Streamlining Manufacturing: How Fixture Design Can Optimize Your Fabrication Process
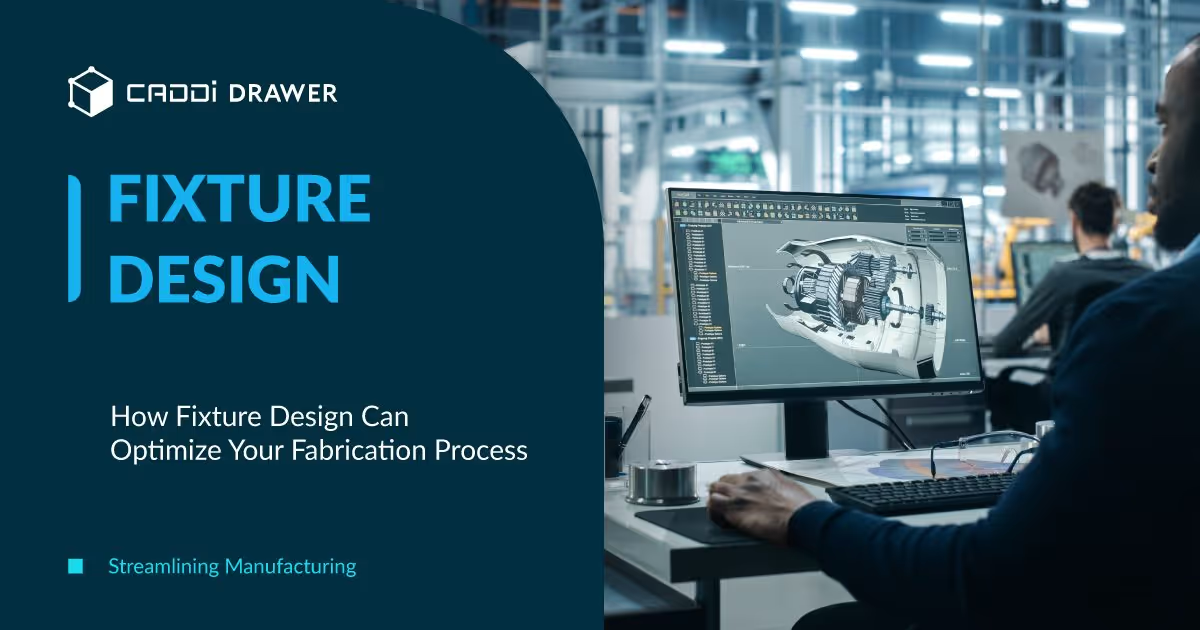
Table of Contents
What is Fixture Design?
Fixture design is a crucial aspect of manufacturing and fabrication processes. A fixture refers to a workholding device that rigidly holds a workpiece in position during manufacturing operations such as machining, welding, assembly, or inspection. Proper fixture design ensures accuracy, precision, safety and efficiency in production.
Fixtures play a vital role in holding workpieces securely and accurately in relation to the cutting tool or measuring device. This minimizes errors, prevents damage to the workpiece, and results in consistent and high-quality finished products. Additionally, fixtures reduce labor time by eliminating the need to manually position and clamp the workpiece for each operation. The fixture designer must have in-depth knowledge of manufacturing processes, materials, and quality control to create effective fixtures suited to the particular workpiece and fabrication methods.
Goals of Fixture Design
Accuracy and precision are primary goals in fixture design. The fixture must securely hold the workpiece in the correct orientation and position for the machining operations to produce parts to precise specifications. Any movement or vibration during machining will negatively impact tolerances.
Operator safety is also a key consideration. The fixture design should eliminate pinch points and sharp edges. It must prevent the workpiece from slipping or coming loose to avoid potential operator injury.
Ease of operation goes hand-in-hand with safety. The fixtures should allow quick, ergonomic loading and unloading of workpieces to maximize productivity. Simple, mistake-proof designs help reduce cycle times. Easy access for measurement and inspection is also important.
Well-designed fixtures make it effortless for the operator to repeatedly position workpieces accurately. This results in higher quality parts produced faster and more safely.
Types of Fixtures
There are three main types of fixtures used in manufacturing:
General fixtures
General fixtures are specially designed devices that firmly secure the workpiece in a set location and orientation, acting as the platform for manufacturing operations. They precisely locate a part in relation to the cutting tool or measuring device. They provide repeatability and interchangeability to facilitate high-volume production. General fixtures impose restraints on the movement of the workpiece, creating stability needed for operations like inspection, welding, assembly, marking or machining.
Jigs
A jig is a type of custom-made tool used to produce identical, interchangeable parts. Jigs provide repeatability, accuracy and interchangeability in the manufacturing process. Jigs securely hold a part and guides the cutting tool. By providing precision and rigidity, jigs produce high quality, uniform products. Jigs are commonly used for repetitive drilling, boring, tapping, reaming, and milling operations.
Mandrels
A mandrel is a tapered or cylindrical shaft used for holding workpieces while manufacturing symmetric parts. Mandrels expand workpiece openings allowing uniform and concentric machining. They provide a firm, stable base for the piece to be shaped around. Mandrels are commonly used in applications like gear manufacturing, metal spinning, and tube bending. They assist in achieving correct shape, size and surface finish.
Elements of Fixture Design
Effective fixture design requires carefully considering and incorporating key elements that enable the fixture to properly locate, support and hold the workpiece during manufacturing operations. The main elements of fixture design include:
Locating Points
- Locating points position and locate the workpiece in the correct orientation and alignment for machining and fabrication operations. They are the main reference points for establishing part position.
- 3-2-1 location is a common principle used to fully constrain a part with a minimum number of points. It involves 3 points to locate the part’s position along the X, Y and Z axes, 2 points to locate orientation around the Z axis, and 1 point to prevent rotation around the X and Y axes.
- Locating points are positioned to contact the machined surfaces of the part, not the raw stock surfaces.
- They should be as close to the cutting tool area as possible to maximize accuracy and rigidity.
Clamping Devices
- Clamps apply forces to rigidly hold the workpiece against the locating points and prevent movement during cutting, drilling and other operations.
- Different types of clamps include strap clamps, wedge clamps, swing clamps, toggle clamps, and hydraulic or pneumatic clamps.
- Clamps must provide adequate force but not apply excessive pressure that can distort the part. Clamp placement is also key.
- Quick-acting clamps allow faster loading and unloading of parts to minimize cycle times.
Tool Guiding Elements
- Tool guides direct and position cutting tools, drill bits, and other implements to ensure they approach the part properly and follow the right machining paths.
- Common tool guiding elements include jigs, fixtures plates, bushes, and tool holders positioned around the workpiece.
- Tool guides provide support very close to the machining operation for maximum accuracy. Their design depends on the type of operation, tools, and optimal approach angles.
Material Considerations
When designing fixtures, choosing the right materials is crucial for creating a fixture that can withstand the rigors of manufacturing while keeping costs down. The material used for fixtures must have sufficient strength, wear resistance, and corrosion resistance.
- Strength – The fixture must be strong enough to hold the workpiece securely in position without deforming or breaking. The material must have high yield and tensile strength to withstand clamping forces and cutting forces during machining.
- Wear resistance – Fixtures undergo significant wear during use. The points where the workpiece contacts the fixture experience friction that can erode the material over time. Materials that resist wear, like tool steel, can prolong the usable life of the fixture.
- Corrosion resistance – Exposure to coolants, oils, and water can cause fixtures to corrode. Using corrosion-resistant materials like stainless steel helps prevent seizing, sticking, and contamination issues caused by rust buildup.
Selecting durable materials that meet the demands of the manufacturing process is key to creating effective, long-lasting fixtures. Strength, wear resistance, and corrosion resistance should all factor into the decision.
Components of Fixtures
Fixtures are made up of various standard components that work together to securely hold the workpiece. The main components are:
- Bases – The base provides a foundation for the fixture and is mounted to the machine table. It maintains the overall structure and position of the fixture components. Common bases include plates, angles, t-slots, and cast iron blocks.
- Locators – Locators position and locate the workpiece in the correct orientation within the fixture. Locators only restrain the workpiece in certain degrees of freedom. Common locators include round pins, diamond pins, buttons, edges, and nests.
- Clamps – Clamps apply forces to clamp and hold the workpiece securely against the locators. Common clamps include strap clamps, wedge clamps, eccentric cams, toggle clamps, and hydraulic clamping.
- Other Components – Other standard components include jacks and risers for adjusting the height of the fixture, bushings and liners to adapt parts of the fixture, screws and bolts to hold components together, and stops to position movable components of the fixture.
Proper selection and positioning of these standard components is crucial for an effective fixture design. The components must work together to hold the workpiece rigidly without deformation while allowing the necessary machining operations.
Design Process
The design process for a fixture involves several key steps:
- Analyze the workpiece – Thoroughly examine the workpiece geometry, required tolerances, amount of material removal needed, and other specifications. This analysis guides decisions on locating points, clamping, and other components.
- Determine locating points – Choose appropriate points on the workpiece to locate it precisely and repeatedly in the fixture. Common locating principles include 3-2-1 location, 6 point location, and divot location.
- Design the clamping system – Select clamps, supports, and pressure mechanisms to securely hold the workpiece without deformation. Consider the forces involved, accessibility for loading/unloading, and potential clamp interference.
- Add other components – Incorporate additional elements as needed for material handling, chip control, lubrication, safety guards, instrumentation, and more. Standardize components when possible.
- Refine and optimize – Evaluate the fixture design via CAD modeling, FEA analysis, machining simulations, and/or prototyping. Refine the design to improve machining performance, safety, longevity, and other factors.
- Documentation – Create detailed drawings, schematics, setup instructions, and specifications to guide fixture fabrication and use on the shop floor. Thorough documentation enables consistent, high-quality fixture replication and operation.
Trends in Fixture Design
The fixture design field continues to evolve as new technologies emerge. Some key trends shaping the future of fixture design include:
- Greater automation – To speed up fixture design and manufacturing, more companies are utilizing automated design software and additive manufacturing. This enables faster iteration and adjustments to fixtures.
- Use of new materials – Newer materials like composites and plastics are gaining popularity for fixtures due to their durability, lightweight nature, and ease of manufacture compared to traditional metal fixtures. The use of new materials allows designers more flexibility.
- Focus on flexibility – There is a rising focus on designing modular, adjustable, and flexible fixtures that can accommodate design changes and product variation. Quick change tooling and fixturing allows reconfiguration and adaption for mixed model production.
Conclusion
Overall, fixture design is an integral engineering task that enables mass-production and automation in manufacturing. Correct fixtures directly impact product quality, productivity and costs. Investing in good fixture design ultimately results in significant savings of time, effort and expenses in the long run. This makes fixture design expertise highly valuable in fabrication and machining industries.
What is Fixture Design?
Fixture design is a crucial aspect of manufacturing and fabrication processes. A fixture refers to a workholding device that rigidly holds a workpiece in position during manufacturing operations such as machining, welding, assembly, or inspection. Proper fixture design ensures accuracy, precision, safety and efficiency in production.
Fixtures play a vital role in holding workpieces securely and accurately in relation to the cutting tool or measuring device. This minimizes errors, prevents damage to the workpiece, and results in consistent and high-quality finished products. Additionally, fixtures reduce labor time by eliminating the need to manually position and clamp the workpiece for each operation. The fixture designer must have in-depth knowledge of manufacturing processes, materials, and quality control to create effective fixtures suited to the particular workpiece and fabrication methods.
Goals of Fixture Design
Accuracy and precision are primary goals in fixture design. The fixture must securely hold the workpiece in the correct orientation and position for the machining operations to produce parts to precise specifications. Any movement or vibration during machining will negatively impact tolerances.
Operator safety is also a key consideration. The fixture design should eliminate pinch points and sharp edges. It must prevent the workpiece from slipping or coming loose to avoid potential operator injury.
Ease of operation goes hand-in-hand with safety. The fixtures should allow quick, ergonomic loading and unloading of workpieces to maximize productivity. Simple, mistake-proof designs help reduce cycle times. Easy access for measurement and inspection is also important.
Well-designed fixtures make it effortless for the operator to repeatedly position workpieces accurately. This results in higher quality parts produced faster and more safely.
Types of Fixtures
There are three main types of fixtures used in manufacturing:
General fixtures
General fixtures are specially designed devices that firmly secure the workpiece in a set location and orientation, acting as the platform for manufacturing operations. They precisely locate a part in relation to the cutting tool or measuring device. They provide repeatability and interchangeability to facilitate high-volume production. General fixtures impose restraints on the movement of the workpiece, creating stability needed for operations like inspection, welding, assembly, marking or machining.
Jigs
A jig is a type of custom-made tool used to produce identical, interchangeable parts. Jigs provide repeatability, accuracy and interchangeability in the manufacturing process. Jigs securely hold a part and guides the cutting tool. By providing precision and rigidity, jigs produce high quality, uniform products. Jigs are commonly used for repetitive drilling, boring, tapping, reaming, and milling operations.
Mandrels
A mandrel is a tapered or cylindrical shaft used for holding workpieces while manufacturing symmetric parts. Mandrels expand workpiece openings allowing uniform and concentric machining. They provide a firm, stable base for the piece to be shaped around. Mandrels are commonly used in applications like gear manufacturing, metal spinning, and tube bending. They assist in achieving correct shape, size and surface finish.
Elements of Fixture Design
Effective fixture design requires carefully considering and incorporating key elements that enable the fixture to properly locate, support and hold the workpiece during manufacturing operations. The main elements of fixture design include:
Locating Points
- Locating points position and locate the workpiece in the correct orientation and alignment for machining and fabrication operations. They are the main reference points for establishing part position.
- 3-2-1 location is a common principle used to fully constrain a part with a minimum number of points. It involves 3 points to locate the part’s position along the X, Y and Z axes, 2 points to locate orientation around the Z axis, and 1 point to prevent rotation around the X and Y axes.
- Locating points are positioned to contact the machined surfaces of the part, not the raw stock surfaces.
- They should be as close to the cutting tool area as possible to maximize accuracy and rigidity.
Clamping Devices
- Clamps apply forces to rigidly hold the workpiece against the locating points and prevent movement during cutting, drilling and other operations.
- Different types of clamps include strap clamps, wedge clamps, swing clamps, toggle clamps, and hydraulic or pneumatic clamps.
- Clamps must provide adequate force but not apply excessive pressure that can distort the part. Clamp placement is also key.
- Quick-acting clamps allow faster loading and unloading of parts to minimize cycle times.
Tool Guiding Elements
- Tool guides direct and position cutting tools, drill bits, and other implements to ensure they approach the part properly and follow the right machining paths.
- Common tool guiding elements include jigs, fixtures plates, bushes, and tool holders positioned around the workpiece.
- Tool guides provide support very close to the machining operation for maximum accuracy. Their design depends on the type of operation, tools, and optimal approach angles.
Material Considerations
When designing fixtures, choosing the right materials is crucial for creating a fixture that can withstand the rigors of manufacturing while keeping costs down. The material used for fixtures must have sufficient strength, wear resistance, and corrosion resistance.
- Strength – The fixture must be strong enough to hold the workpiece securely in position without deforming or breaking. The material must have high yield and tensile strength to withstand clamping forces and cutting forces during machining.
- Wear resistance – Fixtures undergo significant wear during use. The points where the workpiece contacts the fixture experience friction that can erode the material over time. Materials that resist wear, like tool steel, can prolong the usable life of the fixture.
- Corrosion resistance – Exposure to coolants, oils, and water can cause fixtures to corrode. Using corrosion-resistant materials like stainless steel helps prevent seizing, sticking, and contamination issues caused by rust buildup.
Selecting durable materials that meet the demands of the manufacturing process is key to creating effective, long-lasting fixtures. Strength, wear resistance, and corrosion resistance should all factor into the decision.
Components of Fixtures
Fixtures are made up of various standard components that work together to securely hold the workpiece. The main components are:
- Bases – The base provides a foundation for the fixture and is mounted to the machine table. It maintains the overall structure and position of the fixture components. Common bases include plates, angles, t-slots, and cast iron blocks.
- Locators – Locators position and locate the workpiece in the correct orientation within the fixture. Locators only restrain the workpiece in certain degrees of freedom. Common locators include round pins, diamond pins, buttons, edges, and nests.
- Clamps – Clamps apply forces to clamp and hold the workpiece securely against the locators. Common clamps include strap clamps, wedge clamps, eccentric cams, toggle clamps, and hydraulic clamping.
- Other Components – Other standard components include jacks and risers for adjusting the height of the fixture, bushings and liners to adapt parts of the fixture, screws and bolts to hold components together, and stops to position movable components of the fixture.
Proper selection and positioning of these standard components is crucial for an effective fixture design. The components must work together to hold the workpiece rigidly without deformation while allowing the necessary machining operations.
Design Process
The design process for a fixture involves several key steps:
- Analyze the workpiece – Thoroughly examine the workpiece geometry, required tolerances, amount of material removal needed, and other specifications. This analysis guides decisions on locating points, clamping, and other components.
- Determine locating points – Choose appropriate points on the workpiece to locate it precisely and repeatedly in the fixture. Common locating principles include 3-2-1 location, 6 point location, and divot location.
- Design the clamping system – Select clamps, supports, and pressure mechanisms to securely hold the workpiece without deformation. Consider the forces involved, accessibility for loading/unloading, and potential clamp interference.
- Add other components – Incorporate additional elements as needed for material handling, chip control, lubrication, safety guards, instrumentation, and more. Standardize components when possible.
- Refine and optimize – Evaluate the fixture design via CAD modeling, FEA analysis, machining simulations, and/or prototyping. Refine the design to improve machining performance, safety, longevity, and other factors.
- Documentation – Create detailed drawings, schematics, setup instructions, and specifications to guide fixture fabrication and use on the shop floor. Thorough documentation enables consistent, high-quality fixture replication and operation.
Trends in Fixture Design
The fixture design field continues to evolve as new technologies emerge. Some key trends shaping the future of fixture design include:
- Greater automation – To speed up fixture design and manufacturing, more companies are utilizing automated design software and additive manufacturing. This enables faster iteration and adjustments to fixtures.
- Use of new materials – Newer materials like composites and plastics are gaining popularity for fixtures due to their durability, lightweight nature, and ease of manufacture compared to traditional metal fixtures. The use of new materials allows designers more flexibility.
- Focus on flexibility – There is a rising focus on designing modular, adjustable, and flexible fixtures that can accommodate design changes and product variation. Quick change tooling and fixturing allows reconfiguration and adaption for mixed model production.
Conclusion
Overall, fixture design is an integral engineering task that enables mass-production and automation in manufacturing. Correct fixtures directly impact product quality, productivity and costs. Investing in good fixture design ultimately results in significant savings of time, effort and expenses in the long run. This makes fixture design expertise highly valuable in fabrication and machining industries.
Ready to see CADDi Drawer in action? Get a personalized demo.
Subscribe to our Blog!
Related Resources
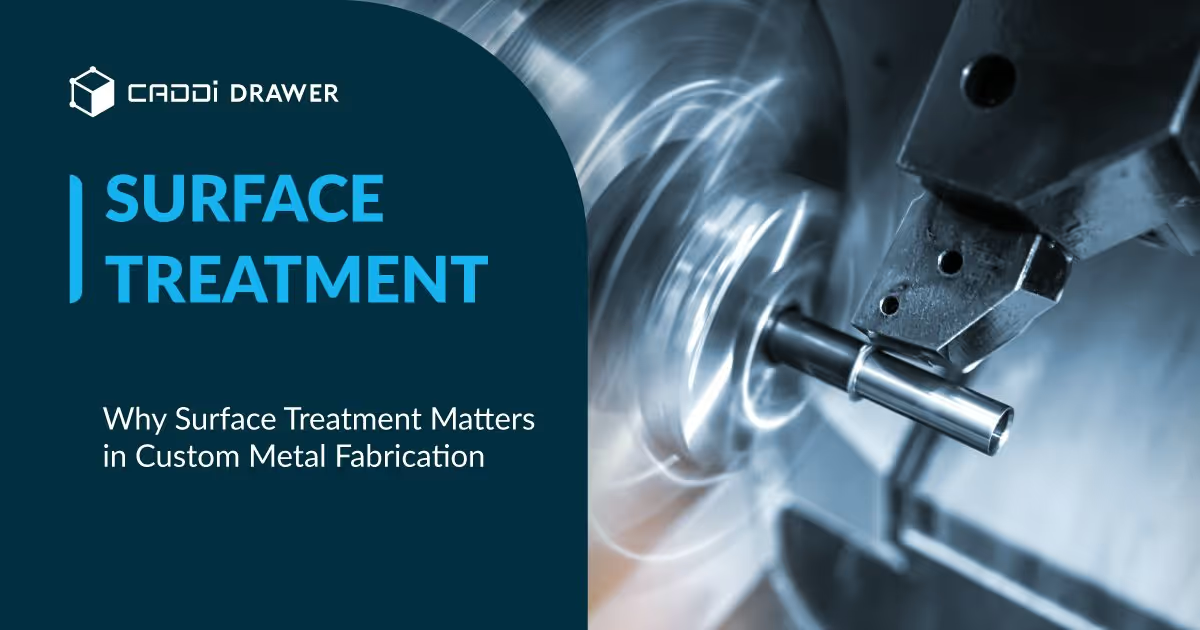
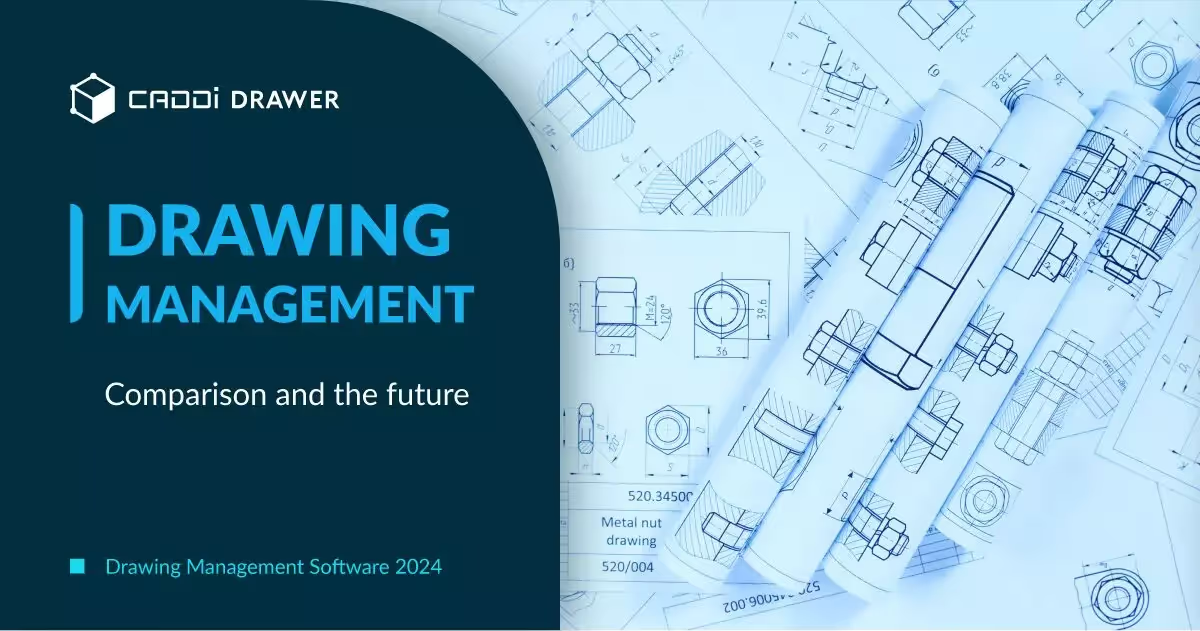

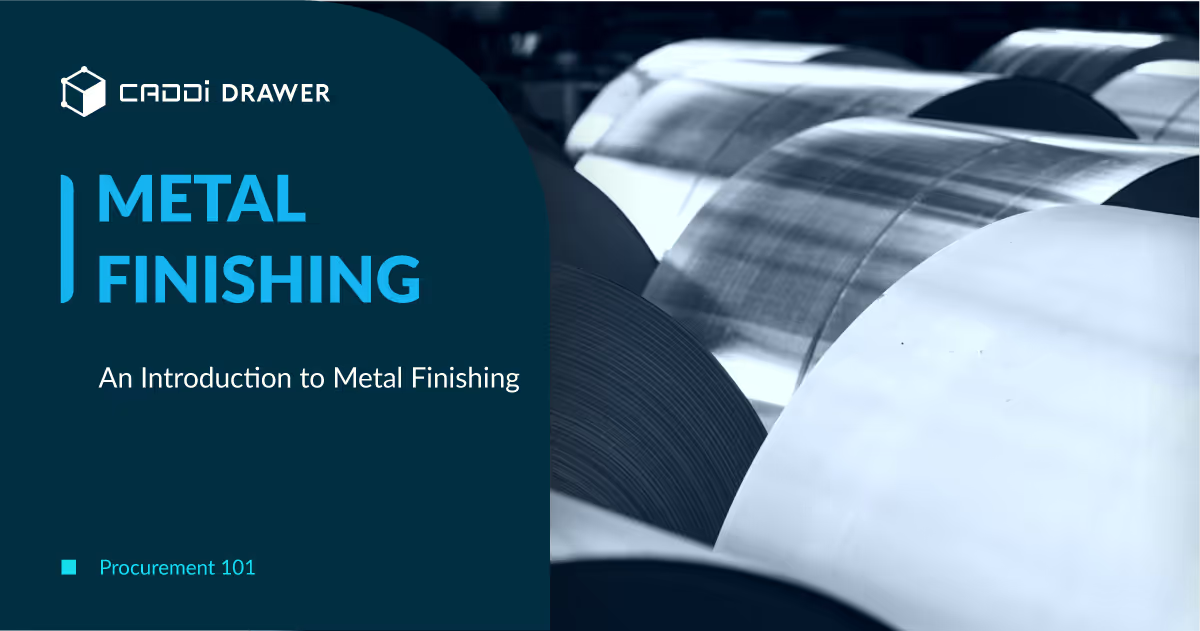
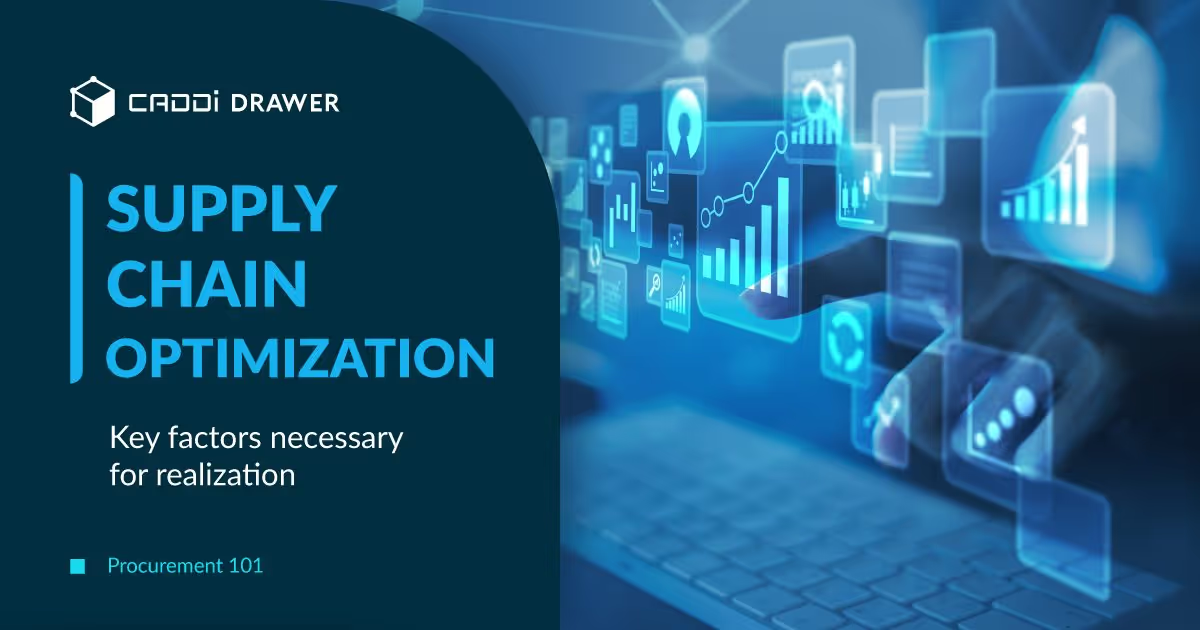
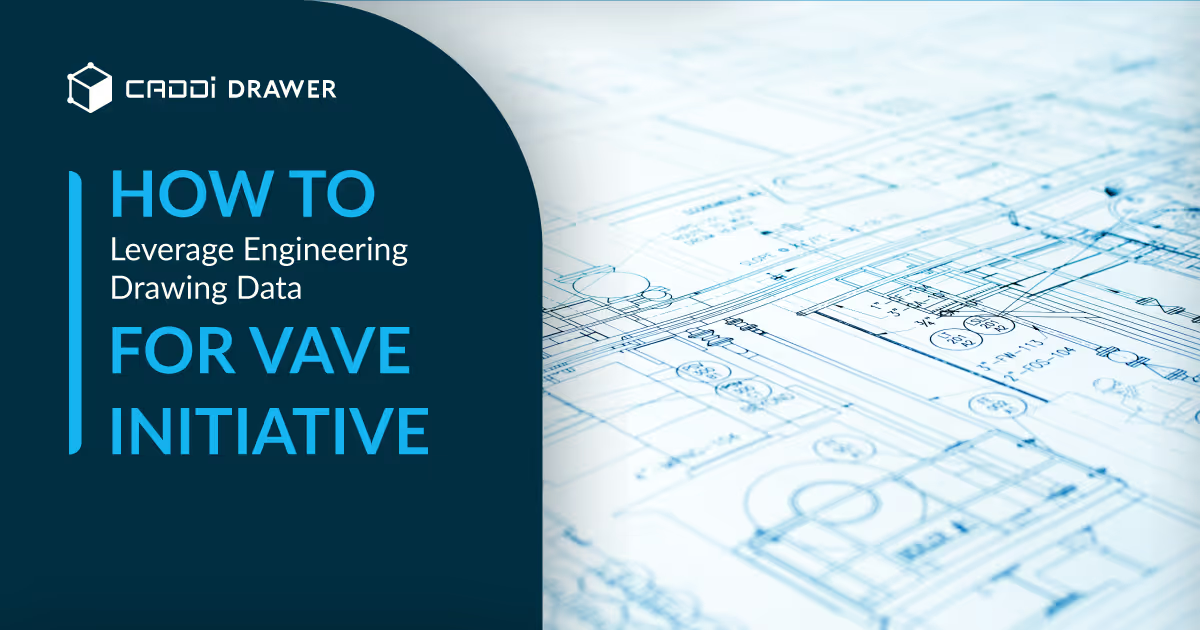