Inventory Optimization – Synergy between systems and operations – Procurement 101
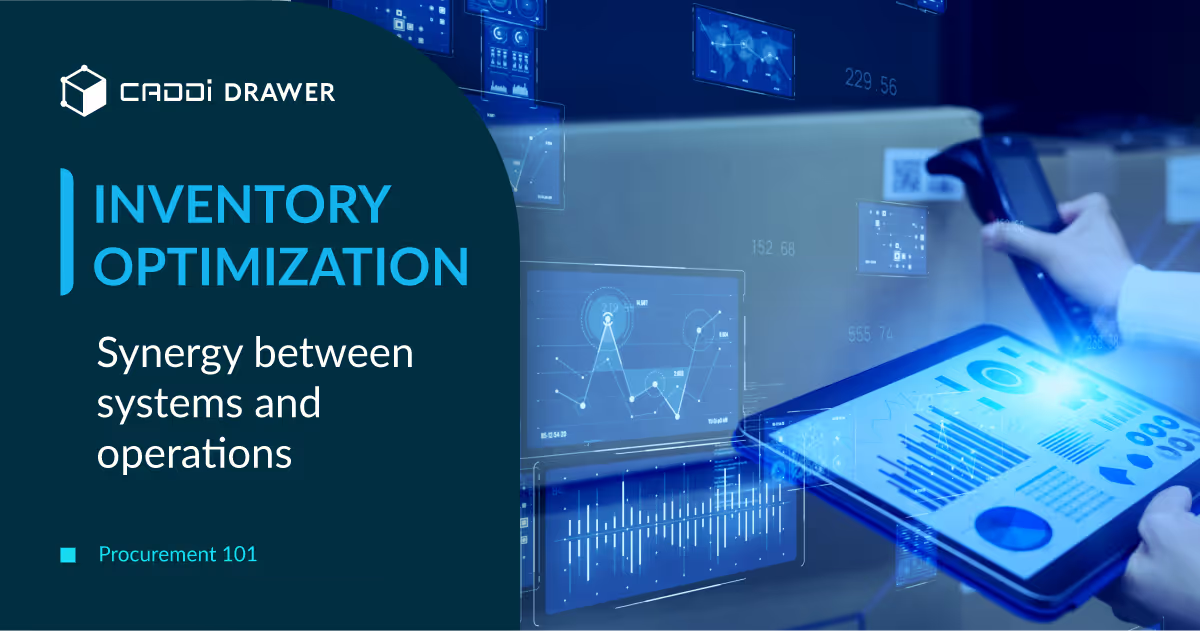
Table of Contents
Inventory optimization is a strategic maneuver aimed at creating the perfect balance between inventory levels and customer demand. It ensures that products are available when needed without tying up unnecessary capital in excess stock.
As you can easily imagine, the goal here is not simply to optimize inventory levels temporarily. Instead, it is to continue optimizing inventory levels under a sustainable system. Below, we would like to explain the key elements and solutions that should be considered for this purpose.
Key Techniques in Inventory Optimization
Demand Planning (Demand forecasting)
Accurate demand planning is critical in the manufacturing industry to ensure that the right amount of products is produced to meet customer demands without leading to overproduction or stockouts. Techniques such as statistical analysis, machine learning models, and historical data analysis are used to predict future demand accurately.
Just-In-Time (JIT) Inventory Management
JIT is a strategy that reduces inventory holding costs by receiving goods only as they are needed in the production process. This requires close collaboration with suppliers and precise demand forecasting to ensure that materials arrive just in time for manufacturing. It reduces the need for large inventories.
Safety Stock Management
Despite the best efforts to forecast demand and supply accurately, variability and uncertainties exist. Safety stock acts as a buffer against this unpredictability. It ensures that production can continue even in the face of delays or higher than expected demand. The key is to calculate the optimal level of safety stock that minimizes risk without tying up excessive capital.
ABC Analysis
This technique involves categorizing inventory into three categories (A, B, and C). Categorize them based on their importance or value to the company. ‘A’ items are the most valuable and require close monitoring and management. ‘B’ items are of moderate value, and ‘C’ items are the least valuable. This allows manufacturers to prioritize their inventory management efforts and resources effectively.
Lean Manufacturing
Lean manufacturing principles focus on eliminating waste throughout the production process, including excess inventory. Techniques such as value stream mapping and continuous improvement processes are used to identify and eliminate non-value-added activities and inventory. This improves efficiency and reduces costs.
Supplier Relationship Management
Developing strong relationships with suppliers based on effective supplier management approaches is key to effective inventory optimization. This can involve negotiating better terms, improving communication and collaboration, and integrating systems for more efficient inventory management and replenishment.
Inventory Turnover Ratio Analysis
Monitoring the inventory turnover ratio helps manufacturers understand how quickly inventory is being used or sold over a certain period. A higher turnover ratio indicates efficient inventory management, while a lower ratio may suggest overstocking or inefficiencies.
Economic Order Quantity (EOQ) Model
The EOQ model is used to determine the optimal order quantity that minimizes the total cost of inventory. This includes ordering, holding, and shortage costs. This calculation helps in making informed purchasing decisions.
Implementing these techniques requires a comprehensive approach that includes data analysis, process improvement, and collaboration across departments and with suppliers. By applying these key techniques, manufacturers can optimize their inventory levels, reduce costs, and increase operational efficiency.
Challenges in Inventory Optimization
Navigating the intricate web of inventory optimization presents a unique set of challenges. Businesses must address these to maintain efficiency and competitiveness. The dynamic nature of supply chains, influenced by global markets and technological advancements, adds layers of complexity to inventory management.
Inventory Optimization in the Face of Uncertainty
The modern supply chain is fraught with uncertainties, from sudden supply chain disruptions to unpredictable consumer demand. Businesses must remain agile, anticipating and adapting to these challenges to prevent stock outs or overstocking, which can erode profit margins. For instance, during the pandemic, companies like Zara adapted quickly. They used their flexible supply chain to adjust inventory levels in response to rapidly changing consumer behavior, showcasing the importance of agility in inventory optimization.
Balancing Cost and Service Level
Striking the right balance between minimizing costs and maximizing service levels is a perennial challenge. Excessive inventory can incur high holding costs, while too little can result in lost sales and customer dissatisfaction. This delicate balance requires sophisticated strategies that align inventory levels with business goals, ensuring that service levels are met without compromising financial efficiency.
Technological and Process Integration Challenges
The integration of advanced inventory optimization software into existing systems poses significant challenges. Ensuring that technology solutions communicate seamlessly with each other and with human operators is critical for creating a cohesive inventory management ecosystem. Furthermore, training staff to utilize these technologies effectively is essential for harnessing their full potential, highlighting the importance of human factors in technological adoption.
Data Accuracy and Analytics
Data is the lifeblood of inventory optimization, yet ensuring its accuracy and effectively analyzing it remain formidable challenges. Inaccurate data can lead to poor decision-making, resulting in overstock or stockouts. Companies must invest in robust data management systems and analytics tools to extract actionable insights from their data, enabling them to make informed decisions about inventory levels and procurement strategies.
Advanced Strategies for Inventory Optimization
The landscape of inventory optimization is continually evolving, demanding not just adaptation but also innovation from businesses. Advanced strategies, such as streamlined ordering processes and a strong emphasis on data analytics, are becoming indispensable in this regard.
Streamlining ordering processes involves utilizing key inventory formulas—economic order quantities, safety stock levels, reorder points, and lead times for all products. This strategic approach enables businesses to balance customer service and cash flow effectively. A notable example is the use of ABC classification, which prioritizes items based on their value to the company, ensuring that the most critical items are always in stock. This methodological approach not only optimizes inventory levels but also significantly reduces costs associated with holding and ordering stock.
Data analytics, on the other hand, empowers businesses with actionable insights, enabling them to make informed decisions about inventory management. By harnessing the power of data, companies can improve demand forecasting, identify unreliable suppliers, and optimize inventory across multiple locations. The emphasis on analytics has transformed inventory optimization from a reactive to a proactive strategy, where decisions are data-driven rather than based on intuition.
Effective Operations Beyond Inventory Management Systems
The ultimate success of inventory optimization strategies hinges not just on the implementation of systems but on their effective operation. It’s a testament to the fact that technology alone is not a panacea; rather, it’s the synergy between technology and operations that unlocks the full potential of inventory optimization. Companies that excel in this area often have a culture of continuous improvement and a commitment to leveraging technology for operational excellence.
CADDi Drawer serves as one of the tools to bridge continuous improvement and technology utilization, working in coordination with inventory management systems. It supports activities such as demand planning, ABC analysis, and supplier management. By transforming various data into actionable assets, it rationalizes procurement activities, which are fundamental to inventory optimization.
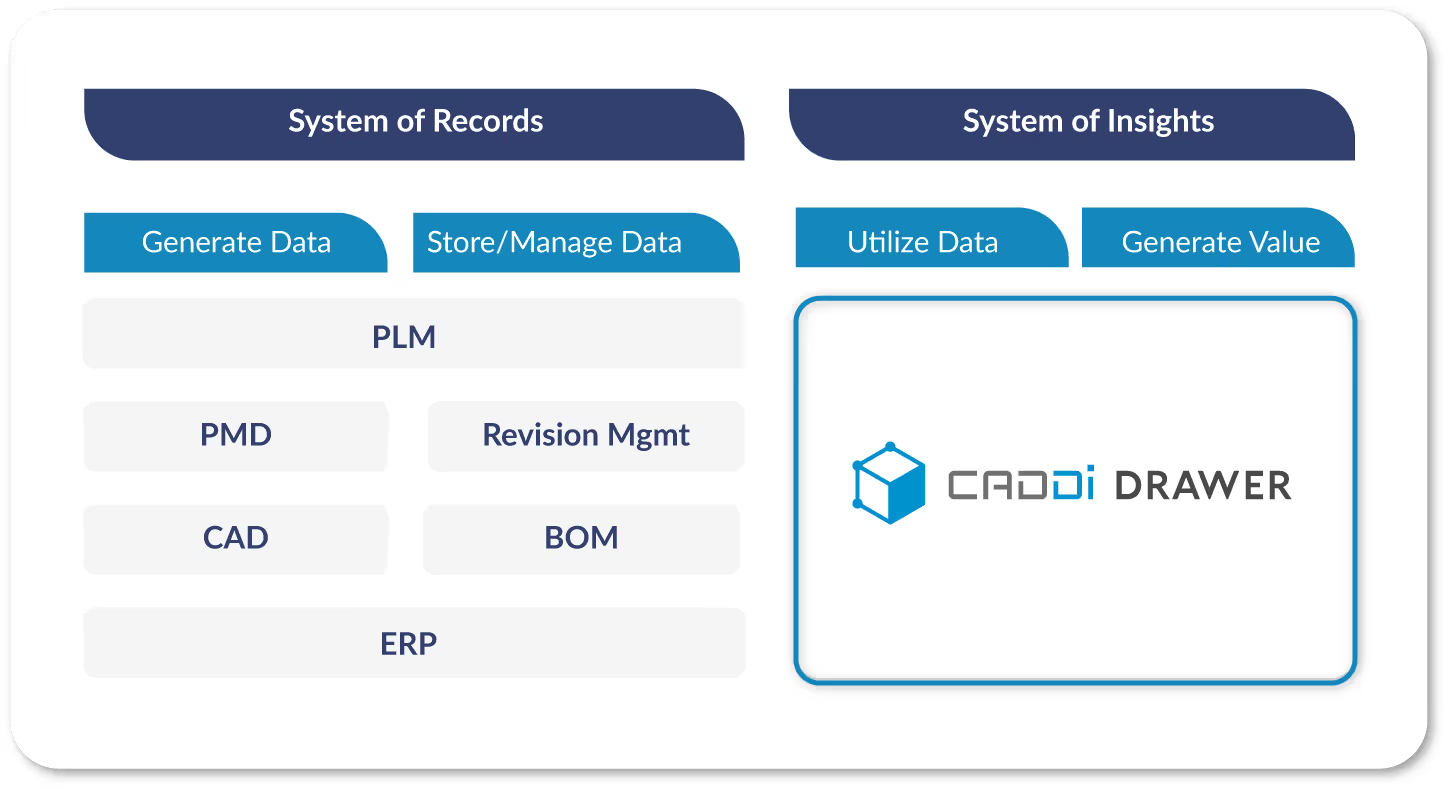
Inventory optimization is a strategic maneuver aimed at creating the perfect balance between inventory levels and customer demand. It ensures that products are available when needed without tying up unnecessary capital in excess stock.
As you can easily imagine, the goal here is not simply to optimize inventory levels temporarily. Instead, it is to continue optimizing inventory levels under a sustainable system. Below, we would like to explain the key elements and solutions that should be considered for this purpose.
Key Techniques in Inventory Optimization
Demand Planning (Demand forecasting)
Accurate demand planning is critical in the manufacturing industry to ensure that the right amount of products is produced to meet customer demands without leading to overproduction or stockouts. Techniques such as statistical analysis, machine learning models, and historical data analysis are used to predict future demand accurately.
Just-In-Time (JIT) Inventory Management
JIT is a strategy that reduces inventory holding costs by receiving goods only as they are needed in the production process. This requires close collaboration with suppliers and precise demand forecasting to ensure that materials arrive just in time for manufacturing. It reduces the need for large inventories.
Safety Stock Management
Despite the best efforts to forecast demand and supply accurately, variability and uncertainties exist. Safety stock acts as a buffer against this unpredictability. It ensures that production can continue even in the face of delays or higher than expected demand. The key is to calculate the optimal level of safety stock that minimizes risk without tying up excessive capital.
ABC Analysis
This technique involves categorizing inventory into three categories (A, B, and C). Categorize them based on their importance or value to the company. ‘A’ items are the most valuable and require close monitoring and management. ‘B’ items are of moderate value, and ‘C’ items are the least valuable. This allows manufacturers to prioritize their inventory management efforts and resources effectively.
Lean Manufacturing
Lean manufacturing principles focus on eliminating waste throughout the production process, including excess inventory. Techniques such as value stream mapping and continuous improvement processes are used to identify and eliminate non-value-added activities and inventory. This improves efficiency and reduces costs.
Supplier Relationship Management
Developing strong relationships with suppliers based on effective supplier management approaches is key to effective inventory optimization. This can involve negotiating better terms, improving communication and collaboration, and integrating systems for more efficient inventory management and replenishment.
Inventory Turnover Ratio Analysis
Monitoring the inventory turnover ratio helps manufacturers understand how quickly inventory is being used or sold over a certain period. A higher turnover ratio indicates efficient inventory management, while a lower ratio may suggest overstocking or inefficiencies.
Economic Order Quantity (EOQ) Model
The EOQ model is used to determine the optimal order quantity that minimizes the total cost of inventory. This includes ordering, holding, and shortage costs. This calculation helps in making informed purchasing decisions.
Implementing these techniques requires a comprehensive approach that includes data analysis, process improvement, and collaboration across departments and with suppliers. By applying these key techniques, manufacturers can optimize their inventory levels, reduce costs, and increase operational efficiency.
Challenges in Inventory Optimization
Navigating the intricate web of inventory optimization presents a unique set of challenges. Businesses must address these to maintain efficiency and competitiveness. The dynamic nature of supply chains, influenced by global markets and technological advancements, adds layers of complexity to inventory management.
Inventory Optimization in the Face of Uncertainty
The modern supply chain is fraught with uncertainties, from sudden supply chain disruptions to unpredictable consumer demand. Businesses must remain agile, anticipating and adapting to these challenges to prevent stock outs or overstocking, which can erode profit margins. For instance, during the pandemic, companies like Zara adapted quickly. They used their flexible supply chain to adjust inventory levels in response to rapidly changing consumer behavior, showcasing the importance of agility in inventory optimization.
Balancing Cost and Service Level
Striking the right balance between minimizing costs and maximizing service levels is a perennial challenge. Excessive inventory can incur high holding costs, while too little can result in lost sales and customer dissatisfaction. This delicate balance requires sophisticated strategies that align inventory levels with business goals, ensuring that service levels are met without compromising financial efficiency.
Technological and Process Integration Challenges
The integration of advanced inventory optimization software into existing systems poses significant challenges. Ensuring that technology solutions communicate seamlessly with each other and with human operators is critical for creating a cohesive inventory management ecosystem. Furthermore, training staff to utilize these technologies effectively is essential for harnessing their full potential, highlighting the importance of human factors in technological adoption.
Data Accuracy and Analytics
Data is the lifeblood of inventory optimization, yet ensuring its accuracy and effectively analyzing it remain formidable challenges. Inaccurate data can lead to poor decision-making, resulting in overstock or stockouts. Companies must invest in robust data management systems and analytics tools to extract actionable insights from their data, enabling them to make informed decisions about inventory levels and procurement strategies.
Advanced Strategies for Inventory Optimization
The landscape of inventory optimization is continually evolving, demanding not just adaptation but also innovation from businesses. Advanced strategies, such as streamlined ordering processes and a strong emphasis on data analytics, are becoming indispensable in this regard.
Streamlining ordering processes involves utilizing key inventory formulas—economic order quantities, safety stock levels, reorder points, and lead times for all products. This strategic approach enables businesses to balance customer service and cash flow effectively. A notable example is the use of ABC classification, which prioritizes items based on their value to the company, ensuring that the most critical items are always in stock. This methodological approach not only optimizes inventory levels but also significantly reduces costs associated with holding and ordering stock.
Data analytics, on the other hand, empowers businesses with actionable insights, enabling them to make informed decisions about inventory management. By harnessing the power of data, companies can improve demand forecasting, identify unreliable suppliers, and optimize inventory across multiple locations. The emphasis on analytics has transformed inventory optimization from a reactive to a proactive strategy, where decisions are data-driven rather than based on intuition.
Effective Operations Beyond Inventory Management Systems
The ultimate success of inventory optimization strategies hinges not just on the implementation of systems but on their effective operation. It’s a testament to the fact that technology alone is not a panacea; rather, it’s the synergy between technology and operations that unlocks the full potential of inventory optimization. Companies that excel in this area often have a culture of continuous improvement and a commitment to leveraging technology for operational excellence.
CADDi Drawer serves as one of the tools to bridge continuous improvement and technology utilization, working in coordination with inventory management systems. It supports activities such as demand planning, ABC analysis, and supplier management. By transforming various data into actionable assets, it rationalizes procurement activities, which are fundamental to inventory optimization.
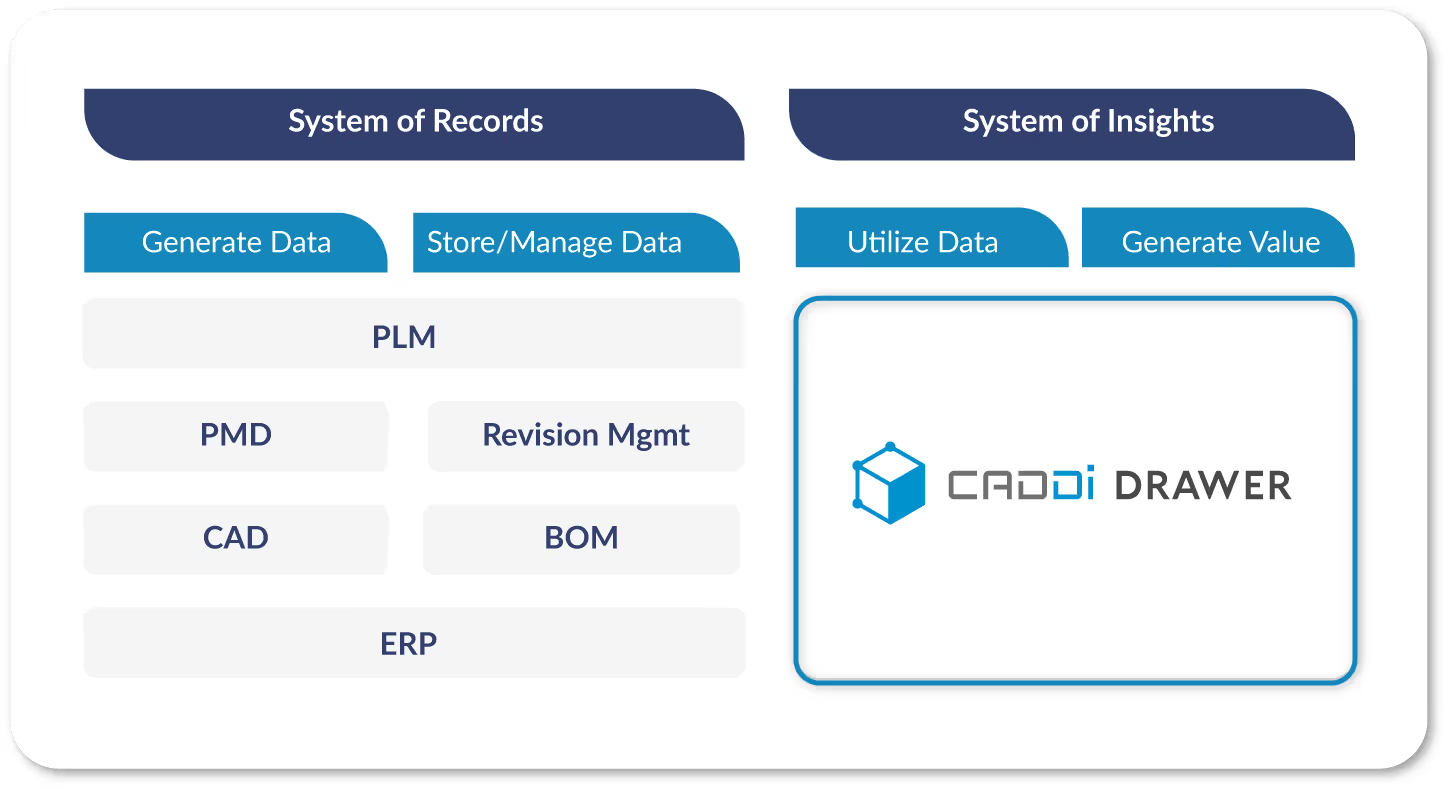
Ready to see CADDi Drawer in action? Get a personalized demo.
Subscribe to our Blog!
Related Resources
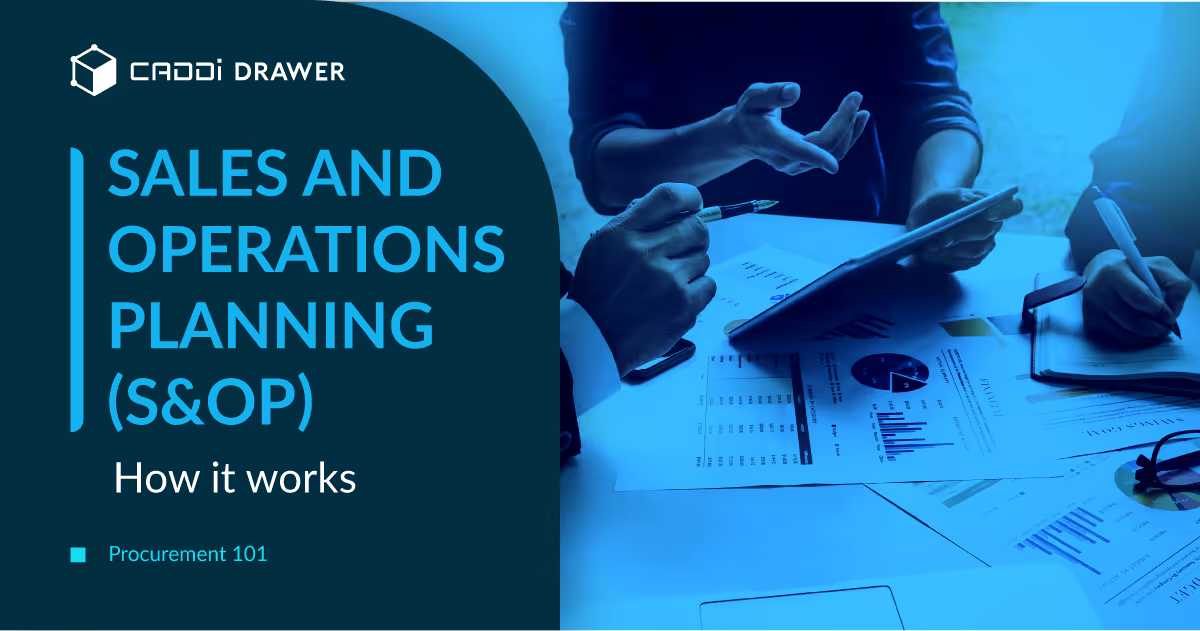
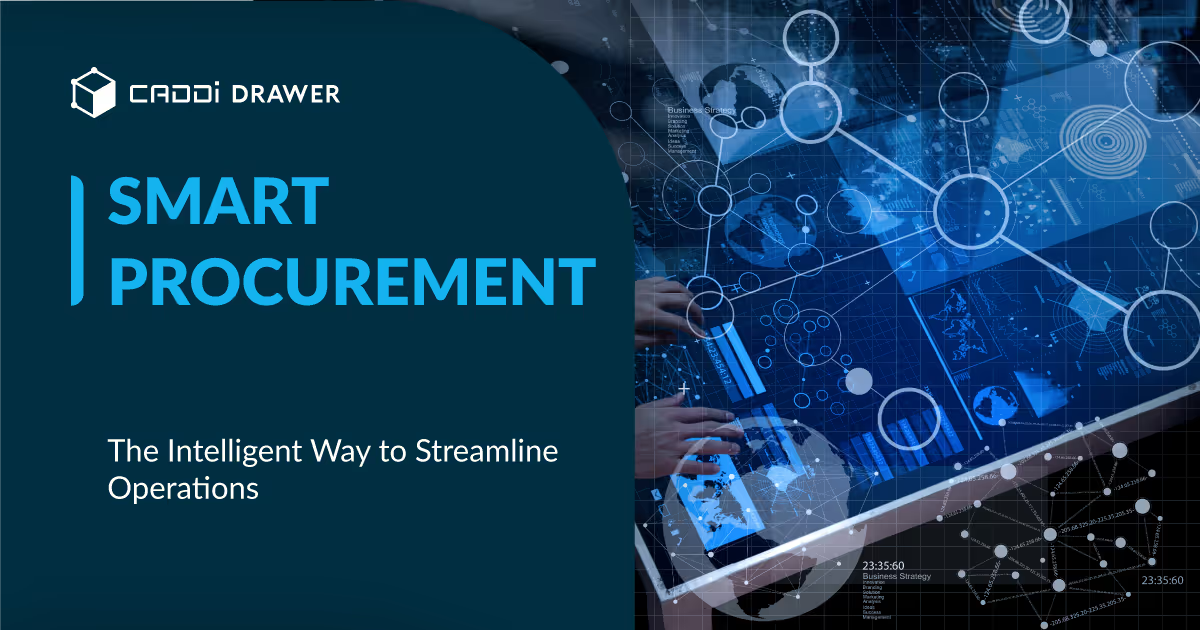
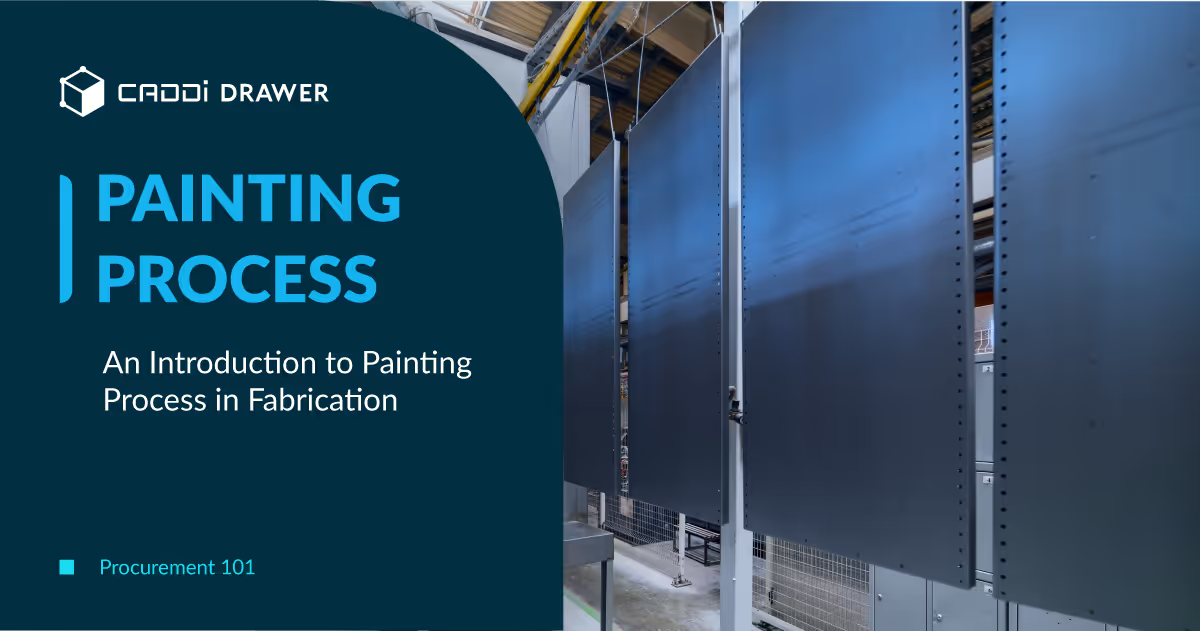

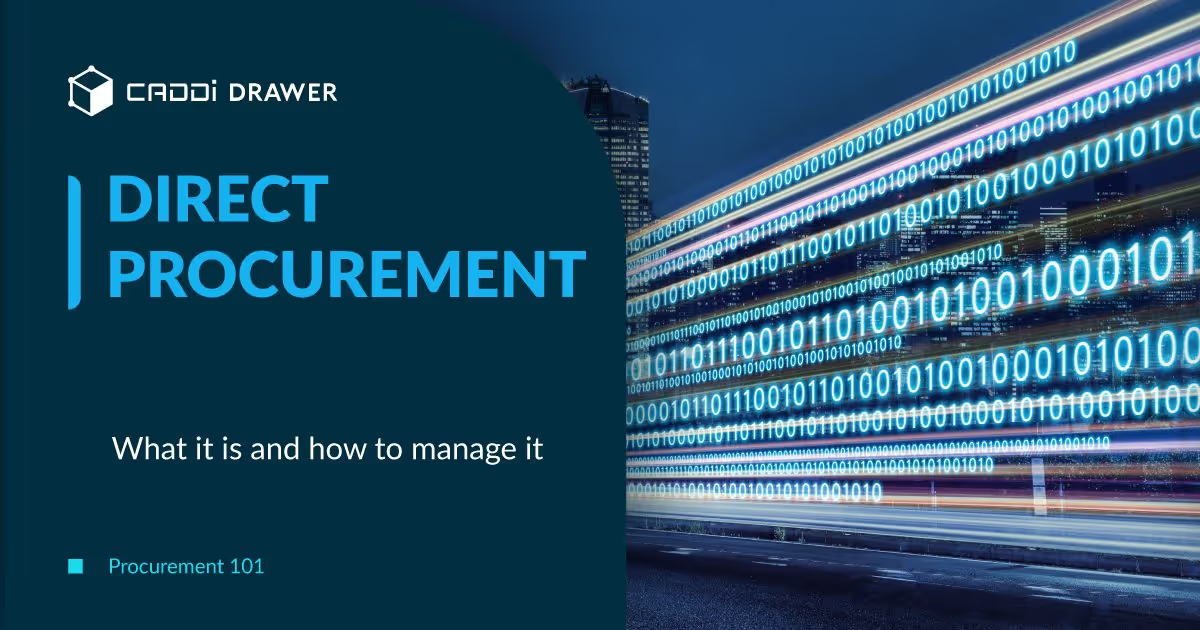
