How to Enhance Collaboration between Engineering and Procurement Departments
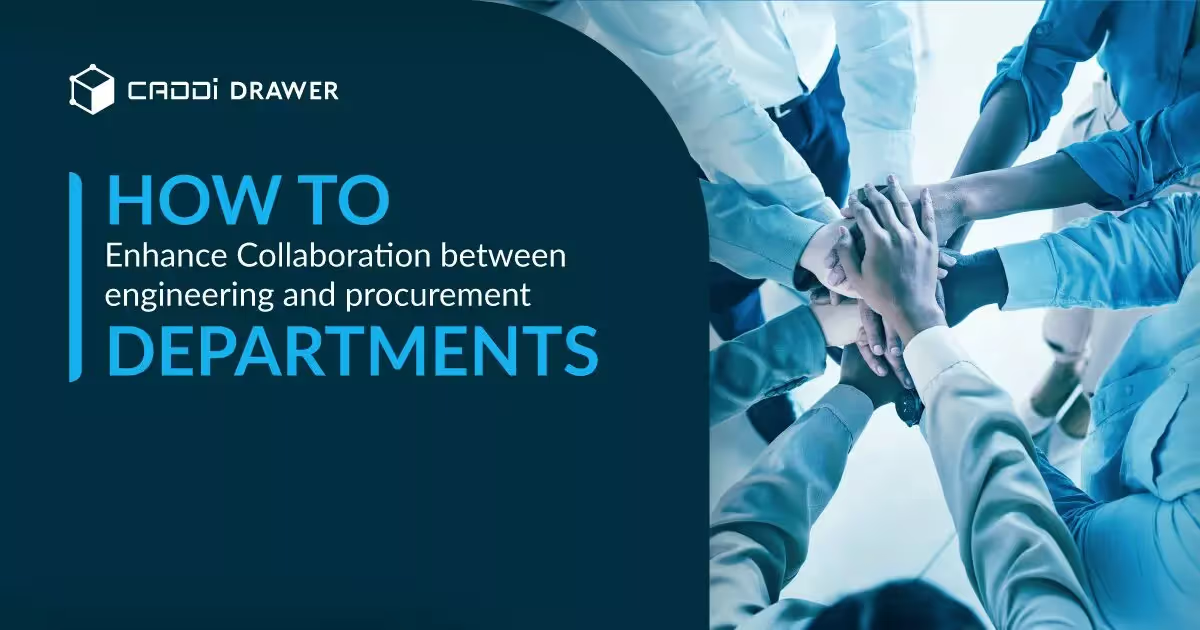
Table of Contents
Issues between engineering and procurement
Engineering and procurement are two critical functions within most companies. The engineering department is responsible for designing, developing, and testing products and services. Meanwhile, the procurement department manages sourcing, purchasing, and supplier relationships.
While these teams have distinct responsibilities, close collaboration between engineering and procurement is essential for business success. When these departments work together effectively, companies can develop higher quality products faster and at lower costs. Tight alignment also enables organizations to take advantage of emerging technologies and innovations from suppliers.
Unfortunately, engineering and procurement teams don’t always see eye-to-eye. Engineers may prioritize product performance and specifications over cost. Procurement professionals tend to focus on getting the lowest price from vendors. Without shared goals and incentives, the relationship can become adversarial. Overcoming this “us vs. them” mentality is key to unlocking the benefits of an integrated approach.
Strengthening the engineering-procurement collaboration requires effort from leaders across the organization. However, the payoff can be tremendous in terms of improved time-to-market, product innovation, and bottom-line results. This guide will explore practical strategies that companies can implement to enhance teamwork between these critical functions.
Define Shared Goals and Metrics
A key step in enhancing collaboration between engineering and procurement is to align both departments on shared objectives and establish common metrics to track progress. Some shared goals to focus on include:
- Reducing costs
- Improving quality
- Increasing efficiency and speed
By defining these types of mutual objectives that both departments care about, it encourages working together versus in silos. Along with shared goals, implement common KPIs that engineering and procurement will both be measured against. This could include metrics like:
- Cost reduction targets
- Quality defect rates
- Cycle time from procurement to production
- Supplier performance
With regular reviews of the KPIs, both departments will be motivated and accountable to work collaboratively to hit the targets. Celebrate wins together when goals are exceeded. If progress stalls, hold joint meetings to identify obstacles and develop solutions jointly.
Aligning on shared goals and metrics is a powerful step to break down silos between engineering and procurement. It provides focus and urgency to enhance integration for the good of the overall organization.
Improve Communication
Regular communication between engineering and procurement is essential for effective collaboration. Here are some ways to improve communication:
- Hold regular meetings between departments to align on project needs, timelines, and specifications. Daily standups or weekly status updates can ensure both teams are on the same page.
- Designate liaisons as main contacts between departments. Having a go-to person in each department gives individuals direct contact for questions and coordination.
- Use collaboration tools to share documents and communicate. Platforms like Slack, Microsoft Teams, and Google Workspace provide channels for messaging, file sharing, and video calls to connect cross-departmental teams.
- Create a shared database to store project information like requirements, design documents, budgets, and timelines in a central location accessible to both departments.
- Encourage informal communication through team building activities. Things like lunch meetings, happy hours, or site visits allow connections between departments to form organically.
- Provide training for employees on collaborative practices like active listening, accountability, and conflict resolution. This ensures productive interactions when issues arise.
- Implement project management protocols requiring sign-offs between departments at key milestones. This ensures proper alignment at each stage.
- Conduct post-project reviews to identify areas for better collaboration in the future. Continuously refining processes is key for improvement over time.
Cross-Training and Job Rotation
One effective way to enhance collaboration between engineering and procurement is through cross-training and job rotation programs. These allow employees to gain firsthand experience in the other department.
- Consider having engineers spend a few weeks working alongside the procurement team to understand their processes, challenges, and objectives. Similarly, procurement staff could job shadow engineers to gain insights into design work and project timelines.
- Formal job rotation programs can also be implemented, where employees rotate between departments for set periods, such as 3-6 months. This builds empathy and shows how their roles connect to achieve shared goals.
- Managers should identify participants who are open to learning and collaborating. Schedule rotations to minimize disruptions. Employees should have a designated buddy or mentor in the department they are visiting.
- After rotations, have employees share their learnings through presentations, workshops, or debriefs. They can provide feedback on processes to improve collaboration. Their unique perspectives often lead to insights others may have missed.
- Make rotations a two-way exchange. This ensures both departments benefit equally from fresh viewpoints. The focus should be on improving collaboration and processes, not evaluating individual employees.
- Consider starting with pilot programs for interested employees first before scaling up. Job rotations require planning but lead to huge payoffs in breaking down silos.
Leadership Commitment
Getting buy-in from senior management is crucial for enhancing collaboration between engineering and procurement. Leaders set the tone and demonstrate what’s important through their actions and communications.
To obtain leadership commitment:
- Present the benefits of collaboration. Show how increased coordination can lead to reduced costs, faster time-to-market, higher quality, and better outcomes for the business overall. Use data and examples to make the case.
- Get leaders publicly behind the initiative. Have senior managers express their support in company meetings, emails, and other communications. Make it clear this is a priority.
- Lead by example. Managers should actively participate in collaborative efforts, attend cross-functional meetings, recognize collaborative wins, and call out siloed behaviors. Their day-to-day involvement emphasizes importance.
- Align collaboration with strategy. Tie cross-functional coordination to core business objectives so it’s not seen as extra work. Show how it directly furthers organizational goals.
- Provide resources. Make sure teams have time, budget, and infrastructure to collaborate. This shows the company is willing to invest in it.
- Measure and track progress. Have senior management monitor and report regularly on collaboration metrics. This demonstrates ongoing commitment vs just initial lip service.
With visible and authentic commitment from leadership, a culture shift towards increased collaboration will take hold. Employees take cues from management’s actions, not just words.
Here is the additional section for the article on enhancing engineering-procurement collaboration, incorporating the information from the text and images:
Leverage Technology to Integrate Data and Break Down Silos
Implementing a platform like CADDi Drawer can be a game-changer for driving collaboration between engineering and procurement by integrating disparate data sources and making information easily accessible across teams.
.avif)
CADDi Drawer allows companies to upload a variety of engineering and supply chain data, including CAD/CAM files, PLM/PDM/BOM info, ERP/EDI details, spec sheets, quality defect reports, and more. The system then automatically links this data to the associated drawings. For example, procurement teams can access cost breakdowns, supplier information, and pricing, while seeing the actual drawing of the part. This provides much-needed context and a “single source of truth”.
The platform also uses AI to automatically extract data from PDF drawings, including handwritten ones. It scans and converts drawings to be fully searchable by any parameter – material, part name, size, designer, etc. This allows teams to quickly find relevant drawings.
What’s more, the patented technology identifies the actual geometry and shape of parts to surface similar drawings, even if they are decades old. Engineers can easily find existing designs, while procurement can see what was previously purchased, from whom, and at what price. This enables teams to identify opportunities to reuse parts, save time, and drive cost savings.
With all drawing data extracted and enriched with corresponding supply chain info, CADDi makes it simple to download everything into a single Excel file for analysis and sharing. This eliminates manual data gathering and ensures everyone is working off the same real-time information.
.avif)
By implementing a central platform to integrate data, automate manual work, and enable easy access to drawings and related information, companies can transform collaboration. With CADDi Drawer, engineering and procurement teams can make more informed decisions together to optimize designs, streamline processes, and maximize profitability. Breaking down those data silos is key to working collaboratively to achieve business goals.
Issues between engineering and procurement
Engineering and procurement are two critical functions within most companies. The engineering department is responsible for designing, developing, and testing products and services. Meanwhile, the procurement department manages sourcing, purchasing, and supplier relationships.
While these teams have distinct responsibilities, close collaboration between engineering and procurement is essential for business success. When these departments work together effectively, companies can develop higher quality products faster and at lower costs. Tight alignment also enables organizations to take advantage of emerging technologies and innovations from suppliers.
Unfortunately, engineering and procurement teams don’t always see eye-to-eye. Engineers may prioritize product performance and specifications over cost. Procurement professionals tend to focus on getting the lowest price from vendors. Without shared goals and incentives, the relationship can become adversarial. Overcoming this “us vs. them” mentality is key to unlocking the benefits of an integrated approach.
Strengthening the engineering-procurement collaboration requires effort from leaders across the organization. However, the payoff can be tremendous in terms of improved time-to-market, product innovation, and bottom-line results. This guide will explore practical strategies that companies can implement to enhance teamwork between these critical functions.
Define Shared Goals and Metrics
A key step in enhancing collaboration between engineering and procurement is to align both departments on shared objectives and establish common metrics to track progress. Some shared goals to focus on include:
- Reducing costs
- Improving quality
- Increasing efficiency and speed
By defining these types of mutual objectives that both departments care about, it encourages working together versus in silos. Along with shared goals, implement common KPIs that engineering and procurement will both be measured against. This could include metrics like:
- Cost reduction targets
- Quality defect rates
- Cycle time from procurement to production
- Supplier performance
With regular reviews of the KPIs, both departments will be motivated and accountable to work collaboratively to hit the targets. Celebrate wins together when goals are exceeded. If progress stalls, hold joint meetings to identify obstacles and develop solutions jointly.
Aligning on shared goals and metrics is a powerful step to break down silos between engineering and procurement. It provides focus and urgency to enhance integration for the good of the overall organization.
Improve Communication
Regular communication between engineering and procurement is essential for effective collaboration. Here are some ways to improve communication:
- Hold regular meetings between departments to align on project needs, timelines, and specifications. Daily standups or weekly status updates can ensure both teams are on the same page.
- Designate liaisons as main contacts between departments. Having a go-to person in each department gives individuals direct contact for questions and coordination.
- Use collaboration tools to share documents and communicate. Platforms like Slack, Microsoft Teams, and Google Workspace provide channels for messaging, file sharing, and video calls to connect cross-departmental teams.
- Create a shared database to store project information like requirements, design documents, budgets, and timelines in a central location accessible to both departments.
- Encourage informal communication through team building activities. Things like lunch meetings, happy hours, or site visits allow connections between departments to form organically.
- Provide training for employees on collaborative practices like active listening, accountability, and conflict resolution. This ensures productive interactions when issues arise.
- Implement project management protocols requiring sign-offs between departments at key milestones. This ensures proper alignment at each stage.
- Conduct post-project reviews to identify areas for better collaboration in the future. Continuously refining processes is key for improvement over time.
Cross-Training and Job Rotation
One effective way to enhance collaboration between engineering and procurement is through cross-training and job rotation programs. These allow employees to gain firsthand experience in the other department.
- Consider having engineers spend a few weeks working alongside the procurement team to understand their processes, challenges, and objectives. Similarly, procurement staff could job shadow engineers to gain insights into design work and project timelines.
- Formal job rotation programs can also be implemented, where employees rotate between departments for set periods, such as 3-6 months. This builds empathy and shows how their roles connect to achieve shared goals.
- Managers should identify participants who are open to learning and collaborating. Schedule rotations to minimize disruptions. Employees should have a designated buddy or mentor in the department they are visiting.
- After rotations, have employees share their learnings through presentations, workshops, or debriefs. They can provide feedback on processes to improve collaboration. Their unique perspectives often lead to insights others may have missed.
- Make rotations a two-way exchange. This ensures both departments benefit equally from fresh viewpoints. The focus should be on improving collaboration and processes, not evaluating individual employees.
- Consider starting with pilot programs for interested employees first before scaling up. Job rotations require planning but lead to huge payoffs in breaking down silos.
Leadership Commitment
Getting buy-in from senior management is crucial for enhancing collaboration between engineering and procurement. Leaders set the tone and demonstrate what’s important through their actions and communications.
To obtain leadership commitment:
- Present the benefits of collaboration. Show how increased coordination can lead to reduced costs, faster time-to-market, higher quality, and better outcomes for the business overall. Use data and examples to make the case.
- Get leaders publicly behind the initiative. Have senior managers express their support in company meetings, emails, and other communications. Make it clear this is a priority.
- Lead by example. Managers should actively participate in collaborative efforts, attend cross-functional meetings, recognize collaborative wins, and call out siloed behaviors. Their day-to-day involvement emphasizes importance.
- Align collaboration with strategy. Tie cross-functional coordination to core business objectives so it’s not seen as extra work. Show how it directly furthers organizational goals.
- Provide resources. Make sure teams have time, budget, and infrastructure to collaborate. This shows the company is willing to invest in it.
- Measure and track progress. Have senior management monitor and report regularly on collaboration metrics. This demonstrates ongoing commitment vs just initial lip service.
With visible and authentic commitment from leadership, a culture shift towards increased collaboration will take hold. Employees take cues from management’s actions, not just words.
Here is the additional section for the article on enhancing engineering-procurement collaboration, incorporating the information from the text and images:
Leverage Technology to Integrate Data and Break Down Silos
Implementing a platform like CADDi Drawer can be a game-changer for driving collaboration between engineering and procurement by integrating disparate data sources and making information easily accessible across teams.
.avif)
CADDi Drawer allows companies to upload a variety of engineering and supply chain data, including CAD/CAM files, PLM/PDM/BOM info, ERP/EDI details, spec sheets, quality defect reports, and more. The system then automatically links this data to the associated drawings. For example, procurement teams can access cost breakdowns, supplier information, and pricing, while seeing the actual drawing of the part. This provides much-needed context and a “single source of truth”.
The platform also uses AI to automatically extract data from PDF drawings, including handwritten ones. It scans and converts drawings to be fully searchable by any parameter – material, part name, size, designer, etc. This allows teams to quickly find relevant drawings.
What’s more, the patented technology identifies the actual geometry and shape of parts to surface similar drawings, even if they are decades old. Engineers can easily find existing designs, while procurement can see what was previously purchased, from whom, and at what price. This enables teams to identify opportunities to reuse parts, save time, and drive cost savings.
With all drawing data extracted and enriched with corresponding supply chain info, CADDi makes it simple to download everything into a single Excel file for analysis and sharing. This eliminates manual data gathering and ensures everyone is working off the same real-time information.
.avif)
By implementing a central platform to integrate data, automate manual work, and enable easy access to drawings and related information, companies can transform collaboration. With CADDi Drawer, engineering and procurement teams can make more informed decisions together to optimize designs, streamline processes, and maximize profitability. Breaking down those data silos is key to working collaboratively to achieve business goals.
Ready to see CADDi Drawer in action? Get a personalized demo.
Subscribe to our Blog!
Related Resources
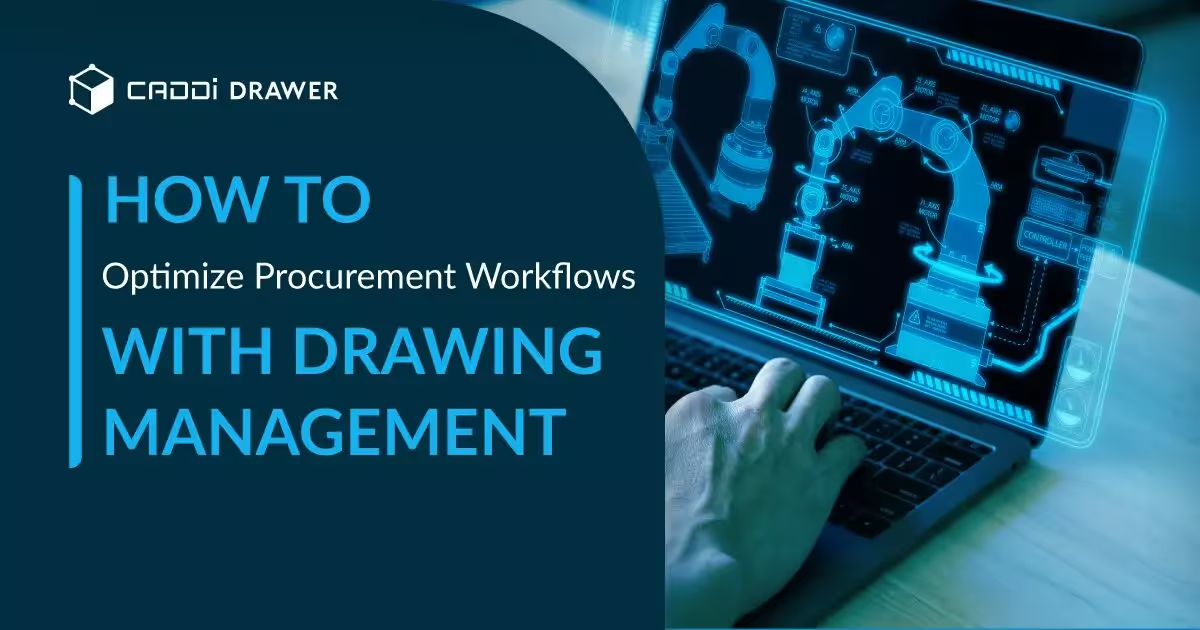
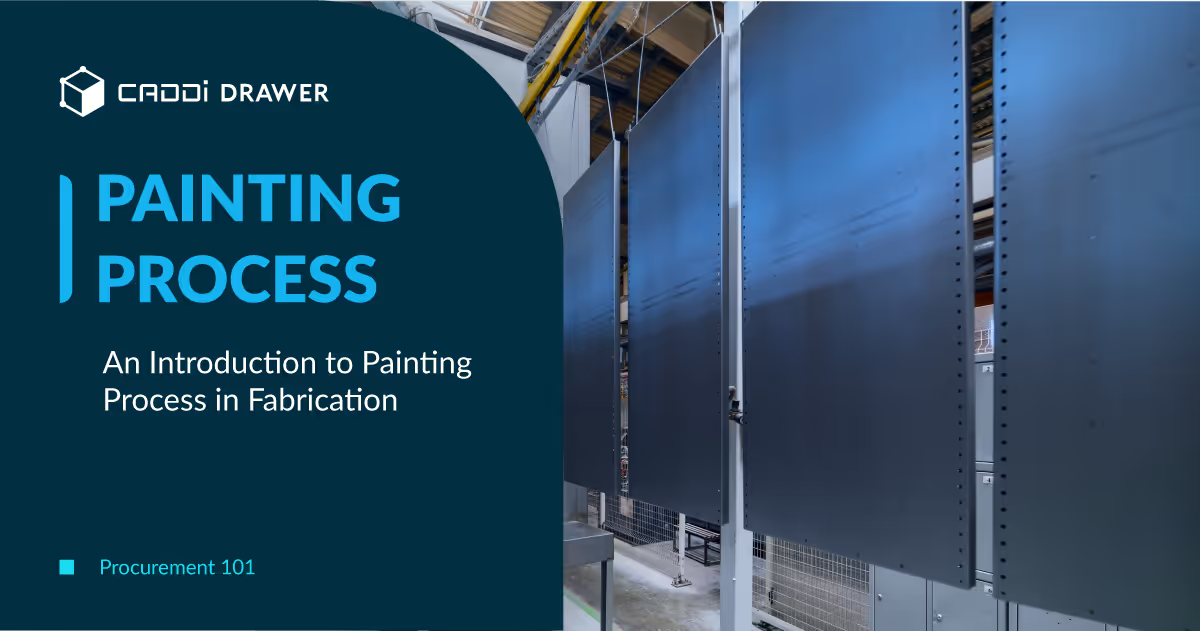
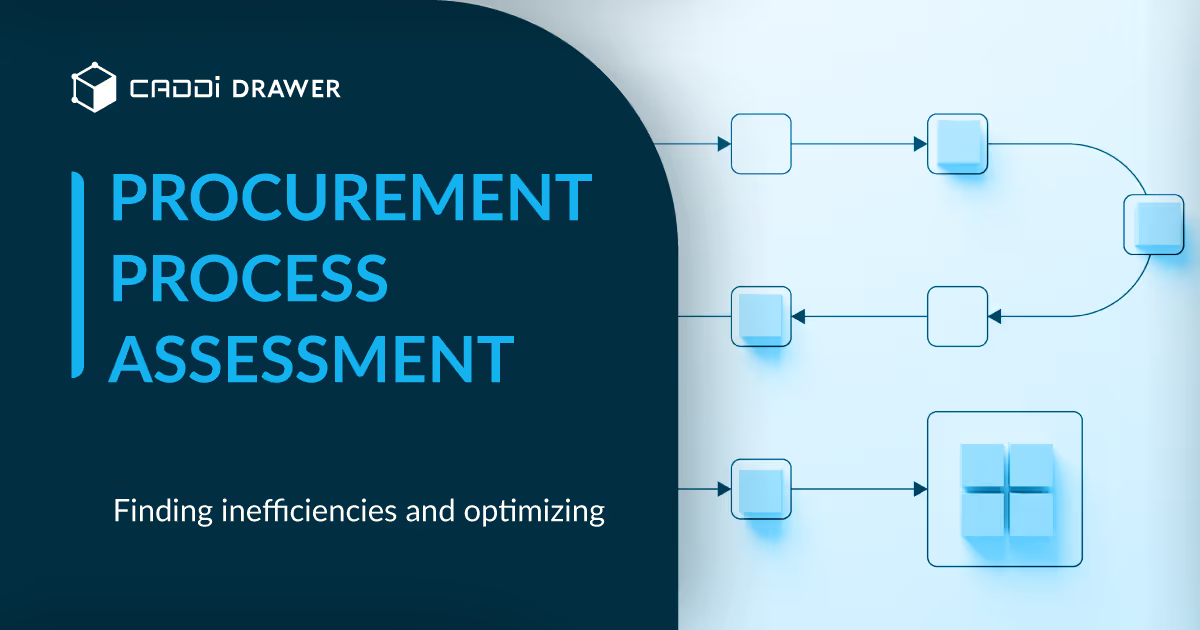
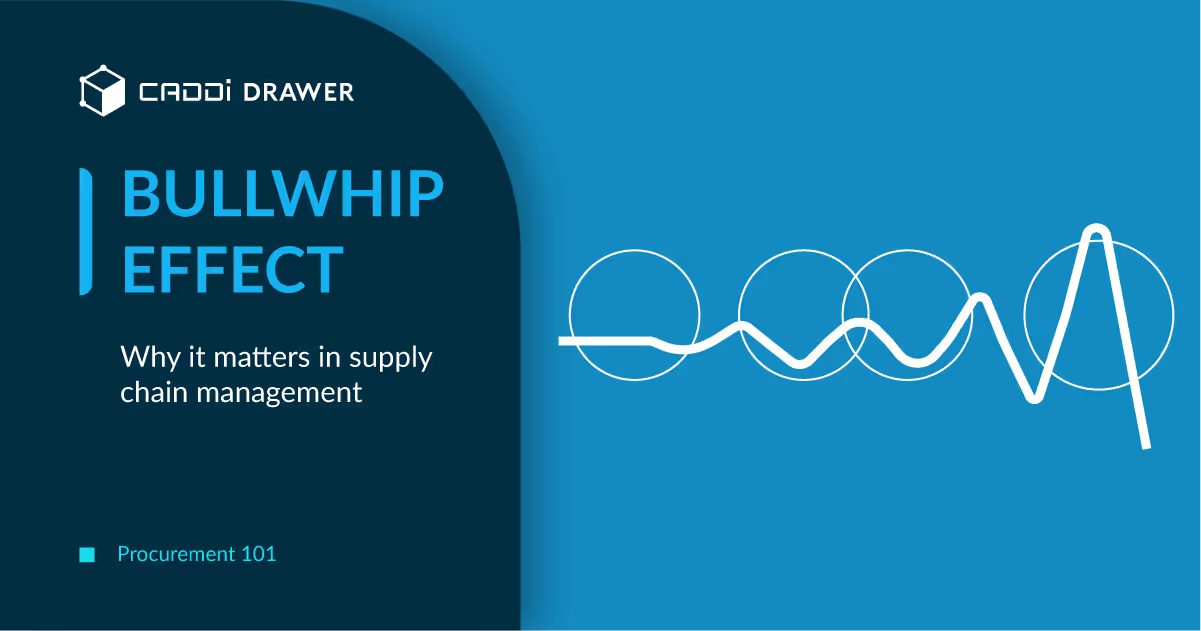
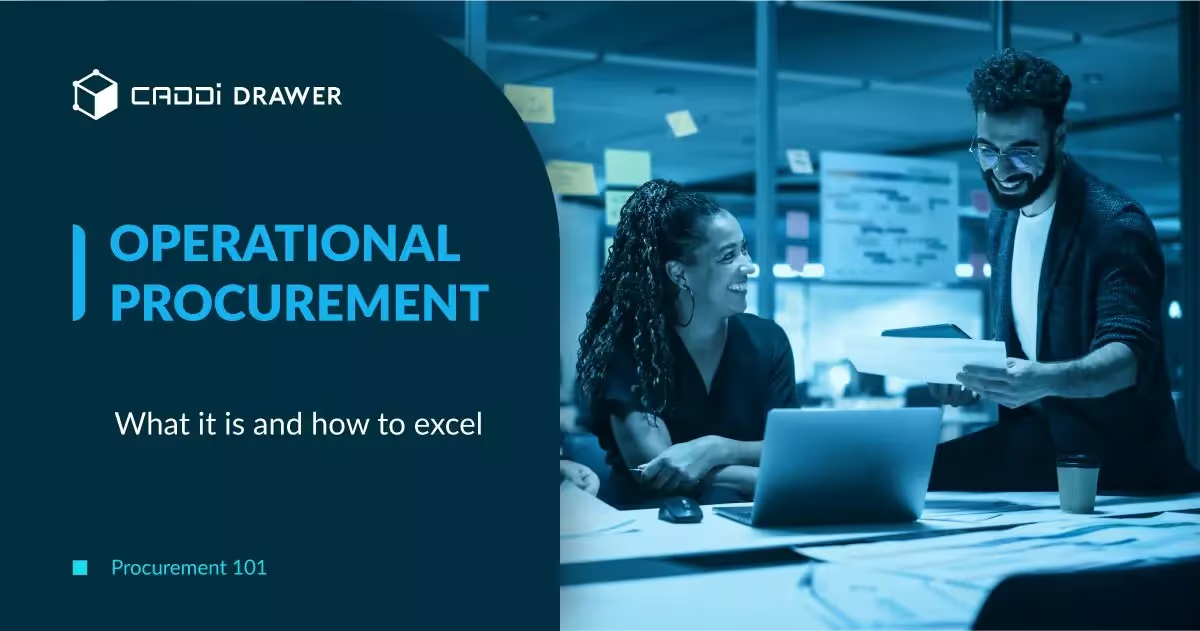
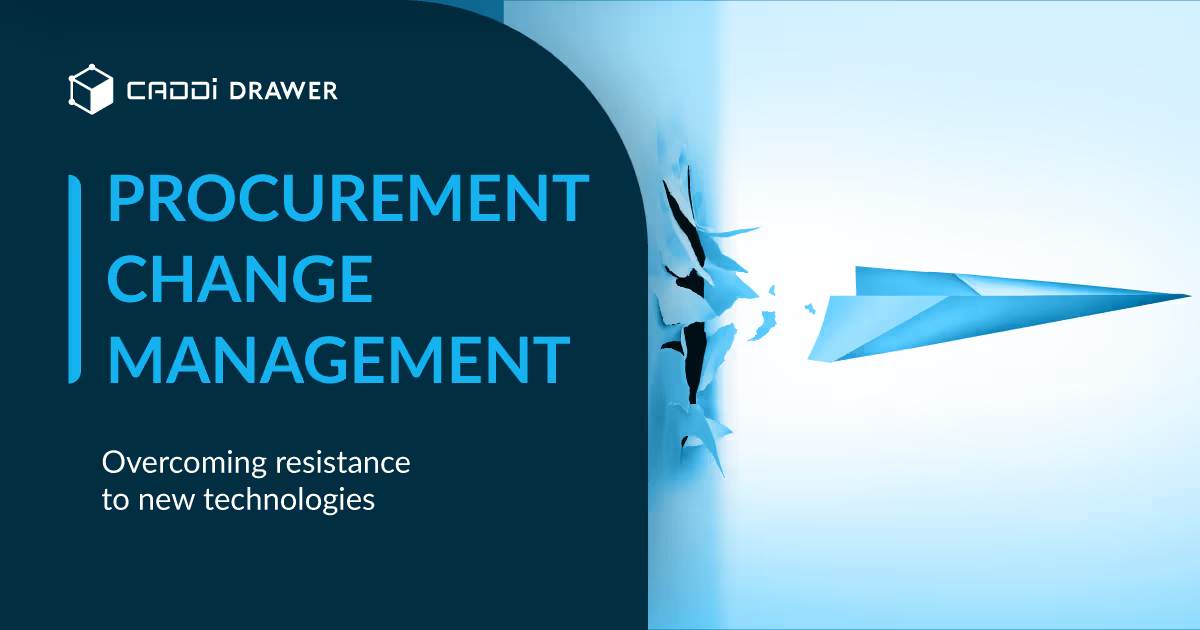