Work Order Management Optimization: Harnessing Manufacturing Prowess
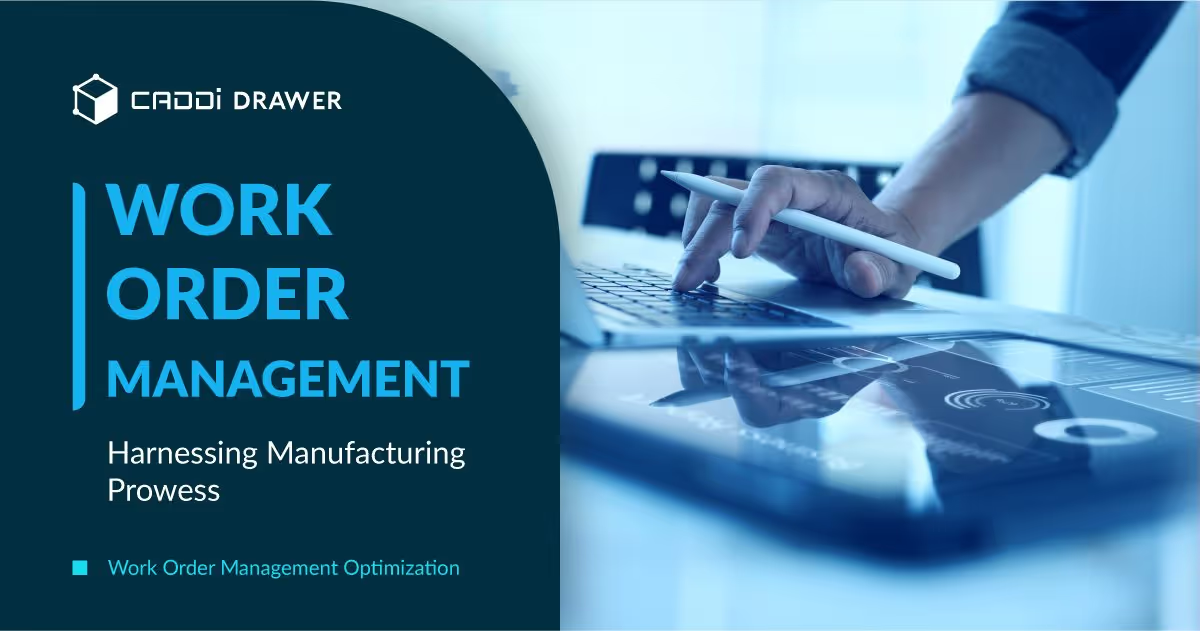
Table of Contents
For manufacturers, the ability to manage work orders efficiently is more than a necessity—it’s a strategic advantage. Work order management encompasses the planning, tracking, and execution of manufacturing tasks and maintenance operations, forming the backbone of a successful production line. This blog post aims to shed light on optimal work order management practices, identifying common challenges and providing actionable solutions. It serves as a guide for manufacturers keen on refining their operations, enhancing productivity, and achieving operational excellence.
Understanding Work Order Management
Work order management in the manufacturing sector is a complex, multi-faceted process that demands meticulous attention to detail. It involves every step of task assignment, from the initial request, scheduling, and execution, to the final review and closure of work orders. These orders could range from preventive maintenance to urgent repairs and routine production tasks, all critical to the uninterrupted flow of the manufacturing process.
Effective work order management is crucial for several reasons. It ensures that resources are used efficiently, helps in maintaining equipment reliability, guarantees the quality of products, and aids in meeting production deadlines. Furthermore, it enables manufacturers to respond swiftly to unforeseen issues, thereby minimizing downtime and maximizing productivity.
The integration of work orders into a centralized system provides a clear roadmap of production activities, facilitating better coordination among teams, improving communication, and enhancing overall operational visibility. This integration is vital for streamlining processes, optimizing resource allocation, and ensuring that every task aligns with the broader production goals.
Challenges in Work Order Management
Manufacturers face numerous challenges in work order management, each potentially impacting the production line’s efficiency and the company’s bottom line.
- Prioritization and Scheduling Conflicts: With a constant stream of work orders, prioritizing and scheduling them in a way that minimizes disruption and maximizes efficiency is a significant challenge. The need to balance routine maintenance with urgent repairs and new production tasks requires a dynamic and flexible approach to scheduling.
- Communication Breakdowns: Effective communication is the cornerstone of efficient work order management. However, miscommunications between departments, unclear work order details, and lack of real-time updates can lead to errors, delays, and frustration among team members.
- Tracking and Visibility Issues: As companies scale, tracking the status of numerous work orders, monitoring progress, and ensuring resource availability becomes increasingly complex. Lack of visibility can result in resource overallocation, underutilization, and bottlenecks that delay production.
- Compliance and Quality Assurance: Adhering to strict industry standards and regulations while ensuring high-quality outputs is paramount. Manufacturers must navigate the challenge of maintaining compliance and quality throughout the work order process, from initial specifications to the final product.
Strategies for Effective Work Order Management
Addressing these challenges requires a strategic approach, leveraging both technology and process improvements:
- Technology Implementation: Advanced Manufacturing Execution Systems (MES) and Enterprise Resource Planning (ERP) systems can dramatically improve work order management. These systems automate scheduling, provide real-time visibility into work order status, facilitate communication, and ensure accurate resource allocation. Adopting cloud-based solutions can further enhance flexibility and accessibility, allowing for remote monitoring and management even when not on-site.
- Process Optimization: Streamlining work order processes through regular review and optimization is crucial. Employing lean manufacturing principles can help eliminate waste, reduce inefficiencies, and improve workflow. Establishing clear protocols for work order creation, approval, and closure ensures consistency and accountability across the production floor.
- Training and Empowerment: Investing in comprehensive training programs for staff on the use of work order management systems and processes ensures that everyone understands their role and the technology at their disposal. Empowering employees to make decisions based on real-time data can lead to more efficient problem-solving and task execution.
- Data-Driven Decision Making: Utilizing analytics and reporting tools within Manufacturing Execution Systems and Enterprise Resource Planning systems can provide valuable insights into work order trends, performance bottlenecks, and areas for improvement. Manufacturers can use this data to make informed decisions, anticipate issues before they arise, and continuously refine their work order management practices.
- Preventive Maintenance Focus: Shifting from a reactive to a preventive maintenance approach can significantly reduce emergency work orders and associated downtime. Scheduled maintenance, based on historical data and predictive analytics, ensures equipment is serviced before failures occur, thereby streamlining work order management.
Future Outlook
Optimizing work order management is crucial for manufacturing companies striving to enhance efficiency, reduce operational costs, and maintain product quality. By understanding the challenges and implementing strategic solutions, manufacturers can improve their work order processes, leading to smoother operations and increased productivity. As technology advances, the adoption of sophisticated systems and tools will play a pivotal role in the future of work order management, enabling manufacturers to achieve greater operational agility and competitiveness.
How CADDi Drawer Can Help
CADDi Drawer stands as a new innovation within the manufacturing industry, taking data from each level of a manufacturing organization and providing the ability to leverage it into actionable insights.
By using the most important asset in manufacturing, engineering drawings, as a link between quality, procurement, production, and engineering, Drawer removes departmental silos to encourage information sharing. This is pivotal when conducting the planning required to optimize work order management. By identifying trends in production, users can more effectively schedule out long-term maintenance projects, and visibility is improved through Drawer’s tagging and projects functions. Additionally, by empowering members to maintain strong records within Drawer, new members are able to reduce the amount of training required to begin completing their tasks.
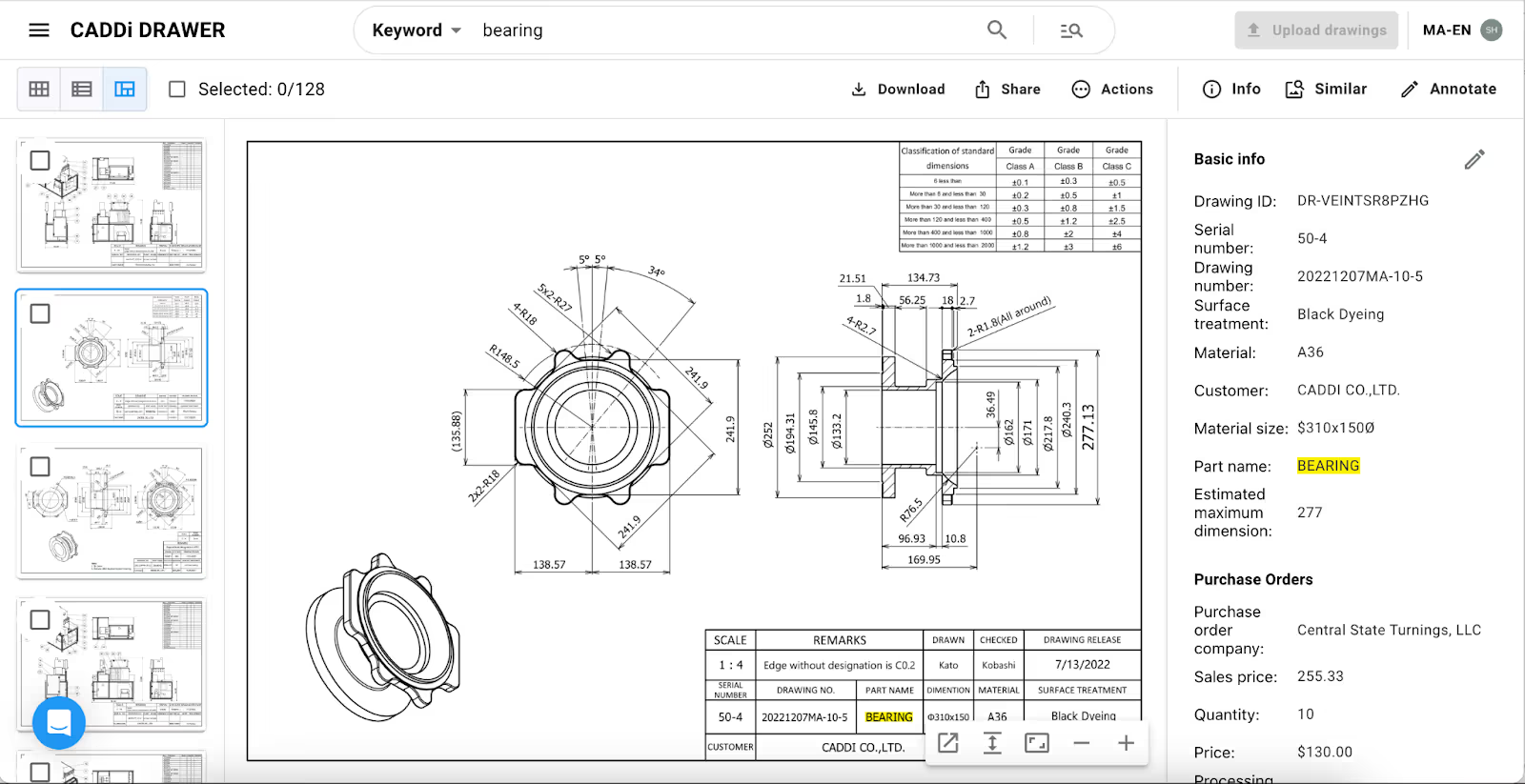
Utilizing CADDi Drawer can streamline the visualization and communication of work order creation, allowing for alignment across departments. As the manufacturing industry trends towards digital transformation, it is integral to leverage technology effectively to stay ahead of the curve. See below to learn more about how companies are utilizing CADDi Drawer’s innovative solution.
Accelerating Company-Wide Digital Transformation with CADDi Drawer
For manufacturers, the ability to manage work orders efficiently is more than a necessity—it’s a strategic advantage. Work order management encompasses the planning, tracking, and execution of manufacturing tasks and maintenance operations, forming the backbone of a successful production line. This blog post aims to shed light on optimal work order management practices, identifying common challenges and providing actionable solutions. It serves as a guide for manufacturers keen on refining their operations, enhancing productivity, and achieving operational excellence.
Understanding Work Order Management
Work order management in the manufacturing sector is a complex, multi-faceted process that demands meticulous attention to detail. It involves every step of task assignment, from the initial request, scheduling, and execution, to the final review and closure of work orders. These orders could range from preventive maintenance to urgent repairs and routine production tasks, all critical to the uninterrupted flow of the manufacturing process.
Effective work order management is crucial for several reasons. It ensures that resources are used efficiently, helps in maintaining equipment reliability, guarantees the quality of products, and aids in meeting production deadlines. Furthermore, it enables manufacturers to respond swiftly to unforeseen issues, thereby minimizing downtime and maximizing productivity.
The integration of work orders into a centralized system provides a clear roadmap of production activities, facilitating better coordination among teams, improving communication, and enhancing overall operational visibility. This integration is vital for streamlining processes, optimizing resource allocation, and ensuring that every task aligns with the broader production goals.
Challenges in Work Order Management
Manufacturers face numerous challenges in work order management, each potentially impacting the production line’s efficiency and the company’s bottom line.
- Prioritization and Scheduling Conflicts: With a constant stream of work orders, prioritizing and scheduling them in a way that minimizes disruption and maximizes efficiency is a significant challenge. The need to balance routine maintenance with urgent repairs and new production tasks requires a dynamic and flexible approach to scheduling.
- Communication Breakdowns: Effective communication is the cornerstone of efficient work order management. However, miscommunications between departments, unclear work order details, and lack of real-time updates can lead to errors, delays, and frustration among team members.
- Tracking and Visibility Issues: As companies scale, tracking the status of numerous work orders, monitoring progress, and ensuring resource availability becomes increasingly complex. Lack of visibility can result in resource overallocation, underutilization, and bottlenecks that delay production.
- Compliance and Quality Assurance: Adhering to strict industry standards and regulations while ensuring high-quality outputs is paramount. Manufacturers must navigate the challenge of maintaining compliance and quality throughout the work order process, from initial specifications to the final product.
Strategies for Effective Work Order Management
Addressing these challenges requires a strategic approach, leveraging both technology and process improvements:
- Technology Implementation: Advanced Manufacturing Execution Systems (MES) and Enterprise Resource Planning (ERP) systems can dramatically improve work order management. These systems automate scheduling, provide real-time visibility into work order status, facilitate communication, and ensure accurate resource allocation. Adopting cloud-based solutions can further enhance flexibility and accessibility, allowing for remote monitoring and management even when not on-site.
- Process Optimization: Streamlining work order processes through regular review and optimization is crucial. Employing lean manufacturing principles can help eliminate waste, reduce inefficiencies, and improve workflow. Establishing clear protocols for work order creation, approval, and closure ensures consistency and accountability across the production floor.
- Training and Empowerment: Investing in comprehensive training programs for staff on the use of work order management systems and processes ensures that everyone understands their role and the technology at their disposal. Empowering employees to make decisions based on real-time data can lead to more efficient problem-solving and task execution.
- Data-Driven Decision Making: Utilizing analytics and reporting tools within Manufacturing Execution Systems and Enterprise Resource Planning systems can provide valuable insights into work order trends, performance bottlenecks, and areas for improvement. Manufacturers can use this data to make informed decisions, anticipate issues before they arise, and continuously refine their work order management practices.
- Preventive Maintenance Focus: Shifting from a reactive to a preventive maintenance approach can significantly reduce emergency work orders and associated downtime. Scheduled maintenance, based on historical data and predictive analytics, ensures equipment is serviced before failures occur, thereby streamlining work order management.
Future Outlook
Optimizing work order management is crucial for manufacturing companies striving to enhance efficiency, reduce operational costs, and maintain product quality. By understanding the challenges and implementing strategic solutions, manufacturers can improve their work order processes, leading to smoother operations and increased productivity. As technology advances, the adoption of sophisticated systems and tools will play a pivotal role in the future of work order management, enabling manufacturers to achieve greater operational agility and competitiveness.
How CADDi Drawer Can Help
CADDi Drawer stands as a new innovation within the manufacturing industry, taking data from each level of a manufacturing organization and providing the ability to leverage it into actionable insights.
By using the most important asset in manufacturing, engineering drawings, as a link between quality, procurement, production, and engineering, Drawer removes departmental silos to encourage information sharing. This is pivotal when conducting the planning required to optimize work order management. By identifying trends in production, users can more effectively schedule out long-term maintenance projects, and visibility is improved through Drawer’s tagging and projects functions. Additionally, by empowering members to maintain strong records within Drawer, new members are able to reduce the amount of training required to begin completing their tasks.
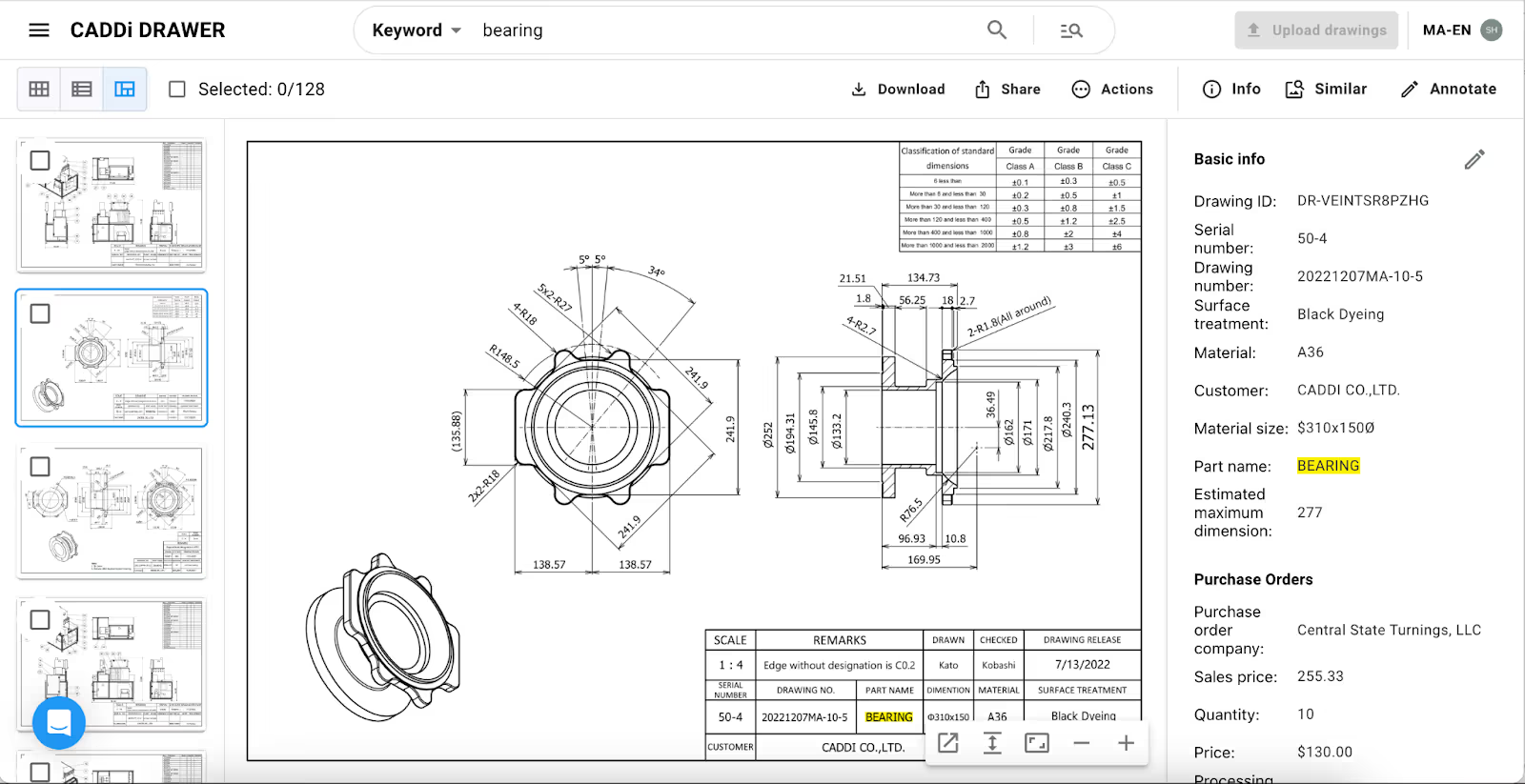
Utilizing CADDi Drawer can streamline the visualization and communication of work order creation, allowing for alignment across departments. As the manufacturing industry trends towards digital transformation, it is integral to leverage technology effectively to stay ahead of the curve. See below to learn more about how companies are utilizing CADDi Drawer’s innovative solution.
Accelerating Company-Wide Digital Transformation with CADDi Drawer
Ready to see CADDi Drawer in action? Get a personalized demo.
Subscribe to our Blog!
Related Resources
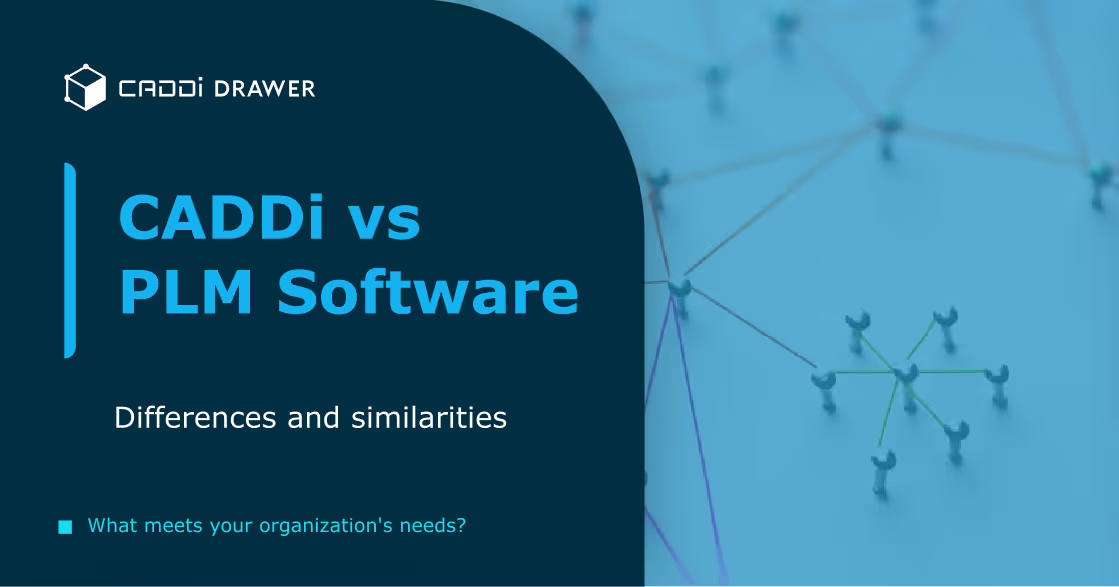
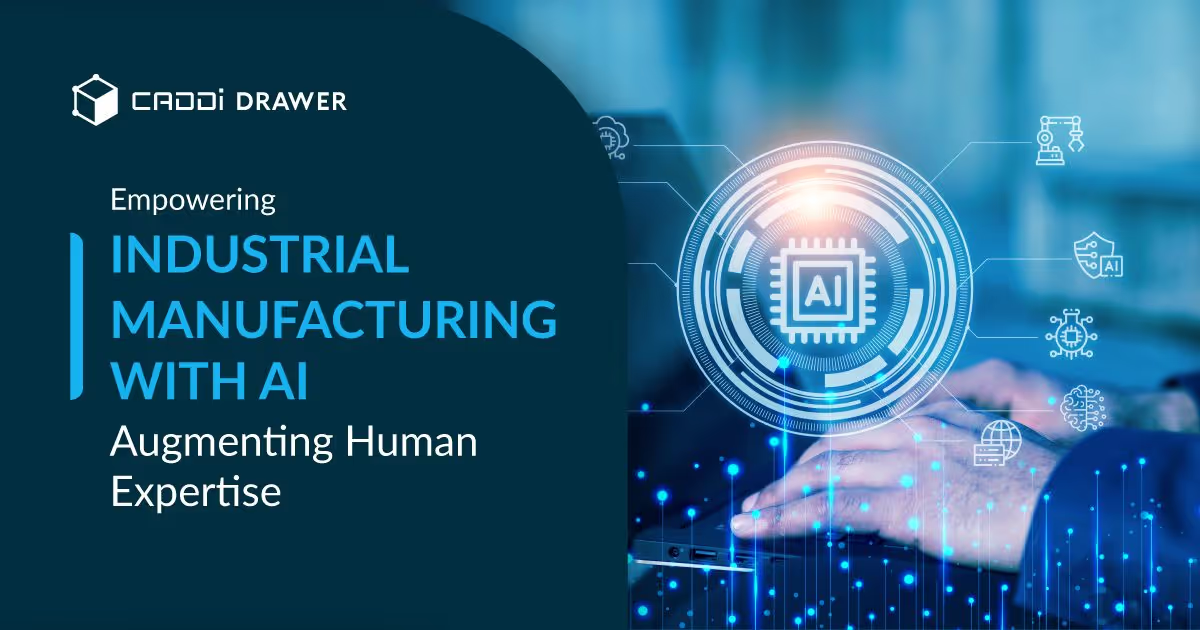
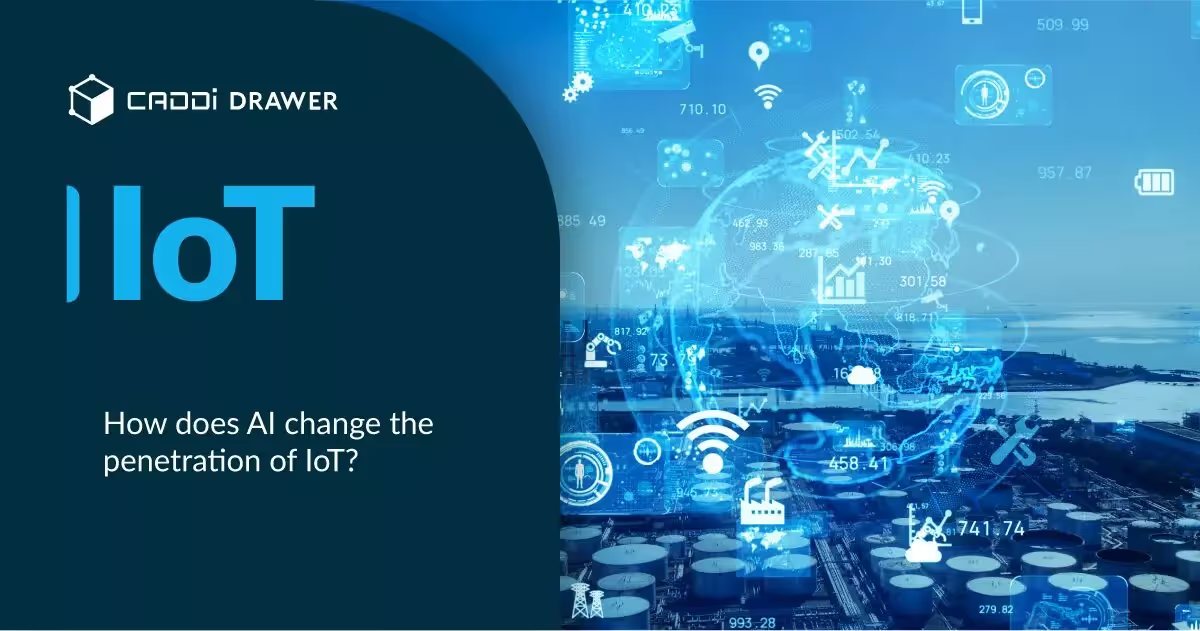
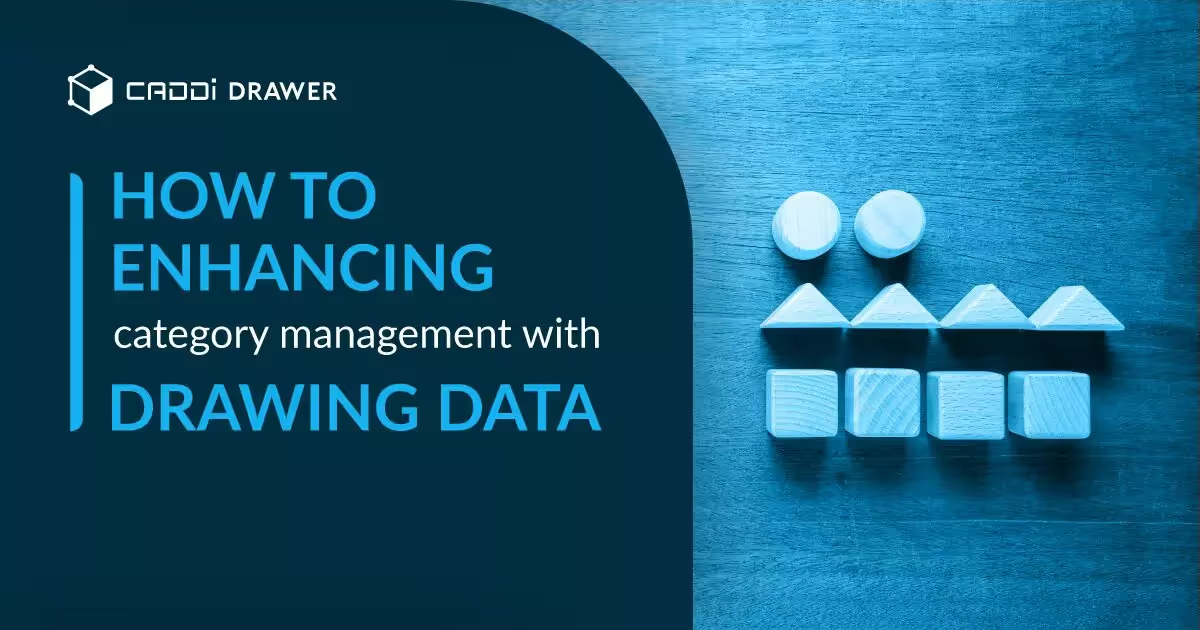
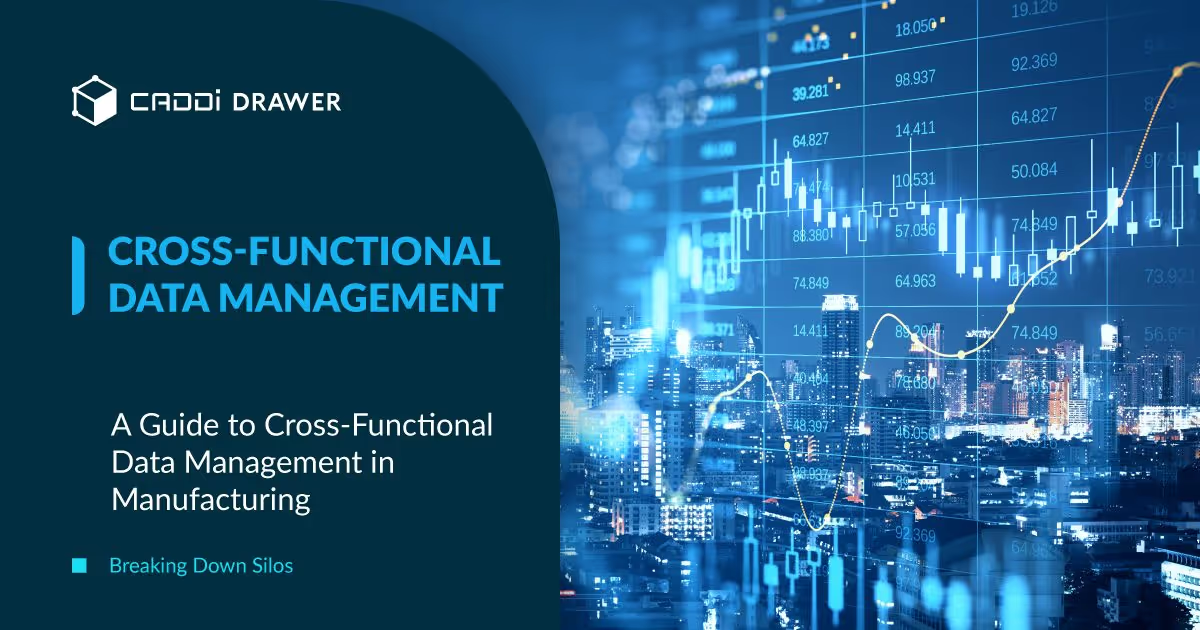
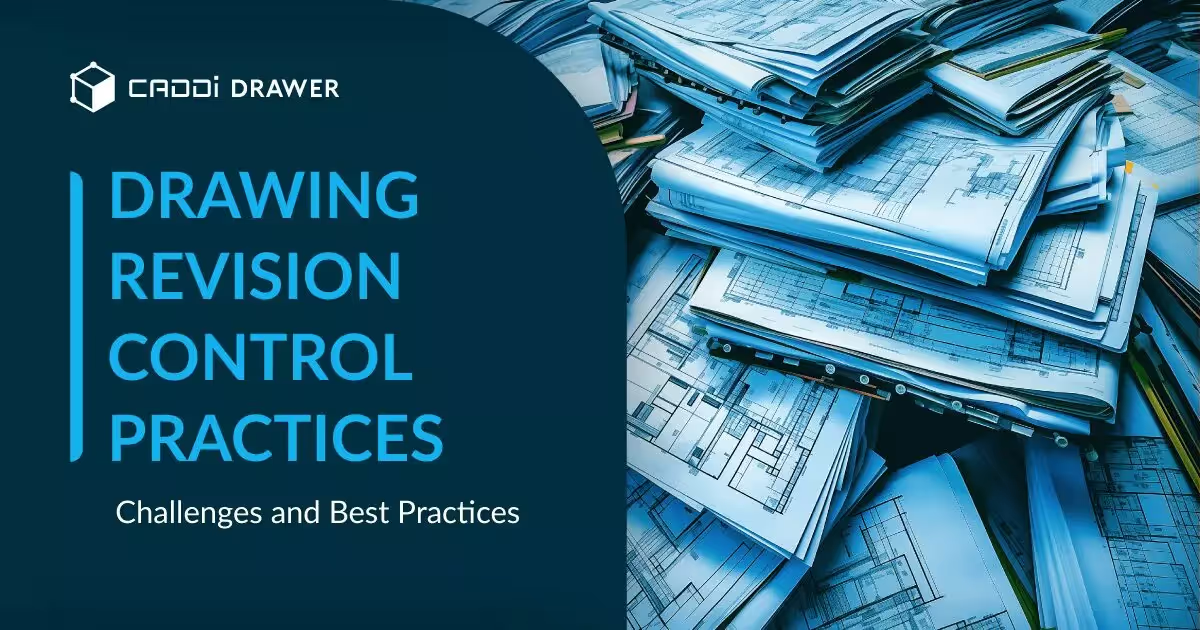