Manufacturing Systems of Insight: Transforming Data into Value
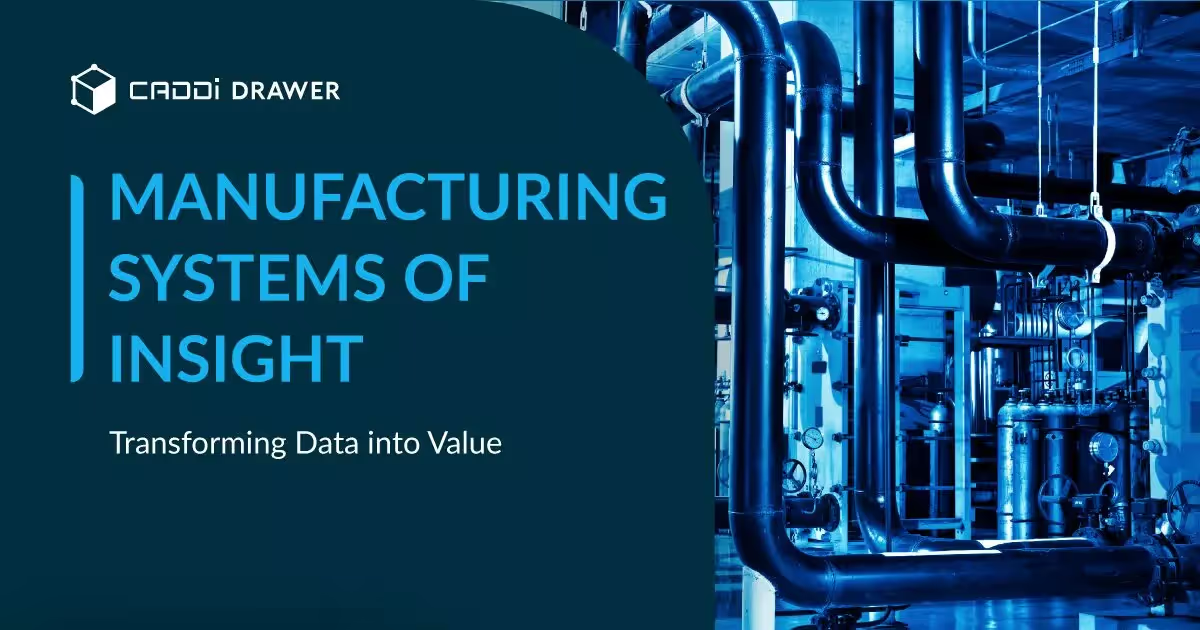
Table of Contents
What Are Systems of Insight?
Manufacturing companies have traditionally relied on systems of record (SoR) like ERP, PLM, MES, and other transactional systems to capture data about their operations. While SoR provide a necessary foundation, manufacturers are now turning to systems of insight (SoI) to derive more value from their data assets.
SoI sit at the intersection of SoR and advanced analytics. They integrate and analyze data from various SoR and apply intelligence to identify trends, patterns, and opportunities that drive better decisions. The goal is to transform the raw transactional data stored in SoR into actionable insights that generate business value.
SoI are becoming increasingly critical for manufacturers for several reasons:
- Data volumes are exploding from IoT sensors, equipment logs, transactional systems, and more. Systems of insight help make sense of all this data.
- Manufacturers need deeper visibility into operations. Systems of insight enable real-time monitoring, alerting, and forecasting.
- There is increasing need for predictive maintenance to reduce downtime. Systems of insight leverage machine learning for equipment diagnostics.
- Competitive pressures require faster and more flexible responsiveness. Systems of insight support rapid scenario modeling.
- Supply chain stakeholders expect personalized optimization. Insightful systems understand individual needs, driving end-to-end efficiency.
SoI enable enterprise transformation by breaking down data silos across engineering, procurement, production and sales. The systems integrate structured data (specs, drawings, BOMs) and unstructured data (quality, maintenance records) into a unified data layer. Advanced analytics are then applied to generate insights for each function, from design to operations to service.
CADDi DRAWER plays a key role as the foundation for SoI in manufacturing. CADDi extracts product data scattered across CAD, PLM, and other engineering systems. It centralizes the data around drawing and supply chain digital threads that connect requirements, designs, parts, costs and changes. This integrated product record makes it easier to access data downstream for use in SoI applications.
.avif)
For example, CADDi can feed design and BOM data into an SoI application that analyzes procurement and supplier performance data for cost and quality trends by category. The SoI can trace issues to specific design choices and provide engineering insights to optimize designs for manufacturability. In this way, CADDi enables drawing and supply chain centric insights not possible with data locked in PLM and ERP silos.
Using Data Analytics and AI for Insight
With a unified data foundation in place, manufacturers can leverage analytics and AI to gain valuable operational insights. By analyzing data from across the product lifecycle, they can identify inefficiencies, risks, and opportunities not apparent from any one data source alone.
- Analyzing sensor data from equipment and machines to identify anomalies and predict maintenance needs. By monitoring vibration, temperature, and other metrics, issues can be detected early.
- Analyzing process data from production runs to identify deviations or patterns indicating process problems. Statistical process control techniques can flag issues for investigation.
- Analyzing customer data from surveys, warranties, and interactions to understand pain points and opportunities to improve quality or service. Sentiment analysis can provide insight.
- Applying AI techniques like machine learning to large datasets from across the manufacturing process to identify hidden patterns and relationships not easily detectable with traditional analytics. These insights can drive optimization.
The key is bringing together data from disparate sources across the product lifecycle to uncover insights that would be difficult to see in isolation.
Some key areas where analytics and AI drive manufacturing insights include:
Predictive maintenance – Analyzing sensor data (vibration, temperature, error codes) and maintenance records to detect failure patterns and optimize service intervals by equipment type and usage.
Quality improvement – Analyzing inspection, test, scrap, and warranty data by product configuration to identify design and process issues. Tracing quality to specific design decisions, suppliers, and manufacturing lines.
Supply chain optimization – Analyzing inventory, supplier performance, logistics, and demand data to reduce costs and improve responsiveness. Simulating what-if scenarios to optimize inventory and capacity.
Engineering change impact – Analyzing the cost and time impact of proposed design changes before implementing. Identifying similar past changes and assessing effects on quality, manufacturing, and service.
The key is linking data across requirements, design, manufacturing, quality, service and the supply chain for holistic insights. Advanced analytics and machine learning then reveal patterns and relationships that are difficult to see with traditional reporting.
Driving Business Value
SoI create a virtuous cycle of using data to continuously improve products and processes. Some of the top benefits include:
- Increased yield, throughput and asset utilization
- Reduced quality defects, scrap, rework and warranty claims
- Optimized inventory levels and lower material costs
- Faster time-to-market and more efficient change management
- Higher customer satisfaction and service levels
SoI ultimately enable manufacturers to make smarter, faster decisions that drive operational excellence and competitive advantage. However, realizing this value requires more than just technology. Manufacturers must foster a data-driven culture and upskill their workforce to leverage insights effectively.
They also need to establish a robust data foundation that integrates information from across the business. CADDi DRAWER provides this foundation by centralizing and connecting product data. With easier access to drawing-centric data, more stakeholders can leverage SoI to optimize their piece of the product lifecycle.
Bringing it all together, Systems of Insight allow manufacturers to exploit their growing data assets for business value. CADDi enables this by delivering the complete, accurate, and connected product data that is the lifeblood of effective SoI.
What Are Systems of Insight?
Manufacturing companies have traditionally relied on systems of record (SoR) like ERP, PLM, MES, and other transactional systems to capture data about their operations. While SoR provide a necessary foundation, manufacturers are now turning to systems of insight (SoI) to derive more value from their data assets.
SoI sit at the intersection of SoR and advanced analytics. They integrate and analyze data from various SoR and apply intelligence to identify trends, patterns, and opportunities that drive better decisions. The goal is to transform the raw transactional data stored in SoR into actionable insights that generate business value.
SoI are becoming increasingly critical for manufacturers for several reasons:
- Data volumes are exploding from IoT sensors, equipment logs, transactional systems, and more. Systems of insight help make sense of all this data.
- Manufacturers need deeper visibility into operations. Systems of insight enable real-time monitoring, alerting, and forecasting.
- There is increasing need for predictive maintenance to reduce downtime. Systems of insight leverage machine learning for equipment diagnostics.
- Competitive pressures require faster and more flexible responsiveness. Systems of insight support rapid scenario modeling.
- Supply chain stakeholders expect personalized optimization. Insightful systems understand individual needs, driving end-to-end efficiency.
SoI enable enterprise transformation by breaking down data silos across engineering, procurement, production and sales. The systems integrate structured data (specs, drawings, BOMs) and unstructured data (quality, maintenance records) into a unified data layer. Advanced analytics are then applied to generate insights for each function, from design to operations to service.
CADDi DRAWER plays a key role as the foundation for SoI in manufacturing. CADDi extracts product data scattered across CAD, PLM, and other engineering systems. It centralizes the data around drawing and supply chain digital threads that connect requirements, designs, parts, costs and changes. This integrated product record makes it easier to access data downstream for use in SoI applications.
.avif)
For example, CADDi can feed design and BOM data into an SoI application that analyzes procurement and supplier performance data for cost and quality trends by category. The SoI can trace issues to specific design choices and provide engineering insights to optimize designs for manufacturability. In this way, CADDi enables drawing and supply chain centric insights not possible with data locked in PLM and ERP silos.
Using Data Analytics and AI for Insight
With a unified data foundation in place, manufacturers can leverage analytics and AI to gain valuable operational insights. By analyzing data from across the product lifecycle, they can identify inefficiencies, risks, and opportunities not apparent from any one data source alone.
- Analyzing sensor data from equipment and machines to identify anomalies and predict maintenance needs. By monitoring vibration, temperature, and other metrics, issues can be detected early.
- Analyzing process data from production runs to identify deviations or patterns indicating process problems. Statistical process control techniques can flag issues for investigation.
- Analyzing customer data from surveys, warranties, and interactions to understand pain points and opportunities to improve quality or service. Sentiment analysis can provide insight.
- Applying AI techniques like machine learning to large datasets from across the manufacturing process to identify hidden patterns and relationships not easily detectable with traditional analytics. These insights can drive optimization.
The key is bringing together data from disparate sources across the product lifecycle to uncover insights that would be difficult to see in isolation.
Some key areas where analytics and AI drive manufacturing insights include:
Predictive maintenance – Analyzing sensor data (vibration, temperature, error codes) and maintenance records to detect failure patterns and optimize service intervals by equipment type and usage.
Quality improvement – Analyzing inspection, test, scrap, and warranty data by product configuration to identify design and process issues. Tracing quality to specific design decisions, suppliers, and manufacturing lines.
Supply chain optimization – Analyzing inventory, supplier performance, logistics, and demand data to reduce costs and improve responsiveness. Simulating what-if scenarios to optimize inventory and capacity.
Engineering change impact – Analyzing the cost and time impact of proposed design changes before implementing. Identifying similar past changes and assessing effects on quality, manufacturing, and service.
The key is linking data across requirements, design, manufacturing, quality, service and the supply chain for holistic insights. Advanced analytics and machine learning then reveal patterns and relationships that are difficult to see with traditional reporting.
Driving Business Value
SoI create a virtuous cycle of using data to continuously improve products and processes. Some of the top benefits include:
- Increased yield, throughput and asset utilization
- Reduced quality defects, scrap, rework and warranty claims
- Optimized inventory levels and lower material costs
- Faster time-to-market and more efficient change management
- Higher customer satisfaction and service levels
SoI ultimately enable manufacturers to make smarter, faster decisions that drive operational excellence and competitive advantage. However, realizing this value requires more than just technology. Manufacturers must foster a data-driven culture and upskill their workforce to leverage insights effectively.
They also need to establish a robust data foundation that integrates information from across the business. CADDi DRAWER provides this foundation by centralizing and connecting product data. With easier access to drawing-centric data, more stakeholders can leverage SoI to optimize their piece of the product lifecycle.
Bringing it all together, Systems of Insight allow manufacturers to exploit their growing data assets for business value. CADDi enables this by delivering the complete, accurate, and connected product data that is the lifeblood of effective SoI.
Ready to see CADDi Drawer in action? Get a personalized demo.
Subscribe to our Blog!
Related Resources
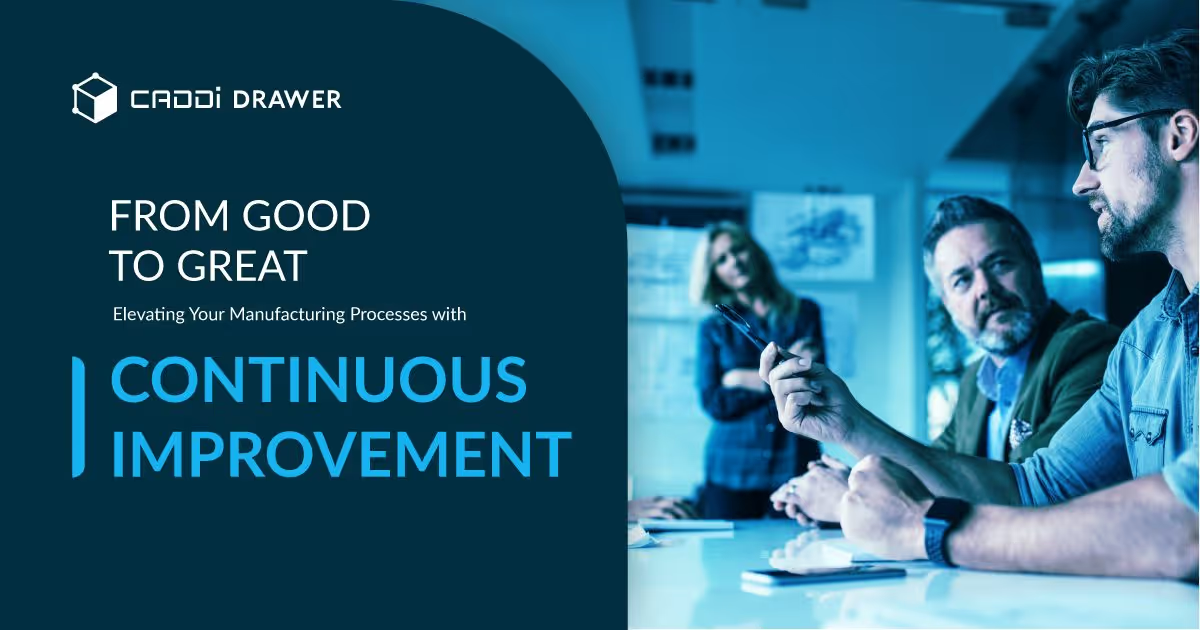
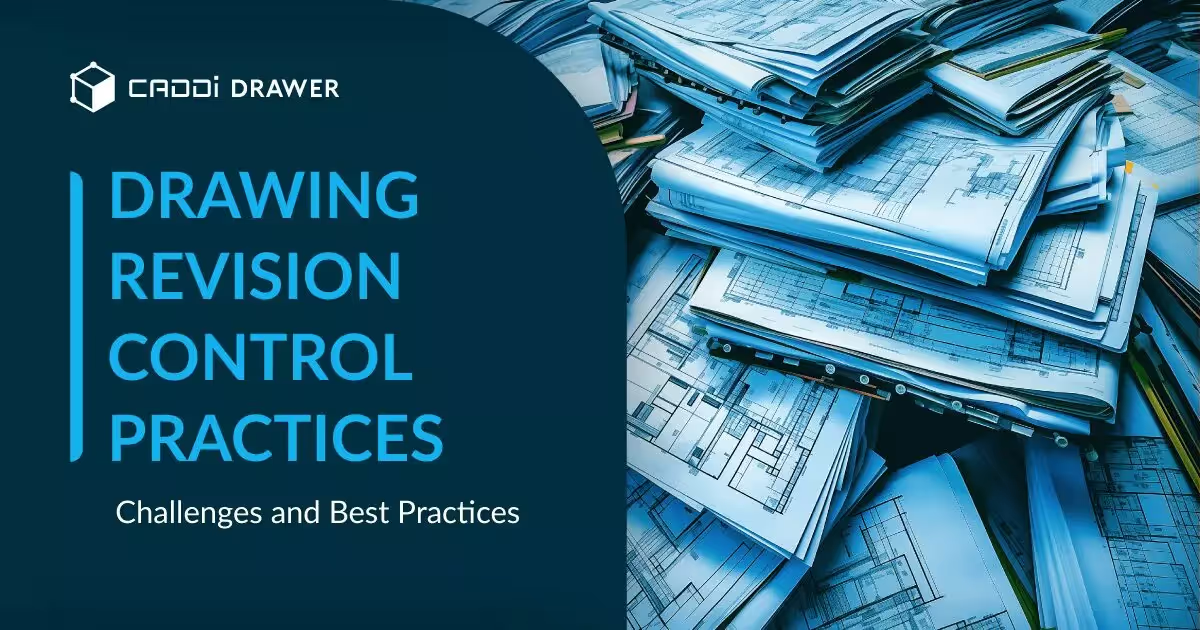
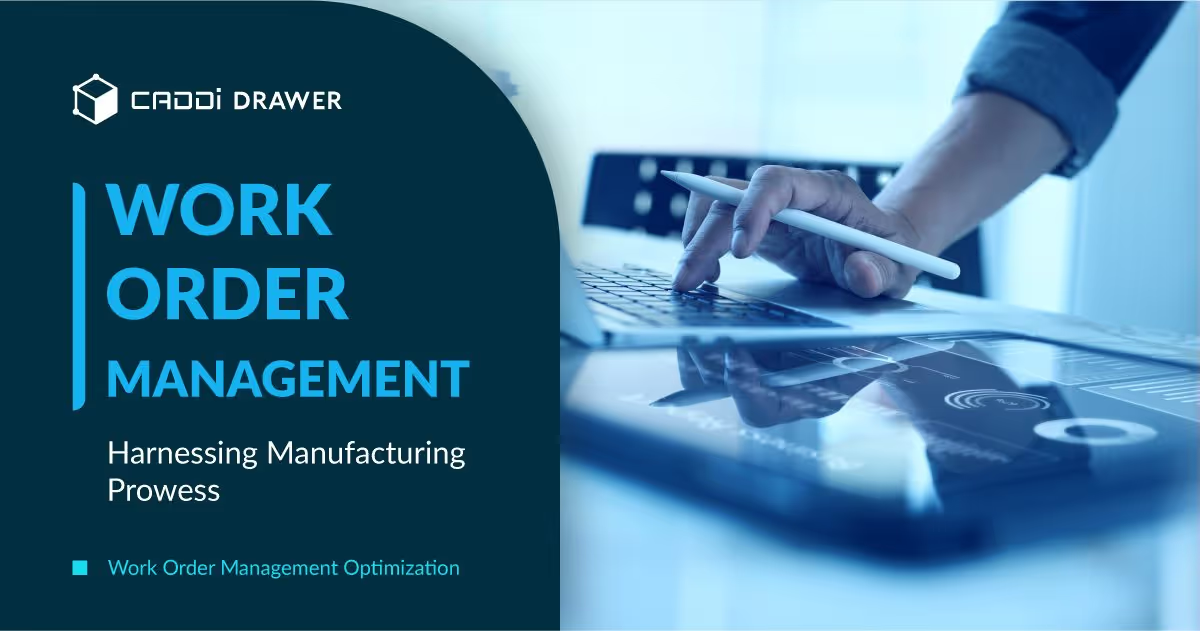
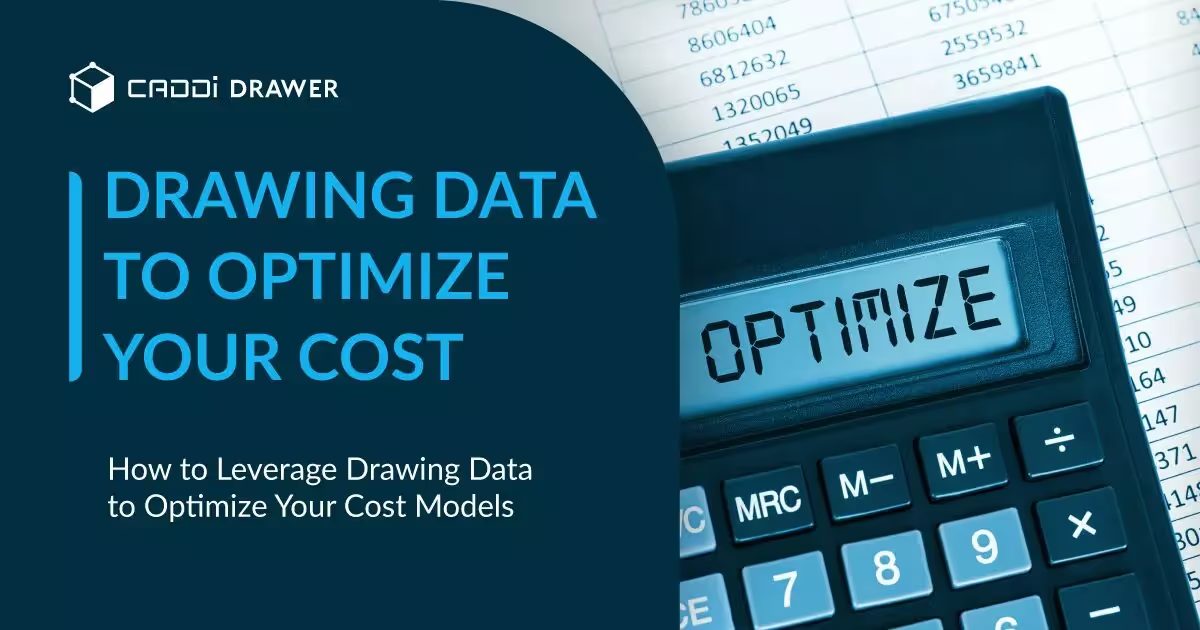
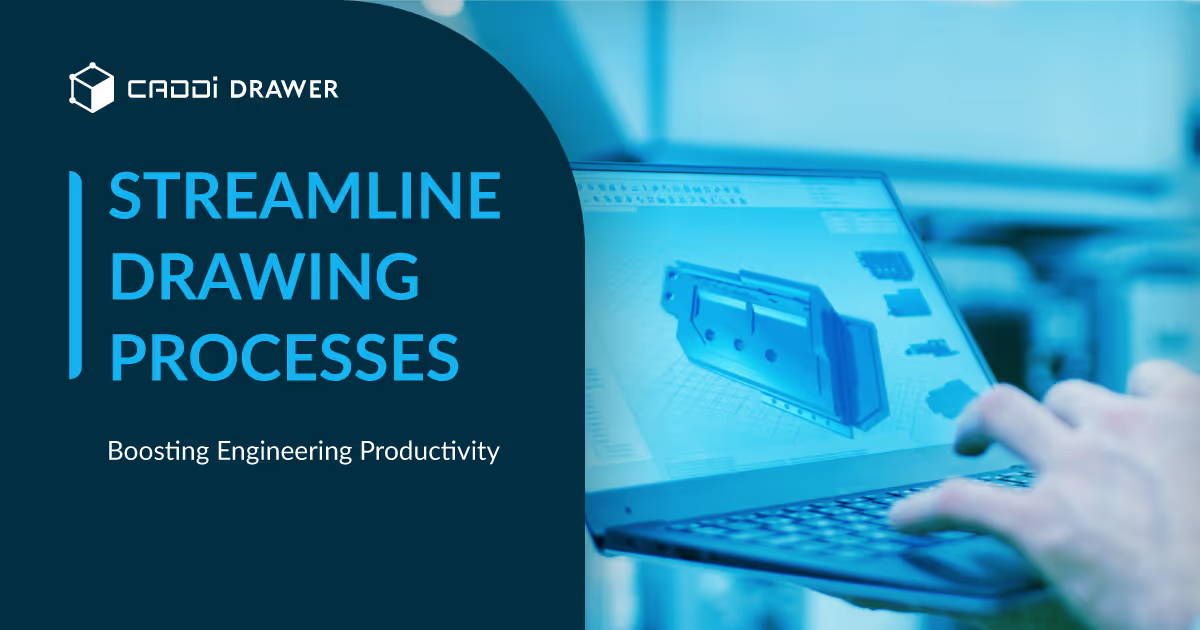
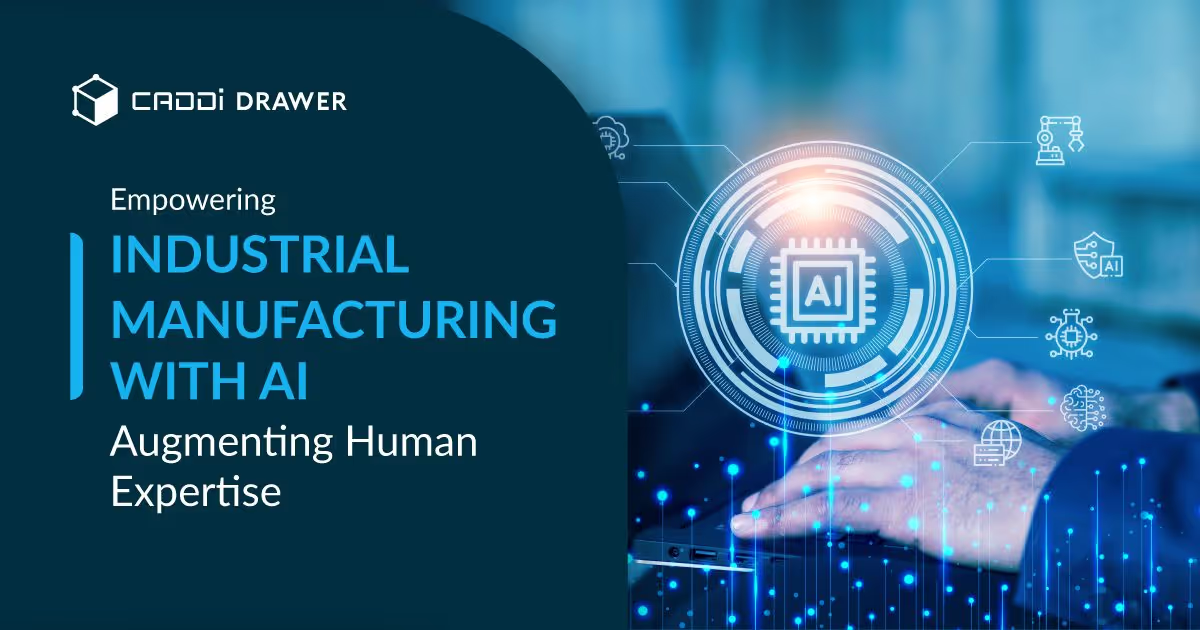