Saving Money in Manufacturing
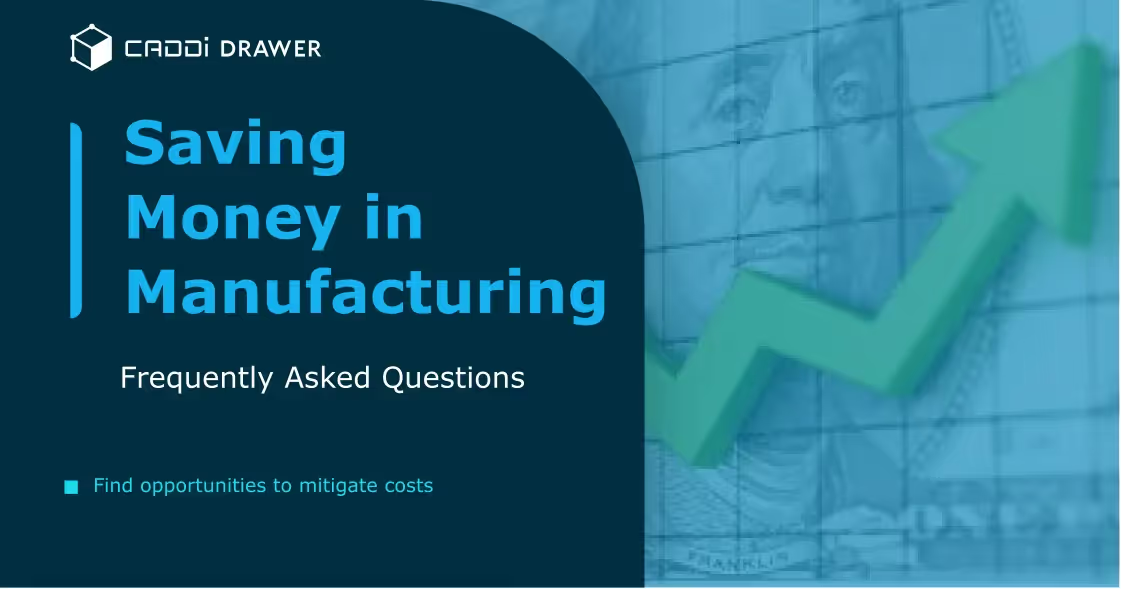
Table of Contents
2025 will likely be a costly year for manufacturing shops across America. Between labour shortages, supply chain disruptions, tariffs, and more, you can expect that your costs of doing business will noticeably increase.
The best way to deal with these costs isn’t to shrink output or increase end user costs. Ideally, you find opportunities to save such that the costs are offset. That sounds nice in theory, but how do you execute it in practice? Check out our FAQ to learn some good tips on attacking costs with proactive savings.
What is the best way to save money in a manufacturing shop?
The best way to save money is by looking for better value opportunities within your practices for procurement and design. This may be surprising to hear. Often, manufacturers will try to save money on the manufacturing process itself. This makes sense, because that’s where their expertise lies and where they feel most confident in finding better options. However, because it’s their expertise, it means most of the “low-hanging fruit” of savings have already been found. Further optimization will have diminishing returns, and also be more and more specialized towards specific processes.
On the other hand, it’s likely that you haven’t focused on optimizing the data-based processes of how you design products and source components. You likely have processes that work well enough and are cost effective enough that your work remains profitable. However, if you haven’t done deliberate analysis and optimization, there’s plenty of room for savings. Not only will these savings be relatively easy to unlock and more substantial than manufacturing process savings, they’ll be universally applicable to all of your products.
How do you save money on manufacturing procurement?
There are many ways to save money on procurement, including:
- Consolidating suppliers to fewer companies in order to negotiate better deals
- Consolidating parts to fewer functional equivalents to negotiate bulk rates
- Finding cheaper alternatives that still meet the necessary quality thresholds
- Designing parts to have cheaper components while still retaining the same functions
- Switching to domestic suppliers to avoid tariffs and reduce shipping costs where possible
The common factor in all of these strategies is that they require comprehensive data analysis of your previous choices and future options. You need to be able to cross-reference past order data, defect rates and quality data in production, and the designs of all of your parts. Most shops aren’t equipped to do this sort of analysis, or at least not without investing a ton of time and effort.
Fortunately, there are technological solutions that can help you make this process easy, fast, and consistent. CADDi is an AI data platform that can consolidate all of your data into one place, removing the need for manual cross-referencing. Then, using AI drawing analysis, it can highlight patterns in your designs to find more cost-effective solutions. Check out a demo or walk through the product tour to learn more.
How do you save money on manufacturing designs?
The most impactful way to lower costs on new designs is to cross reference new designs with previous ones and build off of what was previously successful and cost-effective. It’s not uncommon that engineers will design new products and parts inconsistently from past designs. This will lead to using different components, materials, and processes where a previous design’s choices would have sufficed. These additional requirements increase costs. Moreover, many design choices are simply more expensive than other options that are sufficient.
This seems like an easy issue to avoid, but the problem is that finding the relevant previous drawings is hard, if not impossible. If drawings are stored somewhere in your system, it likely only has an ID number or label to look it up. Searching for the drawings becomes a tedious process involving lots of manual checking and comparing. Even when the relevant drawings are found, often the pricing information is stored in another program, requiring manual cross-referencing. Given all of these headaches, engineers are likely to design something new from scratch.
However, a recent technological solution can overcome this issue. New AI technology can analyze drawings on its own, connecting drawings with similar features without manual comparison. CADDi’s similarity search can take an engineer’s first draft sketch and instantly surface all similar drawings. Saving money by reusing components and materials, or perhaps entire designs, based on these previous drawings becomes easy. Then, CADDi automatically links pricing data to help you understand what design elements are costing you unnecessarily more. Check out a demo or walk through the product tour to learn more.
2025 will likely be a costly year for manufacturing shops across America. Between labour shortages, supply chain disruptions, tariffs, and more, you can expect that your costs of doing business will noticeably increase.
The best way to deal with these costs isn’t to shrink output or increase end user costs. Ideally, you find opportunities to save such that the costs are offset. That sounds nice in theory, but how do you execute it in practice? Check out our FAQ to learn some good tips on attacking costs with proactive savings.
What is the best way to save money in a manufacturing shop?
The best way to save money is by looking for better value opportunities within your practices for procurement and design. This may be surprising to hear. Often, manufacturers will try to save money on the manufacturing process itself. This makes sense, because that’s where their expertise lies and where they feel most confident in finding better options. However, because it’s their expertise, it means most of the “low-hanging fruit” of savings have already been found. Further optimization will have diminishing returns, and also be more and more specialized towards specific processes.
On the other hand, it’s likely that you haven’t focused on optimizing the data-based processes of how you design products and source components. You likely have processes that work well enough and are cost effective enough that your work remains profitable. However, if you haven’t done deliberate analysis and optimization, there’s plenty of room for savings. Not only will these savings be relatively easy to unlock and more substantial than manufacturing process savings, they’ll be universally applicable to all of your products.
How do you save money on manufacturing procurement?
There are many ways to save money on procurement, including:
- Consolidating suppliers to fewer companies in order to negotiate better deals
- Consolidating parts to fewer functional equivalents to negotiate bulk rates
- Finding cheaper alternatives that still meet the necessary quality thresholds
- Designing parts to have cheaper components while still retaining the same functions
- Switching to domestic suppliers to avoid tariffs and reduce shipping costs where possible
The common factor in all of these strategies is that they require comprehensive data analysis of your previous choices and future options. You need to be able to cross-reference past order data, defect rates and quality data in production, and the designs of all of your parts. Most shops aren’t equipped to do this sort of analysis, or at least not without investing a ton of time and effort.
Fortunately, there are technological solutions that can help you make this process easy, fast, and consistent. CADDi is an AI data platform that can consolidate all of your data into one place, removing the need for manual cross-referencing. Then, using AI drawing analysis, it can highlight patterns in your designs to find more cost-effective solutions. Check out a demo or walk through the product tour to learn more.
How do you save money on manufacturing designs?
The most impactful way to lower costs on new designs is to cross reference new designs with previous ones and build off of what was previously successful and cost-effective. It’s not uncommon that engineers will design new products and parts inconsistently from past designs. This will lead to using different components, materials, and processes where a previous design’s choices would have sufficed. These additional requirements increase costs. Moreover, many design choices are simply more expensive than other options that are sufficient.
This seems like an easy issue to avoid, but the problem is that finding the relevant previous drawings is hard, if not impossible. If drawings are stored somewhere in your system, it likely only has an ID number or label to look it up. Searching for the drawings becomes a tedious process involving lots of manual checking and comparing. Even when the relevant drawings are found, often the pricing information is stored in another program, requiring manual cross-referencing. Given all of these headaches, engineers are likely to design something new from scratch.
However, a recent technological solution can overcome this issue. New AI technology can analyze drawings on its own, connecting drawings with similar features without manual comparison. CADDi’s similarity search can take an engineer’s first draft sketch and instantly surface all similar drawings. Saving money by reusing components and materials, or perhaps entire designs, based on these previous drawings becomes easy. Then, CADDi automatically links pricing data to help you understand what design elements are costing you unnecessarily more. Check out a demo or walk through the product tour to learn more.