Machine Shop Management: How to stay ahead of the times
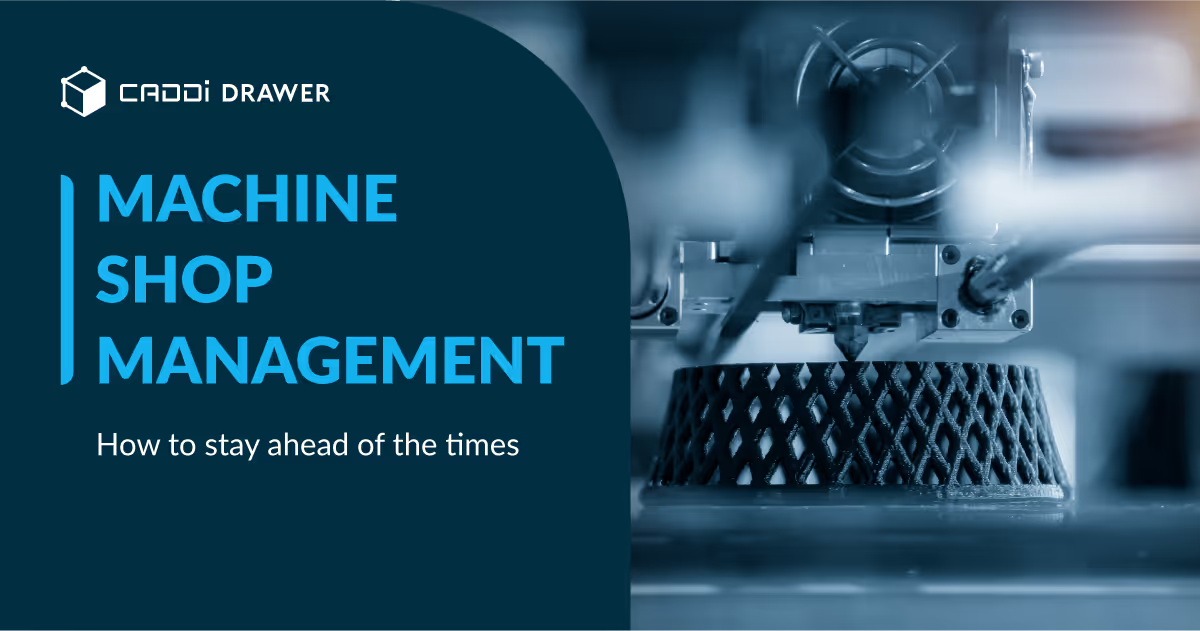
Table of Contents
Introduction
Managing a machine shop in today’s fast-paced manufacturing environment requires the ability to stay ahead of the latest technologies and trends. Shops that don’t adapt quickly risk falling behind competitors who leverage advanced equipment, processes, and business models. However, implementing changes requires careful planning and consideration. This article provides an overview of key strategies machine shop owners and managers can employ to position their businesses for continued success.
Invest in New Equipment
Staying competitive as a machine shop means investing in new equipment on a regular basis. Upgrading to the latest CNC machines, 3D printers, laser cutters and other advanced tools can provide significant benefits:
- Increased Efficiency – Newer machines are faster, more precise, and capable of more complex operations than older equipment. This allows you to take on more complex and profitable jobs.
- Expanded Capabilities – Advanced equipment like 5-axis CNC mills and Swiss-style CNC lathes enable you to manufacture parts that weren’t possible with older technology. This opens up new business opportunities.
- Improved Quality – Precision manufacturing requires precision equipment. The latest machines hold tighter tolerances and produce consistently high quality parts. This helps attract and retain customers.
- Enhanced Reliability – New equipment incorporates the latest innovations, reducing downtime and maintenance issues. This improves productivity and on-time delivery.
- Future-Proofing – Purchasing up-to-date machines ensures your shop stays competitive as manufacturing technologies continue advancing rapidly. It’s an investment in future capabilities.
Regularly budgeting for capital expenditures is key. Machines should be replaced before they become obsolete. Work with quality equipment suppliers that understand your manufacturing needs.
Implement Automation
Adopting automation technologies and processes can provide significant benefits for machine shops. Automating repetitive or dangerous tasks frees up employees for higher-value work while also improving safety. It also enhances consistency and precision, leading to higher quality results.
Investing in CNC machines and integrating automation allows completing jobs faster and more accurately. This increased efficiency can boost shop productivity and capacity without necessarily hiring more staff. The automation handles tasks that previously required manual work, saving on labor costs.
Integrating automated inspection and reporting provides real-time data to easily identify any quality issues or production problems. This prevents wasted time and materials. Automation also minimizes variability and human error in production. Parts have greater uniformity and adherence to specifications when CNC machines perform the work.
Overall, implementing automation intelligently allows machine shops to work smarter. Shops can take on more business and tighten margins while maintaining quality. With the right automation technologies, machine shops position themselves for scalable growth and long-term success. The capital investment pays dividends over time with the labor and efficiency gains.
Adopt Advanced Software
Advances in software technology have opened up many new opportunities for machine shops to improve efficiency and productivity. Adopting the latest CAD, CAM, and ERP software can streamline workflows, reduce errors, and enhance collaboration.
CAD software allows machine shops to create detailed 3D models and technical drawings digitally. The latest CAD programs incorporate automation and parametric modeling to speed up design work. They also integrate seamlessly with CAM software for efficient data transfer. Upgrading to the newest CAD version ensures you can handle the most complex part geometries and rapidly iterate designs.
CAM software uses CAD models to generate toolpaths and G-code to drive CNC machines. New CAM systems incorporate sophisticated algorithms that optimize tool selection, speeds, feeds, and motion planning. This results in more efficient machining, reduced cycle times, and less wear on cutting tools. Advanced simulation and verification tools also minimize waste from potential programming errors.
ERP software centralizes operations and integrates all departments in a machine shop. It provides real-time visibility into inventory, orders, production scheduling, costs, and other metrics. Modern cloud-based ERP platforms enable secure access from anywhere. This allows managers to make data-driven decisions on the fly. ERP systems also facilitate supply chain coordination and make it easier to adapt to changing customer demands.
By implementing the latest CAD, CAM, and ERP software solutions, machine shops can achieve transformative digital workflows. The increased automation, efficiency, and flexibility give shops a competitive advantage in the marketplace.
Leverage Data Analytics
The use of data analytics is becoming increasingly critical for modern machine shops to stay competitive. By collecting and analyzing operational data, shops can gain valuable insights to optimize productivity, efficiency, and quality.
Some ways machine shops can leverage data analytics include:
- Track machine utilization rates to identify bottlenecks and ensure optimal asset usage. Data can show which machines are overburdened and which are underutilized.
- Analyze cycle times for different operations to find ways to streamline workflows. Identifying parts of the process that are taking longer than expected allows you to address inefficiencies.
- Use sensor data from machines to implement predictive maintenance. By monitoring vibration, temperature and other metrics, you can detect issues and schedule maintenance before equipment fails.
- Monitor inventory levels and reorder points to optimize stock. Data can identify fast-moving inventory to avoid stockouts while minimizing tied-up capital.
- Track quality metrics like scrap and rework rates to quickly detect when processes drift out of spec. Analytics enable continuous process improvements.
- Create dashboards with key operational KPIs to provide managers real-time visibility. Quick access to key metrics facilitates faster and better decision making.
- Perform win/loss analysis on sales data to identify trends and improve sales strategies. Analyzing characteristics of won and lost deals can provide insights to refine target customers, adjust offerings, and optimize sales processes.
With the rise of Industrial IoT, more shop data is available than ever before. Leveraging analytics turns this data into powerful insights to help machine shops optimize productivity, boost quality, improve maintenance practices, and reduce costs. Those that embrace data-driven decision making will have a competitive edge.
Focus on Employee Training
Constant training and development of staff skills is crucial for machine shops to keep up with rapidly advancing technologies and manufacturing techniques. Investing in ongoing employee education demonstrates a commitment to supporting workers while ensuring the business has the expertise needed to meet customer demands.
Retraining employees regularly on new equipment, software, and processes empowers them to fully utilize the latest innovations. This boosts productivity, quality control, and safety. Workers who feel confident operating advanced machinery and technologies are more engaged, increasing retention rates.
Consider subsidizing offsite training programs or bringing in qualified instructors. Encourage staff at all levels to participate and make sure learnings are applied immediately afterwards. Tracking certifications helps validate competencies. Multi-skilled cross-training creates flexibility.
Hands-on peer coaching and knowledge sharing reinforces learning. Schedule time for teams to train together and collaborate. Managers should continuously assess gaps and provide feedback. An organizational culture valuing continuous education enables a machine shop to constantly improve.
Offer Additional Services
Expanding beyond basic machining and fabrication into additional offerings can help machine shops stay competitive and meet evolving customer needs. This may involve taking on design work, prototyping, assembly, finishing services, inventory management, shipping and logistics coordination, and more.
Diversifying capabilities allows shops to capture more business from existing customers who may now rely on them for expanded services. It also makes them more attractive to new customers looking for a one-stop provider.
Some ways shops can branch out include:
- Design and Engineering Services – Offering design and engineering support allows shops to get involved earlier in the manufacturing process. This provides more insight into final part requirements.
- Rapid Prototyping – Equipping to produce functional prototypes enables shops to deliver concept validations faster. This speeds up design iterations.
- Sub-Assembly and Finishing – Providing sub-assembly, surface finishing, coatings, heat treatment, and other secondary operations completes parts fully before shipping.
- Testing and Inspection – In-house testing and inspection using CMMs, optical comparators, and other equipment gives customers quality assurance.
- Inventory and Shipping – Managing inventory and coordinating final packaging and shipping reduces hassles for customers.
Diversifying into new offerings requires investment in equipment, people, and processes. But it also strengthens customer relationships, loyalty, and expands business opportunities.
Adapt Business Model
To stay competitive, machine shops must be willing to adapt their business models. Some options to consider include:
- Contract Manufacturing – Become a contract manufacturer that produces parts to customers’ specifications, rather than selling your own proprietary products. This allows you to leverage your machining capabilities for new revenue streams.
- On-Demand Manufacturing – Offer on-demand manufacturing services, where customers can order small batches of custom parts as needed. This caters to prototyping, small startups, and researchers.
- E-Commerce – Develop an e-commerce portal where customers can easily order common parts online. This significantly expands your reach and revenue.
- Diversification – Consider diversifying into other services like 3D printing, engineering consultation, CAD services, etc. This makes your business a one-stop shop.
- Customization – Provide highly customized and personalized parts catered to each customer’s requirements. This provides value that competitors can’t match.
Adapting the business model is critical for machine shops to keep up with market changes. Evaluating different options like contract manufacturing, on-demand services, e-commerce, diversification, and customization can help secure continued growth and profitability. The key is understanding your capabilities and customers’ needs to select the right approach.
How CADDi Drawer Can Help Job Shop Management
CADDi Drawer is a powerful tool designed to support job shop management that leverages AI to analyze and organize technical drawings.
For example, Hilltop, a machine shop, has significantly improved its operational efficiency by integrating CADDi Drawer with its existing systems. For more details, please refer to the article below.
Customer Case – Hilltop: Accelerating Company-Wide Digital Transformation with CADDi Drawer
By identifying similar drawings from past projects, it enables faster quotation creation. Sales teams no longer need to start from scratch or wait for engineers to locate relevant past projects. CADDi quickly determines if a new project is manufacturable in-house or requires outsourcing, allowing for rapid responses to customer inquiries.
Beyond accelerating the quotation process, CADDi Drawer also improves the quotation-to-order ratio. By storing both quotation and order data, it allows shops to compare pricing levels for similar projects. Analyzing won and lost projects side-by-side provides insights to optimize pricing strategies and win more business.
The advanced search capabilities dramatically reduce the time engineers spend searching for information. With the ability to search by keywords, tags, or even images, locating relevant drawings, projects, costs, and other data is easier than ever. Engineers can quickly access the information they need, boosting productivity.
The software also facilitates standardization by identifying similar parts across projects. By comparing drawings for similar assemblies, machine shops can spot opportunities to standardize jigs, streamlining production and reducing costs.
CADDi even supports CAM production by enabling the reuse of CAM data for nearly identical parts. Rather than programming new parts from scratch, machinists can leverage existing CAM data, saving valuable programming time.
Introduction
Managing a machine shop in today’s fast-paced manufacturing environment requires the ability to stay ahead of the latest technologies and trends. Shops that don’t adapt quickly risk falling behind competitors who leverage advanced equipment, processes, and business models. However, implementing changes requires careful planning and consideration. This article provides an overview of key strategies machine shop owners and managers can employ to position their businesses for continued success.
Invest in New Equipment
Staying competitive as a machine shop means investing in new equipment on a regular basis. Upgrading to the latest CNC machines, 3D printers, laser cutters and other advanced tools can provide significant benefits:
- Increased Efficiency – Newer machines are faster, more precise, and capable of more complex operations than older equipment. This allows you to take on more complex and profitable jobs.
- Expanded Capabilities – Advanced equipment like 5-axis CNC mills and Swiss-style CNC lathes enable you to manufacture parts that weren’t possible with older technology. This opens up new business opportunities.
- Improved Quality – Precision manufacturing requires precision equipment. The latest machines hold tighter tolerances and produce consistently high quality parts. This helps attract and retain customers.
- Enhanced Reliability – New equipment incorporates the latest innovations, reducing downtime and maintenance issues. This improves productivity and on-time delivery.
- Future-Proofing – Purchasing up-to-date machines ensures your shop stays competitive as manufacturing technologies continue advancing rapidly. It’s an investment in future capabilities.
Regularly budgeting for capital expenditures is key. Machines should be replaced before they become obsolete. Work with quality equipment suppliers that understand your manufacturing needs.
Implement Automation
Adopting automation technologies and processes can provide significant benefits for machine shops. Automating repetitive or dangerous tasks frees up employees for higher-value work while also improving safety. It also enhances consistency and precision, leading to higher quality results.
Investing in CNC machines and integrating automation allows completing jobs faster and more accurately. This increased efficiency can boost shop productivity and capacity without necessarily hiring more staff. The automation handles tasks that previously required manual work, saving on labor costs.
Integrating automated inspection and reporting provides real-time data to easily identify any quality issues or production problems. This prevents wasted time and materials. Automation also minimizes variability and human error in production. Parts have greater uniformity and adherence to specifications when CNC machines perform the work.
Overall, implementing automation intelligently allows machine shops to work smarter. Shops can take on more business and tighten margins while maintaining quality. With the right automation technologies, machine shops position themselves for scalable growth and long-term success. The capital investment pays dividends over time with the labor and efficiency gains.
Adopt Advanced Software
Advances in software technology have opened up many new opportunities for machine shops to improve efficiency and productivity. Adopting the latest CAD, CAM, and ERP software can streamline workflows, reduce errors, and enhance collaboration.
CAD software allows machine shops to create detailed 3D models and technical drawings digitally. The latest CAD programs incorporate automation and parametric modeling to speed up design work. They also integrate seamlessly with CAM software for efficient data transfer. Upgrading to the newest CAD version ensures you can handle the most complex part geometries and rapidly iterate designs.
CAM software uses CAD models to generate toolpaths and G-code to drive CNC machines. New CAM systems incorporate sophisticated algorithms that optimize tool selection, speeds, feeds, and motion planning. This results in more efficient machining, reduced cycle times, and less wear on cutting tools. Advanced simulation and verification tools also minimize waste from potential programming errors.
ERP software centralizes operations and integrates all departments in a machine shop. It provides real-time visibility into inventory, orders, production scheduling, costs, and other metrics. Modern cloud-based ERP platforms enable secure access from anywhere. This allows managers to make data-driven decisions on the fly. ERP systems also facilitate supply chain coordination and make it easier to adapt to changing customer demands.
By implementing the latest CAD, CAM, and ERP software solutions, machine shops can achieve transformative digital workflows. The increased automation, efficiency, and flexibility give shops a competitive advantage in the marketplace.
Leverage Data Analytics
The use of data analytics is becoming increasingly critical for modern machine shops to stay competitive. By collecting and analyzing operational data, shops can gain valuable insights to optimize productivity, efficiency, and quality.
Some ways machine shops can leverage data analytics include:
- Track machine utilization rates to identify bottlenecks and ensure optimal asset usage. Data can show which machines are overburdened and which are underutilized.
- Analyze cycle times for different operations to find ways to streamline workflows. Identifying parts of the process that are taking longer than expected allows you to address inefficiencies.
- Use sensor data from machines to implement predictive maintenance. By monitoring vibration, temperature and other metrics, you can detect issues and schedule maintenance before equipment fails.
- Monitor inventory levels and reorder points to optimize stock. Data can identify fast-moving inventory to avoid stockouts while minimizing tied-up capital.
- Track quality metrics like scrap and rework rates to quickly detect when processes drift out of spec. Analytics enable continuous process improvements.
- Create dashboards with key operational KPIs to provide managers real-time visibility. Quick access to key metrics facilitates faster and better decision making.
- Perform win/loss analysis on sales data to identify trends and improve sales strategies. Analyzing characteristics of won and lost deals can provide insights to refine target customers, adjust offerings, and optimize sales processes.
With the rise of Industrial IoT, more shop data is available than ever before. Leveraging analytics turns this data into powerful insights to help machine shops optimize productivity, boost quality, improve maintenance practices, and reduce costs. Those that embrace data-driven decision making will have a competitive edge.
Focus on Employee Training
Constant training and development of staff skills is crucial for machine shops to keep up with rapidly advancing technologies and manufacturing techniques. Investing in ongoing employee education demonstrates a commitment to supporting workers while ensuring the business has the expertise needed to meet customer demands.
Retraining employees regularly on new equipment, software, and processes empowers them to fully utilize the latest innovations. This boosts productivity, quality control, and safety. Workers who feel confident operating advanced machinery and technologies are more engaged, increasing retention rates.
Consider subsidizing offsite training programs or bringing in qualified instructors. Encourage staff at all levels to participate and make sure learnings are applied immediately afterwards. Tracking certifications helps validate competencies. Multi-skilled cross-training creates flexibility.
Hands-on peer coaching and knowledge sharing reinforces learning. Schedule time for teams to train together and collaborate. Managers should continuously assess gaps and provide feedback. An organizational culture valuing continuous education enables a machine shop to constantly improve.
Offer Additional Services
Expanding beyond basic machining and fabrication into additional offerings can help machine shops stay competitive and meet evolving customer needs. This may involve taking on design work, prototyping, assembly, finishing services, inventory management, shipping and logistics coordination, and more.
Diversifying capabilities allows shops to capture more business from existing customers who may now rely on them for expanded services. It also makes them more attractive to new customers looking for a one-stop provider.
Some ways shops can branch out include:
- Design and Engineering Services – Offering design and engineering support allows shops to get involved earlier in the manufacturing process. This provides more insight into final part requirements.
- Rapid Prototyping – Equipping to produce functional prototypes enables shops to deliver concept validations faster. This speeds up design iterations.
- Sub-Assembly and Finishing – Providing sub-assembly, surface finishing, coatings, heat treatment, and other secondary operations completes parts fully before shipping.
- Testing and Inspection – In-house testing and inspection using CMMs, optical comparators, and other equipment gives customers quality assurance.
- Inventory and Shipping – Managing inventory and coordinating final packaging and shipping reduces hassles for customers.
Diversifying into new offerings requires investment in equipment, people, and processes. But it also strengthens customer relationships, loyalty, and expands business opportunities.
Adapt Business Model
To stay competitive, machine shops must be willing to adapt their business models. Some options to consider include:
- Contract Manufacturing – Become a contract manufacturer that produces parts to customers’ specifications, rather than selling your own proprietary products. This allows you to leverage your machining capabilities for new revenue streams.
- On-Demand Manufacturing – Offer on-demand manufacturing services, where customers can order small batches of custom parts as needed. This caters to prototyping, small startups, and researchers.
- E-Commerce – Develop an e-commerce portal where customers can easily order common parts online. This significantly expands your reach and revenue.
- Diversification – Consider diversifying into other services like 3D printing, engineering consultation, CAD services, etc. This makes your business a one-stop shop.
- Customization – Provide highly customized and personalized parts catered to each customer’s requirements. This provides value that competitors can’t match.
Adapting the business model is critical for machine shops to keep up with market changes. Evaluating different options like contract manufacturing, on-demand services, e-commerce, diversification, and customization can help secure continued growth and profitability. The key is understanding your capabilities and customers’ needs to select the right approach.
How CADDi Drawer Can Help Job Shop Management
CADDi Drawer is a powerful tool designed to support job shop management that leverages AI to analyze and organize technical drawings.
For example, Hilltop, a machine shop, has significantly improved its operational efficiency by integrating CADDi Drawer with its existing systems. For more details, please refer to the article below.
Customer Case – Hilltop: Accelerating Company-Wide Digital Transformation with CADDi Drawer
By identifying similar drawings from past projects, it enables faster quotation creation. Sales teams no longer need to start from scratch or wait for engineers to locate relevant past projects. CADDi quickly determines if a new project is manufacturable in-house or requires outsourcing, allowing for rapid responses to customer inquiries.
Beyond accelerating the quotation process, CADDi Drawer also improves the quotation-to-order ratio. By storing both quotation and order data, it allows shops to compare pricing levels for similar projects. Analyzing won and lost projects side-by-side provides insights to optimize pricing strategies and win more business.
The advanced search capabilities dramatically reduce the time engineers spend searching for information. With the ability to search by keywords, tags, or even images, locating relevant drawings, projects, costs, and other data is easier than ever. Engineers can quickly access the information they need, boosting productivity.
The software also facilitates standardization by identifying similar parts across projects. By comparing drawings for similar assemblies, machine shops can spot opportunities to standardize jigs, streamlining production and reducing costs.
CADDi even supports CAM production by enabling the reuse of CAM data for nearly identical parts. Rather than programming new parts from scratch, machinists can leverage existing CAM data, saving valuable programming time.
Ready to see CADDi Drawer in action? Get a personalized demo.
Subscribe to our Blog!
Related Resources
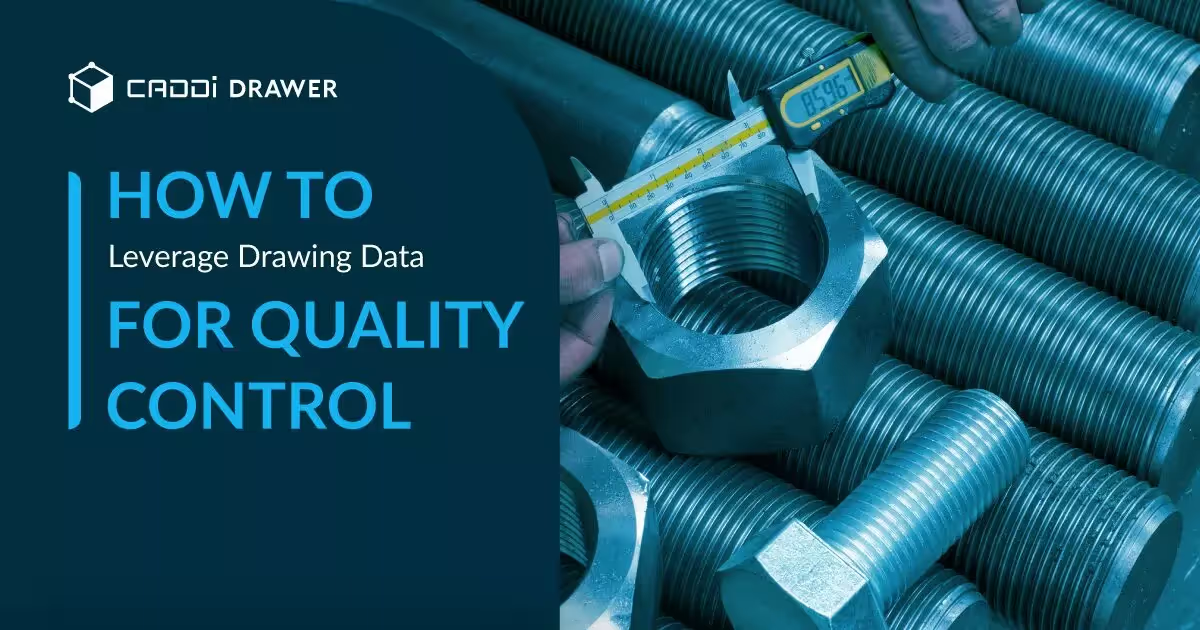
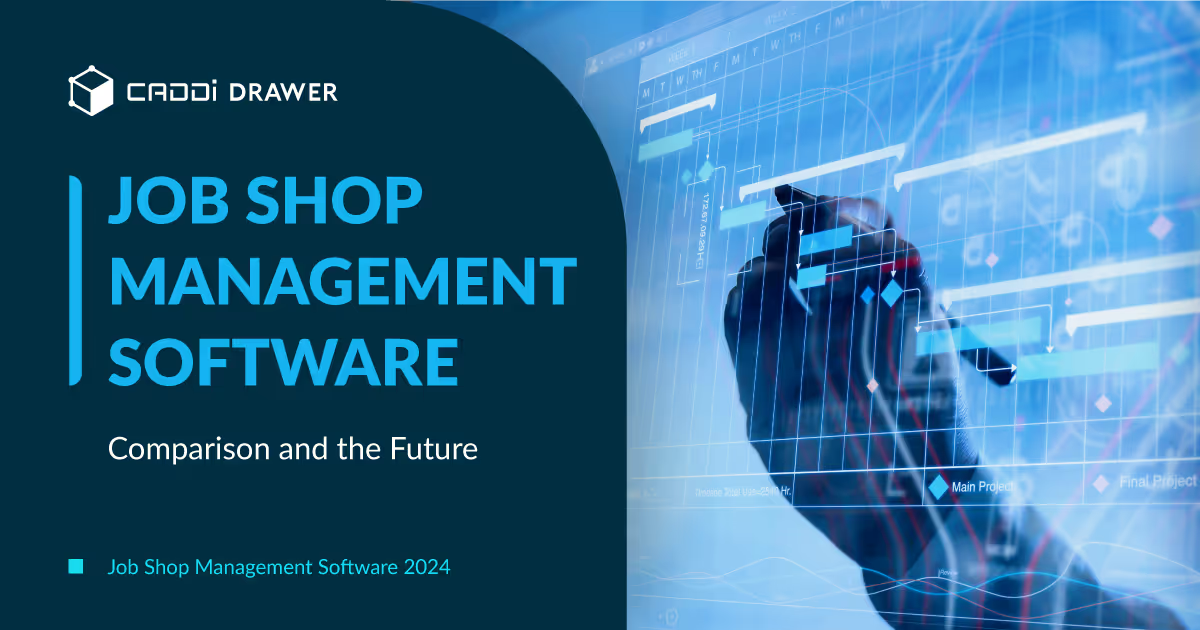
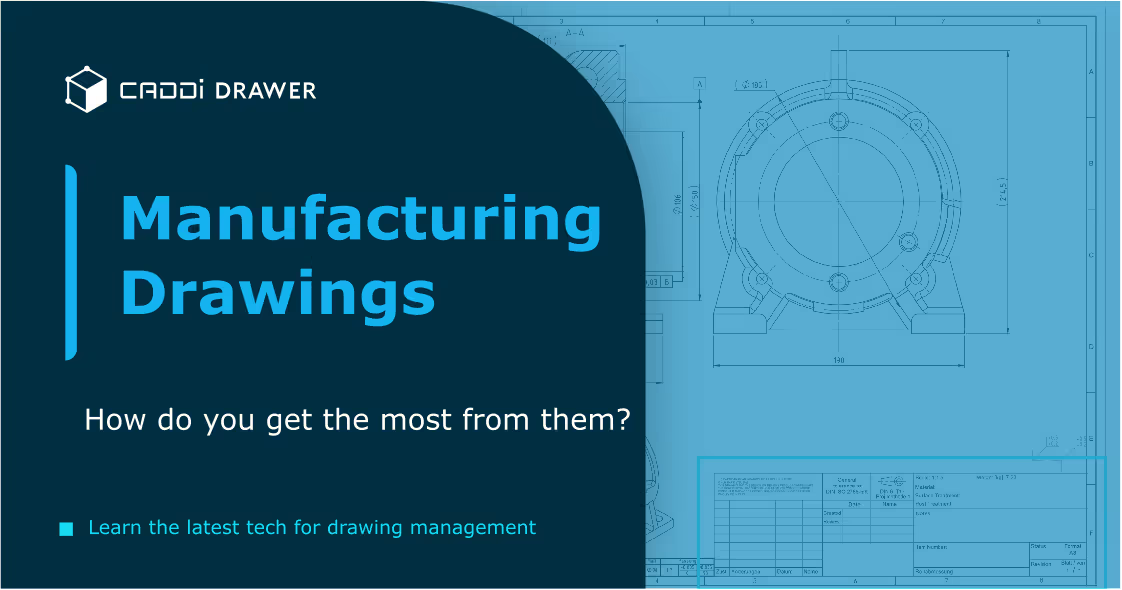

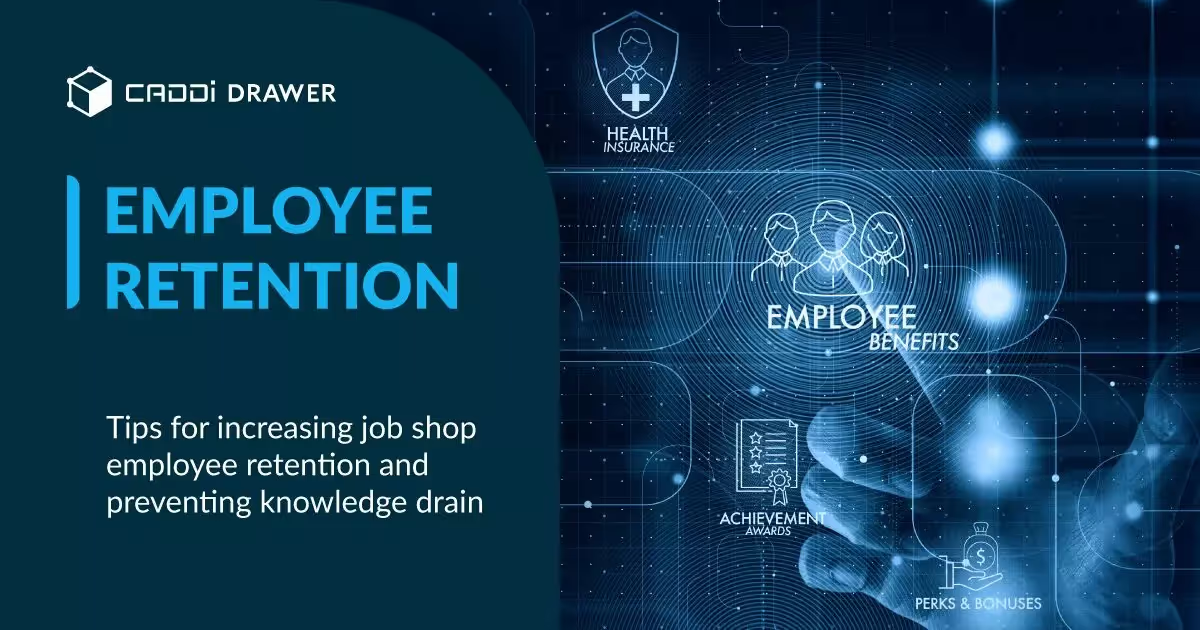
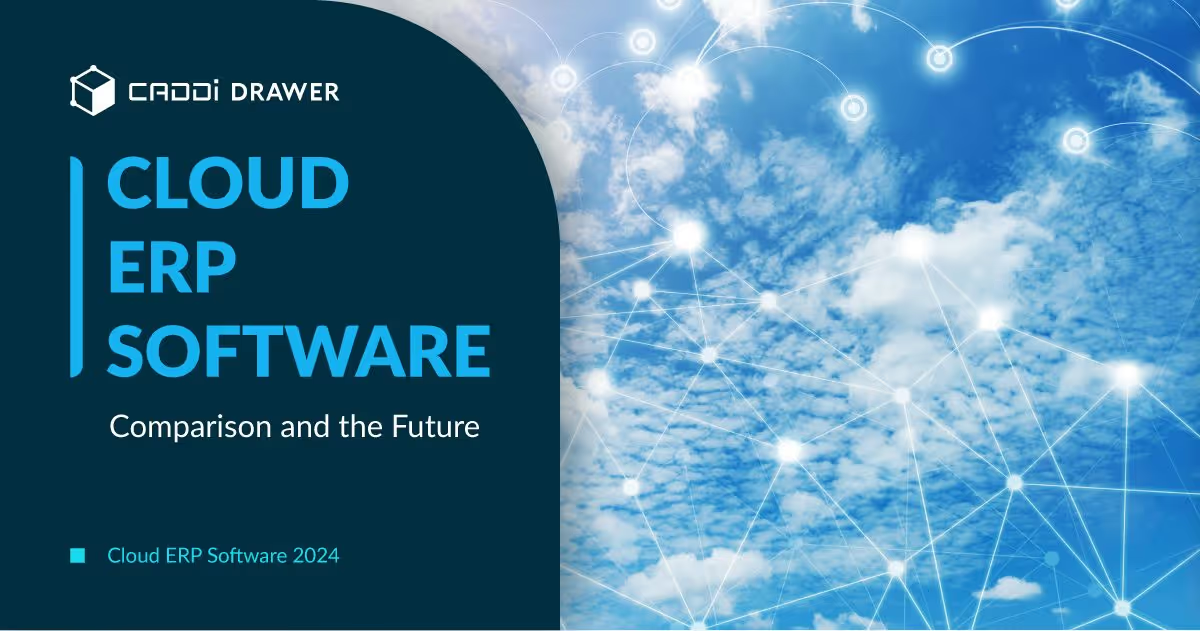