Thriving in the onshoring era: competitive advantage with American labor
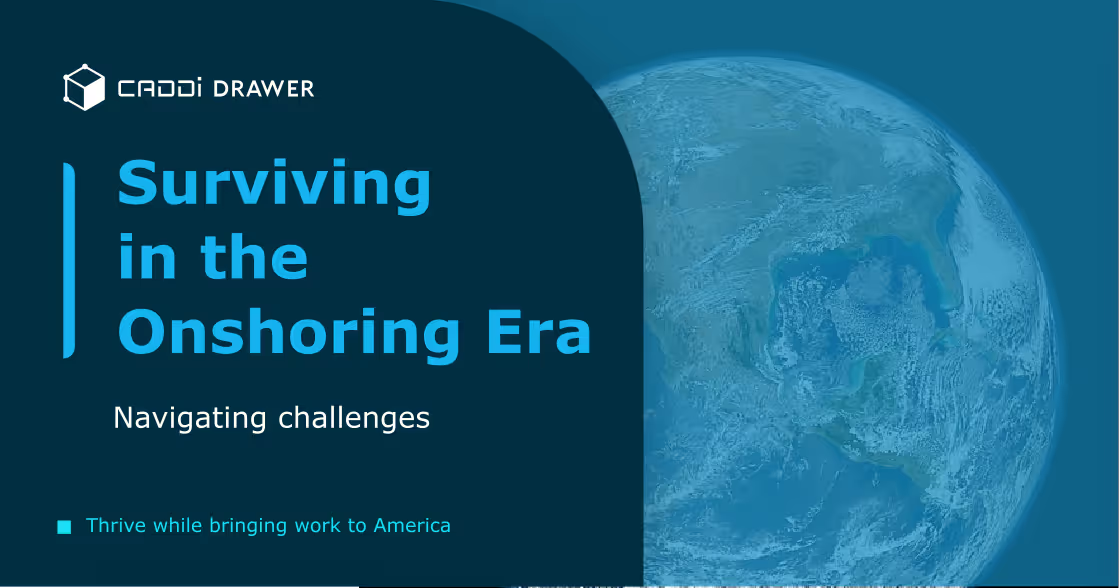
Table of Contents
Ever since the 1980s, the prevailing trend of manufacturing in America was manufacturing leaving America. In search of cheaper labour and other lower costs, American manufacturers offshored jobs to places like India, China, and Vietnam. To say this practice was controversial would be a massive understatement. We’ve seen decades of debate around offshoring’s impact on American prosperity, the quality of the products it produces, the effects on the destination country, and more.
As a result of all this divisiveness, we’ve started to see the tides of job location changing. Now onshoring (also known as re-shoring or backshoring) has become a significant trend for American manufacturers. When we surveyed manufacturing leaders for our American Manufacturing Pressure and Productivity Index, we found that many were concerned about onshoring. When asked for their top three pressure points, 51% cited navigating political demands to bring more production onshore.
Let’s explore what makes onshoring a pressing issue and why companies are finding it challenging to navigate.
Why is there pressure to onshore manufacturing jobs?
Myriad factors contribute to the recent trend of onshoring manufacturing jobs, including:
Government stimulus for American jobs. Starting with programs such as the Obama administration’s SelectUSA, the American government has been encouraging and incentivizing American and foreign companies to move their production to America. There are numerous benefits for an administration that moves jobs back to America: more prosperity for their voting base, better geopolitical leverage against competitors, more control over emerging technologies and markets, more consistent taxation of companies, and more.
Stimulation of American markets. This is a massive subject in economics that we can’t hope to tackle in depth here, but basically, if no one has jobs to buy your product, your product can’t sell. For manufacturers that primarily sell to Americans, injecting their profits back into Americans’ pockets via American jobs may be essential to keeping demand high and their products moving. As other elements of the American economy become destabilized, such as the gig economy cutting into the service economy, or prosperity in tech companies slowing, this stabilizing factor of middle-class manufacturing jobs may become more necessary.
Environmental concerns. Shipping products across oceans is a major cause of pollution and fuel consumption. For the many companies looking to improve their image and attract customers on the basis of being environmentally conscious, onshoring becomes an extremely impactful positive choice.
Supply chain management. The last few years have seen massive disruptions to the global supply chain, from a pandemic to geopolitical sanctions to a big boat stuck in a canal. Individual manufacturers cannot hope to prevent these externalities, but they can mitigate them. One of the most straightforwardly effective ways to mitigate global supply chain disruptions is to operate only with a local supply chain. Onshoring jobs removes hundreds of potential disruption points in your production process. This can also involve practices such as friendshoring, where production is moved to countries with more firm partnerships with America.
Why is onshoring difficult?
There are many challenges in bringing manufacturing jobs back to America – securing the necessary skilled talent, rebuilding infrastructure, navigating local environmental regulations, to name a few. But one stands above them all as the most significant: cost. Jobs were offshored in the first place to chase cheaper labor, and the cost of American labor is still the number one deterrent to having them in the States.
The solution is vehemently not to pay people less. Manufacturers cannot hope to attract the talent they need by posting minimum wage offers. Moreover, many of the benefits of onshoring, such as government support and market stimulation, won’t happen unless these are solidly middle-class, family-sustaining jobs.
Fortunately, but also unfortunately, manufacturers are already going to navigate these costs due to a smaller workforce. Reports indicate that 2.1 manufacturing jobs could go unfilled by 2030. As manufacturers bring shops back to America, they may find that they’ll need to run them with fewer people than they did offshore.
How technology mitigates onshoring challenges
So how do you do more with less? How do you get the productivity of an offshore workforce with one several times smaller? The answer, unsurprisingly, is technology. In 2019, the World Bank’s World Development Report on “The Changing Nature of Work” (pdf link) predicted a growing onshoring movement powered by automation and a lower reliance on labor.
This is a pattern we’ve seen many times before: jobs are offshored to cheaper labor markets, but technological revolutions allow for even more cost effective productivity back home. Eventually the new technology makes it to offshore markets, making them cheaper again and starting the cycle anew. These technological developments can come from anywhere, although America is still a major center for innovation. What matters more than origin is speed of adoption: if new technologies are implemented where the managerial core of a company is located, they can be adopted faster and more impactfully.
The latest era of technological revolution has several major components. There’s new production technologies, like 3D printing (additive manufacturing), and more sophisticated robotics. These make onshored manufacturing shops more versatile and agile, able to tackle new products and projects without slow and costly refactoring. You can still make a wide variety of products without a big workforce.
But the most impactful innovations lately have actually been on the side of software. New technologies, like natural language processing and machine vision, have made data more accessible than ever before. Manufacturing shops generate so much data that doing thorough strategic analysis of it is a full time job, if not multiple full time jobs. It slows down many other jobs too – our surveying found 41% of procurement professionals, 50% of engineers, and 54% of salespeople spent 1-2 hours a day tracking down the information they needed to do their jobs.
New technologies like CADDi change all of this. Our patented, innovative technology allows you to parse your drawings through the features of the drawing itself: everything from the shape of the part, to its dimensions, to material cost information. You can arrive at strategic insights or relevant data that would previously take hours and assistants.
Onshoring means more expensive labor, but talented and determined labor. You want them to be strategizing and innovating, not spending hours digging through files. Thrive in the onshoring era with new technologies like CADDi. Check out a demo or click through our interactive demo to see what we can do for you.
Ever since the 1980s, the prevailing trend of manufacturing in America was manufacturing leaving America. In search of cheaper labour and other lower costs, American manufacturers offshored jobs to places like India, China, and Vietnam. To say this practice was controversial would be a massive understatement. We’ve seen decades of debate around offshoring’s impact on American prosperity, the quality of the products it produces, the effects on the destination country, and more.
As a result of all this divisiveness, we’ve started to see the tides of job location changing. Now onshoring (also known as re-shoring or backshoring) has become a significant trend for American manufacturers. When we surveyed manufacturing leaders for our American Manufacturing Pressure and Productivity Index, we found that many were concerned about onshoring. When asked for their top three pressure points, 51% cited navigating political demands to bring more production onshore.
Let’s explore what makes onshoring a pressing issue and why companies are finding it challenging to navigate.
Why is there pressure to onshore manufacturing jobs?
Myriad factors contribute to the recent trend of onshoring manufacturing jobs, including:
Government stimulus for American jobs. Starting with programs such as the Obama administration’s SelectUSA, the American government has been encouraging and incentivizing American and foreign companies to move their production to America. There are numerous benefits for an administration that moves jobs back to America: more prosperity for their voting base, better geopolitical leverage against competitors, more control over emerging technologies and markets, more consistent taxation of companies, and more.
Stimulation of American markets. This is a massive subject in economics that we can’t hope to tackle in depth here, but basically, if no one has jobs to buy your product, your product can’t sell. For manufacturers that primarily sell to Americans, injecting their profits back into Americans’ pockets via American jobs may be essential to keeping demand high and their products moving. As other elements of the American economy become destabilized, such as the gig economy cutting into the service economy, or prosperity in tech companies slowing, this stabilizing factor of middle-class manufacturing jobs may become more necessary.
Environmental concerns. Shipping products across oceans is a major cause of pollution and fuel consumption. For the many companies looking to improve their image and attract customers on the basis of being environmentally conscious, onshoring becomes an extremely impactful positive choice.
Supply chain management. The last few years have seen massive disruptions to the global supply chain, from a pandemic to geopolitical sanctions to a big boat stuck in a canal. Individual manufacturers cannot hope to prevent these externalities, but they can mitigate them. One of the most straightforwardly effective ways to mitigate global supply chain disruptions is to operate only with a local supply chain. Onshoring jobs removes hundreds of potential disruption points in your production process. This can also involve practices such as friendshoring, where production is moved to countries with more firm partnerships with America.
Why is onshoring difficult?
There are many challenges in bringing manufacturing jobs back to America – securing the necessary skilled talent, rebuilding infrastructure, navigating local environmental regulations, to name a few. But one stands above them all as the most significant: cost. Jobs were offshored in the first place to chase cheaper labor, and the cost of American labor is still the number one deterrent to having them in the States.
The solution is vehemently not to pay people less. Manufacturers cannot hope to attract the talent they need by posting minimum wage offers. Moreover, many of the benefits of onshoring, such as government support and market stimulation, won’t happen unless these are solidly middle-class, family-sustaining jobs.
Fortunately, but also unfortunately, manufacturers are already going to navigate these costs due to a smaller workforce. Reports indicate that 2.1 manufacturing jobs could go unfilled by 2030. As manufacturers bring shops back to America, they may find that they’ll need to run them with fewer people than they did offshore.
How technology mitigates onshoring challenges
So how do you do more with less? How do you get the productivity of an offshore workforce with one several times smaller? The answer, unsurprisingly, is technology. In 2019, the World Bank’s World Development Report on “The Changing Nature of Work” (pdf link) predicted a growing onshoring movement powered by automation and a lower reliance on labor.
This is a pattern we’ve seen many times before: jobs are offshored to cheaper labor markets, but technological revolutions allow for even more cost effective productivity back home. Eventually the new technology makes it to offshore markets, making them cheaper again and starting the cycle anew. These technological developments can come from anywhere, although America is still a major center for innovation. What matters more than origin is speed of adoption: if new technologies are implemented where the managerial core of a company is located, they can be adopted faster and more impactfully.
The latest era of technological revolution has several major components. There’s new production technologies, like 3D printing (additive manufacturing), and more sophisticated robotics. These make onshored manufacturing shops more versatile and agile, able to tackle new products and projects without slow and costly refactoring. You can still make a wide variety of products without a big workforce.
But the most impactful innovations lately have actually been on the side of software. New technologies, like natural language processing and machine vision, have made data more accessible than ever before. Manufacturing shops generate so much data that doing thorough strategic analysis of it is a full time job, if not multiple full time jobs. It slows down many other jobs too – our surveying found 41% of procurement professionals, 50% of engineers, and 54% of salespeople spent 1-2 hours a day tracking down the information they needed to do their jobs.
New technologies like CADDi change all of this. Our patented, innovative technology allows you to parse your drawings through the features of the drawing itself: everything from the shape of the part, to its dimensions, to material cost information. You can arrive at strategic insights or relevant data that would previously take hours and assistants.
Onshoring means more expensive labor, but talented and determined labor. You want them to be strategizing and innovating, not spending hours digging through files. Thrive in the onshoring era with new technologies like CADDi. Check out a demo or click through our interactive demo to see what we can do for you.