Procurement 101: Navigating Procurement Transformation in Manufacturing
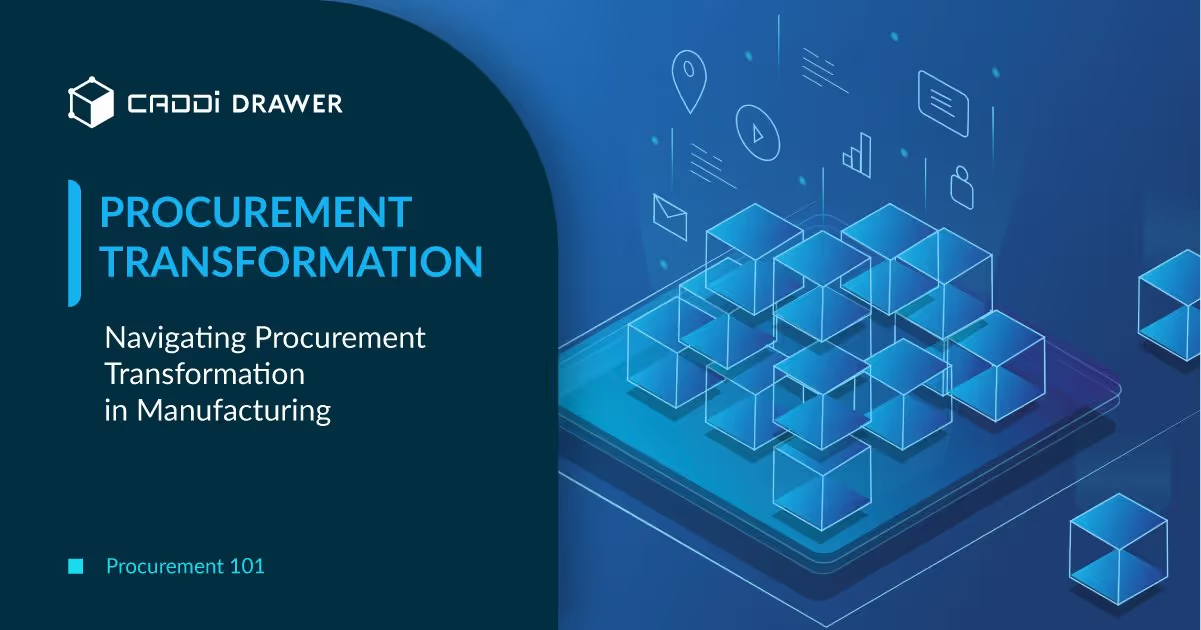
Table of Contents
In the dynamic realm of modern manufacturing, procurement has transcended mere cost management to become a strategic imperative. The concept of procurement transformation encapsulates a holistic reformation of procurement methodologies, approaches, and technological frameworks to synchronize with the evolving dynamics of the global market and technological progress. This metamorphosis is indispensable for manufacturers striving to maintain competitiveness, optimize operational efficiency, and cultivate innovation.
The Forces Driving Change in Procurement
Several key factors are propelling procurement transformation in the manufacturing sector:
Technology Advancements:
Digital tools and platforms are revolutionizing how manufacturers source materials, manage supplier relationships, and analyze procurement data. From cloud-based procurement solutions to AI and machine learning, technology is at the forefront of procurement transformation. 74% of senior executives in the US middle market firms said digital transformation was the most important area of investment for their companies.
Global Supply Chain Crisis:
The global manufacturing landscape is constantly changing, influenced by factors. According to Blue Yonder’s 2023 Supply Chain Executive Survey, 48% of manufacturers have watched their profit margins shrink due to cost increases during the pandemic time.
Regulatory and Sustainability Considerations:
With an increasing focus on sustainability and ethical sourcing, manufacturers are revising their procurement strategies to comply with regulatory requirements and meet sustainability goals.
Four Layers of Manufacturing Digital Transformation
In addressing the challenges faced by the manufacturing industry, the utilization of digital technologies and addressing labor shortages have become indispensable. Companies are called digital transformation when they respond to the rapid changes in the business environment by utilizing data and digital technology to innovate products, services, and business models based on the needs of customers and society. They also transform their operations, organization, processes, and corporate culture/climate to establish competitive advantages.
The journey of digital transformation (DX) in the manufacturing sector is complex and multifaceted, encompassing various aspects of operations, from work processes to the overarching business model. Here, we delve into the four critical layers that constitute the foundation of digital transformation in manufacturing: Work, Value Chain, Business Model, and Culture.
.avif)
Work: Enhancing Efficiency through Automation
At the core of digital transformation is the automation and robotization of tasks traditionally performed by humans, significantly improving work efficiency. Examples include:
- Utilizing Robotic Process Automation (RPA) tools like Ui Path to automate routine Excel data entry tasks. (Ui Path)
- Implementing robots in manufacturing for tasks that are simple yet critical, ensuring consistent quality and efficiency (Caterpillar)
Value Chain: Optimizing for Quality, Cost, and Delivery (QCD)
Digital transformation extends to the optimization and integration of data across the value chain, enhancing the overall Quality, Cost, and Delivery (QCD) and the value created.
This is achieved through:
- Integrating data to improve sales capabilities, such as using past quotation prices to refine sales strategies.
- Accumulating historical defect data to stabilize QCD (Quality, Cost and Delivery), ensuring product quality and reliability.
Business Model: Customer-Centric Transformation
A pivotal aspect of digital transformation is leveraging digital technology to evolve products into offerings that are more fundamentally focused on customer needs. This involves:
Transitioning from selling machinery to providing comprehensive solutions
- Siemens AG successfully transformed its manufacturing through digitalization, leveraging IoT and AI for smart factories, boosting efficiency and creating new revenue streams.
- Realizing 24-hour automation to support High-Mix Low-Volume (HMLV) production, catering to diverse customer demands efficiently.
Culture: Fostering a Digital-First Mindset
The success of digital transformation also hinges on the ability to cultivate a company culture that embraces digital advancements. This includes
- Acquiring and utilizing new data to predict and respond to changes in customer behavior, ensuring that operations are not just efficient but also aligned with market needs.
- Adopting an Agile workstyle, which emphasizes delivering outputs quickly with a focus on customer satisfaction, and enables cross-departmental teams to respond to early signs of change effectively.
In essence, the digital transformation in manufacturing is a holistic process that requires concerted efforts across various dimensions of the business. From automating simple tasks to reshaping the company culture towards agility and customer-centricity, each layer plays a vital role in ensuring manufacturers can navigate the complexities of the modern market and emerge more resilient, efficient, and innovative.
Building Blocks of a Modern Procurement Transformation
Before delving into the intricacies of how to execute a transformation, it’s crucial to anchor our strategies and initiatives in a fundamental understanding of why transformation is not just beneficial but necessary for modern manufacturing firms. The WHY (objective) of transformation varies by company, but they can largely be divided into the following three patterns.
Revenue Expansion
- Digitization and automation of procurement tasks based on each supplier’s attributes.
- Integration of production management systems with suppliers and improvement of compliance with delivery schedules.
Cost Reduction
- Proposals for Value Analysis/Value Engineering (VAVE) based on analysis of past ordering data.
- Reduction of labor through automatic ordering and cost reduction through optimal ordering.
Risk Reduction
- Supplier risk analysis for Business Continuity Planning (BCP). This involves the initiative to identify and replace hazardous materials in response to regulatory changes such as RoHS.
Your Roadmap to Procurement Excellence
Implementing procurement transformation can seem daunting, but with a structured approach, manufacturers can navigate the journey with confidence:
Assess Your Current Procurement Landscape:
Understand your current processes, technologies, and supplier relationships to identify areas for improvement.
Set Clear Objectives and Milestones:
Define what you want to achieve with your transformation initiative, including specific, measurable goals.
Select the Right Technologies and Partners:
Choose technologies and partners that align with your objectives and can support your transformation journey.
Cultivate a Culture of Continuous Improvement:
Encourage innovation and adaptability within your organization to sustain the transformation over the long term.
CADDi Drawer: Your Partner in Procurement Transformation
At CADDi, we understand the complexities of procurement transformation. Our suite of solutions and services is designed to support manufacturers at every step of their transformation journey. From strategic sourcing to risk management, our platform empowers manufacturers to optimize their procurement processes.
.avif)
Integrate siloed data into one place
Just by uploading CSV files, you can connect all relevant information to the associated drawings: cost, quantity, supplier information, sales price, cost breakdown, etc. CADDi Drawer easily connects ERP data, CAM, CAD, quality defect reports, spec sheets automatically. With its proprietary OCR-based AI technology, CADDi Drawer automatically extracts and digitizes non-structural data such as legacy drawings in static scanned PDF files with handwritten texts.
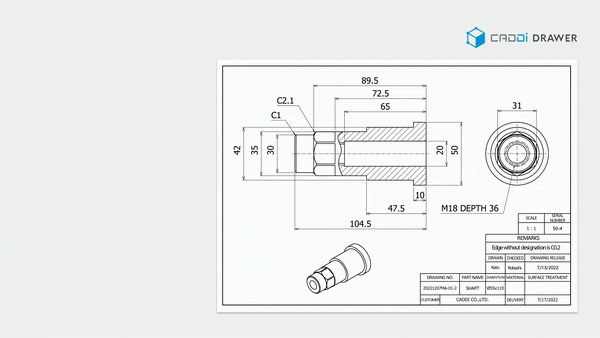
AI-powered Intelligence to assist procurement analytics
CADDi’s patented technology identifies the shape of each part to find “like parts” across all historical drawings, with all the relevant supply chain data (e.g., cost, quality, manufacturing notes, specs) automatically linked to each drawing. This allows you to achieve greater visibility into your dormant drawings within your file storage and draw actionable insights to help you drive cross-functional initiatives such as design standardization, VAVE, and supplier consolidation.
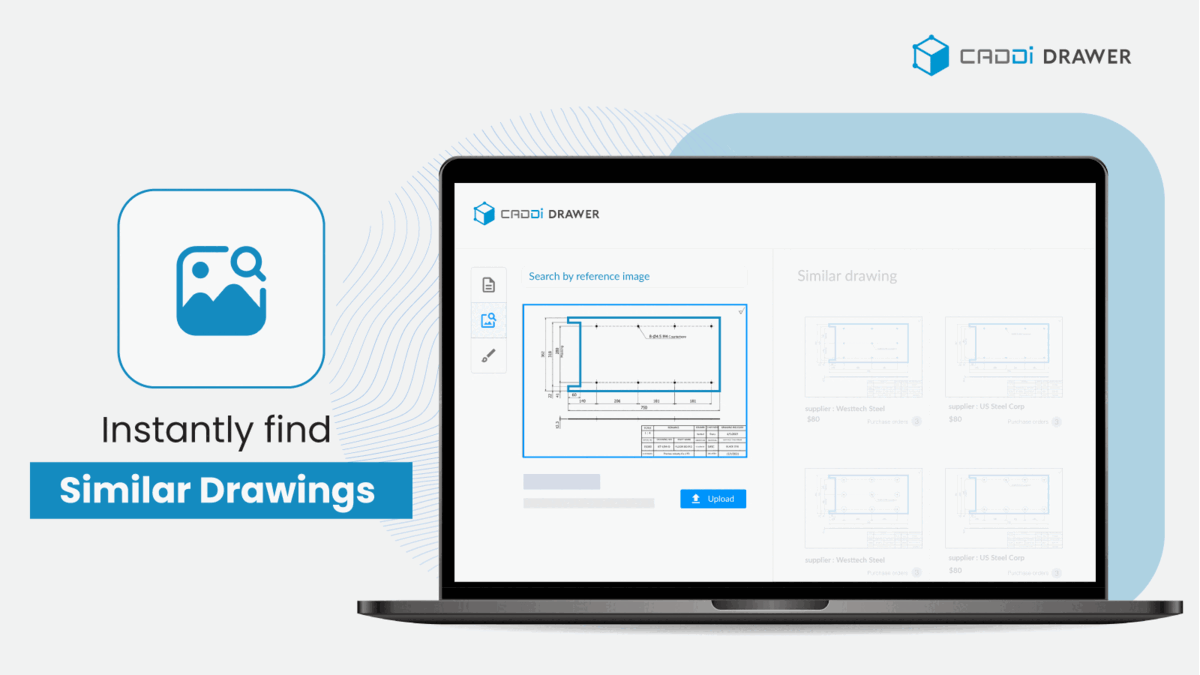
Streamline regulatory compliance work
Dealing with various regulations and standard changes can be difficult and time-consuming. CADDi Drawers enable you to search through a large number of drawings and specifications, which were previously identified manually, to confirm their impact. The system digitizes information on 2D drawings, including supplier names and material information, and integrates this with procurement data and specs. Based on this data, it allows users to search by keywords and identify drawings that include specific substances along with the supplier name. This provides you with sufficient information to collaborate with each supplier on corrective measures to change materials and specifications to those that comply with regulations.
Embracing the Future
Procurement transformation is not just a trend; it’s a strategic imperative for manufacturers aiming to thrive in the modern business ecosystem. By embracing change and leveraging the right strategies and technologies, manufacturers can ensure their procurement practices contribute to long-term success and resilience.
In the dynamic realm of modern manufacturing, procurement has transcended mere cost management to become a strategic imperative. The concept of procurement transformation encapsulates a holistic reformation of procurement methodologies, approaches, and technological frameworks to synchronize with the evolving dynamics of the global market and technological progress. This metamorphosis is indispensable for manufacturers striving to maintain competitiveness, optimize operational efficiency, and cultivate innovation.
The Forces Driving Change in Procurement
Several key factors are propelling procurement transformation in the manufacturing sector:
Technology Advancements:
Digital tools and platforms are revolutionizing how manufacturers source materials, manage supplier relationships, and analyze procurement data. From cloud-based procurement solutions to AI and machine learning, technology is at the forefront of procurement transformation. 74% of senior executives in the US middle market firms said digital transformation was the most important area of investment for their companies.
Global Supply Chain Crisis:
The global manufacturing landscape is constantly changing, influenced by factors. According to Blue Yonder’s 2023 Supply Chain Executive Survey, 48% of manufacturers have watched their profit margins shrink due to cost increases during the pandemic time.
Regulatory and Sustainability Considerations:
With an increasing focus on sustainability and ethical sourcing, manufacturers are revising their procurement strategies to comply with regulatory requirements and meet sustainability goals.
Four Layers of Manufacturing Digital Transformation
In addressing the challenges faced by the manufacturing industry, the utilization of digital technologies and addressing labor shortages have become indispensable. Companies are called digital transformation when they respond to the rapid changes in the business environment by utilizing data and digital technology to innovate products, services, and business models based on the needs of customers and society. They also transform their operations, organization, processes, and corporate culture/climate to establish competitive advantages.
The journey of digital transformation (DX) in the manufacturing sector is complex and multifaceted, encompassing various aspects of operations, from work processes to the overarching business model. Here, we delve into the four critical layers that constitute the foundation of digital transformation in manufacturing: Work, Value Chain, Business Model, and Culture.
.avif)
Work: Enhancing Efficiency through Automation
At the core of digital transformation is the automation and robotization of tasks traditionally performed by humans, significantly improving work efficiency. Examples include:
- Utilizing Robotic Process Automation (RPA) tools like Ui Path to automate routine Excel data entry tasks. (Ui Path)
- Implementing robots in manufacturing for tasks that are simple yet critical, ensuring consistent quality and efficiency (Caterpillar)
Value Chain: Optimizing for Quality, Cost, and Delivery (QCD)
Digital transformation extends to the optimization and integration of data across the value chain, enhancing the overall Quality, Cost, and Delivery (QCD) and the value created.
This is achieved through:
- Integrating data to improve sales capabilities, such as using past quotation prices to refine sales strategies.
- Accumulating historical defect data to stabilize QCD (Quality, Cost and Delivery), ensuring product quality and reliability.
Business Model: Customer-Centric Transformation
A pivotal aspect of digital transformation is leveraging digital technology to evolve products into offerings that are more fundamentally focused on customer needs. This involves:
Transitioning from selling machinery to providing comprehensive solutions
- Siemens AG successfully transformed its manufacturing through digitalization, leveraging IoT and AI for smart factories, boosting efficiency and creating new revenue streams.
- Realizing 24-hour automation to support High-Mix Low-Volume (HMLV) production, catering to diverse customer demands efficiently.
Culture: Fostering a Digital-First Mindset
The success of digital transformation also hinges on the ability to cultivate a company culture that embraces digital advancements. This includes
- Acquiring and utilizing new data to predict and respond to changes in customer behavior, ensuring that operations are not just efficient but also aligned with market needs.
- Adopting an Agile workstyle, which emphasizes delivering outputs quickly with a focus on customer satisfaction, and enables cross-departmental teams to respond to early signs of change effectively.
In essence, the digital transformation in manufacturing is a holistic process that requires concerted efforts across various dimensions of the business. From automating simple tasks to reshaping the company culture towards agility and customer-centricity, each layer plays a vital role in ensuring manufacturers can navigate the complexities of the modern market and emerge more resilient, efficient, and innovative.
Building Blocks of a Modern Procurement Transformation
Before delving into the intricacies of how to execute a transformation, it’s crucial to anchor our strategies and initiatives in a fundamental understanding of why transformation is not just beneficial but necessary for modern manufacturing firms. The WHY (objective) of transformation varies by company, but they can largely be divided into the following three patterns.
Revenue Expansion
- Digitization and automation of procurement tasks based on each supplier’s attributes.
- Integration of production management systems with suppliers and improvement of compliance with delivery schedules.
Cost Reduction
- Proposals for Value Analysis/Value Engineering (VAVE) based on analysis of past ordering data.
- Reduction of labor through automatic ordering and cost reduction through optimal ordering.
Risk Reduction
- Supplier risk analysis for Business Continuity Planning (BCP). This involves the initiative to identify and replace hazardous materials in response to regulatory changes such as RoHS.
Your Roadmap to Procurement Excellence
Implementing procurement transformation can seem daunting, but with a structured approach, manufacturers can navigate the journey with confidence:
Assess Your Current Procurement Landscape:
Understand your current processes, technologies, and supplier relationships to identify areas for improvement.
Set Clear Objectives and Milestones:
Define what you want to achieve with your transformation initiative, including specific, measurable goals.
Select the Right Technologies and Partners:
Choose technologies and partners that align with your objectives and can support your transformation journey.
Cultivate a Culture of Continuous Improvement:
Encourage innovation and adaptability within your organization to sustain the transformation over the long term.
CADDi Drawer: Your Partner in Procurement Transformation
At CADDi, we understand the complexities of procurement transformation. Our suite of solutions and services is designed to support manufacturers at every step of their transformation journey. From strategic sourcing to risk management, our platform empowers manufacturers to optimize their procurement processes.
.avif)
Integrate siloed data into one place
Just by uploading CSV files, you can connect all relevant information to the associated drawings: cost, quantity, supplier information, sales price, cost breakdown, etc. CADDi Drawer easily connects ERP data, CAM, CAD, quality defect reports, spec sheets automatically. With its proprietary OCR-based AI technology, CADDi Drawer automatically extracts and digitizes non-structural data such as legacy drawings in static scanned PDF files with handwritten texts.
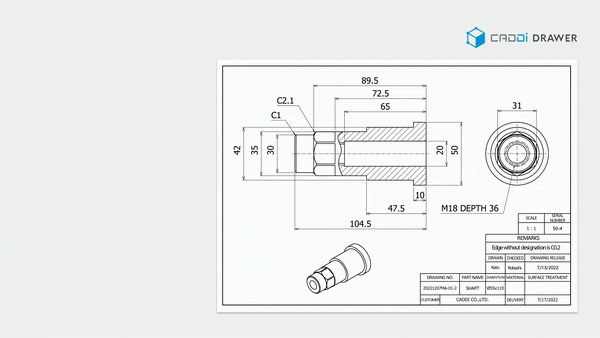
AI-powered Intelligence to assist procurement analytics
CADDi’s patented technology identifies the shape of each part to find “like parts” across all historical drawings, with all the relevant supply chain data (e.g., cost, quality, manufacturing notes, specs) automatically linked to each drawing. This allows you to achieve greater visibility into your dormant drawings within your file storage and draw actionable insights to help you drive cross-functional initiatives such as design standardization, VAVE, and supplier consolidation.
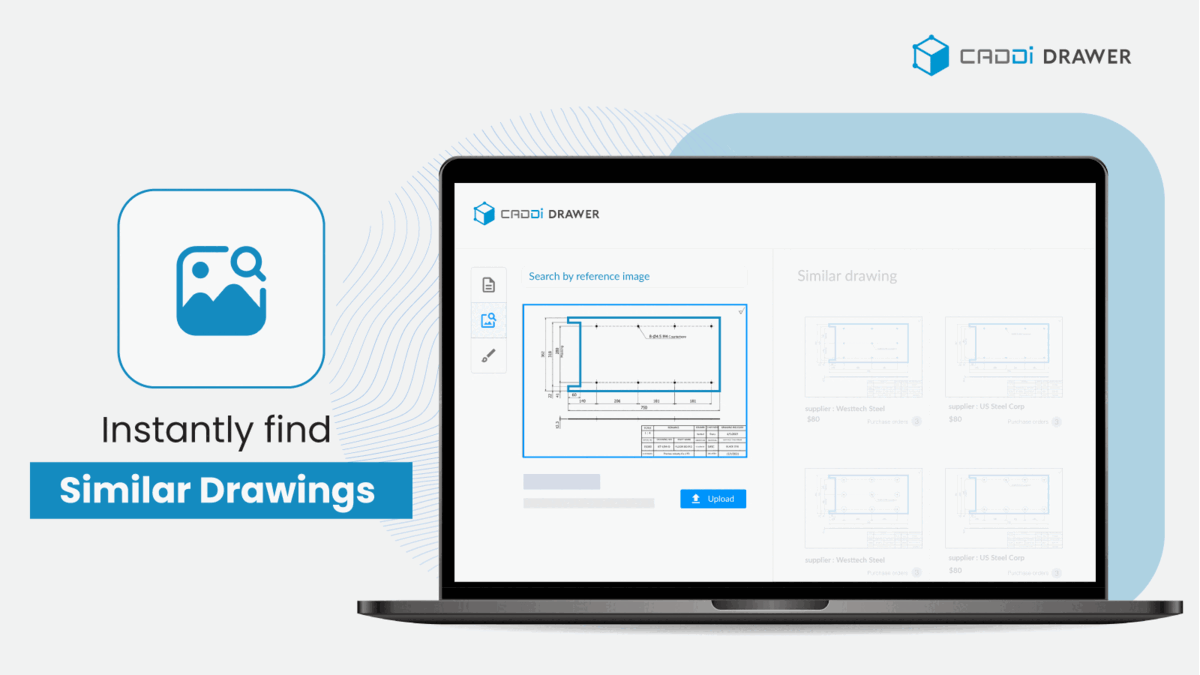
Streamline regulatory compliance work
Dealing with various regulations and standard changes can be difficult and time-consuming. CADDi Drawers enable you to search through a large number of drawings and specifications, which were previously identified manually, to confirm their impact. The system digitizes information on 2D drawings, including supplier names and material information, and integrates this with procurement data and specs. Based on this data, it allows users to search by keywords and identify drawings that include specific substances along with the supplier name. This provides you with sufficient information to collaborate with each supplier on corrective measures to change materials and specifications to those that comply with regulations.
Embracing the Future
Procurement transformation is not just a trend; it’s a strategic imperative for manufacturers aiming to thrive in the modern business ecosystem. By embracing change and leveraging the right strategies and technologies, manufacturers can ensure their procurement practices contribute to long-term success and resilience.
Ready to see CADDi Drawer in action? Get a personalized demo.
Subscribe to our Blog!
Related Resources
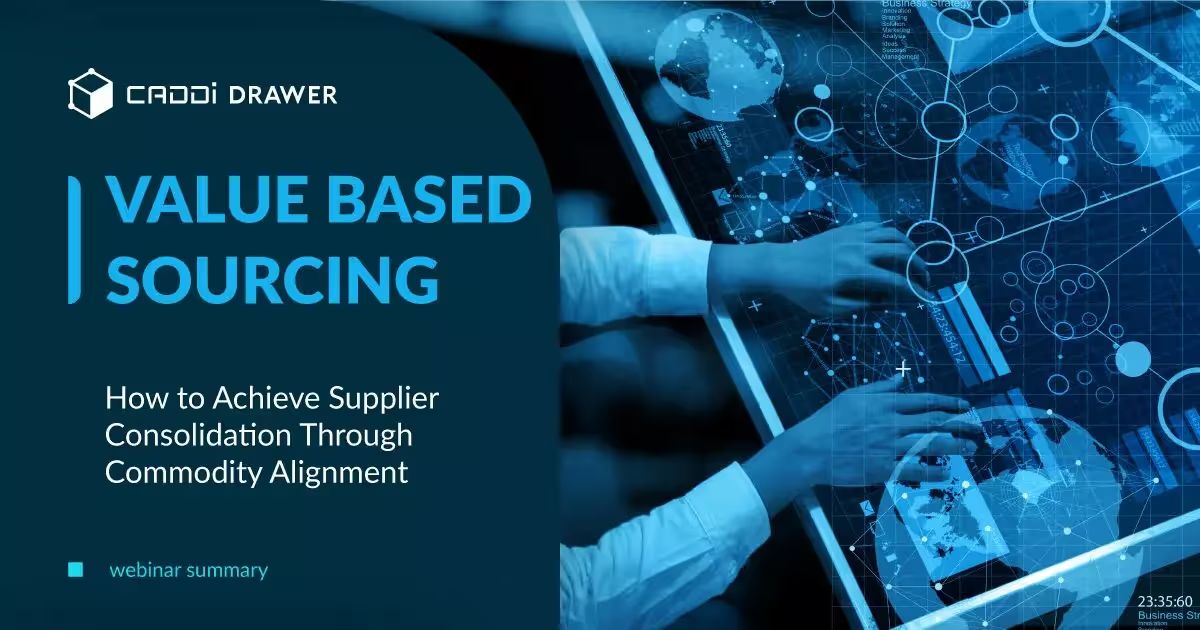

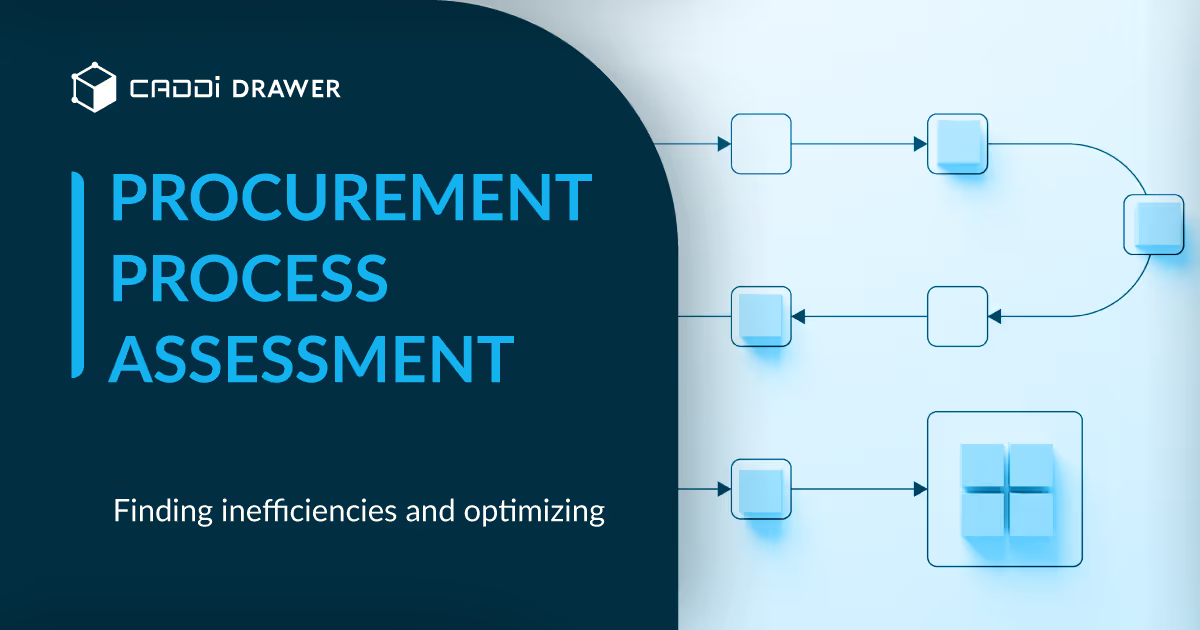


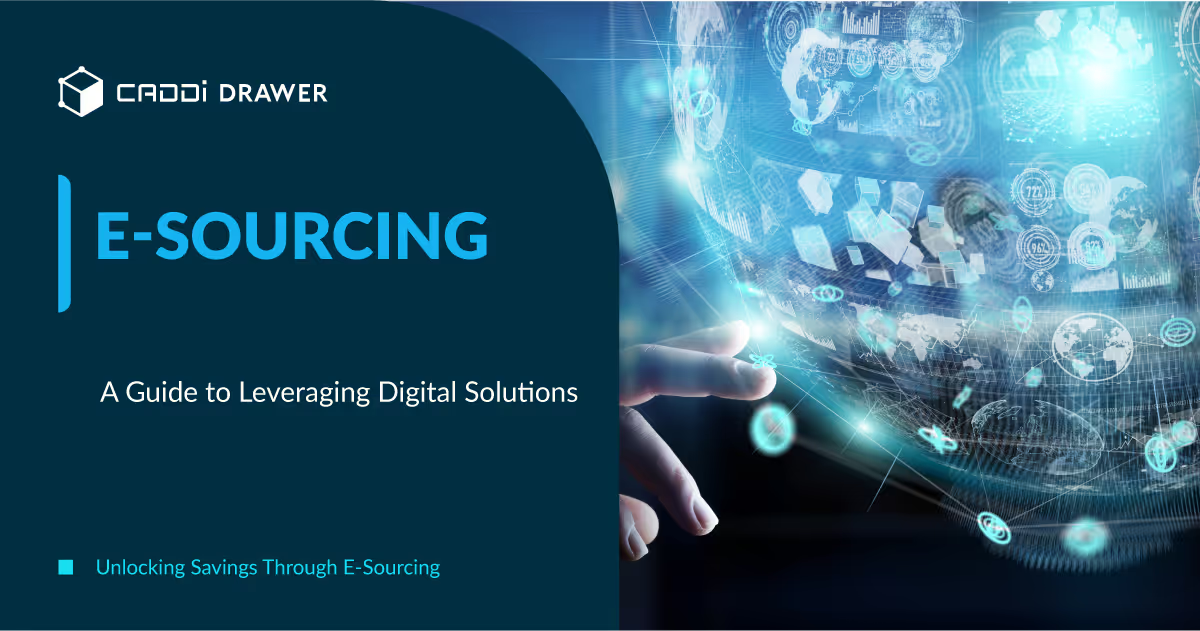