Fastener Consolidation: What it is and how to use AI analysis to achieve it quickly
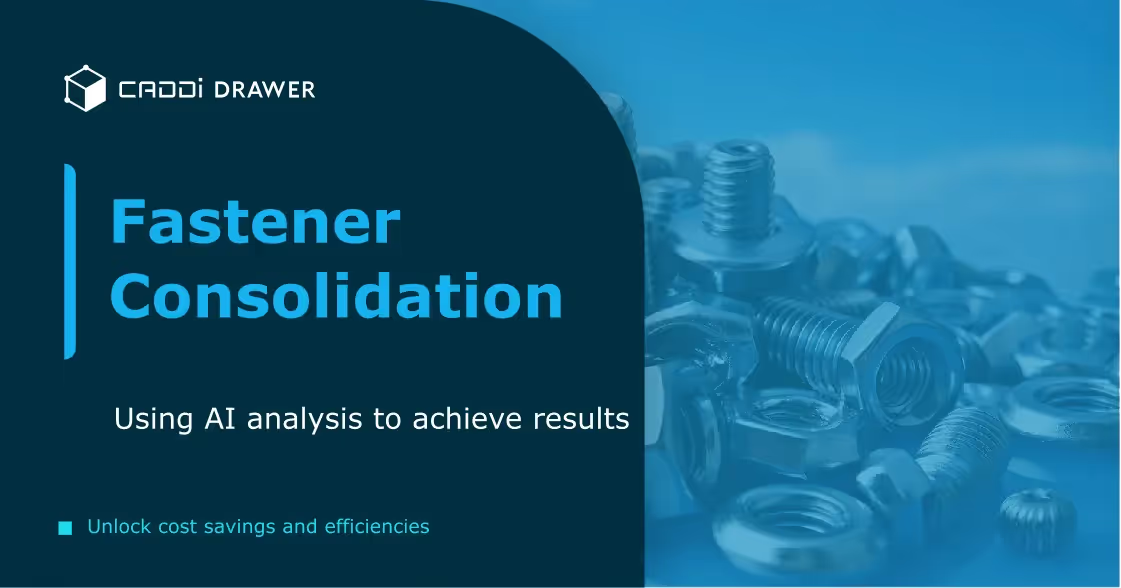
Table of Contents
Fastener consolidation is the process of analyzing all of the fasteners – screws, bolts, clamps, etc. – used across all of your product designs and reducing the number of them. Consolidating the types of fasteners you use provides tremendous benefits in cost savings, faster designs, and lower defect rates. As is the case with general parts proliferation, manufacturing shops often accumulate hundreds of unnecessary fasteners, causing many issues. However, undertaking this exercise to eliminate these redundancies has some challenges that you’ll need to deal with in order to maximize these benefits.
Read on to learn what benefits you should expect from fastener consolidation, what challenges it comes with, and how to overcome those challenges with cutting-edge AI analysis.
Benefits of fastener consolidation
Some of the benefits you can expect to see from achieving fastener consolidation include:
Supplier consolidation and procurement efficiencies
One immediate benefit is that the number of different parts you need to source decreases. Rather than having 80 slightly different screws, you go down to just one. As a result, you’ll order from fewer suppliers. This increases the efficiency of procurement processes, as they’ll need to search for suppliers less often. It also helps you reduce costs per part. You’ll make larger bulk orders from each supplier, allowing for stronger negotiation and rate discounting.
Faster and better designs
Another benefit of fastener consolidation is in the design process. When designing a new part, engineers will know immediately what fastener to use in which situation, instead of having an overwhelming amount of options. Moreover, without fastener consolidation, information on what fasteners have been used before is often scattershot and incomplete. This leads to engineers designing with even more new fasteners, further exacerbating the problem of fastener proliferation. Having a few options, clearly delineated for each case, makes designing new parts much faster and prevents them muddying up your parts catalogue further.
Lower defect and failure rates
Fasteners have a certain failure rate and defect rate, just like any other part. When designing new parts, sourcing component parts, or predicting the failure rate of components in operation, it’s important to know the rates of the fasteners involved. The more different fasteners you’re working with, the less you know about the operation of each of them. Consolidating fasteners allows you to get more testing data for each of them. This allows you to have a more accurate picture of the quality of each product. In turn, this enables designing smarter around this information, leading to higher quality products and lower defect and failure rates.
Better SKU management and reduced organizational costs
As we’ve seen with parts proliferation, having your databases stuffed full of unnecessary entries is costly. You have the direct costs of hosting a larger-than-necessary database, and possibly physical inventory. Then you have the costs of having people maintain the accuracy of the database, which scales quickly with the size of the database. Most impactfully is the time sink in actually using the database. The more unnecessary entries you have, the harder it is to find what you need, creating slowdowns in workflows across your shop and massive opportunity costs.
All of this is just as true for fasteners as any other part. Fastener consolidation can reduce the size of your database, and thus reduce all these associated costs.
Better procurement agility and supply chain management
We live in an uncertain world in terms of the supply chain. Tariffs, other geopolitical conflicts, and shortages can quickly disrupt any procurement strategy and leave teams scrambling to find alternative suppliers. When you’re trying to find an alternative for 800 different types of fasteners, this can be an impossible task. When it’s only 80, it’s a lot more doable. Fastener consolidation allows you to have more options and switch to them more flexibly.
Challenges of fastener consolidation
With all of these benefits, it seems like an obvious choice to undertake a fastener consolidation exercise. And the process itself seems straightforward too. In a nutshell, you:
- Track down all the different fasteners currently used across your shop
- Look at each of them and figure out which are redundant
- Categorize them into as few functionally distinct categories as possible
- Figure out which fastener to go with for each category based on price and quality data
- Update designs to use only the chosen fasteners
It sounds so easy on paper, but when you try to work through this process, you’ll find some stumbling blocks, including:
It takes a long time to do fastener consolidation
The most obvious challenge here is that all of these steps take a very long time when you have lots of fasteners. Tracking down specific designs and reviewing which fasteners are used in each of them is very manual and tedious. It may also require an expert to parse drawings, further bottlenecking your process.
The data you need is likely incomplete or inaccessible
On top of taking a long time, fastener consolidation may also lead you down wild goose chases. You may be digging around for data that exists only on paper, in the memory of other employees, or in gigantic spreadsheets with meaningless ID numbers. You’ll likely have to dive into a variety of tools that each contain their own subset of the story. This isn’t just time-consuming, it’s frustrating, leading many shops to abandon the process.
Cross-referencing contextual data is time-consuming, too
When you’re trying to determine which fasteners are worth keeping, you want to see the big picture on each of them: how much do they cost, which suppliers can we get them from, what are their defect and failure rates, etc. Cross-referencing this data for each part is typically a tedious and manual process, and can also lead to many goose hunts when things are incomplete.
In all, although fastener consolidation sounds easy on paper, in practice it can be anything but. It’s no wonder that shops often don’t have the resources to tackle this project proactively, even when they understand the benefits. However, there is a modern solution that makes fastener consolidation much faster: AI analysis.
Fastener consolidation with CADDi
On top of all the other amazing use cases of CADDi, we make fastener consolidation quick and painless. Here’s how:
Connect unstructured data into a data lake
Rather than having to root through a million spreadsheets, tools, and even filing cabinets, CADDi can receive all your data and organize it into one comprehensive data lake. This way, when you search for fasteners, you can be confident you’re finding them all.
Use AI image search to track down fasteners
Rather than manually looking at each design and trying to find all the fasteners, CADDi uses cutting-edge AI machine vision to “look at” every drawing for you. Upload an example drawing of different types of fasteners – clamps, bolts, etc. – and CADDi will find all the drawings that contain them. You can even start with a hand drawn sketch as your example.
You can also search for how fasteners are labelled in drawings. CADDi uses best-in-class OCR to find where these labels are written on drawings without needing them to be transcribed into text. Using CADDi searching, you can easily track down every fastener currently used by your shop.
AI image analysis to create categories of fastener
CADDi can go even further, automatically categorizing similar fasteners using our similarity search. Search using any example of a fastener and CADDi will instantly surface the most similar designs. This allows you to quickly identify redundant fasteners without requiring expertise or manual analysis.
Surface contextual data to make strategic choices
When it comes time to decide which fasteners should remain in use, CADDi makes the choice easier by automatically surfacing the relevant contextual data for each fastener. This includes quality reports, pricing history, supplier information, and more. Even new members to your teams can make the necessary strategic analysis to make the correct choice with this information surfaced and highlighted.
To see CADDi in action and learn how it can help achieve your fastener consolidation goals, check out a demo today.
Fastener consolidation is the process of analyzing all of the fasteners – screws, bolts, clamps, etc. – used across all of your product designs and reducing the number of them. Consolidating the types of fasteners you use provides tremendous benefits in cost savings, faster designs, and lower defect rates. As is the case with general parts proliferation, manufacturing shops often accumulate hundreds of unnecessary fasteners, causing many issues. However, undertaking this exercise to eliminate these redundancies has some challenges that you’ll need to deal with in order to maximize these benefits.
Read on to learn what benefits you should expect from fastener consolidation, what challenges it comes with, and how to overcome those challenges with cutting-edge AI analysis.
Benefits of fastener consolidation
Some of the benefits you can expect to see from achieving fastener consolidation include:
Supplier consolidation and procurement efficiencies
One immediate benefit is that the number of different parts you need to source decreases. Rather than having 80 slightly different screws, you go down to just one. As a result, you’ll order from fewer suppliers. This increases the efficiency of procurement processes, as they’ll need to search for suppliers less often. It also helps you reduce costs per part. You’ll make larger bulk orders from each supplier, allowing for stronger negotiation and rate discounting.
Faster and better designs
Another benefit of fastener consolidation is in the design process. When designing a new part, engineers will know immediately what fastener to use in which situation, instead of having an overwhelming amount of options. Moreover, without fastener consolidation, information on what fasteners have been used before is often scattershot and incomplete. This leads to engineers designing with even more new fasteners, further exacerbating the problem of fastener proliferation. Having a few options, clearly delineated for each case, makes designing new parts much faster and prevents them muddying up your parts catalogue further.
Lower defect and failure rates
Fasteners have a certain failure rate and defect rate, just like any other part. When designing new parts, sourcing component parts, or predicting the failure rate of components in operation, it’s important to know the rates of the fasteners involved. The more different fasteners you’re working with, the less you know about the operation of each of them. Consolidating fasteners allows you to get more testing data for each of them. This allows you to have a more accurate picture of the quality of each product. In turn, this enables designing smarter around this information, leading to higher quality products and lower defect and failure rates.
Better SKU management and reduced organizational costs
As we’ve seen with parts proliferation, having your databases stuffed full of unnecessary entries is costly. You have the direct costs of hosting a larger-than-necessary database, and possibly physical inventory. Then you have the costs of having people maintain the accuracy of the database, which scales quickly with the size of the database. Most impactfully is the time sink in actually using the database. The more unnecessary entries you have, the harder it is to find what you need, creating slowdowns in workflows across your shop and massive opportunity costs.
All of this is just as true for fasteners as any other part. Fastener consolidation can reduce the size of your database, and thus reduce all these associated costs.
Better procurement agility and supply chain management
We live in an uncertain world in terms of the supply chain. Tariffs, other geopolitical conflicts, and shortages can quickly disrupt any procurement strategy and leave teams scrambling to find alternative suppliers. When you’re trying to find an alternative for 800 different types of fasteners, this can be an impossible task. When it’s only 80, it’s a lot more doable. Fastener consolidation allows you to have more options and switch to them more flexibly.
Challenges of fastener consolidation
With all of these benefits, it seems like an obvious choice to undertake a fastener consolidation exercise. And the process itself seems straightforward too. In a nutshell, you:
- Track down all the different fasteners currently used across your shop
- Look at each of them and figure out which are redundant
- Categorize them into as few functionally distinct categories as possible
- Figure out which fastener to go with for each category based on price and quality data
- Update designs to use only the chosen fasteners
It sounds so easy on paper, but when you try to work through this process, you’ll find some stumbling blocks, including:
It takes a long time to do fastener consolidation
The most obvious challenge here is that all of these steps take a very long time when you have lots of fasteners. Tracking down specific designs and reviewing which fasteners are used in each of them is very manual and tedious. It may also require an expert to parse drawings, further bottlenecking your process.
The data you need is likely incomplete or inaccessible
On top of taking a long time, fastener consolidation may also lead you down wild goose chases. You may be digging around for data that exists only on paper, in the memory of other employees, or in gigantic spreadsheets with meaningless ID numbers. You’ll likely have to dive into a variety of tools that each contain their own subset of the story. This isn’t just time-consuming, it’s frustrating, leading many shops to abandon the process.
Cross-referencing contextual data is time-consuming, too
When you’re trying to determine which fasteners are worth keeping, you want to see the big picture on each of them: how much do they cost, which suppliers can we get them from, what are their defect and failure rates, etc. Cross-referencing this data for each part is typically a tedious and manual process, and can also lead to many goose hunts when things are incomplete.
In all, although fastener consolidation sounds easy on paper, in practice it can be anything but. It’s no wonder that shops often don’t have the resources to tackle this project proactively, even when they understand the benefits. However, there is a modern solution that makes fastener consolidation much faster: AI analysis.
Fastener consolidation with CADDi
On top of all the other amazing use cases of CADDi, we make fastener consolidation quick and painless. Here’s how:
Connect unstructured data into a data lake
Rather than having to root through a million spreadsheets, tools, and even filing cabinets, CADDi can receive all your data and organize it into one comprehensive data lake. This way, when you search for fasteners, you can be confident you’re finding them all.
Use AI image search to track down fasteners
Rather than manually looking at each design and trying to find all the fasteners, CADDi uses cutting-edge AI machine vision to “look at” every drawing for you. Upload an example drawing of different types of fasteners – clamps, bolts, etc. – and CADDi will find all the drawings that contain them. You can even start with a hand drawn sketch as your example.
You can also search for how fasteners are labelled in drawings. CADDi uses best-in-class OCR to find where these labels are written on drawings without needing them to be transcribed into text. Using CADDi searching, you can easily track down every fastener currently used by your shop.
AI image analysis to create categories of fastener
CADDi can go even further, automatically categorizing similar fasteners using our similarity search. Search using any example of a fastener and CADDi will instantly surface the most similar designs. This allows you to quickly identify redundant fasteners without requiring expertise or manual analysis.
Surface contextual data to make strategic choices
When it comes time to decide which fasteners should remain in use, CADDi makes the choice easier by automatically surfacing the relevant contextual data for each fastener. This includes quality reports, pricing history, supplier information, and more. Even new members to your teams can make the necessary strategic analysis to make the correct choice with this information surfaced and highlighted.
To see CADDi in action and learn how it can help achieve your fastener consolidation goals, check out a demo today.