Procurement 101: Manufacturing Document Management – Why it matters and how to excel
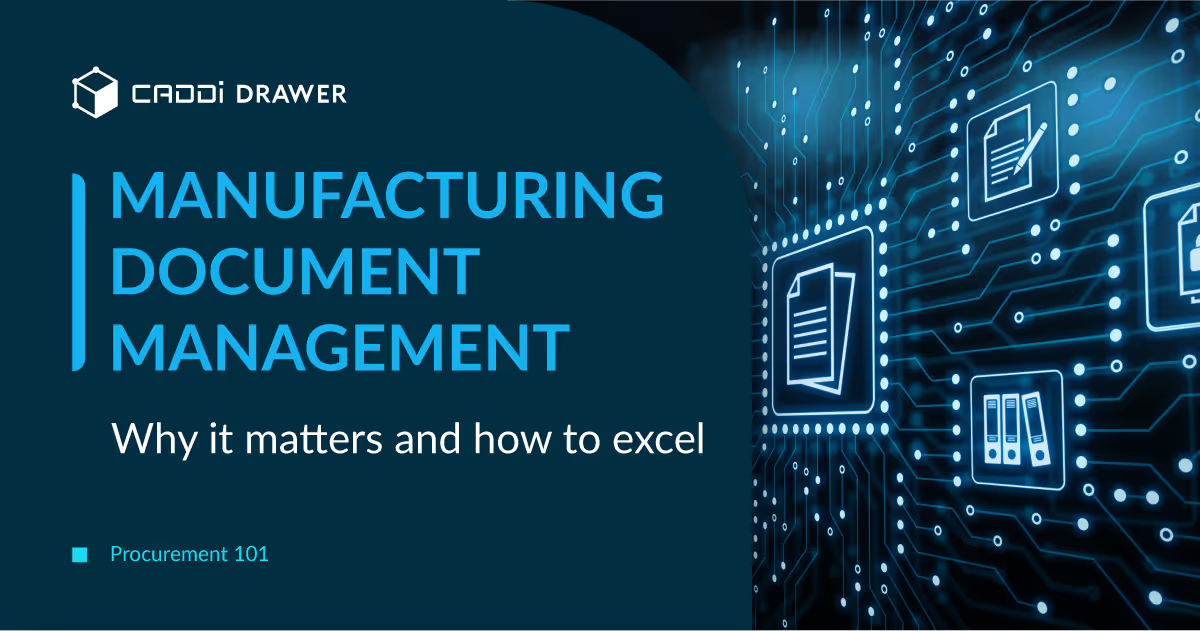
Table of Contents
The urgency for manufacturers to adopt an effective document management system is further highlighted by the findings of a PwC survey, which revealed that nearly 40% of manufacturing companies faced challenges in information mismanagement that directly impacted their operational efficiency and compliance postures. This statistic not only sheds light on the prevalence of the issue but also on the vast potential for improvement and growth that lies in addressing it.
Why Manufacturing Document Management Matters
Without effective document management methods, manufacturers, regardless of size, face numerous risks. Consequences include lost documents leading to production delays, non-compliance with regulations resulting in fines or legal issues, inefficiency due to time wasted searching for documents and lack of knowledge sharing, and compromised performance in cost and quality.
Did inadequate document management lead to:
- Misalignment with suppliers and stakeholders,
- Unforeseen issues arising later,
- Significant time spent searching for specific documents,
- Substantial rework or production errors,
- Challenges in onboarding new team members,
and similar occurrences?
These challenges can severely impact the bottom line, hamper growth, and even jeopardize the survival of the business. Effective document management is crucial for avoiding such pitfalls, enabling even smaller manufacturers to compete more effectively in the market by improving operational efficiency and compliance.
Consider, for instance, the aerospace sector, where Boeing reported a staggering $25 billion in deferred production costs due to documentation and production inefficiencies with its 787 Dreamliner. On the flip side, Airbus’s adoption of a unified document management system streamlined its operations across 150 sites, leading to a significant reduction in production delays and a more agile response to market demands. These examples underscore the tangible impact of robust document management on a company’s bottom line and its ability to meet stringent regulatory standards.
The competitiveness gap stemming from such document management issues is not exclusive to mega-corporations like Boeing or Airbus. It’s a phenomenon widely observed across the entire manufacturing industry, from industry leaders to SMBs.
Types of Documents Manufacturers Need to Manage
Here’s an overview of specific types of documents that should be managed effectively
- Product Design and Engineering Documents: This includes all documents related to product design, engineering drawings, specifications, and blueprints. Managing these documents effectively ensures that all stakeholders have access to the most current and accurate design information.
- Bill of Materials (BOM): The BOM is a comprehensive list of materials, components, and assemblies needed to manufacture a product. It must be meticulously managed to ensure accurate procurement, inventory management, and cost estimation.
- Quality Control Documents: These documents include quality manuals, standard operating procedures (SOPs), inspection reports, and test results. They are essential for maintaining compliance with quality standards and regulatory requirements.
- Compliance and Certification Documents: For manufacturers, compliance with industry standards and regulations is non-negotiable. This requires the management of certification documents, compliance reports, and audit findings.
- Production Scheduling and Control Documents: Effective production planning and control rely on the management of production schedules, work orders, and production reports to ensure timely and efficient manufacturing processes.
- Safety and Training Manuals: Safety manuals and training documents are critical for ensuring a safe working environment and for complying with occupational health and safety regulations.
- Procurement and Supplier Documents: This category includes purchase orders, supplier contracts, and supplier quality assessments. Proper management of these documents is vital for streamlining the procurement process and maintaining strong supplier relationships.
- Inventory Documents: Inventory records, stock levels, and warehouse management documents are crucial for optimizing inventory control and reducing carrying costs.
- Shipping and Receiving Documents: Shipping labels, packing lists, and receiving reports must be managed to ensure accuracy in order fulfillment and inventory management.
- Maintenance Records: For manufacturing equipment, maintaining a log of maintenance schedules, service reports, and repair records is essential for minimizing downtime and extending the lifespan of the machinery.
- Customer Orders and Feedback: Managing customer purchase orders, feedback, and service records is essential for ensuring customer satisfaction and for driving improvements in product quality and service delivery.
- Project Management Documents: In the context of plant engineering and large manufacturing projects, document controllers play a critical role in managing project plans, progress reports, and stakeholder communications.
Key Operations in Manufacturing Document Management
There are multiple operations critical for ensuring the system’s effectiveness and efficiency. These operations encompass a range of activities designed to manage documents through their lifecycle, from creation to disposal. Here’s an overview of the essential operations required in manufacturing document management:
- Document Creation and Capture: This involves generating new documents and capturing external documents. It can include the use of templates for consistency and scanning or digitizing paper documents to bring them into the digital document management system.
- Indexing and Classification: Once documents are created or captured, they need to be indexed and classified according to a predefined taxonomy. This step is crucial for organizing documents in a manner that makes them easily retrievable.
- Storage and Preservation: Secure storage of documents, whether digital or physical, is essential. This operation includes ensuring that digital documents are saved in formats that are not prone to obsolescence and that physical documents are stored in conditions that prevent deterioration.
- Access Control: Defining who has access to what documents is a critical operation. This includes setting permissions based on roles within the organization to ensure that sensitive information is only accessible to authorized personnel.
- Version Control: In manufacturing, where revisions to documents such as design drawings, specifications, and SOPs are common, maintaining version control is essential. This operation ensures that everyone is working from the most current version of a document.
- Review and Approval Processes: Many documents, especially those related to quality control and compliance, require formal review and approval before they become official. Setting up workflows that manage these processes is a vital operation.
- Distribution and Sharing: Documents often need to be shared both internally among team members and externally with suppliers, customers, or regulatory bodies. Efficient distribution mechanisms and sharing protocols are essential operations to ensure that information flows smoothly and securely.
- Retrieval and Search: The ability to quickly find and retrieve documents is one of the primary benefits of a document management system. Operations must ensure that search functionality is robust, using metadata, tags, and full-text search capabilities.
- Archiving and Disposal: Over time, some documents may no longer be active but still need to be retained for historical reference or regulatory compliance. Archiving operations ensure these documents are stored securely but are still accessible if needed. Conversely, the disposal operation involves securely destroying or deleting documents that are no longer needed and have no legal or historical value.
- Compliance Management: Ensuring that document management practices comply with industry regulations and standards is a continuous operation. This includes managing records retention schedules, audit trails, and compliance reporting.
- Disaster Recovery: Planning for the unexpected, such as natural disasters or data breaches, involves establishing and maintaining disaster recovery operations. This ensures that documents are protected and can be recovered to maintain business continuity.
Each of these operations requires careful planning, execution, and ongoing management to ensure that the manufacturing document management supports the organization’s goals for efficiency, compliance, and quality management.
The Need for Document Management Specialists
In the plant engineering industry, it’s quite typical to hire document controllers who play a pivotal role in project management, ensuring that all documentation is accurate, up-to-date, and accessible.
This kind of role is equally critical in the manufacturing sector, where document management specialists ensure the smooth flow of information, maintain compliance with industry standards and regulations, and support the decision-making process. They are instrumental in implementing and maintaining document management systems, training staff, and ensuring that document-related practices align with organizational goals and industry best practices.
Document management specialists certainly perform the aforementioned document management operations themselves. However, it is impossible for them alone to manage the vast amount and variety of documents at every step.
What’s more important is to establish a mechanism that ensures proper document management is carried out throughout the organization, even without their direct involvement. This is where the true skill of document management specialists can be said to shine.
Implementing a Manufacturing Document Management System: Steps to Success
This is where a document management system (DMS) becomes essential. Implementing a DMS is a strategic move that requires careful planning and execution. It’s not just about going paperless; it’s about choosing a system that integrates seamlessly with existing workflows, enhances collaboration, and ensures compliance with industry regulations.
The journey begins with a comprehensive assessment of current document-related processes to identify inefficiencies and areas for improvement. Following this, selecting a DMS that aligns with the organization’s specific needs is crucial.
Training and user adoption are critical to the success of DMS implementation. For instance, Lockheed Martin, a global aerospace, defense, security, and advanced technologies company, attributed its successful DMS implementation to extensive employee training programs and the involvement of end-users in the selection process. This approach not only facilitated a smoother transition to the new system but also ensured that the DMS was utilized to its full potential across the organization.
Ongoing evaluation and improvement are the final steps in the journey. Continuous monitoring of the DMS’s performance against predefined metrics allows for timely adjustments and optimizations. Regular feedback from users further informs the evolution of the system, ensuring it remains responsive to the changing needs of the business.
Improving Procurement Processes through Document Management
The procurement process in manufacturing is a complex orchestration of selecting suppliers, managing purchase orders, and processing invoices. Effective document management plays a critical role in optimizing these operations, leading to significant cost savings and enhanced supplier relationships.
For example, Siemens AG implemented a digital document management solution that streamlined its procurement workflow, resulting in a 20% reduction in procurement cycle times and a substantial improvement in supplier collaboration. The system allowed for real-time tracking of documents, automated approval processes, and centralized storage, which not only expedited procurement operations but also enhanced transparency and accountability.
How CADDi Drawer Can Help in Document Management
CADDi Drawer is one of the systems that can significantly enhance document management, offering unique value propositions distinct from typical document management specialist tools.
Transforms documents and drawings into searchable info
CADDi Drawer transforms documents and drawings into searchable information by automatically and comprehensively reading text across them. Its OCR is applicable not only to drawings but also to general documents and spec sheets. This feature enables the consolidated management and cross-sectional search of drawings and other documents together, without the need to separate them. There’s no longer a need to search through various systems or folders.
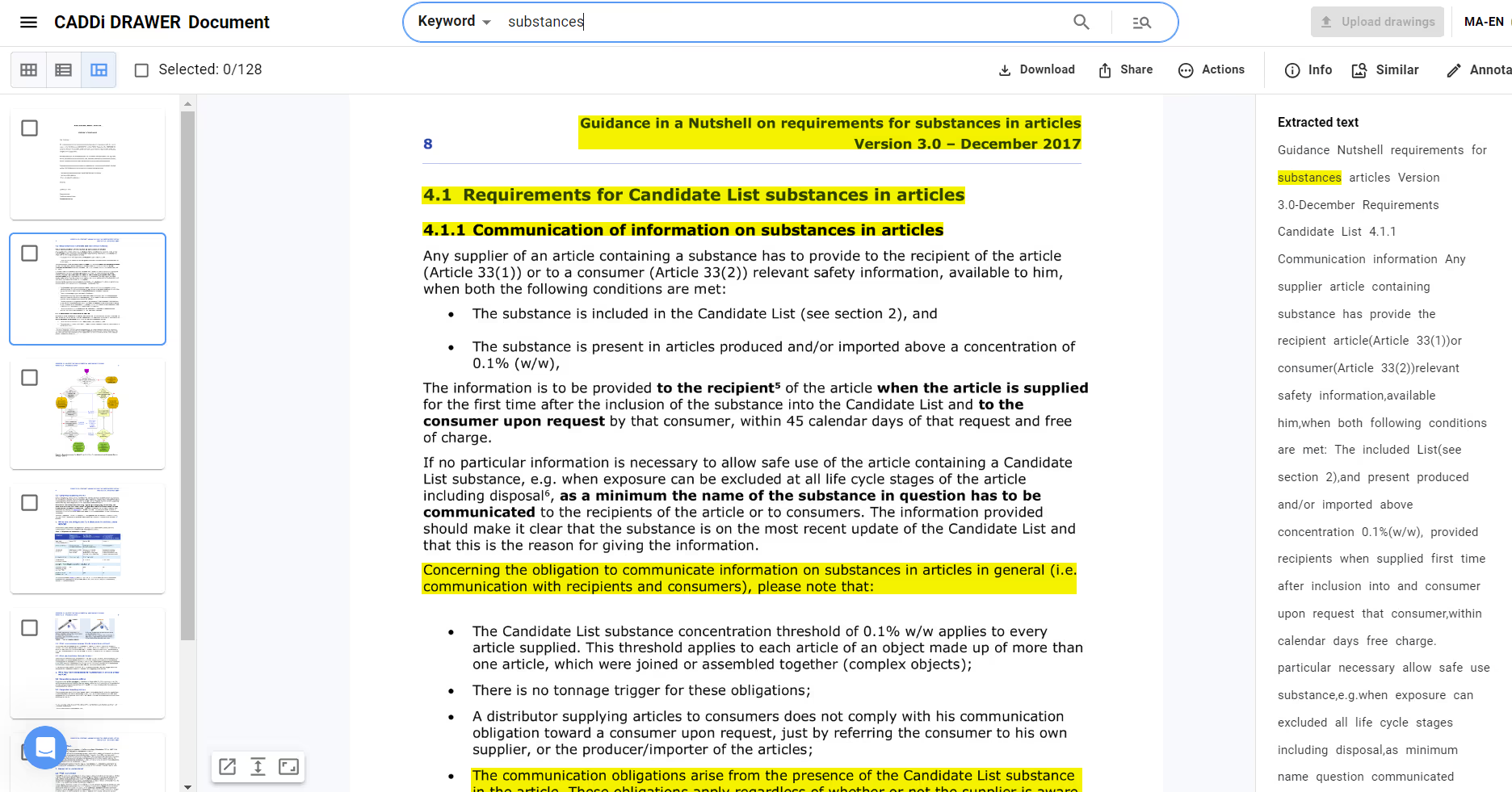
Streamline activities in the procurement process
The following features enable you to streamline the time-consuming tasks of data collection and document organization in procurement operations.
- Price data, supplier information and relevant documents such as specification documents, quality reports and work instructions can be automatically linked to each drawing and can also be exported together.
- By using keyword searches combined with similarity searches, the time spent searching for drawings, data and documents in procurement tasks can be reduced.
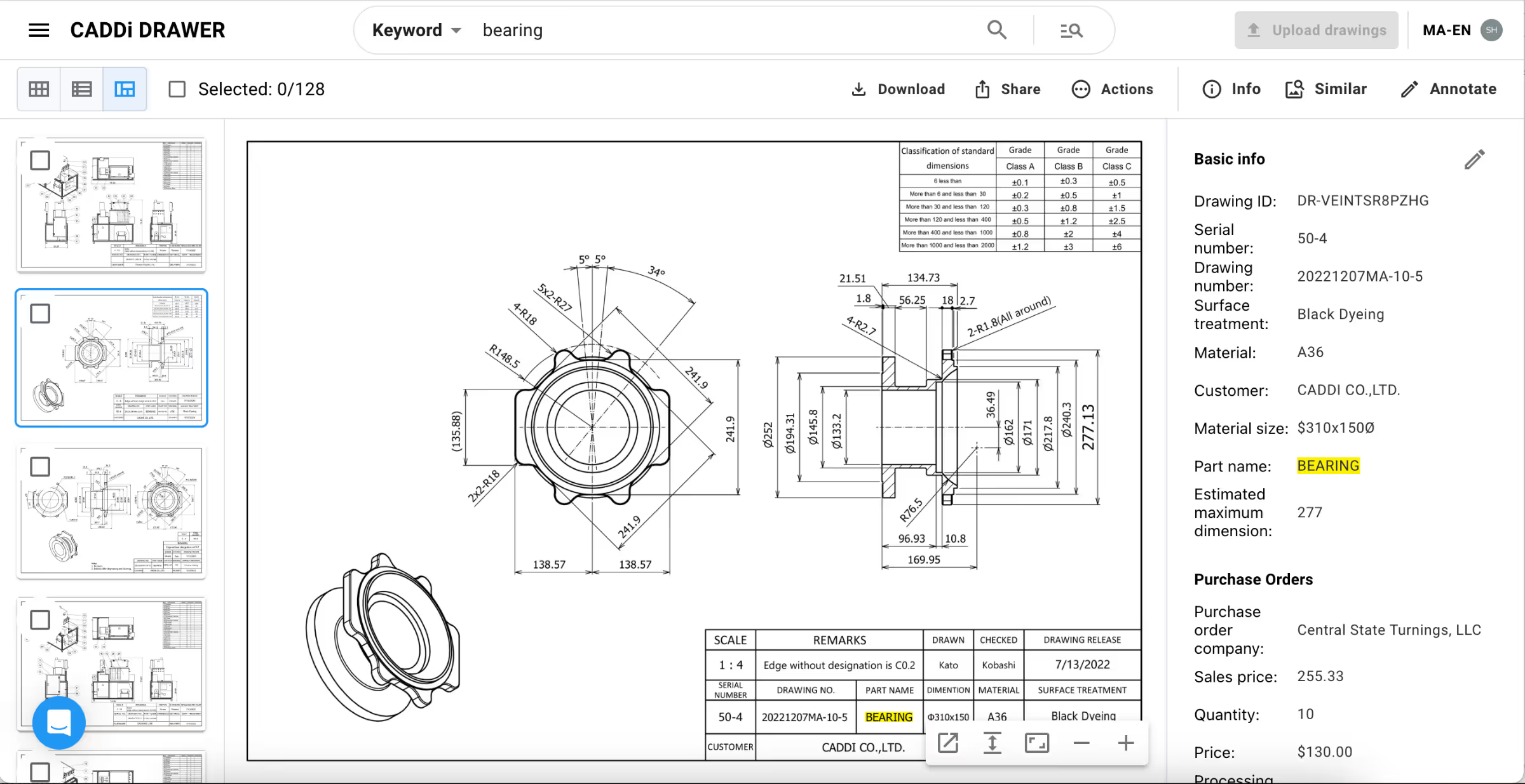
The urgency for manufacturers to adopt an effective document management system is further highlighted by the findings of a PwC survey, which revealed that nearly 40% of manufacturing companies faced challenges in information mismanagement that directly impacted their operational efficiency and compliance postures. This statistic not only sheds light on the prevalence of the issue but also on the vast potential for improvement and growth that lies in addressing it.
Why Manufacturing Document Management Matters
Without effective document management methods, manufacturers, regardless of size, face numerous risks. Consequences include lost documents leading to production delays, non-compliance with regulations resulting in fines or legal issues, inefficiency due to time wasted searching for documents and lack of knowledge sharing, and compromised performance in cost and quality.
Did inadequate document management lead to:
- Misalignment with suppliers and stakeholders,
- Unforeseen issues arising later,
- Significant time spent searching for specific documents,
- Substantial rework or production errors,
- Challenges in onboarding new team members,
and similar occurrences?
These challenges can severely impact the bottom line, hamper growth, and even jeopardize the survival of the business. Effective document management is crucial for avoiding such pitfalls, enabling even smaller manufacturers to compete more effectively in the market by improving operational efficiency and compliance.
Consider, for instance, the aerospace sector, where Boeing reported a staggering $25 billion in deferred production costs due to documentation and production inefficiencies with its 787 Dreamliner. On the flip side, Airbus’s adoption of a unified document management system streamlined its operations across 150 sites, leading to a significant reduction in production delays and a more agile response to market demands. These examples underscore the tangible impact of robust document management on a company’s bottom line and its ability to meet stringent regulatory standards.
The competitiveness gap stemming from such document management issues is not exclusive to mega-corporations like Boeing or Airbus. It’s a phenomenon widely observed across the entire manufacturing industry, from industry leaders to SMBs.
Types of Documents Manufacturers Need to Manage
Here’s an overview of specific types of documents that should be managed effectively
- Product Design and Engineering Documents: This includes all documents related to product design, engineering drawings, specifications, and blueprints. Managing these documents effectively ensures that all stakeholders have access to the most current and accurate design information.
- Bill of Materials (BOM): The BOM is a comprehensive list of materials, components, and assemblies needed to manufacture a product. It must be meticulously managed to ensure accurate procurement, inventory management, and cost estimation.
- Quality Control Documents: These documents include quality manuals, standard operating procedures (SOPs), inspection reports, and test results. They are essential for maintaining compliance with quality standards and regulatory requirements.
- Compliance and Certification Documents: For manufacturers, compliance with industry standards and regulations is non-negotiable. This requires the management of certification documents, compliance reports, and audit findings.
- Production Scheduling and Control Documents: Effective production planning and control rely on the management of production schedules, work orders, and production reports to ensure timely and efficient manufacturing processes.
- Safety and Training Manuals: Safety manuals and training documents are critical for ensuring a safe working environment and for complying with occupational health and safety regulations.
- Procurement and Supplier Documents: This category includes purchase orders, supplier contracts, and supplier quality assessments. Proper management of these documents is vital for streamlining the procurement process and maintaining strong supplier relationships.
- Inventory Documents: Inventory records, stock levels, and warehouse management documents are crucial for optimizing inventory control and reducing carrying costs.
- Shipping and Receiving Documents: Shipping labels, packing lists, and receiving reports must be managed to ensure accuracy in order fulfillment and inventory management.
- Maintenance Records: For manufacturing equipment, maintaining a log of maintenance schedules, service reports, and repair records is essential for minimizing downtime and extending the lifespan of the machinery.
- Customer Orders and Feedback: Managing customer purchase orders, feedback, and service records is essential for ensuring customer satisfaction and for driving improvements in product quality and service delivery.
- Project Management Documents: In the context of plant engineering and large manufacturing projects, document controllers play a critical role in managing project plans, progress reports, and stakeholder communications.
Key Operations in Manufacturing Document Management
There are multiple operations critical for ensuring the system’s effectiveness and efficiency. These operations encompass a range of activities designed to manage documents through their lifecycle, from creation to disposal. Here’s an overview of the essential operations required in manufacturing document management:
- Document Creation and Capture: This involves generating new documents and capturing external documents. It can include the use of templates for consistency and scanning or digitizing paper documents to bring them into the digital document management system.
- Indexing and Classification: Once documents are created or captured, they need to be indexed and classified according to a predefined taxonomy. This step is crucial for organizing documents in a manner that makes them easily retrievable.
- Storage and Preservation: Secure storage of documents, whether digital or physical, is essential. This operation includes ensuring that digital documents are saved in formats that are not prone to obsolescence and that physical documents are stored in conditions that prevent deterioration.
- Access Control: Defining who has access to what documents is a critical operation. This includes setting permissions based on roles within the organization to ensure that sensitive information is only accessible to authorized personnel.
- Version Control: In manufacturing, where revisions to documents such as design drawings, specifications, and SOPs are common, maintaining version control is essential. This operation ensures that everyone is working from the most current version of a document.
- Review and Approval Processes: Many documents, especially those related to quality control and compliance, require formal review and approval before they become official. Setting up workflows that manage these processes is a vital operation.
- Distribution and Sharing: Documents often need to be shared both internally among team members and externally with suppliers, customers, or regulatory bodies. Efficient distribution mechanisms and sharing protocols are essential operations to ensure that information flows smoothly and securely.
- Retrieval and Search: The ability to quickly find and retrieve documents is one of the primary benefits of a document management system. Operations must ensure that search functionality is robust, using metadata, tags, and full-text search capabilities.
- Archiving and Disposal: Over time, some documents may no longer be active but still need to be retained for historical reference or regulatory compliance. Archiving operations ensure these documents are stored securely but are still accessible if needed. Conversely, the disposal operation involves securely destroying or deleting documents that are no longer needed and have no legal or historical value.
- Compliance Management: Ensuring that document management practices comply with industry regulations and standards is a continuous operation. This includes managing records retention schedules, audit trails, and compliance reporting.
- Disaster Recovery: Planning for the unexpected, such as natural disasters or data breaches, involves establishing and maintaining disaster recovery operations. This ensures that documents are protected and can be recovered to maintain business continuity.
Each of these operations requires careful planning, execution, and ongoing management to ensure that the manufacturing document management supports the organization’s goals for efficiency, compliance, and quality management.
The Need for Document Management Specialists
In the plant engineering industry, it’s quite typical to hire document controllers who play a pivotal role in project management, ensuring that all documentation is accurate, up-to-date, and accessible.
This kind of role is equally critical in the manufacturing sector, where document management specialists ensure the smooth flow of information, maintain compliance with industry standards and regulations, and support the decision-making process. They are instrumental in implementing and maintaining document management systems, training staff, and ensuring that document-related practices align with organizational goals and industry best practices.
Document management specialists certainly perform the aforementioned document management operations themselves. However, it is impossible for them alone to manage the vast amount and variety of documents at every step.
What’s more important is to establish a mechanism that ensures proper document management is carried out throughout the organization, even without their direct involvement. This is where the true skill of document management specialists can be said to shine.
Implementing a Manufacturing Document Management System: Steps to Success
This is where a document management system (DMS) becomes essential. Implementing a DMS is a strategic move that requires careful planning and execution. It’s not just about going paperless; it’s about choosing a system that integrates seamlessly with existing workflows, enhances collaboration, and ensures compliance with industry regulations.
The journey begins with a comprehensive assessment of current document-related processes to identify inefficiencies and areas for improvement. Following this, selecting a DMS that aligns with the organization’s specific needs is crucial.
Training and user adoption are critical to the success of DMS implementation. For instance, Lockheed Martin, a global aerospace, defense, security, and advanced technologies company, attributed its successful DMS implementation to extensive employee training programs and the involvement of end-users in the selection process. This approach not only facilitated a smoother transition to the new system but also ensured that the DMS was utilized to its full potential across the organization.
Ongoing evaluation and improvement are the final steps in the journey. Continuous monitoring of the DMS’s performance against predefined metrics allows for timely adjustments and optimizations. Regular feedback from users further informs the evolution of the system, ensuring it remains responsive to the changing needs of the business.
Improving Procurement Processes through Document Management
The procurement process in manufacturing is a complex orchestration of selecting suppliers, managing purchase orders, and processing invoices. Effective document management plays a critical role in optimizing these operations, leading to significant cost savings and enhanced supplier relationships.
For example, Siemens AG implemented a digital document management solution that streamlined its procurement workflow, resulting in a 20% reduction in procurement cycle times and a substantial improvement in supplier collaboration. The system allowed for real-time tracking of documents, automated approval processes, and centralized storage, which not only expedited procurement operations but also enhanced transparency and accountability.
How CADDi Drawer Can Help in Document Management
CADDi Drawer is one of the systems that can significantly enhance document management, offering unique value propositions distinct from typical document management specialist tools.
Transforms documents and drawings into searchable info
CADDi Drawer transforms documents and drawings into searchable information by automatically and comprehensively reading text across them. Its OCR is applicable not only to drawings but also to general documents and spec sheets. This feature enables the consolidated management and cross-sectional search of drawings and other documents together, without the need to separate them. There’s no longer a need to search through various systems or folders.
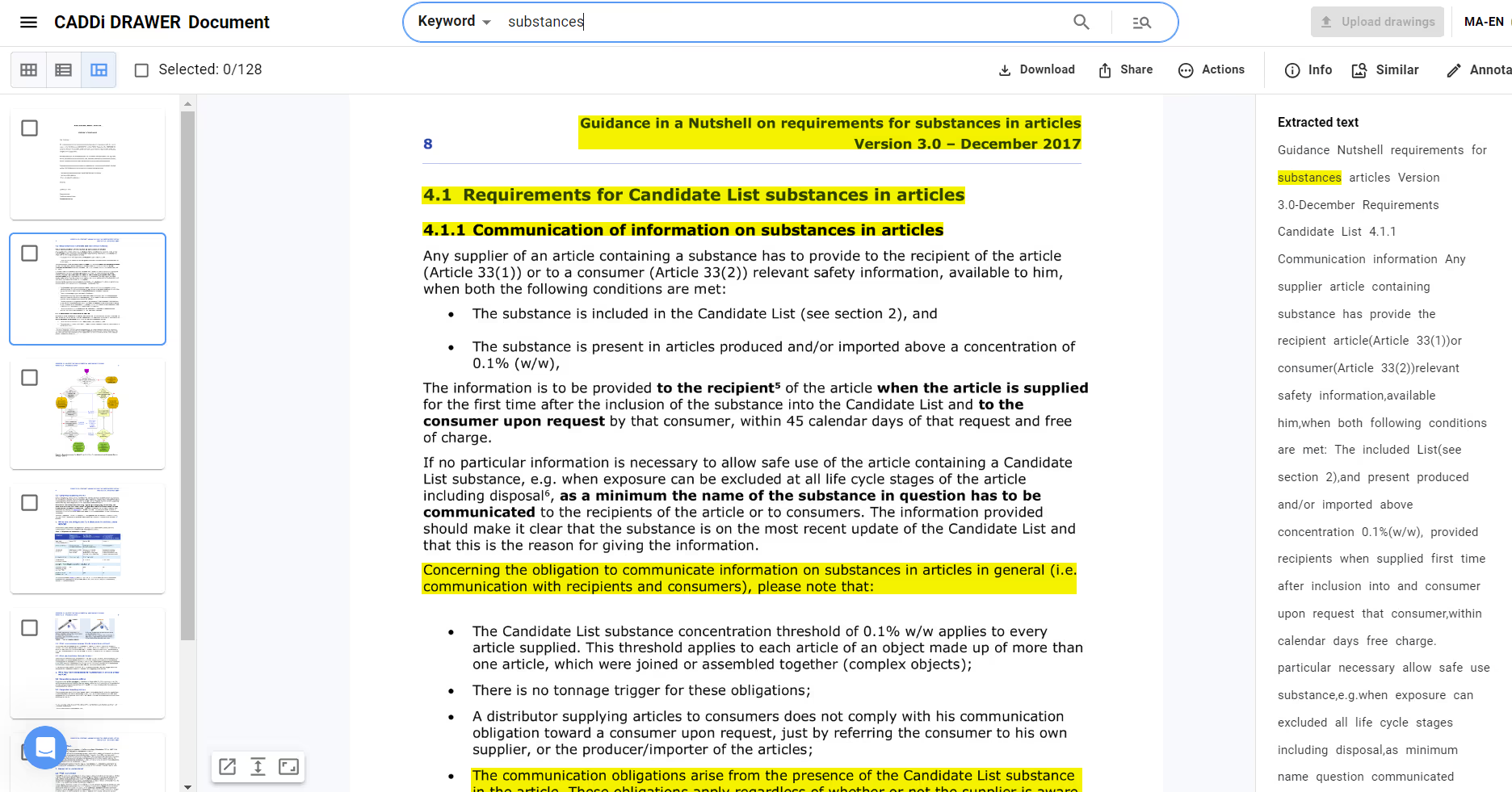
Streamline activities in the procurement process
The following features enable you to streamline the time-consuming tasks of data collection and document organization in procurement operations.
- Price data, supplier information and relevant documents such as specification documents, quality reports and work instructions can be automatically linked to each drawing and can also be exported together.
- By using keyword searches combined with similarity searches, the time spent searching for drawings, data and documents in procurement tasks can be reduced.
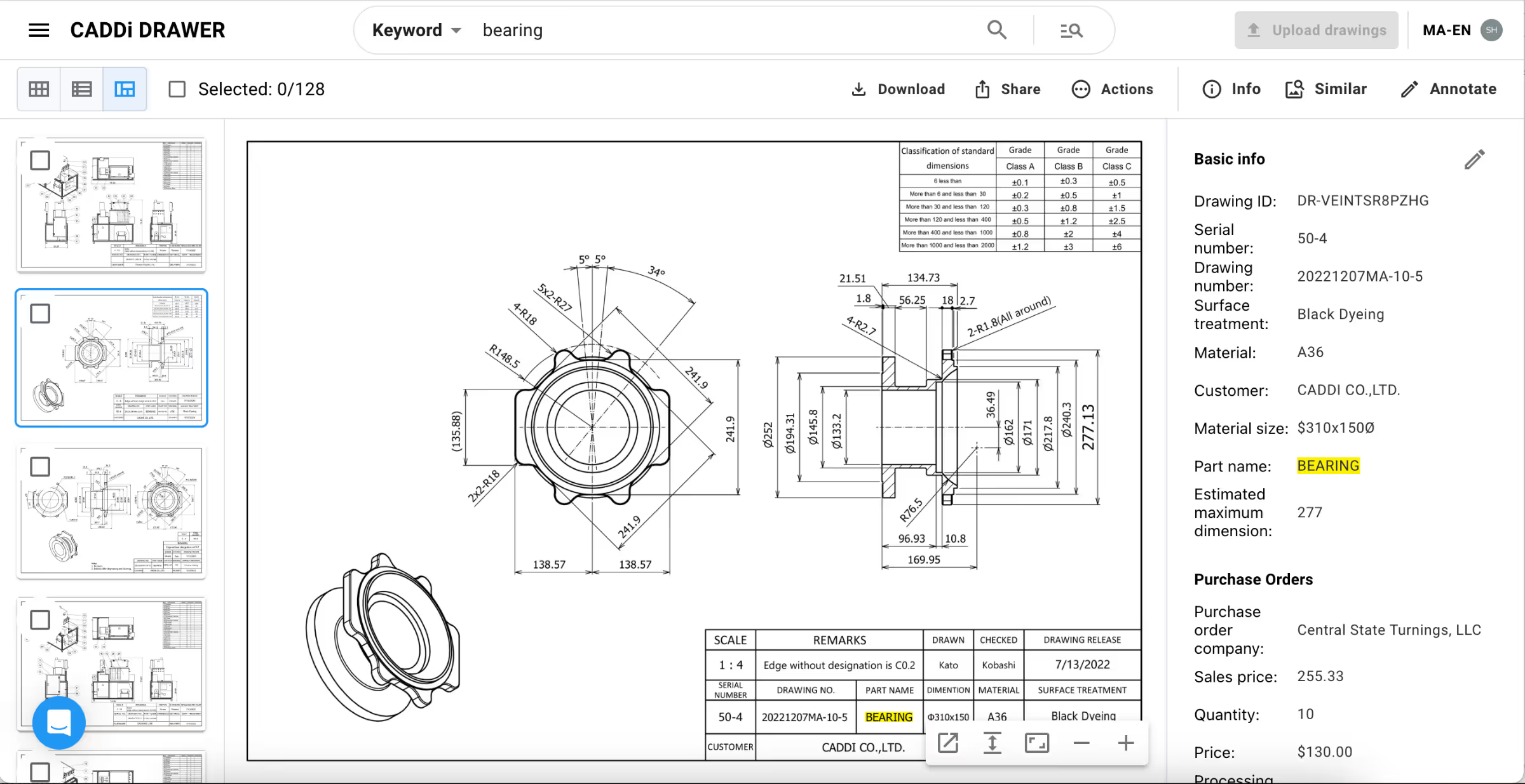
Ready to see CADDi Drawer in action? Get a personalized demo.
Subscribe to our Blog!
Related Resources
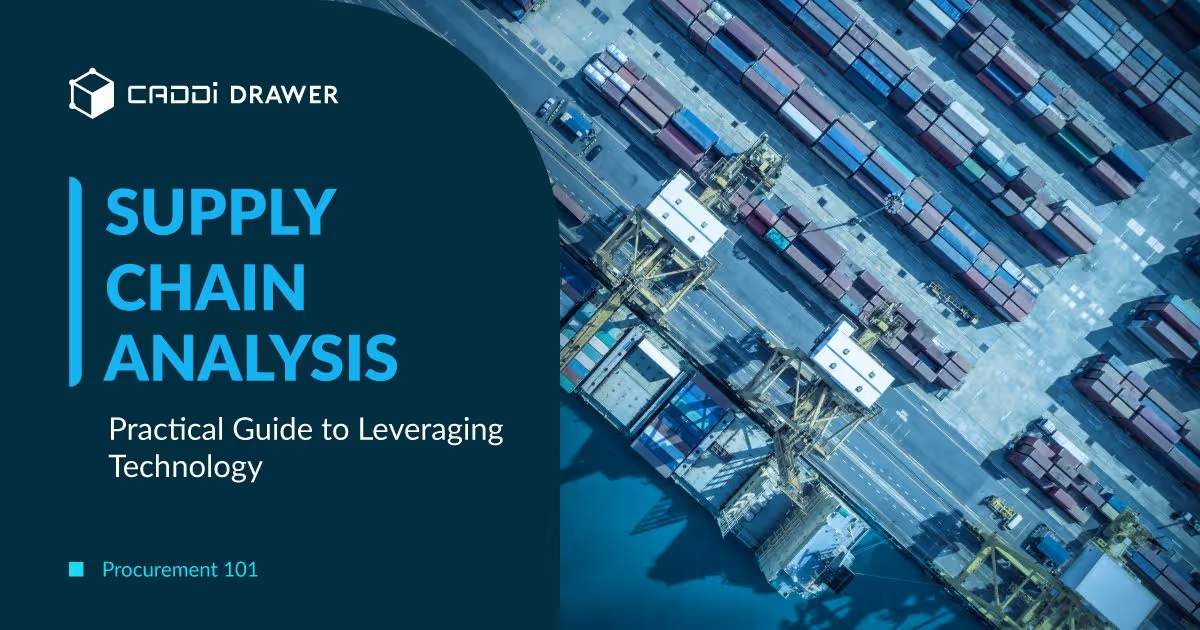
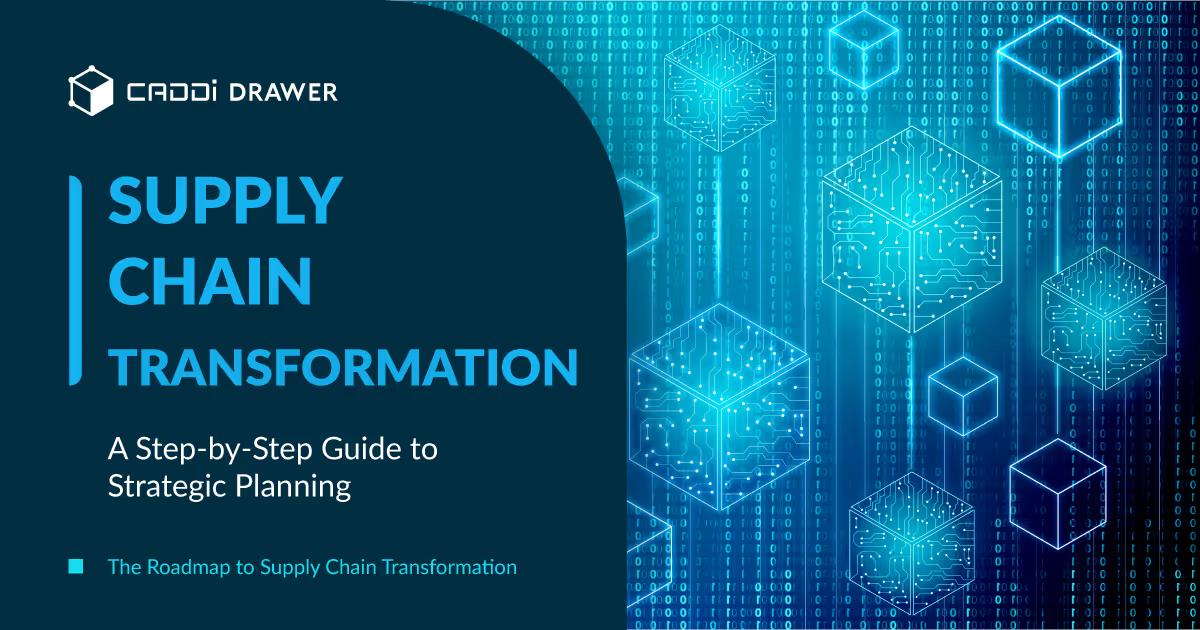
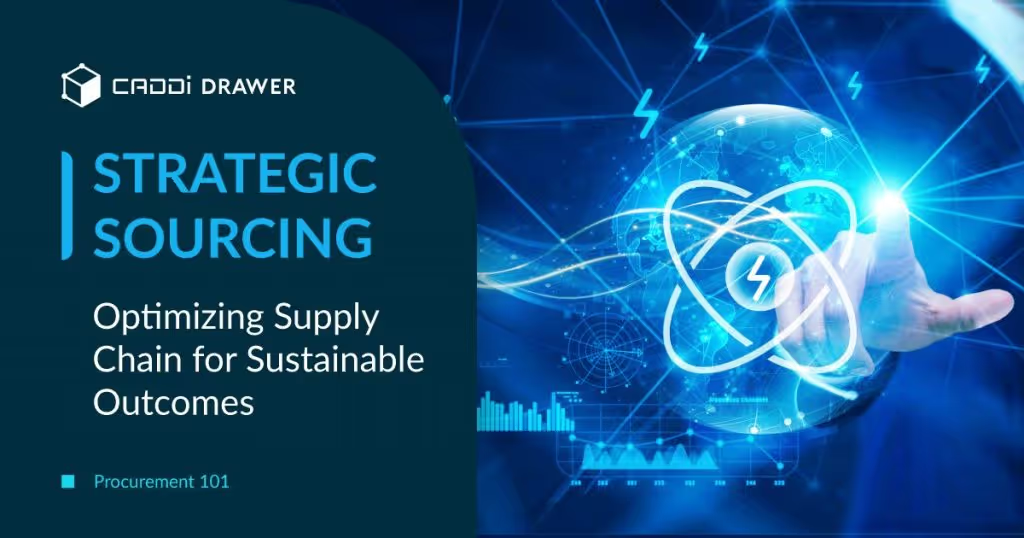
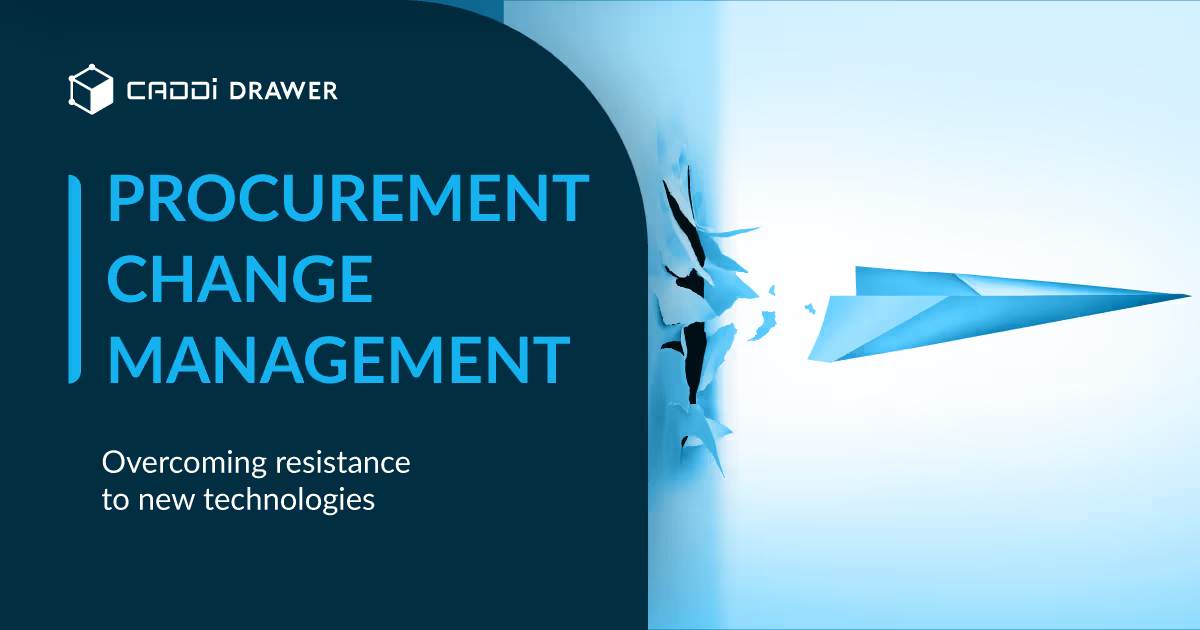
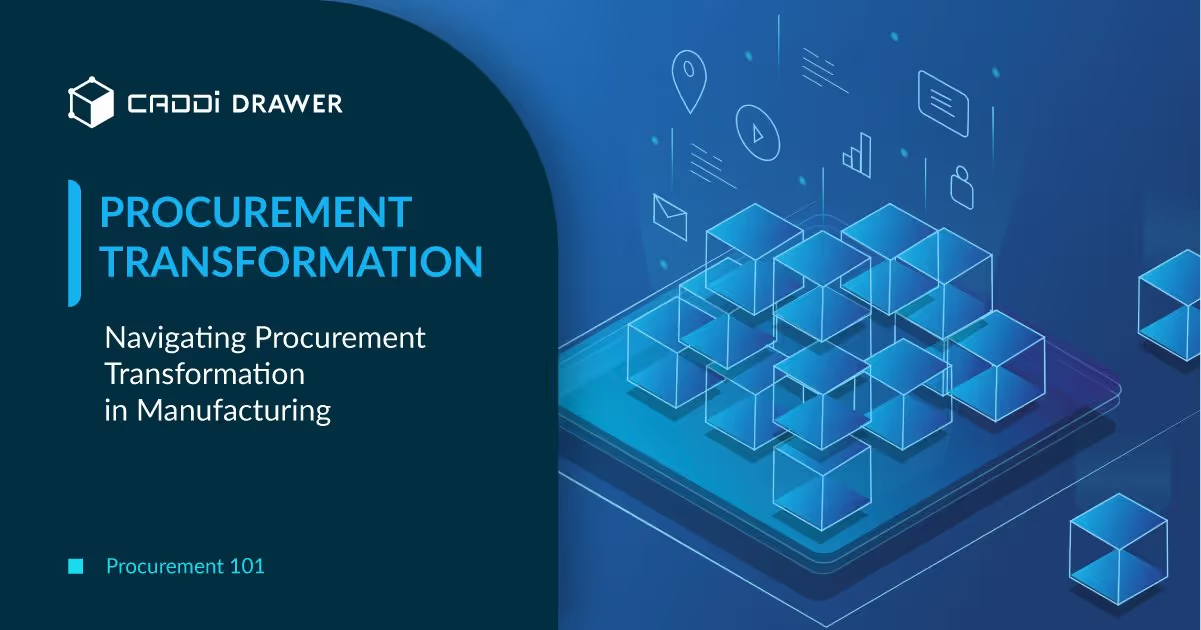
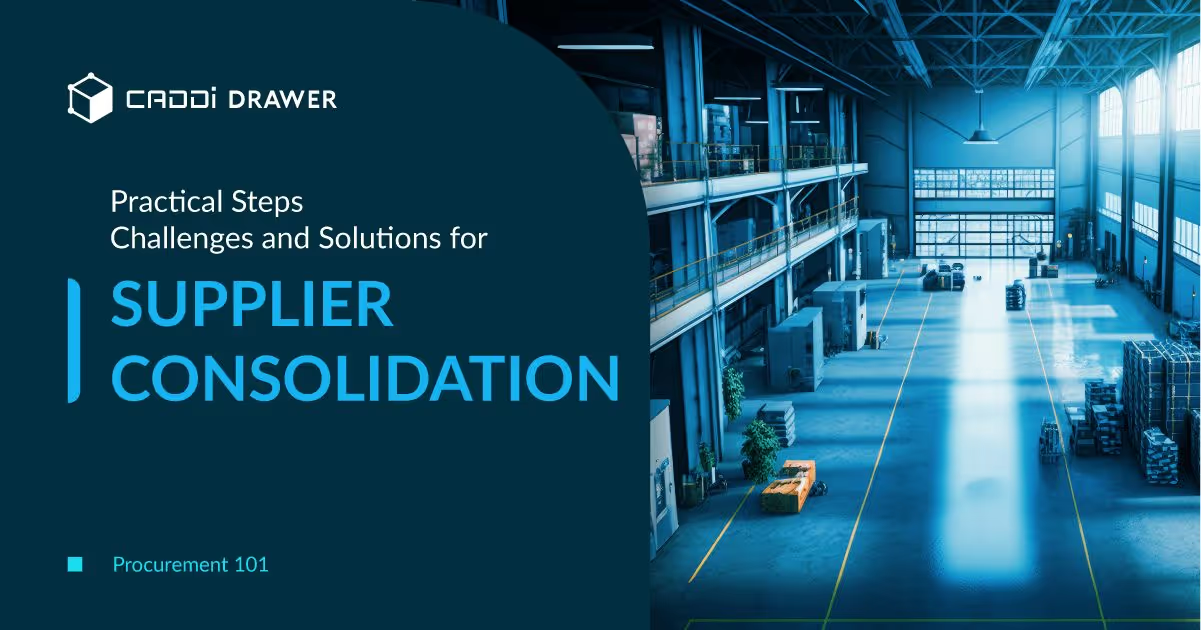