Procurement 101: An Introduction to Plating Process in Fabrication
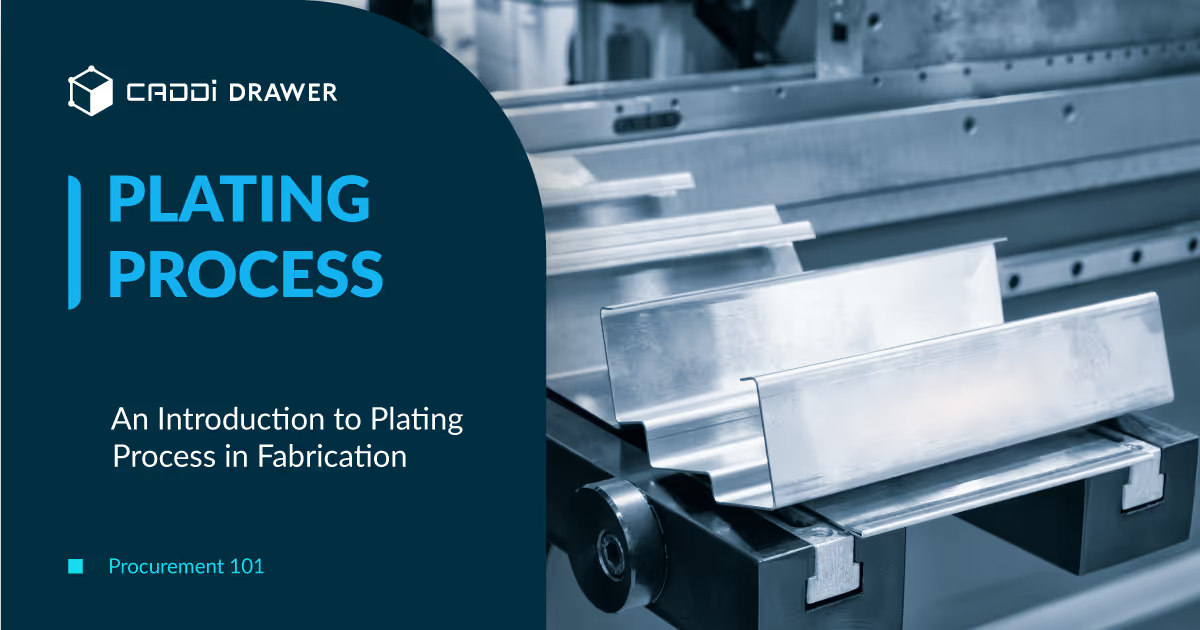
Table of Contents
Plating is an important surface finishing process used in custom fabrication to coat materials with a thin layer of metal. The plating process applies a metal coating to a conductive surface through chemical reactions and electricity.
Plating allows designers and fabricators to enhance the properties and appearance of base materials. It provides materials with improved corrosion and wear resistance, increased hardness, lubricity or solderability, and an attractive decorative finish. This makes plating a versatile process that enables durable and aesthetically appealing custom fabricated parts and products.
The plating process bonds a thin layer of the plating metal onto the base material through electroplating or electroless plating methods. Proper surface preparation, plating solutions, and equipment help ensure high quality and consistent plating results. Understanding the plating process enables custom fabricators to choose suitable techniques and achieve the desired properties in finished components.
Common Plating Processes
Plating in custom fabrication typically refers to electroplating or electroless plating processes. There are a few other less common plating methods as well.
- Electroplating involves using an electrical current to reduce dissolved metal cations so that they form a thin coating on the surface of a conductive material. The part to be plated serves as the cathode (negative electrode) in the electrolytic cell.
- Electroless plating involves an autocatalytic chemical reducing agent in solution to deposit metal without the use of an external electrical current. It allows plating of non-conductive surfaces.
- Conversion coatings like anodizing do not deposit a discrete coating, but instead chemically convert the surface of the base material into a different material. Anodizing forms an oxide layer on aluminum and other metals.
Electroplating and electroless plating allow applying a thin metallic coating to customize the appearance, improve corrosion and wear resistance, build up worn parts, or provide specific functional properties of metal parts and products.
Surface Preparation
Proper surface preparation is a critical step prior to the plating process. The surface must be thoroughly cleaned and polished to ensure proper adhesion and coverage of the plating layer.
Common steps in surface preparation include:
- Cleaning – The surface is cleaned to remove oil, grease, rust, scale and other contaminants. Typical cleaning methods include solvent cleaning, alkaline cleaning and acid cleaning. The type of cleaner used depends on the substrate material and type of contaminants to be removed.
- Polishing – Once cleaned, the surface may require polishing to smooth the surface and prepare it for plating. Mechanical polishing with abrasives or chemical polishing can be used. Polishing helps improve adhesion of the plating layer.
- Masking – Areas that should not receive plating may be masked off using plater’s tape, wax or lacquer. This prevents plating buildup on areas that should remain unplated. The edge of the mask area should have a clean, straight line to facilitate good plating coverage at the edge.
Proper surface prep removes contaminants, provides the desired surface finish and protects areas not to be plated. This allows the subsequent plating process to properly coat the part with good adhesion and coverage.
Plating Solutions and Equipment
The plating solution, also called the plating bath, is a key component in the plating process. It contains the metal ions that will be deposited onto the part surface. Common metal ions used for plating include copper, nickel, chromium, zinc, tin, gold, and silver.
To prepare the plating solution, specific recipes and concentrations are used depending on the metal being deposited. Along with the metal salts, various additives such as wetting agents, brighteners, levelers, buffers, and current carriers are included in the solution. These additives play crucial roles in enhancing solution conductivity, refining the grain structure, increasing brightness, and regulating deposition rates.
The plating process takes place in a plating tank, where the solution is stored. Heating elements are used to keep the solution at optimal temperatures. The size of the tank varies depending on the parts being plated. Rectifiers convert AC current into DC power, which is necessary for electroplating. Lead anodes act as the source of metal ions in the plating bath. As metal ions are deposited onto the surface of the cathode part, the anode dissolves, replenishing the solution.
Proper maintenance of the plating bath composition and operating parameters is critical for achieving quality plating results. The solution is analyzed and adjusted regularly to keep concentrations, pH, temperature, and other factors within specified ranges. Filtration systems remove unwanted contaminants that can degrade the bath.
Electroplating Process Explained
The electroplating process involves depositing a thin layer of metal onto the surface of another metal through electrodeposition. Here are the key steps:
- Surface preparation – The part to be plated must be cleaned thoroughly to remove any rust, scale, grease or dirt on the surface. This ensures the plating solution can spread evenly across the surface. Common methods include alkaline cleaning, acid pickling or abrasion.
- Cathode and anode – The plated part serves as the cathode (negative electrode) which is immersed into the plating solution along with the anode (positive electrode). The anode provides the metal to be deposited. Both electrodes are connected to a power source.
- Plating solution – The solution contains the ionic form of the metal to be deposited, as well as additives like accelerators, inhibitors and wetting agents. The solution conductivity and metal ion concentration must be closely controlled.
- Electric current – When current is applied, metal ions in the solutions are attracted to the cathode and deposit uniformly across the surface. This causes the anode to dissolve and replenish the solution with metal ions.
- Post-plating – After electroplating, the part is rinsed thoroughly in water to remove plating solution. Post-treatments may also be applied like chromating or lacquering to enhance corrosion protection.
- Quality checks – Plated parts undergo quality checks for proper thickness, adhesion, uniformity and appearance according to specifications. Defects can be corrected by re-plating.
Electroless Plating Process
Electroless plating, also known as autocatalytic deposition, is a plating process that does not require the use of external electrical current to plate the part. Instead, a chemical reaction provides the necessary reducing power to deposit the metal onto the surface.
The part to be plated is immersed in a heated solution containing the dissolved plating metal, a reducing agent, and complexing agents. The surface of the part has been pre-treated or seeded to catalyze the reaction. As the reaction proceeds, the reducing agent donates electrons to the metal ions, causing the metal to deposit onto the catalytic surface.
Some key aspects of electroless plating:
- Does not require external power source or electrodes
- Depends on a controlled chemical reaction
- Lower deposition rates compared to electroplating
- Uniform coatings even on complex geometries
- Requires excellent pre-treatment and surface activation
Electroless plating is commonly used in electronics, automotive components, and decorative applications. It allows plating of non-conductive surfaces and provides even coatings regardless of part geometry. Process control is critical to achieve high quality uniform finishes.
Post-Plating Processing
After the plating process is complete, the parts must undergo additional processing to finalize and protect the plated finish. This includes:
Rinsing
Once plating is finished, the parts are thoroughly rinsed in a series of rinse tanks. This is done to remove any residual plating solution from the surface. Proper rinsing prevents staining or contamination of the finish. Deionized water is commonly used for the final rinse.
Drying
The parts are then dried, usually with forced hot air. Some plating lines have centrifugal dryers or vacuum dryers. Proper drying prevents water stains on the finish. The drying process must match the part configuration to ensure no water is retained.
Post-Treatment
Additional surface treatments may be applied after plating to enhance properties like corrosion resistance, lubricity, solderability, etc. Common post-treatments include:
- Chromating – An electrolytic chromate conversion coating adds corrosion protection and improves paint adhesion.
- Lubricants – Coatings like oil, wax or PTFE can be added for lubricity.
- Passivation – An acid treatment forms a thin, transparent oxide layer that enhances corrosion resistance.
- Lacquering – Clear lacquer coatings provide scratch protection and an aesthetic finish.
Proper post-plating processing ensures the plated parts meet specifications before further assembly or use. Checking for water stains, residue, and surface defects is part of quality control.
Quality Control
Plating quality control is critical for ensuring the plated layers meet specifications in a custom fabrication process. Key quality checks include:
Thickness
- Thickness must be measured and tested to confirm it meets design specifications. Too thin and the layer can wear or corrode prematurely. Too thick and it wastes plating chemicals and time.
- Thickness is checked before and after plating using micrometers or x-ray fluorescence. Measurements are taken at multiple spots.
- For multilayer plating, thickness is verified between each layer.
Adhesion
- Adhesion testing confirms proper bonding between the substrate and plated layer. Poor adhesion can lead to plating peeling or flaking off.
- Tests like bend, chisel, or tape pull tests are commonly used. ASTM has standardized adhesion test methods.
- Failures point to issues with surface preparation or plating chemistry/current.
Appearance
- The plated surface is visually inspected for defects like pits, nodules, cracks, or discoloration.
- Magnification helps identify microscopic imperfections. SEM or profilometers precisely analyze surface morphology.
- Defects indicate problems with pretreatment steps or plating conditions.
Quality checks validate the plating process delivers coatings that meet design needs. This prevents rejects or field failures in custom fabricated parts. Adjustments can improve process control.
Closing Summary
In conclusion, plating is a vital surface finishing process in custom fabrication that enhances the properties and appearance of base materials. Understanding the plating processes, surface preparation, solutions, and equipment helps fabricators achieve high-quality results. Post-plating processing and quality control ensure plated parts meet specifications.
However, when outsourcing surface treatment including plating, additional factors must be considered to guarantee quality. We explored the key concerns and best practices for ensuring high standards when outsourcing in another article.
Plating is an important surface finishing process used in custom fabrication to coat materials with a thin layer of metal. The plating process applies a metal coating to a conductive surface through chemical reactions and electricity.
Plating allows designers and fabricators to enhance the properties and appearance of base materials. It provides materials with improved corrosion and wear resistance, increased hardness, lubricity or solderability, and an attractive decorative finish. This makes plating a versatile process that enables durable and aesthetically appealing custom fabricated parts and products.
The plating process bonds a thin layer of the plating metal onto the base material through electroplating or electroless plating methods. Proper surface preparation, plating solutions, and equipment help ensure high quality and consistent plating results. Understanding the plating process enables custom fabricators to choose suitable techniques and achieve the desired properties in finished components.
Common Plating Processes
Plating in custom fabrication typically refers to electroplating or electroless plating processes. There are a few other less common plating methods as well.
- Electroplating involves using an electrical current to reduce dissolved metal cations so that they form a thin coating on the surface of a conductive material. The part to be plated serves as the cathode (negative electrode) in the electrolytic cell.
- Electroless plating involves an autocatalytic chemical reducing agent in solution to deposit metal without the use of an external electrical current. It allows plating of non-conductive surfaces.
- Conversion coatings like anodizing do not deposit a discrete coating, but instead chemically convert the surface of the base material into a different material. Anodizing forms an oxide layer on aluminum and other metals.
Electroplating and electroless plating allow applying a thin metallic coating to customize the appearance, improve corrosion and wear resistance, build up worn parts, or provide specific functional properties of metal parts and products.
Surface Preparation
Proper surface preparation is a critical step prior to the plating process. The surface must be thoroughly cleaned and polished to ensure proper adhesion and coverage of the plating layer.
Common steps in surface preparation include:
- Cleaning – The surface is cleaned to remove oil, grease, rust, scale and other contaminants. Typical cleaning methods include solvent cleaning, alkaline cleaning and acid cleaning. The type of cleaner used depends on the substrate material and type of contaminants to be removed.
- Polishing – Once cleaned, the surface may require polishing to smooth the surface and prepare it for plating. Mechanical polishing with abrasives or chemical polishing can be used. Polishing helps improve adhesion of the plating layer.
- Masking – Areas that should not receive plating may be masked off using plater’s tape, wax or lacquer. This prevents plating buildup on areas that should remain unplated. The edge of the mask area should have a clean, straight line to facilitate good plating coverage at the edge.
Proper surface prep removes contaminants, provides the desired surface finish and protects areas not to be plated. This allows the subsequent plating process to properly coat the part with good adhesion and coverage.
Plating Solutions and Equipment
The plating solution, also called the plating bath, is a key component in the plating process. It contains the metal ions that will be deposited onto the part surface. Common metal ions used for plating include copper, nickel, chromium, zinc, tin, gold, and silver.
To prepare the plating solution, specific recipes and concentrations are used depending on the metal being deposited. Along with the metal salts, various additives such as wetting agents, brighteners, levelers, buffers, and current carriers are included in the solution. These additives play crucial roles in enhancing solution conductivity, refining the grain structure, increasing brightness, and regulating deposition rates.
The plating process takes place in a plating tank, where the solution is stored. Heating elements are used to keep the solution at optimal temperatures. The size of the tank varies depending on the parts being plated. Rectifiers convert AC current into DC power, which is necessary for electroplating. Lead anodes act as the source of metal ions in the plating bath. As metal ions are deposited onto the surface of the cathode part, the anode dissolves, replenishing the solution.
Proper maintenance of the plating bath composition and operating parameters is critical for achieving quality plating results. The solution is analyzed and adjusted regularly to keep concentrations, pH, temperature, and other factors within specified ranges. Filtration systems remove unwanted contaminants that can degrade the bath.
Electroplating Process Explained
The electroplating process involves depositing a thin layer of metal onto the surface of another metal through electrodeposition. Here are the key steps:
- Surface preparation – The part to be plated must be cleaned thoroughly to remove any rust, scale, grease or dirt on the surface. This ensures the plating solution can spread evenly across the surface. Common methods include alkaline cleaning, acid pickling or abrasion.
- Cathode and anode – The plated part serves as the cathode (negative electrode) which is immersed into the plating solution along with the anode (positive electrode). The anode provides the metal to be deposited. Both electrodes are connected to a power source.
- Plating solution – The solution contains the ionic form of the metal to be deposited, as well as additives like accelerators, inhibitors and wetting agents. The solution conductivity and metal ion concentration must be closely controlled.
- Electric current – When current is applied, metal ions in the solutions are attracted to the cathode and deposit uniformly across the surface. This causes the anode to dissolve and replenish the solution with metal ions.
- Post-plating – After electroplating, the part is rinsed thoroughly in water to remove plating solution. Post-treatments may also be applied like chromating or lacquering to enhance corrosion protection.
- Quality checks – Plated parts undergo quality checks for proper thickness, adhesion, uniformity and appearance according to specifications. Defects can be corrected by re-plating.
Electroless Plating Process
Electroless plating, also known as autocatalytic deposition, is a plating process that does not require the use of external electrical current to plate the part. Instead, a chemical reaction provides the necessary reducing power to deposit the metal onto the surface.
The part to be plated is immersed in a heated solution containing the dissolved plating metal, a reducing agent, and complexing agents. The surface of the part has been pre-treated or seeded to catalyze the reaction. As the reaction proceeds, the reducing agent donates electrons to the metal ions, causing the metal to deposit onto the catalytic surface.
Some key aspects of electroless plating:
- Does not require external power source or electrodes
- Depends on a controlled chemical reaction
- Lower deposition rates compared to electroplating
- Uniform coatings even on complex geometries
- Requires excellent pre-treatment and surface activation
Electroless plating is commonly used in electronics, automotive components, and decorative applications. It allows plating of non-conductive surfaces and provides even coatings regardless of part geometry. Process control is critical to achieve high quality uniform finishes.
Post-Plating Processing
After the plating process is complete, the parts must undergo additional processing to finalize and protect the plated finish. This includes:
Rinsing
Once plating is finished, the parts are thoroughly rinsed in a series of rinse tanks. This is done to remove any residual plating solution from the surface. Proper rinsing prevents staining or contamination of the finish. Deionized water is commonly used for the final rinse.
Drying
The parts are then dried, usually with forced hot air. Some plating lines have centrifugal dryers or vacuum dryers. Proper drying prevents water stains on the finish. The drying process must match the part configuration to ensure no water is retained.
Post-Treatment
Additional surface treatments may be applied after plating to enhance properties like corrosion resistance, lubricity, solderability, etc. Common post-treatments include:
- Chromating – An electrolytic chromate conversion coating adds corrosion protection and improves paint adhesion.
- Lubricants – Coatings like oil, wax or PTFE can be added for lubricity.
- Passivation – An acid treatment forms a thin, transparent oxide layer that enhances corrosion resistance.
- Lacquering – Clear lacquer coatings provide scratch protection and an aesthetic finish.
Proper post-plating processing ensures the plated parts meet specifications before further assembly or use. Checking for water stains, residue, and surface defects is part of quality control.
Quality Control
Plating quality control is critical for ensuring the plated layers meet specifications in a custom fabrication process. Key quality checks include:
Thickness
- Thickness must be measured and tested to confirm it meets design specifications. Too thin and the layer can wear or corrode prematurely. Too thick and it wastes plating chemicals and time.
- Thickness is checked before and after plating using micrometers or x-ray fluorescence. Measurements are taken at multiple spots.
- For multilayer plating, thickness is verified between each layer.
Adhesion
- Adhesion testing confirms proper bonding between the substrate and plated layer. Poor adhesion can lead to plating peeling or flaking off.
- Tests like bend, chisel, or tape pull tests are commonly used. ASTM has standardized adhesion test methods.
- Failures point to issues with surface preparation or plating chemistry/current.
Appearance
- The plated surface is visually inspected for defects like pits, nodules, cracks, or discoloration.
- Magnification helps identify microscopic imperfections. SEM or profilometers precisely analyze surface morphology.
- Defects indicate problems with pretreatment steps or plating conditions.
Quality checks validate the plating process delivers coatings that meet design needs. This prevents rejects or field failures in custom fabricated parts. Adjustments can improve process control.
Closing Summary
In conclusion, plating is a vital surface finishing process in custom fabrication that enhances the properties and appearance of base materials. Understanding the plating processes, surface preparation, solutions, and equipment helps fabricators achieve high-quality results. Post-plating processing and quality control ensure plated parts meet specifications.
However, when outsourcing surface treatment including plating, additional factors must be considered to guarantee quality. We explored the key concerns and best practices for ensuring high standards when outsourcing in another article.
Ready to see CADDi Drawer in action? Get a personalized demo.
Subscribe to our Blog!
Related Resources

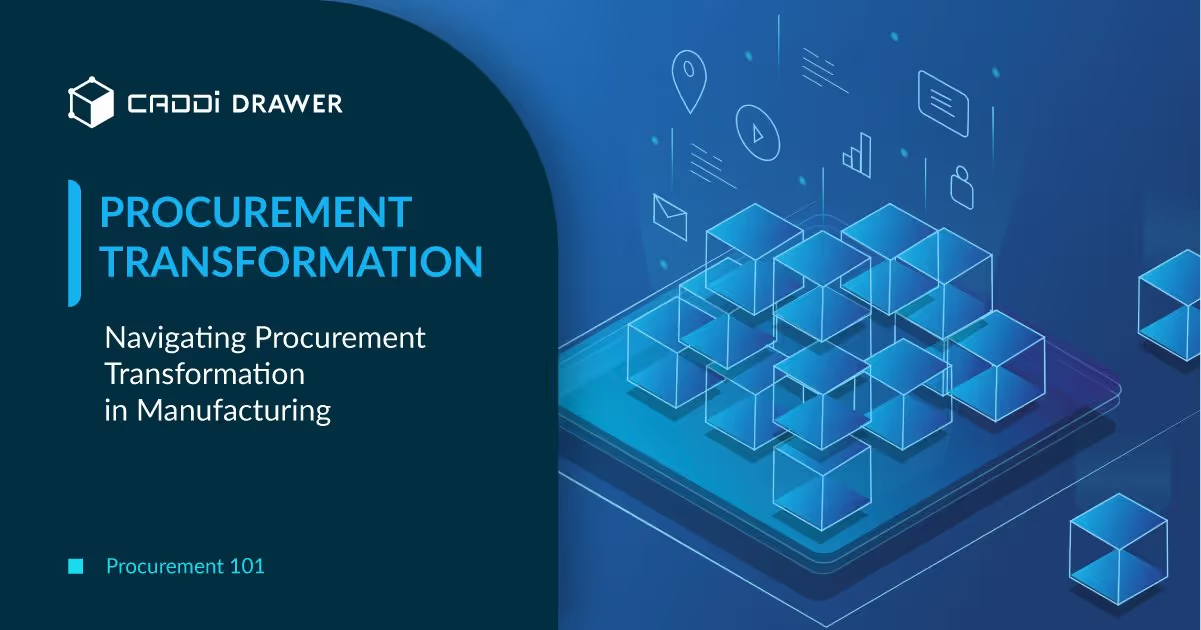

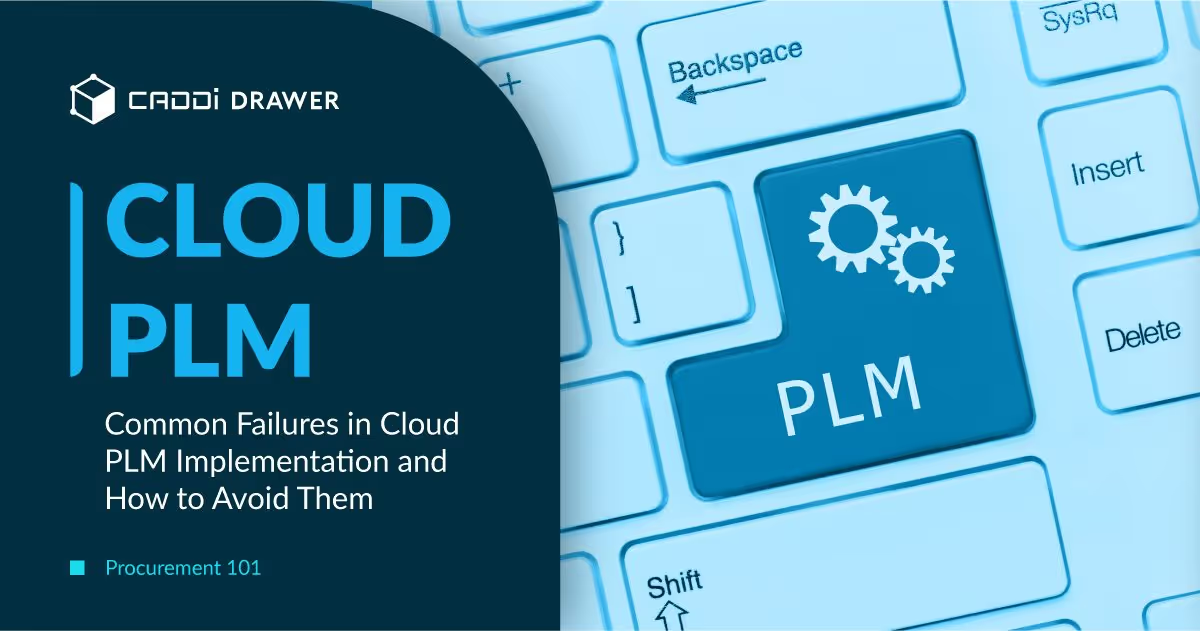
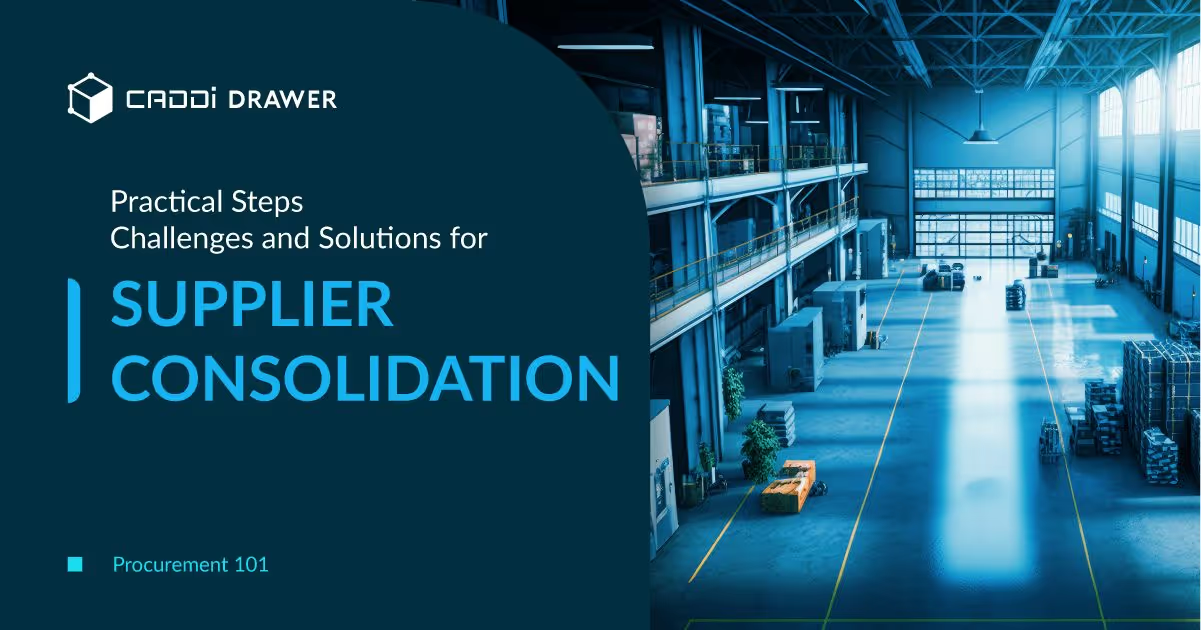
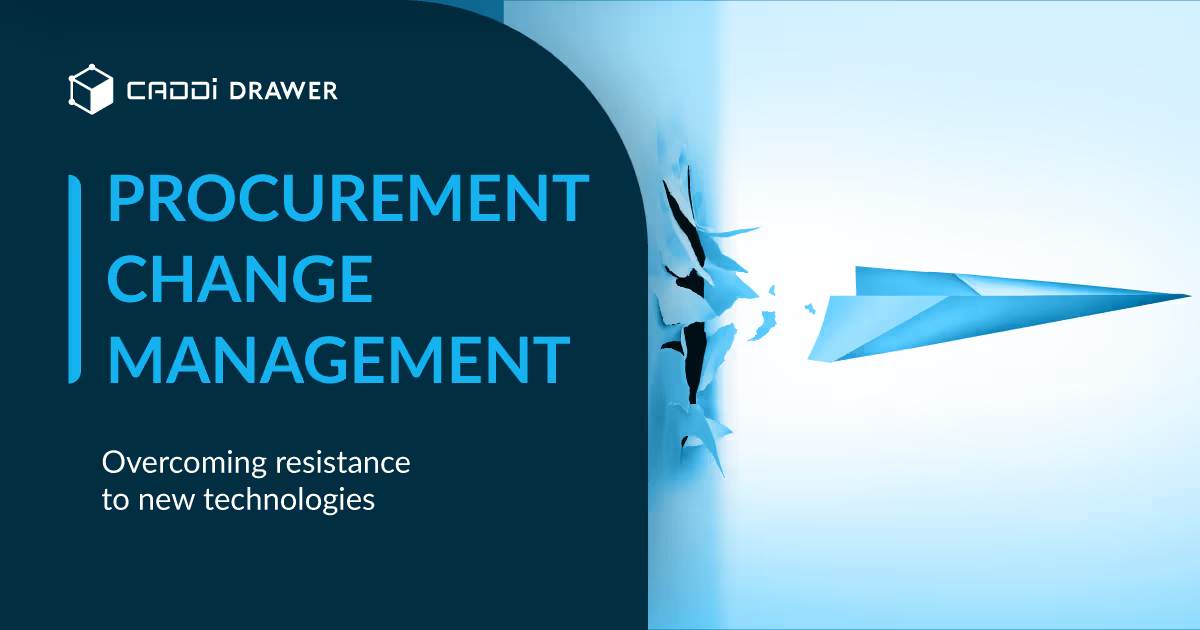