Breaking Down Silos: A Guide to Cross-Functional Data Management in Manufacturing
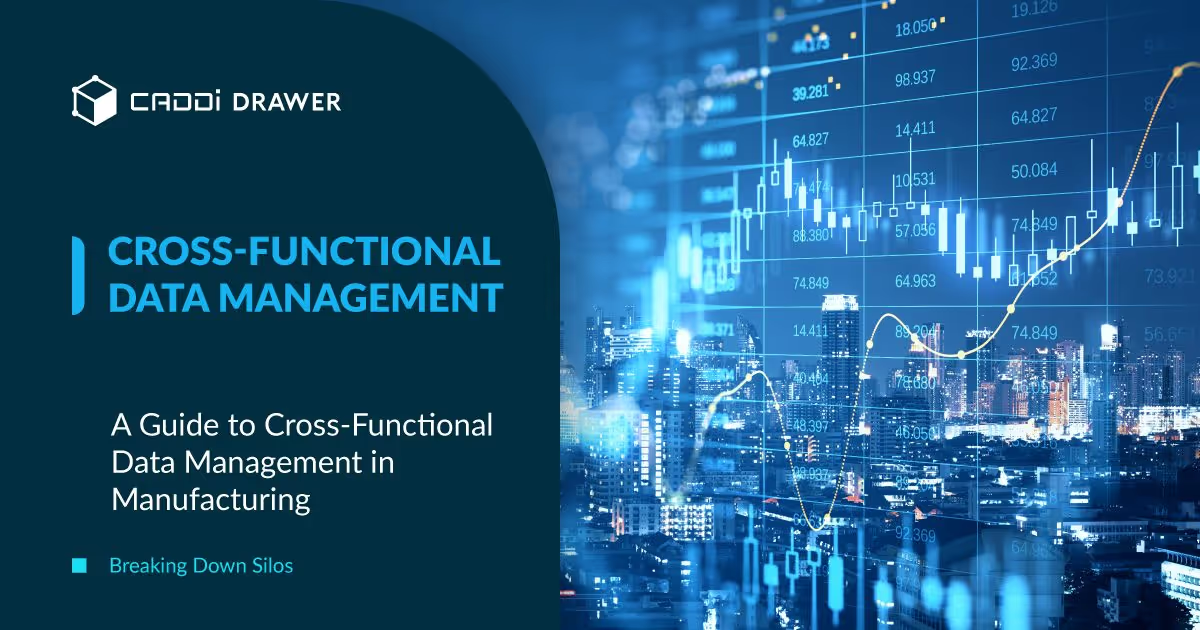
Table of Contents
The ability to efficiently manage data across various functional areas— From design, engineering, procurement, production to quality assurance—has become a cornerstone for success. Navigating this complex data ecosystem is particularly challenging yet critical for driving operational efficiency and competitive advantage. This article delves into the current landscape of software and systems supporting data management in manufacturing, highlights the prevalent issues around cross-functional collaboration, and offers strategies for improvement, underscoring how CADDi can support this transformation.
Current Landscape of Data Management Software and Systems
The manufacturing sector has seen a significant transformation in how data is collected, processed, and analyzed, thanks to advancements in technology. At the heart of this evolution are sophisticated software and systems designed to streamline operations across various departments.
.avif)
Engineering: In the realm of engineering, Computer-Aided Design (CAD) tools such as Autodesk AutoCAD and SolidWorks are indispensable. These platforms not only facilitate the creation of detailed designs but also serve as central repositories for design data, enabling seamless collaboration among team members.
Procurement: For procurement professionals, Enterprise Resource Planning (ERP) systems like SAP Ariba offer a comprehensive solution for managing supplier relationships, contracts, and purchase orders. These systems ensure that procurement data is accurately tracked and easily accessible, fostering strategic decision-making.
Production Quality Assurance: In production quality assurance, Manufacturing Execution Systems (MES) like Siemens Opcenter provide real-time monitoring of production processes. This enables the early detection of quality issues and facilitates the continuous improvement of manufacturing operations.
Despite the availability of these specialized tools, the challenge often lies in integrating data across these disparate systems to achieve a unified view of operations.
Challenges in Cross-Functional Data Management
One of the most pressing issues in cross-functional data management is the existence of data silos. These silos occur when data is isolated within departments, leading to inconsistencies and hindering collaboration. Furthermore, the lack of standardized data formats can complicate the sharing of information, while the absence of real-time data exchange capabilities can delay decision-making processes.
.avif)
Challenges in cross functional collaboration and challenges occur due to the different nature of major value chains within manufacturing companies: Engineering Chain and Supply Chain.
Engineering Chain
Product-focused. Views the product lifecycle as a chain of interconnected processes.
Based on project management principles. It goes without saying that manufacturing begins with the act of engineering, positioning the product-focused view as a foundational perspective in the industry. Within this chain, significant value and data generation occur, underscoring its importance. When exploring the optimization of the engineering chain, major themes frequently arise: “Front-Loading“, “Concurrent Engineering,” and “Mass Customization.” Although the terminology might differ across companies, there is a general consensus around the significance of these concepts. These strategies are crucial for the development of internationally competitive products, highlighting the industry’s drive towards efficiency, innovation, and customization.
Supply Chain
The Supply Chain is fundamentally business-focused, with its primary concern being the efficient and effective flow of goods, information, and resources from the point of origin to the point of consumption. It operates on a foundation of accounting and financial principles, aiming to maximize cost efficiency, minimize waste, and optimize operational performance. Within this framework, several key themes such as Strategic Sourcing, Supplier Relationship Management (SRM), Inventory optimization and Supply chain visibility (SCV), often emerge as focal points for procurement directors aiming to enhance supply chain efficiency and resilience
PLM as a solution to Cross-Functional Data Management
CAD and BOM (Bill of Materials)
Before the widespread adoption of 3D CAD (Computer-Aided Design), all the information required for manufacturing was documented within drawings. With the introduction of 3D CAD, the speed of new modeling and reuse design significantly improved.
However, several challenges emerged such as : Lack of alignment between 3D data and drawings, CAD and BOM are not synchronized, Design changes are not accurately reflected in the original data. The concept of integrating and managing CAD and BOM in a unified manner is the basis of PLM which is the idea of ‘assetization of design deliverables’ as envisioned by PLM solution providers such as Arena and Team Center by Siemens.
Product Information Management centered around BOM
BOMs are transformed according to the purpose for each phase of the product life cycle. E-BOM and M-BOM are fundamental and common, but in recent years, various purpose-specific BOMs with different names such as ‘D-BOM’ and ‘S-BOM’ have emerged. Originally, departments used to transcribe and annotate them in tools like Excel. However, PLM solutions now provide centralized management for these as ‘Integrated BOMs’
.avif)
Various types of information generated throughout the product lifecycle are registered in the integrated BOM as item information. By associating them with the BOM, it becomes possible to centrally manage which parts were used in which products, what events occurred, and how they unfolded. The ingenuity of each PLM vendor can be observed in making data registration and linking effortless
.avif)
As of today, typical PLM packages structurally aggregate component information and manage it in line with the engineering chain’s processes. Treat drawings strictly as “single document files” linked to product items.
1. Inventory item info management and search
- Assign part numbers
- Generate and convert BOMs
- Procurement / Manufacturing information
- Managing related documents
- Search functionalities (attribute-based, similarity-based shape search, etc.)
2. CAD Data Management (PDM)
- CAD data management and sharing
- Direct integration with CAD systems
- Conversion to lightweight viewers
3. Drawings management
- Document Mgmt (Folder)
- Version Control
- Viewer
4. Development Process Management
- Project Management, Schedule Management
- Drawing Release and Approval Process Management, Workflow
- Cost Management, Verification and Evaluation
- Collaborative Design Support, Design Space
Limitation and remaining challenges with the concept of PLM
Product Lifecycle Management (PLM) systems are pivotal in managing the entire lifecycle of a product from inception, through engineering design and manufacture, to service and disposal. They integrate people, data, processes, and business systems to provide a backbone for companies and their extended enterprise. However, when focusing on the utilization of data in procurement and engineering, several challenges and limitations can emerge:
Data Silos and Integration Issues: One of the primary challenges with PLM systems is the fact that the remaining existence of data silos. While PLM systems are excellent for managing product-related data, they often operate independently of other enterprise systems such as ERP (Enterprise Resource Planning), which manages procurement data. This lack of integration can lead to inconsistencies in data across different departments, making it difficult for procurement and engineering teams to access and utilize data effectively.
Complexity and Usability: PLM systems can be complex and difficult to navigate, especially for users who are not deeply technical, such as some procurement professionals. This complexity can hinder the efficient use and adoption of the system, limiting its effectiveness in facilitating cross-functional collaboration between procurement and engineering.
Change Management: Implementing or upgrading a PLM system often requires significant change management efforts. Resistance to change among users can limit the system’s adoption and effectiveness. Procurement and engineering departments may have established processes and systems in place, and the transition to a new or integrated PLM system can disrupt these established workflows.
The Role of CADDi in Streamlining Cross-Functional Data Management
Our service, CADDi Drawer, is designed to address the challenges of cross-functional data management head-on. By offering a standalone platform that can work complimentary with existing systems such as PLM, PDM, and ERP, CADDi enables procurement directors and their teams to access, analyze, and share data more effectively.
.avif)
1. Utilize legacy data as assets
The world is shifting towards 3D, yet 99% of our historical data remains in 2D. We must utilize this rich 2D historical data as a foundational asset for future innovations. There is tremendous value in referencing and learning from engineering drawings and notes from 20 years ago, but only if they can be used together with today’s design and file formats. CADDi’s proprietary OCR-based AI allows you to digitize your historical data into searchable assets that can be compared and referenced side by side with a new drawing you’ve creating today.
.avif)
2. Breakdown silos to drive cross-functional collaboration
Utilizing CADDi’s patented technology, the shape of each drawing is identified to locate similar drawings across historical work, with relevant supply chain data (e.g., cost, quality, manufacturing notes, specs) automatically linked to each drawing. This provides enhanced visibility into dormant drawings within your file storage and enables actionable insights to drive cross-functional initiatives such as design standardization, VAVE, and supplier consolidation.
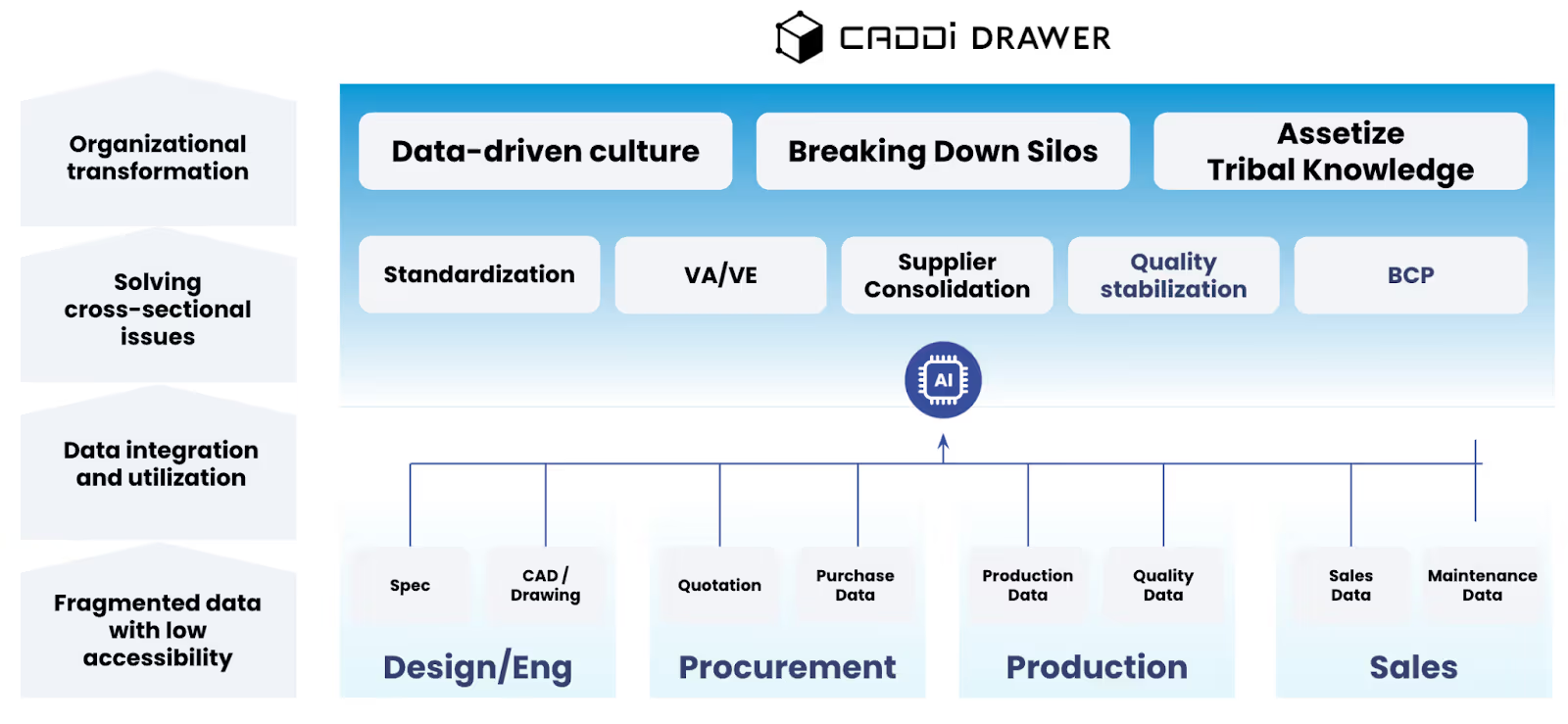
The ability to efficiently manage data across various functional areas— From design, engineering, procurement, production to quality assurance—has become a cornerstone for success. Navigating this complex data ecosystem is particularly challenging yet critical for driving operational efficiency and competitive advantage. This article delves into the current landscape of software and systems supporting data management in manufacturing, highlights the prevalent issues around cross-functional collaboration, and offers strategies for improvement, underscoring how CADDi can support this transformation.
Current Landscape of Data Management Software and Systems
The manufacturing sector has seen a significant transformation in how data is collected, processed, and analyzed, thanks to advancements in technology. At the heart of this evolution are sophisticated software and systems designed to streamline operations across various departments.
.avif)
Engineering: In the realm of engineering, Computer-Aided Design (CAD) tools such as Autodesk AutoCAD and SolidWorks are indispensable. These platforms not only facilitate the creation of detailed designs but also serve as central repositories for design data, enabling seamless collaboration among team members.
Procurement: For procurement professionals, Enterprise Resource Planning (ERP) systems like SAP Ariba offer a comprehensive solution for managing supplier relationships, contracts, and purchase orders. These systems ensure that procurement data is accurately tracked and easily accessible, fostering strategic decision-making.
Production Quality Assurance: In production quality assurance, Manufacturing Execution Systems (MES) like Siemens Opcenter provide real-time monitoring of production processes. This enables the early detection of quality issues and facilitates the continuous improvement of manufacturing operations.
Despite the availability of these specialized tools, the challenge often lies in integrating data across these disparate systems to achieve a unified view of operations.
Challenges in Cross-Functional Data Management
One of the most pressing issues in cross-functional data management is the existence of data silos. These silos occur when data is isolated within departments, leading to inconsistencies and hindering collaboration. Furthermore, the lack of standardized data formats can complicate the sharing of information, while the absence of real-time data exchange capabilities can delay decision-making processes.
.avif)
Challenges in cross functional collaboration and challenges occur due to the different nature of major value chains within manufacturing companies: Engineering Chain and Supply Chain.
Engineering Chain
Product-focused. Views the product lifecycle as a chain of interconnected processes.
Based on project management principles. It goes without saying that manufacturing begins with the act of engineering, positioning the product-focused view as a foundational perspective in the industry. Within this chain, significant value and data generation occur, underscoring its importance. When exploring the optimization of the engineering chain, major themes frequently arise: “Front-Loading“, “Concurrent Engineering,” and “Mass Customization.” Although the terminology might differ across companies, there is a general consensus around the significance of these concepts. These strategies are crucial for the development of internationally competitive products, highlighting the industry’s drive towards efficiency, innovation, and customization.
Supply Chain
The Supply Chain is fundamentally business-focused, with its primary concern being the efficient and effective flow of goods, information, and resources from the point of origin to the point of consumption. It operates on a foundation of accounting and financial principles, aiming to maximize cost efficiency, minimize waste, and optimize operational performance. Within this framework, several key themes such as Strategic Sourcing, Supplier Relationship Management (SRM), Inventory optimization and Supply chain visibility (SCV), often emerge as focal points for procurement directors aiming to enhance supply chain efficiency and resilience
PLM as a solution to Cross-Functional Data Management
CAD and BOM (Bill of Materials)
Before the widespread adoption of 3D CAD (Computer-Aided Design), all the information required for manufacturing was documented within drawings. With the introduction of 3D CAD, the speed of new modeling and reuse design significantly improved.
However, several challenges emerged such as : Lack of alignment between 3D data and drawings, CAD and BOM are not synchronized, Design changes are not accurately reflected in the original data. The concept of integrating and managing CAD and BOM in a unified manner is the basis of PLM which is the idea of ‘assetization of design deliverables’ as envisioned by PLM solution providers such as Arena and Team Center by Siemens.
Product Information Management centered around BOM
BOMs are transformed according to the purpose for each phase of the product life cycle. E-BOM and M-BOM are fundamental and common, but in recent years, various purpose-specific BOMs with different names such as ‘D-BOM’ and ‘S-BOM’ have emerged. Originally, departments used to transcribe and annotate them in tools like Excel. However, PLM solutions now provide centralized management for these as ‘Integrated BOMs’
.avif)
Various types of information generated throughout the product lifecycle are registered in the integrated BOM as item information. By associating them with the BOM, it becomes possible to centrally manage which parts were used in which products, what events occurred, and how they unfolded. The ingenuity of each PLM vendor can be observed in making data registration and linking effortless
.avif)
As of today, typical PLM packages structurally aggregate component information and manage it in line with the engineering chain’s processes. Treat drawings strictly as “single document files” linked to product items.
1. Inventory item info management and search
- Assign part numbers
- Generate and convert BOMs
- Procurement / Manufacturing information
- Managing related documents
- Search functionalities (attribute-based, similarity-based shape search, etc.)
2. CAD Data Management (PDM)
- CAD data management and sharing
- Direct integration with CAD systems
- Conversion to lightweight viewers
3. Drawings management
- Document Mgmt (Folder)
- Version Control
- Viewer
4. Development Process Management
- Project Management, Schedule Management
- Drawing Release and Approval Process Management, Workflow
- Cost Management, Verification and Evaluation
- Collaborative Design Support, Design Space
Limitation and remaining challenges with the concept of PLM
Product Lifecycle Management (PLM) systems are pivotal in managing the entire lifecycle of a product from inception, through engineering design and manufacture, to service and disposal. They integrate people, data, processes, and business systems to provide a backbone for companies and their extended enterprise. However, when focusing on the utilization of data in procurement and engineering, several challenges and limitations can emerge:
Data Silos and Integration Issues: One of the primary challenges with PLM systems is the fact that the remaining existence of data silos. While PLM systems are excellent for managing product-related data, they often operate independently of other enterprise systems such as ERP (Enterprise Resource Planning), which manages procurement data. This lack of integration can lead to inconsistencies in data across different departments, making it difficult for procurement and engineering teams to access and utilize data effectively.
Complexity and Usability: PLM systems can be complex and difficult to navigate, especially for users who are not deeply technical, such as some procurement professionals. This complexity can hinder the efficient use and adoption of the system, limiting its effectiveness in facilitating cross-functional collaboration between procurement and engineering.
Change Management: Implementing or upgrading a PLM system often requires significant change management efforts. Resistance to change among users can limit the system’s adoption and effectiveness. Procurement and engineering departments may have established processes and systems in place, and the transition to a new or integrated PLM system can disrupt these established workflows.
The Role of CADDi in Streamlining Cross-Functional Data Management
Our service, CADDi Drawer, is designed to address the challenges of cross-functional data management head-on. By offering a standalone platform that can work complimentary with existing systems such as PLM, PDM, and ERP, CADDi enables procurement directors and their teams to access, analyze, and share data more effectively.
.avif)
1. Utilize legacy data as assets
The world is shifting towards 3D, yet 99% of our historical data remains in 2D. We must utilize this rich 2D historical data as a foundational asset for future innovations. There is tremendous value in referencing and learning from engineering drawings and notes from 20 years ago, but only if they can be used together with today’s design and file formats. CADDi’s proprietary OCR-based AI allows you to digitize your historical data into searchable assets that can be compared and referenced side by side with a new drawing you’ve creating today.
.avif)
2. Breakdown silos to drive cross-functional collaboration
Utilizing CADDi’s patented technology, the shape of each drawing is identified to locate similar drawings across historical work, with relevant supply chain data (e.g., cost, quality, manufacturing notes, specs) automatically linked to each drawing. This provides enhanced visibility into dormant drawings within your file storage and enables actionable insights to drive cross-functional initiatives such as design standardization, VAVE, and supplier consolidation.
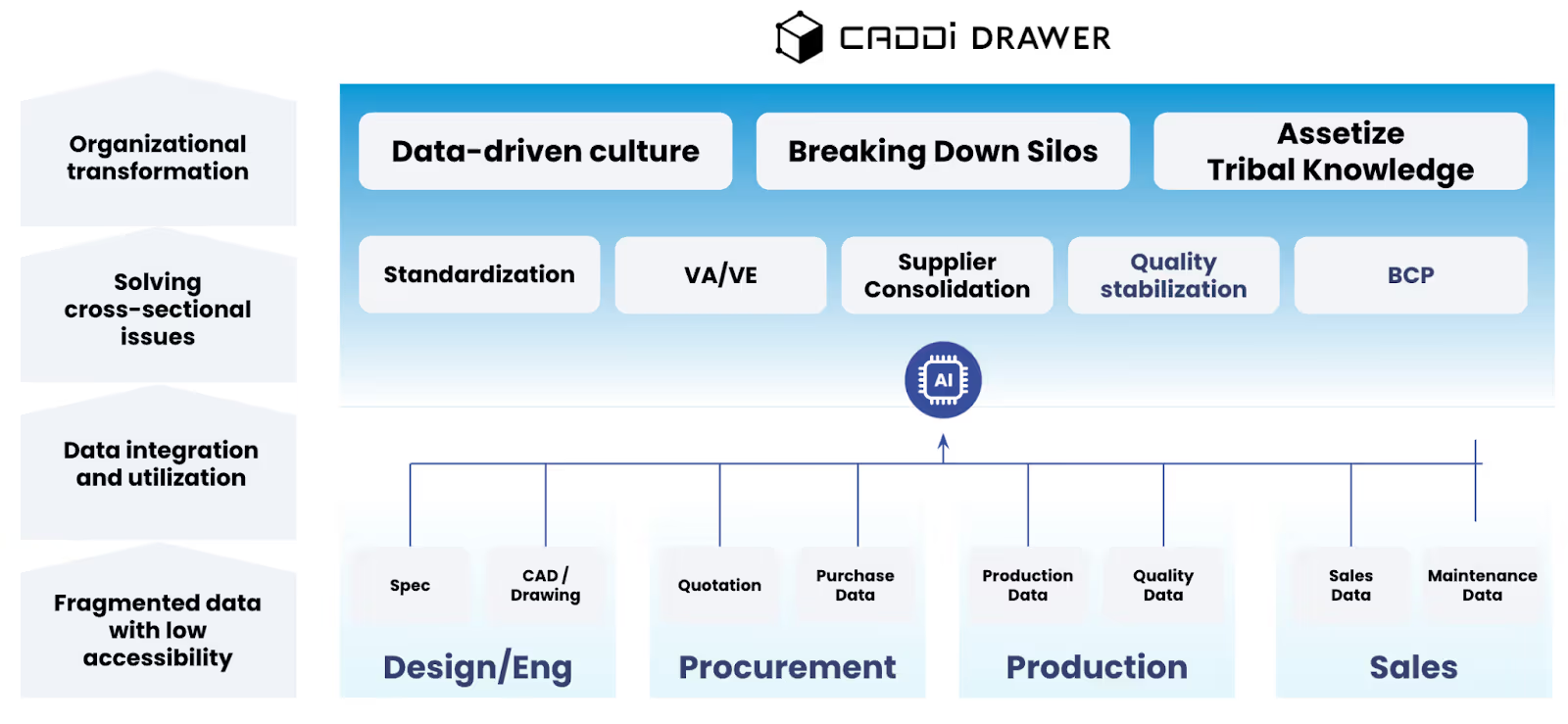
Ready to see CADDi Drawer in action? Get a personalized demo.
Subscribe to our Blog!
Related Resources
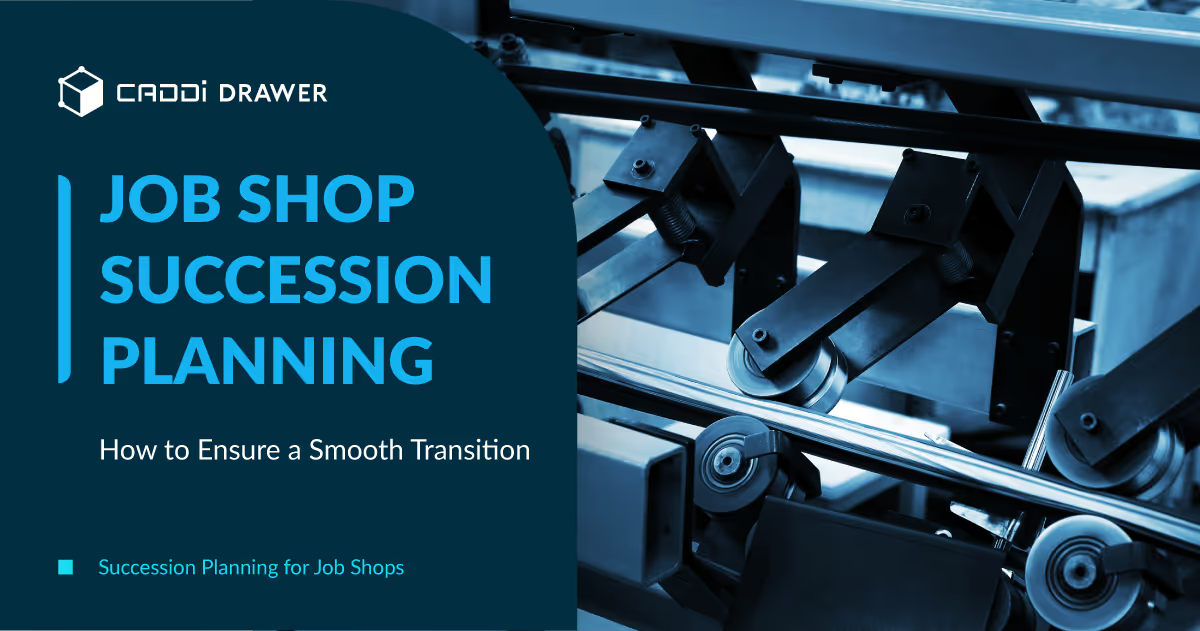
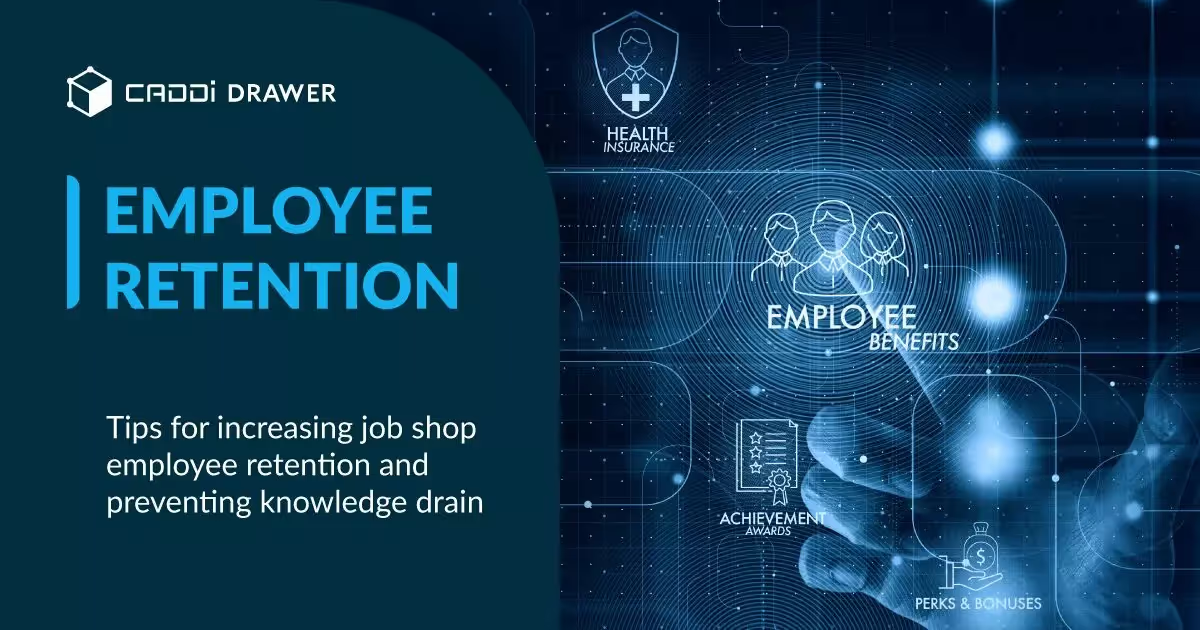
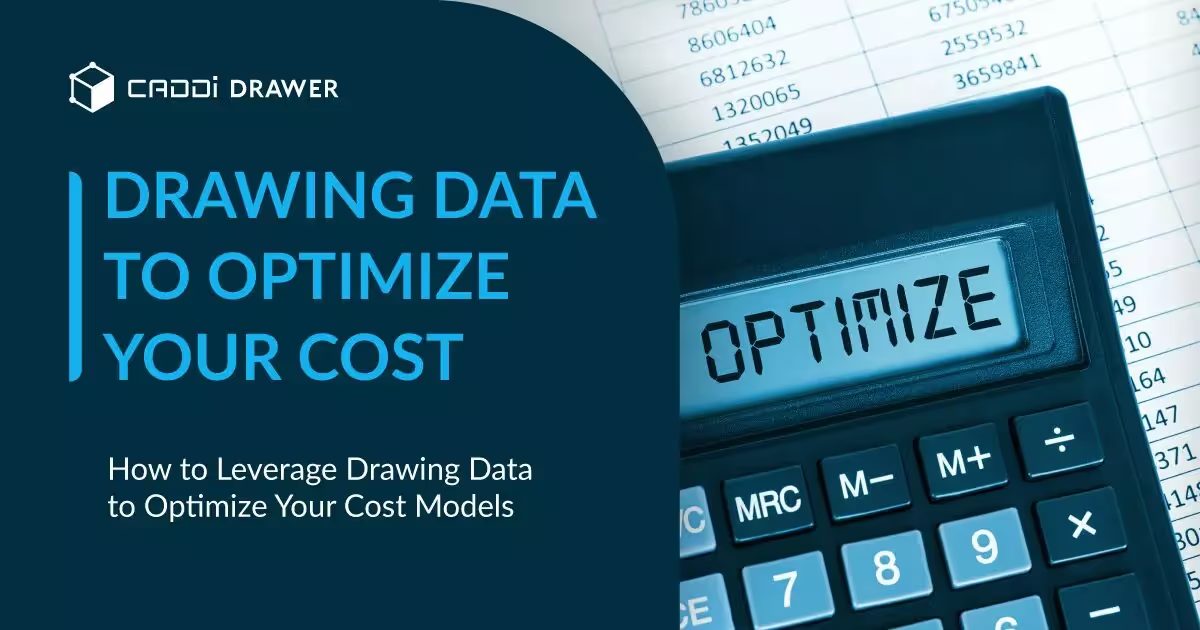
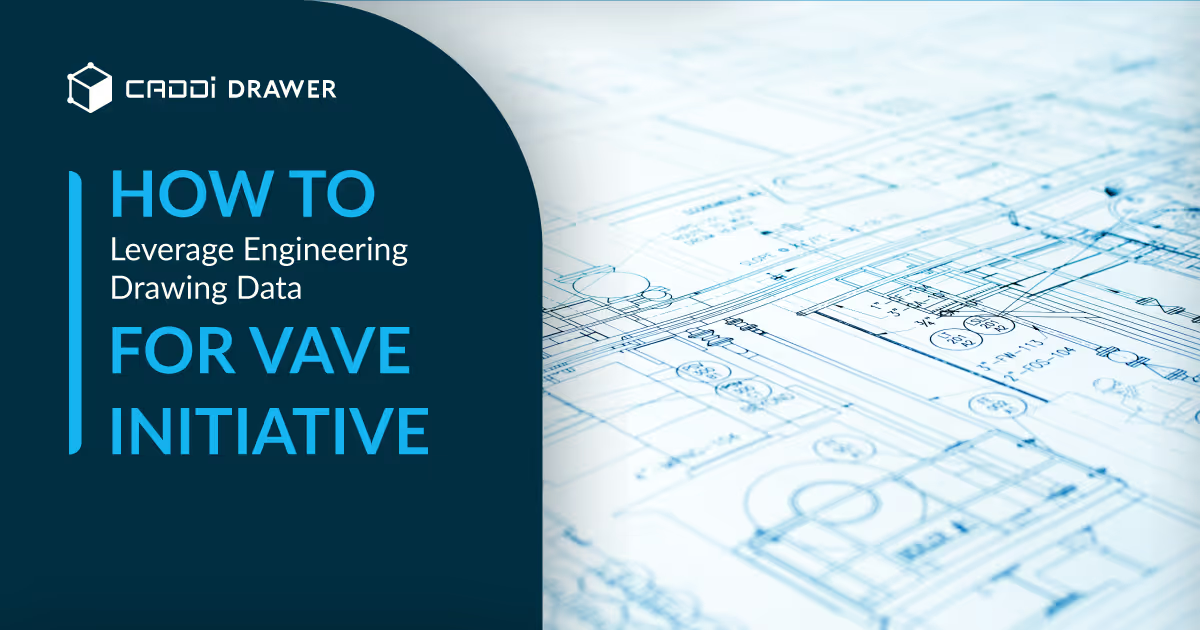
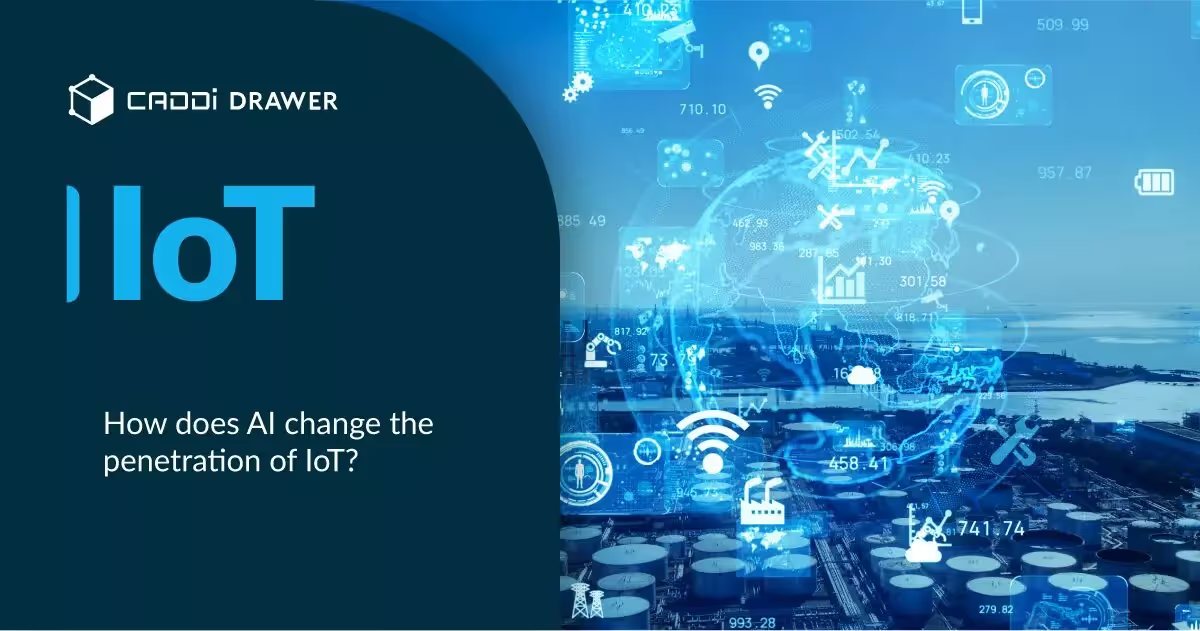
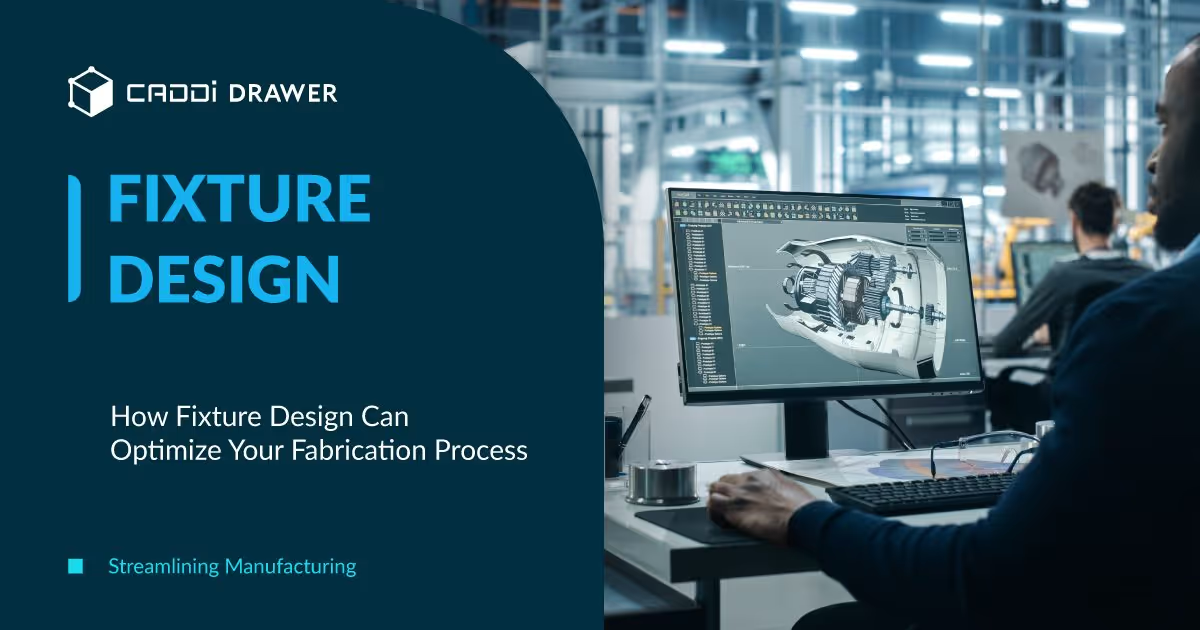