What is a Digital Transformation in Manufacturing and How Does it Help?
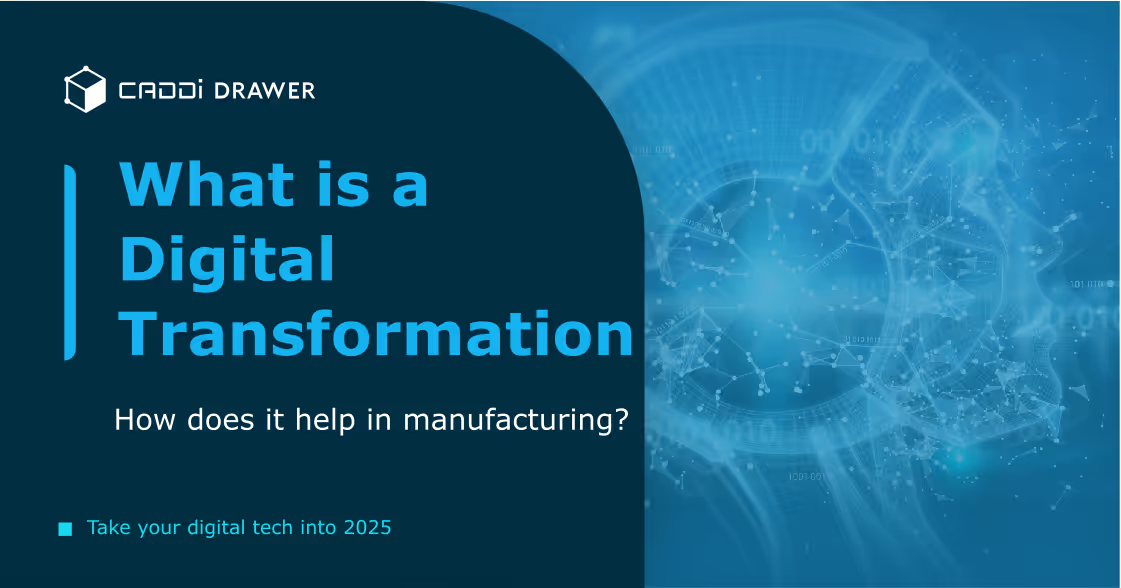
Table of Contents
A digital transformation is a process by which you improve your efficiency and productivity through moving data and operations from physical processes to digital systems. What that exactly involves depends on your particular systems and needs. In manufacturing, generally speaking, it means using digital systems to access your shop’s inputs and outputs, inventory, and data.
The term “digital transformation” has been used in many situations to describe different processes at different times. As such, it’s hard to know exactly what you should be doing to digitally transform, what benefits you should be seeing, and how to measure those benefits. We’ve prepared a digital transformation assessment tool to judge how far your manufacturing shop is in the digital transformation journey. Check it out, and read the rest of the blog to learn more about the concept of a digital transformation.
What have the manufacturing digital transformations been so far?
One challenge in launching headfirst into a digital transformation is the feeling of, well, haven’t we already been doing those before? And it’s true – your shop certainly has already completed several digital transformations over the years. The proof is in the fact that you’re reading this article right now: adopting the habit of educating yourself on the internet is a key outcome of digital transformations.
It can be easier to understand what to do in your upcoming digital transformation by looking at what technological leaps we’ve already experienced.
Computer-integrated manufacturing
Computer-integrated manufacturing means using manufacturing machines that are linked to computer systems which can control them, monitor their inputs and outputs, and help direct manual steps of the manufacturing process. These machines started appearing in the 1980s and have seen continuous improvement in the decades since.
Computer-integrated manufacturing was an extremely impactful digital transformation. It increases the flexibility of machines, the speed at which their outputs can be changed, their consistency, and the strategic data generated as they run.
Emerging technologies like additive manufacturing (including 3D printing) and more sophisticated robotics are making manufacturing machines even more powerful. Modern computer-integrated manufacturing can have an automatic two-way relationship between the production’s output and follow-up instructions. For example, a machine can use AI-driven vision to detect when it produces a defective part, then use adaptive robotics to automatically remove it from the production line.
Fax machines and scanners
Another major digital transformation that occurred in the 1980s was the widespread adoption of fax machines and subsequently scanners. This freed designs and other information from being trapped on individual paper. Instead, drawings and other designs could be duplicated, shared between offices, and stored securely. These documents could be stored on computer systems, in higher quality images, using faster and more convenient techniques.
Although this technology is old, scanning documents is improving even today. Optical character reading (OCR) is a continually-improving practice that can “read” everything written on documents and convert it into digital text. This makes searching, revising, and sharing the contents of documents much easier. Modern OCR can even accurately transcribe handwritten notes.
Cutting-edge technology like CADDi are taking things even further, using AI-driven machine vision to analyze scanned drawings even deeper. Not only can it extract all of the text from a drawing to make it more searchable, it can understand the shapes and features of the drawing itself. This allows you to “search by shape”, making finding the correct designs much faster and easier.
Email and other digital communication
Perhaps the biggest transformation in the last few decades has been how we communicate with our colleagues. Remember when you had to call someone if you wanted to talk to them? Nowadays we have a plethora of ways to communicate – email, text messaging, communication tools like Slack, video calling tools like Zoom, shared digital workspaces like Google Docs or virtual whiteboards… every way you want to express yourself to someone remotely is possible today.
Although not directly linked to manufacturing, this digital transformation has brought massive new opportunities for any machine shop. Collaboration is easier than ever before, with people able to asynchronously leave ideas and comment on each other’s work. The status of production can be relayed to teams wherever they are, allowing for more rapid response to problems. Tools like Slack can make conversations searchable assets, keeping ideas and decisions in a place where they can easily be revisited and revised.
Your team is almost certainly taking advantage of this digital transformation already, but likely in a suboptimal way. Take the time to review your current communication infrastructure. What messages get missed, what is still hard to convey? What tools are you not yet implementing that would be helpful? By being deliberate about communication, you can build a more collaborative and efficient workforce.
Database software and cloud storage
The final digital transformation we’ll mention today is in how you store the data relevant to your shop’s decision-making. This includes tracking metrics around production, inventory, procurement, sales quotes, and more. It also includes storing digital assets, like CAD-created designs, scanned drawings, and process documents. It even includes corporate administrative data, like HR records, financials, and marketing assets.
The first stage of this digital transformation means organizing these data into “dumb databases”. This could look like a spreadsheet tracking inventory levels, or scans of drawings sorted into labeled folders. This is a great starting point, as it does give you access to a lot of information. However, that access is often time-consuming, tedious, and fraught with potential errors. If people don’t really know where something is, it’s very hard for them to find it, or even know that it might be there.
The next step is moving data into specialized programs that make it more usable, such as PLM or ERP software. This makes it much easier to find the data you need. It also enables cloud access, meaning teammates from anywhere can use the data. These specialized tools help you analyze different types of data, helping you make smarter decisions. However, they often lack the ability to make connections across different types of data, or intelligently surface contextual data. As such, they answer specific questions, but don’t help you “learn what you don’t know that you don’t know”.
The final, cutting-edge step in data processing is to build a data lake. This is a type of database that can draw in data from a wide variety of sources without those sources needing to be designed for compatibility. By collecting all of your data in this way, you can start strategizing across vastly different areas of your business. For example, when trying to determine which suppliers to use for a new order, traditional databases may only provide specifics around the price and quantity of specific previous orders, requiring lots of manual cross-reference to get informed. A modern data lake can instead automatically surface all orders of similar parts, alongside other relevant information, like the defect rate of the received parts. This allows for broad and deep comparisons without manual prompting.
What are the benefits of digital transformation?
We’ve hinted at a number of new capabilities that digital transformation unlocks, but how exactly does it benefit your business? Let’s look at a few key areas where you should expect to see improvements after implementing digital transformation.
Convenience
Putting aside anything new that you’ll be capable of doing, digital transformation will make everything you’re currently doing far more convenient. Many tedious, manual, repetitive tasks can be automated to a single click. You likely have some process steps that are sometimes skipped due to being too toilsome in tight deadlines or high stress scenarios, such as additional reviews, or filing and labeling. After digital transformation, those steps become convenient and consistently completed.
Not only does this make things faster, but it makes employees happier. It frees up their time and energy to focus on more creative and forward thinking work. They’re less likely to seek other opportunities and feel more fulfilled and appreciated. There’s no better boost to productivity than investing in the capabilities of each and every employee.
Collaboration
Manufacturing has always been a team sport. From the invention of the assembly line, manufacturing shops have seen the value of everyone contributing a piece to create a whole larger than any individual’s capabilities. A digital transformation in manufacturing unlocks new avenues for collaboration. With cloud storage and software that allows asynchronous comments and revisions, it’s never been easier for people to contribute.
Greater contribution has many benefits. More eyes on a project means less opportunity for errors to sneak through, leading to higher quality products and fewer costly late-stage revisions. It also allows for more chances at breakthrough ideas to make production more efficient or the project more functional. Beyond these immediate practical benefits, it also does a lot for the morale and capabilities of each contributor. Broadening collaborative efforts empowers each individual to improve their skills and knowledge, making them more valuable and productive. A greater sense of ownership and connection to the work makes employees more likely to remain with the company and invest more of their energy.
Strategic insights
Perhaps the most profound change of a manufacturing digital transformation is in the strategic insights it opens you up to. To put it simply, you can shift from a mindset of “asking questions and getting answers” to “having every potential insight available to you before you ask”. You no longer need to “know what you don’t know”. This all sounds very abstract, so let’s explore an example.
Let’s say you’re thinking about suppliers for component parts. You want to save money while still hitting the necessary quality thresholds. You also want to consolidate suppliers to reduce overhead, while exploring potential backup plans if supply chain issues arise. There are many strategic tradeoffs you need to consider, but before you can even begin considering, there’s tons and tons of data you need to gather.
Pre-digital transformation, this information would be extremely time consuming to track down. If you have the information loaded into spreadsheets or other databases, it helps a lot, but still requires essentially asking a series of dozens of specific questions: what orders did we get from supplier A, what was the price for each order, what was the defect rate of each order, etc, etc. This still takes a long time and relies on you knowing each and every question to investigate, and where to investigate it in your database.
Post-digital transformation, with all of this data coexisting in a data lake, you can answer much broader questions instantly. Queries like “give me all the data about supplier A”, “give me all the data about orders of stainless steel parts”, “give me all the data about orders from Mexico” become the type of request you can make. Not only does this speed up data collection immensely, it allows you to explore data without needing to know exactly what you’re looking for. You can simply browse through data organized in these ways and have patterns leap out at you. It may become apparent, for example, that supplier B consistently gives both the lowest price and the highest quality for bearing casings. You may not have thought to consolidate your bearing casing suppliers, but suddenly this cost-saving strategic move becomes obvious to you.
What are the cutting-edge technologies for your next digital transformation?
Let’s say you’ve gotten through all these successive eras of digital transformation already, everything from fax machines to cloud collaboration. A great question is “what’s next?” Digital transformation isn’t a one-and-done change. Instead, it should be an ongoing process in your manufacturing company to identify and adopt new technologies. It’s necessary to be at the same level of adoption as your peers, but being ahead of them is a huge advantage.
So what’s coming down the pike for the next era of digital transformation?
AI Assistants
The biggest technological story of the last few years has been AI, but we may just be getting started. Even if the technology behind AI plateaus, we’re still just scratching the surface of how it can be utilized, especially in the manufacturing industry. When we talked about “asking questions” in the previous sections, it was just an analogy for looking up data in a database. However, with AI assistants, you really can just ask questions. You can literally type in “give me all the information about orders of bearing casings” and have the AI assistant reply with all the data you need. It could even take the next step and suggest “did you notice supplier A has the lowest prices?”
Machine vision
Another emerging technology is for machines to “look” through a camera and understand what they’re “seeing”. Computer-integrated machines have used things like laser measuring to analyze their own outputs for a while, but these are typically narrow solutions that can check for specific things. This new era of machine vision uses AI to parse the whole image, able to detect and respond to a wide range of abnormalities. Machine vision can also be applied to purely digital images. If you have a library of pictures you’ve taken of different products or assemblies, it used to require manual labeling and tagging to make those pictures searchable. Modern AI software lets you search for what it is a picture of without that data being explicitly added.
Predictive design
We’ve discussed how a digital transformation in manufacturing can help accelerate and improve new designs by surfacing past data. But what if, using that data, it could help with design itself? The next wave of digital transformation may include technologies capable of enhancing human creativity with its own design suggestions. Imagine drafting a new design and having real-time information about its expected cost, defect rate, or production time based on previous designs. Imagine getting a breakdown on what parts of the design have especially high costs or defects rates, and suggestions for alternatives. Designing would be faster, more consistent, and accessible to more people. It would free up consideration and creative energy to make bigger breakthroughs and focus on the most nuanced problems.
Take a transformative step with CADDi
There’s no faster way to receive the benefits of digital transformation than investing in a tool. CADDi allows you to search through your data in intuitive ways, surface strategic insights, and get to market faster. See it all in action by signing up for a demo or walking through our interactive tour.
A digital transformation is a process by which you improve your efficiency and productivity through moving data and operations from physical processes to digital systems. What that exactly involves depends on your particular systems and needs. In manufacturing, generally speaking, it means using digital systems to access your shop’s inputs and outputs, inventory, and data.
The term “digital transformation” has been used in many situations to describe different processes at different times. As such, it’s hard to know exactly what you should be doing to digitally transform, what benefits you should be seeing, and how to measure those benefits. We’ve prepared a digital transformation assessment tool to judge how far your manufacturing shop is in the digital transformation journey. Check it out, and read the rest of the blog to learn more about the concept of a digital transformation.
What have the manufacturing digital transformations been so far?
One challenge in launching headfirst into a digital transformation is the feeling of, well, haven’t we already been doing those before? And it’s true – your shop certainly has already completed several digital transformations over the years. The proof is in the fact that you’re reading this article right now: adopting the habit of educating yourself on the internet is a key outcome of digital transformations.
It can be easier to understand what to do in your upcoming digital transformation by looking at what technological leaps we’ve already experienced.
Computer-integrated manufacturing
Computer-integrated manufacturing means using manufacturing machines that are linked to computer systems which can control them, monitor their inputs and outputs, and help direct manual steps of the manufacturing process. These machines started appearing in the 1980s and have seen continuous improvement in the decades since.
Computer-integrated manufacturing was an extremely impactful digital transformation. It increases the flexibility of machines, the speed at which their outputs can be changed, their consistency, and the strategic data generated as they run.
Emerging technologies like additive manufacturing (including 3D printing) and more sophisticated robotics are making manufacturing machines even more powerful. Modern computer-integrated manufacturing can have an automatic two-way relationship between the production’s output and follow-up instructions. For example, a machine can use AI-driven vision to detect when it produces a defective part, then use adaptive robotics to automatically remove it from the production line.
Fax machines and scanners
Another major digital transformation that occurred in the 1980s was the widespread adoption of fax machines and subsequently scanners. This freed designs and other information from being trapped on individual paper. Instead, drawings and other designs could be duplicated, shared between offices, and stored securely. These documents could be stored on computer systems, in higher quality images, using faster and more convenient techniques.
Although this technology is old, scanning documents is improving even today. Optical character reading (OCR) is a continually-improving practice that can “read” everything written on documents and convert it into digital text. This makes searching, revising, and sharing the contents of documents much easier. Modern OCR can even accurately transcribe handwritten notes.
Cutting-edge technology like CADDi are taking things even further, using AI-driven machine vision to analyze scanned drawings even deeper. Not only can it extract all of the text from a drawing to make it more searchable, it can understand the shapes and features of the drawing itself. This allows you to “search by shape”, making finding the correct designs much faster and easier.
Email and other digital communication
Perhaps the biggest transformation in the last few decades has been how we communicate with our colleagues. Remember when you had to call someone if you wanted to talk to them? Nowadays we have a plethora of ways to communicate – email, text messaging, communication tools like Slack, video calling tools like Zoom, shared digital workspaces like Google Docs or virtual whiteboards… every way you want to express yourself to someone remotely is possible today.
Although not directly linked to manufacturing, this digital transformation has brought massive new opportunities for any machine shop. Collaboration is easier than ever before, with people able to asynchronously leave ideas and comment on each other’s work. The status of production can be relayed to teams wherever they are, allowing for more rapid response to problems. Tools like Slack can make conversations searchable assets, keeping ideas and decisions in a place where they can easily be revisited and revised.
Your team is almost certainly taking advantage of this digital transformation already, but likely in a suboptimal way. Take the time to review your current communication infrastructure. What messages get missed, what is still hard to convey? What tools are you not yet implementing that would be helpful? By being deliberate about communication, you can build a more collaborative and efficient workforce.
Database software and cloud storage
The final digital transformation we’ll mention today is in how you store the data relevant to your shop’s decision-making. This includes tracking metrics around production, inventory, procurement, sales quotes, and more. It also includes storing digital assets, like CAD-created designs, scanned drawings, and process documents. It even includes corporate administrative data, like HR records, financials, and marketing assets.
The first stage of this digital transformation means organizing these data into “dumb databases”. This could look like a spreadsheet tracking inventory levels, or scans of drawings sorted into labeled folders. This is a great starting point, as it does give you access to a lot of information. However, that access is often time-consuming, tedious, and fraught with potential errors. If people don’t really know where something is, it’s very hard for them to find it, or even know that it might be there.
The next step is moving data into specialized programs that make it more usable, such as PLM or ERP software. This makes it much easier to find the data you need. It also enables cloud access, meaning teammates from anywhere can use the data. These specialized tools help you analyze different types of data, helping you make smarter decisions. However, they often lack the ability to make connections across different types of data, or intelligently surface contextual data. As such, they answer specific questions, but don’t help you “learn what you don’t know that you don’t know”.
The final, cutting-edge step in data processing is to build a data lake. This is a type of database that can draw in data from a wide variety of sources without those sources needing to be designed for compatibility. By collecting all of your data in this way, you can start strategizing across vastly different areas of your business. For example, when trying to determine which suppliers to use for a new order, traditional databases may only provide specifics around the price and quantity of specific previous orders, requiring lots of manual cross-reference to get informed. A modern data lake can instead automatically surface all orders of similar parts, alongside other relevant information, like the defect rate of the received parts. This allows for broad and deep comparisons without manual prompting.
What are the benefits of digital transformation?
We’ve hinted at a number of new capabilities that digital transformation unlocks, but how exactly does it benefit your business? Let’s look at a few key areas where you should expect to see improvements after implementing digital transformation.
Convenience
Putting aside anything new that you’ll be capable of doing, digital transformation will make everything you’re currently doing far more convenient. Many tedious, manual, repetitive tasks can be automated to a single click. You likely have some process steps that are sometimes skipped due to being too toilsome in tight deadlines or high stress scenarios, such as additional reviews, or filing and labeling. After digital transformation, those steps become convenient and consistently completed.
Not only does this make things faster, but it makes employees happier. It frees up their time and energy to focus on more creative and forward thinking work. They’re less likely to seek other opportunities and feel more fulfilled and appreciated. There’s no better boost to productivity than investing in the capabilities of each and every employee.
Collaboration
Manufacturing has always been a team sport. From the invention of the assembly line, manufacturing shops have seen the value of everyone contributing a piece to create a whole larger than any individual’s capabilities. A digital transformation in manufacturing unlocks new avenues for collaboration. With cloud storage and software that allows asynchronous comments and revisions, it’s never been easier for people to contribute.
Greater contribution has many benefits. More eyes on a project means less opportunity for errors to sneak through, leading to higher quality products and fewer costly late-stage revisions. It also allows for more chances at breakthrough ideas to make production more efficient or the project more functional. Beyond these immediate practical benefits, it also does a lot for the morale and capabilities of each contributor. Broadening collaborative efforts empowers each individual to improve their skills and knowledge, making them more valuable and productive. A greater sense of ownership and connection to the work makes employees more likely to remain with the company and invest more of their energy.
Strategic insights
Perhaps the most profound change of a manufacturing digital transformation is in the strategic insights it opens you up to. To put it simply, you can shift from a mindset of “asking questions and getting answers” to “having every potential insight available to you before you ask”. You no longer need to “know what you don’t know”. This all sounds very abstract, so let’s explore an example.
Let’s say you’re thinking about suppliers for component parts. You want to save money while still hitting the necessary quality thresholds. You also want to consolidate suppliers to reduce overhead, while exploring potential backup plans if supply chain issues arise. There are many strategic tradeoffs you need to consider, but before you can even begin considering, there’s tons and tons of data you need to gather.
Pre-digital transformation, this information would be extremely time consuming to track down. If you have the information loaded into spreadsheets or other databases, it helps a lot, but still requires essentially asking a series of dozens of specific questions: what orders did we get from supplier A, what was the price for each order, what was the defect rate of each order, etc, etc. This still takes a long time and relies on you knowing each and every question to investigate, and where to investigate it in your database.
Post-digital transformation, with all of this data coexisting in a data lake, you can answer much broader questions instantly. Queries like “give me all the data about supplier A”, “give me all the data about orders of stainless steel parts”, “give me all the data about orders from Mexico” become the type of request you can make. Not only does this speed up data collection immensely, it allows you to explore data without needing to know exactly what you’re looking for. You can simply browse through data organized in these ways and have patterns leap out at you. It may become apparent, for example, that supplier B consistently gives both the lowest price and the highest quality for bearing casings. You may not have thought to consolidate your bearing casing suppliers, but suddenly this cost-saving strategic move becomes obvious to you.
What are the cutting-edge technologies for your next digital transformation?
Let’s say you’ve gotten through all these successive eras of digital transformation already, everything from fax machines to cloud collaboration. A great question is “what’s next?” Digital transformation isn’t a one-and-done change. Instead, it should be an ongoing process in your manufacturing company to identify and adopt new technologies. It’s necessary to be at the same level of adoption as your peers, but being ahead of them is a huge advantage.
So what’s coming down the pike for the next era of digital transformation?
AI Assistants
The biggest technological story of the last few years has been AI, but we may just be getting started. Even if the technology behind AI plateaus, we’re still just scratching the surface of how it can be utilized, especially in the manufacturing industry. When we talked about “asking questions” in the previous sections, it was just an analogy for looking up data in a database. However, with AI assistants, you really can just ask questions. You can literally type in “give me all the information about orders of bearing casings” and have the AI assistant reply with all the data you need. It could even take the next step and suggest “did you notice supplier A has the lowest prices?”
Machine vision
Another emerging technology is for machines to “look” through a camera and understand what they’re “seeing”. Computer-integrated machines have used things like laser measuring to analyze their own outputs for a while, but these are typically narrow solutions that can check for specific things. This new era of machine vision uses AI to parse the whole image, able to detect and respond to a wide range of abnormalities. Machine vision can also be applied to purely digital images. If you have a library of pictures you’ve taken of different products or assemblies, it used to require manual labeling and tagging to make those pictures searchable. Modern AI software lets you search for what it is a picture of without that data being explicitly added.
Predictive design
We’ve discussed how a digital transformation in manufacturing can help accelerate and improve new designs by surfacing past data. But what if, using that data, it could help with design itself? The next wave of digital transformation may include technologies capable of enhancing human creativity with its own design suggestions. Imagine drafting a new design and having real-time information about its expected cost, defect rate, or production time based on previous designs. Imagine getting a breakdown on what parts of the design have especially high costs or defects rates, and suggestions for alternatives. Designing would be faster, more consistent, and accessible to more people. It would free up consideration and creative energy to make bigger breakthroughs and focus on the most nuanced problems.
Take a transformative step with CADDi
There’s no faster way to receive the benefits of digital transformation than investing in a tool. CADDi allows you to search through your data in intuitive ways, surface strategic insights, and get to market faster. See it all in action by signing up for a demo or walking through our interactive tour.