Engineering 101: Design Standardization – How to Implement It
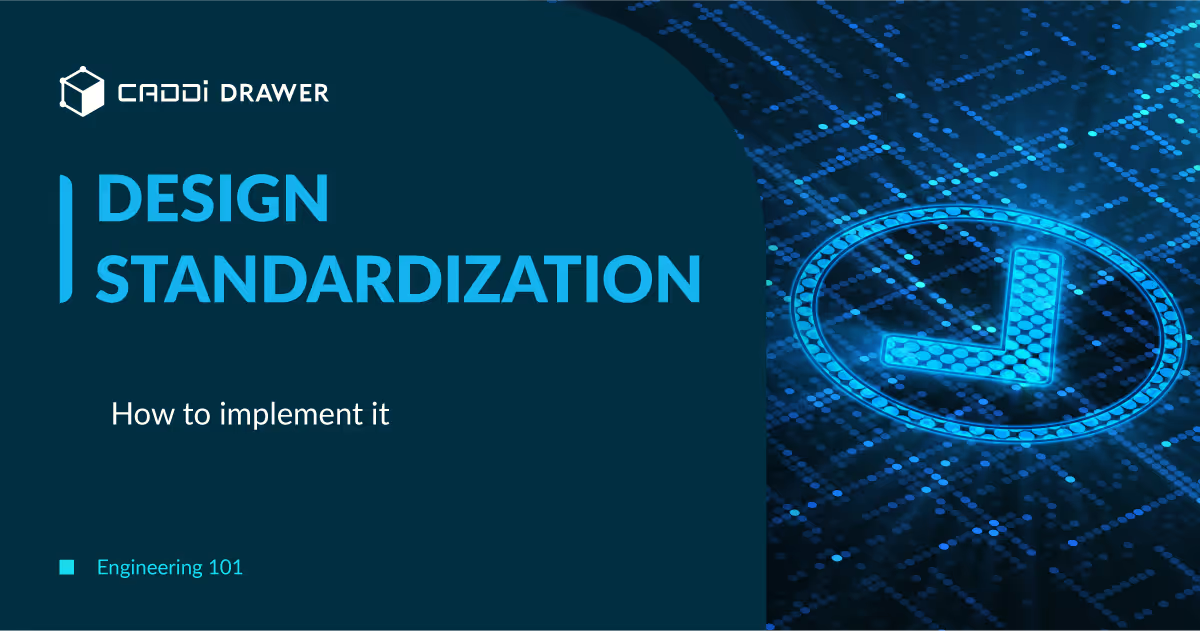
Table of Contents
What is Design Standardization?
Design standardization refers to establishing consistent specifications, procedures, dimensions, materials, and processes that will be used for manufacturing a company’s products. This is an important practice for manufacturing companies for several reasons:
- Improving quality control by reducing errors and defects. When all designs follow the same set of standards, there is less room for mistakes or inconsistencies during production.
- Increasing manufacturing efficiency and productivity. Standardized designs allow manufacturing equipment, tools, and processes to be optimized. Workers also gain familiarity with common standards, working faster and with fewer errors.
- Simplifying logistics and inventory management. Fewer variations in parts and materials are needed with standardized designs. This reduces purchasing costs and inventory requirements.
- Enabling ease of maintenance and servicing. Standardized components are interchangeable between products, making repairs and maintenance faster and more cost effective.
- Enhancing customer satisfaction and company reputation. Consistent product quality and reliable performance result from standardized manufacturing, improving customer opinions of the company and its brands.
Standardization provides significant benefits for companies involved in manufacturing, assembly, and production across a wide range of industries. Implementing design standardization should be a high priority for any company looking to maximize quality, efficiency, and profitability in its operations.
Goals of Design Standardization
- Consistency and interchangeability – Standardizing components and processes allows parts to be interchangeable across products or manufacturing lines. This simplifies production, maintenance, and repair when the same fasteners, connectors, or processes are used.
- Simplified production – With standardized components, tools, documentation, and training, workers can move between stations and lines more easily. Standard workflows and protocols also simplify setup, operation, and monitoring.
- Cost reduction – By reducing unique parts and materials, companies can benefit from economies of scale in procurement. Bulk purchasing of standardized consumables, materials, and components reduces per unit costs.
- Improved quality – Standardization drives process consistency, which improves quality control. Defects are also reduced. Components produced to tighter specifications have less variability.
Areas to Standardize
When implementing design standardization in manufacturing, there are several key areas to focus on:
Parts/Components
- Standardize commonly used parts and components as much as possible. This includes fasteners, motors, gears, seals, bearings, and any other parts used repeatedly across products. Develop a library of approved, standardized components.
- Reduce part numbers by consolidating duplicate and similar parts. Standardize dimensions, materials, coatings, etc.
- Limit custom or proprietary parts only to where absolutely required by the design.
Drawings/Documentation
- Standardize formats and templates for drawings, models, specifications, etc. This improves clarity and makes documentation easier to understand.
- Standard symbol libraries, data presentation, drawing structure, title blocks, etc. should be consistent.
- Store documentation in a central location where the latest versions can be accessed.
Processes
- Identify processes that are common across products, such as machining, welding, painting, assembly steps, testing, etc.
- Standardize these processes as much as possible, including equipment, setup, instructions, quality checks, etc.
- Document processes clearly using standard work instructions, SOPs, or visual job aids.
Tools and Fixtures
- Standardize tooling, jigs, fixtures, and workholding devices.
- Develop modular, adjustable designs that can serve multiple products vs. custom one-off tools.
- Create standard tooling databases, management systems, storage locations, etc.
Materials and Purchased Items
- Standardize on approved supplier lists, grades/types of raw materials, and specifications for purchased items.
- Consolidate to the smallest number of options possible while still meeting design requirements.
- Leverage purchasing power through preferred suppliers, blanket orders, or inventory management agreements.
Challenges in Design Standardization
Implementing design standardization in manufacturing companies can be challenging. Here are some of the main difficulties:
- High initial investment – Creating standards requires upfront effort and cost. Companies need to allocate resources to analyze current designs, determine optimal standards, and document them. This investment may delay revenues.
- Resistance to change – Employees used to custom one-off designs may resist adhering to standards that restrict flexibility. Overcoming cultural inertia requires education on the long-term benefits.
- Difficulty achieving consensus – With diverse product lines and departments, companies can struggle to align on standardized designs. Compromises may be required to get all stakeholders on board.
Implementation Process of Design Standardization
To successfully implement design standards, companies need to follow a systematic approach:
- Form a cross-functional team – Include representatives from engineering, manufacturing, quality, procurement, and any other relevant departments. They will provide diverse perspectives and ensure buy-in.
- Analyze current designs – Thoroughly evaluate existing products and components. Identify differences and inconsistencies. Assess costs, performance, manufacturability etc. This analysis will highlight areas to standardize.
- Identify standardization opportunities – Based on the analysis, determine specific parts and processes to standardize. Prioritize high-impact areas that will maximize benefits. Focus first on interchangeable components.
- Create standards documentation – Develop clear guidelines, drawings, specifications, and procedures. Standardize nomenclature, materials, dimensions, finishes, performance criteria etc.
- Get stakeholder buy-in – Review standards with affected groups. Address concerns through education on benefits. Gain approval before moving to implementation.
- Develop implementation plan – Define specific rollout steps. Set schedules, budgets, responsibilities etc. Allow sufficient time for design, documentation, inventory management, and training.
- Provide training – Educate teams on new standards and processes. Ensure they have the knowledge to apply standards consistently. Emphasize importance of adherence.
Following this structured approach will lead to successful adoption and sustainment of design standards. The upfront effort pays significant dividends through improved quality, reduced costs, faster production, and more.
Documentation
Standardization efforts must be thoroughly documented. Key documentation includes:
- Engineering drawings – Dimensional drawings fully specifying parts, assemblies, and equipment. Standardized templates, fonts, dimensioning styles, and file formats should be used.
- Specifications – Detailed specifications for materials, processes, coatings, performance parameters, and all other requirements. Standard nomenclature and formatting makes specifications consistent.
- Part lists or BOM – Standard part naming conventions and cataloging systems should document all standard, approved parts. Unique part numbers identify each standard component.
- Process documentation – Work instructions, visual worksheets, setup sheets, and control plans codify standardized production and assembly processes. They ensure consistency across shifts and personnel.
Documentation removes tribal knowledge and provides clear, standardized references for manufacturing personnel. Keeping documentation updated and linked to physical standards like gauges and fixtures maintains consistency over time.
Training
Implementing design standards requires proper training for all stakeholders. This ensures everyone understands and adopts the new standards.
- Conduct training sessions to educate engineering, manufacturing, quality, and procurement teams on the new standards. Explain the rationale and benefits.
- Address any resistance to change through open discussions. Emphasize how standardization improves quality, reduces costs, and makes processes more efficient.
- Highlight specific benefits for each stakeholder group. For example, show engineering how design standards simplify and streamline their work. Demonstrate how standards allow manufacturing to be more consistent and optimize operations.
- Use a mix of classroom and hands-on training to reinforce learning. Have engineers walk through creating drawings and designs using the new standards. Give manufacturing teams opportunities to practice setups and processes per the standards.
- Make training mandatory for all relevant employees to ensure complete adoption. Require passing an assessment to verify understanding of the new standards.
- Document the training material and keep records of completed training sessions and assessments. This ensures standardization knowledge is retained within the organization.
Proper training and education are critical to drive the cultural and operational changes needed to successfully implement design standards. Focusing on the benefits can help address resistance to change.
Verification
Once standards are implemented, it’s crucial to verify that they are being followed correctly. This involves several key steps:
- Conduct audits of the manufacturing process, equipment setups, quality inspections, etc. to ensure compliance with the standards. Auditors should check that operators are following standardized work instructions and that equipment/tooling meets specifications.
- Analyze data gathered from the audits and daily operations. Track metrics related to quality, cost, cycle times, and more. Identify areas that need improvement based on deviations from the standards.
- Update standards as needed. Standards are living documents, not set in stone. As issues arise or improvements are identified, standards should be updated to reflect best practices. A systematic process for submitting and approving updates is important.
- Provide feedback loops. Share results of audits and data analysis with production teams. Celebrate successes following standards and discuss opportunities when standards are not met. This facilitates continuous improvement.
- Ongoing training. As standards evolve, ensure employees are kept up to date through refresher training on new or modified standards. This helps standards become second nature.
By verifying standards are followed and continuously improving them, companies can maximize the benefits of standardization including quality, efficiency, and cost reduction. It takes discipline, but pays major dividends.
Maintenance
Implementing design standards is not a one-time initiative. Companies must establish processes for periodically reviewing standards, making updates and revisions, and continual improvement.
- Periodic reviews – Standards should be reviewed on a regular basis (e.g. annually) to evaluate their effectiveness and identify areas for improvement. Key metrics to analyze include manufacturing efficiency, quality, cost, lead time, etc.
- Managing updates – When issues are identified or new technologies/processes emerge, standards will need to be updated. Updates should balance enforcing standardization with allowing flexibility. A structured process for submitting, reviewing, and approving updates should be followed.
- Continual improvement – In addition to updates, there should be a philosophy of continual incremental improvement to standards over time. Lean tools like Kaizen can be applied to regularly enhance standards. Employees who work directly with the standards should be engaged in giving feedback for improvement.
By treating standards as dynamic rather than static documentation, companies can ensure they are maximizing the benefits of design standardization.
How CADDi Drawer Supports Design Standardization
CADDi Drawer is a powerful tool that can significantly streamline and enhance design standardization efforts in manufacturing companies. Key features and benefits include:
- Powerful Search and Retrieval – CADDi Drawer’s search capabilities make it fast and easy to find relevant standardized designs. Users can smoothly identify similar drawings to your target design of standardization and search by keyword, attribute, part number, and more. This saves significant time versus manual searching and ensures the right standard is always used.

- Customizable Attributes and Meta-Data – Standard parts and designs can be tagged with extensive meta-data and custom attributes in CADDi Drawer. This allows for sophisticated categorization and filtering of standardized content. Attributes can identify preferred parts, flag obsolete designs, and link to supporting documentation and specs.
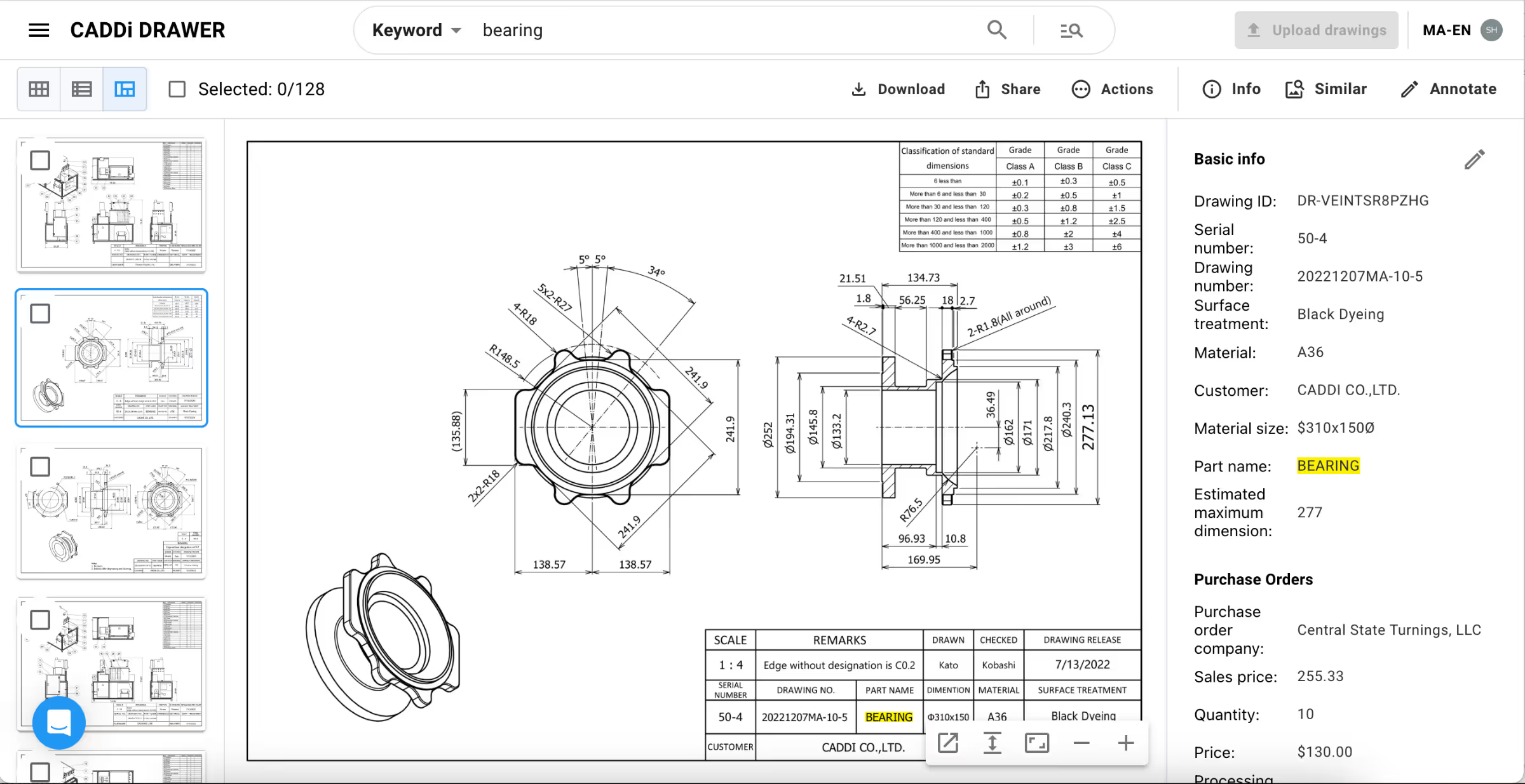
What is Design Standardization?
Design standardization refers to establishing consistent specifications, procedures, dimensions, materials, and processes that will be used for manufacturing a company’s products. This is an important practice for manufacturing companies for several reasons:
- Improving quality control by reducing errors and defects. When all designs follow the same set of standards, there is less room for mistakes or inconsistencies during production.
- Increasing manufacturing efficiency and productivity. Standardized designs allow manufacturing equipment, tools, and processes to be optimized. Workers also gain familiarity with common standards, working faster and with fewer errors.
- Simplifying logistics and inventory management. Fewer variations in parts and materials are needed with standardized designs. This reduces purchasing costs and inventory requirements.
- Enabling ease of maintenance and servicing. Standardized components are interchangeable between products, making repairs and maintenance faster and more cost effective.
- Enhancing customer satisfaction and company reputation. Consistent product quality and reliable performance result from standardized manufacturing, improving customer opinions of the company and its brands.
Standardization provides significant benefits for companies involved in manufacturing, assembly, and production across a wide range of industries. Implementing design standardization should be a high priority for any company looking to maximize quality, efficiency, and profitability in its operations.
Goals of Design Standardization
- Consistency and interchangeability – Standardizing components and processes allows parts to be interchangeable across products or manufacturing lines. This simplifies production, maintenance, and repair when the same fasteners, connectors, or processes are used.
- Simplified production – With standardized components, tools, documentation, and training, workers can move between stations and lines more easily. Standard workflows and protocols also simplify setup, operation, and monitoring.
- Cost reduction – By reducing unique parts and materials, companies can benefit from economies of scale in procurement. Bulk purchasing of standardized consumables, materials, and components reduces per unit costs.
- Improved quality – Standardization drives process consistency, which improves quality control. Defects are also reduced. Components produced to tighter specifications have less variability.
Areas to Standardize
When implementing design standardization in manufacturing, there are several key areas to focus on:
Parts/Components
- Standardize commonly used parts and components as much as possible. This includes fasteners, motors, gears, seals, bearings, and any other parts used repeatedly across products. Develop a library of approved, standardized components.
- Reduce part numbers by consolidating duplicate and similar parts. Standardize dimensions, materials, coatings, etc.
- Limit custom or proprietary parts only to where absolutely required by the design.
Drawings/Documentation
- Standardize formats and templates for drawings, models, specifications, etc. This improves clarity and makes documentation easier to understand.
- Standard symbol libraries, data presentation, drawing structure, title blocks, etc. should be consistent.
- Store documentation in a central location where the latest versions can be accessed.
Processes
- Identify processes that are common across products, such as machining, welding, painting, assembly steps, testing, etc.
- Standardize these processes as much as possible, including equipment, setup, instructions, quality checks, etc.
- Document processes clearly using standard work instructions, SOPs, or visual job aids.
Tools and Fixtures
- Standardize tooling, jigs, fixtures, and workholding devices.
- Develop modular, adjustable designs that can serve multiple products vs. custom one-off tools.
- Create standard tooling databases, management systems, storage locations, etc.
Materials and Purchased Items
- Standardize on approved supplier lists, grades/types of raw materials, and specifications for purchased items.
- Consolidate to the smallest number of options possible while still meeting design requirements.
- Leverage purchasing power through preferred suppliers, blanket orders, or inventory management agreements.
Challenges in Design Standardization
Implementing design standardization in manufacturing companies can be challenging. Here are some of the main difficulties:
- High initial investment – Creating standards requires upfront effort and cost. Companies need to allocate resources to analyze current designs, determine optimal standards, and document them. This investment may delay revenues.
- Resistance to change – Employees used to custom one-off designs may resist adhering to standards that restrict flexibility. Overcoming cultural inertia requires education on the long-term benefits.
- Difficulty achieving consensus – With diverse product lines and departments, companies can struggle to align on standardized designs. Compromises may be required to get all stakeholders on board.
Implementation Process of Design Standardization
To successfully implement design standards, companies need to follow a systematic approach:
- Form a cross-functional team – Include representatives from engineering, manufacturing, quality, procurement, and any other relevant departments. They will provide diverse perspectives and ensure buy-in.
- Analyze current designs – Thoroughly evaluate existing products and components. Identify differences and inconsistencies. Assess costs, performance, manufacturability etc. This analysis will highlight areas to standardize.
- Identify standardization opportunities – Based on the analysis, determine specific parts and processes to standardize. Prioritize high-impact areas that will maximize benefits. Focus first on interchangeable components.
- Create standards documentation – Develop clear guidelines, drawings, specifications, and procedures. Standardize nomenclature, materials, dimensions, finishes, performance criteria etc.
- Get stakeholder buy-in – Review standards with affected groups. Address concerns through education on benefits. Gain approval before moving to implementation.
- Develop implementation plan – Define specific rollout steps. Set schedules, budgets, responsibilities etc. Allow sufficient time for design, documentation, inventory management, and training.
- Provide training – Educate teams on new standards and processes. Ensure they have the knowledge to apply standards consistently. Emphasize importance of adherence.
Following this structured approach will lead to successful adoption and sustainment of design standards. The upfront effort pays significant dividends through improved quality, reduced costs, faster production, and more.
Documentation
Standardization efforts must be thoroughly documented. Key documentation includes:
- Engineering drawings – Dimensional drawings fully specifying parts, assemblies, and equipment. Standardized templates, fonts, dimensioning styles, and file formats should be used.
- Specifications – Detailed specifications for materials, processes, coatings, performance parameters, and all other requirements. Standard nomenclature and formatting makes specifications consistent.
- Part lists or BOM – Standard part naming conventions and cataloging systems should document all standard, approved parts. Unique part numbers identify each standard component.
- Process documentation – Work instructions, visual worksheets, setup sheets, and control plans codify standardized production and assembly processes. They ensure consistency across shifts and personnel.
Documentation removes tribal knowledge and provides clear, standardized references for manufacturing personnel. Keeping documentation updated and linked to physical standards like gauges and fixtures maintains consistency over time.
Training
Implementing design standards requires proper training for all stakeholders. This ensures everyone understands and adopts the new standards.
- Conduct training sessions to educate engineering, manufacturing, quality, and procurement teams on the new standards. Explain the rationale and benefits.
- Address any resistance to change through open discussions. Emphasize how standardization improves quality, reduces costs, and makes processes more efficient.
- Highlight specific benefits for each stakeholder group. For example, show engineering how design standards simplify and streamline their work. Demonstrate how standards allow manufacturing to be more consistent and optimize operations.
- Use a mix of classroom and hands-on training to reinforce learning. Have engineers walk through creating drawings and designs using the new standards. Give manufacturing teams opportunities to practice setups and processes per the standards.
- Make training mandatory for all relevant employees to ensure complete adoption. Require passing an assessment to verify understanding of the new standards.
- Document the training material and keep records of completed training sessions and assessments. This ensures standardization knowledge is retained within the organization.
Proper training and education are critical to drive the cultural and operational changes needed to successfully implement design standards. Focusing on the benefits can help address resistance to change.
Verification
Once standards are implemented, it’s crucial to verify that they are being followed correctly. This involves several key steps:
- Conduct audits of the manufacturing process, equipment setups, quality inspections, etc. to ensure compliance with the standards. Auditors should check that operators are following standardized work instructions and that equipment/tooling meets specifications.
- Analyze data gathered from the audits and daily operations. Track metrics related to quality, cost, cycle times, and more. Identify areas that need improvement based on deviations from the standards.
- Update standards as needed. Standards are living documents, not set in stone. As issues arise or improvements are identified, standards should be updated to reflect best practices. A systematic process for submitting and approving updates is important.
- Provide feedback loops. Share results of audits and data analysis with production teams. Celebrate successes following standards and discuss opportunities when standards are not met. This facilitates continuous improvement.
- Ongoing training. As standards evolve, ensure employees are kept up to date through refresher training on new or modified standards. This helps standards become second nature.
By verifying standards are followed and continuously improving them, companies can maximize the benefits of standardization including quality, efficiency, and cost reduction. It takes discipline, but pays major dividends.
Maintenance
Implementing design standards is not a one-time initiative. Companies must establish processes for periodically reviewing standards, making updates and revisions, and continual improvement.
- Periodic reviews – Standards should be reviewed on a regular basis (e.g. annually) to evaluate their effectiveness and identify areas for improvement. Key metrics to analyze include manufacturing efficiency, quality, cost, lead time, etc.
- Managing updates – When issues are identified or new technologies/processes emerge, standards will need to be updated. Updates should balance enforcing standardization with allowing flexibility. A structured process for submitting, reviewing, and approving updates should be followed.
- Continual improvement – In addition to updates, there should be a philosophy of continual incremental improvement to standards over time. Lean tools like Kaizen can be applied to regularly enhance standards. Employees who work directly with the standards should be engaged in giving feedback for improvement.
By treating standards as dynamic rather than static documentation, companies can ensure they are maximizing the benefits of design standardization.
How CADDi Drawer Supports Design Standardization
CADDi Drawer is a powerful tool that can significantly streamline and enhance design standardization efforts in manufacturing companies. Key features and benefits include:
- Powerful Search and Retrieval – CADDi Drawer’s search capabilities make it fast and easy to find relevant standardized designs. Users can smoothly identify similar drawings to your target design of standardization and search by keyword, attribute, part number, and more. This saves significant time versus manual searching and ensures the right standard is always used.

- Customizable Attributes and Meta-Data – Standard parts and designs can be tagged with extensive meta-data and custom attributes in CADDi Drawer. This allows for sophisticated categorization and filtering of standardized content. Attributes can identify preferred parts, flag obsolete designs, and link to supporting documentation and specs.
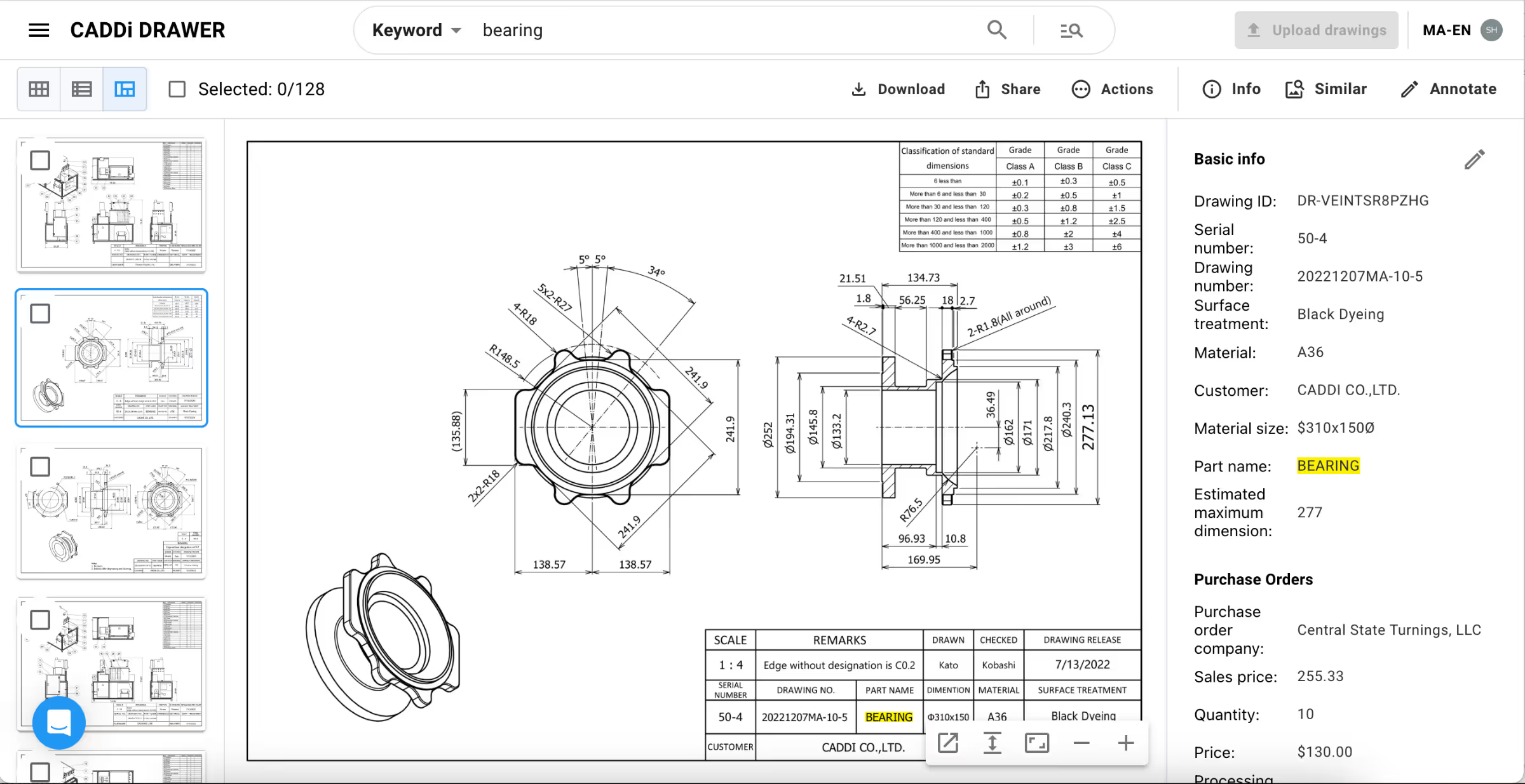
Ready to see CADDi Drawer in action? Get a personalized demo.
Subscribe to our Blog!
Related Resources
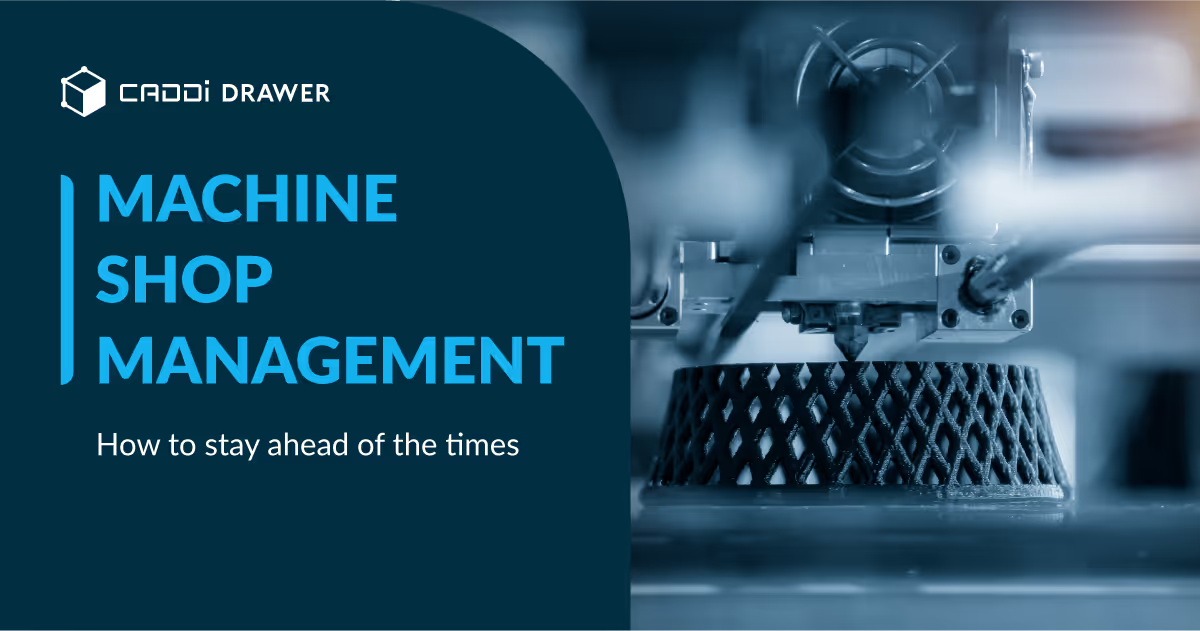
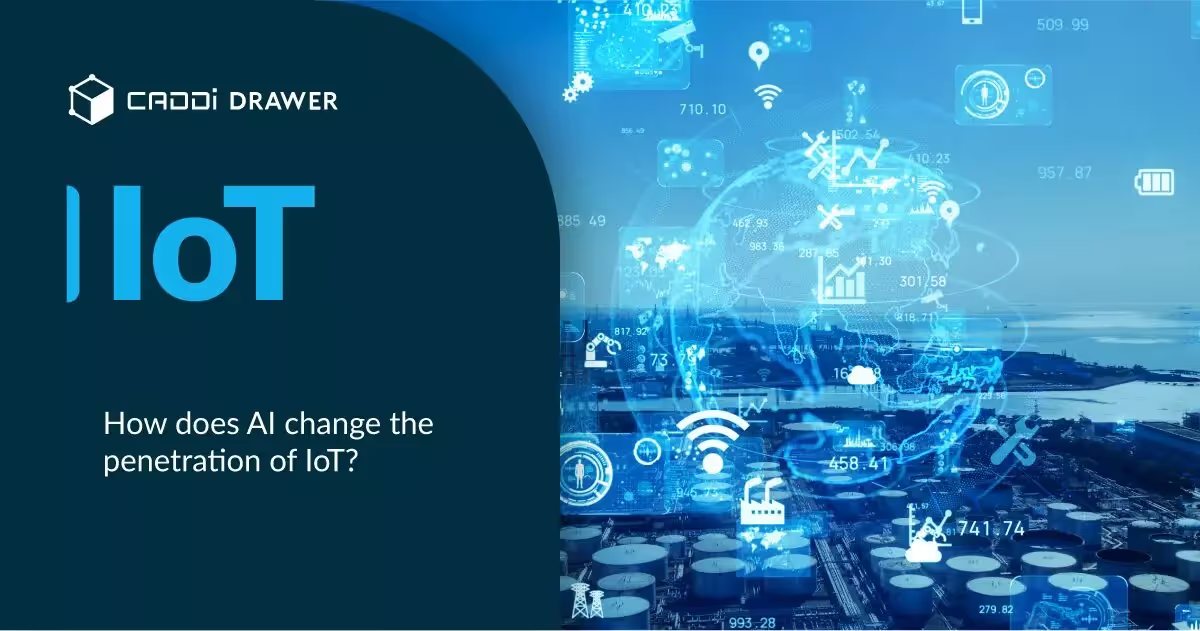
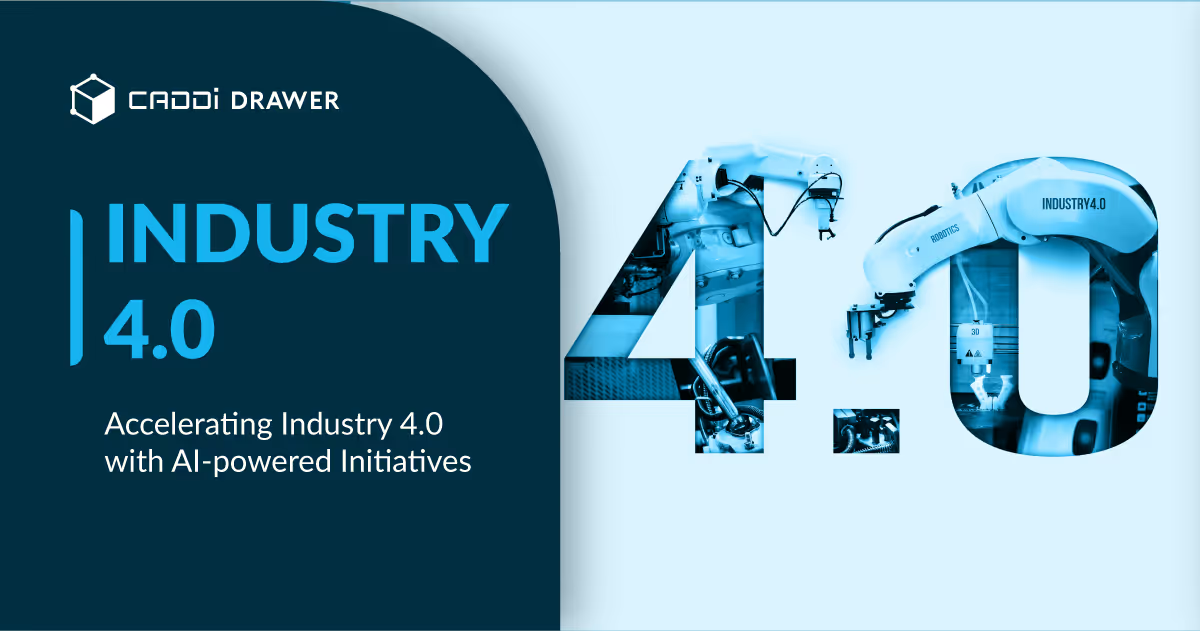
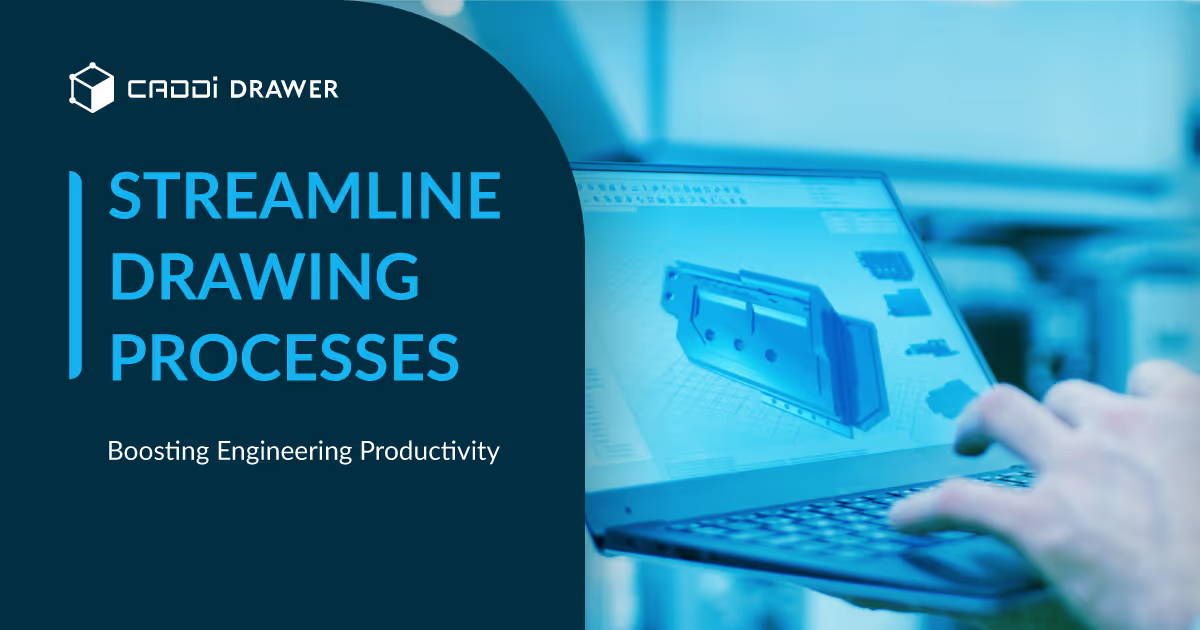
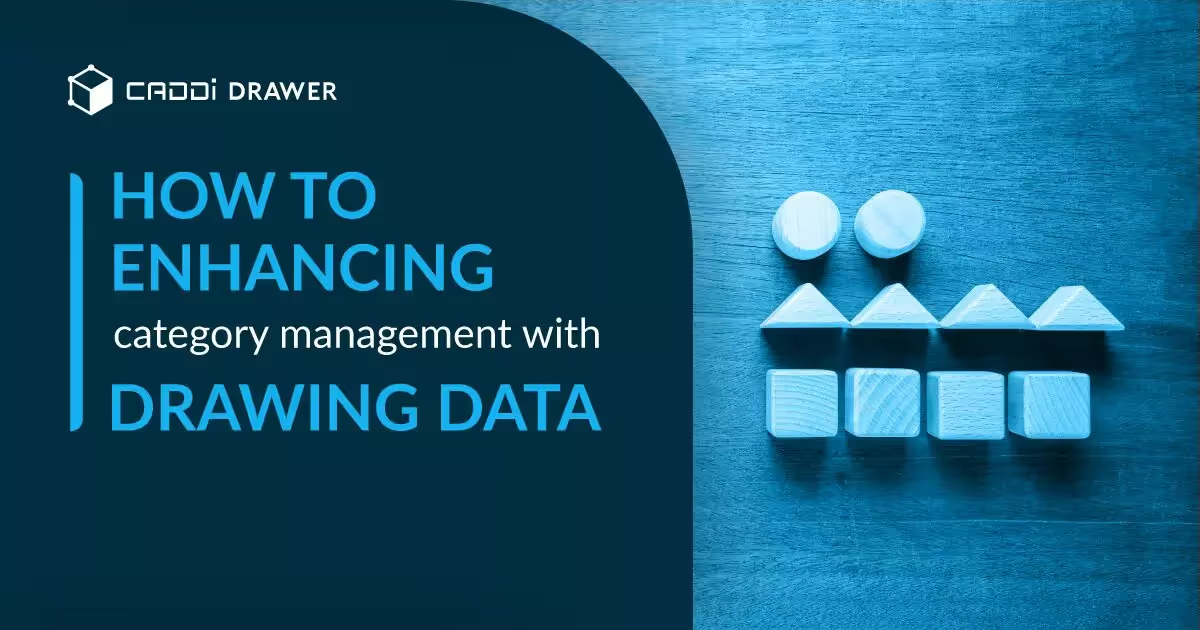
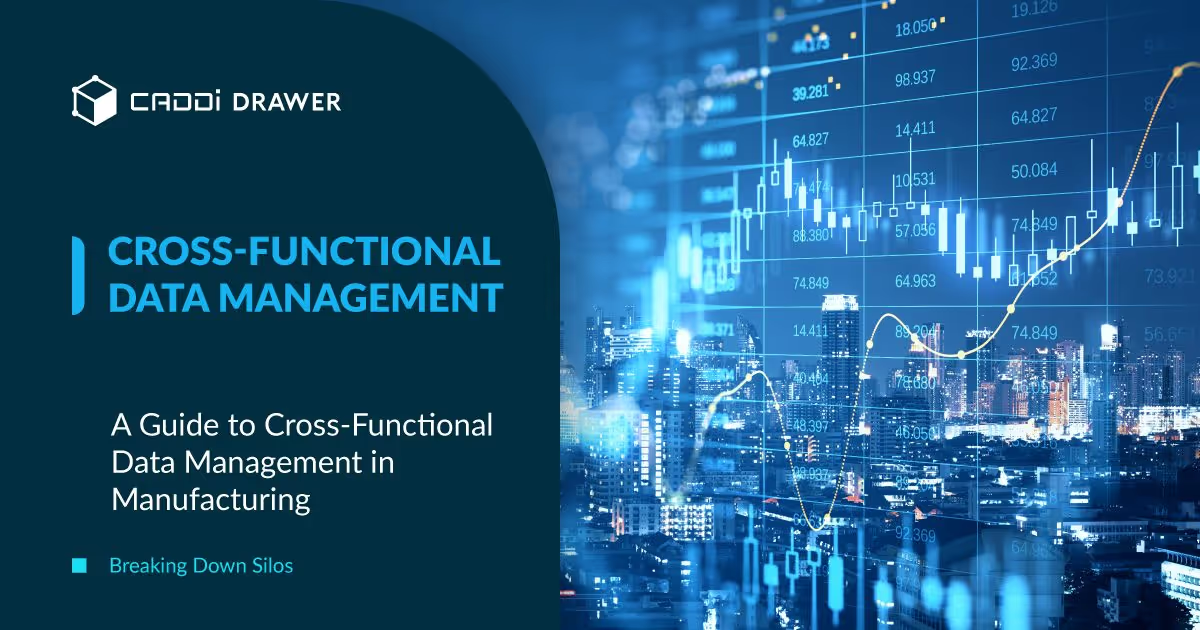