What is a manufacturing parts database and how do you build a good one?
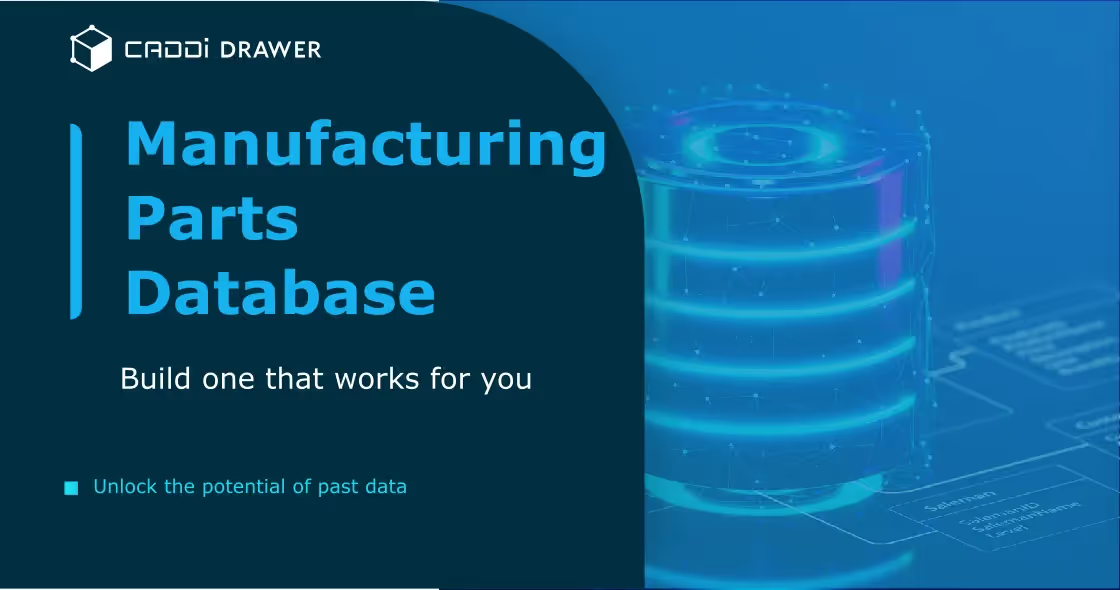
Table of Contents
A manufacturing parts database is a digital place where information about the parts you deal with are stored. This includes the parts you have in production, the parts you have in inventory, and the component parts you source for production. Your database should allow you to quickly surface strategic information about each part when required.
Manufacturing parts databases can operate within PLM (Product Lifecycle Management), PDM (Product Data Management), ERP (Enterprise Resource Planning) software solutions or other types of software platform. It’s common to have different types of information distributed across multiple different software platforms, although this can be suboptimal for strategic data utilization.
Types of data your manufacturing parts database should contain
Your manufacturing parts database should be able to connect all the relevant data for a given part. Depending on the type of part and what your organization does with it (e.g. is it a product you sell, something you produce as part of a larger product, a component part that you buy, etc.) the information you need may differ. Some commonly useful information includes:
Inventory information
If you’re working with parts that you have physically produced and made available for purchase, your parts database should include the logistical information about the actual physical items. This includes how many there are, where they’re stored, what process is required to ship them to a customer, what price you’ll charge, and more.
Material and process information
For parts that you manufacture, storing the data around the manufacturing process is essential. This includes how the part is manufactured, what machines and settings are involved, what materials and component parts are required, what finish is applied to the parts, and more.
Design information
You also should store the pre-production data of how a part was designed. This includes the actual drawing of the part, the data around the measurements, angles, and tolerances, any revisions and notes made during the design process, and more.
Procurement information
For component parts and other parts that you source from suppliers, you need to store all the information about those purchases. That includes costs, the timeline of when the parts were received, the quality data and defect rate for previous orders, and more.
Part metadata
Metadata refers to any information added to your database that helps organize and search it. This could include tags, comments, categories, labels, and more. Having the ability to add this information easily makes your database more dynamic and useful.
How your manufacturing parts database should operate
It’s important to have goals for what your database should be able to achieve for you. If you just make a database for the sake of making a database, it won’t actually be useful. Here are some of the goals your manufacturing parts database should achieve.
Fast data retrieval
The biggest factor for whether your parts database is useful or not is how quickly people can find things in it. Manufacturers often have issues where finding information in their database requires lots of manual checking and searching. If finding things is too slow, people won’t bother, and it’ll be like the data isn’t even there. Even if it’s “fast enough” that people make the effort, any slow aspects add up quickly given the number of searches your team will do. Optimizing speed as much as possible pays for itself.
Contextually complete
Often, you’ll need to see the complete picture for a given part in order to make the right decision. You’ll want the complete story, from the cost and defect rate of the component parts, to the design of the part, to the sales data of the produced part. If your database requires you to cross-reference multiple tools or locations to find all of this data, you’ll open yourself up to gaps, errors, and reduce time.
Easily comprehensible
It’s easy to build a database that you understand, where you know where to find things. But that’s only step one. You need to make a database that everyone on your team can understand and use, without your instruction. Even new team members should be able to use it to find what they need. Having everything linked to arbitrary ID numbers that need to be memorized or inconsistent language, or having things spread across multiple systems, makes it hard for new users to get what they need.
Quick to update and keep accurate
If your manufacturing parts database is out of date, it will be useless – or worse, leading you to make errors. It needs to automatically update from all of your sources. If updating it is manual, then it will inevitably get missed sooner or later.
Proactively surface strategic insights
Your manufacturing parts database should quickly and accurately answer any question you have for it. It should also allow you to proactively study the data within to find opportunities for proactive savings and efficiencies. For example, when looking up manufacturing processes across all your parts, your database should make it easy to compare timelines and costs for similar parts. This highlights outliers that should be addressed and opportunities to consolidate towards more efficient processes.
Making a manufacturing parts database with CADDi
CADDi can be the foundation of your manufacturing parts database. We provide a data lake, where data from all of your tools and platforms can be consolidated without manual reformatting. Then we connect all the data for a given part to the part’s drawing and make the drawing easily searchable. This makes your database easily searchable, even if you don’t know part IDs.
Check out how we can do this all for your organization by checking out a demo or exploring our product tour.
A manufacturing parts database is a digital place where information about the parts you deal with are stored. This includes the parts you have in production, the parts you have in inventory, and the component parts you source for production. Your database should allow you to quickly surface strategic information about each part when required.
Manufacturing parts databases can operate within PLM (Product Lifecycle Management), PDM (Product Data Management), ERP (Enterprise Resource Planning) software solutions or other types of software platform. It’s common to have different types of information distributed across multiple different software platforms, although this can be suboptimal for strategic data utilization.
Types of data your manufacturing parts database should contain
Your manufacturing parts database should be able to connect all the relevant data for a given part. Depending on the type of part and what your organization does with it (e.g. is it a product you sell, something you produce as part of a larger product, a component part that you buy, etc.) the information you need may differ. Some commonly useful information includes:
Inventory information
If you’re working with parts that you have physically produced and made available for purchase, your parts database should include the logistical information about the actual physical items. This includes how many there are, where they’re stored, what process is required to ship them to a customer, what price you’ll charge, and more.
Material and process information
For parts that you manufacture, storing the data around the manufacturing process is essential. This includes how the part is manufactured, what machines and settings are involved, what materials and component parts are required, what finish is applied to the parts, and more.
Design information
You also should store the pre-production data of how a part was designed. This includes the actual drawing of the part, the data around the measurements, angles, and tolerances, any revisions and notes made during the design process, and more.
Procurement information
For component parts and other parts that you source from suppliers, you need to store all the information about those purchases. That includes costs, the timeline of when the parts were received, the quality data and defect rate for previous orders, and more.
Part metadata
Metadata refers to any information added to your database that helps organize and search it. This could include tags, comments, categories, labels, and more. Having the ability to add this information easily makes your database more dynamic and useful.
How your manufacturing parts database should operate
It’s important to have goals for what your database should be able to achieve for you. If you just make a database for the sake of making a database, it won’t actually be useful. Here are some of the goals your manufacturing parts database should achieve.
Fast data retrieval
The biggest factor for whether your parts database is useful or not is how quickly people can find things in it. Manufacturers often have issues where finding information in their database requires lots of manual checking and searching. If finding things is too slow, people won’t bother, and it’ll be like the data isn’t even there. Even if it’s “fast enough” that people make the effort, any slow aspects add up quickly given the number of searches your team will do. Optimizing speed as much as possible pays for itself.
Contextually complete
Often, you’ll need to see the complete picture for a given part in order to make the right decision. You’ll want the complete story, from the cost and defect rate of the component parts, to the design of the part, to the sales data of the produced part. If your database requires you to cross-reference multiple tools or locations to find all of this data, you’ll open yourself up to gaps, errors, and reduce time.
Easily comprehensible
It’s easy to build a database that you understand, where you know where to find things. But that’s only step one. You need to make a database that everyone on your team can understand and use, without your instruction. Even new team members should be able to use it to find what they need. Having everything linked to arbitrary ID numbers that need to be memorized or inconsistent language, or having things spread across multiple systems, makes it hard for new users to get what they need.
Quick to update and keep accurate
If your manufacturing parts database is out of date, it will be useless – or worse, leading you to make errors. It needs to automatically update from all of your sources. If updating it is manual, then it will inevitably get missed sooner or later.
Proactively surface strategic insights
Your manufacturing parts database should quickly and accurately answer any question you have for it. It should also allow you to proactively study the data within to find opportunities for proactive savings and efficiencies. For example, when looking up manufacturing processes across all your parts, your database should make it easy to compare timelines and costs for similar parts. This highlights outliers that should be addressed and opportunities to consolidate towards more efficient processes.
Making a manufacturing parts database with CADDi
CADDi can be the foundation of your manufacturing parts database. We provide a data lake, where data from all of your tools and platforms can be consolidated without manual reformatting. Then we connect all the data for a given part to the part’s drawing and make the drawing easily searchable. This makes your database easily searchable, even if you don’t know part IDs.
Check out how we can do this all for your organization by checking out a demo or exploring our product tour.