Procurement 101: An Introduction to Machining Process
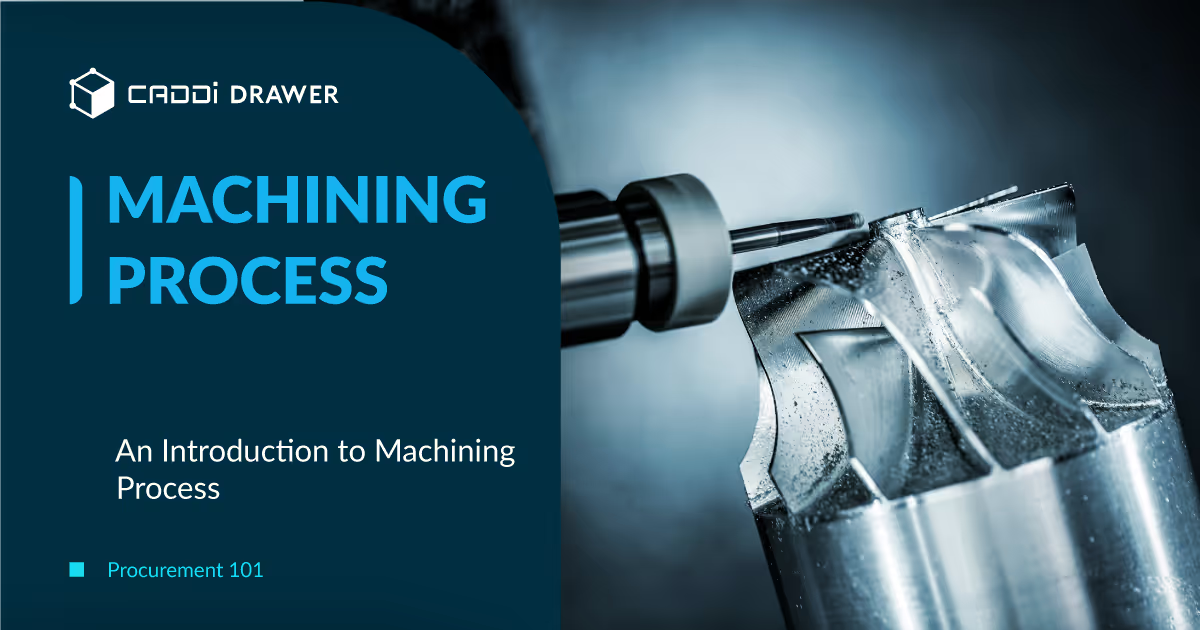
Table of Contents
What is machining?
Machining processes are manufacturing processes that use machine tools and cutting tools to physically remove material from a raw workpiece to reach a desired final shape and size. Machining is one of the most common and versatile manufacturing processes used across industries like automotive, aerospace, medical devices, tool and die making, and more.
Some of the most common machining processes include:
- Milling – Employs rotary cutters to remove material from a workpiece along various axes.
- Turning – Utilizes a single point tool to eliminate material as the workpiece rotates.
- Drilling – Creates cylindrical holes in the workpiece using drill bits.
- Sawing – Cuts off pieces of the raw material with a saw blade.
- Grinding – Removes fine amounts of material for high precision by employing an abrasive wheel.
- Broaching – Shapes internal or external keyways and gears using a specialized toothed tool.
- Electrical Discharge Machining (EDM) – Uses electrical sparks to erode conductive materials into the desired shape.
These and some other major machining processes will be explored in more detail throughout this article. Proper selection and application of the right machining process is key to producing quality components efficiently.
CNC machine tools are widely used as equipment for carrying out these processes. There are various types of machine tools, such as milling machines that primarily perform milling operations, lathes or turning machines that mainly carry out turning processes, and mill-turn machines or multi-tasking machines that can handle both milling and turning in a single unit.
Milling
Milling is a machining process that involves the use of a milling machine to remove material from a workpiece via the movement of a rotating cutter. The milling cutter rotates at high speeds and has cutting teeth along its edges that shear away material as the cutter feeds into the stationary workpiece.
Milling machines come in two main configurations – horizontal and vertical. On a horizontal milling machine, the cutters are mounted on an horizontally oriented spindle that can selectively advance into the stationary workpiece. On a vertical milling machine, the cutters are mounted on a vertically oriented spindle that can selectively advance downward into a fixed workpiece. Both configurations allow for precise control of the cutting depth.
Also, they come in 3-axis, 4-axis, and 5-axis configurations. 3-axis machines can move the tool along the X, Y, and Z axes. 4-axis machines add a rotary axis (A or B), while 5-axis machines incorporate two rotary axes (A/B and C), enabling the tool to approach the workpiece from various angles, facilitating complex contours and reducing setups.
3-axis milling machines are the most widely used and are employed for machining many types of parts. On the other hand, 4-axis and 5-axis milling machines enable the machining of more complex shapes and reduce the number of setups required, making them valuable in industries demanding advanced machining, such as aerospace and mold manufacturing. However, 4-axis and 5-axis milling machines tend to have higher equipment costs due to their more complex mechanisms.
The most common types of milling operations include:
- Face milling – machining flat surfaces into the workpiece.
- End milling – machining slots, grooves, pockets and keyways into the workpiece.
- Profile milling – machining complex three-dimensional contours into the workpiece. This relies on using a shaped cutter or moving the workpiece relative to the cutter.
- Helical milling – producing grooves and ridges using a cylindrical cutter fed at an angle to the workpiece axis.
Turning
Turning is a machining process used to create cylindrical parts by rotating a workpiece while a cutting tool is moved along its axis to cut away material. This process can create precise cylindrical shapes and produce a high-quality surface finish.
Turning operations are performed on a lathe, which holds the workpiece firmly while it rotates at high speeds. The cutting tool is fed slowly into the workpiece, removing material uniformly around the outside diameter of the part being machined. Common types of lathes used for turning operations include:
- Engine lathes – Used for precision turning of small, medium and large diameter pieces. The bed can be horizontal or vertical.
- Turret lathes – Have multiple cutting tools mounted on a turret that allows for automatic indexed operations. Good for high production.
- CNC lathes – Computer numerically controlled lathes can precisely control movement and cutting parameters. Ideal for complex parts.
The main types of turning processes include straight turning, taper turning, profiling or contour turning, grooving, and boring. Turning can produce cylindrical shapes, cones, spherical sections and concave or convex contours. The material is fed into the lathe with a longitudinal motion along the axis of the workpiece.
Turning is an essential machining process used to create rotational, cylindrical components to extremely tight tolerances and fine surface finishes. It’s ideal for producing parts that have axial symmetry and do not require complex internal geometries.
Drilling
Drilling is a machining process that uses a drill bit to create round holes in the workpiece. The drill bit is usually attached to a drill press or vertical milling machine and rotated while being pressed against the workpiece to cut into it.
Proper speeds and feeds must be used based on the material to avoid damage to the workpiece or drill bit. Cutting fluid is often used to cool the drill bit and workpiece and flush away chips during drilling. The size of the finished hole depends on the diameter of the drill bit used.
There are several types of drill bits that are designed for different materials and applications:
- Twist drill bits – Most common type made of high speed steel with a helical flute design to draw up chips. Good for drilling metals. Come in a wide range of diameters.
- Brad point bits – Have a center point to keep the drill bit steady and minimized wandering when starting a hole. Good for drilling wood and soft plastics.
- Masonry bits – Have a carbide tip and are optimized for drilling concrete, brick, and other masonry materials.
- Countersink bits – Have a conical shape to enlarge just the surface of a hole and create a beveled edge.
Key features that impact drilling performance include the material the bit is made from, number of flutes, thickness and width of the lands, point angle, and flute length. Proper drill bit selection and replacement helps achieve good hole quality.
Sawing
Sawing is a machining process that uses a saw blade to cut and remove material from a workpiece. The process involves a toothed cutting tool with edges consisting of a series of sharp teeth that repeatedly cut into the workpiece at a constant rate as the blade moves.
The sawing process can either be carried out by the machine shop itself, or alternatively, material wholesalers may use sawing to cut blocks into the sizes required by their customers before selling them.
Compared to other machining processes like milling, turning and drilling, sawing has some key differences:
- It is typically used for gross removal of material rather than for precision operations. The finish and tolerance is lower.
- The direction of cutting is orthogonal to the blade’s direction of movement, unlike the orthogonal cutting in turning or the rotary cutting in milling.
- No unique cutting tool geometry like in turning or milling. Just the saw blade teeth for repetitive cutting.
- Lower rigidity, precision and control compared to cutting tools used in milling, turning and drilling.
Overall, sawing is ideal for rapidly cutting large, thick workpieces into smaller pieces rather than finishing operations. It is commonly used in operations like slicing metal bars, tubes, blocks into rough cut parts before further precision machining.
Broaching
Broaching is a machining process for removing material by inserting a tool called a broach. The broach contains sharp teeth that each cut away a small amount of material. As the broach is pushed or pulled through the workpiece, the teeth make overlapping cuts to create the desired shape.
Broaching is highly effective for creating precise, complex forms like splines, keyways, and slots. It works on internal or external surfaces, making it a versatile option.
How Broaching Works
The broach contains rows of progressive teeth. Each tooth is slightly larger than the previous one. As the tool advances through the workpiece, the teeth shave away material little by little to form the desired shape. The cut starts out wide and shallow and gets deeper with each tooth.
The broach can be pushed or pulled through the workpiece. Pushing is called direct broaching, while pulling is called pull broaching. The direction depends on the shape being machined.
Lubricant is critical during broaching to flush chips, minimize friction, and prevent the broach from overheating. Too much heat can damage the broach teeth. Proper lubrication allows faster broaching speeds.
Grinding
Grinding is an abrasive machining process that uses a grinding wheel as the cutting tool. The purpose of grinding is to produce very fine finishes and very accurate dimensions on workpieces.
Purpose of Grinding
The primary purpose of grinding is to remove material and achieve the desired geometry, size, and surface finish on workpieces. It is capable of producing extremely fine finishes below 1 micron and grinding tolerances below 0.001mm. Unlike many other machining processes, grinding can often achieve perfect geometric shapes and dimensions. The flexibility of grinding allows grinding wheels to be shaped to produce complex forms.
Grinding is commonly used when a hardened material is difficult to machine with traditional methods. It can achieve the desired tolerances and surface finishes that are beyond the capabilities of other machining techniques. Grinding generates minimal heat which prevents workpiece damage. It also requires rigid holding of the workpiece because of the high grinding forces needed.
Types of Grinding Machines
There are several types of grinding machines used for different purposes:
- Surface grinders are used for grinding flat surfaces. The workpiece is held on a table that moves back and forth under the grinding wheel.
- Cylindrical grinders are used for external cylindrical grinding and internal cylindrical grinding. The workpiece rotates between fixed or rotating centers as the grinding wheel reciprocates along its axis.
- Centerless grinders use the principle of through-feed grinding where the workpiece is held between two grinding wheels and supported by a work rest blade. The speed ratio between the grinding wheel and workpiece provides the grinding action.
- Tool and cutter grinders are designed for sharpening cutting tools like milling cutters, drills, reamers, and broaches. The grinding head typically swivels to bring the wheel into contact with the tool to grind the cutting edges.
Electrical Discharge Machining
Electrical discharge machining (EDM) is a manufacturing process that uses electrical discharges to erode material and form shapes. There are two main types of EDM:
In die-sinking EDM, the electrode tool is shaped to form the desired cavity by being plunged into the workpiece. With wire EDM, a thin wire electrode follows a programmed path to slice through the workpiece, enabling intricate contours to be cut without contact.
How EDM Works
EDM works by creating an electric spark between an electrode tool and the workpiece to melt and vaporize material from the workpiece. The electrode and workpiece are submerged in an insulating liquid, usually oil or deionized water. As the electrode approaches the workpiece, voltage builds until it discharges a spark across the small gap between the electrode and workpiece. This quickly melts a small amount of material from the workpiece which forms debris that is washed away by the liquid. Thousands of sparks occur per second, enabling EDM to quickly and accurately machine parts and cavities without physical contact between tool and workpiece. The electrode is guided by CNC to achieve the desired final shape.
Advantages of EDM
- Extremely hard electrically conductive materials can be machined, including hardened tool steels, carbides, titanium alloys, and heat treated metals. These would be difficult or impossible to machine with traditional cutting tools.
- Very complex and intricate shapes can be produced using sinking or wire EDM that would otherwise require multiple machining processes.
- No cutting forces or mechanical stresses are exerted on the workpiece since no contact is made. This enables machining of fragile and slender parts.
- Burr-free machining with no need for post-processing or de-burring.
- No tool wear from EDM eliminates tool changes and reduces costs.
The unique EDM process fills a useful niche for mold production, toolmaking, prototype parts and micromachining applications.
Conclusion
Machining processes involve removing material from a workpiece to achieve a desired shape and finish. This was an overview of the most common types of machining processes used in manufacturing.
Each machining process has its strengths and limitations. Selecting the right process requires considering factors like precision, surface finish, speed, cost effectiveness, and more. Improvements in machine tool technology, cutting tools, automation, and computer numerical control systems continue to advance machining capabilities.
The future outlook for machining points towards more automation, as well as hybrid processes that combine additive and subtractive techniques. Machining will remain critical for high-precision parts, but additive manufacturing allows more design freedom. As advanced materials like composites and ceramics become more prevalent, machining processes will evolve to effectively work these hard-to-machine materials. Overall, machining will continue to be an essential part of manufacturing into the future.
What is machining?
Machining processes are manufacturing processes that use machine tools and cutting tools to physically remove material from a raw workpiece to reach a desired final shape and size. Machining is one of the most common and versatile manufacturing processes used across industries like automotive, aerospace, medical devices, tool and die making, and more.
Some of the most common machining processes include:
- Milling – Employs rotary cutters to remove material from a workpiece along various axes.
- Turning – Utilizes a single point tool to eliminate material as the workpiece rotates.
- Drilling – Creates cylindrical holes in the workpiece using drill bits.
- Sawing – Cuts off pieces of the raw material with a saw blade.
- Grinding – Removes fine amounts of material for high precision by employing an abrasive wheel.
- Broaching – Shapes internal or external keyways and gears using a specialized toothed tool.
- Electrical Discharge Machining (EDM) – Uses electrical sparks to erode conductive materials into the desired shape.
These and some other major machining processes will be explored in more detail throughout this article. Proper selection and application of the right machining process is key to producing quality components efficiently.
CNC machine tools are widely used as equipment for carrying out these processes. There are various types of machine tools, such as milling machines that primarily perform milling operations, lathes or turning machines that mainly carry out turning processes, and mill-turn machines or multi-tasking machines that can handle both milling and turning in a single unit.
Milling
Milling is a machining process that involves the use of a milling machine to remove material from a workpiece via the movement of a rotating cutter. The milling cutter rotates at high speeds and has cutting teeth along its edges that shear away material as the cutter feeds into the stationary workpiece.
Milling machines come in two main configurations – horizontal and vertical. On a horizontal milling machine, the cutters are mounted on an horizontally oriented spindle that can selectively advance into the stationary workpiece. On a vertical milling machine, the cutters are mounted on a vertically oriented spindle that can selectively advance downward into a fixed workpiece. Both configurations allow for precise control of the cutting depth.
Also, they come in 3-axis, 4-axis, and 5-axis configurations. 3-axis machines can move the tool along the X, Y, and Z axes. 4-axis machines add a rotary axis (A or B), while 5-axis machines incorporate two rotary axes (A/B and C), enabling the tool to approach the workpiece from various angles, facilitating complex contours and reducing setups.
3-axis milling machines are the most widely used and are employed for machining many types of parts. On the other hand, 4-axis and 5-axis milling machines enable the machining of more complex shapes and reduce the number of setups required, making them valuable in industries demanding advanced machining, such as aerospace and mold manufacturing. However, 4-axis and 5-axis milling machines tend to have higher equipment costs due to their more complex mechanisms.
The most common types of milling operations include:
- Face milling – machining flat surfaces into the workpiece.
- End milling – machining slots, grooves, pockets and keyways into the workpiece.
- Profile milling – machining complex three-dimensional contours into the workpiece. This relies on using a shaped cutter or moving the workpiece relative to the cutter.
- Helical milling – producing grooves and ridges using a cylindrical cutter fed at an angle to the workpiece axis.
Turning
Turning is a machining process used to create cylindrical parts by rotating a workpiece while a cutting tool is moved along its axis to cut away material. This process can create precise cylindrical shapes and produce a high-quality surface finish.
Turning operations are performed on a lathe, which holds the workpiece firmly while it rotates at high speeds. The cutting tool is fed slowly into the workpiece, removing material uniformly around the outside diameter of the part being machined. Common types of lathes used for turning operations include:
- Engine lathes – Used for precision turning of small, medium and large diameter pieces. The bed can be horizontal or vertical.
- Turret lathes – Have multiple cutting tools mounted on a turret that allows for automatic indexed operations. Good for high production.
- CNC lathes – Computer numerically controlled lathes can precisely control movement and cutting parameters. Ideal for complex parts.
The main types of turning processes include straight turning, taper turning, profiling or contour turning, grooving, and boring. Turning can produce cylindrical shapes, cones, spherical sections and concave or convex contours. The material is fed into the lathe with a longitudinal motion along the axis of the workpiece.
Turning is an essential machining process used to create rotational, cylindrical components to extremely tight tolerances and fine surface finishes. It’s ideal for producing parts that have axial symmetry and do not require complex internal geometries.
Drilling
Drilling is a machining process that uses a drill bit to create round holes in the workpiece. The drill bit is usually attached to a drill press or vertical milling machine and rotated while being pressed against the workpiece to cut into it.
Proper speeds and feeds must be used based on the material to avoid damage to the workpiece or drill bit. Cutting fluid is often used to cool the drill bit and workpiece and flush away chips during drilling. The size of the finished hole depends on the diameter of the drill bit used.
There are several types of drill bits that are designed for different materials and applications:
- Twist drill bits – Most common type made of high speed steel with a helical flute design to draw up chips. Good for drilling metals. Come in a wide range of diameters.
- Brad point bits – Have a center point to keep the drill bit steady and minimized wandering when starting a hole. Good for drilling wood and soft plastics.
- Masonry bits – Have a carbide tip and are optimized for drilling concrete, brick, and other masonry materials.
- Countersink bits – Have a conical shape to enlarge just the surface of a hole and create a beveled edge.
Key features that impact drilling performance include the material the bit is made from, number of flutes, thickness and width of the lands, point angle, and flute length. Proper drill bit selection and replacement helps achieve good hole quality.
Sawing
Sawing is a machining process that uses a saw blade to cut and remove material from a workpiece. The process involves a toothed cutting tool with edges consisting of a series of sharp teeth that repeatedly cut into the workpiece at a constant rate as the blade moves.
The sawing process can either be carried out by the machine shop itself, or alternatively, material wholesalers may use sawing to cut blocks into the sizes required by their customers before selling them.
Compared to other machining processes like milling, turning and drilling, sawing has some key differences:
- It is typically used for gross removal of material rather than for precision operations. The finish and tolerance is lower.
- The direction of cutting is orthogonal to the blade’s direction of movement, unlike the orthogonal cutting in turning or the rotary cutting in milling.
- No unique cutting tool geometry like in turning or milling. Just the saw blade teeth for repetitive cutting.
- Lower rigidity, precision and control compared to cutting tools used in milling, turning and drilling.
Overall, sawing is ideal for rapidly cutting large, thick workpieces into smaller pieces rather than finishing operations. It is commonly used in operations like slicing metal bars, tubes, blocks into rough cut parts before further precision machining.
Broaching
Broaching is a machining process for removing material by inserting a tool called a broach. The broach contains sharp teeth that each cut away a small amount of material. As the broach is pushed or pulled through the workpiece, the teeth make overlapping cuts to create the desired shape.
Broaching is highly effective for creating precise, complex forms like splines, keyways, and slots. It works on internal or external surfaces, making it a versatile option.
How Broaching Works
The broach contains rows of progressive teeth. Each tooth is slightly larger than the previous one. As the tool advances through the workpiece, the teeth shave away material little by little to form the desired shape. The cut starts out wide and shallow and gets deeper with each tooth.
The broach can be pushed or pulled through the workpiece. Pushing is called direct broaching, while pulling is called pull broaching. The direction depends on the shape being machined.
Lubricant is critical during broaching to flush chips, minimize friction, and prevent the broach from overheating. Too much heat can damage the broach teeth. Proper lubrication allows faster broaching speeds.
Grinding
Grinding is an abrasive machining process that uses a grinding wheel as the cutting tool. The purpose of grinding is to produce very fine finishes and very accurate dimensions on workpieces.
Purpose of Grinding
The primary purpose of grinding is to remove material and achieve the desired geometry, size, and surface finish on workpieces. It is capable of producing extremely fine finishes below 1 micron and grinding tolerances below 0.001mm. Unlike many other machining processes, grinding can often achieve perfect geometric shapes and dimensions. The flexibility of grinding allows grinding wheels to be shaped to produce complex forms.
Grinding is commonly used when a hardened material is difficult to machine with traditional methods. It can achieve the desired tolerances and surface finishes that are beyond the capabilities of other machining techniques. Grinding generates minimal heat which prevents workpiece damage. It also requires rigid holding of the workpiece because of the high grinding forces needed.
Types of Grinding Machines
There are several types of grinding machines used for different purposes:
- Surface grinders are used for grinding flat surfaces. The workpiece is held on a table that moves back and forth under the grinding wheel.
- Cylindrical grinders are used for external cylindrical grinding and internal cylindrical grinding. The workpiece rotates between fixed or rotating centers as the grinding wheel reciprocates along its axis.
- Centerless grinders use the principle of through-feed grinding where the workpiece is held between two grinding wheels and supported by a work rest blade. The speed ratio between the grinding wheel and workpiece provides the grinding action.
- Tool and cutter grinders are designed for sharpening cutting tools like milling cutters, drills, reamers, and broaches. The grinding head typically swivels to bring the wheel into contact with the tool to grind the cutting edges.
Electrical Discharge Machining
Electrical discharge machining (EDM) is a manufacturing process that uses electrical discharges to erode material and form shapes. There are two main types of EDM:
In die-sinking EDM, the electrode tool is shaped to form the desired cavity by being plunged into the workpiece. With wire EDM, a thin wire electrode follows a programmed path to slice through the workpiece, enabling intricate contours to be cut without contact.
How EDM Works
EDM works by creating an electric spark between an electrode tool and the workpiece to melt and vaporize material from the workpiece. The electrode and workpiece are submerged in an insulating liquid, usually oil or deionized water. As the electrode approaches the workpiece, voltage builds until it discharges a spark across the small gap between the electrode and workpiece. This quickly melts a small amount of material from the workpiece which forms debris that is washed away by the liquid. Thousands of sparks occur per second, enabling EDM to quickly and accurately machine parts and cavities without physical contact between tool and workpiece. The electrode is guided by CNC to achieve the desired final shape.
Advantages of EDM
- Extremely hard electrically conductive materials can be machined, including hardened tool steels, carbides, titanium alloys, and heat treated metals. These would be difficult or impossible to machine with traditional cutting tools.
- Very complex and intricate shapes can be produced using sinking or wire EDM that would otherwise require multiple machining processes.
- No cutting forces or mechanical stresses are exerted on the workpiece since no contact is made. This enables machining of fragile and slender parts.
- Burr-free machining with no need for post-processing or de-burring.
- No tool wear from EDM eliminates tool changes and reduces costs.
The unique EDM process fills a useful niche for mold production, toolmaking, prototype parts and micromachining applications.
Conclusion
Machining processes involve removing material from a workpiece to achieve a desired shape and finish. This was an overview of the most common types of machining processes used in manufacturing.
Each machining process has its strengths and limitations. Selecting the right process requires considering factors like precision, surface finish, speed, cost effectiveness, and more. Improvements in machine tool technology, cutting tools, automation, and computer numerical control systems continue to advance machining capabilities.
The future outlook for machining points towards more automation, as well as hybrid processes that combine additive and subtractive techniques. Machining will remain critical for high-precision parts, but additive manufacturing allows more design freedom. As advanced materials like composites and ceramics become more prevalent, machining processes will evolve to effectively work these hard-to-machine materials. Overall, machining will continue to be an essential part of manufacturing into the future.
Ready to see CADDi Drawer in action? Get a personalized demo.
Subscribe to our Blog!
Related Resources
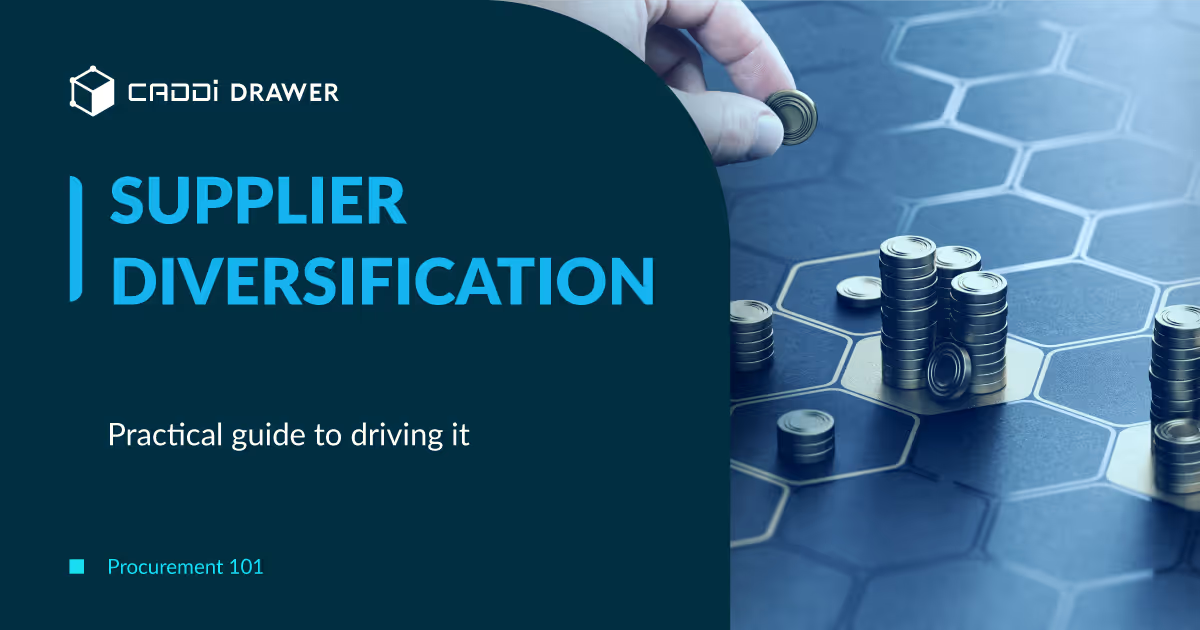
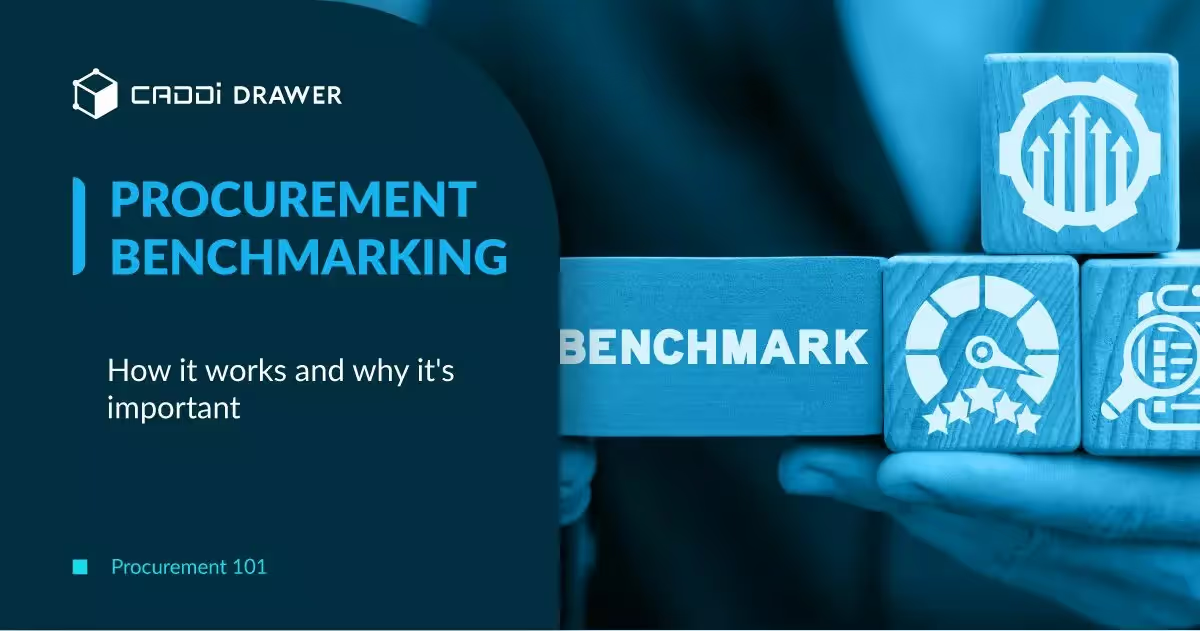
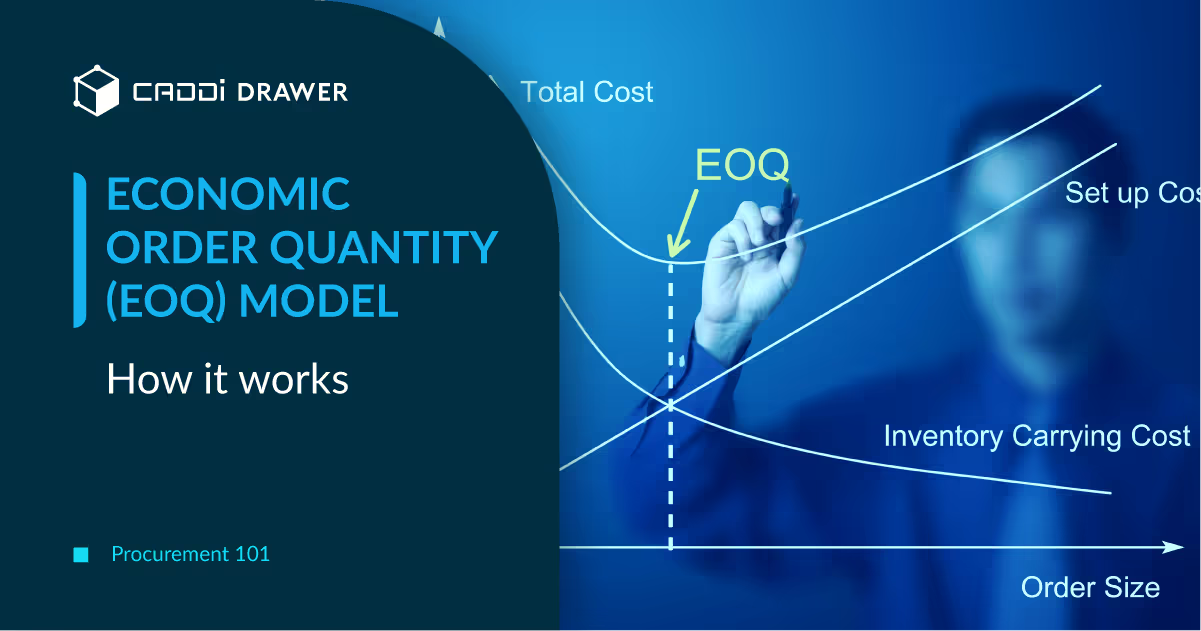
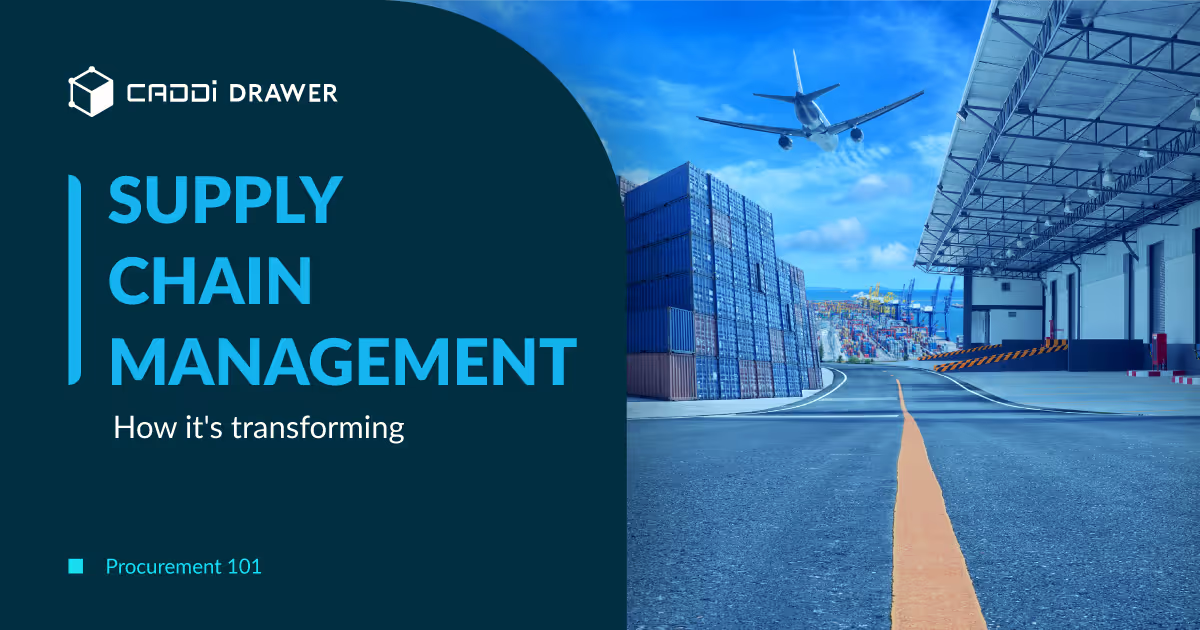
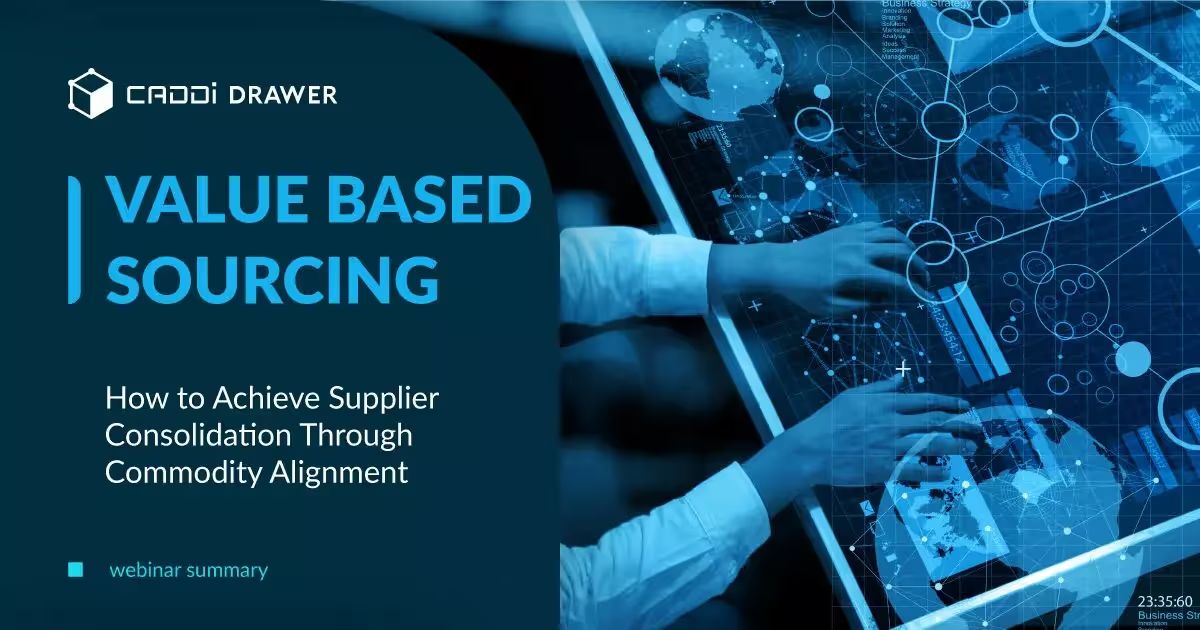
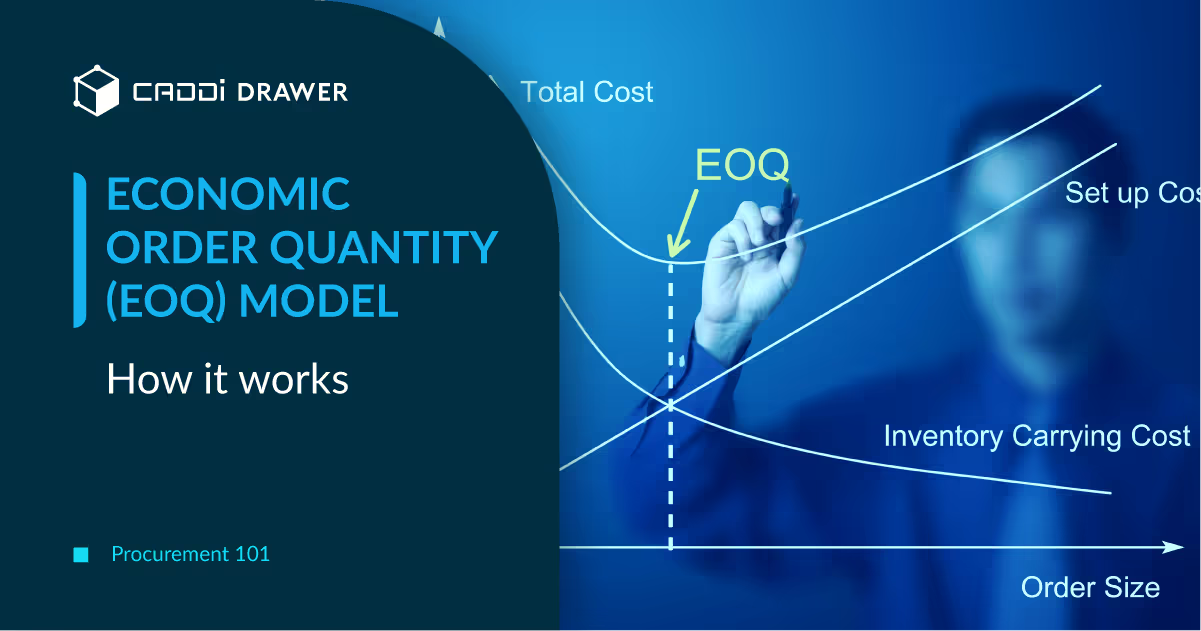