Procurement 101: Common Failures in Cloud PLM Implementation and How to Avoid Them
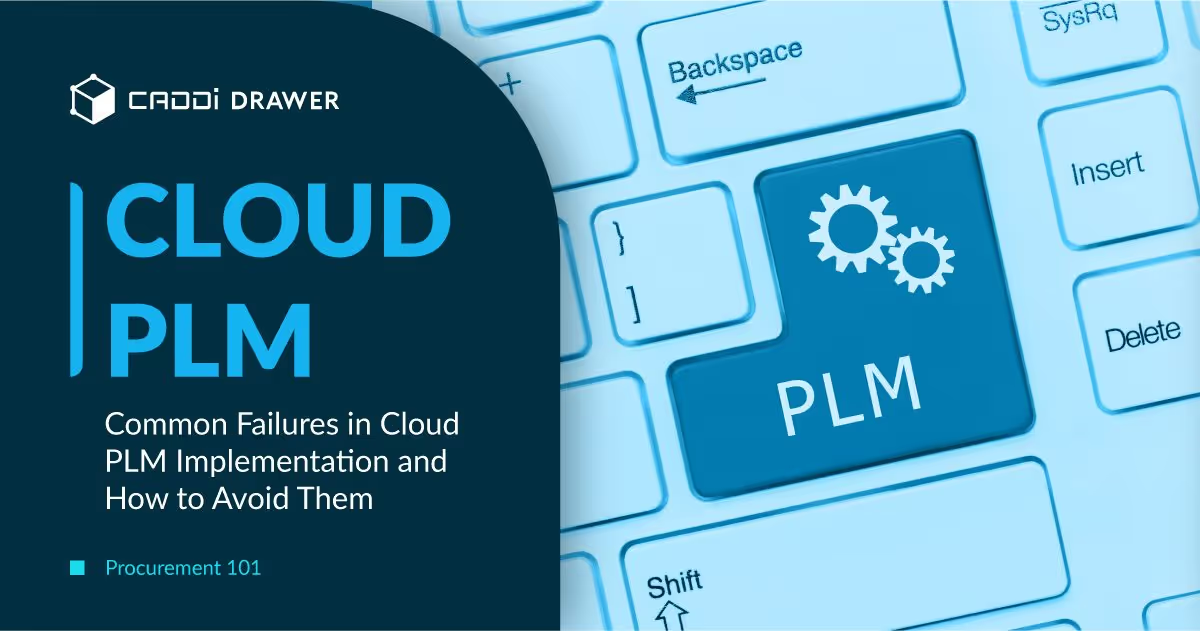
Table of Contents
Product Lifecycle Management (PLM) in the cloud represents a transformative shift for the manufacturing sector, enabling enhanced collaboration, efficiency, and innovation. However, transitioning to a cloud-based PLM solution is not without its challenges. This article aims to shed light on common pitfalls encountered during cloud PLM implementations and offers practical advice to procurement and engineering managers on how to navigate these challenges effectively.
Understanding of Cloud PLM
PLM is an integrated system for managing the entire lifecycle of a product within the manufacturing sector, encompassing the stages of planning, development, design, production preparation, production, sales, maintenance, and disposal. In contrast, Product Data Management (PDM) refers to the methods and products that manage the foundational data necessary for realizing PLM. The roles of PLM and PDM are distinct; while PLM manages the entire product lifecycle, PDM focuses on the centralized management of design data.
.avif)
By implementing PLM, companies can centralize product information, which in the context of manufacturing-centric businesses, contributes to improved production efficiency, cost reduction, quicker product launches to market, and enhanced governance. In many manufacturing industries, the management of the product lifecycle significantly influences revenue. Optimizing and appropriately maintaining PLM can contribute to maximizing profits and reducing costs.
Recently, the clear distinction between PLM and PDM has been blurring, with vendors now offering comprehensive product lifecycle management systems that include both PLM and PDM functionalities. For instance, Windchill by PTC, a renowned PLM product, encompasses PDM capabilities within its PLM package. This evolution reflects a trend towards integrated solutions that provide a holistic approach to managing the complex needs of product development and manufacturing processes.
What are included in the PLM Systems?
Product Lifecycle Management (PLM) systems offer a comprehensive suite of features designed to manage the entire lifecycle of a product efficiently. Key features included in PLM systems are:
1. Data Management
- Centralized Product Data Repository: A single source of truth for all product-related information, including designs, specifications, documentation, and BOM (Bill of Materials).
- Document Management: Tools for managing product documentation, version control, and ensuring that all stakeholders have access to the latest information.
2. Product Design and Development
- CAD Integration: Integration with Computer-Aided Design (CAD) tools to manage design files and changes directly within the PLM system.
- Change Management: Processes for managing changes to product designs and documentation, including change requests, impact analysis, and approval workflows.
3. Project Management
- Project Planning and Scheduling: Tools to plan, schedule, and track product development projects, including resource allocation and milestone tracking.
- Collaboration Tools: Features that facilitate communication and collaboration among cross-functional teams, suppliers, and partners.
4. Quality Management
- Quality Control: Processes and tools for ensuring product quality, including quality planning, defect tracking, and CAPA (Corrective and Preventive Actions).
- Compliance Management: Management of compliance with industry standards and regulations throughout the product lifecycle.
5. Supply Chain Management
- Supplier Collaboration: Tools for collaborating with suppliers, including sharing product designs, specifications, and procurement information.
- BOM Management: Management of the Bill of Materials, including creation, modification, and communication with manufacturing and supply chain partners.
6. Manufacturing Process Management
- Manufacturing Planning: Tools for planning manufacturing processes, including workflow definition and factory layout optimization.
- Production Scheduling: Scheduling production runs, managing work orders, and tracking manufacturing progress.
7. Product Portfolio Management
- Product Roadmapping: Tools for planning product portfolios, including market analysis, product strategy development, and lifecycle management.
- Portfolio Analysis: Analysis and reporting tools to evaluate product performance, market trends, and investment returns.
8. Configuration Management
- Version Control: Managing different versions of product designs and documents to ensure consistency and traceability.
- Variant Management: Managing different product variants and configurations to meet diverse market and customer requirements.
9. Service and Maintenance
- Service Lifecycle Management: Tools for managing post-sale service and maintenance, including service plans, warranty tracking, and customer support.
- Feedback Integration: Integrating customer feedback into product development and improvement processes.
Common Failures in Cloud PLM Implementation
It’s not hard to imagine that implementing a PLM system with such an extensive range of features can be challenging. Below, we would like to introduce some common points of failure in PLM implementation.
Alignment in Strategic Objectives, Planning and Priority
A significant gap between the visions of CxO-level executives and the managers or leaders implementing PLM can lead to misaligned strategic objectives and operational processes.
Immature planning and a failure to differentiate between essential and important requirements can lead to misguided priorities.
The Big Bang Approach
Deploying numerous PLM modules overnight often overwhelms users, leading to system rejection. This attempt at rapid implementation fails to consider user adaptation and learning curves.
Automating too many processes too soon can introduce complexity and delays, leading to increased costs and inflexible business rules.
Stakeholder Engagement and Cultural Change
Failure to engage key stakeholders throughout the implementation process can lead to a lack of buy-in and support for the PLM system.
Implementing a PLM system is not just a technological shift but also a significant cultural change for an organization, requiring clear communication and support to navigate.
Missteps in Vendor Selection
Selecting the wrong technology can stall the implementation from the beginning. Organizations frequently seek a PLM solution that is immediately usable without considering the constraints imposed by these solutions.
User interfaces that do not cater to the specific needs of different roles can deter users from adopting the system.
Also, opting for a Product Data Management (PDM) system when a PLM solution is needed can lead organizations to a dead end, as PDM systems are not designed to manage information across the entire product lifecycle.
Cost Concerns
PLM projects often face high costs, particularly due to user licensing fees, which can inhibit the project before it fully begins.
The high cost of PLM licenses can limit the system’s deployment across the organization, restricting the true benefit of PLM from being realized.
Data Integrity and System Integration
Migrating data into a new PLM system is daunting, especially if existing data is unstructured, incomplete, or inaccurate.
Off-the-shelf PLM solutions may not fully align with an organization’s specific processes and needs, highlighting the necessity for customization and seamless integration with other enterprise systems.
Training, Support, and Continuous Improvement
Underestimating the need for comprehensive training and ongoing support can result in the underutilization of the system and resistance to adoption.
Treating a PLM implementation as a one-time project, rather than an ongoing process, can hinder the system’s ability to adapt to changing business needs and technologies.
Hot to Avoid the Pitfalls
Here’s a consolidated guide to ensure a smooth PLM implementation, focusing solely on the solutions that have proven effective.
Strategic Planning and Integration
Comprehensive Integration: To bridge solution gaps, it’s crucial to implement a PLM that integrates all applications comprehensively. Leveraging technologies like Web Services Federation can bring data from various systems into a unified user interface without altering existing solutions.
Evaluating Technology Alignment: Ensure the selected PLM technology aligns with both current and future business objectives. It should be scalable, adaptable, and capable of integrating with existing systems to avoid the pitfalls of starting point errors.
Implementation Approach
Phased Rollout: Adopt a phased approach to avoid overwhelming users. Begin with a single process, solicit feedback, make necessary adjustments, and then proceed to the next. This method not only engages users but also flattens the learning curve, contrasting the “Big Bang” implementation strategy.
Change Management: Underestimating the change management required is a common oversight. Develop a comprehensive strategy that includes training, communication, and support to help staff adapt. Engaging users early and continuously is key to managing resistance and ensuring smooth adoption.
Cost Management and Access
Cost-effective Licensing: Address high cost estimates by limiting licenses to essential users and exploring shared access methods, such as Microsoft SharePoint or open-source PLM systems, to make PLM benefits accessible across the supply chain without prohibitive costs.
Vision, Support, and Data Governance
Aligning Vision and Roadmap: Align everyone’s understanding by defining clear business goals, setting priorities, and creating a plan to achieve them. Secure strong executive sponsorship to communicate this vision, emphasizing that PLM supports the company’s strategic goals.
Data Quality and Governance: Prioritize data quality and establish robust data governance policies from the outset. This includes defining data standards, roles, and responsibilities to ensure data accuracy and consistency.
User Experience and System Usability
Tailored User Interfaces: To counteract the challenge of overly complex UIs, pre-plan to select a PLM solution that offers role-based interfaces tailored to different user needs. Conduct user testing early to ensure the system meets users’ needs, facilitating smoother adoption.
Tool Selection and Automation
Appropriate Tool Selection: Avoid the trap of choosing the wrong tools by not forcing a fit where it does not exist. If multiple PDM systems are currently in use effectively, continue to do so while building a PLM system atop to manage broader business challenges.
Balanced Automation: Over-automation can complicate implementation. Automate consistent and predictable routine tasks while allowing room for human judgment. Not every decision needs to be automated to realize the true value of PLM in facilitating process integration and enabling informed decision-making.
Conclusion
In conclusion, successfully implementing a Cloud PLM system is a multifaceted endeavor that requires careful planning, strategic decision-making, and a user-centric approach. By focusing on comprehensive integration, a phased implementation strategy, effective change management, and cost management, businesses can lay a solid foundation for their PLM journey. Aligning the project with the company’s strategic vision, ensuring executive support, prioritizing data quality, and embracing a role-based user experience further enhance the potential for success.
Moreover, selecting the right tools and maintaining a balanced approach to automation are crucial steps that cannot be overlooked. In another article – “Cloud PLM Software 2024 – Comparison and the future,” we have provided a classification and list of major cloud PLM systems and introduced software to support PLM utilization for your reference.
Product Lifecycle Management (PLM) in the cloud represents a transformative shift for the manufacturing sector, enabling enhanced collaboration, efficiency, and innovation. However, transitioning to a cloud-based PLM solution is not without its challenges. This article aims to shed light on common pitfalls encountered during cloud PLM implementations and offers practical advice to procurement and engineering managers on how to navigate these challenges effectively.
Understanding of Cloud PLM
PLM is an integrated system for managing the entire lifecycle of a product within the manufacturing sector, encompassing the stages of planning, development, design, production preparation, production, sales, maintenance, and disposal. In contrast, Product Data Management (PDM) refers to the methods and products that manage the foundational data necessary for realizing PLM. The roles of PLM and PDM are distinct; while PLM manages the entire product lifecycle, PDM focuses on the centralized management of design data.
.avif)
By implementing PLM, companies can centralize product information, which in the context of manufacturing-centric businesses, contributes to improved production efficiency, cost reduction, quicker product launches to market, and enhanced governance. In many manufacturing industries, the management of the product lifecycle significantly influences revenue. Optimizing and appropriately maintaining PLM can contribute to maximizing profits and reducing costs.
Recently, the clear distinction between PLM and PDM has been blurring, with vendors now offering comprehensive product lifecycle management systems that include both PLM and PDM functionalities. For instance, Windchill by PTC, a renowned PLM product, encompasses PDM capabilities within its PLM package. This evolution reflects a trend towards integrated solutions that provide a holistic approach to managing the complex needs of product development and manufacturing processes.
What are included in the PLM Systems?
Product Lifecycle Management (PLM) systems offer a comprehensive suite of features designed to manage the entire lifecycle of a product efficiently. Key features included in PLM systems are:
1. Data Management
- Centralized Product Data Repository: A single source of truth for all product-related information, including designs, specifications, documentation, and BOM (Bill of Materials).
- Document Management: Tools for managing product documentation, version control, and ensuring that all stakeholders have access to the latest information.
2. Product Design and Development
- CAD Integration: Integration with Computer-Aided Design (CAD) tools to manage design files and changes directly within the PLM system.
- Change Management: Processes for managing changes to product designs and documentation, including change requests, impact analysis, and approval workflows.
3. Project Management
- Project Planning and Scheduling: Tools to plan, schedule, and track product development projects, including resource allocation and milestone tracking.
- Collaboration Tools: Features that facilitate communication and collaboration among cross-functional teams, suppliers, and partners.
4. Quality Management
- Quality Control: Processes and tools for ensuring product quality, including quality planning, defect tracking, and CAPA (Corrective and Preventive Actions).
- Compliance Management: Management of compliance with industry standards and regulations throughout the product lifecycle.
5. Supply Chain Management
- Supplier Collaboration: Tools for collaborating with suppliers, including sharing product designs, specifications, and procurement information.
- BOM Management: Management of the Bill of Materials, including creation, modification, and communication with manufacturing and supply chain partners.
6. Manufacturing Process Management
- Manufacturing Planning: Tools for planning manufacturing processes, including workflow definition and factory layout optimization.
- Production Scheduling: Scheduling production runs, managing work orders, and tracking manufacturing progress.
7. Product Portfolio Management
- Product Roadmapping: Tools for planning product portfolios, including market analysis, product strategy development, and lifecycle management.
- Portfolio Analysis: Analysis and reporting tools to evaluate product performance, market trends, and investment returns.
8. Configuration Management
- Version Control: Managing different versions of product designs and documents to ensure consistency and traceability.
- Variant Management: Managing different product variants and configurations to meet diverse market and customer requirements.
9. Service and Maintenance
- Service Lifecycle Management: Tools for managing post-sale service and maintenance, including service plans, warranty tracking, and customer support.
- Feedback Integration: Integrating customer feedback into product development and improvement processes.
Common Failures in Cloud PLM Implementation
It’s not hard to imagine that implementing a PLM system with such an extensive range of features can be challenging. Below, we would like to introduce some common points of failure in PLM implementation.
Alignment in Strategic Objectives, Planning and Priority
A significant gap between the visions of CxO-level executives and the managers or leaders implementing PLM can lead to misaligned strategic objectives and operational processes.
Immature planning and a failure to differentiate between essential and important requirements can lead to misguided priorities.
The Big Bang Approach
Deploying numerous PLM modules overnight often overwhelms users, leading to system rejection. This attempt at rapid implementation fails to consider user adaptation and learning curves.
Automating too many processes too soon can introduce complexity and delays, leading to increased costs and inflexible business rules.
Stakeholder Engagement and Cultural Change
Failure to engage key stakeholders throughout the implementation process can lead to a lack of buy-in and support for the PLM system.
Implementing a PLM system is not just a technological shift but also a significant cultural change for an organization, requiring clear communication and support to navigate.
Missteps in Vendor Selection
Selecting the wrong technology can stall the implementation from the beginning. Organizations frequently seek a PLM solution that is immediately usable without considering the constraints imposed by these solutions.
User interfaces that do not cater to the specific needs of different roles can deter users from adopting the system.
Also, opting for a Product Data Management (PDM) system when a PLM solution is needed can lead organizations to a dead end, as PDM systems are not designed to manage information across the entire product lifecycle.
Cost Concerns
PLM projects often face high costs, particularly due to user licensing fees, which can inhibit the project before it fully begins.
The high cost of PLM licenses can limit the system’s deployment across the organization, restricting the true benefit of PLM from being realized.
Data Integrity and System Integration
Migrating data into a new PLM system is daunting, especially if existing data is unstructured, incomplete, or inaccurate.
Off-the-shelf PLM solutions may not fully align with an organization’s specific processes and needs, highlighting the necessity for customization and seamless integration with other enterprise systems.
Training, Support, and Continuous Improvement
Underestimating the need for comprehensive training and ongoing support can result in the underutilization of the system and resistance to adoption.
Treating a PLM implementation as a one-time project, rather than an ongoing process, can hinder the system’s ability to adapt to changing business needs and technologies.
Hot to Avoid the Pitfalls
Here’s a consolidated guide to ensure a smooth PLM implementation, focusing solely on the solutions that have proven effective.
Strategic Planning and Integration
Comprehensive Integration: To bridge solution gaps, it’s crucial to implement a PLM that integrates all applications comprehensively. Leveraging technologies like Web Services Federation can bring data from various systems into a unified user interface without altering existing solutions.
Evaluating Technology Alignment: Ensure the selected PLM technology aligns with both current and future business objectives. It should be scalable, adaptable, and capable of integrating with existing systems to avoid the pitfalls of starting point errors.
Implementation Approach
Phased Rollout: Adopt a phased approach to avoid overwhelming users. Begin with a single process, solicit feedback, make necessary adjustments, and then proceed to the next. This method not only engages users but also flattens the learning curve, contrasting the “Big Bang” implementation strategy.
Change Management: Underestimating the change management required is a common oversight. Develop a comprehensive strategy that includes training, communication, and support to help staff adapt. Engaging users early and continuously is key to managing resistance and ensuring smooth adoption.
Cost Management and Access
Cost-effective Licensing: Address high cost estimates by limiting licenses to essential users and exploring shared access methods, such as Microsoft SharePoint or open-source PLM systems, to make PLM benefits accessible across the supply chain without prohibitive costs.
Vision, Support, and Data Governance
Aligning Vision and Roadmap: Align everyone’s understanding by defining clear business goals, setting priorities, and creating a plan to achieve them. Secure strong executive sponsorship to communicate this vision, emphasizing that PLM supports the company’s strategic goals.
Data Quality and Governance: Prioritize data quality and establish robust data governance policies from the outset. This includes defining data standards, roles, and responsibilities to ensure data accuracy and consistency.
User Experience and System Usability
Tailored User Interfaces: To counteract the challenge of overly complex UIs, pre-plan to select a PLM solution that offers role-based interfaces tailored to different user needs. Conduct user testing early to ensure the system meets users’ needs, facilitating smoother adoption.
Tool Selection and Automation
Appropriate Tool Selection: Avoid the trap of choosing the wrong tools by not forcing a fit where it does not exist. If multiple PDM systems are currently in use effectively, continue to do so while building a PLM system atop to manage broader business challenges.
Balanced Automation: Over-automation can complicate implementation. Automate consistent and predictable routine tasks while allowing room for human judgment. Not every decision needs to be automated to realize the true value of PLM in facilitating process integration and enabling informed decision-making.
Conclusion
In conclusion, successfully implementing a Cloud PLM system is a multifaceted endeavor that requires careful planning, strategic decision-making, and a user-centric approach. By focusing on comprehensive integration, a phased implementation strategy, effective change management, and cost management, businesses can lay a solid foundation for their PLM journey. Aligning the project with the company’s strategic vision, ensuring executive support, prioritizing data quality, and embracing a role-based user experience further enhance the potential for success.
Moreover, selecting the right tools and maintaining a balanced approach to automation are crucial steps that cannot be overlooked. In another article – “Cloud PLM Software 2024 – Comparison and the future,” we have provided a classification and list of major cloud PLM systems and introduced software to support PLM utilization for your reference.
Ready to see CADDi Drawer in action? Get a personalized demo.
Subscribe to our Blog!
Related Resources
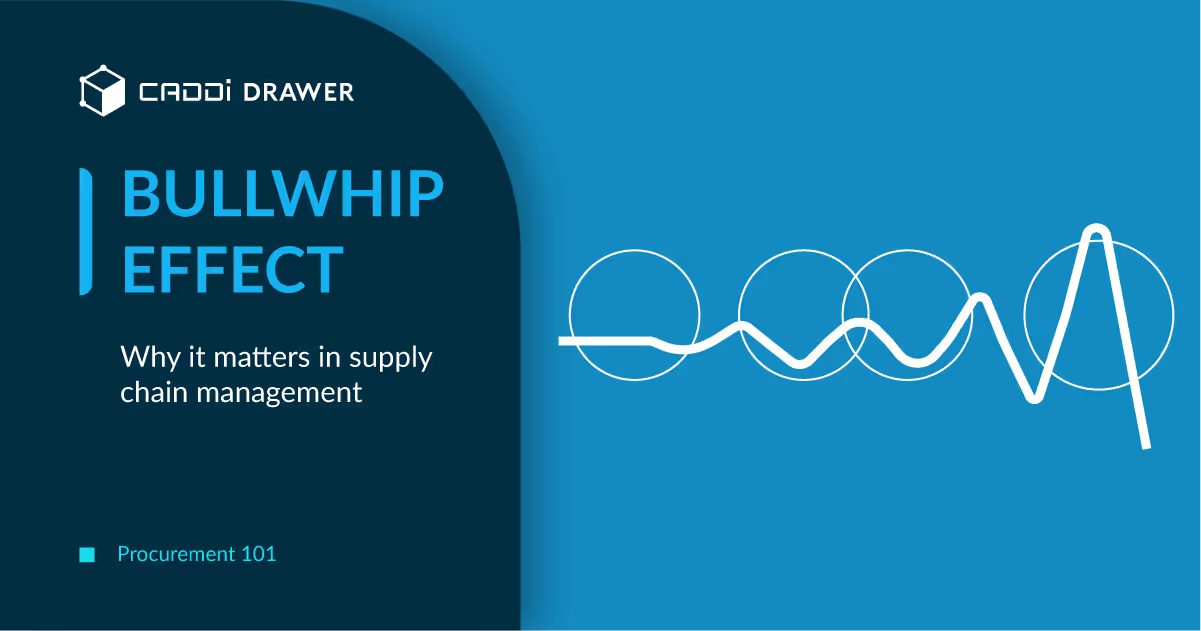
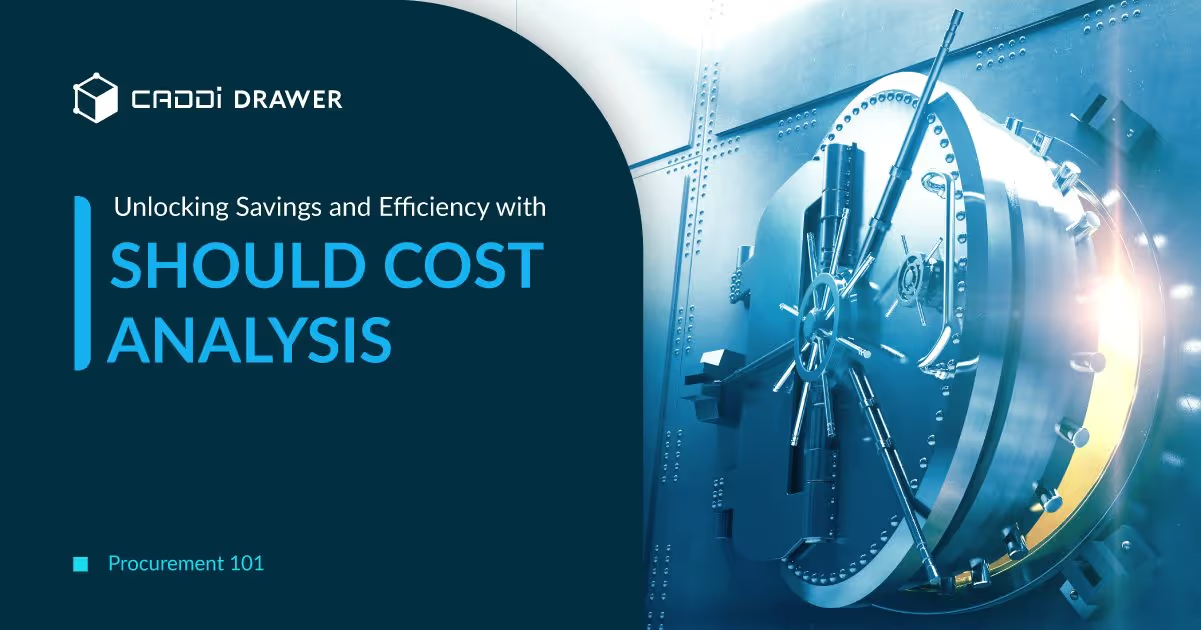
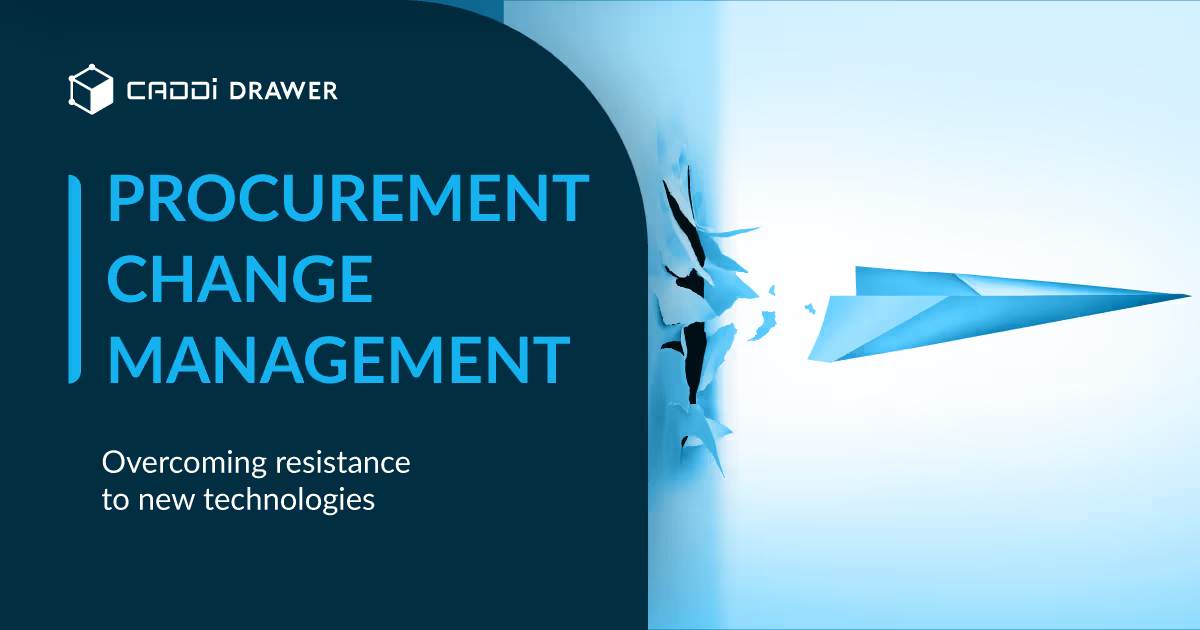
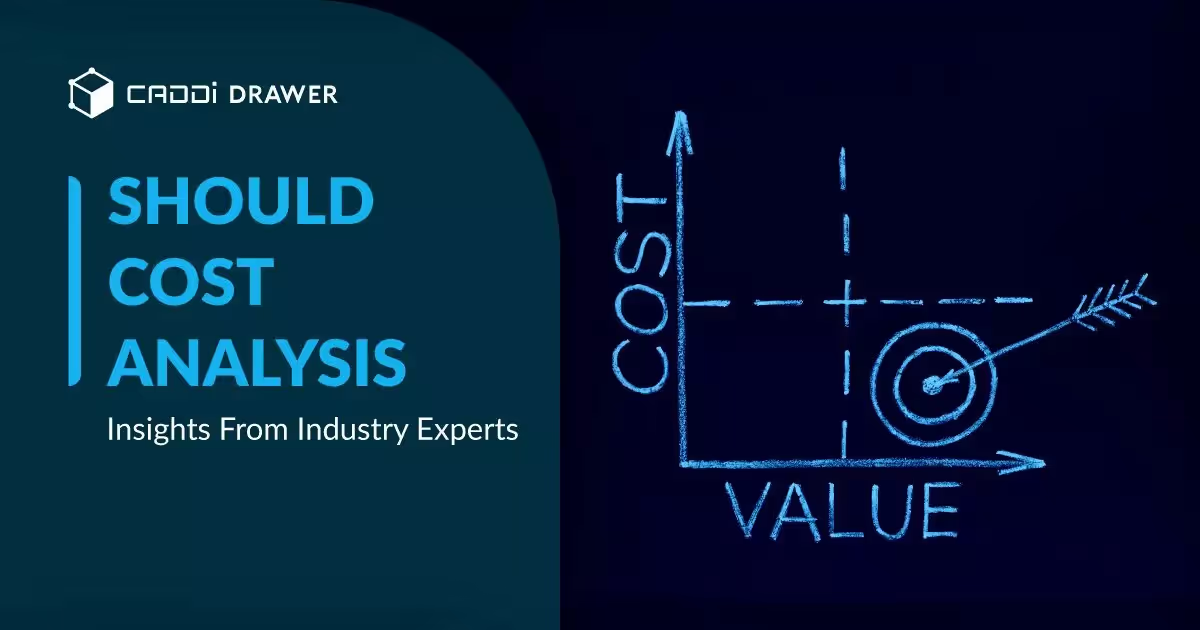
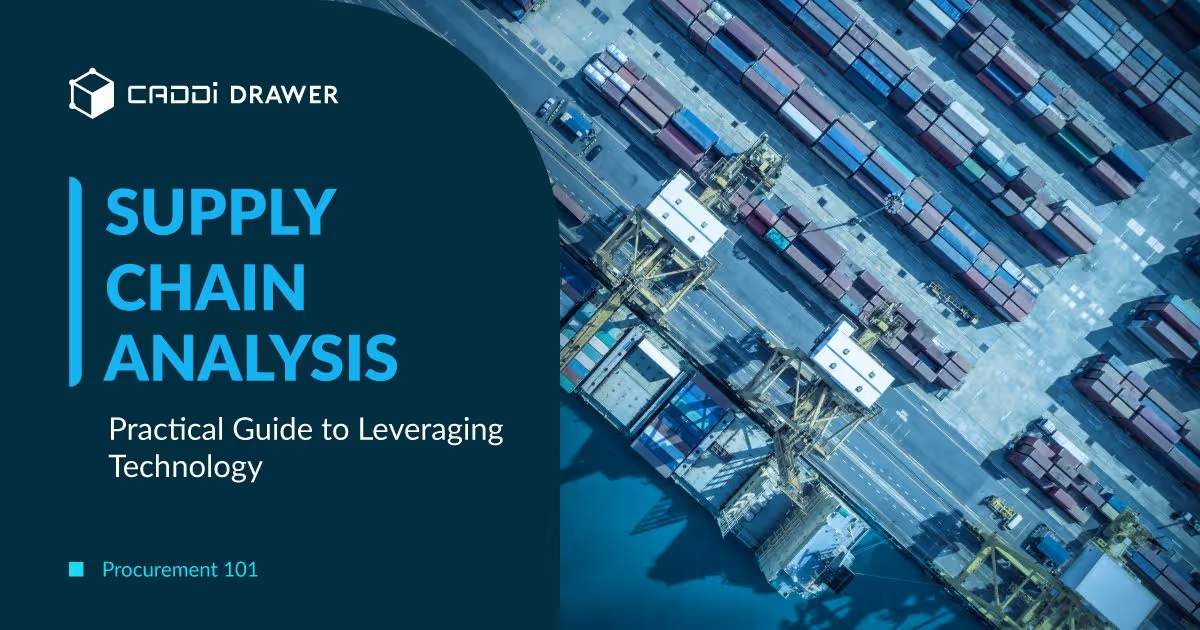
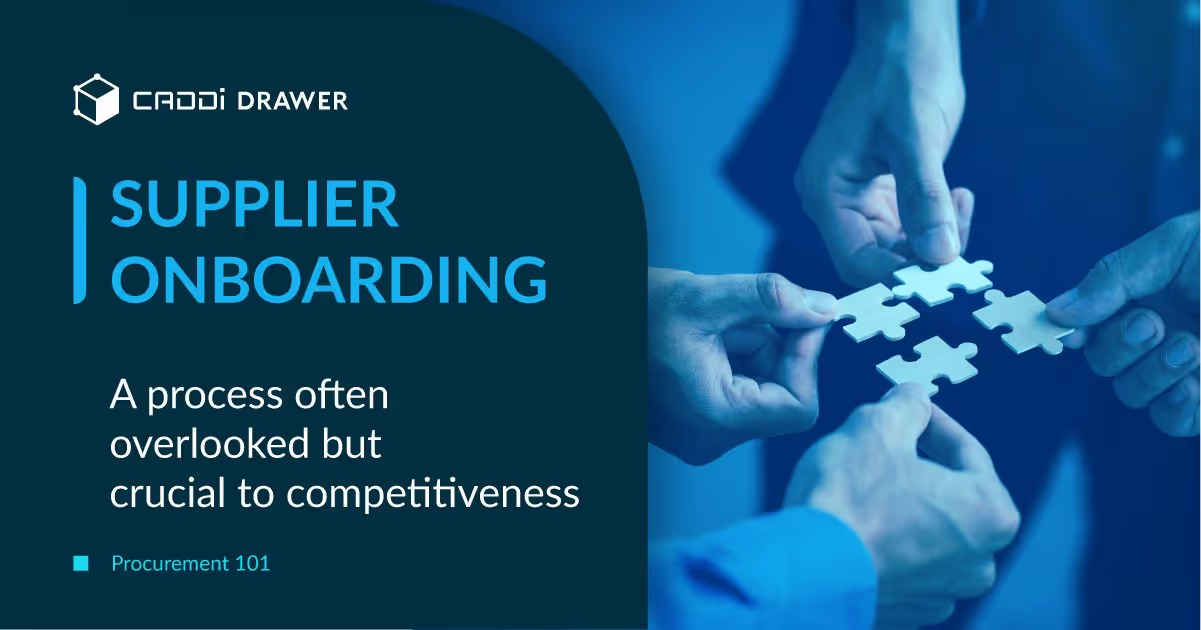