Procurement 101: An Introduction to Sheet Metal Fabrication Process
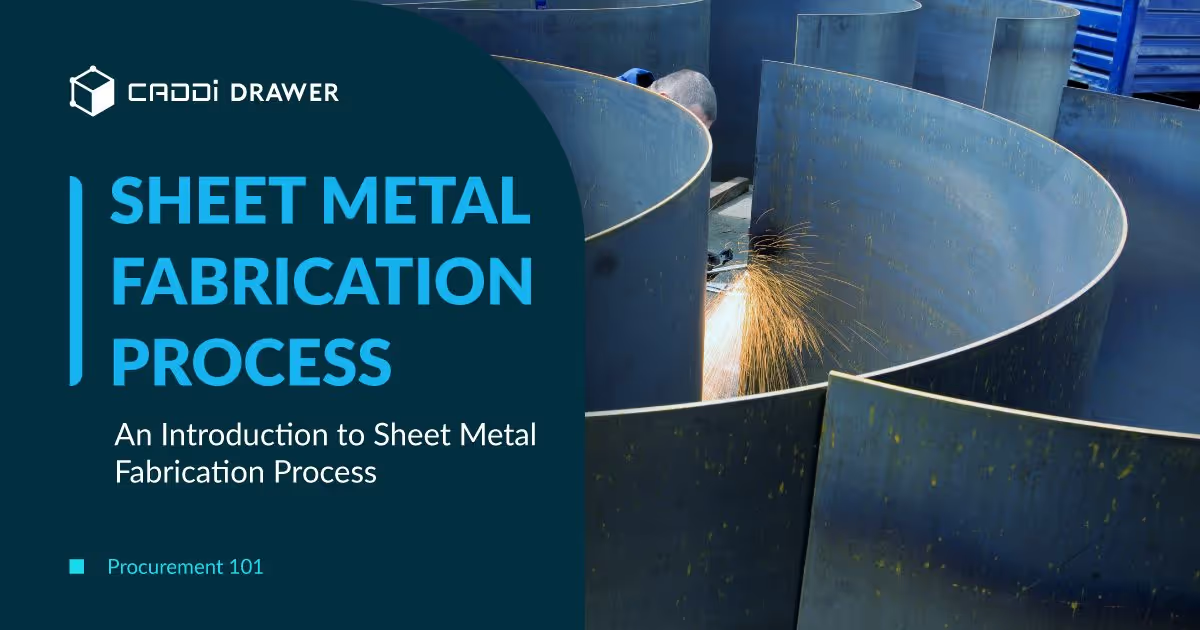
Table of Contents
What is sheet metal fabrication?
Sheet metal fabrication is the process of shaping thin sheets of metal into useful structures and products. It involves taking flat sheet metal, cutting it into required shapes and sizes, and then bending it into the desired forms.
Sheet metal fabrication has numerous applications across industries like aerospace, automotive, construction, electronics, and manufacturing. It offers several benefits over other manufacturing processes like casting or machining:
- Versatile – A wide range of products from simple brackets to complex enclosures can be fabricated. Sheet metal can be worked into curved, cylindrical and other organic shapes relatively easily.
- Fast and efficient – Modern laser and plasma cutting allow quick and precise cutting of sheet metal. Automated stamping and bending processes enable mass production. Overall, sheet metal fabrication is fast and cost-effective.
- Material conservation – Sheet metal fabrication produces very little waste material compared to machining processes. Complex parts can be made from single sheets using bending, stamping and pressing. This results in significant material savings.
- Strength – Sheet metal parts can be designed to have excellent strength-to-weight ratios. The material thickness can be varied to increase strength in areas under more stress.
- Corrosion resistance – Metals like aluminum and galvanized steel have inherent corrosion resistance. They can withstand exposure to weather elements over long periods. Additional coatings can also enhance corrosion protection.
So in summary, sheet metal fabrication allows quick, efficient and versatile production of lightweight but strong metal components. Its minimal material wastage provides additional cost benefits. These qualities make it ideal for high volume manufacturing across many industries.
Sheet Metal Materials
Sheet metal fabrication utilizes a variety of metals, each with properties that make them suitable for different applications. The most common base metals used are:
- Steel – Steel is the most popular choice for sheet metal due to its high strength, formability, weldability, and relatively low cost. Common forms of steel used include low carbon steel, mild steel, stainless steel, and galvanized steel. Steel is suitable for applications requiring durability, strength, and corrosion resistance.
- Aluminum – Aluminum is lightweight, corrosion resistant, conductive, and easily formed and machined. It is commonly used for electronic enclosures, chemical equipment, appliances, and aircraft components. Aluminum has high reflectivity and a bright, attractive finish.
- Copper – Copper offers excellent conductivity, corrosion resistance, and antimicrobial properties. It is commonly used for electrical wiring, plumbing, heat exchangers, and architectural finishes. The softness and malleability of copper makes it ideal for forming complex parts.
- Brass – Brass is an alloy of copper and zinc that is stronger and more formable than copper. It offers good corrosion resistance and an attractive golden color. Brass is used for musical instruments, valves, and decorative trims.
- Titanium – Titanium offers very high strength-to-weight ratio and excellent corrosion resistance while maintaining formability and weldability. It is used for aircraft, chemical processing, marine applications, and medical implants.
Sheet metal thickness is measured in gauge or inches/millimeters. Gauge refers to the number of sheets per inch of thickness. As gauge number increases, thickness decreases. Common sheet metal gauge sizes are 22 gauge (.70mm) to 10 gauge (3.5mm). For thicker metals, thickness is measured directly in fractional inches or millimeters.
Cutting Processes
There are several main methods for cutting sheet metal in fabrication.
Laser Cutting
Laser cutting uses a high power laser beam to melt and vaporize sheet metal.
- It can cut complex shapes with high accuracy and smooth edges.
- No tooling required so fast design changes are possible.
- More expensive per part than mechanical cutting.
Plasma Cutting
Plasma cutting uses a high-velocity jet of ionized gas (plasma) to melt and expel material from the cutting area.
- It can quickly cut through thick sheets of electrically conductive materials, such as steel and aluminum.
- Produces a clean, relatively smooth edge with a narrow kerf (cut width).
- Faster and more economical than laser cutting for thicker materials.
- Limited to conductive materials and may produce some heat-affected zones.
Waterjet Cutting
Waterjet cutting uses an extremely high pressure stream of water with abrasives to erode sheet metal.
- It can cut precise and complex shapes in almost any material.
- No heat damage or fumes compared to laser cutting.
- Slower than laser and more expensive to operate.
Punching
Punching uses a machine press, such as CNC turret punch machines, with tool and die sets to punch holes or shapes out of sheet metal.
- Very fast process for high volume hole patterns or shapes.
- Limited to simple geometries compared to laser and waterjet cutting.
- Low operating costs once initial tooling investment is made.
Shearing
Shearing uses a machine press with a guillotine blade to slice sheet metal.
- Fast and economical process for cutting flat patterns out of sheet metal.
- Accuracy and edge quality may be lower than other cutting methods.
- Works for sheets up to 10mm thickness.
Bending and Forming
Sheet metal must be formed or bent to create many end products or parts. There are several common bending and forming processes used in sheet metal fabrication.
Press Braking
Press braking uses a machine press with a V-shaped die to bend sheet metal. A bottom die supports the sheet while the upper die presses down to create precise and repeatable bends. Press brakes are commonly used to create folds and box-like structures out of sheet metal.
Slip Rolling
In slip rolling, sheet metal is passed between cylindrical/conical shaped rollers which exert pressure to bend the metal. Slip rolling forms cones and cylindrical shapes through a cold rolling process. It can bend metal up to 180 degrees using multiple passes through the rollers.
Stamping
Stamping is a high-volume, cost-effective cold forming process that uses dies and punches to shape sheet metal into various parts and features, such as holes, flanges, and embossments.
Flaring (or Flanging)
Flaring, also known as flanging, is a process that forms a flared or flanged edge on a sheet metal part, often used to create a lip or rim for joining or reinforcing the part.
Other Forming Methods
Other specialized forming methods that require custom dies include:
- Embossing – Creating raised or recessed designs on the surface of sheet metal.
- Louvering – Forming a series of parallel, angled slits or vents in sheet metal for ventilation or aesthetic purposes.
- Coining – Using extreme pressure to create precise, detailed impressions on sheet metal surfaces.
Spinning
Spinning involves placing sheet metal on a rotating mandrel/form and using rollers or pressure bars to gradually shape the metal against the mandrel. It produces axially symmetric hollow parts like tubes, funnels, and bowls. Spinning can form complex seamless shapes through localized deformation.
Roll Forming
Roll forming involves gradual bending of sheet metal through a series of contoured rollers. As the sheet metal passes through the rollers, it takes on the shape of the rollers to form the desired bends and curves. This process is ideal for producing parts with long bends or curves like cylindrical tubes.
Hot vs. Cold Forming
Hot forming is done when the sheet metal is heated to increase its malleability, while cold forming is done at room temperature. Hot forming allows more extreme deformation but can affect the material properties and requires heating equipment. Cold forming produces high-precision parts while maintaining the original metal strength. The appropriate method depends on the desired part, tolerances, and material type.
Welding and Fastening
Sheet metal pieces are often joined together to create more complex parts and assemblies. There are several techniques used in sheet metal fabrication for joining.
Arc Welding
A high current electric arc is created between an electrode and the base materials to melt the metals at the joint. As the electrode melts, it provides filler material for the joint. Shielded metal arc welding and gas metal arc welding are common in sheet metal fabrication.
Spot Welding
This is one of the most common methods. Two shaped copper alloy electrodes are pressed against the metal surfaces to be joined. A large electrical current is passed briefly between the electrodes, causing localized melting and fusing of the metal. The heat also allows the surfaces to conform to each other for a tight seal.
Mechanical Fasteners
Rivets, bolts, tabs, and clips can join sheet metal without fusion or adhesives. Mechanical fastening allows nondestructive disassembly for maintenance and repair. It requires holes to be added to the materials.
Bonding Adhesives
Adhesives like epoxies and polyurethanes can be applied between parts to be joined. The adhesive hardens and creates a strong bond with minimal heat. Surface preparation is critical for good adhesion. Adhesives distribute stresses evenly. They add minimal weight and thickness.
Secondary Processing
After the primary fabrication processes are complete, secondary processing is often required before the final product is ready. This includes:
Deburring
Removal of any rough edges, burrs or sharp protrusions left over from cutting, punching or forming. This helps create a smooth and safe finished part. Deburring can be done manually, chemically or with various power tools and machines.
Adding holes, threads, grommets
Precision drilling of holes, tapping threads or inserting grommets allows other components to be attached to the sheet metal. CNC machines ensure these holes and features are correctly aligned and positioned.
Cleaning and Degreasing
Cleaning and degreasing are essential pre-treatment steps before applying any type of surface finish. Contaminants like dirt, oil, grease, oxides, and drawing compounds must be thoroughly removed or they will interfere with proper coating adhesion and lead to coating failures down the line. Common methods for cleaning and degreasing metal surfaces include Solvent Cleaning, Emulsion Cleaning, Alkaline Cleaning, Abrasive Blasting, and Vapor Degreasing
Assembly
Sheet metal fabrication often produces components or sub-assemblies that must be assembled together to create the final product. This may involve additional welding, mechanical fasteners or adhesive bonding. Proper assembly jigs and fixtures are needed to align parts and efficiently put them together.
Secondary processing is an important stage that takes the initial fabricated parts and prepares them for functionality in the end product. Deburring, finishing and adding secondary features are critical steps before the metal fabrication is truly complete.
Surface Finishing
Surface finishing is commonly applied to sheet metal to enhance its properties and appearance. Various finishing processes can improve corrosion resistance, wear resistance, reflectivity, color, and overall aesthetic appeal.
Some popular surface finishing techniques for sheet metal include:
- Painting and coating
- Plating (e.g., electroplating, electroless plating)
- Anodizing
- Galvanizing
- Polishing and grinding
- Blasting
- Thermal spraying
- Physical vapor deposition (PVD) and chemical vapor deposition (CVD)
The choice of surface finishing method depends on the specific requirements of the application, such as the desired properties, environmental conditions, and cost considerations.
For more detailed information on each of these surface finishing processes, please refer to our separate articles dedicated to each technique.
Procurement 101: An Introduction to Metal Finishing
Benefits and Limitations
Sheet metal fabrication offers many advantages as well as some limitations compared to other manufacturing processes.
Benefits
- Speed – Sheet metal parts can be produced very quickly, especially with automated laser and punching equipment. Shorter manufacturing times allow for fast production and quick turnarounds.
- Precision – Modern CNC machines offer extremely precise and repeatable results for cutting and forming. Tolerances under 0.1mm are achievable.
- Material versatility – A very wide range of metals can be formed including steel, aluminum, titanium and copper alloys. Plastics and composites can also be fabricated to some extent.
Limitations
- High tooling costs – The molds, dies and jigs needed for repetitive bending and forming carry high upfront costs. This can make short production runs quite expensive.
- Dimensional limits – There are restrictions on the maximum size of parts that can be pressed and formed. Very large panels are difficult to handle and process.
Comparison with Machining
Sheet metal fabrication is preferred over other processes generally when low to mid production volumes are required, close dimensional tolerances and finishes are needed, and the geometry is suited to bending, punching and welding.
Here we compares sheet metal fabrication and machining, which are two distinct manufacturing processes that have their own unique advantages and limitations.
- Precision – Both machining and sheet metal fabrication can achieve high levels of precision, but machining typically offers tighter tolerances, especially for complex geometries.
- Production Volume – Machining is often more suitable for low-volume production or prototyping, as it does not require extensive tooling or setup. Sheet metal fabrication is more cost-effective for low to medium production volumes, as it can produce parts quickly once the necessary tooling is in place.
- Complexity – Machining can produce more intricate and complex geometries than sheet metal fabrication, which is limited by the capabilities of bending and forming processes.
- Waste – Machining generates more material waste in the form of chips and shavings, whereas sheet metal fabrication minimizes waste by using optimized cutting layouts.
In summary, sheet metal fabrication offers advantages in terms of speed, material usage, and cost-effectiveness for low to medium volume production of parts with relatively simple geometries. Machining, on the other hand, offers greater flexibility in terms of achievable geometries, precision, and material options, making it suitable for a wide range of applications, including low-volume production and prototyping.
What is sheet metal fabrication?
Sheet metal fabrication is the process of shaping thin sheets of metal into useful structures and products. It involves taking flat sheet metal, cutting it into required shapes and sizes, and then bending it into the desired forms.
Sheet metal fabrication has numerous applications across industries like aerospace, automotive, construction, electronics, and manufacturing. It offers several benefits over other manufacturing processes like casting or machining:
- Versatile – A wide range of products from simple brackets to complex enclosures can be fabricated. Sheet metal can be worked into curved, cylindrical and other organic shapes relatively easily.
- Fast and efficient – Modern laser and plasma cutting allow quick and precise cutting of sheet metal. Automated stamping and bending processes enable mass production. Overall, sheet metal fabrication is fast and cost-effective.
- Material conservation – Sheet metal fabrication produces very little waste material compared to machining processes. Complex parts can be made from single sheets using bending, stamping and pressing. This results in significant material savings.
- Strength – Sheet metal parts can be designed to have excellent strength-to-weight ratios. The material thickness can be varied to increase strength in areas under more stress.
- Corrosion resistance – Metals like aluminum and galvanized steel have inherent corrosion resistance. They can withstand exposure to weather elements over long periods. Additional coatings can also enhance corrosion protection.
So in summary, sheet metal fabrication allows quick, efficient and versatile production of lightweight but strong metal components. Its minimal material wastage provides additional cost benefits. These qualities make it ideal for high volume manufacturing across many industries.
Sheet Metal Materials
Sheet metal fabrication utilizes a variety of metals, each with properties that make them suitable for different applications. The most common base metals used are:
- Steel – Steel is the most popular choice for sheet metal due to its high strength, formability, weldability, and relatively low cost. Common forms of steel used include low carbon steel, mild steel, stainless steel, and galvanized steel. Steel is suitable for applications requiring durability, strength, and corrosion resistance.
- Aluminum – Aluminum is lightweight, corrosion resistant, conductive, and easily formed and machined. It is commonly used for electronic enclosures, chemical equipment, appliances, and aircraft components. Aluminum has high reflectivity and a bright, attractive finish.
- Copper – Copper offers excellent conductivity, corrosion resistance, and antimicrobial properties. It is commonly used for electrical wiring, plumbing, heat exchangers, and architectural finishes. The softness and malleability of copper makes it ideal for forming complex parts.
- Brass – Brass is an alloy of copper and zinc that is stronger and more formable than copper. It offers good corrosion resistance and an attractive golden color. Brass is used for musical instruments, valves, and decorative trims.
- Titanium – Titanium offers very high strength-to-weight ratio and excellent corrosion resistance while maintaining formability and weldability. It is used for aircraft, chemical processing, marine applications, and medical implants.
Sheet metal thickness is measured in gauge or inches/millimeters. Gauge refers to the number of sheets per inch of thickness. As gauge number increases, thickness decreases. Common sheet metal gauge sizes are 22 gauge (.70mm) to 10 gauge (3.5mm). For thicker metals, thickness is measured directly in fractional inches or millimeters.
Cutting Processes
There are several main methods for cutting sheet metal in fabrication.
Laser Cutting
Laser cutting uses a high power laser beam to melt and vaporize sheet metal.
- It can cut complex shapes with high accuracy and smooth edges.
- No tooling required so fast design changes are possible.
- More expensive per part than mechanical cutting.
Plasma Cutting
Plasma cutting uses a high-velocity jet of ionized gas (plasma) to melt and expel material from the cutting area.
- It can quickly cut through thick sheets of electrically conductive materials, such as steel and aluminum.
- Produces a clean, relatively smooth edge with a narrow kerf (cut width).
- Faster and more economical than laser cutting for thicker materials.
- Limited to conductive materials and may produce some heat-affected zones.
Waterjet Cutting
Waterjet cutting uses an extremely high pressure stream of water with abrasives to erode sheet metal.
- It can cut precise and complex shapes in almost any material.
- No heat damage or fumes compared to laser cutting.
- Slower than laser and more expensive to operate.
Punching
Punching uses a machine press, such as CNC turret punch machines, with tool and die sets to punch holes or shapes out of sheet metal.
- Very fast process for high volume hole patterns or shapes.
- Limited to simple geometries compared to laser and waterjet cutting.
- Low operating costs once initial tooling investment is made.
Shearing
Shearing uses a machine press with a guillotine blade to slice sheet metal.
- Fast and economical process for cutting flat patterns out of sheet metal.
- Accuracy and edge quality may be lower than other cutting methods.
- Works for sheets up to 10mm thickness.
Bending and Forming
Sheet metal must be formed or bent to create many end products or parts. There are several common bending and forming processes used in sheet metal fabrication.
Press Braking
Press braking uses a machine press with a V-shaped die to bend sheet metal. A bottom die supports the sheet while the upper die presses down to create precise and repeatable bends. Press brakes are commonly used to create folds and box-like structures out of sheet metal.
Slip Rolling
In slip rolling, sheet metal is passed between cylindrical/conical shaped rollers which exert pressure to bend the metal. Slip rolling forms cones and cylindrical shapes through a cold rolling process. It can bend metal up to 180 degrees using multiple passes through the rollers.
Stamping
Stamping is a high-volume, cost-effective cold forming process that uses dies and punches to shape sheet metal into various parts and features, such as holes, flanges, and embossments.
Flaring (or Flanging)
Flaring, also known as flanging, is a process that forms a flared or flanged edge on a sheet metal part, often used to create a lip or rim for joining or reinforcing the part.
Other Forming Methods
Other specialized forming methods that require custom dies include:
- Embossing – Creating raised or recessed designs on the surface of sheet metal.
- Louvering – Forming a series of parallel, angled slits or vents in sheet metal for ventilation or aesthetic purposes.
- Coining – Using extreme pressure to create precise, detailed impressions on sheet metal surfaces.
Spinning
Spinning involves placing sheet metal on a rotating mandrel/form and using rollers or pressure bars to gradually shape the metal against the mandrel. It produces axially symmetric hollow parts like tubes, funnels, and bowls. Spinning can form complex seamless shapes through localized deformation.
Roll Forming
Roll forming involves gradual bending of sheet metal through a series of contoured rollers. As the sheet metal passes through the rollers, it takes on the shape of the rollers to form the desired bends and curves. This process is ideal for producing parts with long bends or curves like cylindrical tubes.
Hot vs. Cold Forming
Hot forming is done when the sheet metal is heated to increase its malleability, while cold forming is done at room temperature. Hot forming allows more extreme deformation but can affect the material properties and requires heating equipment. Cold forming produces high-precision parts while maintaining the original metal strength. The appropriate method depends on the desired part, tolerances, and material type.
Welding and Fastening
Sheet metal pieces are often joined together to create more complex parts and assemblies. There are several techniques used in sheet metal fabrication for joining.
Arc Welding
A high current electric arc is created between an electrode and the base materials to melt the metals at the joint. As the electrode melts, it provides filler material for the joint. Shielded metal arc welding and gas metal arc welding are common in sheet metal fabrication.
Spot Welding
This is one of the most common methods. Two shaped copper alloy electrodes are pressed against the metal surfaces to be joined. A large electrical current is passed briefly between the electrodes, causing localized melting and fusing of the metal. The heat also allows the surfaces to conform to each other for a tight seal.
Mechanical Fasteners
Rivets, bolts, tabs, and clips can join sheet metal without fusion or adhesives. Mechanical fastening allows nondestructive disassembly for maintenance and repair. It requires holes to be added to the materials.
Bonding Adhesives
Adhesives like epoxies and polyurethanes can be applied between parts to be joined. The adhesive hardens and creates a strong bond with minimal heat. Surface preparation is critical for good adhesion. Adhesives distribute stresses evenly. They add minimal weight and thickness.
Secondary Processing
After the primary fabrication processes are complete, secondary processing is often required before the final product is ready. This includes:
Deburring
Removal of any rough edges, burrs or sharp protrusions left over from cutting, punching or forming. This helps create a smooth and safe finished part. Deburring can be done manually, chemically or with various power tools and machines.
Adding holes, threads, grommets
Precision drilling of holes, tapping threads or inserting grommets allows other components to be attached to the sheet metal. CNC machines ensure these holes and features are correctly aligned and positioned.
Cleaning and Degreasing
Cleaning and degreasing are essential pre-treatment steps before applying any type of surface finish. Contaminants like dirt, oil, grease, oxides, and drawing compounds must be thoroughly removed or they will interfere with proper coating adhesion and lead to coating failures down the line. Common methods for cleaning and degreasing metal surfaces include Solvent Cleaning, Emulsion Cleaning, Alkaline Cleaning, Abrasive Blasting, and Vapor Degreasing
Assembly
Sheet metal fabrication often produces components or sub-assemblies that must be assembled together to create the final product. This may involve additional welding, mechanical fasteners or adhesive bonding. Proper assembly jigs and fixtures are needed to align parts and efficiently put them together.
Secondary processing is an important stage that takes the initial fabricated parts and prepares them for functionality in the end product. Deburring, finishing and adding secondary features are critical steps before the metal fabrication is truly complete.
Surface Finishing
Surface finishing is commonly applied to sheet metal to enhance its properties and appearance. Various finishing processes can improve corrosion resistance, wear resistance, reflectivity, color, and overall aesthetic appeal.
Some popular surface finishing techniques for sheet metal include:
- Painting and coating
- Plating (e.g., electroplating, electroless plating)
- Anodizing
- Galvanizing
- Polishing and grinding
- Blasting
- Thermal spraying
- Physical vapor deposition (PVD) and chemical vapor deposition (CVD)
The choice of surface finishing method depends on the specific requirements of the application, such as the desired properties, environmental conditions, and cost considerations.
For more detailed information on each of these surface finishing processes, please refer to our separate articles dedicated to each technique.
Procurement 101: An Introduction to Metal Finishing
Benefits and Limitations
Sheet metal fabrication offers many advantages as well as some limitations compared to other manufacturing processes.
Benefits
- Speed – Sheet metal parts can be produced very quickly, especially with automated laser and punching equipment. Shorter manufacturing times allow for fast production and quick turnarounds.
- Precision – Modern CNC machines offer extremely precise and repeatable results for cutting and forming. Tolerances under 0.1mm are achievable.
- Material versatility – A very wide range of metals can be formed including steel, aluminum, titanium and copper alloys. Plastics and composites can also be fabricated to some extent.
Limitations
- High tooling costs – The molds, dies and jigs needed for repetitive bending and forming carry high upfront costs. This can make short production runs quite expensive.
- Dimensional limits – There are restrictions on the maximum size of parts that can be pressed and formed. Very large panels are difficult to handle and process.
Comparison with Machining
Sheet metal fabrication is preferred over other processes generally when low to mid production volumes are required, close dimensional tolerances and finishes are needed, and the geometry is suited to bending, punching and welding.
Here we compares sheet metal fabrication and machining, which are two distinct manufacturing processes that have their own unique advantages and limitations.
- Precision – Both machining and sheet metal fabrication can achieve high levels of precision, but machining typically offers tighter tolerances, especially for complex geometries.
- Production Volume – Machining is often more suitable for low-volume production or prototyping, as it does not require extensive tooling or setup. Sheet metal fabrication is more cost-effective for low to medium production volumes, as it can produce parts quickly once the necessary tooling is in place.
- Complexity – Machining can produce more intricate and complex geometries than sheet metal fabrication, which is limited by the capabilities of bending and forming processes.
- Waste – Machining generates more material waste in the form of chips and shavings, whereas sheet metal fabrication minimizes waste by using optimized cutting layouts.
In summary, sheet metal fabrication offers advantages in terms of speed, material usage, and cost-effectiveness for low to medium volume production of parts with relatively simple geometries. Machining, on the other hand, offers greater flexibility in terms of achievable geometries, precision, and material options, making it suitable for a wide range of applications, including low-volume production and prototyping.
Ready to see CADDi Drawer in action? Get a personalized demo.
Subscribe to our Blog!
Related Resources

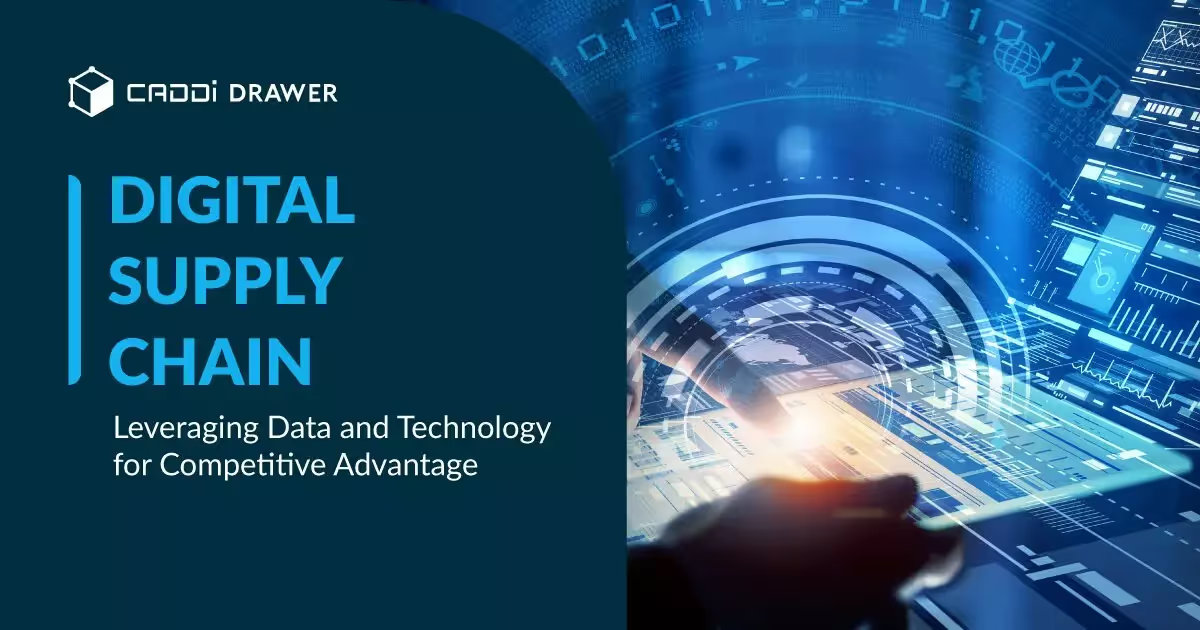
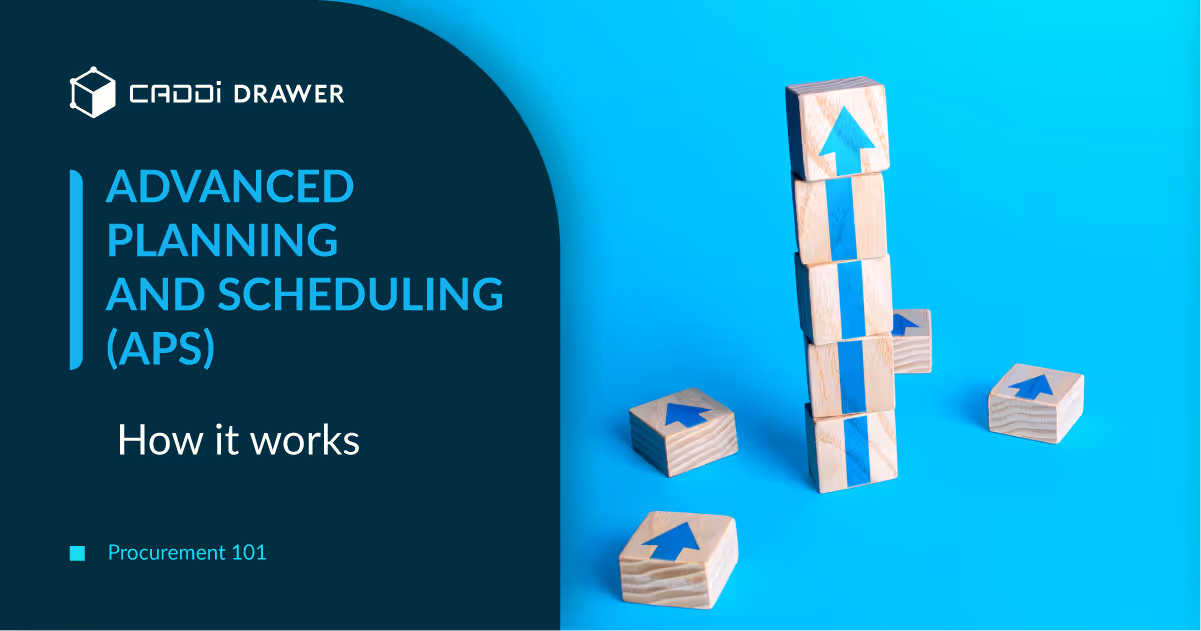
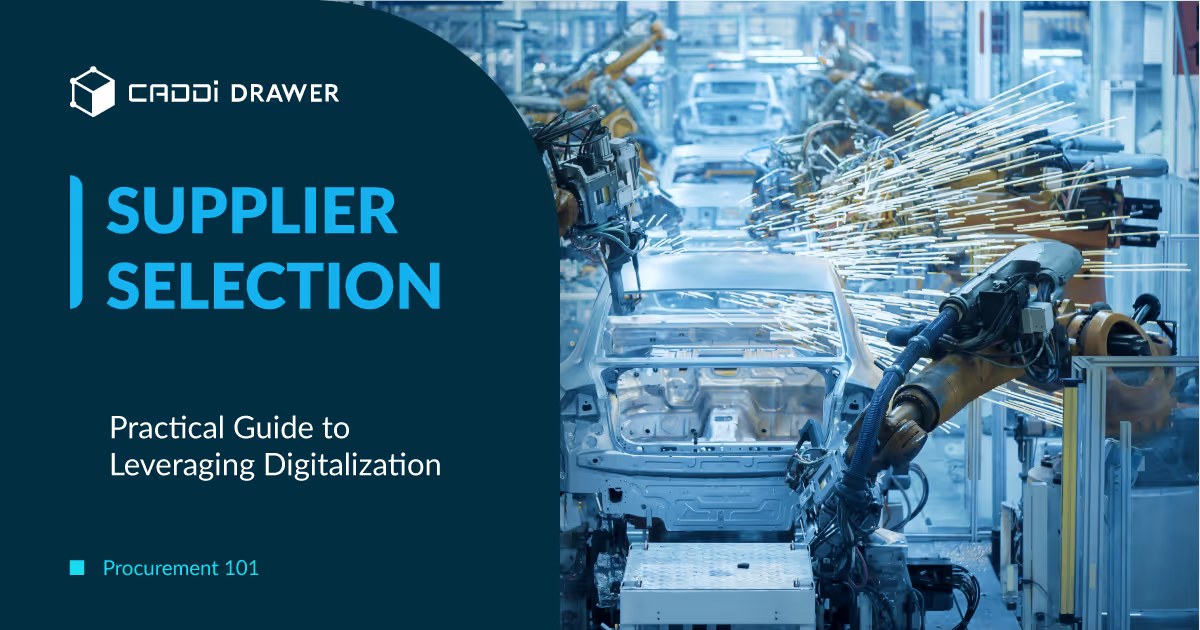
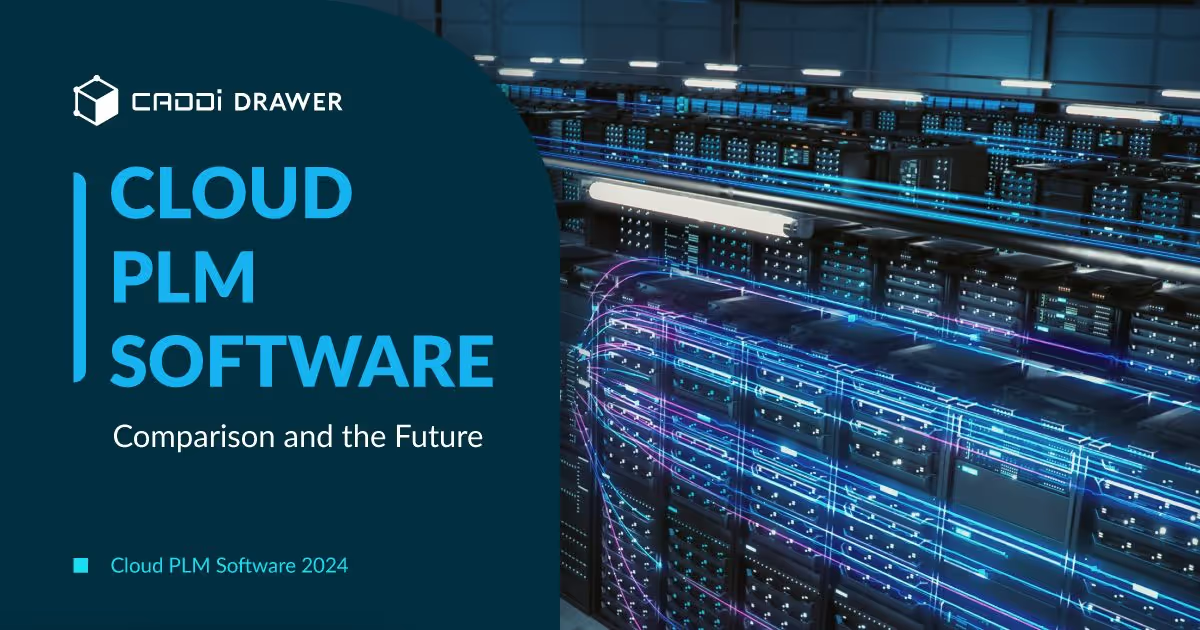
