Engineering 101: Front-Loading in Product Design: A Game-Changer for Manufacturing Efficiency
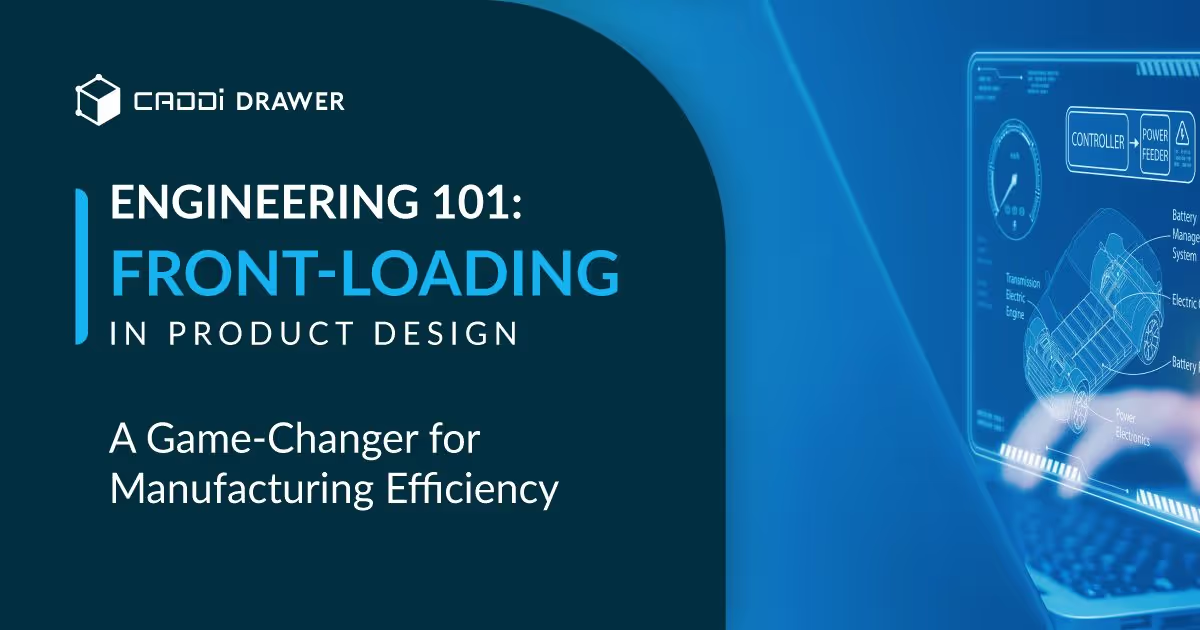
Table of Contents
Among the many strategies that promise to revolutionize product development processes, front-loading stands out as a particularly strong approach. This method, which prioritizes critical decision-making and problem-solving at the earliest stages of product design, offers a pathway to significant improvements in manufacturing outcomes.
According to research, it is said that over 70% of a product’s development costs are determined during the design phase. From this perspective, the importance of front-loading is undeniable.
The Essence of Front-Loading in Product Design
Front-loading is a strategic approach in product design and development that focuses on addressing and resolving key issues at the beginning of the product development cycle. This proactive stance is designed to anticipate and mitigate potential challenges that could arise later on, thereby streamlining the entire manufacturing process. But what makes front-loading so impactful?
- Early Problem Identification: By concentrating on identifying potential design and manufacturing issues at the outset, companies can avoid costly and time-consuming revisions down the line.
- Enhanced Collaboration: Front-loading encourages early collaboration among designers, engineers, and manufacturing teams, fostering a holistic view of the product development process.
- Risk Mitigation: With early risk identification and mitigation, manufacturers can reduce the likelihood of project overruns, ensuring projects stay on schedule and within budget.
Unpacking the Benefits
The adoption of front-loading in product design can translate into tangible benefits for manufacturers. Here are several key advantages:
- Improved Product Quality: Early detection and resolution of design flaws lead to superior product quality, enhancing customer satisfaction and competitive edge.
- Cost Efficiency: By minimizing the need for late-stage changes, front-loading significantly reduces overall development and production costs.
- Faster Time-to-Market: Streamlining the design and development process accelerates the product’s journey from concept to market, a crucial factor in today’s fast-paced competitive landscapes.
Front-Loading and the Influence Curve
The influence curve illustrates the relationship between the stage of the product development process and the ability to influence the cost and outcome of a product. At the initial stages of design and development, the potential to impact product cost and performance is at its highest. As the process advances, the ability to effect change diminishes, leading to increased costs and complexity for any modifications made later in the cycle, as additional design elements are impacted.
This curve underscores the importance of front-loading in the design process, where critical decisions and analyses are conducted early on to capitalize on the high-influence, low-cost window of opportunity.
The Dangers of Neglecting Front-Loading
Failing to implement front-loading in product design can lead to significant challenges and costs, particularly as a project progresses. This negligence reflects poorly on the influence curve, compounding critical issues that can emerge. Key dangers include:
- Escalating Costs: Making changes to a product’s design in the later stages of development can be exponentially more expensive than addressing these issues early on. The cost of alterations rises dramatically as the project moves closer to production and launch.
- Extended Timelines: Modifications in the later phases can lead to delays in product development, affecting time-to-market and potentially missing critical market opportunities.
- Compromised Quality: Late-stage changes can also lead to compromises in product quality, as the rush to address issues can result in less than optimal solutions.
This scenario underscores the critical importance of front-loading. By allocating resources and attention to the early stages of product design, manufacturers can significantly mitigate risks, control costs, and improve overall outcomes.
Implementing Front-Loading in Your Product Design Process
Incorporating front-loading into the product design process requires a methodical approach. Here are steps to get started:
- Foster Cross-Functional Collaboration: Encourage open communication and collaboration between design, engineering, and manufacturing teams from the project’s inception. Utilize processes to continually share data between departments, strengthening the knowledge base of all departments.
- Invest in Early Stage Analysis Tools: Utilize simulation and prototyping tools to assess and optimize designs before finalizing specifications. By reducing the amount of physical prototypes created, overall costs and prototyping lead time can be controlled much more strictly.
- Leverage past data: Utilizing data from previous designs and processes can reduce the time to make optimal design decisions, and easily accessible nonconformance data from the Quality department will reduce downstream quality issues.
- Train for a Front-Loading Mindset: Equip your team with the skills and knowledge to effectively implement front-loading strategies, emphasizing the importance of early problem-solving and decision-making.
Front-loading in product design offers a powerful strategy for manufacturers aiming to enhance efficiency, reduce costs, and improve product quality. By addressing key issues early in the design process, companies can streamline their manufacturing operations, achieving faster time-to-market and a stronger competitive position. As the manufacturing landscape continues to evolve, embracing innovative approaches like front-loading will be crucial for those looking to stay ahead in the game.
How CADDi Drawer can help the implementation of front-loading
CADDi Drawer stands as a pivotal innovation in the manufacturing sector, particularly enhancing the implementation of front-loading in the design process. It aids this process significantly by centralizing and streamlining access to drawing data, which is a cornerstone of the design process. It facilitates improved front-loading through its advanced AI-enabled search platform. This platform allows for the centralization of drawings in a single, accessible location, regardless of their format.
The proprietary image-analysis algorithms enable high-precision similarity searches among the most crucial digital assets in manufacturing—drawings. This not only aids in the reduction of design and production costs but also significantly speeds up the design process by making it easier to find and use existing drawings and data. The efficiency in accessing and analyzing drawing data early in the design process ensures that potential issues can be identified and addressed sooner, reducing the need for costly revisions later on.

Front Loading with CADDi Drawer: A Case Study
A rubber product manufacturer found CADDi Drawer during a difficult period; while they maintained records for defects and created in-depth specification sheets, they still found non-conformances within their products. They had the data available to reduce these defects, but employees struggled to locate and use them proactively, and they spent numerous hours in the inspection process to manually confirm non-conformance.
Additionally, during the design review process issues were raised, but they were not often implemented because the employees expressed difficulty in incorporating past knowledge into new designs.
Implementing CADDi Drawer revolutionized this company’s reporting process. Instead of storing this data within separate folders and relying on more experienced employees’ past experiences, CADDi Drawer was able to link over 90,000 documents directly to their drawings.
By doing so, this information became available to all members of the team, regardless of their skill level. During the design process a workflow was put in place for members to search their Drawer database for similar parts, in order to reduce the amount of repeated parts designed.
Additionally, historical data is referenced in the initial design phase for every product in order to consider past defects and leverage past production information, increasing machine productivity.
By instituting CADDi Drawer within manufacturing workflows, employees are empowered through access to decades of manufacturing intelligence. With this data at their fingertips, employees can much more proactively consider front-loading design improvements at the outset of projects, minimizing cost and improving their competitiveness.
Among the many strategies that promise to revolutionize product development processes, front-loading stands out as a particularly strong approach. This method, which prioritizes critical decision-making and problem-solving at the earliest stages of product design, offers a pathway to significant improvements in manufacturing outcomes.
According to research, it is said that over 70% of a product’s development costs are determined during the design phase. From this perspective, the importance of front-loading is undeniable.
The Essence of Front-Loading in Product Design
Front-loading is a strategic approach in product design and development that focuses on addressing and resolving key issues at the beginning of the product development cycle. This proactive stance is designed to anticipate and mitigate potential challenges that could arise later on, thereby streamlining the entire manufacturing process. But what makes front-loading so impactful?
- Early Problem Identification: By concentrating on identifying potential design and manufacturing issues at the outset, companies can avoid costly and time-consuming revisions down the line.
- Enhanced Collaboration: Front-loading encourages early collaboration among designers, engineers, and manufacturing teams, fostering a holistic view of the product development process.
- Risk Mitigation: With early risk identification and mitigation, manufacturers can reduce the likelihood of project overruns, ensuring projects stay on schedule and within budget.
Unpacking the Benefits
The adoption of front-loading in product design can translate into tangible benefits for manufacturers. Here are several key advantages:
- Improved Product Quality: Early detection and resolution of design flaws lead to superior product quality, enhancing customer satisfaction and competitive edge.
- Cost Efficiency: By minimizing the need for late-stage changes, front-loading significantly reduces overall development and production costs.
- Faster Time-to-Market: Streamlining the design and development process accelerates the product’s journey from concept to market, a crucial factor in today’s fast-paced competitive landscapes.
Front-Loading and the Influence Curve
The influence curve illustrates the relationship between the stage of the product development process and the ability to influence the cost and outcome of a product. At the initial stages of design and development, the potential to impact product cost and performance is at its highest. As the process advances, the ability to effect change diminishes, leading to increased costs and complexity for any modifications made later in the cycle, as additional design elements are impacted.
This curve underscores the importance of front-loading in the design process, where critical decisions and analyses are conducted early on to capitalize on the high-influence, low-cost window of opportunity.
The Dangers of Neglecting Front-Loading
Failing to implement front-loading in product design can lead to significant challenges and costs, particularly as a project progresses. This negligence reflects poorly on the influence curve, compounding critical issues that can emerge. Key dangers include:
- Escalating Costs: Making changes to a product’s design in the later stages of development can be exponentially more expensive than addressing these issues early on. The cost of alterations rises dramatically as the project moves closer to production and launch.
- Extended Timelines: Modifications in the later phases can lead to delays in product development, affecting time-to-market and potentially missing critical market opportunities.
- Compromised Quality: Late-stage changes can also lead to compromises in product quality, as the rush to address issues can result in less than optimal solutions.
This scenario underscores the critical importance of front-loading. By allocating resources and attention to the early stages of product design, manufacturers can significantly mitigate risks, control costs, and improve overall outcomes.
Implementing Front-Loading in Your Product Design Process
Incorporating front-loading into the product design process requires a methodical approach. Here are steps to get started:
- Foster Cross-Functional Collaboration: Encourage open communication and collaboration between design, engineering, and manufacturing teams from the project’s inception. Utilize processes to continually share data between departments, strengthening the knowledge base of all departments.
- Invest in Early Stage Analysis Tools: Utilize simulation and prototyping tools to assess and optimize designs before finalizing specifications. By reducing the amount of physical prototypes created, overall costs and prototyping lead time can be controlled much more strictly.
- Leverage past data: Utilizing data from previous designs and processes can reduce the time to make optimal design decisions, and easily accessible nonconformance data from the Quality department will reduce downstream quality issues.
- Train for a Front-Loading Mindset: Equip your team with the skills and knowledge to effectively implement front-loading strategies, emphasizing the importance of early problem-solving and decision-making.
Front-loading in product design offers a powerful strategy for manufacturers aiming to enhance efficiency, reduce costs, and improve product quality. By addressing key issues early in the design process, companies can streamline their manufacturing operations, achieving faster time-to-market and a stronger competitive position. As the manufacturing landscape continues to evolve, embracing innovative approaches like front-loading will be crucial for those looking to stay ahead in the game.
How CADDi Drawer can help the implementation of front-loading
CADDi Drawer stands as a pivotal innovation in the manufacturing sector, particularly enhancing the implementation of front-loading in the design process. It aids this process significantly by centralizing and streamlining access to drawing data, which is a cornerstone of the design process. It facilitates improved front-loading through its advanced AI-enabled search platform. This platform allows for the centralization of drawings in a single, accessible location, regardless of their format.
The proprietary image-analysis algorithms enable high-precision similarity searches among the most crucial digital assets in manufacturing—drawings. This not only aids in the reduction of design and production costs but also significantly speeds up the design process by making it easier to find and use existing drawings and data. The efficiency in accessing and analyzing drawing data early in the design process ensures that potential issues can be identified and addressed sooner, reducing the need for costly revisions later on.

Front Loading with CADDi Drawer: A Case Study
A rubber product manufacturer found CADDi Drawer during a difficult period; while they maintained records for defects and created in-depth specification sheets, they still found non-conformances within their products. They had the data available to reduce these defects, but employees struggled to locate and use them proactively, and they spent numerous hours in the inspection process to manually confirm non-conformance.
Additionally, during the design review process issues were raised, but they were not often implemented because the employees expressed difficulty in incorporating past knowledge into new designs.
Implementing CADDi Drawer revolutionized this company’s reporting process. Instead of storing this data within separate folders and relying on more experienced employees’ past experiences, CADDi Drawer was able to link over 90,000 documents directly to their drawings.
By doing so, this information became available to all members of the team, regardless of their skill level. During the design process a workflow was put in place for members to search their Drawer database for similar parts, in order to reduce the amount of repeated parts designed.
Additionally, historical data is referenced in the initial design phase for every product in order to consider past defects and leverage past production information, increasing machine productivity.
By instituting CADDi Drawer within manufacturing workflows, employees are empowered through access to decades of manufacturing intelligence. With this data at their fingertips, employees can much more proactively consider front-loading design improvements at the outset of projects, minimizing cost and improving their competitiveness.
Ready to see CADDi Drawer in action? Get a personalized demo.
Subscribe to our Blog!
Related Resources
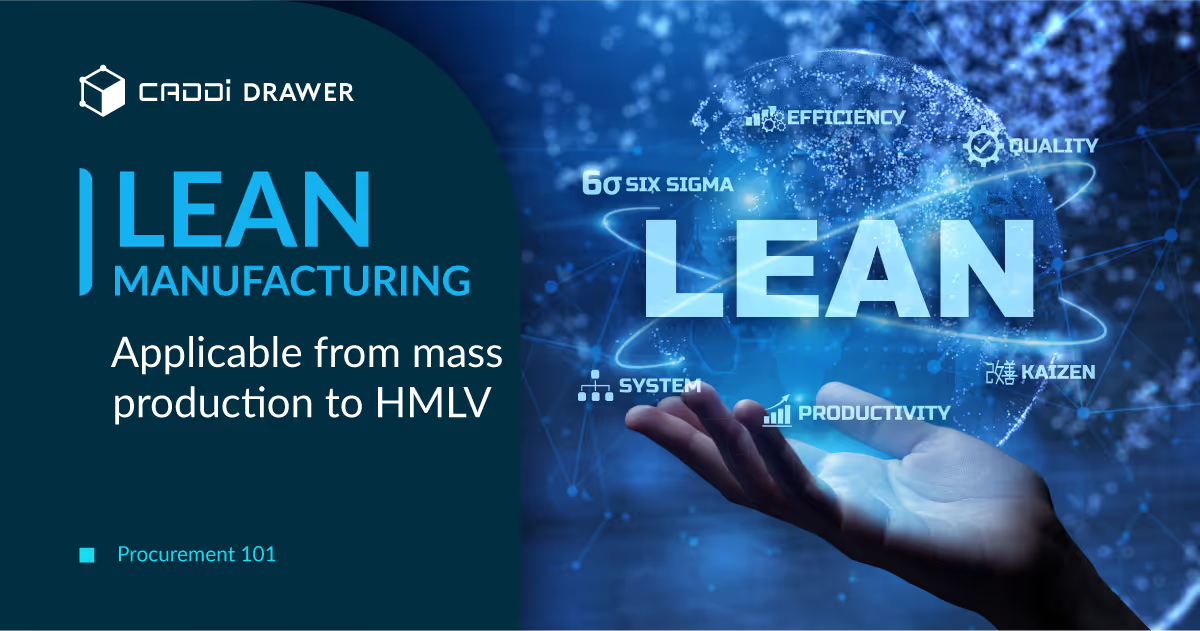

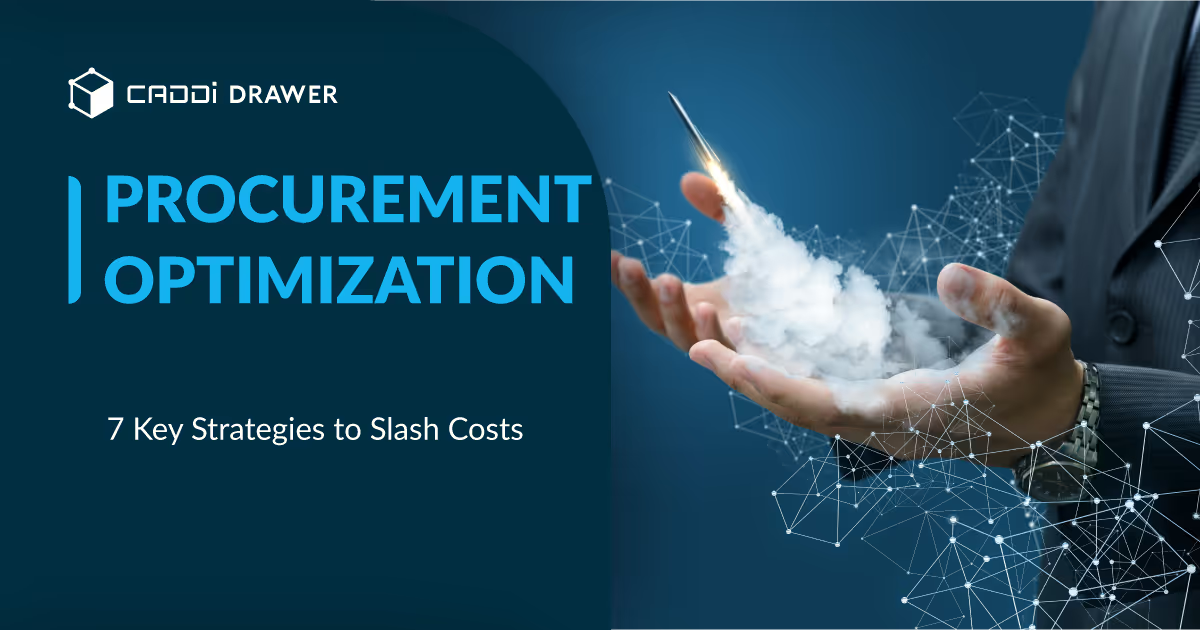
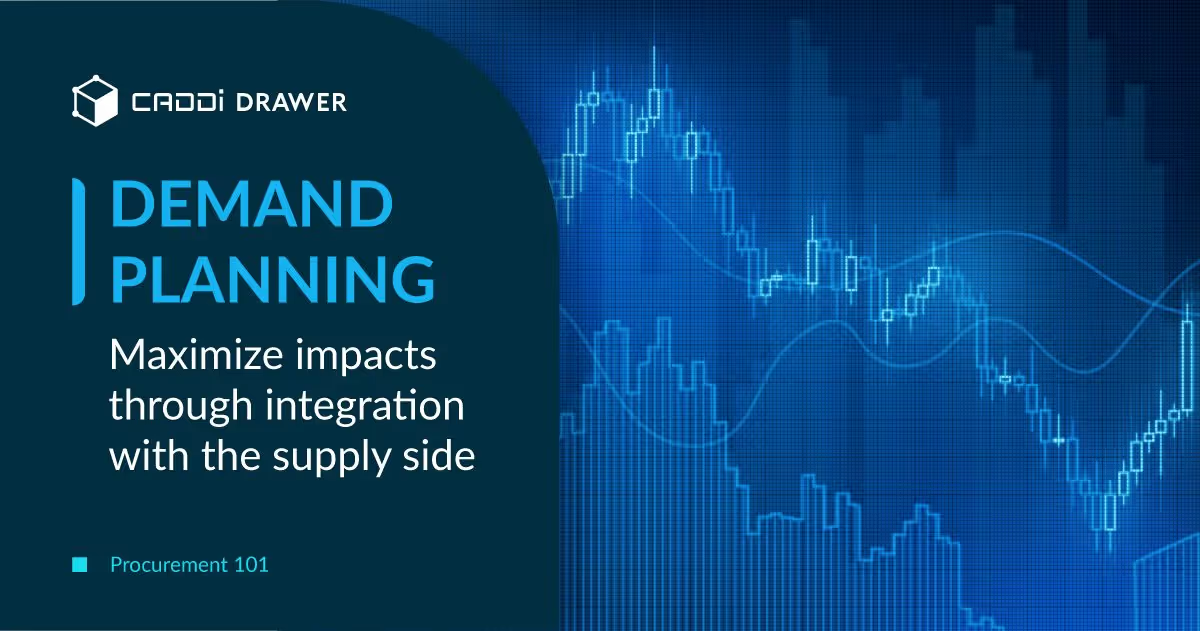
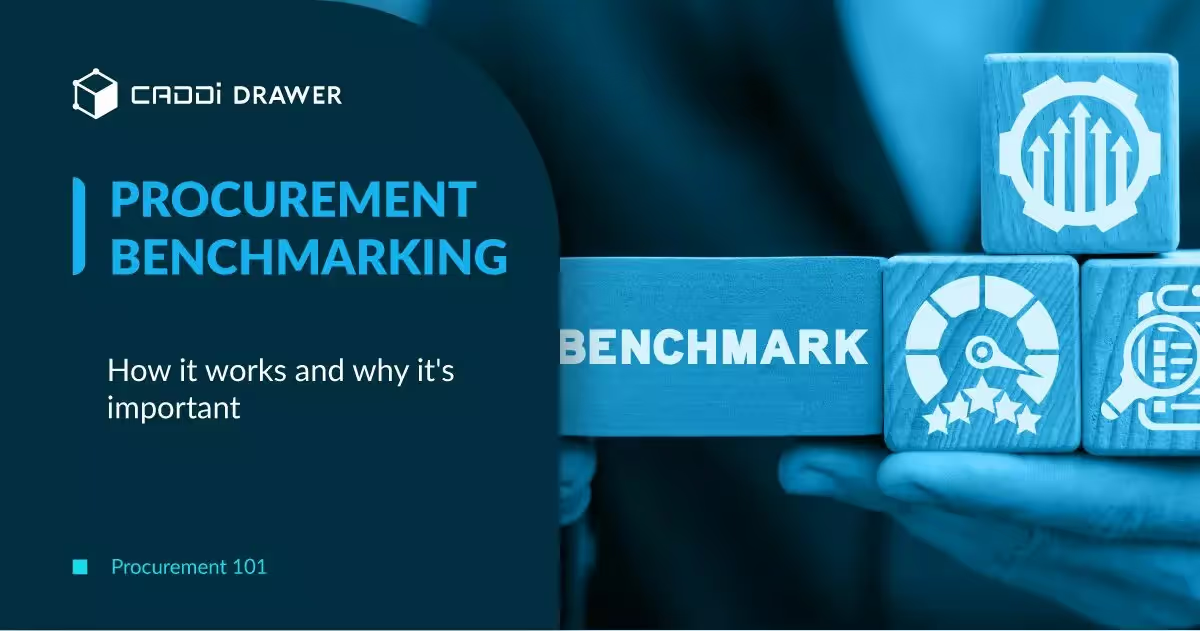
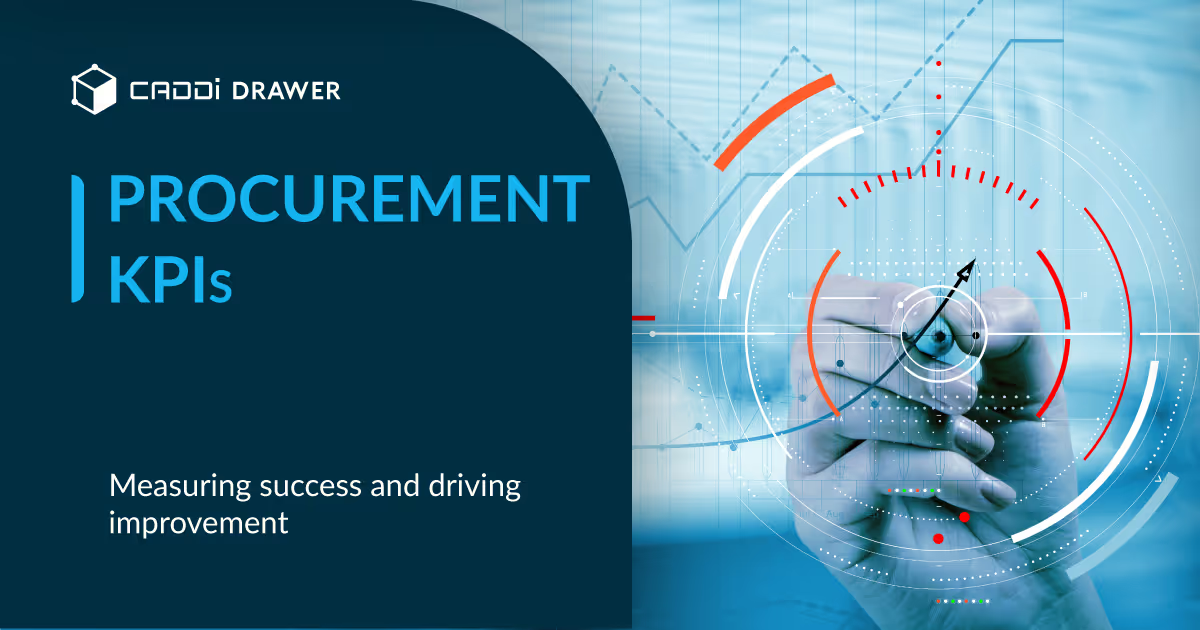