Procurement 101: Demand Planning – Maximize impacts through integration with the supply side
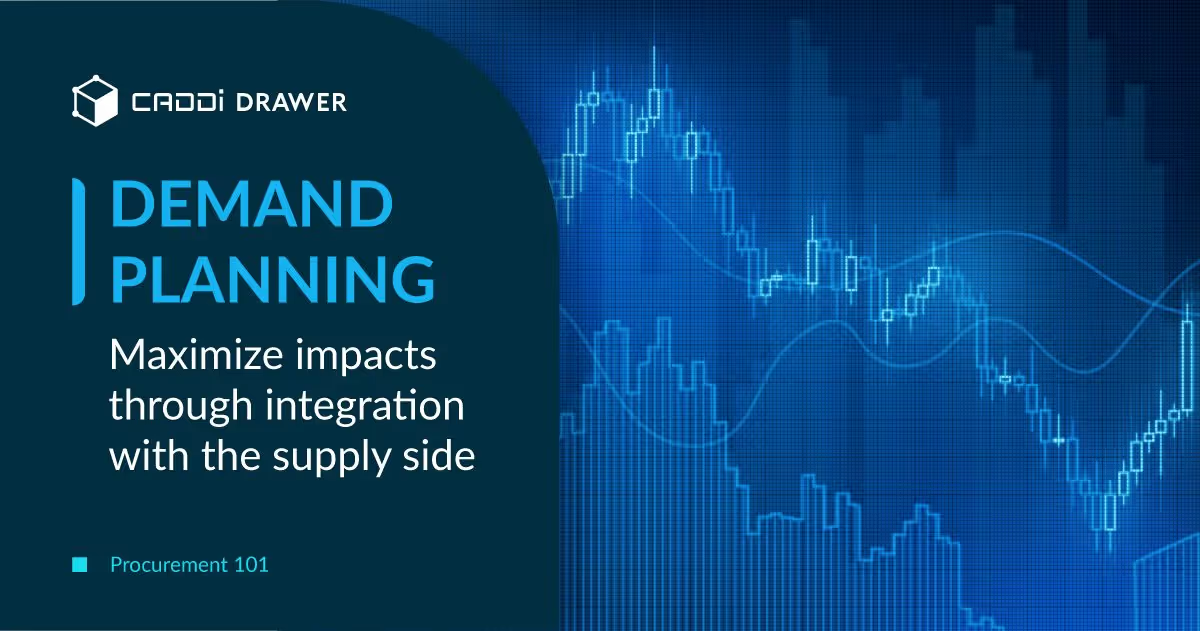
Table of Contents
Imagine the scenario: a leading electronics manufacturer, facing the annual surge in demand ahead of the holiday season, leverages advanced demand planning techniques to align its production schedules precisely with market expectations. By meticulously analyzing past sales data, current market trends, and future forecasts, the company not only meets the spike in consumer demand but does so without accruing excess inventory, thus optimizing its profitability.
This tale is not unique but a testament to the transformative power of effective demand planning in the manufacturing landscape. It underscores the process’s role as a linchpin in the supply chain, ensuring products are delivered reliably and customer satisfaction remains high.
Key Approaches in Demand Planning
Demand planning is the strategic process that underpins supply chain management, ensuring that manufacturing aligns seamlessly with market demand. It’s a multifaceted discipline that encompasses sales forecasting, inventory management, and comprehensive supply chain oversight. Effective demand planning facilitates accurate revenue forecasts, optimizes inventory levels to match demand fluctuations, and enhances overall profitability for specific channels or products.
The essence of demand planning lies in its processes, which are critical for forecasting demand accurately.
These include trade promotion management (TPM), which involves marketing tactics like discounts and in-store promotions to generate demand. By collaborating at detailed and aggregated levels, companies can swiftly adjust their products, campaigns, and promotions, ensuring they remain aligned with distributor and customer signals across all timeframes.
Another crucial aspect is sales and operations planning (S&OP). This cross-functional process brings together all relevant departments, including sales, marketing, production, and finance, to ensure that the demand forecast aligns with production capacity and financial objectives. S&OP meetings facilitate consensus on a single demand plan, which serves as the foundation for operational planning and resource allocation, helping to balance supply and demand effectively.
Collaborative planning, forecasting, and replenishment (CPFR) further enhances demand planning by fostering collaboration between suppliers, manufacturers, and retailers. By sharing information and forecasts, all parties can work together to improve the accuracy of demand predictions, optimize inventory levels, and reduce costs. This collaborative approach not only strengthens supply chain partnerships but also ensures that the end-to-end supply chain is more responsive to consumer needs.
Technology plays a pivotal role in streamlining demand planning processes. Advanced planning and scheduling (APS) systems integrate data from various sources, providing a comprehensive view of demand, inventory, production capacity, and supply chain constraints. These systems use sophisticated algorithms to generate optimal production plans that meet demand while minimizing costs and maximizing resource utilization.
Demand Planning Models
Diving deeper into the world of demand planning, we encounter various models that businesses employ to forecast future demand accurately.
Econometric models, for instance, consider both dependent and independent variables, analyzing the intricate web of cause and effect that influences demand. A famous case is that of a multinational technology company which, by employing econometric models, was able to anticipate market shifts with a remarkable 85% accuracy rate, significantly improving its supply chain efficiency.
Trend projection models, another pillar of demand planning, rely on historical data to forecast future demand. By identifying patterns and controlling for anomalies, companies can prepare for predictable fluctuations in demand. A retail giant exemplified the power of trend projection by adjusting its inventory levels ahead of peak shopping seasons, resulting in a 20% improvement in customer satisfaction due to reduced stockouts.
Barometric models, which take into account economic indicators like inflation rates and consumer spending trends, have proven essential for industries sensitive to economic cycles. A leading automobile manufacturer used these models to adjust production in anticipation of an economic downturn, effectively avoiding overproduction and aligning inventory with reduced consumer spending, thus maintaining profitability during challenging times.
If you are in charge of procurement for a manufacturer of industrial machines or plant equipment, that is, products that are high-mix low-volume (HMLV), you might think that the above models are difficult to directly apply because they are designed for mass production. That is indeed the case.
Of course, don’t forget to utilize the essence of the above models, but in addition, approaches like the following can be applicable.
For HMLV manufacturers, building strong relationships with key customers and engaging in collaborative forecasting can significantly enhance demand planning accuracy. This practice involves sharing data and insights between the manufacturer and its customers to jointly develop more accurate forecasts. Given the customized nature of many HMLV products, understanding customer plans and expectations can lead to better-aligned production schedules and improved customer satisfaction.
Lean Demand Planning and Its Benefits
Lean demand planning emphasizes efficiency and waste reduction throughout the supply chain. By identifying and eliminating non-value-added steps, companies can significantly enhance their operational efficiency. For example, a consumer electronics company implemented lean principles in its demand planning process, automating data entry and report generation.
In the manufacturing industry, lean demand planning goes beyond just automating processes and adopting a pull-based approach; it incorporates a set of specific methods and practices designed to streamline operations, minimize waste, and closely align production with customer demand. These practices include:
Value Stream Mapping (VSM): This tool involves mapping out all the steps involved in the demand planning process, from raw material procurement to product delivery to the customer. By visualizing the entire process, companies can easily identify and eliminate steps that do not add value, thereby streamlining operations and focusing resources on activities that directly contribute to meeting customer demand.
Continuous Improvement (Kaizen): Lean demand planning is not a one-time initiative but an ongoing effort to improve efficiency and effectiveness. Kaizen, or continuous improvement, is a core principle of lean philosophy, encouraging companies to constantly seek ways to refine their demand planning processes. This could involve regular reviews of forecasting accuracy, inventory levels, and production schedules to identify areas for improvement.
Demand Segmentation: By segmenting demand based on characteristics such as product type, customer group, or sales channel, manufacturers can apply different forecasting and replenishment strategies tailored to each segment’s specific needs. This targeted approach allows for more accurate demand planning and can help to reduce inventory levels and increase service levels.
Synchronization of Supply Chain Activities: Lean demand planning requires tight coordination between all parts of the supply chain, from suppliers to manufacturers to distributors. By synchronizing activities such as material procurement, production scheduling, and product delivery, companies can ensure that each component of the supply chain is operating in harmony, reducing lead times and improving responsiveness to changes in demand.
Advanced Forecasting Techniques: Incorporating advanced forecasting techniques such as predictive analytics and machine learning can significantly improve the accuracy of demand forecasts. These technologies can analyze large volumes of data to identify patterns and predict future demand trends, allowing manufacturers to adjust their production plans proactively.
Pull-based Replenishment Systems: Implementing pull-based systems such as Kanban can help to align production more closely with actual demand. In a Kanban system, production is triggered by consumption, ensuring that inventory levels are kept to a minimum and that products are produced only when there is a real need.
How to leverage demand planning in procurement and supply chain management
In procurement and supply chain management, the following are key activities where the output from demand planning should be utilized:
Supplier Collaboration
Close collaboration with suppliers is essential to align procurement strategies with forecasted demand. Sharing demand forecasts with suppliers can help them prepare and ensure they have the capacity to meet your needs, leading to stronger relationships and more reliable supply chains. This can involve collaborative planning, forecasting, and replenishment (CPFR) initiatives, which enhance visibility and coordination between partners.
Inventory Optimization
Effective demand planning enables manufacturers to optimize their inventory levels, striking a balance between having enough stock to meet demand without holding excessive inventory that ties up capital. Techniques such as just-in-time (JIT) inventory management can be employed to reduce waste and improve cash flow. This approach relies on the timely procurement of materials in response to demand forecasts, minimizing stock levels while ensuring production continuity.
Flexible Supply Chain
Flexibility in the supply chain is crucial to respond to fluctuations in demand. By understanding demand patterns, manufacturers can develop contingency plans, such as identifying alternative suppliers or diversifying procurement sources. This agility allows companies to adapt to unexpected changes in demand or supply disruptions quickly.
Challenges and Strategies in Demand Planning
Executing demand planning in the manufacturing industries involves navigating a complex landscape of challenges that can significantly impact the efficiency and effectiveness of supply chain operations.
One of the primary challenges is the accuracy of demand forecasts. Forecasting errors can lead to either overproduction, resulting in excess inventory costs, or underproduction, leading to stockouts and lost sales. The variability and unpredictability of market demand, influenced by factors such as economic shifts, consumer preferences, and geopolitical events, make accurate forecasting exceedingly difficult.
Another major challenge is the integration of demand planning with other business processes. Many manufacturing companies struggle with siloed departments where information and data are not shared effectively across the organization. This lack of integration can hinder the alignment of demand planning with production scheduling, procurement, and inventory management, leading to inefficiencies and increased operational costs.
Data quality and management also pose significant challenges. Demand planning requires high-quality, timely, and relevant data to be effective. However, collecting, processing, and analyzing large volumes of data from various sources can be daunting. Data inconsistencies, inaccuracies, and the absence of a unified data management strategy can compromise the integrity of demand forecasts.
Enhancing Demand Planning with CADDi Drawer
CADDi Drawer not only facilitates more accurate demand forecasting but also provides the means to execute on these forecasts with precision. Its integrated platform allows for seamless communication between procurement, production, and sales departments, ensuring that each segment of the supply chain is aligned with the overall demand planning strategy.
Streamline activities in the planning process
The following features enable you to streamline the time-consuming tasks of data collection and organization in procurement operations.
- Price data, quantity data, customer information and supplier information can be automatically linked to each drawing and can also be exported together.
- By using keyword searches combined with similarity searches, the time spent searching for drawings and data in planning tasks can be reduced.
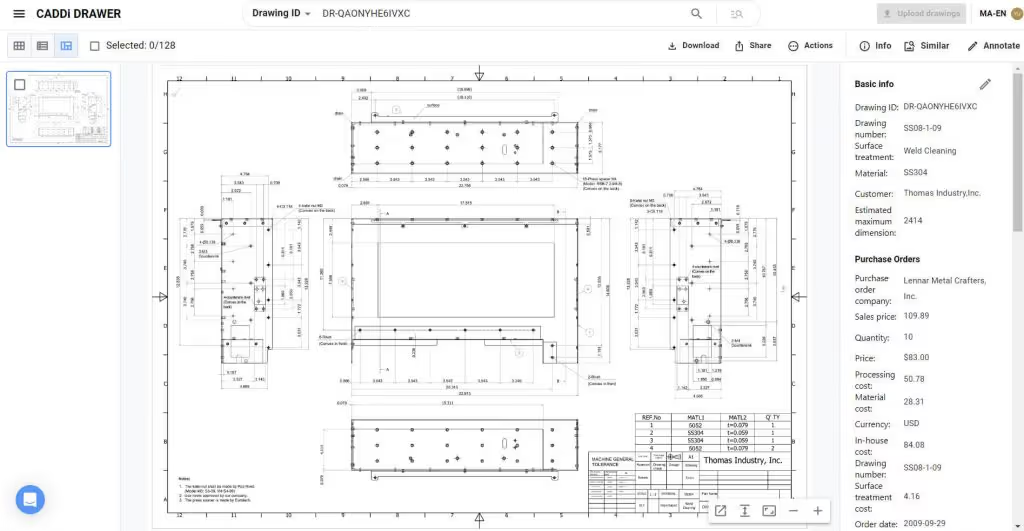
Linking demand forecasting and procurement activities
By using CADDi Drawer to link various demand-side data, such as drawings and purchase data, as the basis for forecasts, it is possible to reverse-engineer from the created demand forecasts to predict necessary procurement volumes and facilitate supplier selection.
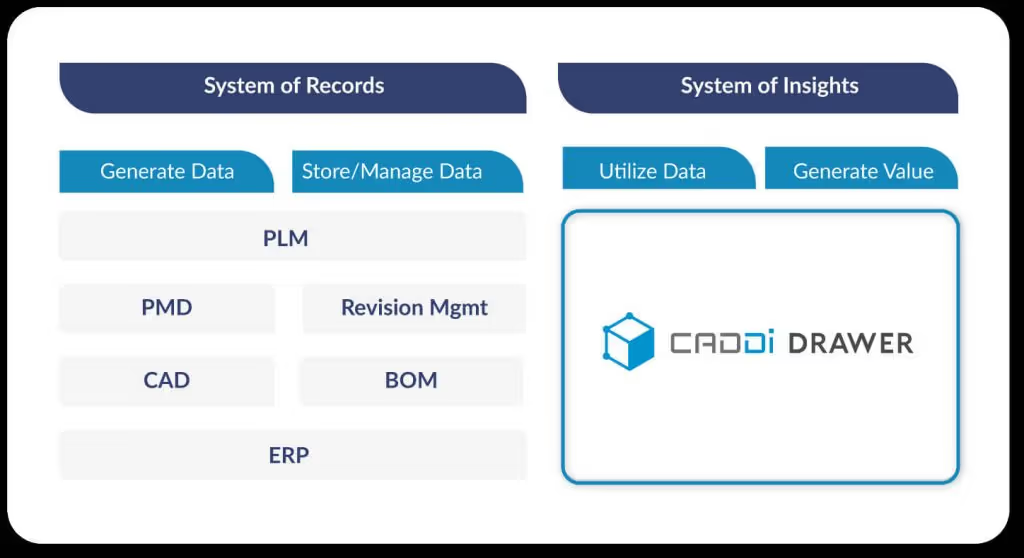
Imagine the scenario: a leading electronics manufacturer, facing the annual surge in demand ahead of the holiday season, leverages advanced demand planning techniques to align its production schedules precisely with market expectations. By meticulously analyzing past sales data, current market trends, and future forecasts, the company not only meets the spike in consumer demand but does so without accruing excess inventory, thus optimizing its profitability.
This tale is not unique but a testament to the transformative power of effective demand planning in the manufacturing landscape. It underscores the process’s role as a linchpin in the supply chain, ensuring products are delivered reliably and customer satisfaction remains high.
Key Approaches in Demand Planning
Demand planning is the strategic process that underpins supply chain management, ensuring that manufacturing aligns seamlessly with market demand. It’s a multifaceted discipline that encompasses sales forecasting, inventory management, and comprehensive supply chain oversight. Effective demand planning facilitates accurate revenue forecasts, optimizes inventory levels to match demand fluctuations, and enhances overall profitability for specific channels or products.
The essence of demand planning lies in its processes, which are critical for forecasting demand accurately.
These include trade promotion management (TPM), which involves marketing tactics like discounts and in-store promotions to generate demand. By collaborating at detailed and aggregated levels, companies can swiftly adjust their products, campaigns, and promotions, ensuring they remain aligned with distributor and customer signals across all timeframes.
Another crucial aspect is sales and operations planning (S&OP). This cross-functional process brings together all relevant departments, including sales, marketing, production, and finance, to ensure that the demand forecast aligns with production capacity and financial objectives. S&OP meetings facilitate consensus on a single demand plan, which serves as the foundation for operational planning and resource allocation, helping to balance supply and demand effectively.
Collaborative planning, forecasting, and replenishment (CPFR) further enhances demand planning by fostering collaboration between suppliers, manufacturers, and retailers. By sharing information and forecasts, all parties can work together to improve the accuracy of demand predictions, optimize inventory levels, and reduce costs. This collaborative approach not only strengthens supply chain partnerships but also ensures that the end-to-end supply chain is more responsive to consumer needs.
Technology plays a pivotal role in streamlining demand planning processes. Advanced planning and scheduling (APS) systems integrate data from various sources, providing a comprehensive view of demand, inventory, production capacity, and supply chain constraints. These systems use sophisticated algorithms to generate optimal production plans that meet demand while minimizing costs and maximizing resource utilization.
Demand Planning Models
Diving deeper into the world of demand planning, we encounter various models that businesses employ to forecast future demand accurately.
Econometric models, for instance, consider both dependent and independent variables, analyzing the intricate web of cause and effect that influences demand. A famous case is that of a multinational technology company which, by employing econometric models, was able to anticipate market shifts with a remarkable 85% accuracy rate, significantly improving its supply chain efficiency.
Trend projection models, another pillar of demand planning, rely on historical data to forecast future demand. By identifying patterns and controlling for anomalies, companies can prepare for predictable fluctuations in demand. A retail giant exemplified the power of trend projection by adjusting its inventory levels ahead of peak shopping seasons, resulting in a 20% improvement in customer satisfaction due to reduced stockouts.
Barometric models, which take into account economic indicators like inflation rates and consumer spending trends, have proven essential for industries sensitive to economic cycles. A leading automobile manufacturer used these models to adjust production in anticipation of an economic downturn, effectively avoiding overproduction and aligning inventory with reduced consumer spending, thus maintaining profitability during challenging times.
If you are in charge of procurement for a manufacturer of industrial machines or plant equipment, that is, products that are high-mix low-volume (HMLV), you might think that the above models are difficult to directly apply because they are designed for mass production. That is indeed the case.
Of course, don’t forget to utilize the essence of the above models, but in addition, approaches like the following can be applicable.
For HMLV manufacturers, building strong relationships with key customers and engaging in collaborative forecasting can significantly enhance demand planning accuracy. This practice involves sharing data and insights between the manufacturer and its customers to jointly develop more accurate forecasts. Given the customized nature of many HMLV products, understanding customer plans and expectations can lead to better-aligned production schedules and improved customer satisfaction.
Lean Demand Planning and Its Benefits
Lean demand planning emphasizes efficiency and waste reduction throughout the supply chain. By identifying and eliminating non-value-added steps, companies can significantly enhance their operational efficiency. For example, a consumer electronics company implemented lean principles in its demand planning process, automating data entry and report generation.
In the manufacturing industry, lean demand planning goes beyond just automating processes and adopting a pull-based approach; it incorporates a set of specific methods and practices designed to streamline operations, minimize waste, and closely align production with customer demand. These practices include:
Value Stream Mapping (VSM): This tool involves mapping out all the steps involved in the demand planning process, from raw material procurement to product delivery to the customer. By visualizing the entire process, companies can easily identify and eliminate steps that do not add value, thereby streamlining operations and focusing resources on activities that directly contribute to meeting customer demand.
Continuous Improvement (Kaizen): Lean demand planning is not a one-time initiative but an ongoing effort to improve efficiency and effectiveness. Kaizen, or continuous improvement, is a core principle of lean philosophy, encouraging companies to constantly seek ways to refine their demand planning processes. This could involve regular reviews of forecasting accuracy, inventory levels, and production schedules to identify areas for improvement.
Demand Segmentation: By segmenting demand based on characteristics such as product type, customer group, or sales channel, manufacturers can apply different forecasting and replenishment strategies tailored to each segment’s specific needs. This targeted approach allows for more accurate demand planning and can help to reduce inventory levels and increase service levels.
Synchronization of Supply Chain Activities: Lean demand planning requires tight coordination between all parts of the supply chain, from suppliers to manufacturers to distributors. By synchronizing activities such as material procurement, production scheduling, and product delivery, companies can ensure that each component of the supply chain is operating in harmony, reducing lead times and improving responsiveness to changes in demand.
Advanced Forecasting Techniques: Incorporating advanced forecasting techniques such as predictive analytics and machine learning can significantly improve the accuracy of demand forecasts. These technologies can analyze large volumes of data to identify patterns and predict future demand trends, allowing manufacturers to adjust their production plans proactively.
Pull-based Replenishment Systems: Implementing pull-based systems such as Kanban can help to align production more closely with actual demand. In a Kanban system, production is triggered by consumption, ensuring that inventory levels are kept to a minimum and that products are produced only when there is a real need.
How to leverage demand planning in procurement and supply chain management
In procurement and supply chain management, the following are key activities where the output from demand planning should be utilized:
Supplier Collaboration
Close collaboration with suppliers is essential to align procurement strategies with forecasted demand. Sharing demand forecasts with suppliers can help them prepare and ensure they have the capacity to meet your needs, leading to stronger relationships and more reliable supply chains. This can involve collaborative planning, forecasting, and replenishment (CPFR) initiatives, which enhance visibility and coordination between partners.
Inventory Optimization
Effective demand planning enables manufacturers to optimize their inventory levels, striking a balance between having enough stock to meet demand without holding excessive inventory that ties up capital. Techniques such as just-in-time (JIT) inventory management can be employed to reduce waste and improve cash flow. This approach relies on the timely procurement of materials in response to demand forecasts, minimizing stock levels while ensuring production continuity.
Flexible Supply Chain
Flexibility in the supply chain is crucial to respond to fluctuations in demand. By understanding demand patterns, manufacturers can develop contingency plans, such as identifying alternative suppliers or diversifying procurement sources. This agility allows companies to adapt to unexpected changes in demand or supply disruptions quickly.
Challenges and Strategies in Demand Planning
Executing demand planning in the manufacturing industries involves navigating a complex landscape of challenges that can significantly impact the efficiency and effectiveness of supply chain operations.
One of the primary challenges is the accuracy of demand forecasts. Forecasting errors can lead to either overproduction, resulting in excess inventory costs, or underproduction, leading to stockouts and lost sales. The variability and unpredictability of market demand, influenced by factors such as economic shifts, consumer preferences, and geopolitical events, make accurate forecasting exceedingly difficult.
Another major challenge is the integration of demand planning with other business processes. Many manufacturing companies struggle with siloed departments where information and data are not shared effectively across the organization. This lack of integration can hinder the alignment of demand planning with production scheduling, procurement, and inventory management, leading to inefficiencies and increased operational costs.
Data quality and management also pose significant challenges. Demand planning requires high-quality, timely, and relevant data to be effective. However, collecting, processing, and analyzing large volumes of data from various sources can be daunting. Data inconsistencies, inaccuracies, and the absence of a unified data management strategy can compromise the integrity of demand forecasts.
Enhancing Demand Planning with CADDi Drawer
CADDi Drawer not only facilitates more accurate demand forecasting but also provides the means to execute on these forecasts with precision. Its integrated platform allows for seamless communication between procurement, production, and sales departments, ensuring that each segment of the supply chain is aligned with the overall demand planning strategy.
Streamline activities in the planning process
The following features enable you to streamline the time-consuming tasks of data collection and organization in procurement operations.
- Price data, quantity data, customer information and supplier information can be automatically linked to each drawing and can also be exported together.
- By using keyword searches combined with similarity searches, the time spent searching for drawings and data in planning tasks can be reduced.
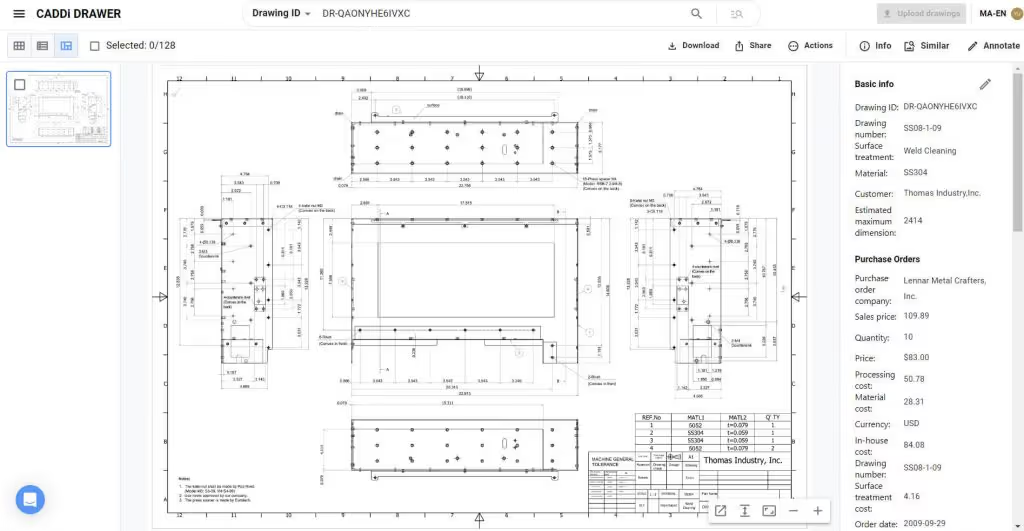
Linking demand forecasting and procurement activities
By using CADDi Drawer to link various demand-side data, such as drawings and purchase data, as the basis for forecasts, it is possible to reverse-engineer from the created demand forecasts to predict necessary procurement volumes and facilitate supplier selection.
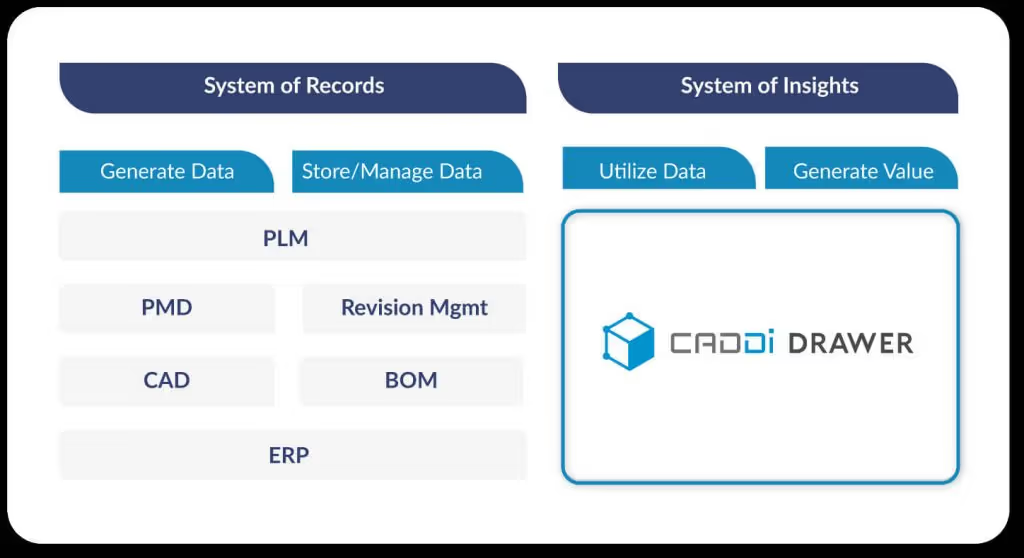
Ready to see CADDi Drawer in action? Get a personalized demo.
Subscribe to our Blog!
Related Resources


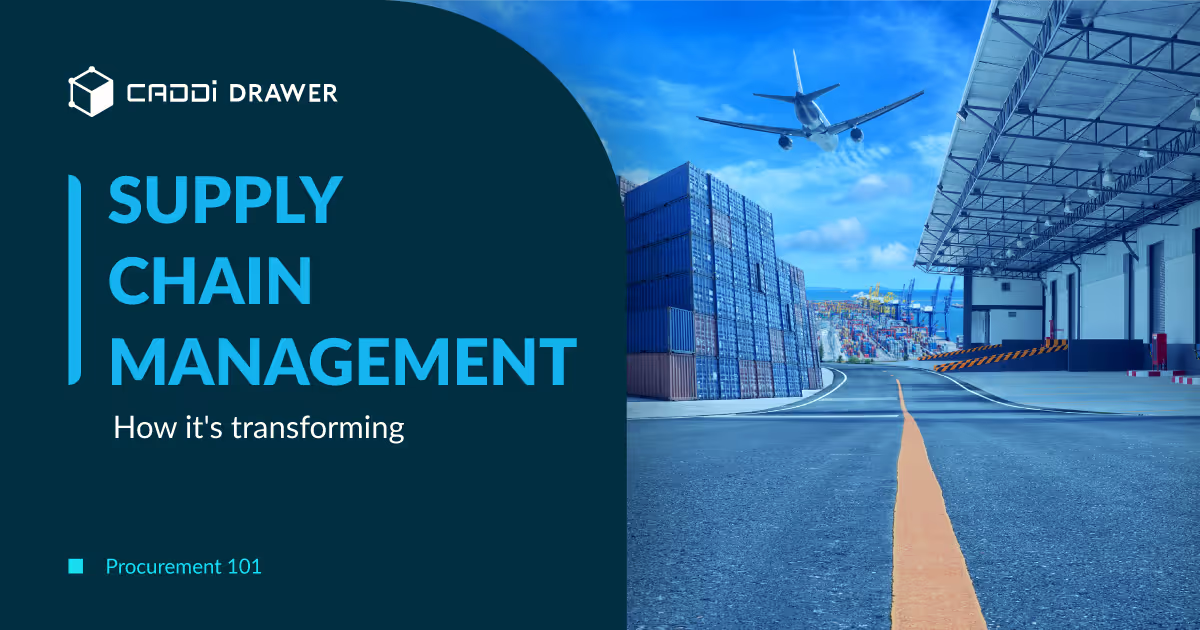
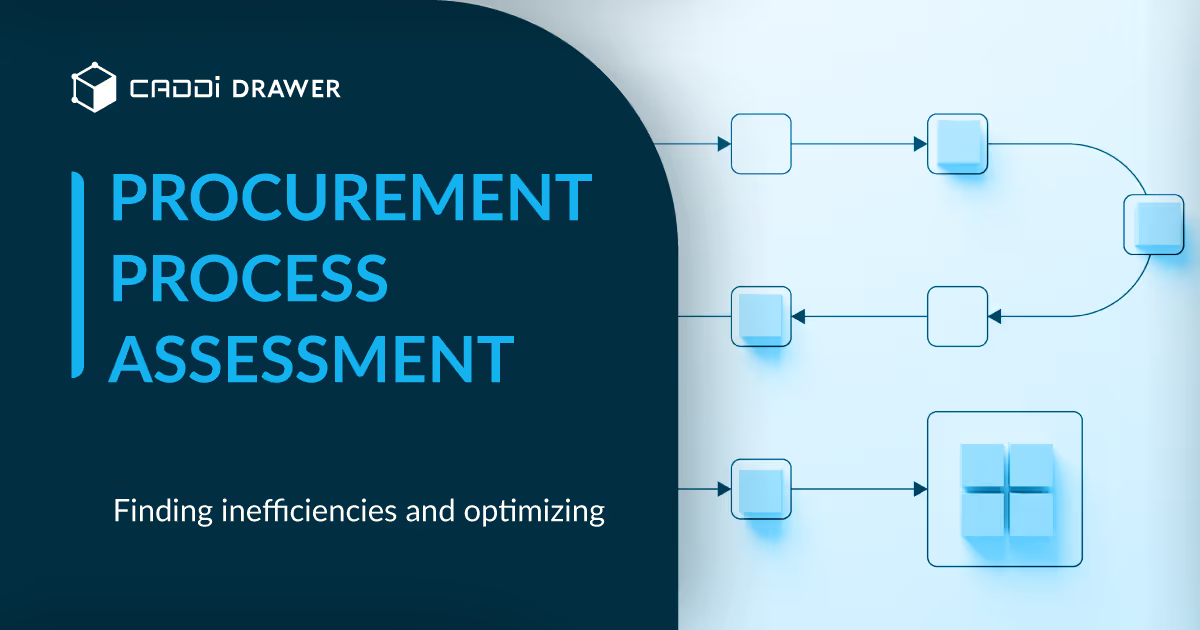
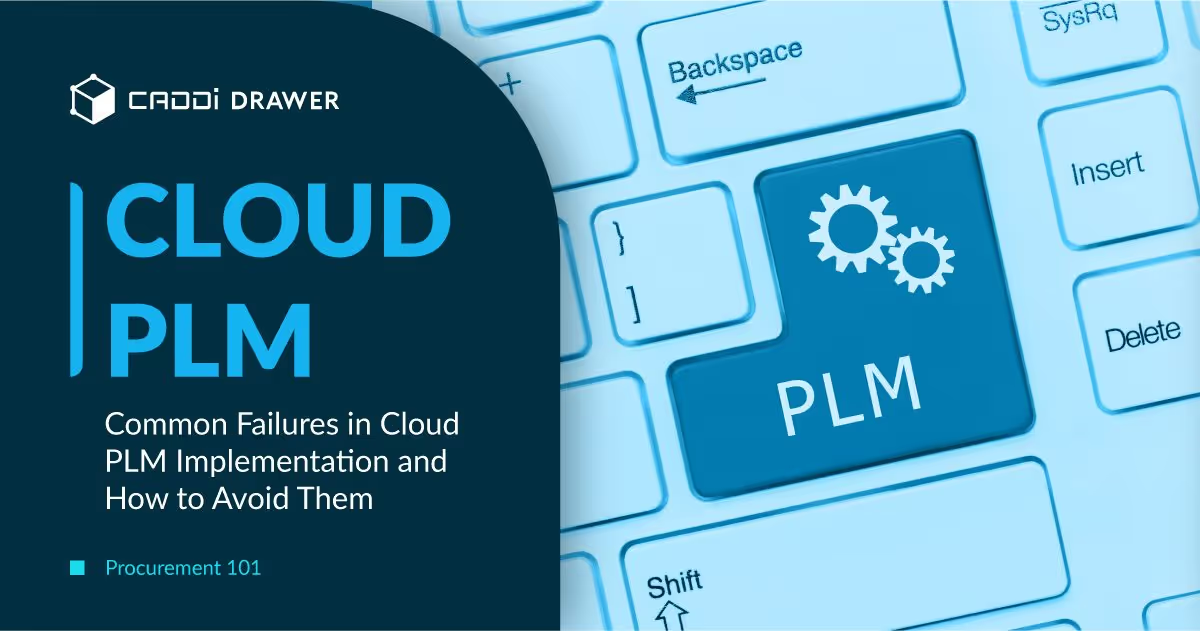
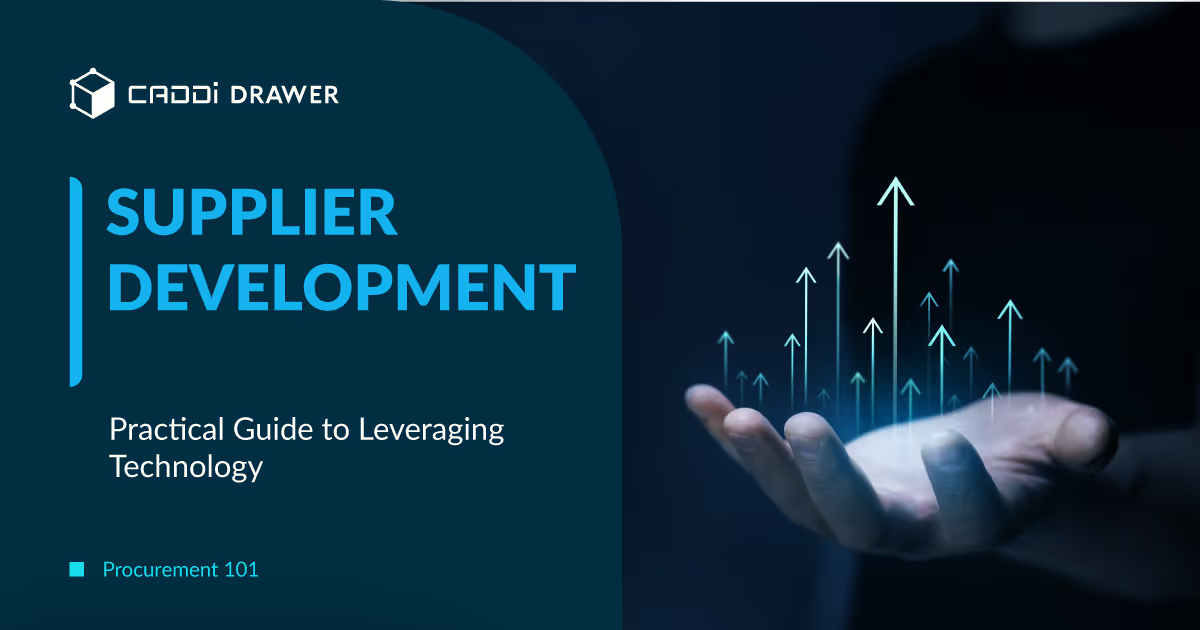