Job Shop Management Software 2024 – Comparison and the future
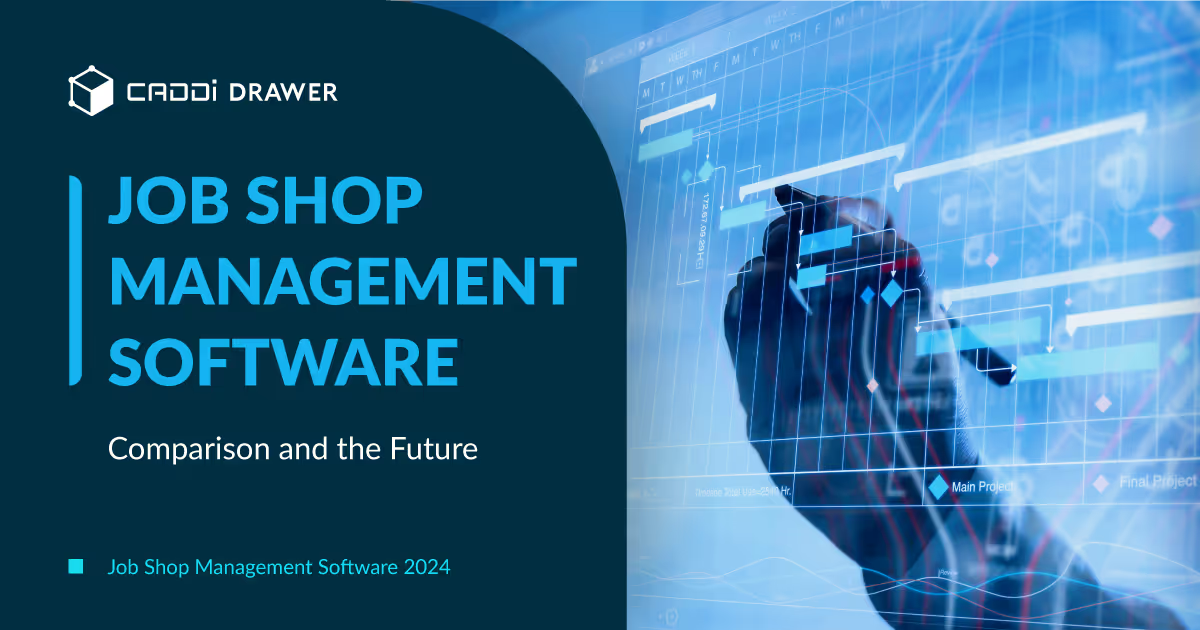
Table of Contents
What is Job Shop Management?
Job shop manufacturing involves producing custom, low-volume parts, creating challenges in tracking orders, scheduling resources, and managing inventory. Job shop management software helps efficiently plan and control workflow in this complex environment.
Job shops need flexible systems to handle variability, custom work, and short lead times. Intricate dependencies between tasks, equipment, staff skills, and inventory require responsive systems to maximize output.
Job shop software offers specialized capabilities to accurately quote, intelligently schedule, precisely track costs, and optimize resources. Key features enable systematic execution for on-time delivery, including:
- Increased on-time delivery through production planning and control
- Faster, accurate quoting based on previous jobs
- Profitability insights by job, product line, or customer
- Real-time visibility of work in progress and bottlenecks
- Inventory, purchasing, and material requirements management
- Seamless workflows from estimating through delivery
- Data collection, analysis, and reporting for continuous improvement
Key Features of Job Shop Management Software
Tracking Jobs and Operations
Job shop management software enables manufacturers to closely track the status of jobs and operations across the production floor in real-time. This allows managers and workers to monitor job progress and identify any bottlenecks or issues that may impact on-time delivery.
- Real-time visibility into job status: Software provides up-to-date statuses for all in-process jobs such as queued, in production, awaiting quality inspection, complete, etc. Dashboards and screens show current status of every job.
- Operation monitoring: In addition to high-level job tracking, systems drill down to monitor the status of individual operations within each job. Users can see which operations are running on schedule versus delayed.
- Job scheduling: Software assists with scheduling jobs and sequencing operations in the most efficient workflow. Scheduling engines optimize job timelines based on due dates, machine/worker availability, and shop floor capacity.
- Dispatching jobs to machines/workers: Systems facilitate dispatching jobs to machines and workers on the shop floor based on schedules and availability. Jobs can be automatically routed or assigned for execution based on predefined parameters.
- Bottleneck identification: By tracking real-time status of all jobs and operations, software can rapidly identify bottlenecks that threaten on-time delivery. Users are alerted to jobs or machines that are delayed so issues can be addressed quickly.
- Reports and analytics: Robust reporting provides production managers with insights into job tracking metrics. Key performance indicators relating to job status, machine utilization, worker productivity, and more can be analyzed.
Quoting and Estimating
Developing accurate quotes is critical for the profitability and competitiveness of any job shop. Job shop management software provides powerful tools to streamline and optimize the quoting process. Tight integration with planning, scheduling, inventory, and costing ensures the entire business is run on realistic production data.
- Estimating based on operations: The software allows you to build quotes by defining the operations required, including operation times and labor costs. This ensures quotes reflect the true processing requirements.
- Material costing: You can assign materials, consumable tools, and purchased items to the quote with unit costs and quantities. This rolls up into the final quote amount.
- Overhead allocation: Overhead rates based on machine hourly rates can be automatically applied to operations to cover indirect costs. This prevents underquoting jobs.
- Standard vs actual costing: You can choose to quote based on standard costs for materials and operations set in the software. Or you can base it on actual costs if preferred. Estimates based on actual costs help achieve faster quotation.
- Analysis of profitability: When the quote is complete, profitability analysis shows the estimated margin by comparing the quoted cost to the selling price. You can iterate to optimize profitability.
- Quotation accuracy: As jobs are executed, you can compare actual costs to the original quote to identify process improvements. This improves future quoting accuracy.
Data Collection and Reporting
Job shop management software provides robust data collection and reporting capabilities to help manufacturers optimize processes and performance. The software captures detailed data on shop floor activities, including:
- Labor tracking: Record employee hours, monitor productivity, analyze costs. Integrate with timeclock systems.
- Machine monitoring: Track machine runtime, utilization, downtime. Identify bottlenecks.
- Job progress: Log operations completed, track cycle times, identify delays.
- Quality metrics: Capture reject rates, identify issues, implement corrective actions.
- Inventory transactions: Log material issues and receipts, track inventory accuracy.
Powerful reporting tools then generate insightful reports and analysis from the collected data. Common reports include:
- Job status reports – Realtime visibility into work in progress. Identify late jobs
- Labor analysis – Evaluate efficiency, balance workloads, reduce overtime
- Machine utilization reports – Optimize production by identifying underutilized machines
- Quality control charts – Spot defects, trace root causes, reduce scraps
- Costing reports – Calculate precise job costs, analyze profitability
- Inventory analysis – Manage stock levels, reduce excess inventory
- Custom reports – Tailor reports to your specific needs
Integrations and Connectivity
Job shop management software often needs to integrate with other systems to share data and improve workflows. Two key integration capabilities to consider are connecting to accounting, ERP, CRM, Electronic data interchange (EDI) and other business systems, as well as having APIs available for developing custom integrations. Popular integrations for job shop software include:
- Accounting: Send completed job financials to accounting software to eliminate duplicate data entry. Many job shop systems integrate with Intuit QuickBooks, Sage 100, Microsoft Dynamics, and more.
- ERP: Bi-directional integration with ERP systems like SAP, Oracle, Infor helps production and inventory data flow between the shop floor and back office.
- CRM: Integration with Salesforce, Zoho and other CRMs makes customer data available to production teams and keeps both systems in sync.
- EDI: Electronic data interchange standardizes B2B data transfer with customers and suppliers.
- Shipping: Get real-time shipping rates and print labels by connecting to carriers like UPS, FedEx and USPS.
Planning and Scheduling Optimization
Job shop management software helps optimize production planning and job scheduling to improve workflow and maximize resource utilization. Effective planning and scheduling is critical for job shops to deliver quality products on time while controlling costs.
- Forward and backward scheduling to allocate jobs considering constraints. The software schedules tasks as early as possible or backwards from due dates.
- Multi-level pegging to link material requirements with job operations. This ensures components and materials are available when needed.
- Capacity planning tools to visualize workloads. The system highlights overloads and underutilized resources.
- Drag and drop Gantt charts for easy scheduling adjustments. Users can reschedule operations by dragging them on the interactive chart.
- Automated schedule optimization to maximize throughput. The software can automatically sequence jobs and balance loads based on set rules.
- Machine utilization tracking to balance work and prevent overloading.
- Scheduling analytics to assess on-time delivery and identify bottlenecks.
Optimizing Inventory and Purchasing for Efficiency
Job shop management software provides robust tools to optimize inventory levels and streamline purchasing. By closely monitoring raw materials, work-in-process, and finished goods, manufacturers gain real-time visibility into stock levels.
The software uses algorithms and analysis to determine ideal inventory quantities, balancing holding costs with the risk of stock-outs. Material requirements planning functionality projects future usage based on production schedules to fine-tune purchasing.
Automated alerts trigger purchase orders when stock is low, while integration with suppliers enables seamless ordering and tracking. With these capabilities, job shops can minimize inventory investment while ensuring materials are available when needed for smooth production and on-time delivery.
Leading Job Shop Management Software
Manufacturers running job shops require software that can handle their unique workflow needs and challenges. There are several leading options on the market that provide robust job shop management capabilities.
CADDi Drawer
CADDi Drawer is a cloud-based solution that streamlines quotations and data management for job shops by enabling full utilization of drawing data. Key features include:
- Centralized storage and management of drawing data in the cloud
- Powerful search capabilities, including searching handwritten text on drawings
- Ability to link drawings with supplementary information like purchase orders and manufacturing data
- Mobile access to drawings from tablets for the shop floor
- Seamless sharing of drawing data across departments
By digitizing drawings and linking them with key data, CADDi Drawer eliminates manual, person-dependent processes. This allows job shops to speed up quotations, reduce manufacturing errors, optimize estimates, and enable company-wide productivity gains.
Hilltop, a machine shop with high technical capabilities not only in manufacturing but also in systems, having developed in-house systems from sales to production and achieving 24-hour factory operation through automation, successfully introduced CADDi Drawer to make up for insufficient utilization of drawing data. This allowed them to significantly streamline their quotation process and procurement of materials and parts.
Hilltop’s Success Case: Accelerating Company-Wide Digital Transformation with CADDi Drawer
Pricing is not available, but requesting a demo allows you to learn more details, including pricing.
JobBOSS
JobBOSS from Exact provides complete shop floor control and visibility across the production process. Key features include:
- Powerful scheduling tools with drag-and-drop Gantt charts
- Real-time labor tracking with clock-in/out
- Materials Requirements Planning
- Automated data collection via barcoding and terminals
- Quality control with corrective action tracking
- Cost tracking by job and operation
JobBOSS is designed for make-to-order, assemble-to-order, engineer-to-order, and other custom manufacturing environments. It offers real-time insights into WIP, costs, profitability, resource utilization, and other KPIs.
Pricing starts at $200 per user per month. JobBOSS is best suited for small to mid-sized custom manufacturers.
Global Shop Solutions One-System ERP
Global Shop Solutions One-System ERP provides integrated modules across the entire manufacturing organization. Key features include:
- Scheduling and capacity planning
- MRP and inventory control
- Quality management
- Tool tracking
- Data collection
- Accounting/ERP
One-System ERP manages the entire job shop workflow in a single integrated system. This eliminates redundant data entry and provides end-to-end visibility.
Pricing starts at $2,995 per user. Global Shop Solutions targets small to mid-sized manufacturers with mixed-mode production.
S2K Manufacturing for Visionaries
S2K Manufacturing is part of the S2K Vision ERP system. Key job shop features include:
- Complete shop floor scheduling
- Real-time job costing
- Paperless shop floor execution
- Inventory and MRP optimization
- Preventative maintenance
- Document control
S2K provides out-of-the-box best practices for repetitive, batch, and custom job shops. Rules-based scheduling optimizes production efficiency.
Pricing for S2K Manufacturing starts at $250 per month per user. The solution scales from small to large enterprises.
The Future of Job Shop Management Software
The future of job shop management software is promising, with advancements in technology driving innovation and efficiency. Cloud-based solutions will become more prevalent, enabling real-time collaboration and access to data from anywhere. AI and machine learning will enhance decision-making, optimizing scheduling, resource allocation, and predictive maintenance. Integration with IoT devices will provide granular, real-time data collection for improved visibility and control.
As software becomes more intelligent and connected, job shops will gain unprecedented insights and automation capabilities to remain competitive in an increasingly complex manufacturing landscape.
Conclusion
When evaluating job shop software, key aspects to compare include scheduling, inventory/MRP, data collection, quality and tooling, real-time reporting, and rules-based optimization. Leading options include CADDi Drawer, JobBOSS, Global Shop Solutions, and S2K Manufacturing, among others. The right solution depends on production environment, scale, and budget. Thoroughly reviewing options ensures finding the best fit.
What is Job Shop Management?
Job shop manufacturing involves producing custom, low-volume parts, creating challenges in tracking orders, scheduling resources, and managing inventory. Job shop management software helps efficiently plan and control workflow in this complex environment.
Job shops need flexible systems to handle variability, custom work, and short lead times. Intricate dependencies between tasks, equipment, staff skills, and inventory require responsive systems to maximize output.
Job shop software offers specialized capabilities to accurately quote, intelligently schedule, precisely track costs, and optimize resources. Key features enable systematic execution for on-time delivery, including:
- Increased on-time delivery through production planning and control
- Faster, accurate quoting based on previous jobs
- Profitability insights by job, product line, or customer
- Real-time visibility of work in progress and bottlenecks
- Inventory, purchasing, and material requirements management
- Seamless workflows from estimating through delivery
- Data collection, analysis, and reporting for continuous improvement
Key Features of Job Shop Management Software
Tracking Jobs and Operations
Job shop management software enables manufacturers to closely track the status of jobs and operations across the production floor in real-time. This allows managers and workers to monitor job progress and identify any bottlenecks or issues that may impact on-time delivery.
- Real-time visibility into job status: Software provides up-to-date statuses for all in-process jobs such as queued, in production, awaiting quality inspection, complete, etc. Dashboards and screens show current status of every job.
- Operation monitoring: In addition to high-level job tracking, systems drill down to monitor the status of individual operations within each job. Users can see which operations are running on schedule versus delayed.
- Job scheduling: Software assists with scheduling jobs and sequencing operations in the most efficient workflow. Scheduling engines optimize job timelines based on due dates, machine/worker availability, and shop floor capacity.
- Dispatching jobs to machines/workers: Systems facilitate dispatching jobs to machines and workers on the shop floor based on schedules and availability. Jobs can be automatically routed or assigned for execution based on predefined parameters.
- Bottleneck identification: By tracking real-time status of all jobs and operations, software can rapidly identify bottlenecks that threaten on-time delivery. Users are alerted to jobs or machines that are delayed so issues can be addressed quickly.
- Reports and analytics: Robust reporting provides production managers with insights into job tracking metrics. Key performance indicators relating to job status, machine utilization, worker productivity, and more can be analyzed.
Quoting and Estimating
Developing accurate quotes is critical for the profitability and competitiveness of any job shop. Job shop management software provides powerful tools to streamline and optimize the quoting process. Tight integration with planning, scheduling, inventory, and costing ensures the entire business is run on realistic production data.
- Estimating based on operations: The software allows you to build quotes by defining the operations required, including operation times and labor costs. This ensures quotes reflect the true processing requirements.
- Material costing: You can assign materials, consumable tools, and purchased items to the quote with unit costs and quantities. This rolls up into the final quote amount.
- Overhead allocation: Overhead rates based on machine hourly rates can be automatically applied to operations to cover indirect costs. This prevents underquoting jobs.
- Standard vs actual costing: You can choose to quote based on standard costs for materials and operations set in the software. Or you can base it on actual costs if preferred. Estimates based on actual costs help achieve faster quotation.
- Analysis of profitability: When the quote is complete, profitability analysis shows the estimated margin by comparing the quoted cost to the selling price. You can iterate to optimize profitability.
- Quotation accuracy: As jobs are executed, you can compare actual costs to the original quote to identify process improvements. This improves future quoting accuracy.
Data Collection and Reporting
Job shop management software provides robust data collection and reporting capabilities to help manufacturers optimize processes and performance. The software captures detailed data on shop floor activities, including:
- Labor tracking: Record employee hours, monitor productivity, analyze costs. Integrate with timeclock systems.
- Machine monitoring: Track machine runtime, utilization, downtime. Identify bottlenecks.
- Job progress: Log operations completed, track cycle times, identify delays.
- Quality metrics: Capture reject rates, identify issues, implement corrective actions.
- Inventory transactions: Log material issues and receipts, track inventory accuracy.
Powerful reporting tools then generate insightful reports and analysis from the collected data. Common reports include:
- Job status reports – Realtime visibility into work in progress. Identify late jobs
- Labor analysis – Evaluate efficiency, balance workloads, reduce overtime
- Machine utilization reports – Optimize production by identifying underutilized machines
- Quality control charts – Spot defects, trace root causes, reduce scraps
- Costing reports – Calculate precise job costs, analyze profitability
- Inventory analysis – Manage stock levels, reduce excess inventory
- Custom reports – Tailor reports to your specific needs
Integrations and Connectivity
Job shop management software often needs to integrate with other systems to share data and improve workflows. Two key integration capabilities to consider are connecting to accounting, ERP, CRM, Electronic data interchange (EDI) and other business systems, as well as having APIs available for developing custom integrations. Popular integrations for job shop software include:
- Accounting: Send completed job financials to accounting software to eliminate duplicate data entry. Many job shop systems integrate with Intuit QuickBooks, Sage 100, Microsoft Dynamics, and more.
- ERP: Bi-directional integration with ERP systems like SAP, Oracle, Infor helps production and inventory data flow between the shop floor and back office.
- CRM: Integration with Salesforce, Zoho and other CRMs makes customer data available to production teams and keeps both systems in sync.
- EDI: Electronic data interchange standardizes B2B data transfer with customers and suppliers.
- Shipping: Get real-time shipping rates and print labels by connecting to carriers like UPS, FedEx and USPS.
Planning and Scheduling Optimization
Job shop management software helps optimize production planning and job scheduling to improve workflow and maximize resource utilization. Effective planning and scheduling is critical for job shops to deliver quality products on time while controlling costs.
- Forward and backward scheduling to allocate jobs considering constraints. The software schedules tasks as early as possible or backwards from due dates.
- Multi-level pegging to link material requirements with job operations. This ensures components and materials are available when needed.
- Capacity planning tools to visualize workloads. The system highlights overloads and underutilized resources.
- Drag and drop Gantt charts for easy scheduling adjustments. Users can reschedule operations by dragging them on the interactive chart.
- Automated schedule optimization to maximize throughput. The software can automatically sequence jobs and balance loads based on set rules.
- Machine utilization tracking to balance work and prevent overloading.
- Scheduling analytics to assess on-time delivery and identify bottlenecks.
Optimizing Inventory and Purchasing for Efficiency
Job shop management software provides robust tools to optimize inventory levels and streamline purchasing. By closely monitoring raw materials, work-in-process, and finished goods, manufacturers gain real-time visibility into stock levels.
The software uses algorithms and analysis to determine ideal inventory quantities, balancing holding costs with the risk of stock-outs. Material requirements planning functionality projects future usage based on production schedules to fine-tune purchasing.
Automated alerts trigger purchase orders when stock is low, while integration with suppliers enables seamless ordering and tracking. With these capabilities, job shops can minimize inventory investment while ensuring materials are available when needed for smooth production and on-time delivery.
Leading Job Shop Management Software
Manufacturers running job shops require software that can handle their unique workflow needs and challenges. There are several leading options on the market that provide robust job shop management capabilities.
CADDi Drawer
CADDi Drawer is a cloud-based solution that streamlines quotations and data management for job shops by enabling full utilization of drawing data. Key features include:
- Centralized storage and management of drawing data in the cloud
- Powerful search capabilities, including searching handwritten text on drawings
- Ability to link drawings with supplementary information like purchase orders and manufacturing data
- Mobile access to drawings from tablets for the shop floor
- Seamless sharing of drawing data across departments
By digitizing drawings and linking them with key data, CADDi Drawer eliminates manual, person-dependent processes. This allows job shops to speed up quotations, reduce manufacturing errors, optimize estimates, and enable company-wide productivity gains.
Hilltop, a machine shop with high technical capabilities not only in manufacturing but also in systems, having developed in-house systems from sales to production and achieving 24-hour factory operation through automation, successfully introduced CADDi Drawer to make up for insufficient utilization of drawing data. This allowed them to significantly streamline their quotation process and procurement of materials and parts.
Hilltop’s Success Case: Accelerating Company-Wide Digital Transformation with CADDi Drawer
Pricing is not available, but requesting a demo allows you to learn more details, including pricing.
JobBOSS
JobBOSS from Exact provides complete shop floor control and visibility across the production process. Key features include:
- Powerful scheduling tools with drag-and-drop Gantt charts
- Real-time labor tracking with clock-in/out
- Materials Requirements Planning
- Automated data collection via barcoding and terminals
- Quality control with corrective action tracking
- Cost tracking by job and operation
JobBOSS is designed for make-to-order, assemble-to-order, engineer-to-order, and other custom manufacturing environments. It offers real-time insights into WIP, costs, profitability, resource utilization, and other KPIs.
Pricing starts at $200 per user per month. JobBOSS is best suited for small to mid-sized custom manufacturers.
Global Shop Solutions One-System ERP
Global Shop Solutions One-System ERP provides integrated modules across the entire manufacturing organization. Key features include:
- Scheduling and capacity planning
- MRP and inventory control
- Quality management
- Tool tracking
- Data collection
- Accounting/ERP
One-System ERP manages the entire job shop workflow in a single integrated system. This eliminates redundant data entry and provides end-to-end visibility.
Pricing starts at $2,995 per user. Global Shop Solutions targets small to mid-sized manufacturers with mixed-mode production.
S2K Manufacturing for Visionaries
S2K Manufacturing is part of the S2K Vision ERP system. Key job shop features include:
- Complete shop floor scheduling
- Real-time job costing
- Paperless shop floor execution
- Inventory and MRP optimization
- Preventative maintenance
- Document control
S2K provides out-of-the-box best practices for repetitive, batch, and custom job shops. Rules-based scheduling optimizes production efficiency.
Pricing for S2K Manufacturing starts at $250 per month per user. The solution scales from small to large enterprises.
The Future of Job Shop Management Software
The future of job shop management software is promising, with advancements in technology driving innovation and efficiency. Cloud-based solutions will become more prevalent, enabling real-time collaboration and access to data from anywhere. AI and machine learning will enhance decision-making, optimizing scheduling, resource allocation, and predictive maintenance. Integration with IoT devices will provide granular, real-time data collection for improved visibility and control.
As software becomes more intelligent and connected, job shops will gain unprecedented insights and automation capabilities to remain competitive in an increasingly complex manufacturing landscape.
Conclusion
When evaluating job shop software, key aspects to compare include scheduling, inventory/MRP, data collection, quality and tooling, real-time reporting, and rules-based optimization. Leading options include CADDi Drawer, JobBOSS, Global Shop Solutions, and S2K Manufacturing, among others. The right solution depends on production environment, scale, and budget. Thoroughly reviewing options ensures finding the best fit.
Ready to see CADDi Drawer in action? Get a personalized demo.
Subscribe to our Blog!
Related Resources
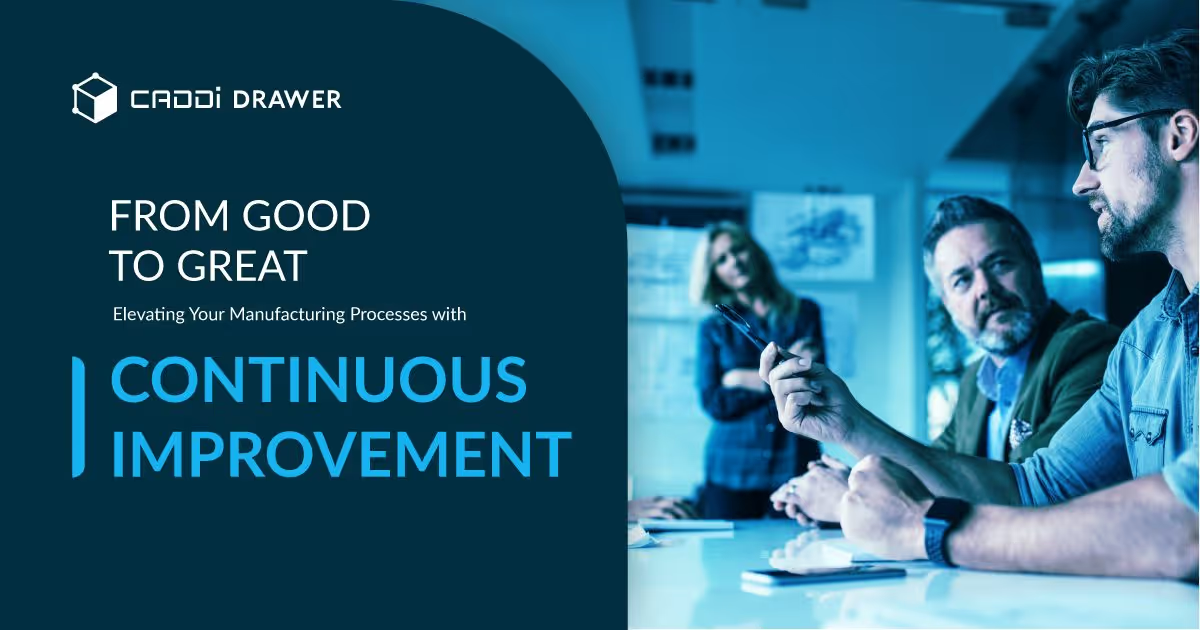
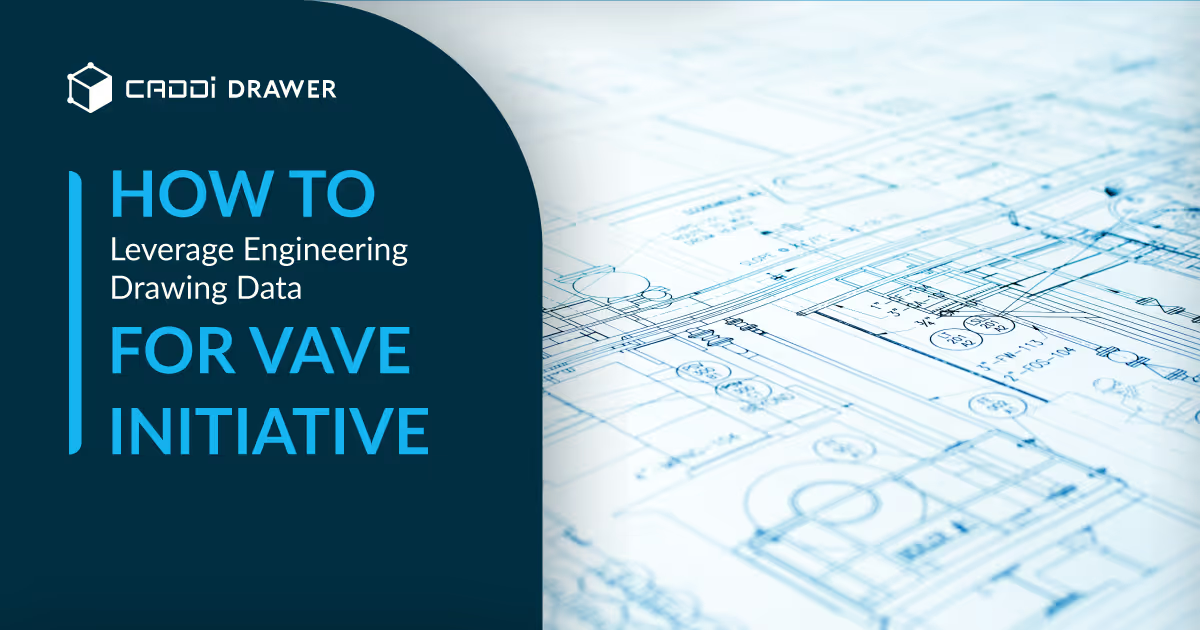
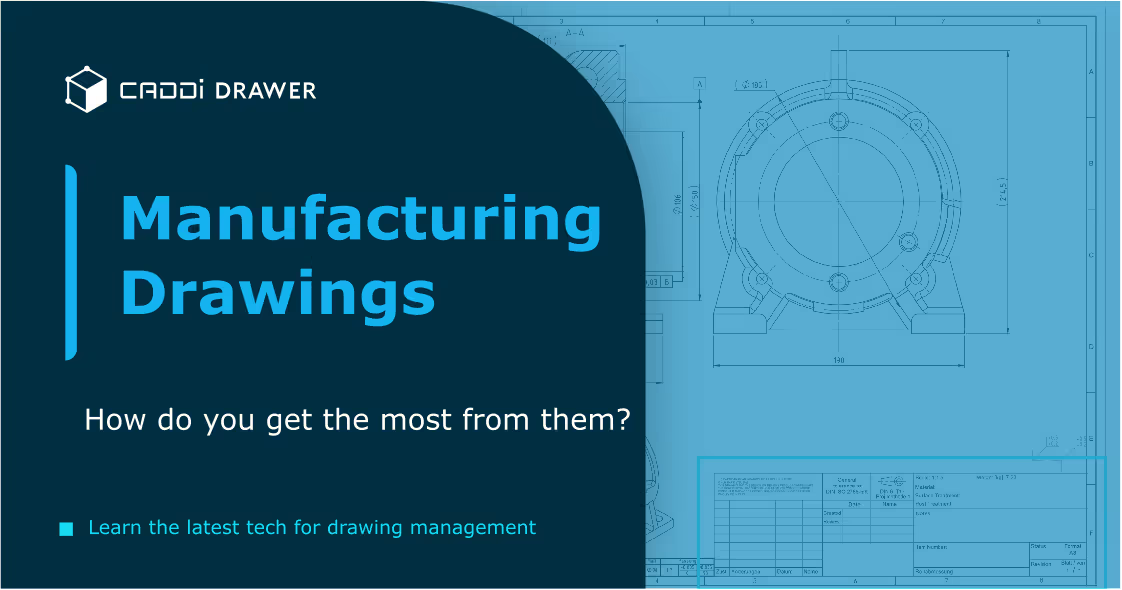
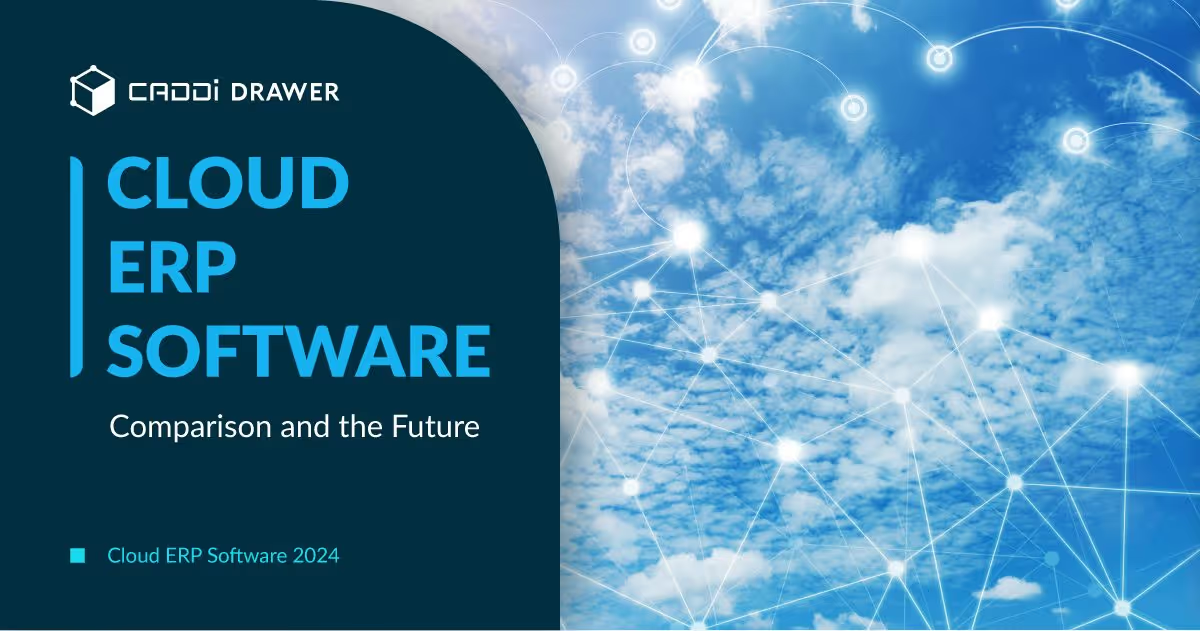
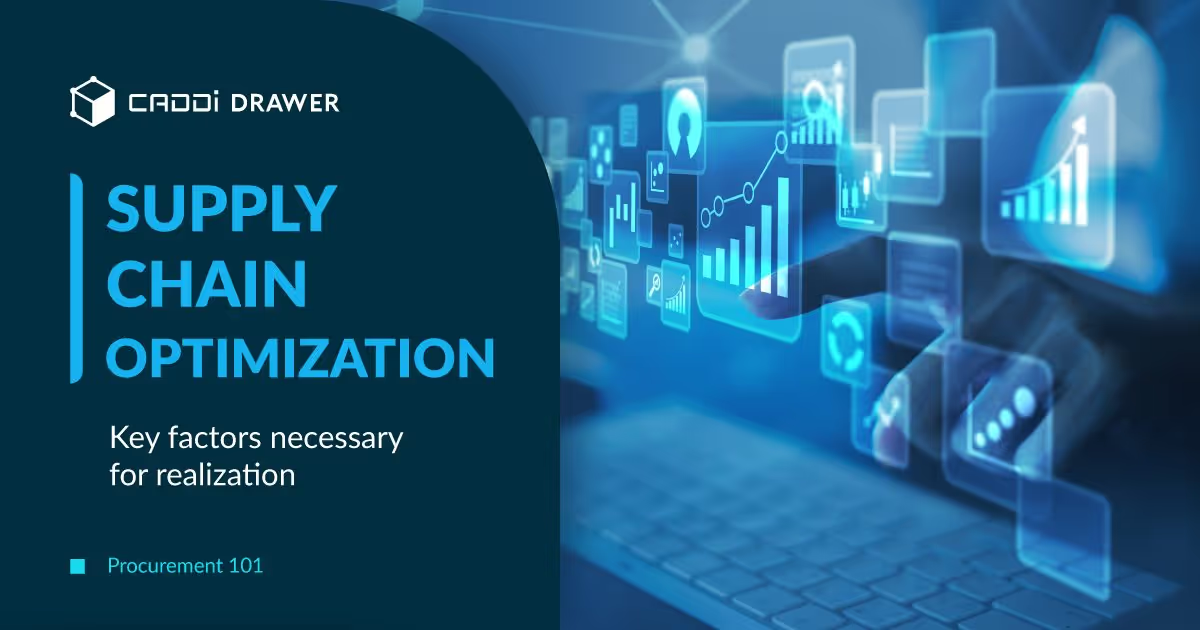
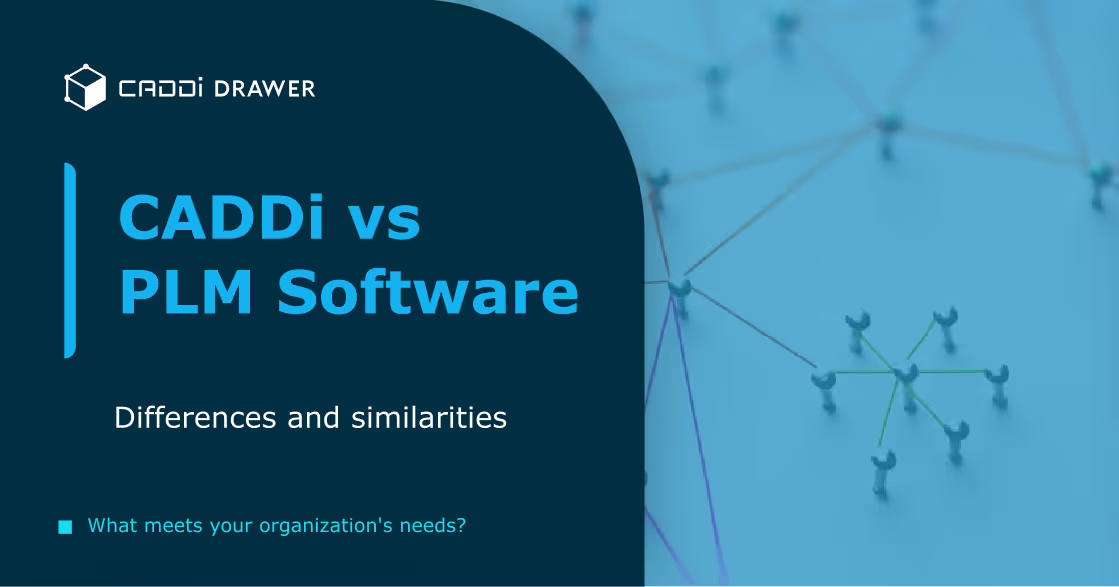