Procurement 101: An Introduction to Painting Process in Fabrication
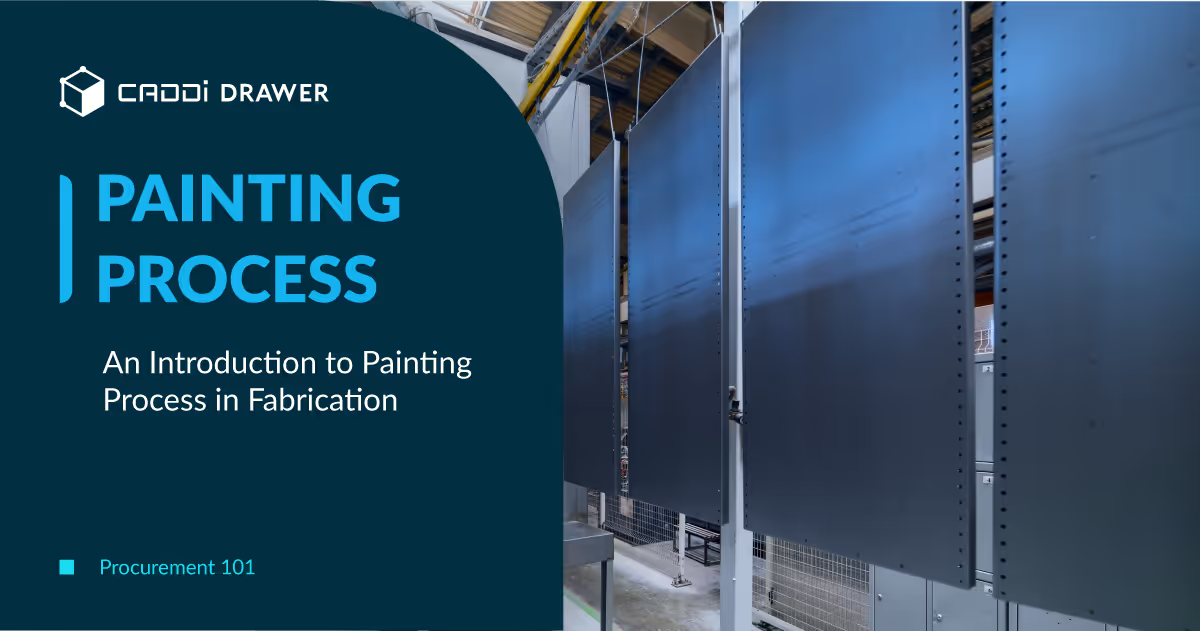
Table of Contents
Custom fabrication involves building specialized parts and products that are not mass manufactured. This allows for complete customization and uniqueness suited for the specific application.
Painting is an essential process in custom fabrication, both for aesthetics and protection. Properly painting custom fabricated parts promotes durability, enhances appearance, and prevents corrosion and wear.
This article will provide an overview of the complete painting process for custom fabricated parts. We will cover critical steps including surface preparation, primer, paint selection and application, as well as curing and drying. Proper technique and materials throughout the painting process are crucial for achieving professional, long-lasting results. In the following sections, we will explain each process step by step.
Surface Preparation
Proper surface preparation is crucial for achieving a high-quality, long-lasting paint finish on any custom fabrication project. The surface must be thoroughly cleaned, abraded, and masked prior to painting.
Cleaning removes any dirt, grease, oil, wax, mold release agents, and other contaminants. Solvents like mineral spirits, acetone, or wax and grease remover can be used, followed by washing with soap and water. For metal surfaces, alkaline cleaners may be used to remove any corrosion before addressing rust with sandpaper, steel wool, or a wire brush. Plastics may require a chemical etchant. Be sure to follow all safety precautions when using any hazardous cleaning agents.
Sanding abrades the surface to promote paint adhesion. Start with coarser grit sandpaper (80-120) to remove large imperfections, then use finer grits to smooth everything out. Sand in the same direction as the grain on wood, or in small circular motions on metal and plastic. Bevel any sharp edges and round off corners slightly. Finally, tack cloth the surface to remove sanding dust before painting.
Masking protects areas you don’t want painted. Cover adjoining surfaces with paper or plastic sheeting and tape it securely at the edges. For fine details like stripes or letters, use masking tape directly on the surface. Liquid masking solutions can also be painted on and peeled off after finishing. Proper masking saves cleanup time later.
Priming
Priming is an essential step in the painting process for custom fabricated parts and components. The main purposes of primer are:
- To provide a uniform surface for the paint to adhere to. Bare metal and other surfaces can be uneven and inconsistent, so primer creates a consistent foundation.
- To prevent corrosion and rust. Primers often contain anti-corrosive pigments and inhibitors that seal and protect the metal underneath.
- To improve paint adhesion and durability. Primers bind securely to surfaces and provide a “tooth” for paints to grab onto.
- To hide surface imperfections. Primer helps fill in small scratches, pits, and other flaws to create a smooth canvas for paint.
There are several types of primer used in custom fabrication:
- Etching primers contain acids that etch into the surface to provide extra grip for paints. They work especially well on aluminum and galvanized metals.
- Epoxy primers offer superior corrosion resistance and flexibility. They are extremely durable and work well on steel parts.
- Urethane primers provide a smooth finish and are resistant to chipping and abrasion. They also have a fast drying time which speeds up the painting workflow.
- Surfacer/filler primers are thicker to fill scratches and imperfections in surfaces. They are often used when a flawless finished appearance is desired.
Choosing the right primer is critical to ensure proper paint adhesion and provide long-lasting protection against rust and corrosion. Consulting with paint manufacturers to match the right primer with the selected paint type and fabrication materials is highly recommended.
Paint Selection
The type of paint used in custom fabrication depends on several factors:
- Application method – Will the paint be sprayed or brushed on? Some paints are designed for airbrush or HVLP spraying rather than brush painting. Spray paint also requires thinning with solvents.
- Paint type – Common options include polyurethane, enamel, lacquer and epoxy. Each has advantages and disadvantages regarding durability, chemical resistance, finish, and ease of application.
- Sheen – Is a glossy or matte finish preferred? Satin/semi-gloss paints are a compromise. More gloss shows off the color but can accentuate surface imperfections.
- Durability – More durable paints like polyurethanes and epoxies provide better protection for parts exposed to weather, chemicals or abrasion. But they are harder to apply than enamels and lacquers.
- Color options – Does the paint need to exactly match a custom color? Certain paint lines offer more pre-mixed colors versus mixing custom colors.
- Environment – Will the painted object be used outdoors or indoors? Outdoor paints resist UV rays better. Low VOC paints are better suited for indoor fabrication shops.
- Substrate – The paint compatibility varies for different materials like metal, plastic, wood or fiberglass. Primers aid adhesion.
- Budget – Higher performance paints cost more. The required durability and quality should determine the budget.
Proper paint selection ensures the desired finish, appearance and lifespan for custom fabricated parts and equipment. Consulting the paint manufacturer’s technical data sheet aids choosing the optimal product.
Spray Painting
Spray painting is a common technique for applying paint in a custom fabrication shop. It requires some specialized equipment but allows for an efficient, high-quality finish when done properly.
Equipment
The basic equipment needed for spray painting includes:
- Spray gun – This is connected to the air compressor to atomize the paint and direct it onto the surface. There are various types like HVLP (high volume, low pressure) or LVLP (low volume, low pressure).
- Air compressor – Provides the compressed air to propel the paint through the spray gun. It needs to provide clean, dry air at sufficient pressure and volume.
- Paint booth – A specialized, ventilated booth to contain overspray and fumes. Can be a downdraft booth or a crossflow booth. Requires proper ventilation and filtering.
- Masking – Paper, plastic sheets, or masking tape to cover areas not being painted.
- Personal protective equipment – Respirator, goggles, gloves, and protective suit to avoid inhaling or contacting paint.
Technique
Proper spray painting technique is essential for an even, consistent finish. Key steps include:
- Proper surface preparation – The surface must be clean and free of any oil, dirt, or defects. Sanding or chemical pre-treatment may be required.
- Applying primer – A primer coat enhances paint adhesion and prevents reactions with the substrate.
- Maintaining ideal spray distance – Around 6 to 8 inches between the gun nozzle and the surface.
- Using proper arm motion – Keeping the arm moving at a constant speed in parallel passes to cover the surface evenly.
- Overlapping spray patterns – Each stroke should overlap the preceding one by 30-50% to ensure even coverage.
- Maintaining ideal air pressure – Enough to properly atomize the paint without causing excessive overspray.
- Applying thin coats – 2-3 coats of thin paint are better than 1 thick coat. Allow proper drying between coats.
- Checking for defects – Watch for runs, sags, drips, or uneven coverage and correct with additional coats.
Pros and Cons
Spray painting provides some advantages but also has some disadvantages to consider:
- Pros: Highly efficient, even coverage, smooth uniform finish, ability to apply thick coats.
- Cons: Overspray and bounce-back waste, requires skill to master technique, requires masking, cannot get into tight spaces.
Brush Painting
Paint brushes allow for great control and high quality finishes on custom fabricated pieces. Selecting the right brush is crucial – look for ones made with soft natural bristles and a chisel-shaped tip. Prepare the brushes before use by conditioning them to avoid leaving stray hairs on the surface.
When brush painting, load the brush up halfway with paint and then gently tap it against the side of the can to remove any excess. Apply the paint in smooth, even strokes following the contour of the surface. Overlap strokes slightly to ensure full coverage. Take care when painting edges or corners.
The main advantages of brush painting are:
- More control and ability to paint fine details compared to spraying
- Avoids paint mist and overspray
- Can touch up small areas easily
- Less prep work compared to spraying
The disadvantages are:
- Can leave brush strokes in the finish
- Takes longer than spraying for large areas
- Increased chance of drips and uneven coats compared to spraying
- Not ideal for porous or abrasive surfaces
Proper brush technique, high quality brushes, and patience are key to achieving an attractive hand-brushed finish on custom fabricated pieces. Multiple coats may be required, allowing proper drying time between each.
Curing and Drying
The curing and drying process is a critical step in achieving a high-quality, durable paint finish in custom fabrication. Proper cure times allow coatings to fully crosslink and reach their designed hardness and chemical resistance.
Curing refers to the chemical process by which the components in paint or clear coat react and bond together after application. Curing happens more slowly, and continues for days or weeks after the coating has initially dried. During curing, the paint film develops hardness, gloss, resistance to solvents, and protection from the elements.
Drying is the process where the solvents in the paint evaporate into the air. Drying happens more quickly, usually within hours after applying the coating. While the paint may feel dry to the touch, the curing process will continue for much longer.
It is essential to allow adequate cure time between coats, and after the final clear coat has been applied. The required cure time depends on the product used, but is typically 24-72 hours between coats, and 5-7 days for the finished product at 70°F. Cure times should be extended at cooler temperatures. Always follow the coating manufacturer’s recommendations for minimum cure times.
Rushing the curing process can result in issues like solvent pop, loss of gloss, reduced hardness, and improper adhesion between coats. Allowing extra cure time will ensure the paint has sufficient hardness and chemical resistance for its intended use. Proper curing is what gives painted finishes their toughness and longevity.
Closing Summary
In conclusion, the painting process is a crucial aspect of custom fabrication, ensuring both the aesthetic appeal and long-term durability of specialized parts and products. By following the proper techniques and using the appropriate materials throughout the steps of surface preparation, priming, paint selection and application, curing, and drying, fabricators can achieve professional, long-lasting results.
However, when outsourcing surface treatment including painting, additional factors must be considered to ensure the quality of the finished product. We explored the key concerns and best practices for maintaining high standards when entrusting the painting process to an external provider in another article.
Custom fabrication involves building specialized parts and products that are not mass manufactured. This allows for complete customization and uniqueness suited for the specific application.
Painting is an essential process in custom fabrication, both for aesthetics and protection. Properly painting custom fabricated parts promotes durability, enhances appearance, and prevents corrosion and wear.
This article will provide an overview of the complete painting process for custom fabricated parts. We will cover critical steps including surface preparation, primer, paint selection and application, as well as curing and drying. Proper technique and materials throughout the painting process are crucial for achieving professional, long-lasting results. In the following sections, we will explain each process step by step.
Surface Preparation
Proper surface preparation is crucial for achieving a high-quality, long-lasting paint finish on any custom fabrication project. The surface must be thoroughly cleaned, abraded, and masked prior to painting.
Cleaning removes any dirt, grease, oil, wax, mold release agents, and other contaminants. Solvents like mineral spirits, acetone, or wax and grease remover can be used, followed by washing with soap and water. For metal surfaces, alkaline cleaners may be used to remove any corrosion before addressing rust with sandpaper, steel wool, or a wire brush. Plastics may require a chemical etchant. Be sure to follow all safety precautions when using any hazardous cleaning agents.
Sanding abrades the surface to promote paint adhesion. Start with coarser grit sandpaper (80-120) to remove large imperfections, then use finer grits to smooth everything out. Sand in the same direction as the grain on wood, or in small circular motions on metal and plastic. Bevel any sharp edges and round off corners slightly. Finally, tack cloth the surface to remove sanding dust before painting.
Masking protects areas you don’t want painted. Cover adjoining surfaces with paper or plastic sheeting and tape it securely at the edges. For fine details like stripes or letters, use masking tape directly on the surface. Liquid masking solutions can also be painted on and peeled off after finishing. Proper masking saves cleanup time later.
Priming
Priming is an essential step in the painting process for custom fabricated parts and components. The main purposes of primer are:
- To provide a uniform surface for the paint to adhere to. Bare metal and other surfaces can be uneven and inconsistent, so primer creates a consistent foundation.
- To prevent corrosion and rust. Primers often contain anti-corrosive pigments and inhibitors that seal and protect the metal underneath.
- To improve paint adhesion and durability. Primers bind securely to surfaces and provide a “tooth” for paints to grab onto.
- To hide surface imperfections. Primer helps fill in small scratches, pits, and other flaws to create a smooth canvas for paint.
There are several types of primer used in custom fabrication:
- Etching primers contain acids that etch into the surface to provide extra grip for paints. They work especially well on aluminum and galvanized metals.
- Epoxy primers offer superior corrosion resistance and flexibility. They are extremely durable and work well on steel parts.
- Urethane primers provide a smooth finish and are resistant to chipping and abrasion. They also have a fast drying time which speeds up the painting workflow.
- Surfacer/filler primers are thicker to fill scratches and imperfections in surfaces. They are often used when a flawless finished appearance is desired.
Choosing the right primer is critical to ensure proper paint adhesion and provide long-lasting protection against rust and corrosion. Consulting with paint manufacturers to match the right primer with the selected paint type and fabrication materials is highly recommended.
Paint Selection
The type of paint used in custom fabrication depends on several factors:
- Application method – Will the paint be sprayed or brushed on? Some paints are designed for airbrush or HVLP spraying rather than brush painting. Spray paint also requires thinning with solvents.
- Paint type – Common options include polyurethane, enamel, lacquer and epoxy. Each has advantages and disadvantages regarding durability, chemical resistance, finish, and ease of application.
- Sheen – Is a glossy or matte finish preferred? Satin/semi-gloss paints are a compromise. More gloss shows off the color but can accentuate surface imperfections.
- Durability – More durable paints like polyurethanes and epoxies provide better protection for parts exposed to weather, chemicals or abrasion. But they are harder to apply than enamels and lacquers.
- Color options – Does the paint need to exactly match a custom color? Certain paint lines offer more pre-mixed colors versus mixing custom colors.
- Environment – Will the painted object be used outdoors or indoors? Outdoor paints resist UV rays better. Low VOC paints are better suited for indoor fabrication shops.
- Substrate – The paint compatibility varies for different materials like metal, plastic, wood or fiberglass. Primers aid adhesion.
- Budget – Higher performance paints cost more. The required durability and quality should determine the budget.
Proper paint selection ensures the desired finish, appearance and lifespan for custom fabricated parts and equipment. Consulting the paint manufacturer’s technical data sheet aids choosing the optimal product.
Spray Painting
Spray painting is a common technique for applying paint in a custom fabrication shop. It requires some specialized equipment but allows for an efficient, high-quality finish when done properly.
Equipment
The basic equipment needed for spray painting includes:
- Spray gun – This is connected to the air compressor to atomize the paint and direct it onto the surface. There are various types like HVLP (high volume, low pressure) or LVLP (low volume, low pressure).
- Air compressor – Provides the compressed air to propel the paint through the spray gun. It needs to provide clean, dry air at sufficient pressure and volume.
- Paint booth – A specialized, ventilated booth to contain overspray and fumes. Can be a downdraft booth or a crossflow booth. Requires proper ventilation and filtering.
- Masking – Paper, plastic sheets, or masking tape to cover areas not being painted.
- Personal protective equipment – Respirator, goggles, gloves, and protective suit to avoid inhaling or contacting paint.
Technique
Proper spray painting technique is essential for an even, consistent finish. Key steps include:
- Proper surface preparation – The surface must be clean and free of any oil, dirt, or defects. Sanding or chemical pre-treatment may be required.
- Applying primer – A primer coat enhances paint adhesion and prevents reactions with the substrate.
- Maintaining ideal spray distance – Around 6 to 8 inches between the gun nozzle and the surface.
- Using proper arm motion – Keeping the arm moving at a constant speed in parallel passes to cover the surface evenly.
- Overlapping spray patterns – Each stroke should overlap the preceding one by 30-50% to ensure even coverage.
- Maintaining ideal air pressure – Enough to properly atomize the paint without causing excessive overspray.
- Applying thin coats – 2-3 coats of thin paint are better than 1 thick coat. Allow proper drying between coats.
- Checking for defects – Watch for runs, sags, drips, or uneven coverage and correct with additional coats.
Pros and Cons
Spray painting provides some advantages but also has some disadvantages to consider:
- Pros: Highly efficient, even coverage, smooth uniform finish, ability to apply thick coats.
- Cons: Overspray and bounce-back waste, requires skill to master technique, requires masking, cannot get into tight spaces.
Brush Painting
Paint brushes allow for great control and high quality finishes on custom fabricated pieces. Selecting the right brush is crucial – look for ones made with soft natural bristles and a chisel-shaped tip. Prepare the brushes before use by conditioning them to avoid leaving stray hairs on the surface.
When brush painting, load the brush up halfway with paint and then gently tap it against the side of the can to remove any excess. Apply the paint in smooth, even strokes following the contour of the surface. Overlap strokes slightly to ensure full coverage. Take care when painting edges or corners.
The main advantages of brush painting are:
- More control and ability to paint fine details compared to spraying
- Avoids paint mist and overspray
- Can touch up small areas easily
- Less prep work compared to spraying
The disadvantages are:
- Can leave brush strokes in the finish
- Takes longer than spraying for large areas
- Increased chance of drips and uneven coats compared to spraying
- Not ideal for porous or abrasive surfaces
Proper brush technique, high quality brushes, and patience are key to achieving an attractive hand-brushed finish on custom fabricated pieces. Multiple coats may be required, allowing proper drying time between each.
Curing and Drying
The curing and drying process is a critical step in achieving a high-quality, durable paint finish in custom fabrication. Proper cure times allow coatings to fully crosslink and reach their designed hardness and chemical resistance.
Curing refers to the chemical process by which the components in paint or clear coat react and bond together after application. Curing happens more slowly, and continues for days or weeks after the coating has initially dried. During curing, the paint film develops hardness, gloss, resistance to solvents, and protection from the elements.
Drying is the process where the solvents in the paint evaporate into the air. Drying happens more quickly, usually within hours after applying the coating. While the paint may feel dry to the touch, the curing process will continue for much longer.
It is essential to allow adequate cure time between coats, and after the final clear coat has been applied. The required cure time depends on the product used, but is typically 24-72 hours between coats, and 5-7 days for the finished product at 70°F. Cure times should be extended at cooler temperatures. Always follow the coating manufacturer’s recommendations for minimum cure times.
Rushing the curing process can result in issues like solvent pop, loss of gloss, reduced hardness, and improper adhesion between coats. Allowing extra cure time will ensure the paint has sufficient hardness and chemical resistance for its intended use. Proper curing is what gives painted finishes their toughness and longevity.
Closing Summary
In conclusion, the painting process is a crucial aspect of custom fabrication, ensuring both the aesthetic appeal and long-term durability of specialized parts and products. By following the proper techniques and using the appropriate materials throughout the steps of surface preparation, priming, paint selection and application, curing, and drying, fabricators can achieve professional, long-lasting results.
However, when outsourcing surface treatment including painting, additional factors must be considered to ensure the quality of the finished product. We explored the key concerns and best practices for maintaining high standards when entrusting the painting process to an external provider in another article.
Ready to see CADDi Drawer in action? Get a personalized demo.
Subscribe to our Blog!
Related Resources
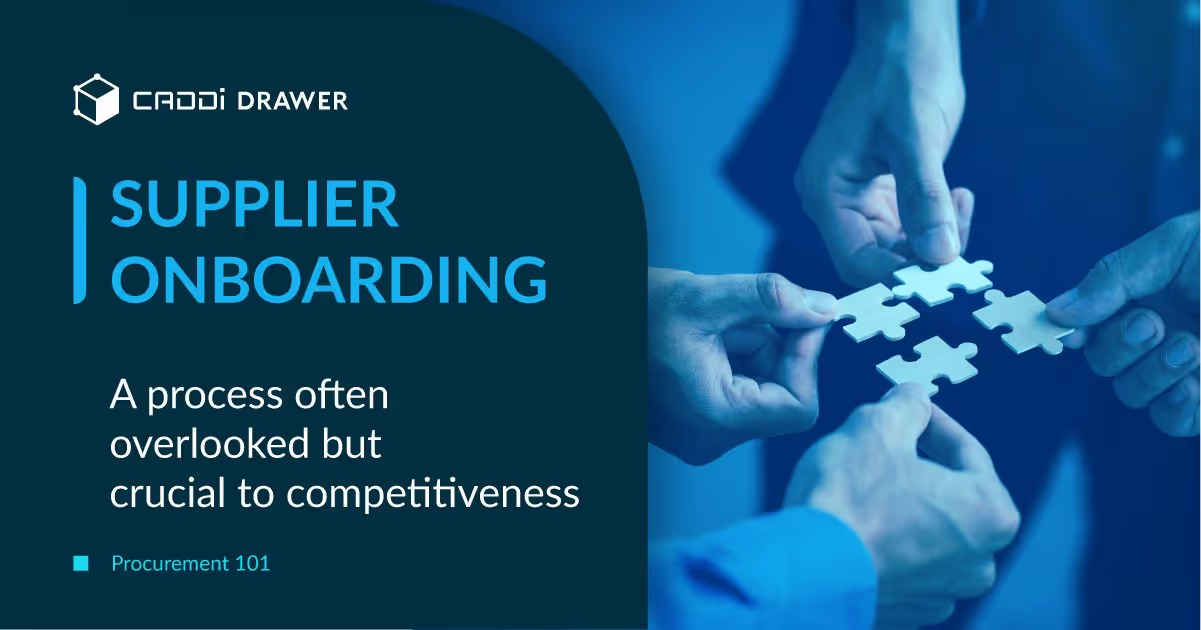


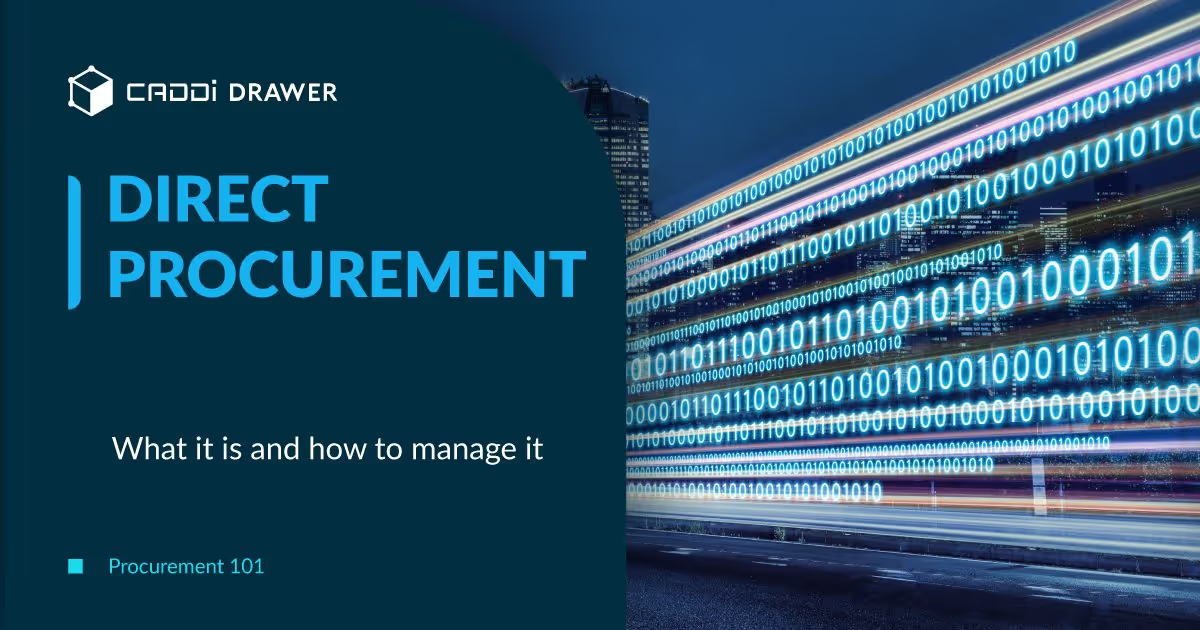
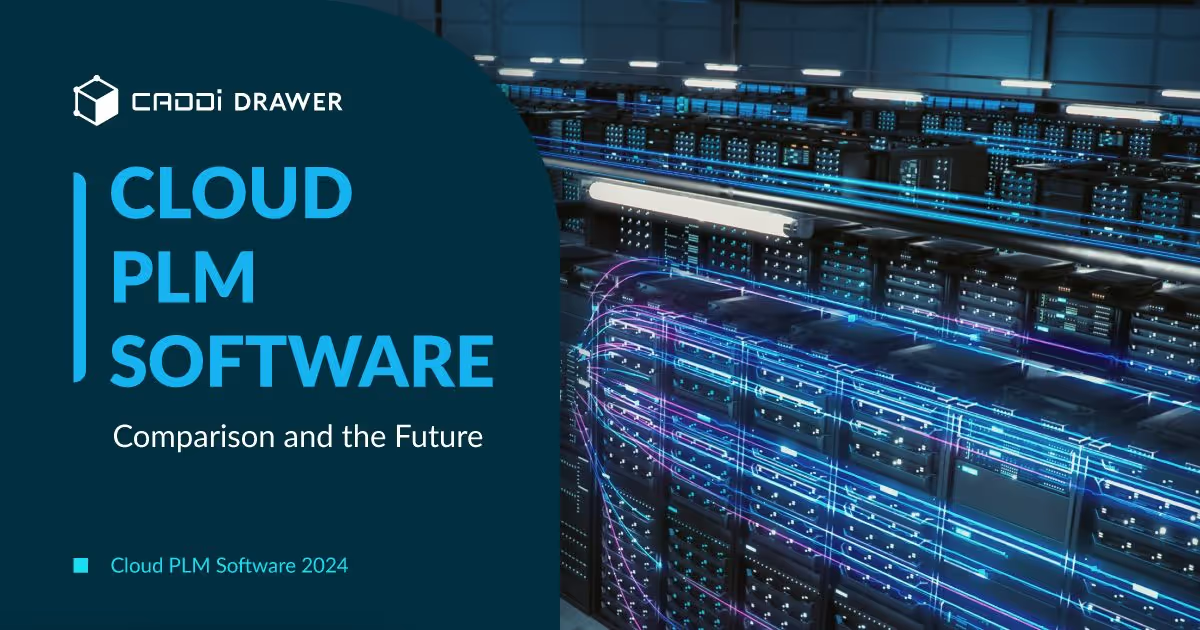
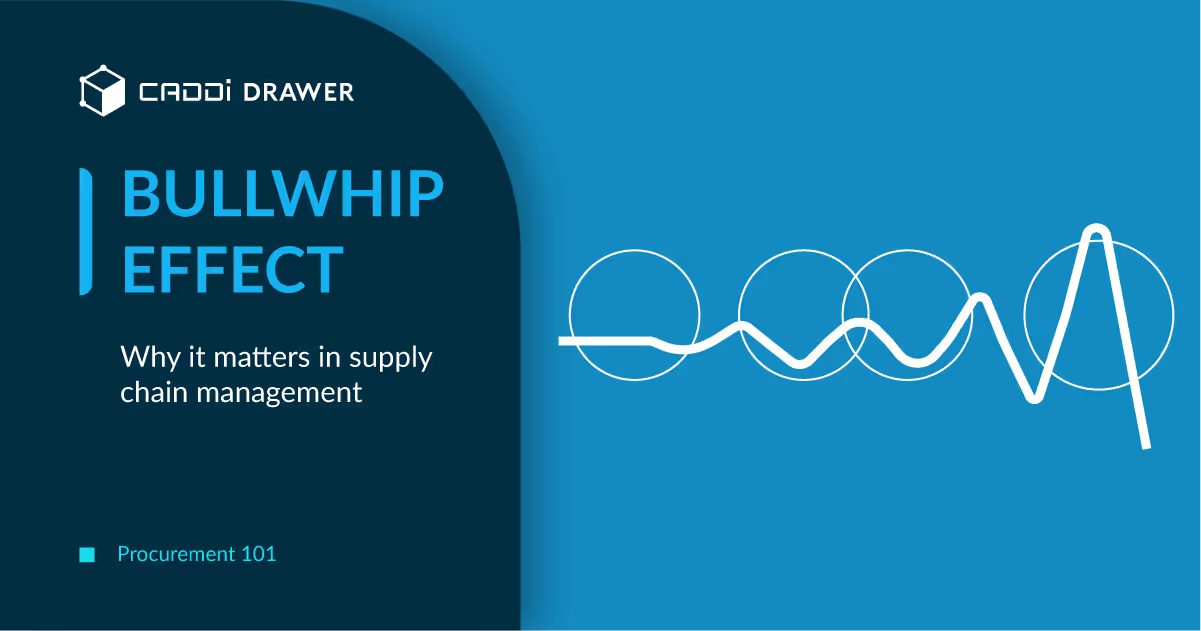