Procurement 101: An Introduction to Metal Finishing
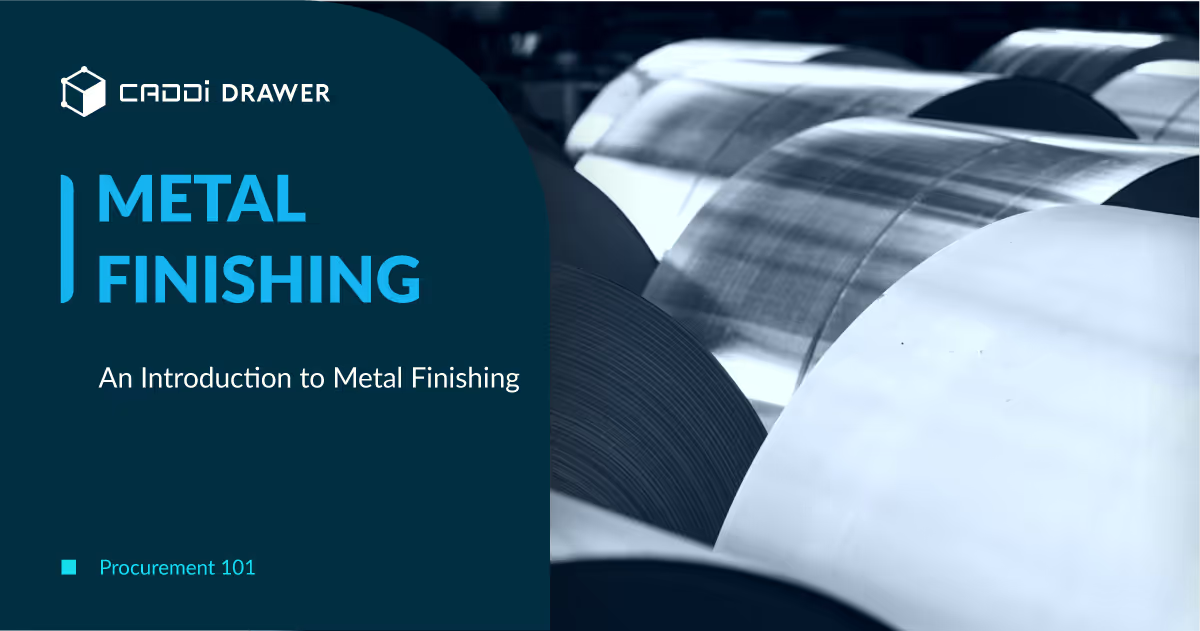
Table of Contents
What is metal finishing?
Metal finishing refers to processes that alter the surface properties of metals through mechanical, chemical, electrochemical, or thermal means. The primary goal of metal finishing is to enhance durability, appearance, conductivity, solderability, resistance to corrosion, hardness, and other properties.
Common metal finishing techniques include:
- Electroplating: Coating metal surfaces with a thin layer of metal using electrical current
- Anodizing: Forming a protective oxide layer on metals like aluminum and titanium through electrolysis
- Galvanizing: Applying a zinc coating to steel or iron to prevent rusting
- Painting: Applying a polymer powder, a liquid paint or resin to a surface, which then baked, dries or cures to form a protective layer
- Blasting: Using compressed air to propel abrasive particles (such as sand or glass beads) at a surface to clean, roughen, or prepare it for coating
- Grinding and polishing: Mechanically removing surface material and smoothing the surface using abrasive tools like grinding wheels, sandpaper, or polishing compounds
- Pickling and etching: Chemically removing surface contaminants, scale, or oxide layers using acidic solutions, and roughening or patterning the surface through controlled chemical dissolution
- Thermal spray coating: Melting powdered metals and spraying them onto a surface to form a coating
- Thin-film coating: Depositing thin layers of material onto a surface using physical vapor deposition (PVD) or chemical vapor deposition (CVD) techniques to improve properties such as hardness, wear resistance, or optical characteristics
Metal finishing is used across many industries including automotive, aerospace, medical devices, architecture, jewelry, and more. Highly engineered parts often require tailored metal finishes to achieve durability, aesthetics, performance, and longevity. The wide range of metal finishing processes allows the physical, chemical, and visual properties of metal components and products to be precisely controlled.
Electroplating
Electroplating is a process that uses electrical current to coat a conductive surface with a thin layer of metal. The part to be plated is immersed in a solution containing metal salts and acts as the cathode (negative electrode). When electrical current is applied, metal ions in the solution are reduced at the surface of the part, forming a thin metal coating.
Some common types of electroplating include:
- Chrome plating – Provides a bright, shiny decorative finish as well as abrasion and corrosion resistance. Used on automotive trim, hardware, appliances.
- Nickel plating – Offers wear resistance along with corrosion protection. Used on machinery parts, hand tools, kitchen utensils.
- Copper plating – Provides electrical conductivity and lubricity. Used in electrical contacts and bearings.
- Silver plating – Has higher electrical conductivity than copper. Used in electrical contacts and conductors.
- Gold plating – Decorative finish and enhanced electrical conductivity. Used in jewelry, electronics, dental implants.
Benefits of electroplating include:
- Improved corrosion and wear resistance
- Enhanced conductivity
- Decorative appeal
- Restoration of dimensions on worn parts
- Ability to plate non-metallic surfaces like plastics
- Cost-effective and efficient method to coat large quantities of small parts
The process allows the properties of the plating metal to be imparted to the surface of the base material, expanding the potential applications of the substrate.
Anodizing
Anodizing is an electrolytic passivation process used to increase the thickness of the natural oxide layer on the surface of metal parts. The process is called anodizing because the part to be treated forms the anode electrode of an electrical circuit. Aluminum is the most widely anodized metal.
There are three main types of anodizing for aluminum:
- Chromic acid anodizing – Produces a thin, clear, yellowish coating that is durable, corrosion resistant, and electrically non-conductive.
- Sulfuric acid anodizing – The most common anodizing process. Produces a thicker coating that is a porous aluminum oxide integrated with the surface, instead of a deposit on the surface. The coating color ranges from light gray to black, depending on specific process. Provides corrosion resistance while maintaining electrical and thermal conductivity.
- Hard anodizing – Produces a very hard, abrasion-resistant coating. Achieved with baths at lower temperatures and higher current densities compared to sulfuric acid anodizing. The coating is nonconductive and ranges from gray to black in color. Commonly used in applications like hydraulic pistons and machine parts due to its hardened wear-resistant surface.
Key benefits of anodizing aluminum include:
- Excellent corrosion resistance and wear resistance
- Harder surface layer while retaining base material properties
- Ability to retain precise dimensions across surface
- Provides electrical insulation
- A wide range of application-specific coloring effects
Anodizing increases durability, longevity, and electrical insulation properties compared to bare aluminum. It is a common finishing process for critical aluminum components and parts across many industries.
Galvanizing
Galvanizing is a process that involves applying a protective zinc coating to steel or iron surfaces to prevent corrosion. The zinc layer acts as a barrier and sacrificial anode, protecting the underlying metal from rust and extending its lifespan.
There are several types of galvanizing, such as:
- Hot-dip galvanizing – The most common method, where steel parts are submerged in a bath of molten zinc.
- Electrogalvanizing – A process that uses electric current to deposit a thin layer of zinc onto the steel surface.
- Sherardizing – A diffusion process where steel parts are heated in a closed container with zinc dust, creating a zinc-iron alloy coating.
Benefits of galvanizing include:
- Long-lasting corrosion protection, even in harsh environments
- Durable, abrasion-resistant coating that does not chip, peel, or flake off
- Cost-effective method for protecting large steel structures
- Low maintenance requirements, as the zinc coating slowly corrodes over time, protecting the steel beneath
- Versatility in application, suitable for a wide range of steel products and components
Galvanizing is a proven and efficient method for protecting steel and iron from corrosion, making it an essential process in various industries, from construction to manufacturing.
Painting
Painting is a process that involves applying a protective or decorative layer of paint or other coating material to the surface of metal parts. This layer serves to protect the underlying metal from corrosion, wear, and environmental factors while also providing an attractive finish.
There are several types of painting for metal parts, such as:
- Powder coating – A process where a fine, dry powder is electrostatically charged and sprayed onto the metal surface, then heated to form a smooth, durable coating. It offers excellent corrosion resistance, mechanical properties, and a wide range of colors and finishes.
- Liquid coating – A method that involves applying a liquid paint or resin to the metal surface, which then dries or cures to form a protective layer. Depending on the type of solvent, desired finish, and coating conditions, the coating can be allowed to dry naturally (air drying) or can be baked (heat curing) to speed up the drying process and achieve specific properties.
- Electrophoretic deposition (EPD) – A process that uses an electric field to deposit charged particles from a liquid suspension onto the metal surface, creating a uniform coating. Cathodic electrophoretic deposition, where the metal substrate acts as the cathode, is the most common type of EPD. The coated metal is then rinsed and baked to cure the coating, resulting in a durable, corrosion-resistant finish.
Benefits of painting include:
- Protection against corrosion, scratches, and UV radiation
- Improved aesthetic appearance, with a wide range of color and texture options
- Enhanced durability and longevity of metal parts
- Increased resistance to chemicals, solvents, and other environmental factors
- Customizable properties, such as electrical insulation or conductivity, depending on the coating material used
Painting is a versatile and widely used method for protecting and enhancing the properties of metal parts, finding applications in various industries, from automotive and aerospace to consumer products and construction.
Blasting
Blasting is a surface treatment process that involves propelling abrasive particles at high velocities onto a metal surface using compressed air or centrifugal force. The purpose of blasting is to clean, roughen, or prepare the surface for subsequent coating applications or to achieve a desired finish.
There are several types of blasting used on metal parts, such as:
- Sand blasting – A process that uses sand or silica particles as the abrasive media to remove surface contaminants, rust, or old coatings from metal surfaces.
- Glass bead blasting – A method that employs small glass beads as the abrasive to create a uniform, matte finish on metal surfaces without removing significant amounts of material.
- Shot blasting – A process that uses metal shot (steel or stainless steel) as the abrasive to clean and strengthen metal surfaces through the introduction of compressive stress.
Benefits of blasting include:
- Removal of surface contaminants, rust, and old coatings
- Improved adhesion for subsequent coating applications
- Creation of desired surface finishes, such as matte or textured
- Increased surface hardness and durability through compressive stress (shot blasting)
- Versatility in application, with the ability to process large and small metal parts
Blasting is a crucial surface preparation technique used in various industries, including automotive, aerospace, and construction. It ensures that metal surfaces are clean, uniform, and ready for further processing, ultimately contributing to the improved performance and longevity of the final product.
Grinding and Polishing
Grinding and polishing are surface finishing processes used to remove material from a workpiece to achieve a desired surface finish, texture, or dimension. These processes are commonly employed in various industries, including metalworking, automotive, aerospace, and manufacturing.
There are several types of grinding and polishing, such as:
- Surface grinding – A process that uses a rotating abrasive wheel to remove material from the surface of a workpiece, creating a flat, smooth finish.
- Cylindrical grinding – A method used to grind the external or internal surfaces of cylindrical workpieces, such as shafts, bores, and bushings.
- Centerless grinding – A process that involves grinding the external surface of a workpiece without the need for a spindle or work holding device, making it suitable for high-volume production.
- Polishing – A finishing process that uses abrasive materials, such as diamond paste, aluminum oxide, or silicon carbide, to create a smooth, reflective surface finish. Mirror finishing is a type of polishing treatment that results in a highly reflective, mirror-like surface.
- Buffing – A finishing process that uses a soft wheel or belt with a fine abrasive compound to achieve a smooth, glossy surface finish. Buffing is often performed after polishing to remove any remaining fine scratches and enhance the overall appearance of the workpiece. This process is commonly used on metals, plastics, and other materials to create a high-luster finish.
Benefits of grinding and polishing include:
- Improved surface finish and aesthetic appearance
- Enhanced dimensional accuracy and precision
- Increased surface hardness and wear resistance
- Removal of surface defects, such as scratches, burrs, or tool marks
- Preparation of surfaces for subsequent coating or plating processes
Grinding and polishing are essential processes in the manufacturing industry, allowing for the production of high-quality, precision components with superior surface finishes and mechanical properties.
Pickling and Etching
Pickling and etching are chemical surface treatments used to remove contaminants, scale, rust, or unwanted layers from metal surfaces. These processes are essential for preparing metal parts for subsequent finishing processes, such as plating, coating, or painting.
There are two main types of pickling and etching:
- Pickling – A process that involves immersing metal parts in an acidic solution to remove surface impurities, such as rust, scale, or oxide layers. Common pickling solutions include hydrochloric acid, sulfuric acid, and nitric acid, depending on the metal being treated.
- Etching – A process that uses chemical solutions or acids to selectively remove material from the surface of a metal part, creating specific patterns, textures, or designs. Etching can also be used to reveal the microstructure of a metal for quality control or metallurgical analysis purposes.
Benefits of pickling and etching include:
- Removal of surface contaminants, rust, and scale
- Improved adhesion for subsequent coating or plating processes
- Creation of specific surface textures or patterns through etching
- Enhanced corrosion resistance by removing surface impurities
- Preparation of metal surfaces for further processing or finishing
Pickling and etching are crucial processes in the metal finishing industry, ensuring that metal surfaces are clean, uniform, and ready for subsequent treatments. These processes are widely used in various sectors, including automotive, aerospace, and manufacturing, to improve the quality and performance of metal components.
Thermal Spray Coating
Thermal spray coating is a process in which melted (or heated) materials are sprayed onto a surface to provide a protective coating. Some common thermal spray methods include:
- Flame spraying – Materials are melted with an oxy-fuel gas flame and sprayed onto the surface. This is one of the most economical thermal spray methods.
- Electric arc spraying – Materials are heated to a molten or semi-molten state with an electric arc and sprayed. This allows for higher spray velocities than flame spraying.
- Plasma spraying – Materials are turned into a plasma state with an electric arc and high temperature argon-hydrogen gas jets. This provides extremely high temperatures to melt difficult materials.
- High Velocity Oxygen Fuel (HVOF) – Similar to flame spraying but with higher particle velocities. Provides very dense, high-quality coatings.
Thermal sprays are commonly used to provide wear and corrosion resistance, or sometimes for aesthetic purposes. The high-temperature spraying process allows materials with very high melting points such as ceramics to be applied as coatings.
Compared to other coating methods, thermal spraying is advantageous because it provides very high bond strength, thick coatings, and versatility in applicable materials.
However, the surface finish is not as smooth as electroplated or anodized finishes. Also, capital equipment costs tend to be higher compared to some other coating methods.
Thin-Film Coating
Thin-film coating is a process that involves depositing a thin layer of material, typically in the range of nanometers to microns, onto the surface of a substrate. Two common methods for thin-film coating are Physical Vapor Deposition (PVD) and Chemical Vapor Deposition (CVD). These techniques are used to improve the properties and performance of various components and products.
The main types of thin-film coating include:
- Physical Vapor Deposition (PVD) – A process where a solid material is vaporized and then condensed onto the substrate surface in a vacuum chamber. Common PVD methods include sputtering, evaporation, and cathodic arc deposition.
- Chemical Vapor Deposition (CVD) – A process that involves the deposition of a thin film from a vapor phase onto a heated substrate surface. The coating material is formed by chemical reactions of gaseous precursors in the reactor.
- Atomic Layer Deposition (ALD) – A subtype of CVD that deposits thin films one atomic layer at a time, allowing for precise control over the coating thickness and composition.
Benefits of thin-film coating include:
- Improved hardness, wear resistance, and corrosion resistance
- Enhanced optical, electrical, and magnetic properties
- Reduced friction and improved lubricity
- Ability to deposit a wide range of materials, including metals, ceramics, and polymers
- Precise control over coating thickness, composition, and uniformity
Thin-film coating techniques like PVD and CVD are essential in various high-tech industries, such as semiconductor manufacturing, aerospace, automotive, and biomedical engineering, where they are used to create advanced materials and devices with superior properties and performance.
Environmental Considerations
The metal finishing industry must operate in an environmentally responsible manner by properly treating wastewater, following regulations, and implementing sustainable practices.
- Wastewater treatment is critical for metal finishing facilities as the wastewater contains heavy metals, acids, solvents, and other contaminants. Facilities must have proper pretreatment systems to remove pollutants before discharging water.
- Regulations govern air emissions, wastewater discharges, and hazardous waste disposal in metal finishing. Facilities must obtain required permits, test effluents, and install pollution controls to comply with regulations.
- The industry is developing more sustainable practices, such as using less hazardous materials, recycling chemicals, reducing energy and water use, and recovering metals for reuse.
Adopting safer chemicals, recycling, advanced wastewater treatment, and pollution prevention strategies promotes greener metal finishing, allowing the industry to protect the environment while meeting regulatory obligations and public expectations.
What is metal finishing?
Metal finishing refers to processes that alter the surface properties of metals through mechanical, chemical, electrochemical, or thermal means. The primary goal of metal finishing is to enhance durability, appearance, conductivity, solderability, resistance to corrosion, hardness, and other properties.
Common metal finishing techniques include:
- Electroplating: Coating metal surfaces with a thin layer of metal using electrical current
- Anodizing: Forming a protective oxide layer on metals like aluminum and titanium through electrolysis
- Galvanizing: Applying a zinc coating to steel or iron to prevent rusting
- Painting: Applying a polymer powder, a liquid paint or resin to a surface, which then baked, dries or cures to form a protective layer
- Blasting: Using compressed air to propel abrasive particles (such as sand or glass beads) at a surface to clean, roughen, or prepare it for coating
- Grinding and polishing: Mechanically removing surface material and smoothing the surface using abrasive tools like grinding wheels, sandpaper, or polishing compounds
- Pickling and etching: Chemically removing surface contaminants, scale, or oxide layers using acidic solutions, and roughening or patterning the surface through controlled chemical dissolution
- Thermal spray coating: Melting powdered metals and spraying them onto a surface to form a coating
- Thin-film coating: Depositing thin layers of material onto a surface using physical vapor deposition (PVD) or chemical vapor deposition (CVD) techniques to improve properties such as hardness, wear resistance, or optical characteristics
Metal finishing is used across many industries including automotive, aerospace, medical devices, architecture, jewelry, and more. Highly engineered parts often require tailored metal finishes to achieve durability, aesthetics, performance, and longevity. The wide range of metal finishing processes allows the physical, chemical, and visual properties of metal components and products to be precisely controlled.
Electroplating
Electroplating is a process that uses electrical current to coat a conductive surface with a thin layer of metal. The part to be plated is immersed in a solution containing metal salts and acts as the cathode (negative electrode). When electrical current is applied, metal ions in the solution are reduced at the surface of the part, forming a thin metal coating.
Some common types of electroplating include:
- Chrome plating – Provides a bright, shiny decorative finish as well as abrasion and corrosion resistance. Used on automotive trim, hardware, appliances.
- Nickel plating – Offers wear resistance along with corrosion protection. Used on machinery parts, hand tools, kitchen utensils.
- Copper plating – Provides electrical conductivity and lubricity. Used in electrical contacts and bearings.
- Silver plating – Has higher electrical conductivity than copper. Used in electrical contacts and conductors.
- Gold plating – Decorative finish and enhanced electrical conductivity. Used in jewelry, electronics, dental implants.
Benefits of electroplating include:
- Improved corrosion and wear resistance
- Enhanced conductivity
- Decorative appeal
- Restoration of dimensions on worn parts
- Ability to plate non-metallic surfaces like plastics
- Cost-effective and efficient method to coat large quantities of small parts
The process allows the properties of the plating metal to be imparted to the surface of the base material, expanding the potential applications of the substrate.
Anodizing
Anodizing is an electrolytic passivation process used to increase the thickness of the natural oxide layer on the surface of metal parts. The process is called anodizing because the part to be treated forms the anode electrode of an electrical circuit. Aluminum is the most widely anodized metal.
There are three main types of anodizing for aluminum:
- Chromic acid anodizing – Produces a thin, clear, yellowish coating that is durable, corrosion resistant, and electrically non-conductive.
- Sulfuric acid anodizing – The most common anodizing process. Produces a thicker coating that is a porous aluminum oxide integrated with the surface, instead of a deposit on the surface. The coating color ranges from light gray to black, depending on specific process. Provides corrosion resistance while maintaining electrical and thermal conductivity.
- Hard anodizing – Produces a very hard, abrasion-resistant coating. Achieved with baths at lower temperatures and higher current densities compared to sulfuric acid anodizing. The coating is nonconductive and ranges from gray to black in color. Commonly used in applications like hydraulic pistons and machine parts due to its hardened wear-resistant surface.
Key benefits of anodizing aluminum include:
- Excellent corrosion resistance and wear resistance
- Harder surface layer while retaining base material properties
- Ability to retain precise dimensions across surface
- Provides electrical insulation
- A wide range of application-specific coloring effects
Anodizing increases durability, longevity, and electrical insulation properties compared to bare aluminum. It is a common finishing process for critical aluminum components and parts across many industries.
Galvanizing
Galvanizing is a process that involves applying a protective zinc coating to steel or iron surfaces to prevent corrosion. The zinc layer acts as a barrier and sacrificial anode, protecting the underlying metal from rust and extending its lifespan.
There are several types of galvanizing, such as:
- Hot-dip galvanizing – The most common method, where steel parts are submerged in a bath of molten zinc.
- Electrogalvanizing – A process that uses electric current to deposit a thin layer of zinc onto the steel surface.
- Sherardizing – A diffusion process where steel parts are heated in a closed container with zinc dust, creating a zinc-iron alloy coating.
Benefits of galvanizing include:
- Long-lasting corrosion protection, even in harsh environments
- Durable, abrasion-resistant coating that does not chip, peel, or flake off
- Cost-effective method for protecting large steel structures
- Low maintenance requirements, as the zinc coating slowly corrodes over time, protecting the steel beneath
- Versatility in application, suitable for a wide range of steel products and components
Galvanizing is a proven and efficient method for protecting steel and iron from corrosion, making it an essential process in various industries, from construction to manufacturing.
Painting
Painting is a process that involves applying a protective or decorative layer of paint or other coating material to the surface of metal parts. This layer serves to protect the underlying metal from corrosion, wear, and environmental factors while also providing an attractive finish.
There are several types of painting for metal parts, such as:
- Powder coating – A process where a fine, dry powder is electrostatically charged and sprayed onto the metal surface, then heated to form a smooth, durable coating. It offers excellent corrosion resistance, mechanical properties, and a wide range of colors and finishes.
- Liquid coating – A method that involves applying a liquid paint or resin to the metal surface, which then dries or cures to form a protective layer. Depending on the type of solvent, desired finish, and coating conditions, the coating can be allowed to dry naturally (air drying) or can be baked (heat curing) to speed up the drying process and achieve specific properties.
- Electrophoretic deposition (EPD) – A process that uses an electric field to deposit charged particles from a liquid suspension onto the metal surface, creating a uniform coating. Cathodic electrophoretic deposition, where the metal substrate acts as the cathode, is the most common type of EPD. The coated metal is then rinsed and baked to cure the coating, resulting in a durable, corrosion-resistant finish.
Benefits of painting include:
- Protection against corrosion, scratches, and UV radiation
- Improved aesthetic appearance, with a wide range of color and texture options
- Enhanced durability and longevity of metal parts
- Increased resistance to chemicals, solvents, and other environmental factors
- Customizable properties, such as electrical insulation or conductivity, depending on the coating material used
Painting is a versatile and widely used method for protecting and enhancing the properties of metal parts, finding applications in various industries, from automotive and aerospace to consumer products and construction.
Blasting
Blasting is a surface treatment process that involves propelling abrasive particles at high velocities onto a metal surface using compressed air or centrifugal force. The purpose of blasting is to clean, roughen, or prepare the surface for subsequent coating applications or to achieve a desired finish.
There are several types of blasting used on metal parts, such as:
- Sand blasting – A process that uses sand or silica particles as the abrasive media to remove surface contaminants, rust, or old coatings from metal surfaces.
- Glass bead blasting – A method that employs small glass beads as the abrasive to create a uniform, matte finish on metal surfaces without removing significant amounts of material.
- Shot blasting – A process that uses metal shot (steel or stainless steel) as the abrasive to clean and strengthen metal surfaces through the introduction of compressive stress.
Benefits of blasting include:
- Removal of surface contaminants, rust, and old coatings
- Improved adhesion for subsequent coating applications
- Creation of desired surface finishes, such as matte or textured
- Increased surface hardness and durability through compressive stress (shot blasting)
- Versatility in application, with the ability to process large and small metal parts
Blasting is a crucial surface preparation technique used in various industries, including automotive, aerospace, and construction. It ensures that metal surfaces are clean, uniform, and ready for further processing, ultimately contributing to the improved performance and longevity of the final product.
Grinding and Polishing
Grinding and polishing are surface finishing processes used to remove material from a workpiece to achieve a desired surface finish, texture, or dimension. These processes are commonly employed in various industries, including metalworking, automotive, aerospace, and manufacturing.
There are several types of grinding and polishing, such as:
- Surface grinding – A process that uses a rotating abrasive wheel to remove material from the surface of a workpiece, creating a flat, smooth finish.
- Cylindrical grinding – A method used to grind the external or internal surfaces of cylindrical workpieces, such as shafts, bores, and bushings.
- Centerless grinding – A process that involves grinding the external surface of a workpiece without the need for a spindle or work holding device, making it suitable for high-volume production.
- Polishing – A finishing process that uses abrasive materials, such as diamond paste, aluminum oxide, or silicon carbide, to create a smooth, reflective surface finish. Mirror finishing is a type of polishing treatment that results in a highly reflective, mirror-like surface.
- Buffing – A finishing process that uses a soft wheel or belt with a fine abrasive compound to achieve a smooth, glossy surface finish. Buffing is often performed after polishing to remove any remaining fine scratches and enhance the overall appearance of the workpiece. This process is commonly used on metals, plastics, and other materials to create a high-luster finish.
Benefits of grinding and polishing include:
- Improved surface finish and aesthetic appearance
- Enhanced dimensional accuracy and precision
- Increased surface hardness and wear resistance
- Removal of surface defects, such as scratches, burrs, or tool marks
- Preparation of surfaces for subsequent coating or plating processes
Grinding and polishing are essential processes in the manufacturing industry, allowing for the production of high-quality, precision components with superior surface finishes and mechanical properties.
Pickling and Etching
Pickling and etching are chemical surface treatments used to remove contaminants, scale, rust, or unwanted layers from metal surfaces. These processes are essential for preparing metal parts for subsequent finishing processes, such as plating, coating, or painting.
There are two main types of pickling and etching:
- Pickling – A process that involves immersing metal parts in an acidic solution to remove surface impurities, such as rust, scale, or oxide layers. Common pickling solutions include hydrochloric acid, sulfuric acid, and nitric acid, depending on the metal being treated.
- Etching – A process that uses chemical solutions or acids to selectively remove material from the surface of a metal part, creating specific patterns, textures, or designs. Etching can also be used to reveal the microstructure of a metal for quality control or metallurgical analysis purposes.
Benefits of pickling and etching include:
- Removal of surface contaminants, rust, and scale
- Improved adhesion for subsequent coating or plating processes
- Creation of specific surface textures or patterns through etching
- Enhanced corrosion resistance by removing surface impurities
- Preparation of metal surfaces for further processing or finishing
Pickling and etching are crucial processes in the metal finishing industry, ensuring that metal surfaces are clean, uniform, and ready for subsequent treatments. These processes are widely used in various sectors, including automotive, aerospace, and manufacturing, to improve the quality and performance of metal components.
Thermal Spray Coating
Thermal spray coating is a process in which melted (or heated) materials are sprayed onto a surface to provide a protective coating. Some common thermal spray methods include:
- Flame spraying – Materials are melted with an oxy-fuel gas flame and sprayed onto the surface. This is one of the most economical thermal spray methods.
- Electric arc spraying – Materials are heated to a molten or semi-molten state with an electric arc and sprayed. This allows for higher spray velocities than flame spraying.
- Plasma spraying – Materials are turned into a plasma state with an electric arc and high temperature argon-hydrogen gas jets. This provides extremely high temperatures to melt difficult materials.
- High Velocity Oxygen Fuel (HVOF) – Similar to flame spraying but with higher particle velocities. Provides very dense, high-quality coatings.
Thermal sprays are commonly used to provide wear and corrosion resistance, or sometimes for aesthetic purposes. The high-temperature spraying process allows materials with very high melting points such as ceramics to be applied as coatings.
Compared to other coating methods, thermal spraying is advantageous because it provides very high bond strength, thick coatings, and versatility in applicable materials.
However, the surface finish is not as smooth as electroplated or anodized finishes. Also, capital equipment costs tend to be higher compared to some other coating methods.
Thin-Film Coating
Thin-film coating is a process that involves depositing a thin layer of material, typically in the range of nanometers to microns, onto the surface of a substrate. Two common methods for thin-film coating are Physical Vapor Deposition (PVD) and Chemical Vapor Deposition (CVD). These techniques are used to improve the properties and performance of various components and products.
The main types of thin-film coating include:
- Physical Vapor Deposition (PVD) – A process where a solid material is vaporized and then condensed onto the substrate surface in a vacuum chamber. Common PVD methods include sputtering, evaporation, and cathodic arc deposition.
- Chemical Vapor Deposition (CVD) – A process that involves the deposition of a thin film from a vapor phase onto a heated substrate surface. The coating material is formed by chemical reactions of gaseous precursors in the reactor.
- Atomic Layer Deposition (ALD) – A subtype of CVD that deposits thin films one atomic layer at a time, allowing for precise control over the coating thickness and composition.
Benefits of thin-film coating include:
- Improved hardness, wear resistance, and corrosion resistance
- Enhanced optical, electrical, and magnetic properties
- Reduced friction and improved lubricity
- Ability to deposit a wide range of materials, including metals, ceramics, and polymers
- Precise control over coating thickness, composition, and uniformity
Thin-film coating techniques like PVD and CVD are essential in various high-tech industries, such as semiconductor manufacturing, aerospace, automotive, and biomedical engineering, where they are used to create advanced materials and devices with superior properties and performance.
Environmental Considerations
The metal finishing industry must operate in an environmentally responsible manner by properly treating wastewater, following regulations, and implementing sustainable practices.
- Wastewater treatment is critical for metal finishing facilities as the wastewater contains heavy metals, acids, solvents, and other contaminants. Facilities must have proper pretreatment systems to remove pollutants before discharging water.
- Regulations govern air emissions, wastewater discharges, and hazardous waste disposal in metal finishing. Facilities must obtain required permits, test effluents, and install pollution controls to comply with regulations.
- The industry is developing more sustainable practices, such as using less hazardous materials, recycling chemicals, reducing energy and water use, and recovering metals for reuse.
Adopting safer chemicals, recycling, advanced wastewater treatment, and pollution prevention strategies promotes greener metal finishing, allowing the industry to protect the environment while meeting regulatory obligations and public expectations.
Ready to see CADDi Drawer in action? Get a personalized demo.
Subscribe to our Blog!
Related Resources
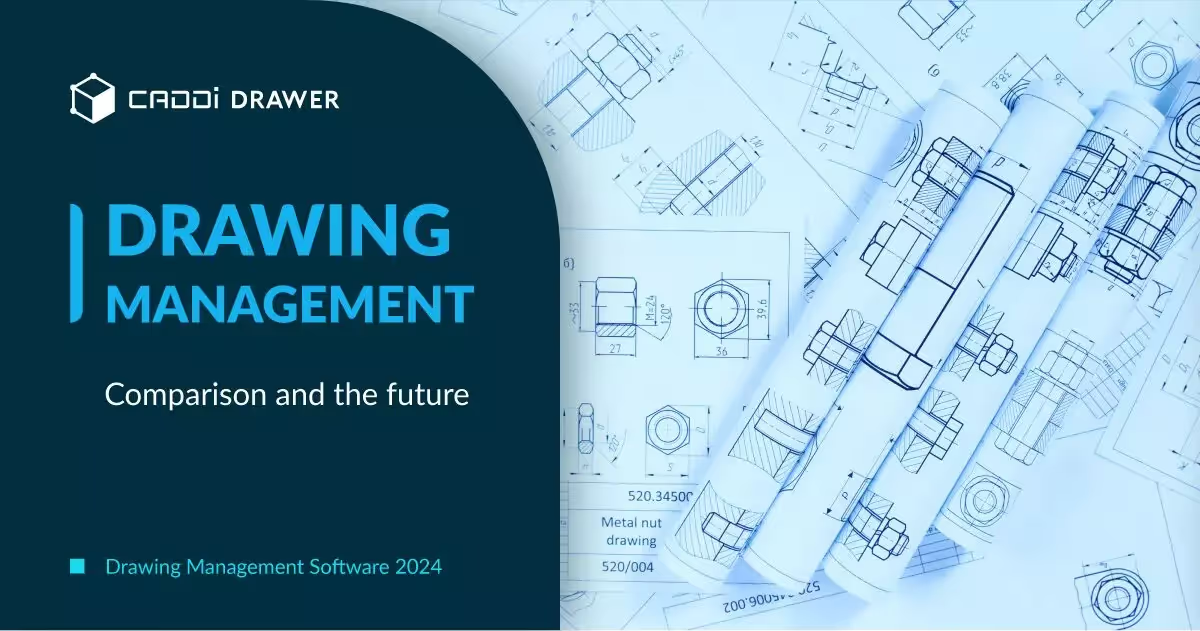
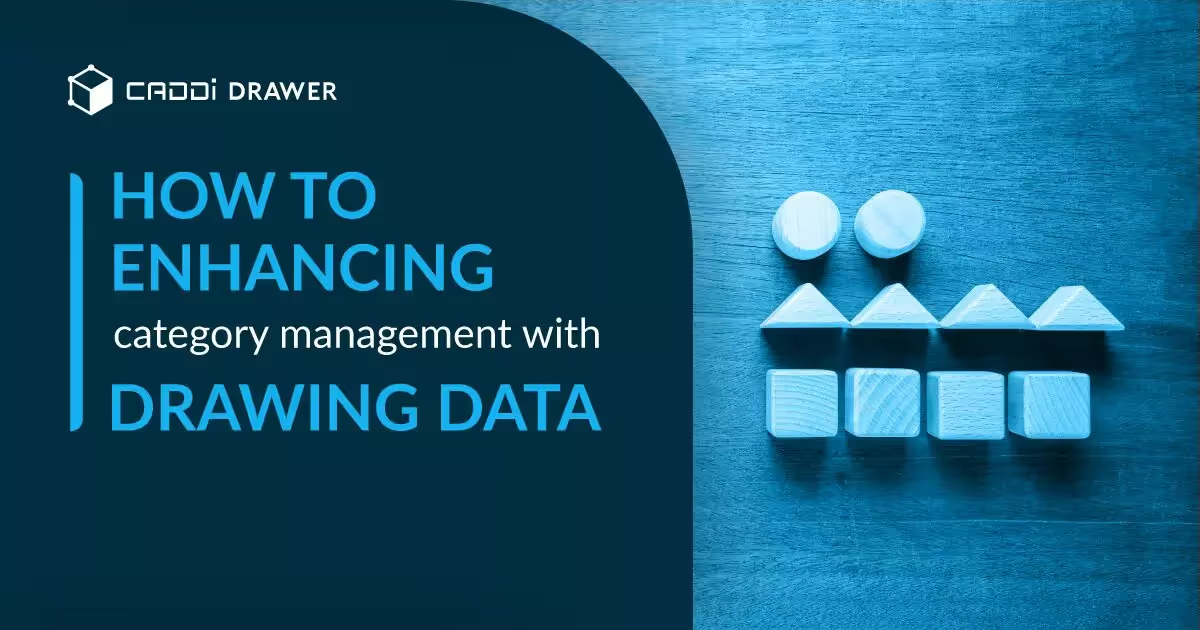
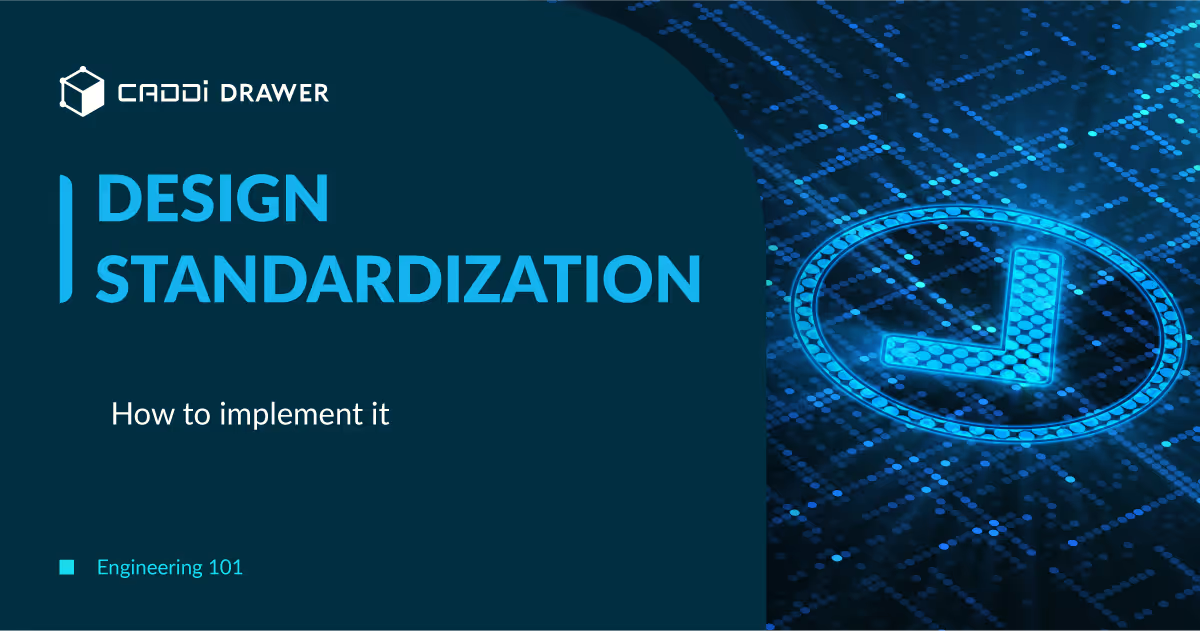
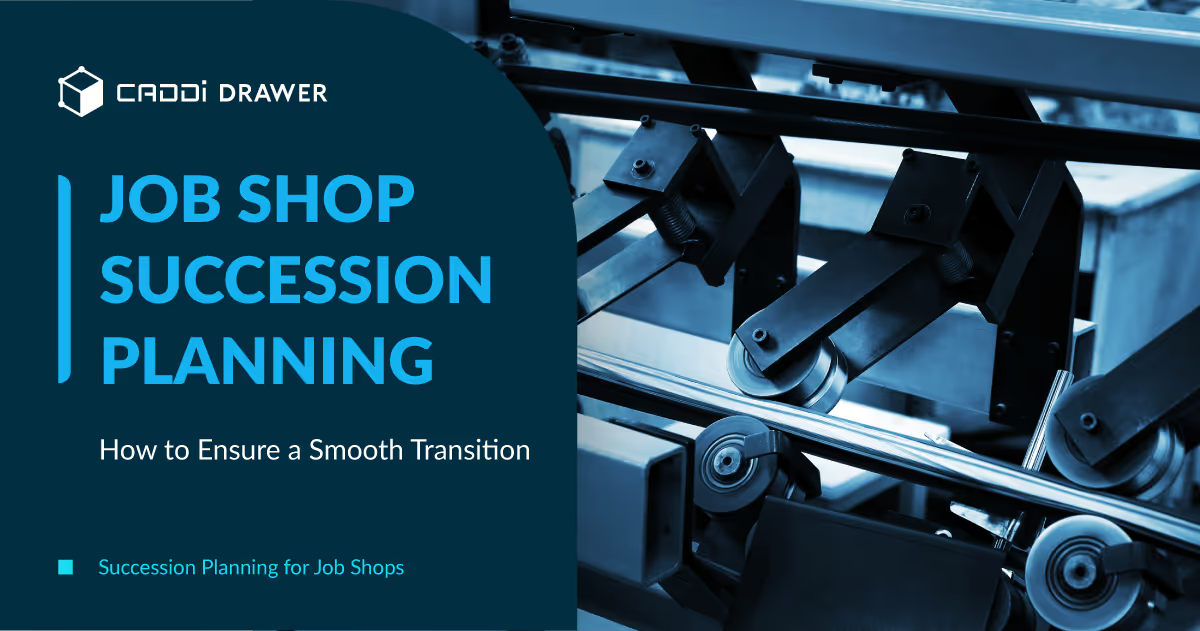
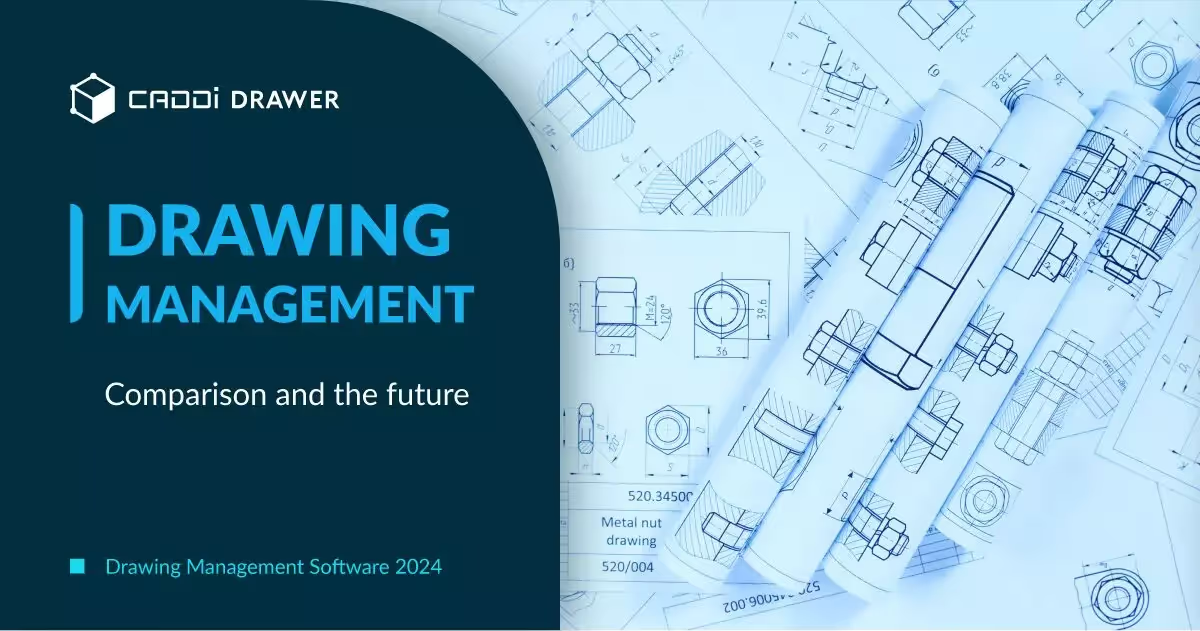
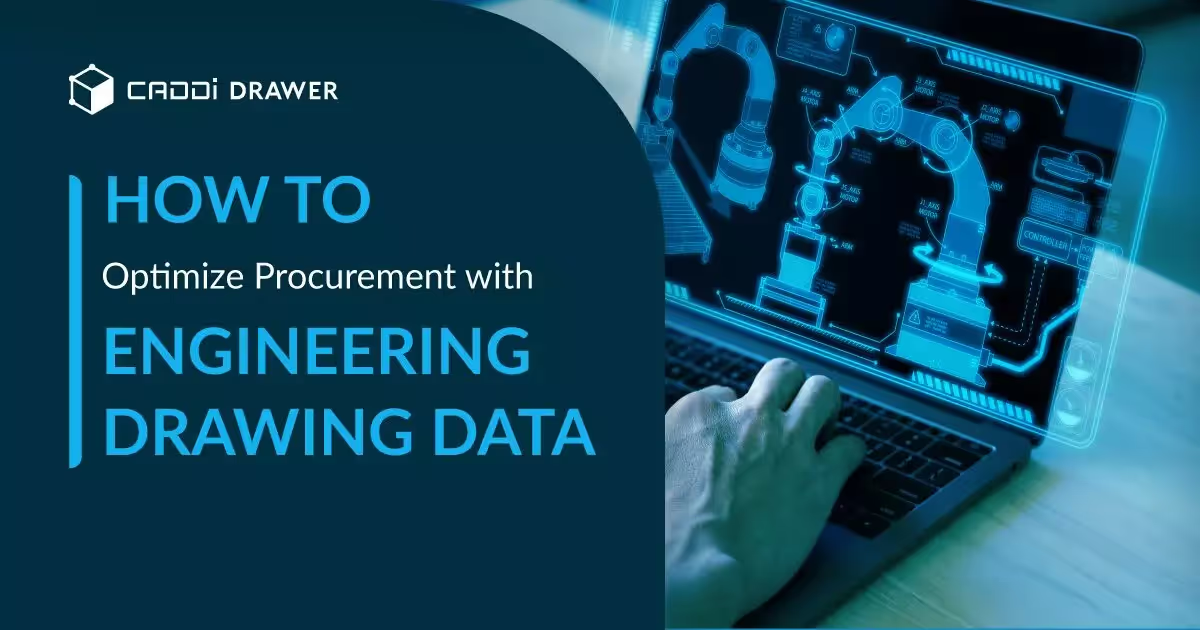