturing volumes, warehouse restocking, and transportation modes.
Granular Forecasting with AI: The advent of AI and machine learning has enabled a new breed of supply-chain-optimization solutions. These solutions offer granular forecasting at levels such as per article per customer per day, significantly enhancing inventory management and distribution efficiency.
Outsourcing Non-Core Activities: Outsourcing procurement, logistics, or customer service can lead to significant improvements in focus and efficiency.
Enhancing Supplier-Retailer Communication: Transparent communication between suppliers and retailers ensures timely fulfillment of demand and avoids confusion.
Adopting Centralized Management Software: Integrating different facets of a business through centralized management software enables cohesive operation, making data accessible across departments.
Case Studies of Supply Chain Optimization
Increased Supply Chain Throughput and Reduced Costs
According to McKinsey, companies adopting optimization tools and processes in manufacturing industries have seen supply chain throughput increase by 10 to 15 percent in the short term without changing assets or overall configurations. Furthermore, these optimizations can reduce costs by 5 to 10 percent and CO2 emissions by 10 to 15 percent, thereby increasing operational flexibility and resilience toward disruptions. This is achieved through best practices such as improving information flows, elevating customer centricity, and bridging the gap between long-term planning and day-to-day operations.
Diversification of Manufacturing Locations for Resilience
A US-based electronics manufacturer faced challenges due to overreliance on materials and manufacturing in Asia, exacerbated by the COVID-19 pandemic and geopolitical instability. By engaging with EY for supply chain modeling and optimization, the company diversified its manufacturing locations, reducing long-term supply chain risk. This strategic move, facilitated by a comprehensive analysis and an integrated digital model, led to the selection of a new manufacturing site in North America, ultimately reducing excess product inventory by 27%.
Implementing Technology for Advanced Optimization
In today’s digital age, leveraging technology is non-negotiable for achieving advanced supply chain optimization. Modern technologies such as AI and machine learning enable predictive demand planning, inventory management, and supply chain visibility, ensuring more informed decision-making and efficient operations.
Data plays a pivotal role in refining supply chain operations. Modern solutions leverage granular data analysis to forecast demand accurately, optimize inventory levels, and ensure timely distribution. This data-centric approach not only improves operational efficiency but also significantly reduces costs and enhances customer satisfaction.
Here are some best practices of leveraging technology.
Predictive Demand Planning: The application of AI and machine learning for predictive demand planning exemplifies technology’s pivotal role. A specific case is Amazon’s anticipatory shipping model, which uses big data analytics to predict customer purchases before orders are placed. By analyzing previous purchase history, product searches, and even the time spent on each page, Amazon pre-positions goods in warehouses closer to potential buyers, drastically reducing delivery times and enhancing customer satisfaction.
Inventory Management: In inventory management, IoT devices and RFID tags offer real-time tracking of goods, significantly improving inventory accuracy and reducing the risk of stockouts or overstocking. For instance, Zara utilizes RFID technology to track items from manufacturing through to sale, enabling precise inventory levels and rapid restocking of popular items, which is critical for their fast-fashion business model.
Supply Chain Visibility: Enhanced supply chain visibility is another critical advantage. Maersk and IBM’s collaboration on TradeLens, a blockchain-enabled shipping solution, illustrates how technology can provide transparency across the supply chain. By digitizing the supply chain process from end to end, TradeLens allows all participants, including shippers, shipping lines, and customs authorities, to access real-time data, reducing delays and improving the efficiency of global trade.
Granular Data Analysis: The utilization of granular data analysis for forecasting demand accurately is revolutionizing supply chain operations. For example, Coca-Cola leverages big data to analyze sales across different regions and adjust its supply chain operations accordingly. This enables the beverage giant to optimize its inventory levels based on regional preferences and seasonal demand, ensuring that popular products are always available while minimizing waste and storage costs.
Cost Reduction and Customer Satisfaction: The data-centric approach also plays a crucial role in reducing costs and enhancing customer satisfaction. UPS’s ORION (On-Road Integrated Optimization and Navigation) system uses advanced algorithms to determine the most efficient delivery routes, considering traffic, weather conditions, and the delivery commitments of millions of packages. This not only reduces fuel consumption and emissions but also ensures timely deliveries, directly impacting customer satisfaction positively.
How CADDi Drawer can assist Supply Chain Optimization
At CADDi, we recognize the intricacies involved in transforming procurement processes. Our range of solutions and services is tailored to assist manufacturers at every stage of their transformation journey. From strategic sourcing to risk management, our platform empowers manufacturers to enhance their procurement processes.
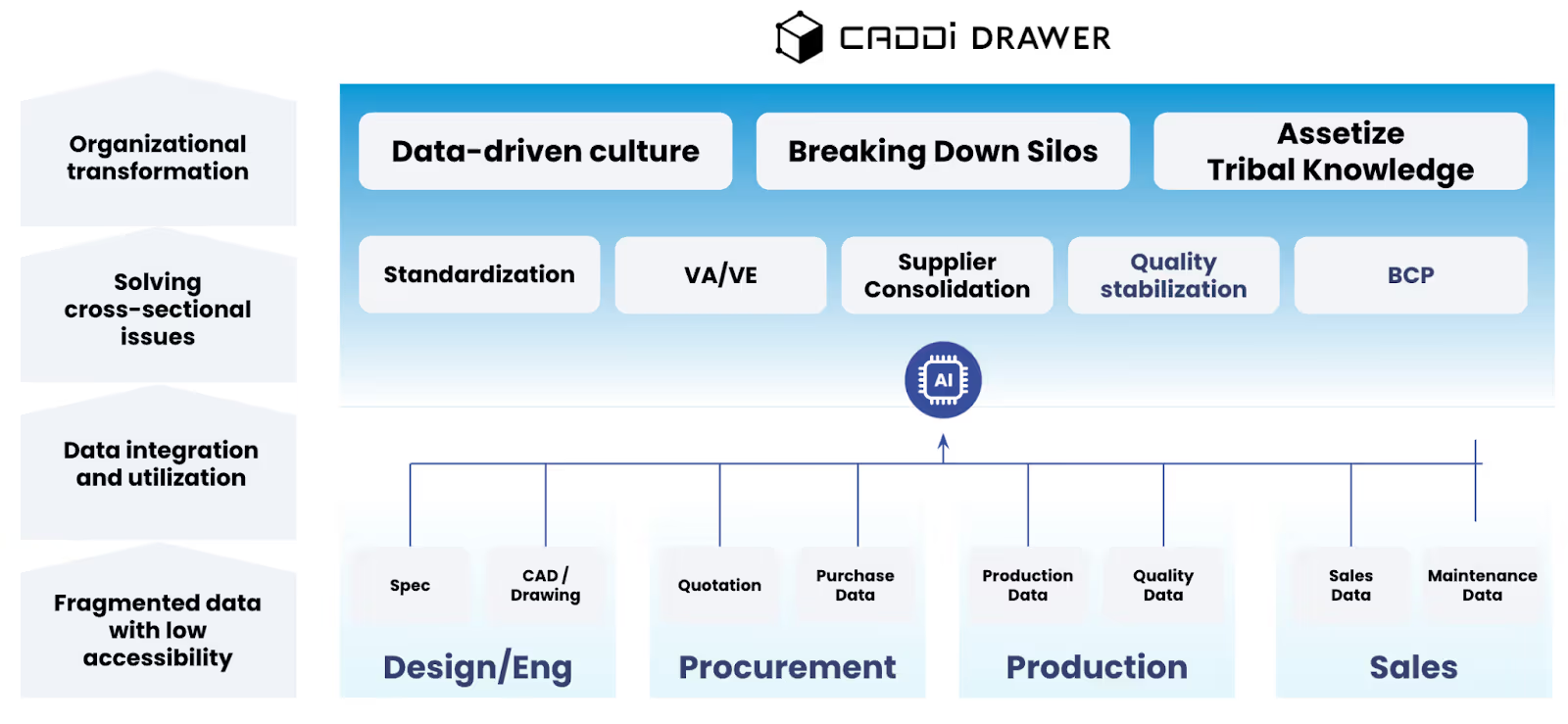
Consolidate scattered data into a centralized location
By simply uploading CSV files, you can consolidate all pertinent information related to associated drawings: costs, quantities, supplier details, sales prices, breakdowns, and more. CADDi Drawer seamlessly integrates ERP data, CAM, CAD, quality defect reports, and spec sheets automatically. Leveraging our proprietary OCR-based AI technology, CADDi Drawer effortlessly extracts and digitizes non-structural data, such as legacy drawings in static scanned PDF files containing handwritten text.
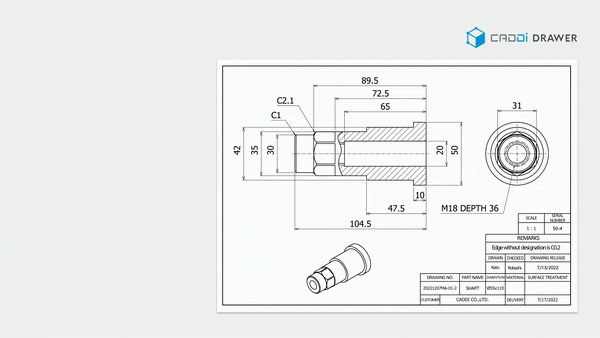
Utilize AI-driven intelligence for supply chain data analysis
Utilizing CADDi’s patented technology, each part’s shape is identified to locate “like parts” across historical drawings, with relevant supply chain data (e.g., cost, quality, manufacturing notes, specs) automatically linked to each drawing. This provides enhanced visibility into dormant drawings within your file storage and enables actionable insights to drive cross-functional initiatives such as design standardization, VAVE, and supplier consolidation.
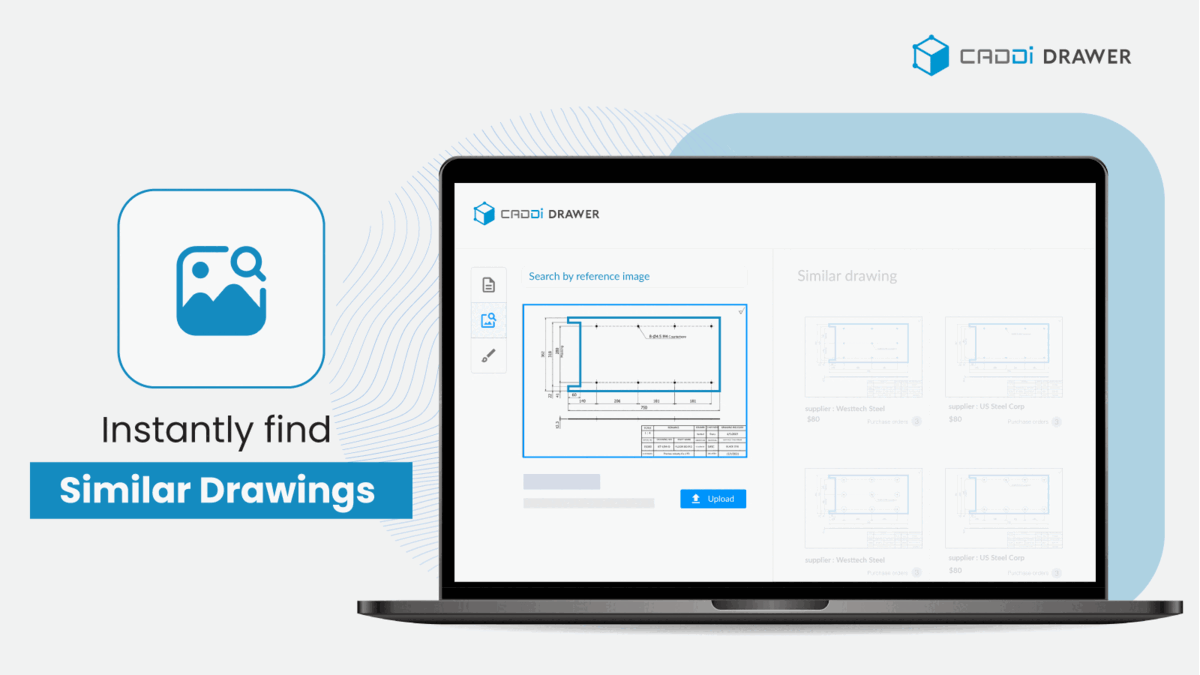
Streamline document management and compliance efforts
Navigating various regulations and standards changes can be challenging and time-consuming. CADDi Drawer enables efficient searching through numerous drawings and specifications, previously identified manually, to verify their compliance status. The system digitizes information from 2D drawings, including supplier names and material details, and integrates this with procurement data and specifications. Leveraging this data, users can conduct keyword searches to identify drawings containing specific substances, along with supplier names, facilitating collaboration with suppliers on corrective measures to ensure compliance with regulations.
Ready to see CADDi Drawer in action? Get a personalized demo.
Subscribe to our Blog!
Related Resources
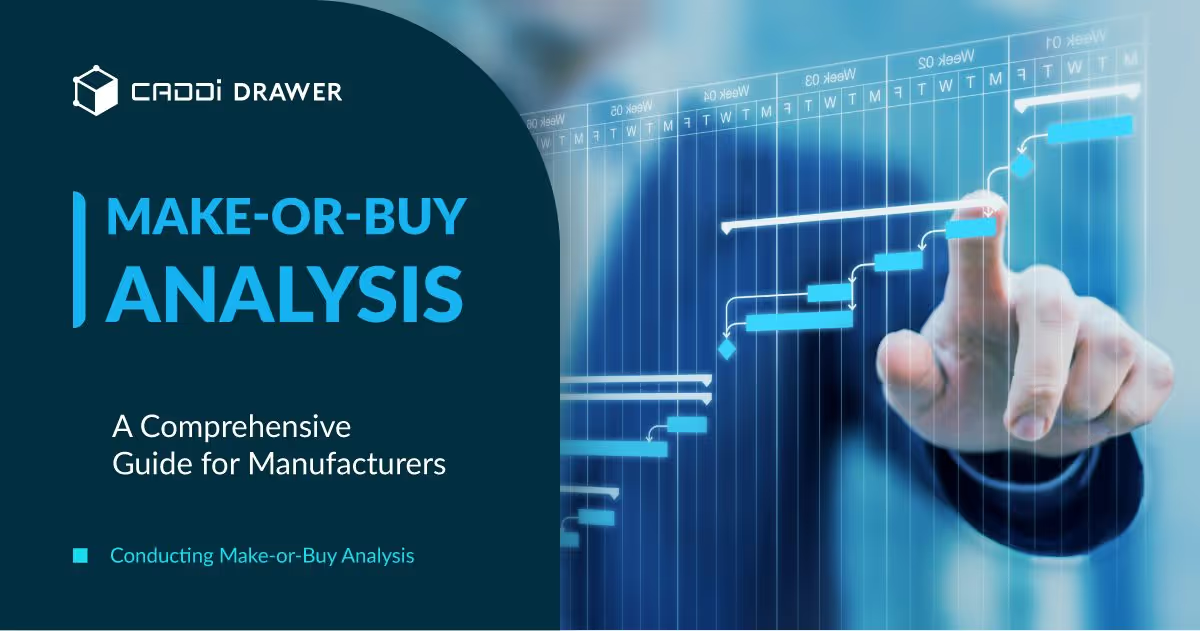
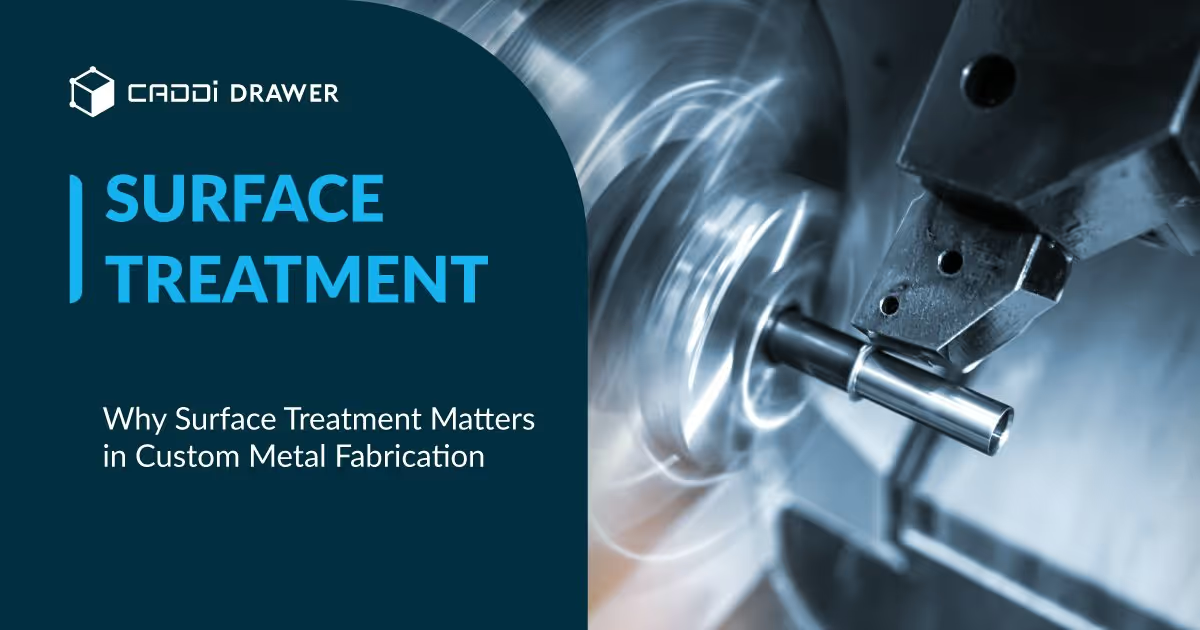
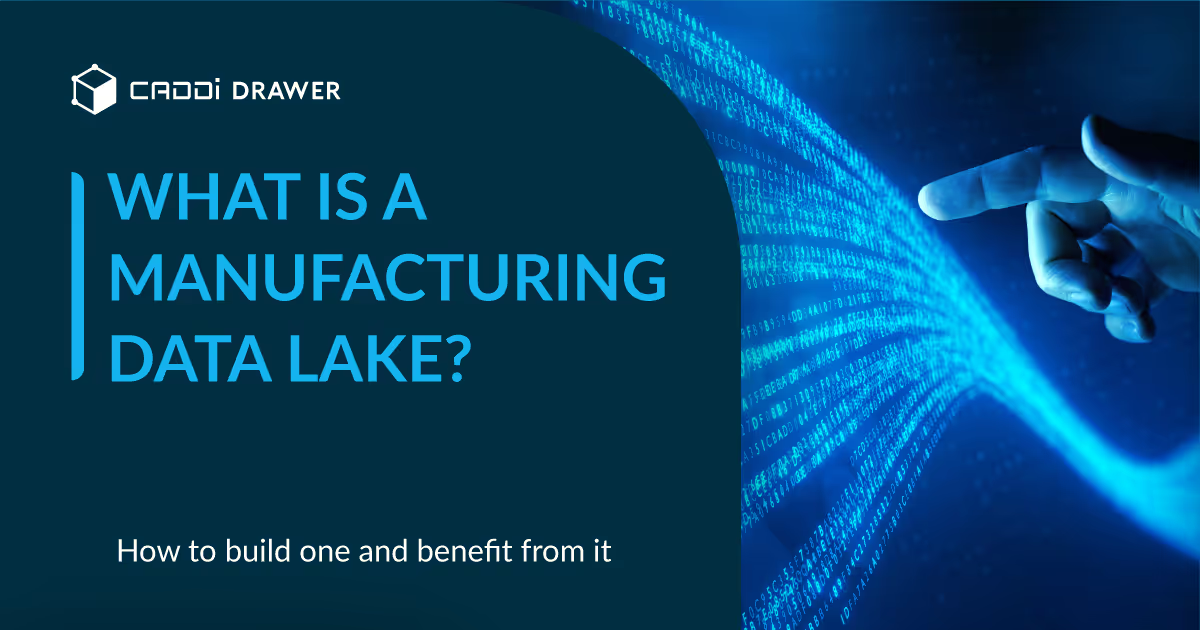
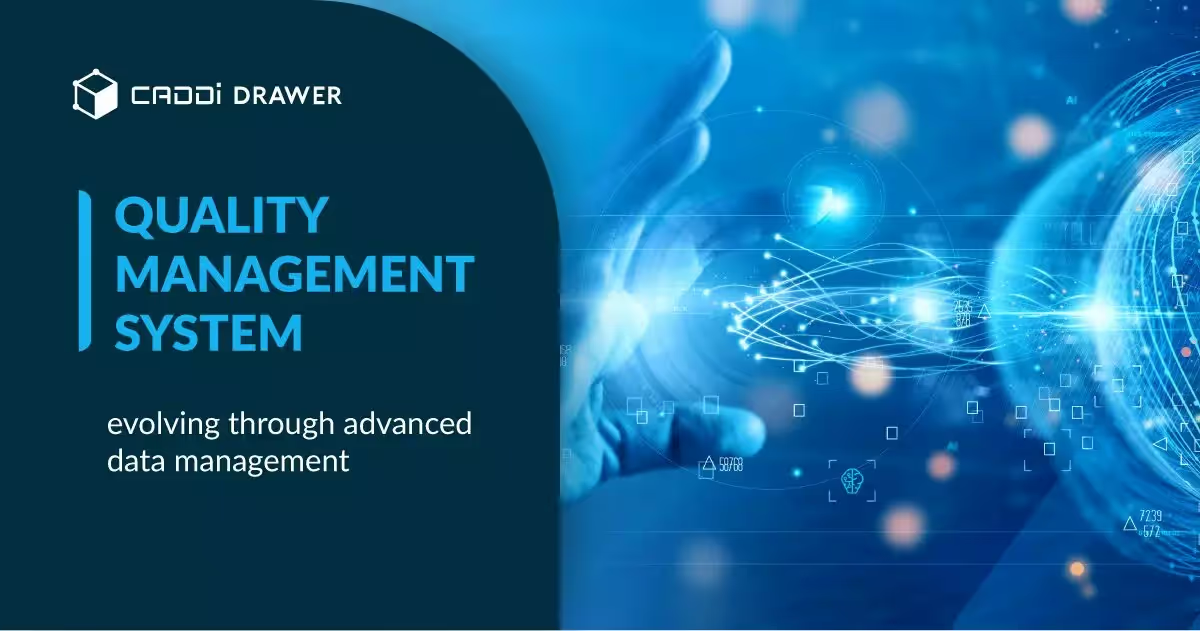
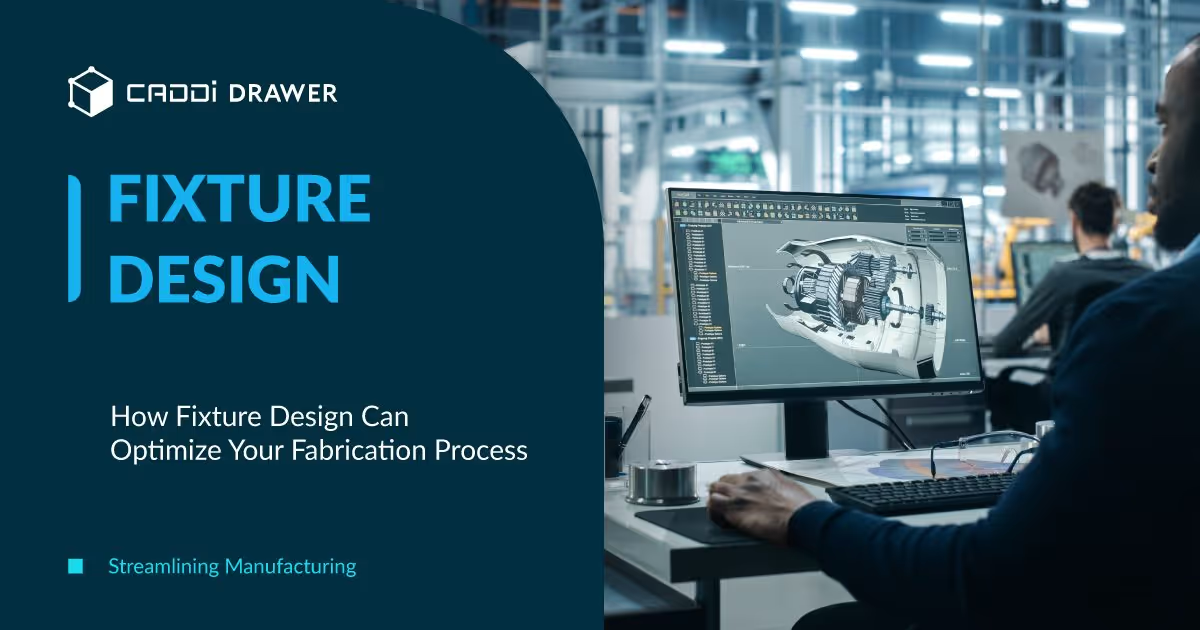
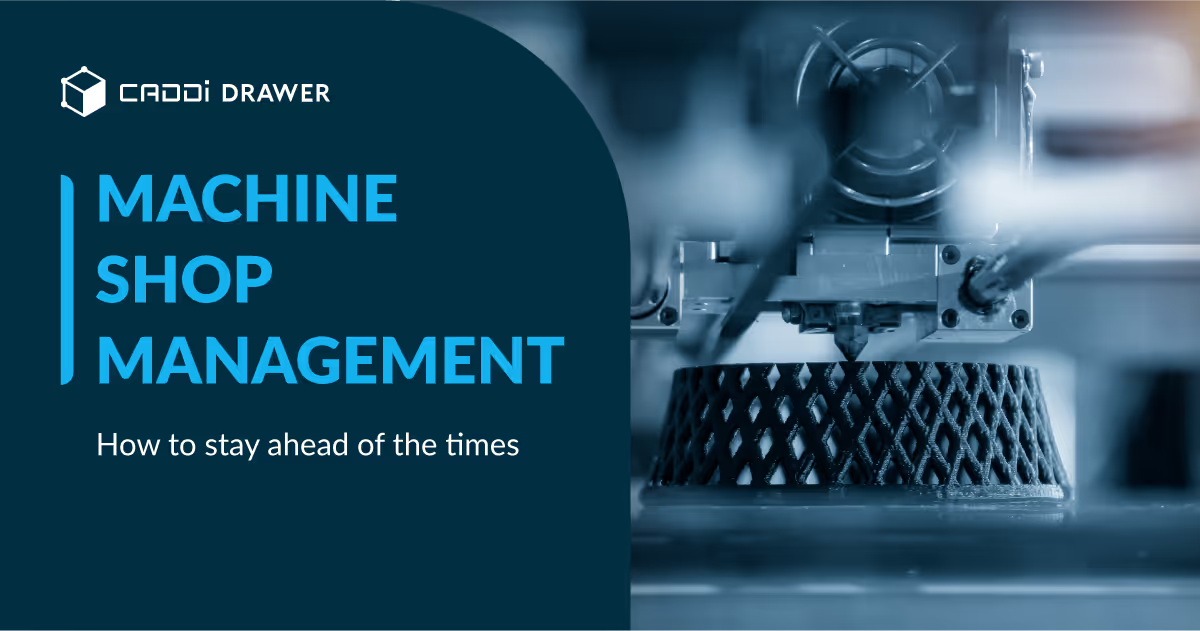