The Roadmap to Supply Chain Transformation: A Step-by-Step Guide to Strategic Planning
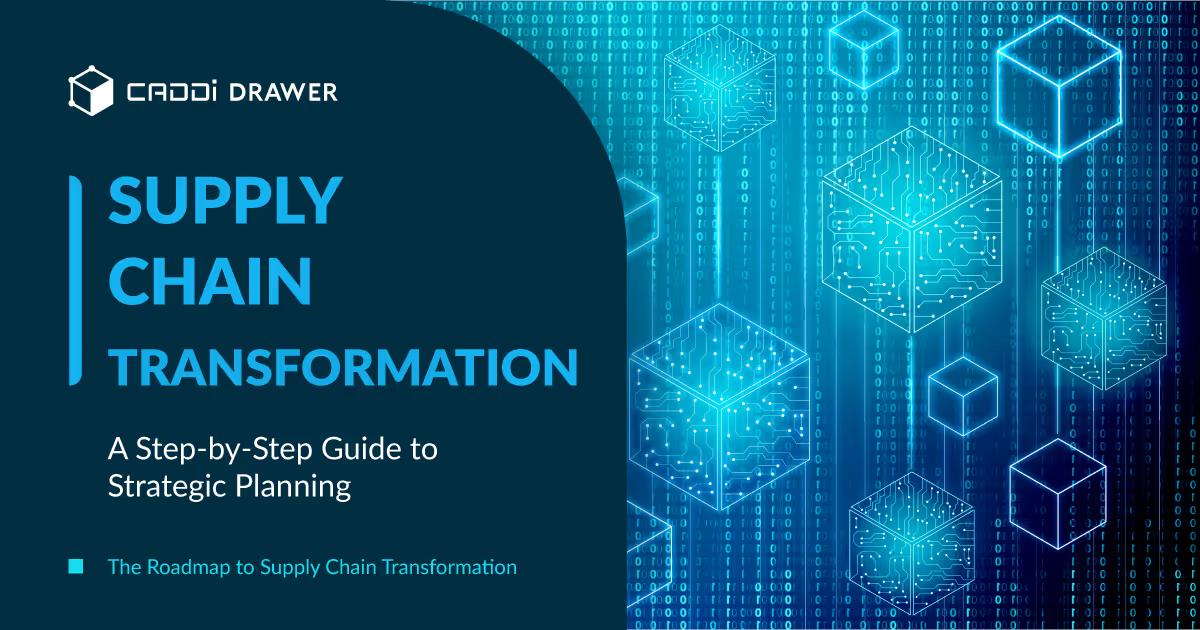
Table of Contents
Why Supply Chain Transformation Is Critical Today
The pandemic exposed supply chain weaknesses globally. Disruptions in manufacturing, transportation, and logistics made meeting demand difficult. Transformation is needed for resilience, agility, and efficiency.
Visibility and real-time data are crucial to predict disruptions. Digitization and automation streamline processes. New technologies optimize ROI. Proactive transformation enhances supplier collaboration, inventory management, logistics, and customer experience for competitive advantage.
With rising expectations and complexity, intelligent supply chains create value and prepare organizations for the future. Transformation is imperative now.
Assess Current State
The first step in creating a strategic roadmap is to thoroughly assess your current supply chain operations. This involves mapping out all existing processes, partnerships, costs and identifying areas for improvement.
- Map current processes: Document the full end-to-end workflow from sourcing to delivery. Define the steps, inputs and outputs for each process while highlighting process bottlenecks, redundancies and inefficiencies.
- Identify partners: Make a list of all supply chain partners involved including suppliers, 3PLs, transportation providers, IT solution vendors, etc. Analyze existing contracts and relationships.
- Understand costs: Gather data on supply chain costs by category and activity. This includes procurement, inventory carrying costs, transportation and logistics, IT, overhead, etc. Link costs to specific processes and partnerships.
Conducting a detailed assessment establishes the current state baseline from which the future vision and roadmap can be built upon. The goal is to thoroughly understand how the supply chain operates today in order to identify the most impactful areas to target for improvement.
Identify Pain Points
To create an effective supply chain transformation roadmap, it’s critical to identify current pain points and inefficiencies. This involves taking a deep look at the supply chain to determine:
Where Are Inefficiencies and Waste?
- Long lead times
- Excess inventory carrying costs
- Quality issues leading to rework
- Poor forecasting accuracy
- Excess transportation costs
- Manual processes and data errors
- Lack of visibility across the supply chain
Where Are There Risks?
- Single points of failure
- Lack of supplier redundancy
- Exposure to natural disasters, geopolitical issues
- Cybersecurity vulnerabilities
- Compliance risks
- Poor business continuity planning
What Are the Biggest Opportunities for Improvement?
Prioritize addressing pain points that enable the biggest potential savings and improvements. Look for areas with:
- High costs that can be reduced
- Quality and customer service issues
- Greatest inefficiency and waste
- Highest risk exposure
Carefully analyzing and quantifying pain points provides the foundation for mapping supply chain transformation priorities and initiatives.
Define Future Vision
For this step, focus on envisioning the ideal future state for your supply chain. As the saying goes, you need to begin with the end in mind. Define what an excellent, world-class supply chain would look like for your company 3-5 years in the future.
- What will your key supply chain metrics be? Improved perfect order fulfillment? Reduced cash-to-cash cycle time? Increased inventory turns? Determine the KPIs that indicate supply chain success.
- What capabilities will your future supply chain have? Increased visibility through real-time data sharing with suppliers? Integrated sales and operations planning? Enhanced distribution center automation? Define the critical capabilities needed.
- How will your supply chain enable corporate strategy and what value will it bring? Supporting business growth into new markets and channels? Enabling fast delivery of new products? Delivering on sustainability goals? Link the future vision to strategic objectives.
- What does your future operating model look like? Are there organizational changes, new roles, or external partnerships needed? Detail the operating model.
- Describe the overall customer experience your future supply chain will enable. How will it improve service levels and remove friction?
Clearly defining the ideal future state provides direction and aligns stakeholders. It acts as the North Star guiding strategic priorities and transformation initiatives. Vividly depict what excellence looks like across key metrics, capabilities, alignment to strategy, operating model, and customer experience. This future vision sets the stage for mapping out the journey ahead.
Strategic Priorities
When developing a strategic roadmap for supply chain transformation, it’s critical to identify and prioritize the key focus areas that will drive the most value. This requires taking a step back to look at the end-to-end supply chain holistically, rather than getting lost in functional silos. Some top priorities to consider include:
- Customer-centricity – Putting the customer at the heart of supply chain priorities and processes. This may require changes to how sales and operations planning is done, introducing customer-driven metrics, and mapping processes from the outside-in.
- Agility and resilience – Building in the ability to rapidly respond to changes in demand or supply disruptions. This can be enabled through supply chain segmentation, increasing supply chain visibility, and introducing flexibility in production and logistics.
- Sustainability – Incorporating environmental and social sustainability into supply chain decision making. This may include supplier selection criteria, transportation mode optimization, packaging reduction, and circular economy initiatives.
- Talent development – Investing in upskilling the current workforce and recruiting new skills needed for the future supply chain. Change management and training will be critical to enable the workforce to adopt new technologies and processes.
- Innovation – Leveraging new technologies and digital capabilities to enable transformation, including automation, advanced analytics, AI/ML, control towers, and IoT. Innovation needs to become a core competency across the supply chain.
- Collaboration – Increased collaboration and shared goals across functions and with external supply chain partners. This requires breaking down silos and taking an end-to-end view.
By identifying and prioritizing strategic focus areas in this way, companies can develop a transformation roadmap that drives maximum value.
Roadmap Development
Once the strategic priorities have been identified, the next step is to map specific initiatives to the timeline for achieving the future vision. This involves:
- Clearly defining each initiative and its scope
- Identifying hard dependencies between initiatives
- Sequencing the initiatives in a logical order
- Assigning broad timeframes for short, medium and long-term
- Identifying initiative owners and working teams
- Mapping initiatives visually on a timeline roadmap
The key is to break down the transformation into manageable chunks that can be executed and tracked incrementally. Each initiative should have clear objectives, roles and interim milestones.
There should be a healthy balance of short and long-term initiatives. The short-term ones enable quick wins and momentum, while the longer-term ones align to the bigger strategic goals.
The timeline should have in-built flexibility to adapt as changes occur over the transformation journey. The roadmap is a living document and regular reviews must be scheduled to update the status of initiatives.
As owners drive initiatives, they should coordinate with each other on interdependencies for smooth overall execution. The transformation program oversight team provides guidance and support as needed.
Technology Enablement
Technology is a critical enabler of supply chain transformation initiatives. Companies need to assess their current technology landscape and identify gaps that may inhibit transformation. Some key technology considerations include:
- Cloud platforms: Migrating supply chain systems to the cloud enables greater scalability, flexibility and analytics capabilities. Cloud ERP, warehouse management systems, transportation management systems and supply chain control towers provide needed agility.
- Automation: Automating repetitive tasks through robotics and AI frees up employees for higher value work and improves efficiency. This includes warehouse automation, predictive analytics and cognitive technologies.
- IoT & sensors: Connecting assets through the Internet of Things provides real-time visibility into operations. RFID tags, sensors and connected fleet enable proactive issue resolution.
- Advanced AI technologies: Advanced analytics and machine learning extract insights from large data sets, unstructured data and Retrieval Augmented Generation (RAG)-powered systems in supply chain management. This powers demand forecasting, dynamic planning and Prescriptive Analytics.
- Digital collaboration: Platforms like procurement intelligence systems and supplier portals break down silos and promote collaboration across the extended supply chain.
Companies must invest in technologies that enable transformation use cases rather than implementing technology for its own sake. The right technologies tailored to strategic priorities provide the digital foundation for supply chain success.
Change Management
Most supply chain transformations require people across the organization to change their ways of working. A strategic change management program is crucial to gain buy-in for the transformation, prepare stakeholders for changes, and drive adoption of new processes and technology.
Key aspects of change management include:
- Identify key stakeholders and determine change impact – Understand who will be impacted by the transformation, and conduct impact assessments to determine the breadth and depth of change at individual job levels.
- Develop customized change plans for stakeholders – Create detailed plans tailored to each stakeholder group describing the transformation, benefits, timeline, impacts on roles, required training, and how stakeholders will be supported.
- Communications and training – Provide frequent, transparent communication about the changes through multiple channels. Offer extensive training and resources to build new capabilities and skills required for transformed roles and processes.
- Leadership alignment – Ensure leaders actively participate in the change program through their own training, regular communications, and visibly modeling desired changes.
- Resistance management – Proactively identify potential resistance, understand underlying causes, and develop targeted mitigation plans, such as additional training, stakeholder involvement in design, piloting changes, or incentives.
- Adoption tracking – Put metrics and feedback channels in place to monitor adoption of changes and take corrective actions to address lagging adoption.
- Celebrate wins – Recognize successful adoption and results through celebrations and rewards to reinforce changes.
With an effective change management approach, the organization will be well-prepared for the transformation journey ahead. Employees will have the mindsets, capabilities, and motivation to successfully adopt the end-state vision.
Performance Tracking
To ensure the supply chain transformation roadmap is effective, it’s critical to establish key performance indicators (KPIs) to track progress. Some recommended KPIs to monitor include:
- Order cycle time – Measure the time it takes from order creation to delivery. Reductions indicate improved efficiency.
- Forecast accuracy – Track how close forecasts come to actual demand. Improvements show better demand planning.
- Inventory turns – Calculate how many times a year inventory is turned over and sold. Higher turns mean less excess stock.
- Perfect order percentage – Monitor the % of orders delivered complete, on-time, damage-free and with accurate documentation.
- Transportation costs – Track spending on transportation as a % of sales. Declines suggest savings from network optimization.
- Supplier lead time – Measure the time from order to receipt for purchased materials. Faster times demonstrate supplier improvement.
- On-time delivery – Calculate % of orders arriving on the scheduled delivery date. Increases show greater reliability.
- Sustainability metrics – Track waste reduction, carbon footprint, energy use to monitor environmental impact.
Regularly reviewing KPIs versus targets will indicate where the transformation roadmap is succeeding or needs adjustment. KPIs provide quantitative insights to help manage progress.
Conclusion
Supply chain transformation is an ongoing journey, not a one-time event. The strategic roadmap provides direction, but it must be revisited and updated regularly. Continuously monitor performance, gather feedback, and identify new opportunities for improvement.
The supply chain environment is constantly evolving. Agility and adaptability will allow the supply chain to continuously improve over time. The strategic roadmap is not a static document; it must be revisited frequently to keep pace with change. By making incremental enhancements, the supply chain will steadily increase efficiency, resiliency, and competitive advantage.
Why Supply Chain Transformation Is Critical Today
The pandemic exposed supply chain weaknesses globally. Disruptions in manufacturing, transportation, and logistics made meeting demand difficult. Transformation is needed for resilience, agility, and efficiency.
Visibility and real-time data are crucial to predict disruptions. Digitization and automation streamline processes. New technologies optimize ROI. Proactive transformation enhances supplier collaboration, inventory management, logistics, and customer experience for competitive advantage.
With rising expectations and complexity, intelligent supply chains create value and prepare organizations for the future. Transformation is imperative now.
Assess Current State
The first step in creating a strategic roadmap is to thoroughly assess your current supply chain operations. This involves mapping out all existing processes, partnerships, costs and identifying areas for improvement.
- Map current processes: Document the full end-to-end workflow from sourcing to delivery. Define the steps, inputs and outputs for each process while highlighting process bottlenecks, redundancies and inefficiencies.
- Identify partners: Make a list of all supply chain partners involved including suppliers, 3PLs, transportation providers, IT solution vendors, etc. Analyze existing contracts and relationships.
- Understand costs: Gather data on supply chain costs by category and activity. This includes procurement, inventory carrying costs, transportation and logistics, IT, overhead, etc. Link costs to specific processes and partnerships.
Conducting a detailed assessment establishes the current state baseline from which the future vision and roadmap can be built upon. The goal is to thoroughly understand how the supply chain operates today in order to identify the most impactful areas to target for improvement.
Identify Pain Points
To create an effective supply chain transformation roadmap, it’s critical to identify current pain points and inefficiencies. This involves taking a deep look at the supply chain to determine:
Where Are Inefficiencies and Waste?
- Long lead times
- Excess inventory carrying costs
- Quality issues leading to rework
- Poor forecasting accuracy
- Excess transportation costs
- Manual processes and data errors
- Lack of visibility across the supply chain
Where Are There Risks?
- Single points of failure
- Lack of supplier redundancy
- Exposure to natural disasters, geopolitical issues
- Cybersecurity vulnerabilities
- Compliance risks
- Poor business continuity planning
What Are the Biggest Opportunities for Improvement?
Prioritize addressing pain points that enable the biggest potential savings and improvements. Look for areas with:
- High costs that can be reduced
- Quality and customer service issues
- Greatest inefficiency and waste
- Highest risk exposure
Carefully analyzing and quantifying pain points provides the foundation for mapping supply chain transformation priorities and initiatives.
Define Future Vision
For this step, focus on envisioning the ideal future state for your supply chain. As the saying goes, you need to begin with the end in mind. Define what an excellent, world-class supply chain would look like for your company 3-5 years in the future.
- What will your key supply chain metrics be? Improved perfect order fulfillment? Reduced cash-to-cash cycle time? Increased inventory turns? Determine the KPIs that indicate supply chain success.
- What capabilities will your future supply chain have? Increased visibility through real-time data sharing with suppliers? Integrated sales and operations planning? Enhanced distribution center automation? Define the critical capabilities needed.
- How will your supply chain enable corporate strategy and what value will it bring? Supporting business growth into new markets and channels? Enabling fast delivery of new products? Delivering on sustainability goals? Link the future vision to strategic objectives.
- What does your future operating model look like? Are there organizational changes, new roles, or external partnerships needed? Detail the operating model.
- Describe the overall customer experience your future supply chain will enable. How will it improve service levels and remove friction?
Clearly defining the ideal future state provides direction and aligns stakeholders. It acts as the North Star guiding strategic priorities and transformation initiatives. Vividly depict what excellence looks like across key metrics, capabilities, alignment to strategy, operating model, and customer experience. This future vision sets the stage for mapping out the journey ahead.
Strategic Priorities
When developing a strategic roadmap for supply chain transformation, it’s critical to identify and prioritize the key focus areas that will drive the most value. This requires taking a step back to look at the end-to-end supply chain holistically, rather than getting lost in functional silos. Some top priorities to consider include:
- Customer-centricity – Putting the customer at the heart of supply chain priorities and processes. This may require changes to how sales and operations planning is done, introducing customer-driven metrics, and mapping processes from the outside-in.
- Agility and resilience – Building in the ability to rapidly respond to changes in demand or supply disruptions. This can be enabled through supply chain segmentation, increasing supply chain visibility, and introducing flexibility in production and logistics.
- Sustainability – Incorporating environmental and social sustainability into supply chain decision making. This may include supplier selection criteria, transportation mode optimization, packaging reduction, and circular economy initiatives.
- Talent development – Investing in upskilling the current workforce and recruiting new skills needed for the future supply chain. Change management and training will be critical to enable the workforce to adopt new technologies and processes.
- Innovation – Leveraging new technologies and digital capabilities to enable transformation, including automation, advanced analytics, AI/ML, control towers, and IoT. Innovation needs to become a core competency across the supply chain.
- Collaboration – Increased collaboration and shared goals across functions and with external supply chain partners. This requires breaking down silos and taking an end-to-end view.
By identifying and prioritizing strategic focus areas in this way, companies can develop a transformation roadmap that drives maximum value.
Roadmap Development
Once the strategic priorities have been identified, the next step is to map specific initiatives to the timeline for achieving the future vision. This involves:
- Clearly defining each initiative and its scope
- Identifying hard dependencies between initiatives
- Sequencing the initiatives in a logical order
- Assigning broad timeframes for short, medium and long-term
- Identifying initiative owners and working teams
- Mapping initiatives visually on a timeline roadmap
The key is to break down the transformation into manageable chunks that can be executed and tracked incrementally. Each initiative should have clear objectives, roles and interim milestones.
There should be a healthy balance of short and long-term initiatives. The short-term ones enable quick wins and momentum, while the longer-term ones align to the bigger strategic goals.
The timeline should have in-built flexibility to adapt as changes occur over the transformation journey. The roadmap is a living document and regular reviews must be scheduled to update the status of initiatives.
As owners drive initiatives, they should coordinate with each other on interdependencies for smooth overall execution. The transformation program oversight team provides guidance and support as needed.
Technology Enablement
Technology is a critical enabler of supply chain transformation initiatives. Companies need to assess their current technology landscape and identify gaps that may inhibit transformation. Some key technology considerations include:
- Cloud platforms: Migrating supply chain systems to the cloud enables greater scalability, flexibility and analytics capabilities. Cloud ERP, warehouse management systems, transportation management systems and supply chain control towers provide needed agility.
- Automation: Automating repetitive tasks through robotics and AI frees up employees for higher value work and improves efficiency. This includes warehouse automation, predictive analytics and cognitive technologies.
- IoT & sensors: Connecting assets through the Internet of Things provides real-time visibility into operations. RFID tags, sensors and connected fleet enable proactive issue resolution.
- Advanced AI technologies: Advanced analytics and machine learning extract insights from large data sets, unstructured data and Retrieval Augmented Generation (RAG)-powered systems in supply chain management. This powers demand forecasting, dynamic planning and Prescriptive Analytics.
- Digital collaboration: Platforms like procurement intelligence systems and supplier portals break down silos and promote collaboration across the extended supply chain.
Companies must invest in technologies that enable transformation use cases rather than implementing technology for its own sake. The right technologies tailored to strategic priorities provide the digital foundation for supply chain success.
Change Management
Most supply chain transformations require people across the organization to change their ways of working. A strategic change management program is crucial to gain buy-in for the transformation, prepare stakeholders for changes, and drive adoption of new processes and technology.
Key aspects of change management include:
- Identify key stakeholders and determine change impact – Understand who will be impacted by the transformation, and conduct impact assessments to determine the breadth and depth of change at individual job levels.
- Develop customized change plans for stakeholders – Create detailed plans tailored to each stakeholder group describing the transformation, benefits, timeline, impacts on roles, required training, and how stakeholders will be supported.
- Communications and training – Provide frequent, transparent communication about the changes through multiple channels. Offer extensive training and resources to build new capabilities and skills required for transformed roles and processes.
- Leadership alignment – Ensure leaders actively participate in the change program through their own training, regular communications, and visibly modeling desired changes.
- Resistance management – Proactively identify potential resistance, understand underlying causes, and develop targeted mitigation plans, such as additional training, stakeholder involvement in design, piloting changes, or incentives.
- Adoption tracking – Put metrics and feedback channels in place to monitor adoption of changes and take corrective actions to address lagging adoption.
- Celebrate wins – Recognize successful adoption and results through celebrations and rewards to reinforce changes.
With an effective change management approach, the organization will be well-prepared for the transformation journey ahead. Employees will have the mindsets, capabilities, and motivation to successfully adopt the end-state vision.
Performance Tracking
To ensure the supply chain transformation roadmap is effective, it’s critical to establish key performance indicators (KPIs) to track progress. Some recommended KPIs to monitor include:
- Order cycle time – Measure the time it takes from order creation to delivery. Reductions indicate improved efficiency.
- Forecast accuracy – Track how close forecasts come to actual demand. Improvements show better demand planning.
- Inventory turns – Calculate how many times a year inventory is turned over and sold. Higher turns mean less excess stock.
- Perfect order percentage – Monitor the % of orders delivered complete, on-time, damage-free and with accurate documentation.
- Transportation costs – Track spending on transportation as a % of sales. Declines suggest savings from network optimization.
- Supplier lead time – Measure the time from order to receipt for purchased materials. Faster times demonstrate supplier improvement.
- On-time delivery – Calculate % of orders arriving on the scheduled delivery date. Increases show greater reliability.
- Sustainability metrics – Track waste reduction, carbon footprint, energy use to monitor environmental impact.
Regularly reviewing KPIs versus targets will indicate where the transformation roadmap is succeeding or needs adjustment. KPIs provide quantitative insights to help manage progress.
Conclusion
Supply chain transformation is an ongoing journey, not a one-time event. The strategic roadmap provides direction, but it must be revisited and updated regularly. Continuously monitor performance, gather feedback, and identify new opportunities for improvement.
The supply chain environment is constantly evolving. Agility and adaptability will allow the supply chain to continuously improve over time. The strategic roadmap is not a static document; it must be revisited frequently to keep pace with change. By making incremental enhancements, the supply chain will steadily increase efficiency, resiliency, and competitive advantage.
Ready to see CADDi Drawer in action? Get a personalized demo.
Subscribe to our Blog!
Related Resources
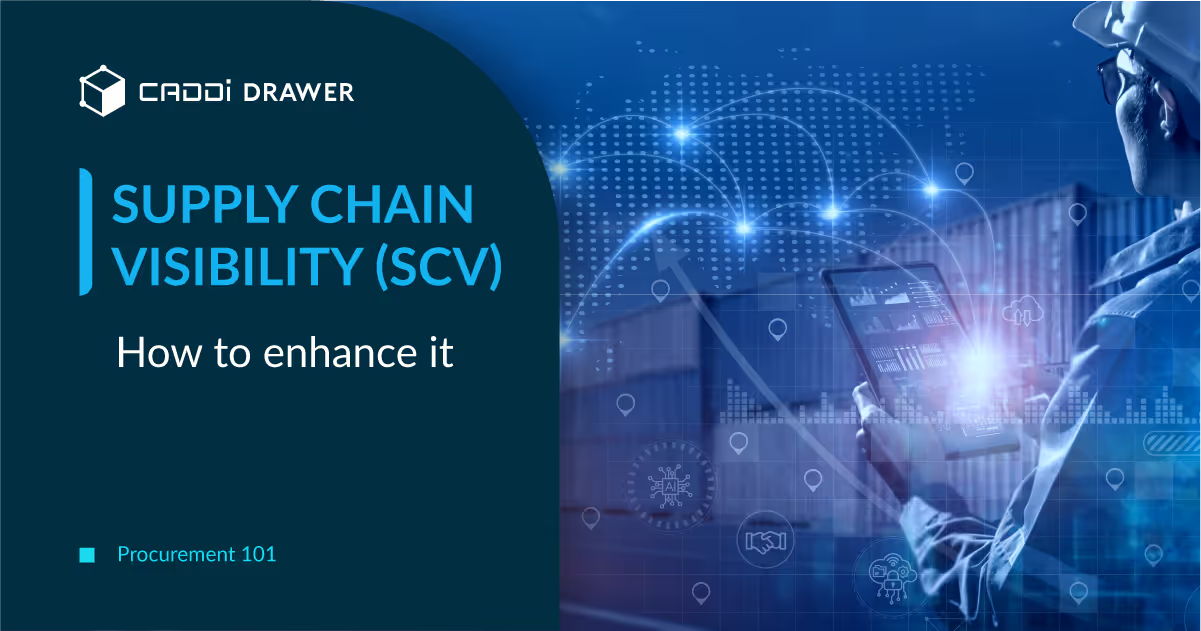

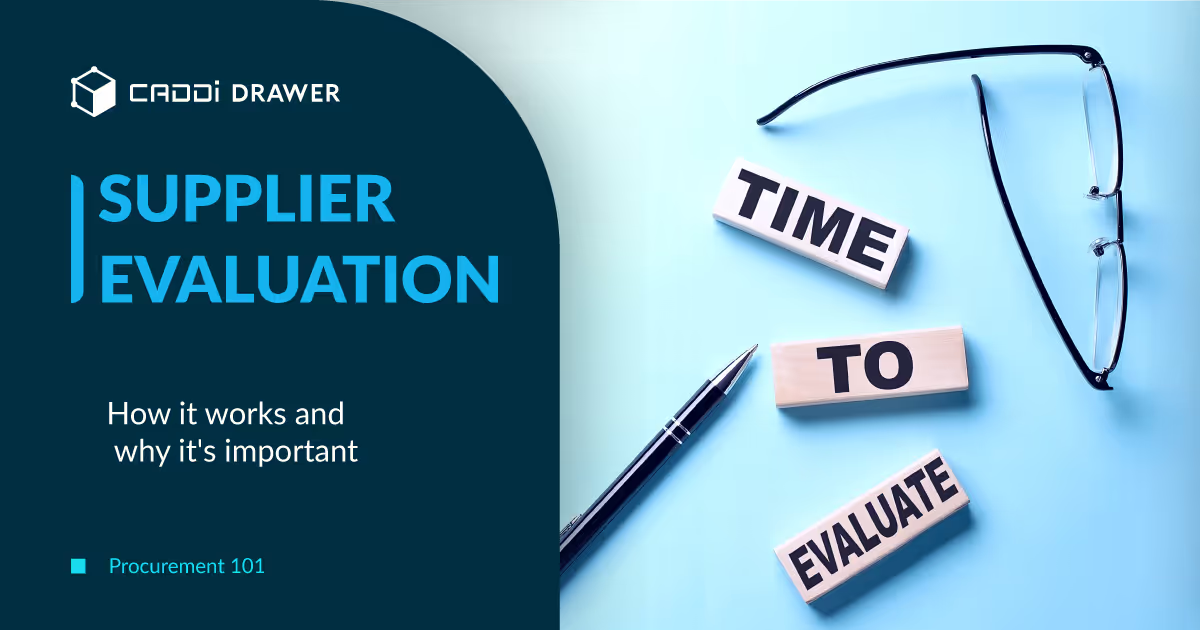

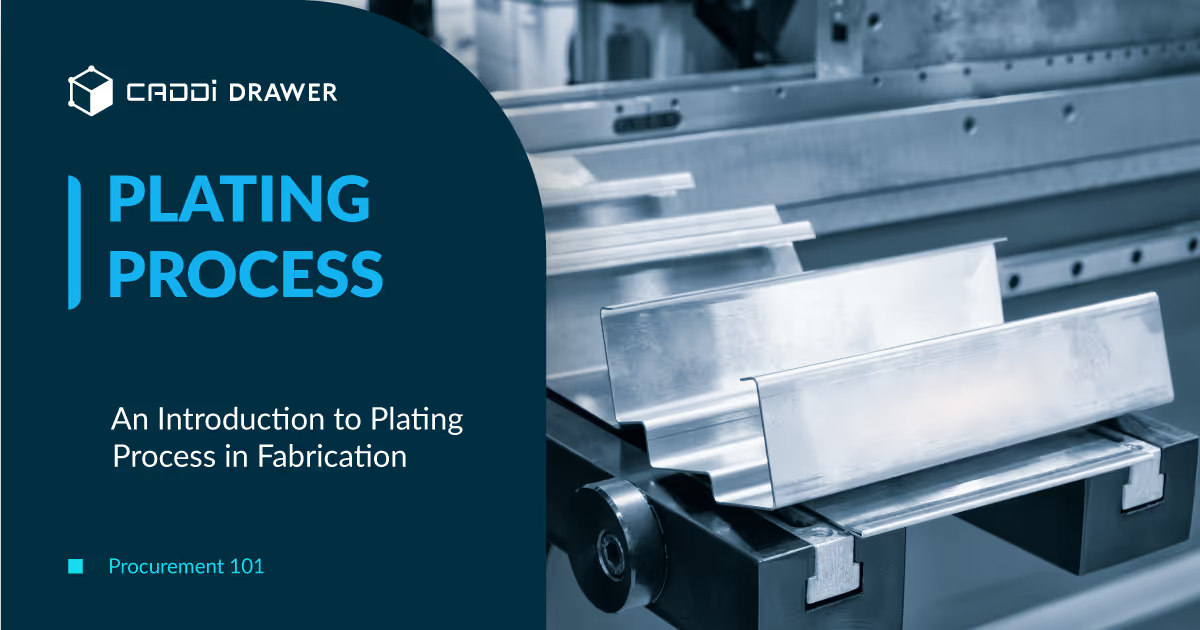
