How does AI change the penetration of IoT?
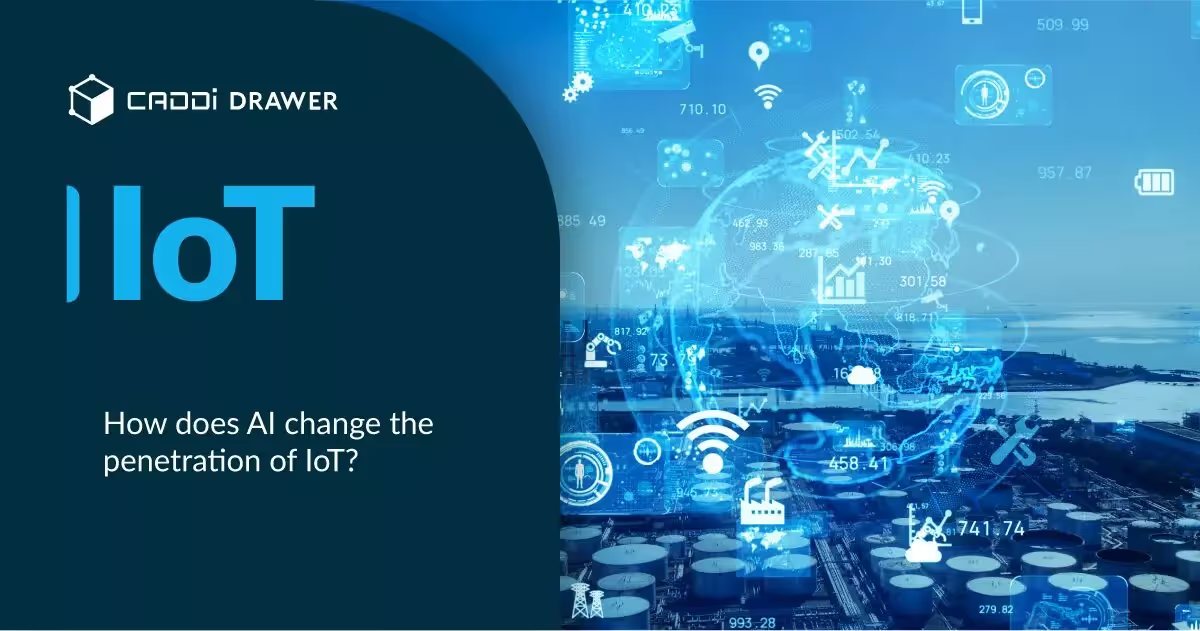
Table of Contents
Picture a symphony orchestra, each instrument playing its part to create a harmonious melody. Now imagine that orchestra with a brilliant conductor at the helm, guiding each musician to play their best and adapting to changes in real-time. This is the perfect analogy for how AI is transforming the Industrial Internet of Things (IIoT) in manufacturing.
The AI-IoT Duet
In recent years, the convergence of AI and IoT has been a hot topic in the tech world. According to a McKinsey report, the number of businesses using AI with IoT increased from 19% in 2018 to 27% in 2020, and this trend is expected to continue as more companies recognize the benefits of combining these two technologies.
AI is like the brain that processes the vast amounts of data generated by IoT sensors, providing insights and making decisions that optimize manufacturing processes. It’s the conductor that brings all the pieces together, creating a seamless and efficient operation.
Edge Computing: Bringing AI Closer to the Action
One of the key trends in the AI-IoT duet is the rise of edge computing. Instead of sending all the data generated by IoT sensors to the cloud for processing, edge computing allows data to be analyzed and acted upon closer to the source. This reduces latency and improves efficiency, enabling real-time decision-making and automation.
Imagine a quality control system that uses machine vision to inspect products on the production line. With edge computing, the AI algorithms can analyze the images in real-time, identifying defects and triggering corrective actions immediately. This prevents defective products from reaching customers and reduces waste, ultimately saving time and money.
Predictive Maintenance: Preventing Downtime Before it Happens
Another area where AI is making a significant impact in manufacturing is predictive maintenance. By analyzing data from IoT sensors on machines, AI algorithms can predict when a machine is likely to fail, allowing maintenance to be scheduled before a breakdown occurs.
Think of it like a car that tells you when it needs an oil change or when the brakes are wearing out. By addressing these issues proactively, you can avoid costly repairs and extend the life of the vehicle. The same principle applies to manufacturing equipment, where unplanned downtime can be incredibly expensive.
Real-World Success Stories
- Rolls-Royce uses IoT sensors in its aircraft engines to monitor performance and predict maintenance needs, saving airlines millions of dollars in potential downtime.
- Cisco uses IoT sensors to track the location and condition of its products throughout the supply chain, reducing inventory costs and improving customer satisfaction.
- BMW uses IoT sensors to monitor the quality of its cars as they move through the production line, identifying potential issues before they reach the customer.
These are just a few examples of how AI and IoT are delivering value in manufacturing. As the technology matures and standards emerge, we can expect to see even more remarkable results in the years to come.
Key Solutions: Samsara and Tulip
As the demand for AI and IoT solutions in manufacturing grows, several key players have emerged to help companies harness the power of these technologies. Two notable examples are Samsara and Tulip.
Samsara offers a Connected Operations Cloud that enables businesses in industries such as transportation, construction, and manufacturing to harness and analyze IoT data. Their platform collects trillions of data points from sensors, cameras, and other IoT devices, providing real-time visibility and insights across operations.
For example, Samsara’s AI Dash Cams can detect distracted driving in real-time, prompting drivers to self-correct and reducing unsafe behavior by up to 50% in just three months. Their platform also enables predictive maintenance, helping companies spot potential issues before they lead to costly downtime.
Tulip, on the other hand, focuses on empowering frontline workers with IoT-enabled apps. Their no-code platform allows manufacturers to digitize their operations, connecting workers, machines, and devices in a seamless ecosystem.
With Tulip, companies can create digital work instructions, track production in real-time, and analyze performance data to drive continuous improvement. Their IoT-enabled apps have helped manufacturers reduce defects by up to 60%, increase productivity by up to 30%, and cut training time by up to 90%.
Both Samsara and Tulip are prime examples of how AI and IoT can be leveraged to transform manufacturing operations. By providing intuitive platforms and actionable insights, these solutions are helping companies unlock new levels of efficiency, quality, and agility.
The Future: Autonomous Everything
Looking ahead, the combination of AI and IoT is poised to transform manufacturing in ways we can only imagine. As IoT devices become more intelligent and interconnected, we can expect to see a rise in autonomous systems, from self-driving forklifts to self-optimizing production lines.
AI will enable these systems to make decisions and adapt to changing conditions in real-time, improving efficiency, quality, and safety. It’s like having a team of expert operators working 24/7, never getting tired or making mistakes.
Challenges and Considerations
Of course, implementing AI and IoT in manufacturing is not without its challenges. Cybersecurity is a major concern, as the increased connectivity of devices creates more potential entry points for hackers. Manufacturers need to prioritize security and implement robust measures to protect their systems and data.
Data quality is another critical factor. AI is only as good as the data it’s trained on, so manufacturers need to ensure that the data collected by IoT sensors is accurate, consistent, and relevant. This requires careful planning and ongoing maintenance of the IoT infrastructure.
Finally, there’s the issue of skills and talent. Implementing and maintaining AI and IoT systems requires a new set of skills that may not be readily available in the current workforce. Manufacturers need to invest in training and education to build the necessary expertise in-house or partner with external providers who can fill the gap.
Conclusion
The convergence of AI and IoT is ushering in a new era of smart manufacturing, where machines talk to each other, learn from their experiences, and optimize themselves for maximum efficiency. It’s a world where downtime is minimized, quality is assured, and waste is eliminated.
As manufacturers embrace this technology, they unlock new levels of productivity, agility, and competitiveness. The journey may be challenging, but the rewards are immense. With the help of key solutions like Samsara and Tulip, companies can navigate this new landscape with confidence, conducting a symphony of machines and data that will propel them to the forefront of Industry 4.0.
Picture a symphony orchestra, each instrument playing its part to create a harmonious melody. Now imagine that orchestra with a brilliant conductor at the helm, guiding each musician to play their best and adapting to changes in real-time. This is the perfect analogy for how AI is transforming the Industrial Internet of Things (IIoT) in manufacturing.
The AI-IoT Duet
In recent years, the convergence of AI and IoT has been a hot topic in the tech world. According to a McKinsey report, the number of businesses using AI with IoT increased from 19% in 2018 to 27% in 2020, and this trend is expected to continue as more companies recognize the benefits of combining these two technologies.
AI is like the brain that processes the vast amounts of data generated by IoT sensors, providing insights and making decisions that optimize manufacturing processes. It’s the conductor that brings all the pieces together, creating a seamless and efficient operation.
Edge Computing: Bringing AI Closer to the Action
One of the key trends in the AI-IoT duet is the rise of edge computing. Instead of sending all the data generated by IoT sensors to the cloud for processing, edge computing allows data to be analyzed and acted upon closer to the source. This reduces latency and improves efficiency, enabling real-time decision-making and automation.
Imagine a quality control system that uses machine vision to inspect products on the production line. With edge computing, the AI algorithms can analyze the images in real-time, identifying defects and triggering corrective actions immediately. This prevents defective products from reaching customers and reduces waste, ultimately saving time and money.
Predictive Maintenance: Preventing Downtime Before it Happens
Another area where AI is making a significant impact in manufacturing is predictive maintenance. By analyzing data from IoT sensors on machines, AI algorithms can predict when a machine is likely to fail, allowing maintenance to be scheduled before a breakdown occurs.
Think of it like a car that tells you when it needs an oil change or when the brakes are wearing out. By addressing these issues proactively, you can avoid costly repairs and extend the life of the vehicle. The same principle applies to manufacturing equipment, where unplanned downtime can be incredibly expensive.
Real-World Success Stories
- Rolls-Royce uses IoT sensors in its aircraft engines to monitor performance and predict maintenance needs, saving airlines millions of dollars in potential downtime.
- Cisco uses IoT sensors to track the location and condition of its products throughout the supply chain, reducing inventory costs and improving customer satisfaction.
- BMW uses IoT sensors to monitor the quality of its cars as they move through the production line, identifying potential issues before they reach the customer.
These are just a few examples of how AI and IoT are delivering value in manufacturing. As the technology matures and standards emerge, we can expect to see even more remarkable results in the years to come.
Key Solutions: Samsara and Tulip
As the demand for AI and IoT solutions in manufacturing grows, several key players have emerged to help companies harness the power of these technologies. Two notable examples are Samsara and Tulip.
Samsara offers a Connected Operations Cloud that enables businesses in industries such as transportation, construction, and manufacturing to harness and analyze IoT data. Their platform collects trillions of data points from sensors, cameras, and other IoT devices, providing real-time visibility and insights across operations.
For example, Samsara’s AI Dash Cams can detect distracted driving in real-time, prompting drivers to self-correct and reducing unsafe behavior by up to 50% in just three months. Their platform also enables predictive maintenance, helping companies spot potential issues before they lead to costly downtime.
Tulip, on the other hand, focuses on empowering frontline workers with IoT-enabled apps. Their no-code platform allows manufacturers to digitize their operations, connecting workers, machines, and devices in a seamless ecosystem.
With Tulip, companies can create digital work instructions, track production in real-time, and analyze performance data to drive continuous improvement. Their IoT-enabled apps have helped manufacturers reduce defects by up to 60%, increase productivity by up to 30%, and cut training time by up to 90%.
Both Samsara and Tulip are prime examples of how AI and IoT can be leveraged to transform manufacturing operations. By providing intuitive platforms and actionable insights, these solutions are helping companies unlock new levels of efficiency, quality, and agility.
The Future: Autonomous Everything
Looking ahead, the combination of AI and IoT is poised to transform manufacturing in ways we can only imagine. As IoT devices become more intelligent and interconnected, we can expect to see a rise in autonomous systems, from self-driving forklifts to self-optimizing production lines.
AI will enable these systems to make decisions and adapt to changing conditions in real-time, improving efficiency, quality, and safety. It’s like having a team of expert operators working 24/7, never getting tired or making mistakes.
Challenges and Considerations
Of course, implementing AI and IoT in manufacturing is not without its challenges. Cybersecurity is a major concern, as the increased connectivity of devices creates more potential entry points for hackers. Manufacturers need to prioritize security and implement robust measures to protect their systems and data.
Data quality is another critical factor. AI is only as good as the data it’s trained on, so manufacturers need to ensure that the data collected by IoT sensors is accurate, consistent, and relevant. This requires careful planning and ongoing maintenance of the IoT infrastructure.
Finally, there’s the issue of skills and talent. Implementing and maintaining AI and IoT systems requires a new set of skills that may not be readily available in the current workforce. Manufacturers need to invest in training and education to build the necessary expertise in-house or partner with external providers who can fill the gap.
Conclusion
The convergence of AI and IoT is ushering in a new era of smart manufacturing, where machines talk to each other, learn from their experiences, and optimize themselves for maximum efficiency. It’s a world where downtime is minimized, quality is assured, and waste is eliminated.
As manufacturers embrace this technology, they unlock new levels of productivity, agility, and competitiveness. The journey may be challenging, but the rewards are immense. With the help of key solutions like Samsara and Tulip, companies can navigate this new landscape with confidence, conducting a symphony of machines and data that will propel them to the forefront of Industry 4.0.
Ready to see CADDi Drawer in action? Get a personalized demo.
Subscribe to our Blog!
Related Resources
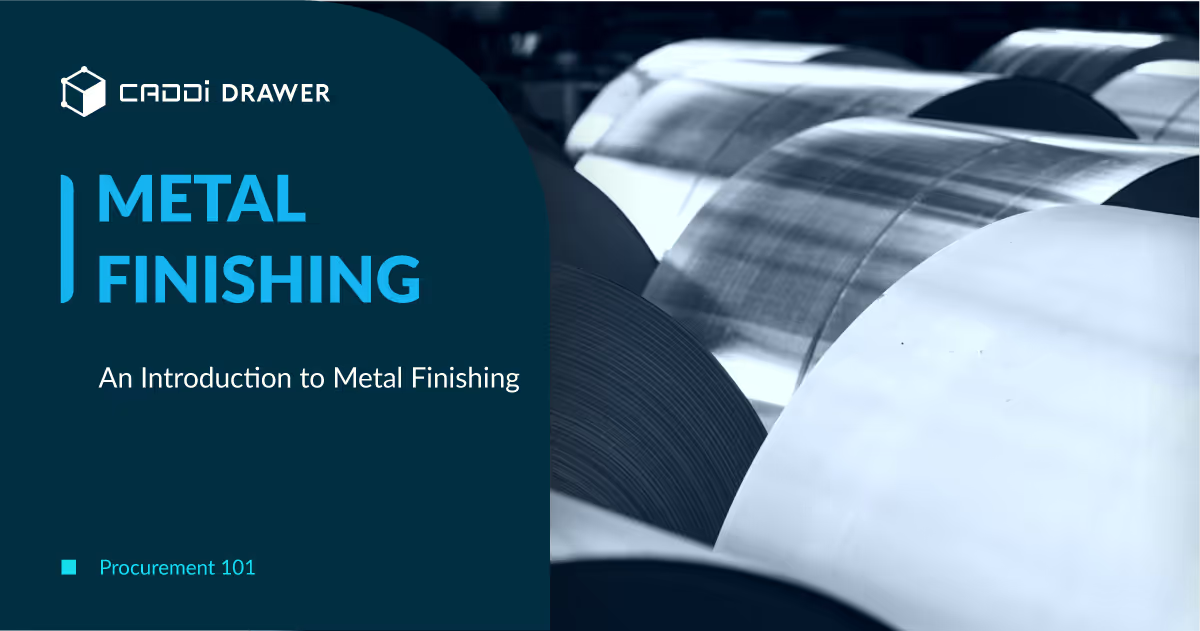
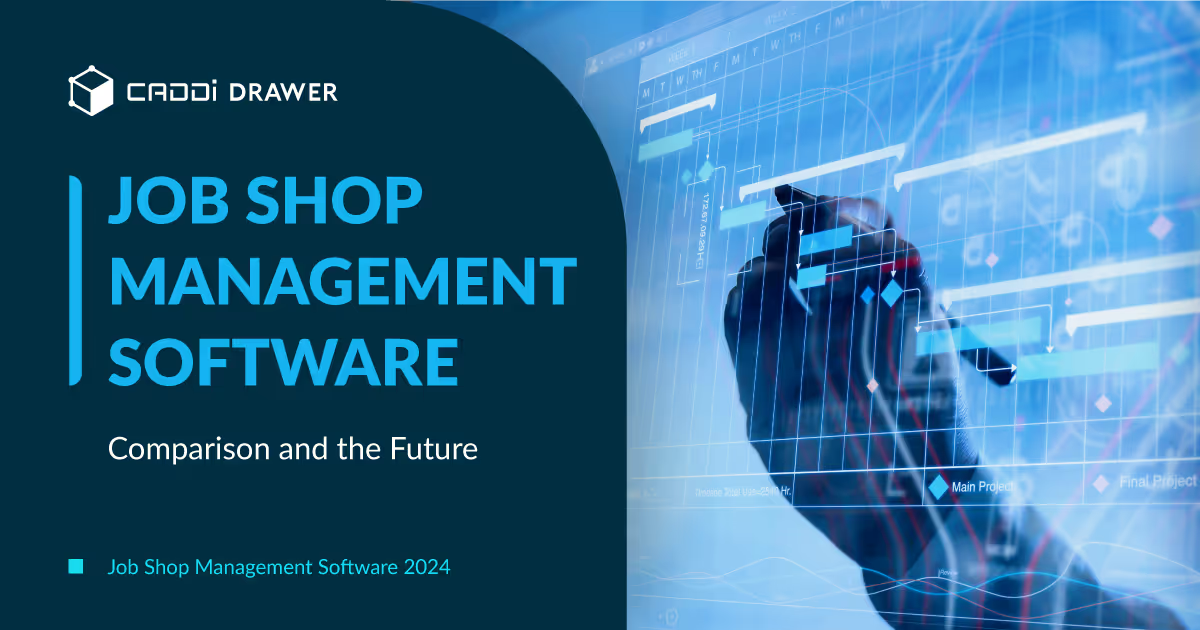
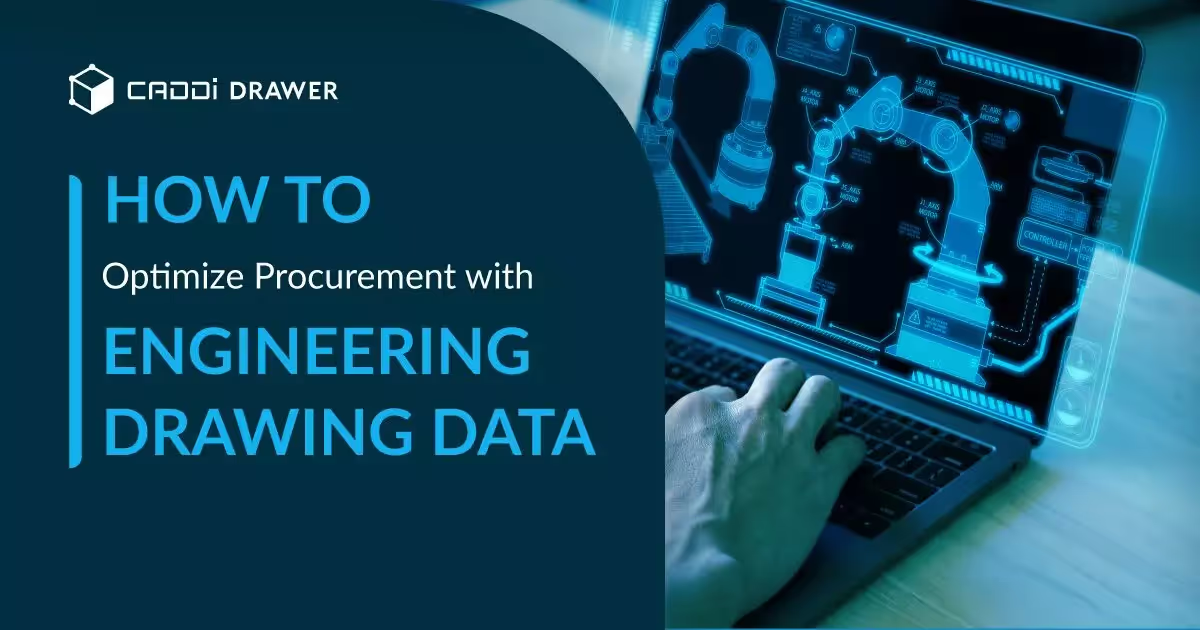
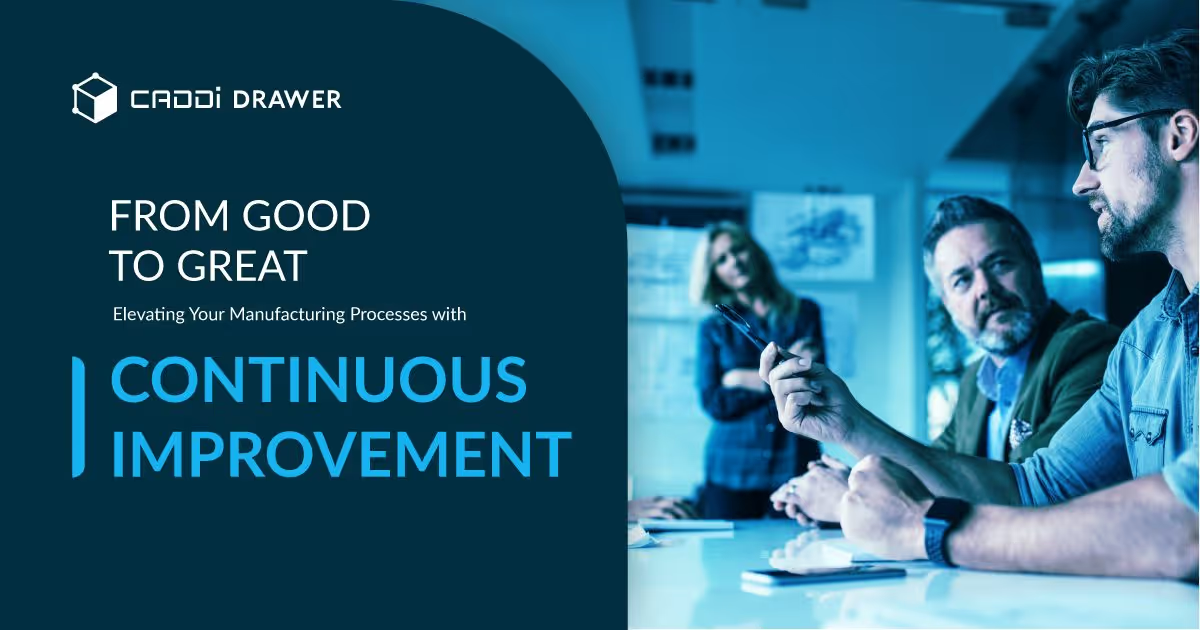
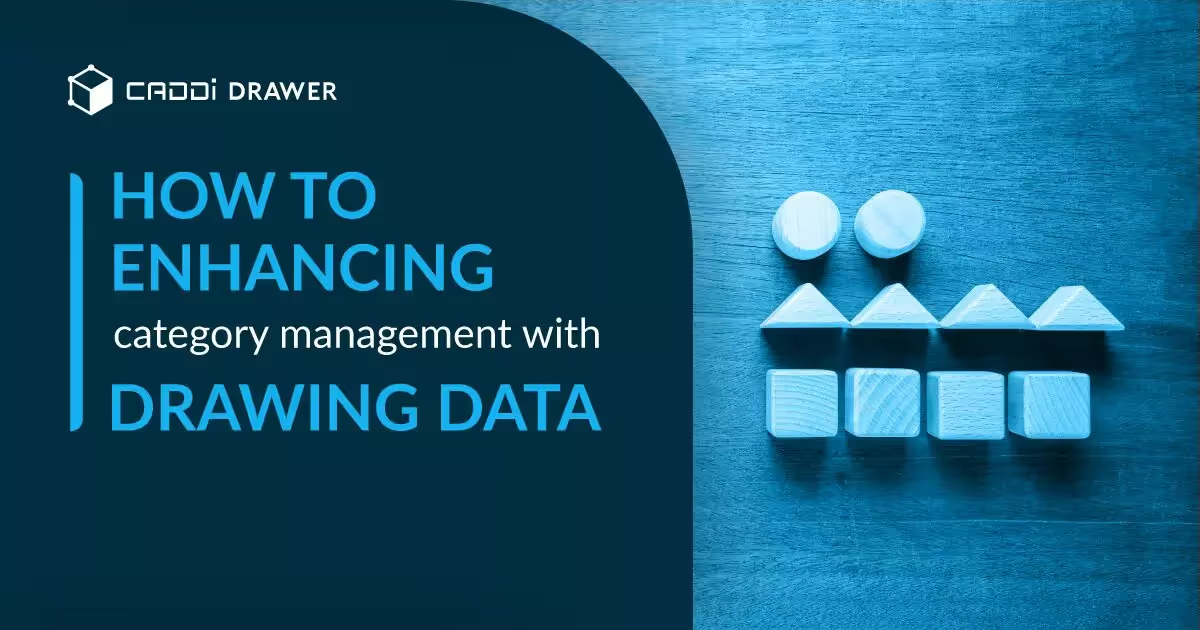
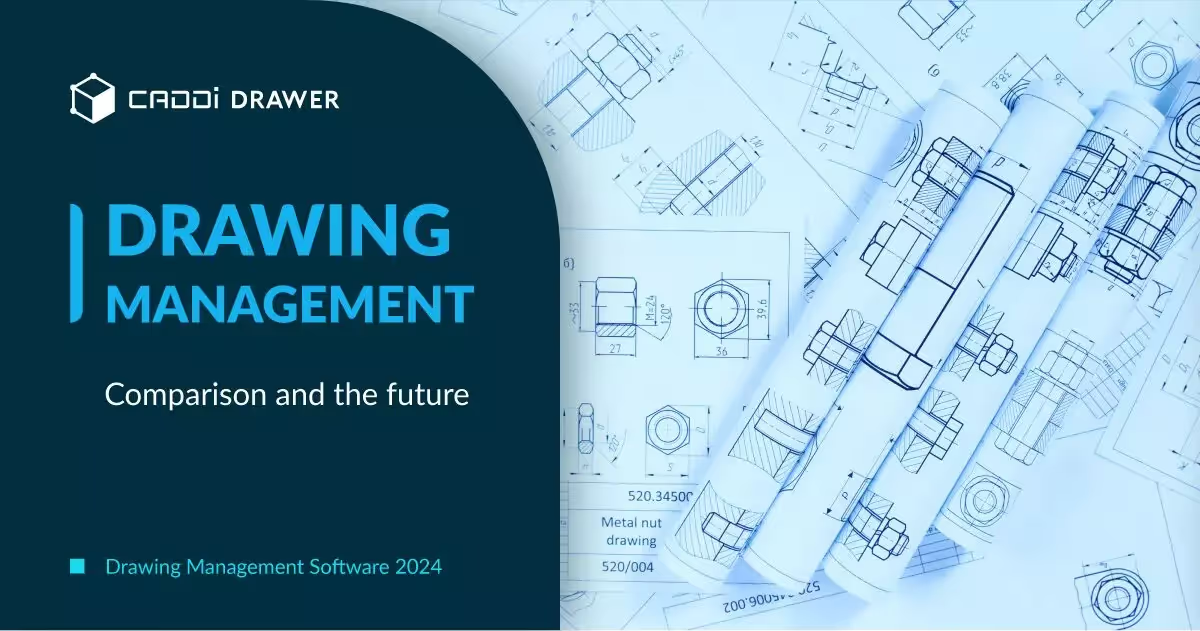