Data Gaps: Causes, Symptoms, and Cures
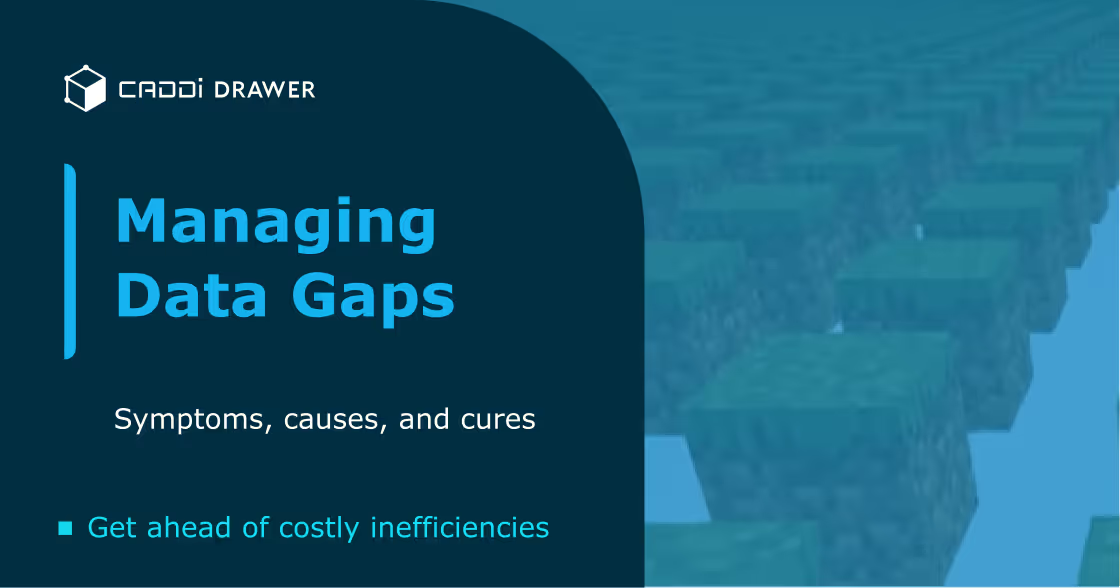
Table of Contents
When you think about the big picture of your company’s digital systems – your ERP, your PLM, your PDM, etc. – how do you imagine it? It’s nice to envision a well-oiled factory, where data seamlessly flows from where it’s produced to where it’s needed. You can probably map out how each program’s data ought to connect each other.
But the word “ought” is doing some heavy lifting here. In reality, your mental image should be of a factory where boxes of data are frequently falling off conveyor belts, being stored on the wrong shelves, or left collecting cobwebs in some forgotten corner. No matter how well constructed your digital systems are, there will always be some shortcomings in capturing the real state of your inventory and designs.
These shortcomings are called data gaps, and they’re a big deal. In our recent American Manufacturing Pressure and Productivity Index, we identified data gaps as a major cause of unnecessary cost and inefficiency for manufacturing shops of every size. Data gaps aren’t insurmountable, though. By creating a more comprehensive and insightful digital system, closing data gaps can become one of the most impactful changes you can make to reduce costs and accelerate processes. Making these changes is especially important in this era of economic uncertainty and stressors.
What causes data gaps?
Data gaps are largely caused by data silos, where data lives in one location that insufficiently communicates with other locations. For example, you might have quality data for a part in your PLM system, and you want to look it up when placing a procurement order for a similar part. If your procurement system can’t automatically bring up that data, your data is siloed. It may be possible to manually cross-reference some part IDs or specifications, but if that process is too tedious or time-consuming, it functionally doesn’t exist.
You can also accumulate data gaps when legacy data is incompatible with new systems. When you adopt new software, sometimes your historical records need to be manually converted to exist in the new system. This can be a very tedious and time consuming process, and it’s tempting to skip it because “the old data is still there”. It’s technically true that you could dig through old spreadsheets or paper files to find what you need, but if it’s unlikely for someone to think to or make the effort, it’s functionally a data gap. New employees may lack the experience or knowledge to parse these old records, or understand when they should be consulted.
Finally, data gaps can accumulate when data simply isn’t stored in the first place. You likely have processes in place to track and record things with the granularity you need, but in practice, these can easily be skipped due to time constraints, done quickly and shoddily, or forgotten. These are the most difficult data gaps to close; you don’t know what you don’t know.
What problems are caused by data gaps?
Data gaps cause major inefficiencies and unnecessary costs. For slowdowns, we found that 41% of procurement professionals, 50% of engineers, and 54% of salespeople spent 1-2 hours a day tracking down the information they needed. Some – 18% of procurement professionals, 13% of engineers, and 21% of salespeople – spent over four hours per day. We found similar stats for other tasks, such as ensuring information is accurate, complete, and accessible. Such challenges resulting from data gaps, when added up, can easily consume half a professional’s day, delaying other work and reducing employee satisfaction.
When employees are burdened with such time-consuming requirements, they’re likely to find shortcuts to maintain productivity. In the case of navigating data gaps, it means making assumptions that are “good enough” with what data you have available. These can be educated assumptions, but they’re unlikely to be ideal. We found that 60% of procurement professionals have sourced a part at a higher price than what they knew was possible, and that 71% of sales professionals have quoted or sold an unprofitable deal. Notably, these are only the stats for people who are aware of making suboptimal decisions. Many more are made in ignorance.
The reason for not being able to make the best possible deal is due to data gaps. If these professionals had easy access to comprehensive historic data, they’d be able to negotiate better prices, find and consolidate better suppliers, and provide faster and more accurate quotations.
How to prevent and solve data gaps
So we know data gaps are problematic, and that they’re likely to occur as your system evolves. But how do you prevent them, and remove those that already exist? The key is building a digital system that uses cutting-edge technology to transcend silos and make data available quickly and intuitively. Here are some of the qualities that this system needs to have:
System agnostic – your system needs to be able to incorporate data from any possible source, without demanding any specific consistent structure. It should be able to cover everything from your most recent digitally created data to old scanned documents. This creates a manufacturing data lake that contains everything needed for any role or requirement.
Intuitive data linking – typically, you need to memorize arbitrary IDs or inconsistent tags to connect data across systems. This creates data gaps, especially for less experienced employees. Instead, your system needs to connect data via intuitive aspects. For example, if you want to look up data for a part, you should be able to find all the data you need just based on the drawing of the part.
Foregrounded insights – making strategic decisions, like swapping or consolidating suppliers, requires lots of data – every past order, its cost, and the resulting quality data, for starters. If that data is available, but only in spreadsheets spread across multiple programs that need to be cross referenced, it presents a functional data gap for someone who needs to quickly assess a pattern. A modern data system can highlight trends and insights by aligning data on the qualities that matter most and consolidating it in one searchable and filterable place.
Welcome to CADDi
CADDi provides a modern, AI-driven, data lake that overcomes and prevents data gaps. With our mass digitalization tool, we turn all of your parts drawings – from old scanned hand-drawn drafts to modern CAD-produced files – into searchable digital assets. You can search not just the tags and titles assigned to them, but any text that appears in the drawing, or even by the features of the drawing itself. Need to find all the data on every 8-flange bearing you’ve ever designed, ordered, or sold? CADDi makes it easy.
With this intuitive linking across all of your systems, even a novice user can surface crucial patterns around procurement, RFQs, and design data. Rather than needing to make costly assumptions or waste hours digging through data, all the answers you need from your PDM, ERP, and more appear simply by searching with the part itself. You can even start with a hand-drawn sketch of what you’re looking for.
Data gaps are a chronic problem for manufacturers of every size. However, by proactively investing in new technologies like CADDi, you can turn this challenge into a competitive advantage. In tight economic times, upleveling your technology is a cheaper investment than finding more labour or completely restructuring your supply chain.
Start on your journey to making this impactful change by booking a demo of CADDi.
When you think about the big picture of your company’s digital systems – your ERP, your PLM, your PDM, etc. – how do you imagine it? It’s nice to envision a well-oiled factory, where data seamlessly flows from where it’s produced to where it’s needed. You can probably map out how each program’s data ought to connect each other.
But the word “ought” is doing some heavy lifting here. In reality, your mental image should be of a factory where boxes of data are frequently falling off conveyor belts, being stored on the wrong shelves, or left collecting cobwebs in some forgotten corner. No matter how well constructed your digital systems are, there will always be some shortcomings in capturing the real state of your inventory and designs.
These shortcomings are called data gaps, and they’re a big deal. In our recent American Manufacturing Pressure and Productivity Index, we identified data gaps as a major cause of unnecessary cost and inefficiency for manufacturing shops of every size. Data gaps aren’t insurmountable, though. By creating a more comprehensive and insightful digital system, closing data gaps can become one of the most impactful changes you can make to reduce costs and accelerate processes. Making these changes is especially important in this era of economic uncertainty and stressors.
What causes data gaps?
Data gaps are largely caused by data silos, where data lives in one location that insufficiently communicates with other locations. For example, you might have quality data for a part in your PLM system, and you want to look it up when placing a procurement order for a similar part. If your procurement system can’t automatically bring up that data, your data is siloed. It may be possible to manually cross-reference some part IDs or specifications, but if that process is too tedious or time-consuming, it functionally doesn’t exist.
You can also accumulate data gaps when legacy data is incompatible with new systems. When you adopt new software, sometimes your historical records need to be manually converted to exist in the new system. This can be a very tedious and time consuming process, and it’s tempting to skip it because “the old data is still there”. It’s technically true that you could dig through old spreadsheets or paper files to find what you need, but if it’s unlikely for someone to think to or make the effort, it’s functionally a data gap. New employees may lack the experience or knowledge to parse these old records, or understand when they should be consulted.
Finally, data gaps can accumulate when data simply isn’t stored in the first place. You likely have processes in place to track and record things with the granularity you need, but in practice, these can easily be skipped due to time constraints, done quickly and shoddily, or forgotten. These are the most difficult data gaps to close; you don’t know what you don’t know.
What problems are caused by data gaps?
Data gaps cause major inefficiencies and unnecessary costs. For slowdowns, we found that 41% of procurement professionals, 50% of engineers, and 54% of salespeople spent 1-2 hours a day tracking down the information they needed. Some – 18% of procurement professionals, 13% of engineers, and 21% of salespeople – spent over four hours per day. We found similar stats for other tasks, such as ensuring information is accurate, complete, and accessible. Such challenges resulting from data gaps, when added up, can easily consume half a professional’s day, delaying other work and reducing employee satisfaction.
When employees are burdened with such time-consuming requirements, they’re likely to find shortcuts to maintain productivity. In the case of navigating data gaps, it means making assumptions that are “good enough” with what data you have available. These can be educated assumptions, but they’re unlikely to be ideal. We found that 60% of procurement professionals have sourced a part at a higher price than what they knew was possible, and that 71% of sales professionals have quoted or sold an unprofitable deal. Notably, these are only the stats for people who are aware of making suboptimal decisions. Many more are made in ignorance.
The reason for not being able to make the best possible deal is due to data gaps. If these professionals had easy access to comprehensive historic data, they’d be able to negotiate better prices, find and consolidate better suppliers, and provide faster and more accurate quotations.
How to prevent and solve data gaps
So we know data gaps are problematic, and that they’re likely to occur as your system evolves. But how do you prevent them, and remove those that already exist? The key is building a digital system that uses cutting-edge technology to transcend silos and make data available quickly and intuitively. Here are some of the qualities that this system needs to have:
System agnostic – your system needs to be able to incorporate data from any possible source, without demanding any specific consistent structure. It should be able to cover everything from your most recent digitally created data to old scanned documents. This creates a manufacturing data lake that contains everything needed for any role or requirement.
Intuitive data linking – typically, you need to memorize arbitrary IDs or inconsistent tags to connect data across systems. This creates data gaps, especially for less experienced employees. Instead, your system needs to connect data via intuitive aspects. For example, if you want to look up data for a part, you should be able to find all the data you need just based on the drawing of the part.
Foregrounded insights – making strategic decisions, like swapping or consolidating suppliers, requires lots of data – every past order, its cost, and the resulting quality data, for starters. If that data is available, but only in spreadsheets spread across multiple programs that need to be cross referenced, it presents a functional data gap for someone who needs to quickly assess a pattern. A modern data system can highlight trends and insights by aligning data on the qualities that matter most and consolidating it in one searchable and filterable place.
Welcome to CADDi
CADDi provides a modern, AI-driven, data lake that overcomes and prevents data gaps. With our mass digitalization tool, we turn all of your parts drawings – from old scanned hand-drawn drafts to modern CAD-produced files – into searchable digital assets. You can search not just the tags and titles assigned to them, but any text that appears in the drawing, or even by the features of the drawing itself. Need to find all the data on every 8-flange bearing you’ve ever designed, ordered, or sold? CADDi makes it easy.
With this intuitive linking across all of your systems, even a novice user can surface crucial patterns around procurement, RFQs, and design data. Rather than needing to make costly assumptions or waste hours digging through data, all the answers you need from your PDM, ERP, and more appear simply by searching with the part itself. You can even start with a hand-drawn sketch of what you’re looking for.
Data gaps are a chronic problem for manufacturers of every size. However, by proactively investing in new technologies like CADDi, you can turn this challenge into a competitive advantage. In tight economic times, upleveling your technology is a cheaper investment than finding more labour or completely restructuring your supply chain.
Start on your journey to making this impactful change by booking a demo of CADDi.