An Inside Look at the Engineering Process

Table of Contents
The engineering process is a series of steps that guides the development and manufacturing of products in the industry. It involves translating design concepts into physical products efficiently through planning, prototyping, testing, production, and product launch.
It takes an idea for a product and uses scientific principles, technical knowledge, and experience to design, develop, and deploy it. It is an iterative process, meaning improvements are made in a cyclical fashion as more is learned throughout the phases. The end goal is to create quality products that meet specifications in a systematic, cost-effective way.
Key Stages of Engineering Process
There are typically five high-level stages in the engineering process for manufactured goods:
- Product design – The specifications and technical drawings are created to meet customer requirements.
- Process design – The manufacturing process itself is designed, including equipment, tooling, quality control, etc.
- Production – Raw materials are sourced and used to mass produce the product according to the engineering plans.
- Testing & refinement – Products are tested to ensure they meet requirements, with tweaks made as needed.
- Product launch – The finished product is released to customers once standards are met.
Proper application of the engineering process allows companies to maximize efficiency, reduce costs, and deliver quality goods at scale. It blends innovation with practical development grounded in science and technology. For any manufactured product, the engineering process is crucial for translating ideas into optimized physical forms.
Next, let us explain each stage in order.
Product Design
The product design process is critical in manufacturing as it determines the look, function and specifications of a product before it heads into production. Industrial designers work closely with engineers and marketers to ideate and iterate on product designs that meet customer needs and can be reliably produced.
Key aspects of product design include:
- Industrial Design This involves coming up with the aesthetic design of a product, including its shape, color, texture, sounds and feel. Industrial designers create sketches, 3D models, prototypes and renderings to visualize and refine the product design. The goal is to make the product visually appealing and intuitive for customers to use.
- Prototyping – Prototypes allow designers and engineers to test product concepts and get feedback before committing to full production. There are various prototyping techniques from 3D printing, CNC machining to virtual simulations. Building multiple prototypes enables iterative improvement of the design.
- Specifications – The product specifications serve as technical requirements that the product must meet. This includes dimensions, materials, performance criteria, regulatory compliance and other technical details that enable manufacturing.
- CAD Models – CAD software is used to create digital 3D models that fully define the product design in an engineering format. The CAD files provide the inputs for programming automated production equipment.
Getting the product design right ensures that the final manufactured product will meet customer expectations while being producible at scale. This upfront engineering work is essential for an efficient overall manufacturing process.
Process Design
Process design is a critical step in manufacturing engineering where the actual production processes and tooling are developed. This involves determining the optimal workflow and methods to transform raw materials into finished products.
The process design team maps out each step of the manufacturing process, from receiving raw materials to final packaging of the product. They analyze the product requirements and production volumes to design efficient workflows that maximize productivity and quality.
Some key aspects of process design include:
- Selecting production methods such as casting, machining, injection molding, etc. based on product specifications, materials used, and production volumes. CNC machining may be ideal for low volume production while injection molding works better for mass production.
- Designing fixtures, jigs, tools, molds, and dies to enable the production processes. This requires engineering expertise to create tooling that forms, holds, and assembles component parts precisely and repeatedly.
- Determining optimal equipment layout and material flow to create efficient production lines or cells. This includes deciding on automated vs manual processes and the logistics for moving materials between workstations.
- Integrating quality control points throughout the process, such as inspections, tests, and measurements to catch defects early on.
- Considering health and safety factors involved in operating the designed processes, such as points requiring personal protective equipment.
- Validating and optimizing the designed processes through prototyping, testing, and simulations before full scale production.
The process design team works closely with product designers, automation engineers, and other groups to develop robust production processes that result in high quality, cost-effective manufacturing.
Production
Production is the stage where the actual products are mass-produced in the factory based on the finalized product design and engineered manufacturing processes.
Some key aspects of production include:
- Material preparation – Sourcing and preparing the raw materials needed to make the product, ensuring they meet quality standards and are ready for production.
- Equipment setup – Setting up the production lines, work cells, equipment, and tooling based on the process design to enable efficient manufacturing.
- Manufacturing execution – Executing the designed manufacturing processes to fabricate individual components and assemble the final products.
- Quality control – Conducting in-process quality checks and testing to identify and address any production issues or defects.
Efficient and well-controlled production is crucial to manufacture products at the required volumes, quality levels, and costs to meet business objectives.
Testing & Refinement
Testing and refinement is the stage where finished products from production undergo thorough validation to ensure they meet all functional and quality requirements before being released to customers.
Some key aspects of testing and refinement include:
- Product inspection – Visually inspecting products for any cosmetic defects, surface flaws, or blemishes and removing defective units.
- Functional testing – Rigorously testing the functionality and performance of products against specifications and requirements.
- Reliability testing – Conducting tests that simulate real-world use conditions over time to validate product reliability and durability.
- Design refinements – Analyzing test results and customer feedback to identify opportunities for refining product designs or production processes.
- Regulatory compliance – Verifying that products meet all applicable regulatory standards and obtaining required certifications.
Through iterative cycles of testing and refinement, the product is optimized to a high level of quality and performance that is ready for customer use.
Product Launch
The product launch is the final stage where validated products are released to the market, promoted to customers, and transitioned to ongoing sales and support.
Some key aspects of product launch include:
- Production ramp-up – Increasing production volumes and preparing inventory to meet expected customer demand for the new product.
- Marketing preparation – Developing marketing content, product demos, and sales collateral to effectively promote the new product to target customers.
- Sales and distribution – Selling, distributing, and shipping products to customers, resellers, and distributors through established channels.
- Training and support – Training sales, support, and service staff on the new product and preparing them to assist customers effectively.
- Launch monitoring – Closely monitoring initial sales, customer feedback, and quality metrics to gauge the success of the product launch and quickly respond to any issues.
A successful product launch generates strong customer demand, positive market reception, and lays the foundation for ongoing growth and profitability.
Closing Summary
In this article, we examined the engineering process used to develop and manufacture products:
Proper engineering across all these stages is critical to create innovative, cost-effective, and high-quality products at scale. The engineering process blends creativity, scientific knowledge, and practical problem-solving to transform ideas into successful commercial goods.
By following a disciplined engineering approach, companies can efficiently launch compelling products that delight customers and drive business growth. The end result of a well-executed engineering process is a successful product in the hands of satisfied customers.
The engineering process is a series of steps that guides the development and manufacturing of products in the industry. It involves translating design concepts into physical products efficiently through planning, prototyping, testing, production, and product launch.
It takes an idea for a product and uses scientific principles, technical knowledge, and experience to design, develop, and deploy it. It is an iterative process, meaning improvements are made in a cyclical fashion as more is learned throughout the phases. The end goal is to create quality products that meet specifications in a systematic, cost-effective way.
Key Stages of Engineering Process
There are typically five high-level stages in the engineering process for manufactured goods:
- Product design – The specifications and technical drawings are created to meet customer requirements.
- Process design – The manufacturing process itself is designed, including equipment, tooling, quality control, etc.
- Production – Raw materials are sourced and used to mass produce the product according to the engineering plans.
- Testing & refinement – Products are tested to ensure they meet requirements, with tweaks made as needed.
- Product launch – The finished product is released to customers once standards are met.
Proper application of the engineering process allows companies to maximize efficiency, reduce costs, and deliver quality goods at scale. It blends innovation with practical development grounded in science and technology. For any manufactured product, the engineering process is crucial for translating ideas into optimized physical forms.
Next, let us explain each stage in order.
Product Design
The product design process is critical in manufacturing as it determines the look, function and specifications of a product before it heads into production. Industrial designers work closely with engineers and marketers to ideate and iterate on product designs that meet customer needs and can be reliably produced.
Key aspects of product design include:
- Industrial Design This involves coming up with the aesthetic design of a product, including its shape, color, texture, sounds and feel. Industrial designers create sketches, 3D models, prototypes and renderings to visualize and refine the product design. The goal is to make the product visually appealing and intuitive for customers to use.
- Prototyping – Prototypes allow designers and engineers to test product concepts and get feedback before committing to full production. There are various prototyping techniques from 3D printing, CNC machining to virtual simulations. Building multiple prototypes enables iterative improvement of the design.
- Specifications – The product specifications serve as technical requirements that the product must meet. This includes dimensions, materials, performance criteria, regulatory compliance and other technical details that enable manufacturing.
- CAD Models – CAD software is used to create digital 3D models that fully define the product design in an engineering format. The CAD files provide the inputs for programming automated production equipment.
Getting the product design right ensures that the final manufactured product will meet customer expectations while being producible at scale. This upfront engineering work is essential for an efficient overall manufacturing process.
Process Design
Process design is a critical step in manufacturing engineering where the actual production processes and tooling are developed. This involves determining the optimal workflow and methods to transform raw materials into finished products.
The process design team maps out each step of the manufacturing process, from receiving raw materials to final packaging of the product. They analyze the product requirements and production volumes to design efficient workflows that maximize productivity and quality.
Some key aspects of process design include:
- Selecting production methods such as casting, machining, injection molding, etc. based on product specifications, materials used, and production volumes. CNC machining may be ideal for low volume production while injection molding works better for mass production.
- Designing fixtures, jigs, tools, molds, and dies to enable the production processes. This requires engineering expertise to create tooling that forms, holds, and assembles component parts precisely and repeatedly.
- Determining optimal equipment layout and material flow to create efficient production lines or cells. This includes deciding on automated vs manual processes and the logistics for moving materials between workstations.
- Integrating quality control points throughout the process, such as inspections, tests, and measurements to catch defects early on.
- Considering health and safety factors involved in operating the designed processes, such as points requiring personal protective equipment.
- Validating and optimizing the designed processes through prototyping, testing, and simulations before full scale production.
The process design team works closely with product designers, automation engineers, and other groups to develop robust production processes that result in high quality, cost-effective manufacturing.
Production
Production is the stage where the actual products are mass-produced in the factory based on the finalized product design and engineered manufacturing processes.
Some key aspects of production include:
- Material preparation – Sourcing and preparing the raw materials needed to make the product, ensuring they meet quality standards and are ready for production.
- Equipment setup – Setting up the production lines, work cells, equipment, and tooling based on the process design to enable efficient manufacturing.
- Manufacturing execution – Executing the designed manufacturing processes to fabricate individual components and assemble the final products.
- Quality control – Conducting in-process quality checks and testing to identify and address any production issues or defects.
Efficient and well-controlled production is crucial to manufacture products at the required volumes, quality levels, and costs to meet business objectives.
Testing & Refinement
Testing and refinement is the stage where finished products from production undergo thorough validation to ensure they meet all functional and quality requirements before being released to customers.
Some key aspects of testing and refinement include:
- Product inspection – Visually inspecting products for any cosmetic defects, surface flaws, or blemishes and removing defective units.
- Functional testing – Rigorously testing the functionality and performance of products against specifications and requirements.
- Reliability testing – Conducting tests that simulate real-world use conditions over time to validate product reliability and durability.
- Design refinements – Analyzing test results and customer feedback to identify opportunities for refining product designs or production processes.
- Regulatory compliance – Verifying that products meet all applicable regulatory standards and obtaining required certifications.
Through iterative cycles of testing and refinement, the product is optimized to a high level of quality and performance that is ready for customer use.
Product Launch
The product launch is the final stage where validated products are released to the market, promoted to customers, and transitioned to ongoing sales and support.
Some key aspects of product launch include:
- Production ramp-up – Increasing production volumes and preparing inventory to meet expected customer demand for the new product.
- Marketing preparation – Developing marketing content, product demos, and sales collateral to effectively promote the new product to target customers.
- Sales and distribution – Selling, distributing, and shipping products to customers, resellers, and distributors through established channels.
- Training and support – Training sales, support, and service staff on the new product and preparing them to assist customers effectively.
- Launch monitoring – Closely monitoring initial sales, customer feedback, and quality metrics to gauge the success of the product launch and quickly respond to any issues.
A successful product launch generates strong customer demand, positive market reception, and lays the foundation for ongoing growth and profitability.
Closing Summary
In this article, we examined the engineering process used to develop and manufacture products:
Proper engineering across all these stages is critical to create innovative, cost-effective, and high-quality products at scale. The engineering process blends creativity, scientific knowledge, and practical problem-solving to transform ideas into successful commercial goods.
By following a disciplined engineering approach, companies can efficiently launch compelling products that delight customers and drive business growth. The end result of a well-executed engineering process is a successful product in the hands of satisfied customers.
Ready to see CADDi Drawer in action? Get a personalized demo.
Subscribe to our Blog!
Related Resources
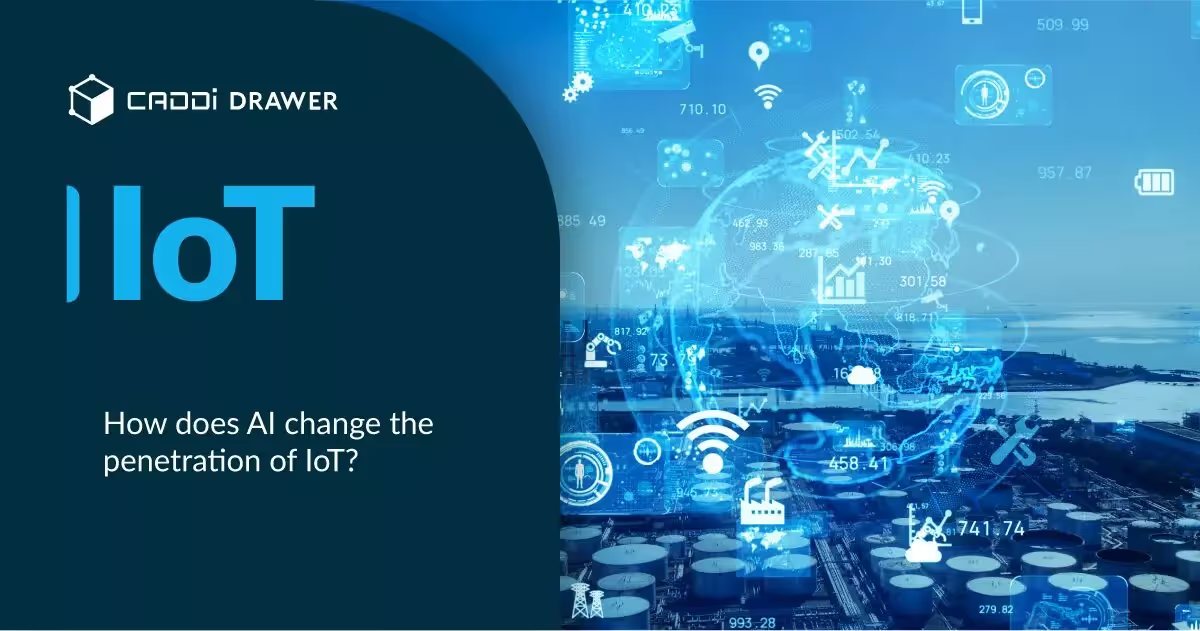
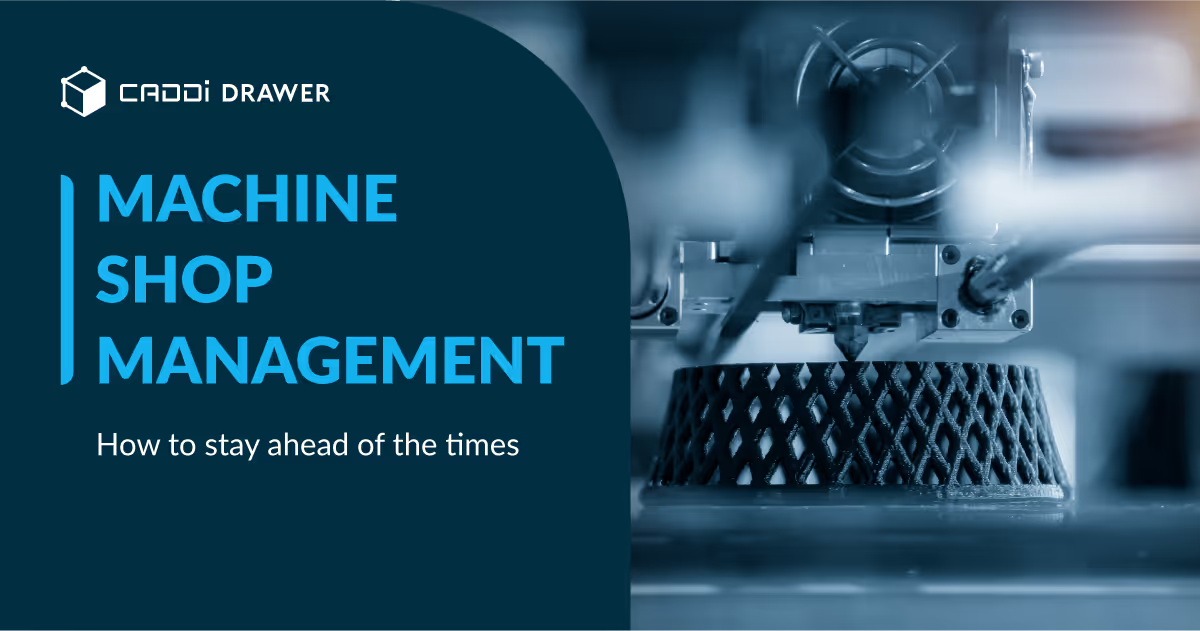
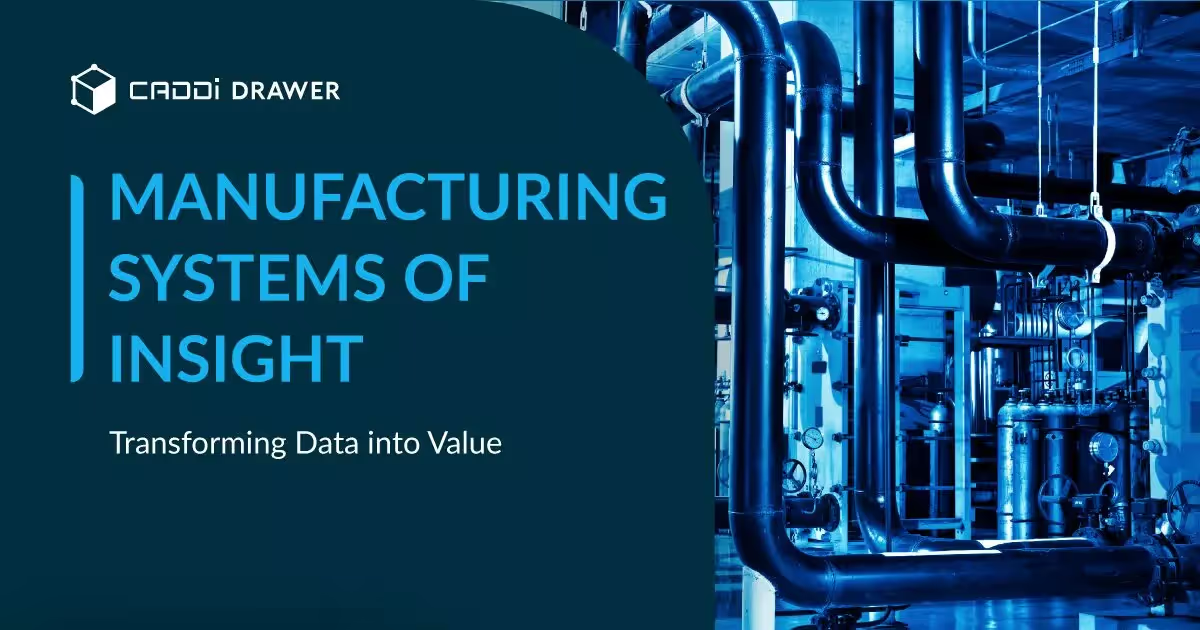
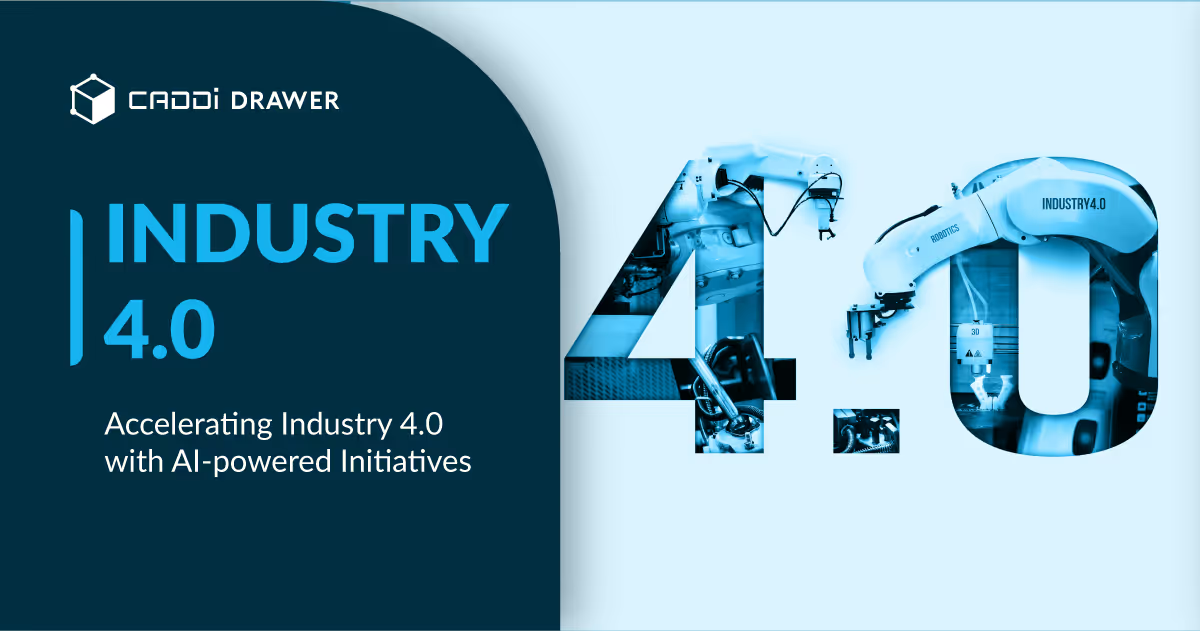
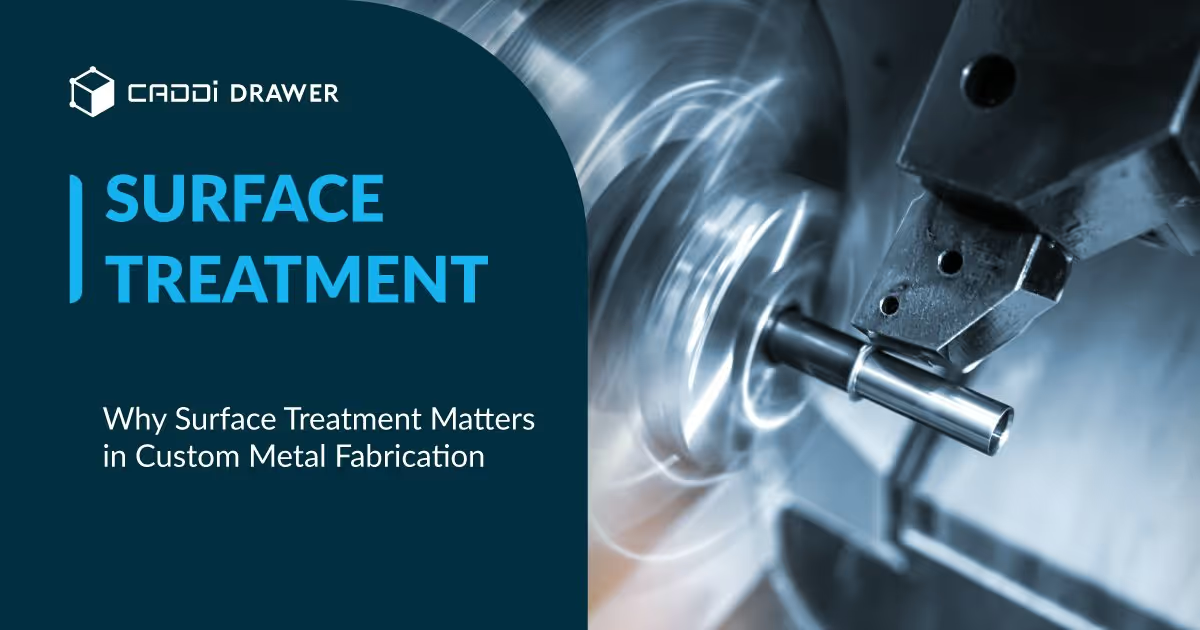
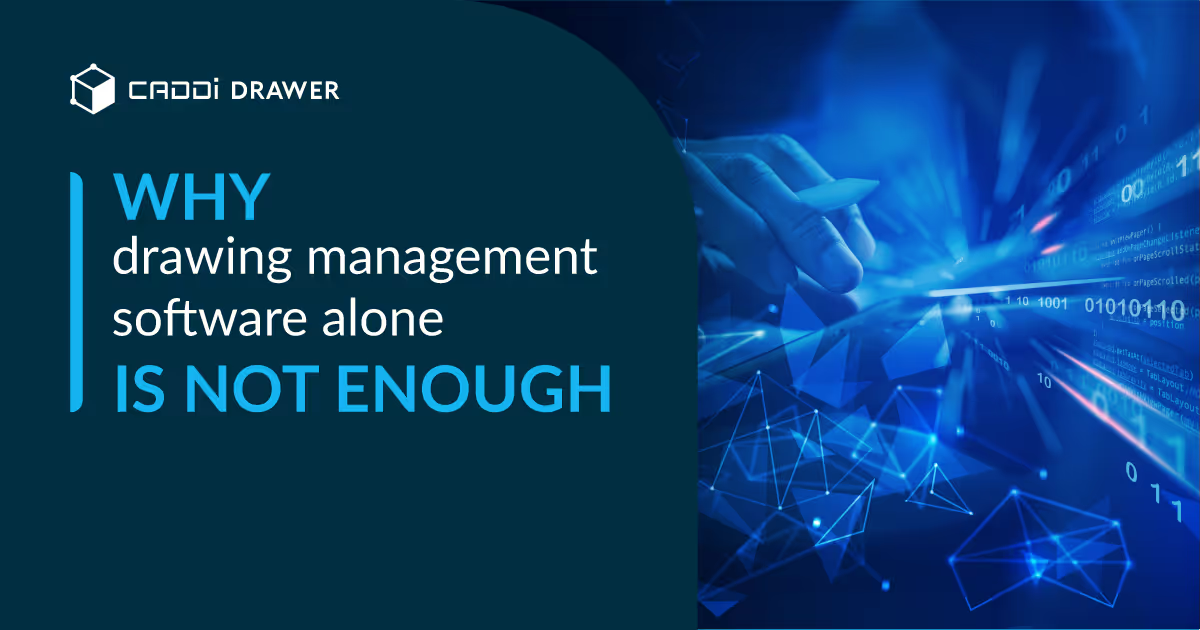