Procurement 101: ABC Analysis – How it works and why it’s important
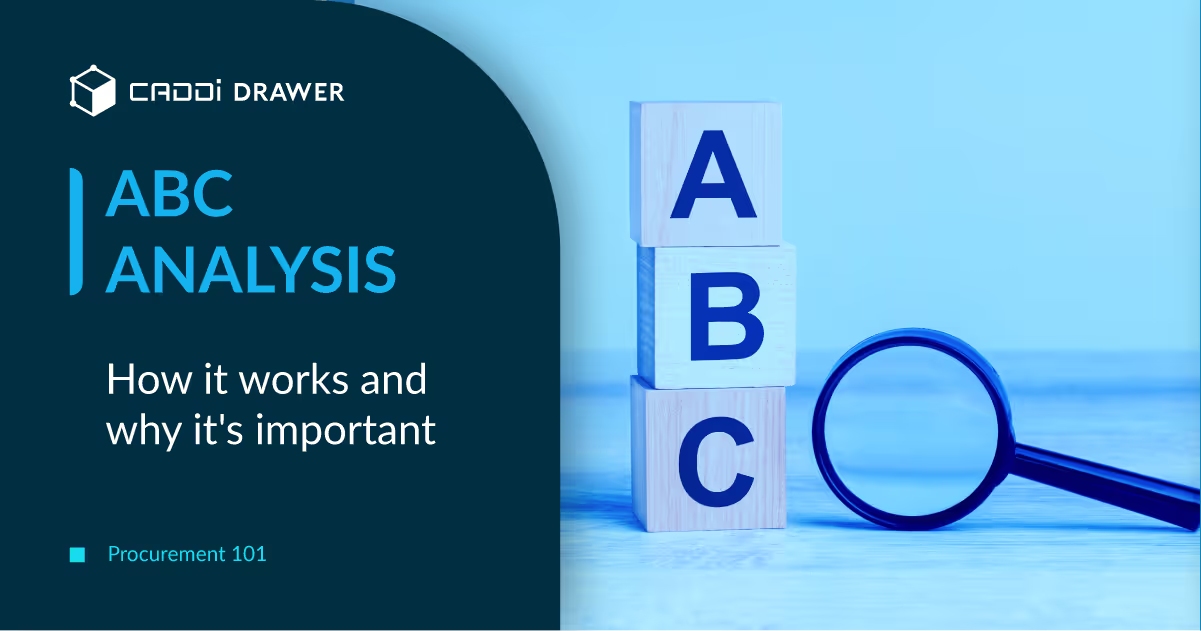
Table of Contents
Are you grappling with the challenge of optimizing your inventory to meet demand efficiently? ABC Analysis, coupled with XYZ Analysis, provides a robust framework for procurement professionals.
This article delves into how strategic classification of inventory into A, B, and C categories, based on value and demand predictability, can streamline operations, enhance customer satisfaction, and improve demand forecasting. With practical insights and step-by-step guides, it equips you to navigate the complexities of procurement and manufacturing sectors effectively.
Understanding ABC Analysis
At the heart of supply chain optimization lies ABC Analysis, a systematic approach that classifies inventory based on its importance. The principle is straightforward yet powerful:
- Class A items are the VIPs of your inventory, accounting for a substantial portion of your company’s value with a relatively small percentage of total items.
- Class B items straddle the fence in terms of value and quantity, not as critical as A but more significant than C.
- Class C items, while numerous, contribute the least to your bottom line.
This classification enables businesses to tailor their focus and resources, ensuring that the most critical items receive the attention they deserve.
The Benefits of Implementing ABC Analysis
Strategic Resource Allocation: ABC Analysis isn’t just about knowing your inventory; it’s about smartly allocating your resources. By identifying Class A items, companies can align their efforts with customer demand, optimizing the use of personnel, time, and space for items that drive success.
- Better Customer Service: Understanding which items are most profitable allows for prioritizing higher service levels for those products, directly impacting customer satisfaction.
- Enhanced Product Life Cycle Management: Gaining insights into the life cycle stages of products aids in forecasting demand and maintaining appropriate inventory levels.
- Control Over High-Cost Items: Prioritizing Class A inventory ensures a company’s key products are always available, maintaining a healthy stock level.
- Reduced Storage Expenses: Carrying the right proportion of A, B, or C class stock minimizes the costs associated with excess inventory.
- Simplified Supply Chain Management: ABC Analysis aids in making informed decisions about supplier consolidation or shifts to reduce carrying costs and streamline operations.
Conducting an ABC Analysis: A Step-by-Step Guide
Embarking on ABC Analysis involves a meticulous process that transforms raw data into actionable insights. Here’s how to navigate through this critical path:
- Gather Your Data: Start with a comprehensive dataset of your inventory, including annual demand, unit cost, and total cost.
- Calculate the Value Percentage: Determine the cumulative value of each item to your overall inventory. This involves multiplying the annual demand by the unit cost for each item.
- Rank and Classify: Sort your items from highest to lowest based on their value percentage. Then, categorize them into A, B, and C classes, aligning with the principles of ABC Analysis. Typically, A items represent 70-80% of inventory value, B items 15-25%, and C items around 5%.
Addressing the Limitations and Challenges of ABC Analysis
While ABC Analysis offers a structured approach to inventory management, it’s not without its challenges. Awareness of these limitations enables businesses to navigate potential pitfalls more effectively:
- Parameter Instability: The dynamic nature of markets means classifications may need frequent revisions to reflect current realities.
- Limited Pattern Consideration: Standard ABC models might not fully account for variables like seasonality or new product launches.
- Resource Intensiveness: The process can be time-consuming and requires dedicated resources to maintain accuracy.
The Role of ABC Analysis in Demand Forecasting and Inventory Control
The true power of ABC Analysis lies in its ability to enhance demand forecasting and inventory control, leading to:
- More Accurate Demand Forecasting: By focusing on high-value A items, businesses can refine their forecasting models, minimizing the risk of overstock or stockouts.
- Strategic Inventory Control: Identifying which items to stock more of and which to reduce can significantly impact storage costs and capital allocation.
- Informed Pricing Strategies: Insights from ABC Analysis can guide pricing decisions, ensuring that high-demand items are priced for maximum profitability.
Incorporating ABC Analysis into your inventory management practices offers a roadmap to optimized operations. By understanding its benefits, navigating its challenges, and leveraging its insights for better demand forecasting and inventory control, businesses can position themselves for greater efficiency and competitiveness.
Combining ABC with XYZ Analysis for Comprehensive Inventory Management
For a more granular view of inventory management, ABC Analysis pairs seamlessly with XYZ Analysis. While ABC classifies items based on value, XYZ Analysis categorizes them by the predictability of demand:
- X items have stable consumption.
- Y items experience some fluctuation in consumption.
- Z items face heavy fluctuations.
This dual approach creates a classification matrix, offering a panoramic view of inventory that highlights items needing more attention due to demand uncertainties. It’s a strategy that prevents overstocking and shortages, ensuring a balanced inventory that can swiftly adapt to market changes.
By merging ABC with XYZ, businesses wield a powerful tool in the quest for supply chain efficiency, capable of navigating the unpredictable seas of customer demand and inventory management. This methodology not only sharpens focus on high-value items but also illuminates the nuances of demand variability, guiding strategic decisions that bolster both customer satisfaction and the bottom line.
Leveraging Technology for Effective ABC Analysis
The digital era has transformed ABC Analysis from a manual, labor-intensive process into an automated, data-driven strategy. Advanced software tools and platforms now offer:
- Automated Classification: Sophisticated algorithms automatically categorize inventory based on predefined criteria, significantly reducing manual workload and the potential for error.
- Real-Time Data Analysis: Instant access to sales data, stock levels, and other key metrics allows for dynamic adjustments to inventory classifications.
- Integrated Forecasting Tools: Combining ABC with predictive analytics, businesses can anticipate demand fluctuations with greater accuracy, ensuring optimal stock levels.
How CADDi Drawer Can Help
CADDi Drawer, a cutting-edge digital platform designed for the manufacturing and procurement sectors, directly addresses the pressing challenges in data management within ABC analysis. Its capabilities can provide an innovative solution to many of the hurdles discussed earlier, particularly those related to data inconsistency, fragmentation, and the lack of a centralized system for data sharing and analysis.
Streamline activities in the procurement process
The following features enable you to streamline the time-consuming tasks of data collection and organization in procurement operations.
- Price data and supplier information can be automatically linked to each drawing and can also be exported together.
- By using keyword searches combined with similarity searches, the time spent searching for drawings and data in procurement tasks can be reduced.
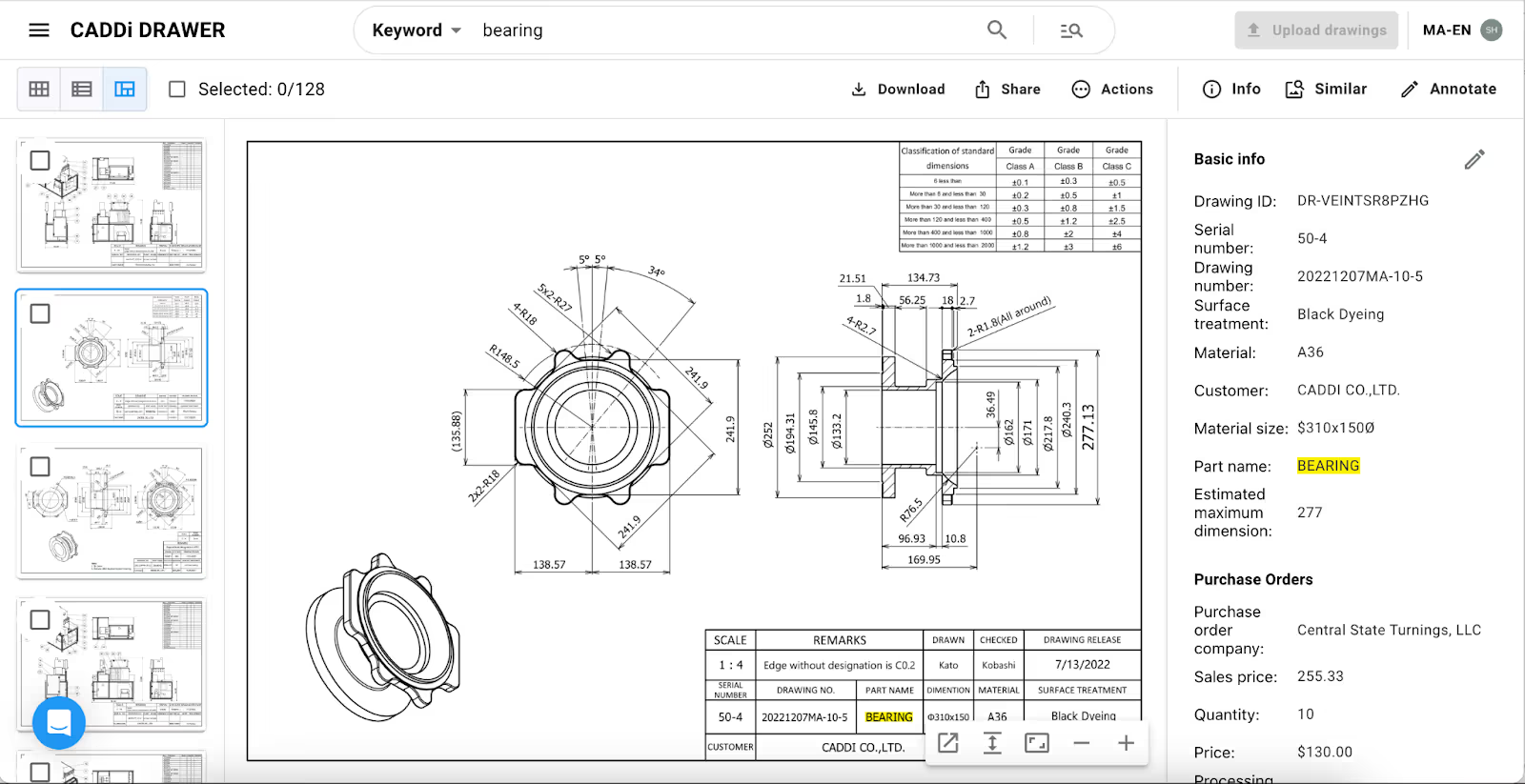
Enhancing Collaboration and Standardization
Collaboration and standardization across the supply chain are crucial for overcoming visibility challenges. CADDi Drawer fosters collaboration by enabling easy sharing and access to data among all supply chain participants. This collaborative environment ensures that everyone is on the same page, enhancing coordination and efficiency. Additionally, the platform supports data standardization, which is vital for integrating data from diverse sources and ensuring that it is comparable and actionable.
CADDi Drawer serves as a System of Insights (SoI), designed to leverage data primarily managed and stored by Systems of Records (SoR), like those represented by ERPs. Utilizing data stored in SoRs and data extracted and structured from drawings by CADDi Drawer, it supports procurement intelligence processes, including analyses and data processing for supplier selection and management, RFQ creation, and quote evaluations.
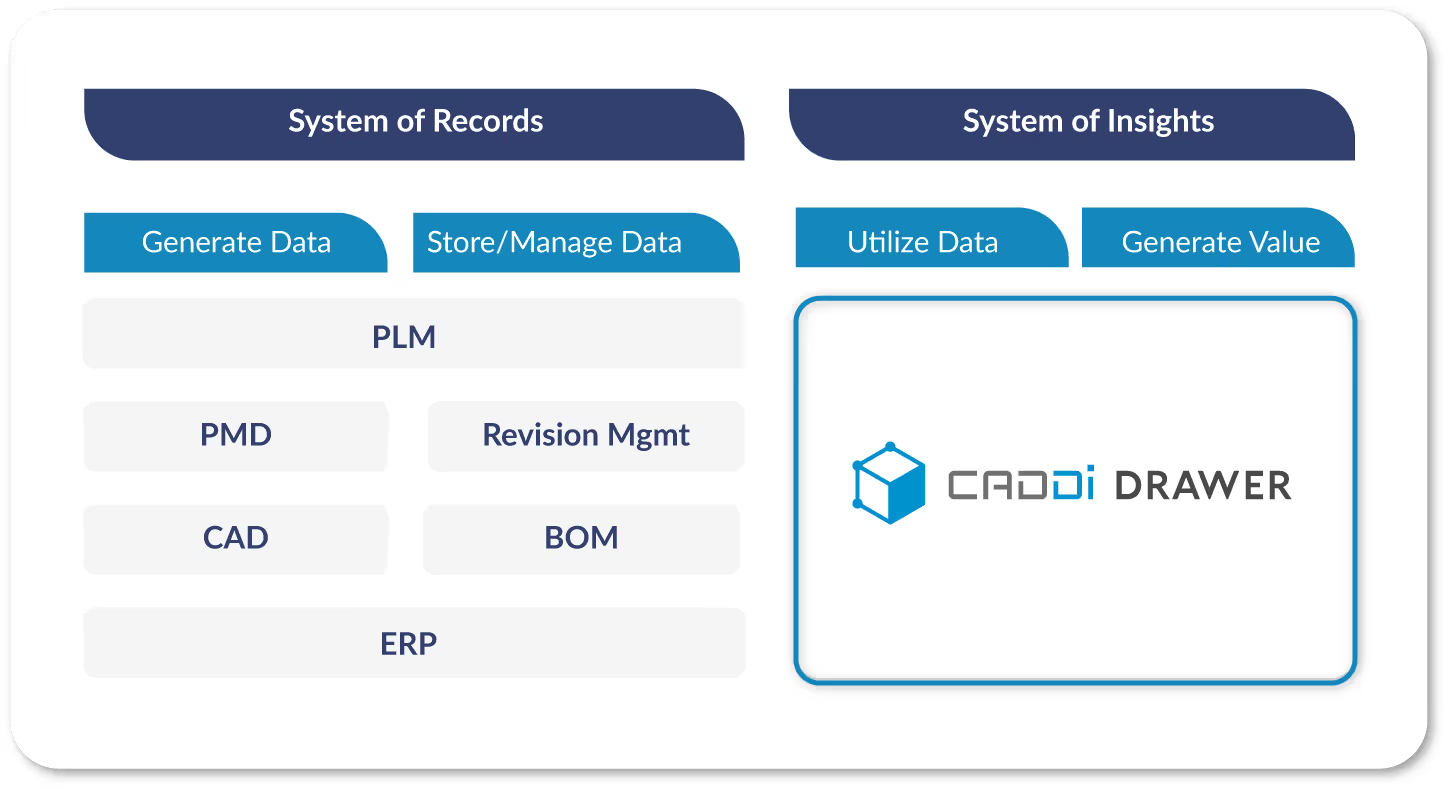
Are you grappling with the challenge of optimizing your inventory to meet demand efficiently? ABC Analysis, coupled with XYZ Analysis, provides a robust framework for procurement professionals.
This article delves into how strategic classification of inventory into A, B, and C categories, based on value and demand predictability, can streamline operations, enhance customer satisfaction, and improve demand forecasting. With practical insights and step-by-step guides, it equips you to navigate the complexities of procurement and manufacturing sectors effectively.
Understanding ABC Analysis
At the heart of supply chain optimization lies ABC Analysis, a systematic approach that classifies inventory based on its importance. The principle is straightforward yet powerful:
- Class A items are the VIPs of your inventory, accounting for a substantial portion of your company’s value with a relatively small percentage of total items.
- Class B items straddle the fence in terms of value and quantity, not as critical as A but more significant than C.
- Class C items, while numerous, contribute the least to your bottom line.
This classification enables businesses to tailor their focus and resources, ensuring that the most critical items receive the attention they deserve.
The Benefits of Implementing ABC Analysis
Strategic Resource Allocation: ABC Analysis isn’t just about knowing your inventory; it’s about smartly allocating your resources. By identifying Class A items, companies can align their efforts with customer demand, optimizing the use of personnel, time, and space for items that drive success.
- Better Customer Service: Understanding which items are most profitable allows for prioritizing higher service levels for those products, directly impacting customer satisfaction.
- Enhanced Product Life Cycle Management: Gaining insights into the life cycle stages of products aids in forecasting demand and maintaining appropriate inventory levels.
- Control Over High-Cost Items: Prioritizing Class A inventory ensures a company’s key products are always available, maintaining a healthy stock level.
- Reduced Storage Expenses: Carrying the right proportion of A, B, or C class stock minimizes the costs associated with excess inventory.
- Simplified Supply Chain Management: ABC Analysis aids in making informed decisions about supplier consolidation or shifts to reduce carrying costs and streamline operations.
Conducting an ABC Analysis: A Step-by-Step Guide
Embarking on ABC Analysis involves a meticulous process that transforms raw data into actionable insights. Here’s how to navigate through this critical path:
- Gather Your Data: Start with a comprehensive dataset of your inventory, including annual demand, unit cost, and total cost.
- Calculate the Value Percentage: Determine the cumulative value of each item to your overall inventory. This involves multiplying the annual demand by the unit cost for each item.
- Rank and Classify: Sort your items from highest to lowest based on their value percentage. Then, categorize them into A, B, and C classes, aligning with the principles of ABC Analysis. Typically, A items represent 70-80% of inventory value, B items 15-25%, and C items around 5%.
Addressing the Limitations and Challenges of ABC Analysis
While ABC Analysis offers a structured approach to inventory management, it’s not without its challenges. Awareness of these limitations enables businesses to navigate potential pitfalls more effectively:
- Parameter Instability: The dynamic nature of markets means classifications may need frequent revisions to reflect current realities.
- Limited Pattern Consideration: Standard ABC models might not fully account for variables like seasonality or new product launches.
- Resource Intensiveness: The process can be time-consuming and requires dedicated resources to maintain accuracy.
The Role of ABC Analysis in Demand Forecasting and Inventory Control
The true power of ABC Analysis lies in its ability to enhance demand forecasting and inventory control, leading to:
- More Accurate Demand Forecasting: By focusing on high-value A items, businesses can refine their forecasting models, minimizing the risk of overstock or stockouts.
- Strategic Inventory Control: Identifying which items to stock more of and which to reduce can significantly impact storage costs and capital allocation.
- Informed Pricing Strategies: Insights from ABC Analysis can guide pricing decisions, ensuring that high-demand items are priced for maximum profitability.
Incorporating ABC Analysis into your inventory management practices offers a roadmap to optimized operations. By understanding its benefits, navigating its challenges, and leveraging its insights for better demand forecasting and inventory control, businesses can position themselves for greater efficiency and competitiveness.
Combining ABC with XYZ Analysis for Comprehensive Inventory Management
For a more granular view of inventory management, ABC Analysis pairs seamlessly with XYZ Analysis. While ABC classifies items based on value, XYZ Analysis categorizes them by the predictability of demand:
- X items have stable consumption.
- Y items experience some fluctuation in consumption.
- Z items face heavy fluctuations.
This dual approach creates a classification matrix, offering a panoramic view of inventory that highlights items needing more attention due to demand uncertainties. It’s a strategy that prevents overstocking and shortages, ensuring a balanced inventory that can swiftly adapt to market changes.
By merging ABC with XYZ, businesses wield a powerful tool in the quest for supply chain efficiency, capable of navigating the unpredictable seas of customer demand and inventory management. This methodology not only sharpens focus on high-value items but also illuminates the nuances of demand variability, guiding strategic decisions that bolster both customer satisfaction and the bottom line.
Leveraging Technology for Effective ABC Analysis
The digital era has transformed ABC Analysis from a manual, labor-intensive process into an automated, data-driven strategy. Advanced software tools and platforms now offer:
- Automated Classification: Sophisticated algorithms automatically categorize inventory based on predefined criteria, significantly reducing manual workload and the potential for error.
- Real-Time Data Analysis: Instant access to sales data, stock levels, and other key metrics allows for dynamic adjustments to inventory classifications.
- Integrated Forecasting Tools: Combining ABC with predictive analytics, businesses can anticipate demand fluctuations with greater accuracy, ensuring optimal stock levels.
How CADDi Drawer Can Help
CADDi Drawer, a cutting-edge digital platform designed for the manufacturing and procurement sectors, directly addresses the pressing challenges in data management within ABC analysis. Its capabilities can provide an innovative solution to many of the hurdles discussed earlier, particularly those related to data inconsistency, fragmentation, and the lack of a centralized system for data sharing and analysis.
Streamline activities in the procurement process
The following features enable you to streamline the time-consuming tasks of data collection and organization in procurement operations.
- Price data and supplier information can be automatically linked to each drawing and can also be exported together.
- By using keyword searches combined with similarity searches, the time spent searching for drawings and data in procurement tasks can be reduced.
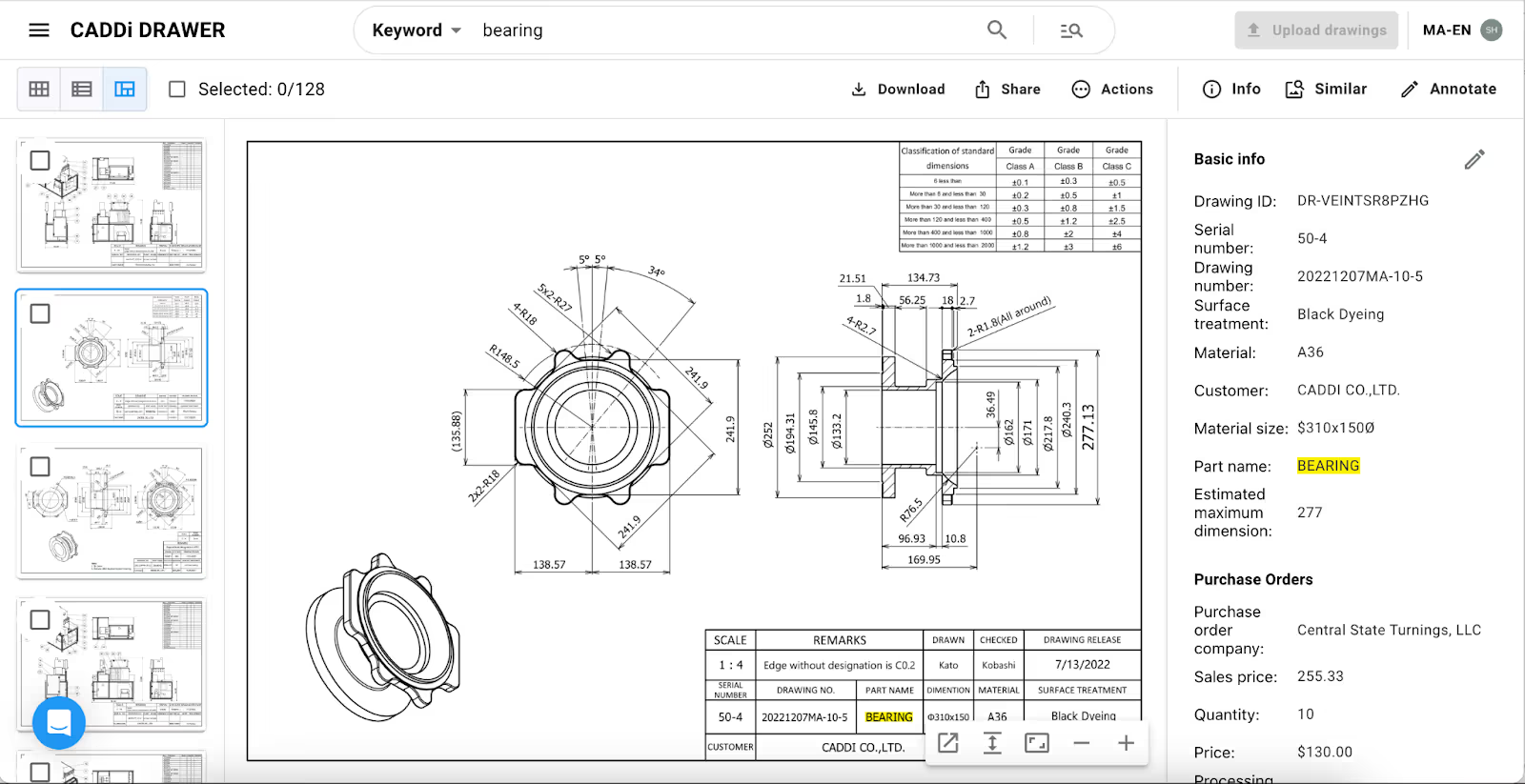
Enhancing Collaboration and Standardization
Collaboration and standardization across the supply chain are crucial for overcoming visibility challenges. CADDi Drawer fosters collaboration by enabling easy sharing and access to data among all supply chain participants. This collaborative environment ensures that everyone is on the same page, enhancing coordination and efficiency. Additionally, the platform supports data standardization, which is vital for integrating data from diverse sources and ensuring that it is comparable and actionable.
CADDi Drawer serves as a System of Insights (SoI), designed to leverage data primarily managed and stored by Systems of Records (SoR), like those represented by ERPs. Utilizing data stored in SoRs and data extracted and structured from drawings by CADDi Drawer, it supports procurement intelligence processes, including analyses and data processing for supplier selection and management, RFQ creation, and quote evaluations.
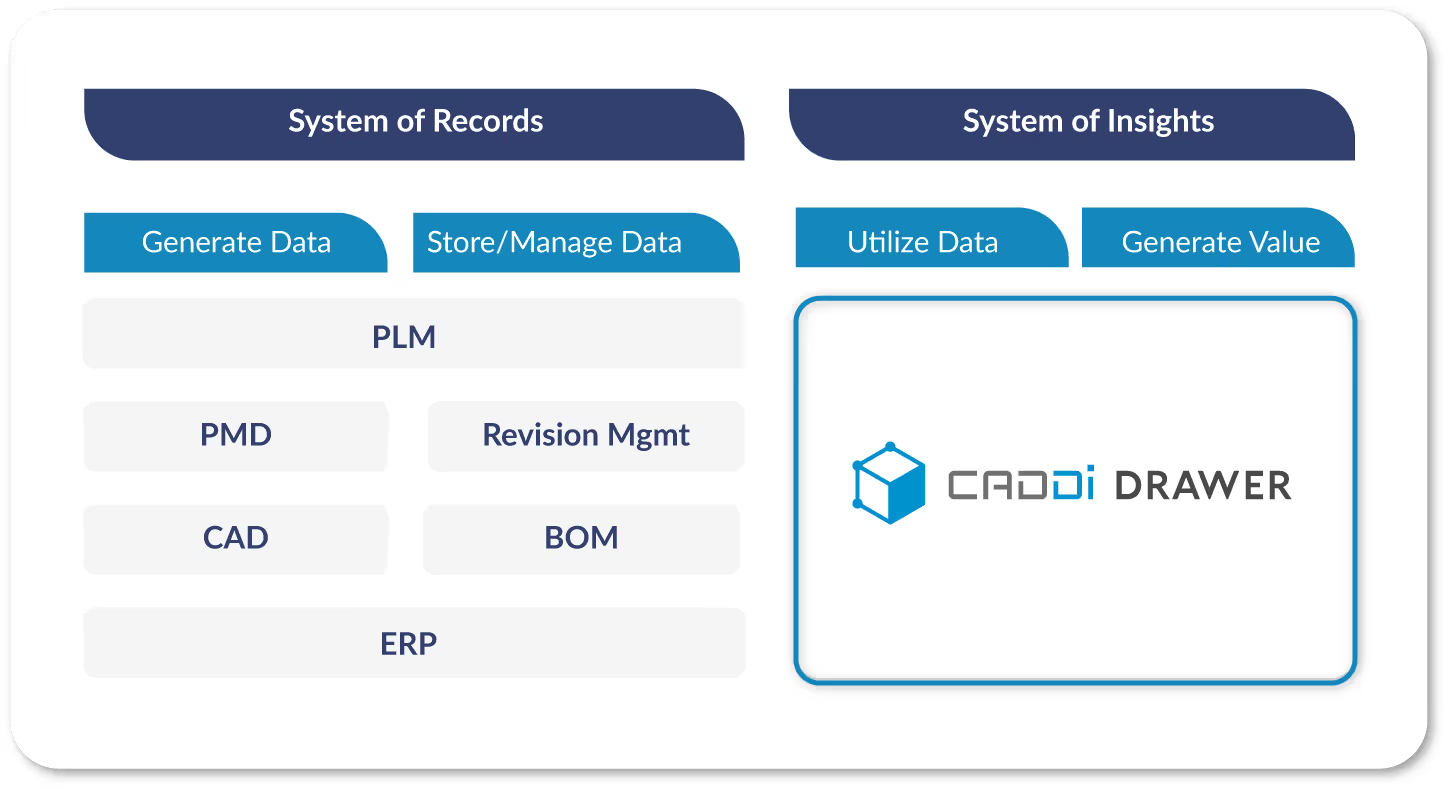
Ready to see CADDi Drawer in action? Get a personalized demo.
Subscribe to our Blog!
Related Resources
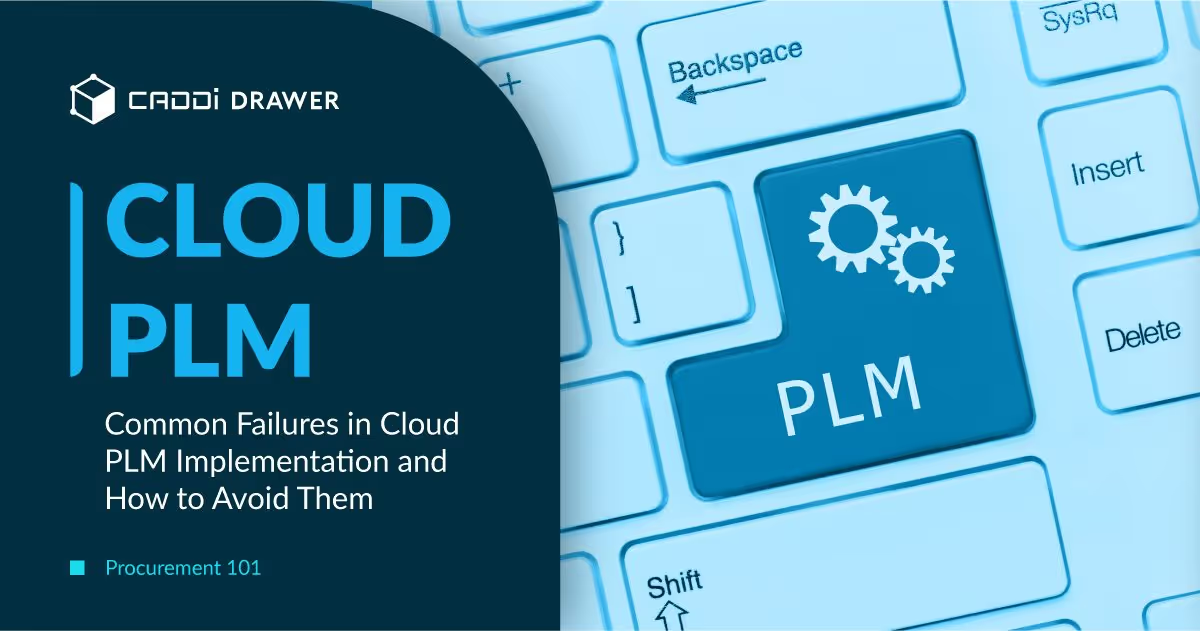
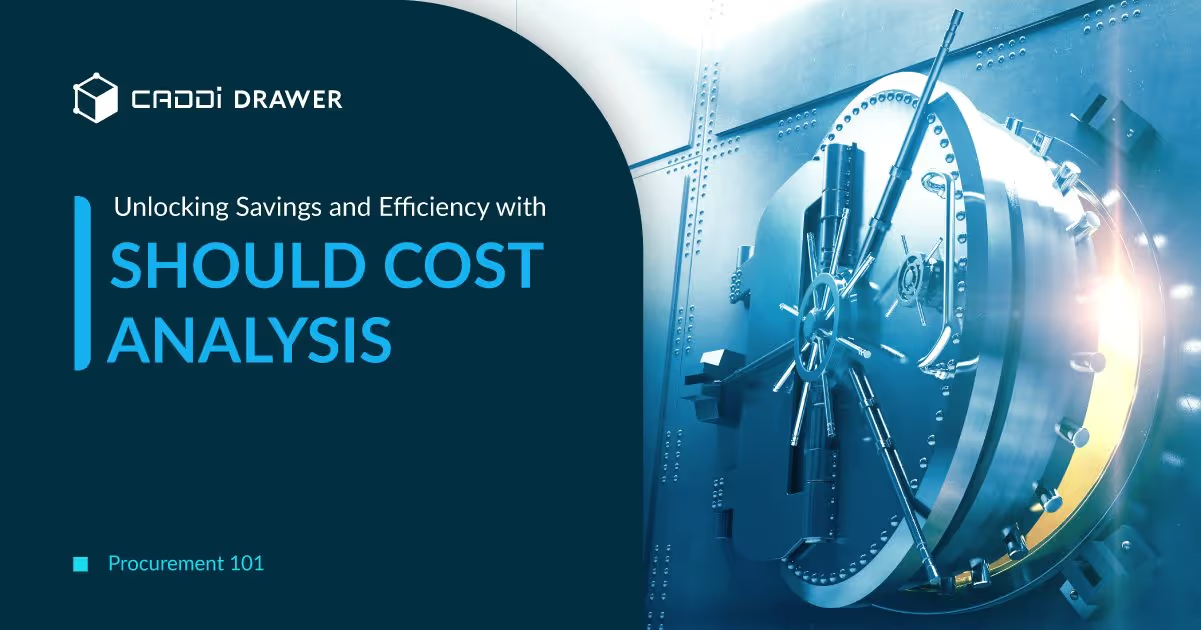
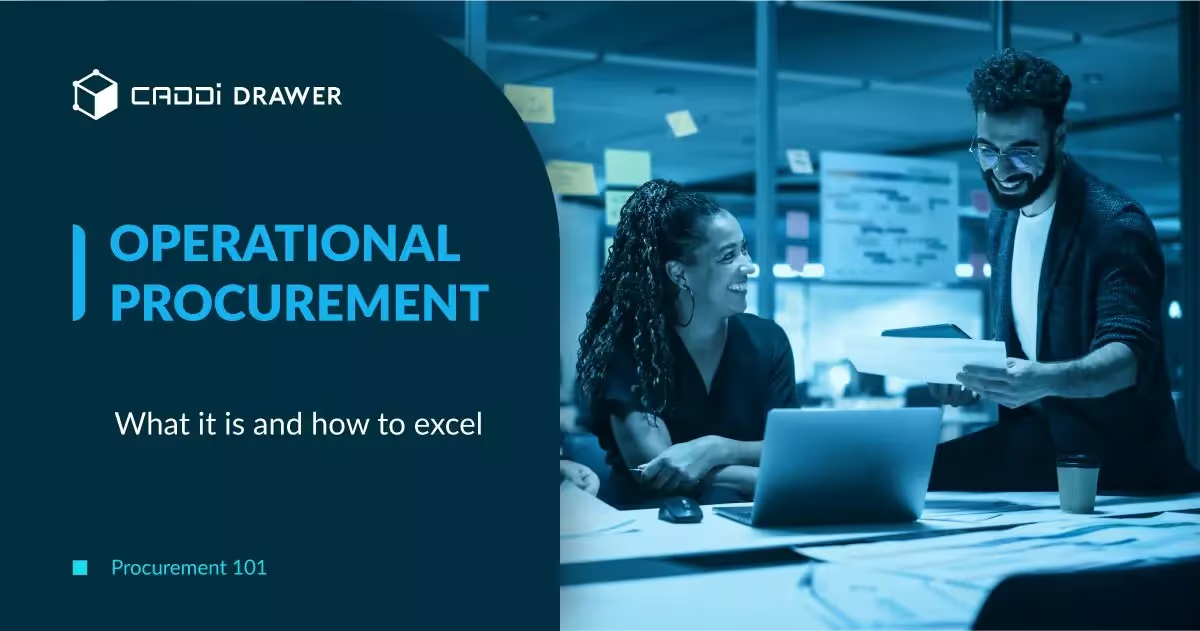
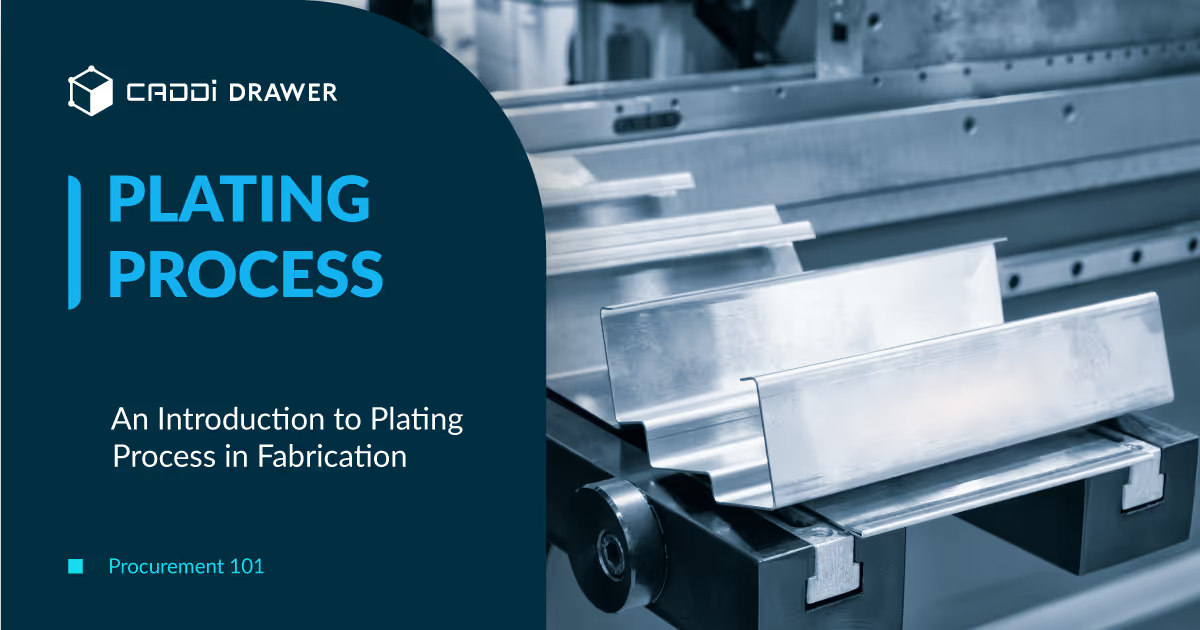
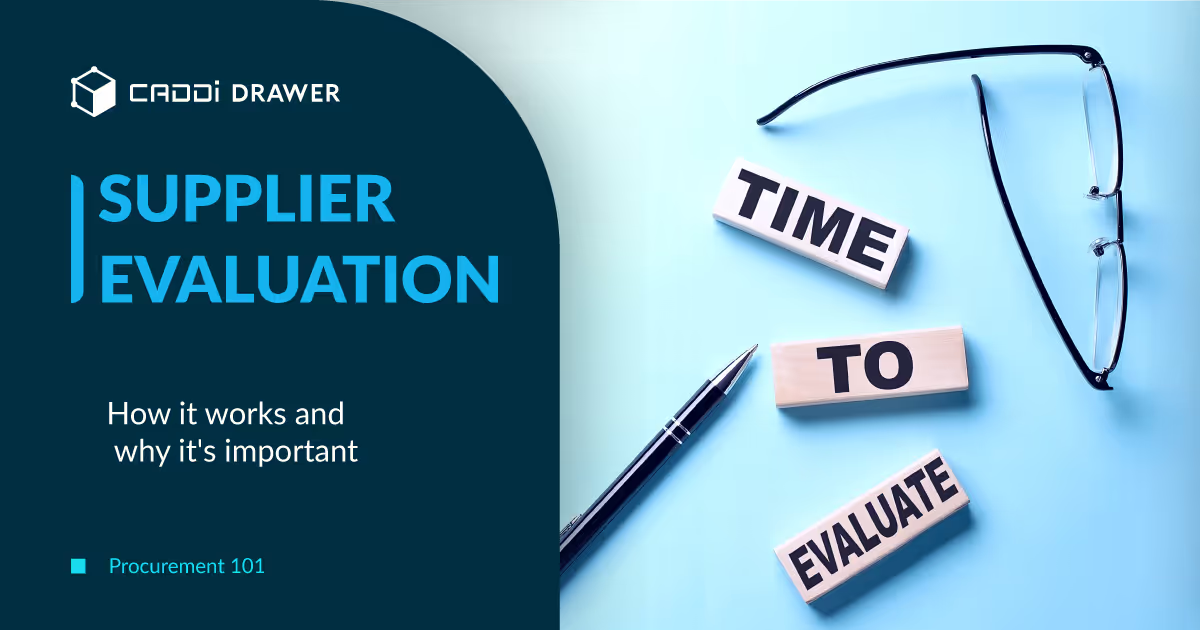
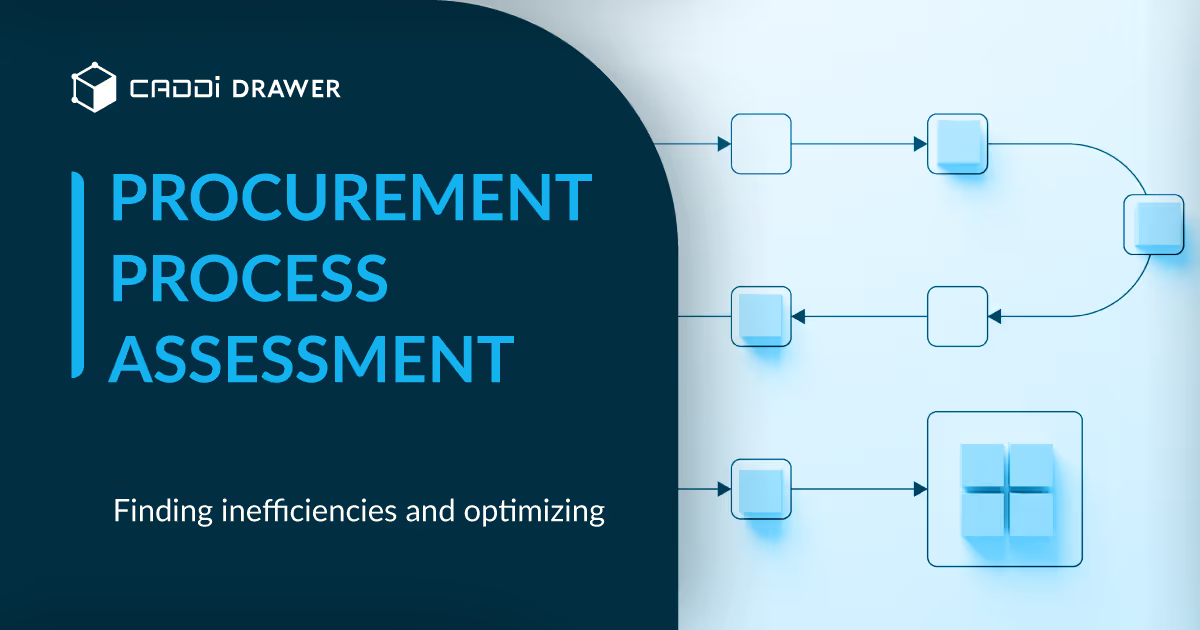