CADDi vs ERP Software - What are the Differences
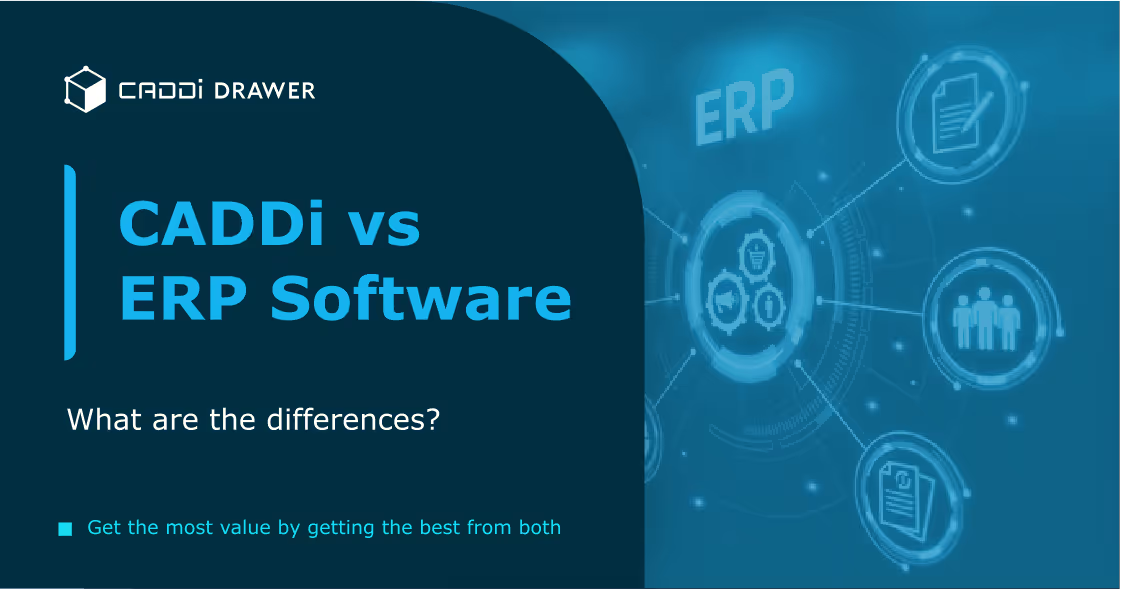
Table of Contents
Enterprise Resource Planning (ERP) software is a product and set of processes that track data about your business, including human resources, accounting, and project management. In manufacturing, ERP includes and often focuses on data such as supply chain information, inventory, and procurement. Generally speaking, ERP operates on a more general level than PLM software, looking at the overall inputs and outputs of your processes as a whole, rather than tracking specific parts.
CADDi is a manufacturing intelligence software that functions as a data lake, combining data from multiple services, including ERP. It contextualizes specific product and part data by surfacing and connecting related information. Essentially, it lets you zoom in on your ERP data to see which specific parts are forming trends or are critical outliers. Or you can zoom out from a particular product, purchase, or drawing, finding how it connects to other data to build a big picture.
Before we discuss the details of what sets CADDi apart from ERP tools, let’s summarize the differences in a chart:
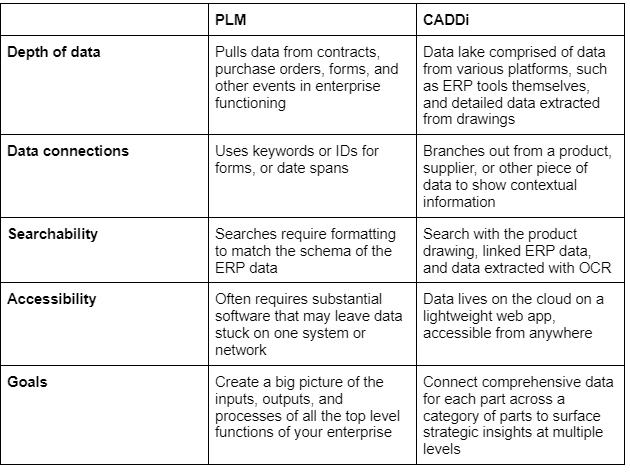
What does a manufacturing ERP tool do?
Manufacturing ERP tools are software platforms that help collect and manage the data that is generated by your enterprise as a whole as it operates. Here are some examples of types of data that these tools can organize and store for you, and some questions this data should be able to answer. Some of these are specific to manufacturing shops, whereas others apply to all companies.
- Human resources data – how many people work in each role? How long have they been there? What accreditation and training have they received? What roles have they worked in the past?
- Supply chain data – what components have been ordered from which suppliers? How long did they take to arrive? How much did they cost? What tariffs and import fees were they subject to? What countries do you order from?
- Sales data – how much does your company sell per month? What products are sold and for what price? How are they processed and shipped? What customers do you have and what have they purchased?
- Inventory data – what products do you have in inventory? Where are they stored and how are they accessed? How long have they been there? How frequently is new inventory added for each product? When will storage areas fill up based on current rates?
- Accounting data – what are the financials of your business? How much money is being spent on payroll vs procurement vs production, etc.? How much will you need to pay in taxes and other fees? What are all your sources of revenue and cost?
- Project management data – what initiatives is your business taking? How long have they been underway? What are the key milestones for each project? What resources have been assigned? What outcomes are you hoping to achieve?
A given ERP tool may only cover only a few of these data areas. Each one may require a different database schema to organize. They may also have their own methods for inputting data. However, your ERP system in totality should be able to track all of these business areas in a fairly automated and easy-to-read manner.
Modern ERP software should be able to gather significant parts of this data automatically. You should be able to do work in whatever program is most relevant and have the ERP collect the produced data. If you have a dedicated HR program, a program for creating procurement orders, and a program that tracks financials, your ERP program should be able to take in data from all of these and display it in a centralized location.
Modern ERP software also makes this data accessible on the cloud. This allows multiple sources to collaborate on it from multiple locations. It prevents data becoming desynchronized between different viewpoints, becoming a “single source of truth” about the state of your enterprise.
What does CADDi do differently from ERP software?
CADDi takes a different perspective on your enterprise data than ERP tools. ERP tools provide a “top down” big picture, summarizing the overall inputs and outputs of your systems. CADDi, on the other hand, builds a “bottom up” big picture, contextualizing data from individual parts and transactions to highlight larger trends.
CADDi is capable of making the leap between individual pieces of information to bigger strategic insights because of how it links data. Let’s say you’re trying to analyze all the data around a given product. It’ll have a very specific and arbitrary ID, something like HF5320328, and maybe a label that might be too generic, like “bearing with eight flanges”. Imagine there’s some data stored for this product under HF53203328, because someone made a typo, or “bearing with 8 flanges”, because someone forgot the formatting.
With CADDi, all of this data would be linked and would surface just by searching with the product drawing itself. No matter how it might get IDed or labelled in other systems, CADDi knows when two entries have the same or very similar drawings associated with them. This accounts for revised versions of the drawing that might differ slightly. This helps you make sure all of your data is accessible, even when human error would disconnect it. It also helps make sure you don’t have redundant versions of parts taking up space in your database.
This searching technology also allows you to find insights about types of products. This is a middle layer between the total perspective of ERP tools and the individual parts data of PLM tools. Often you’ll want to understand data not just about one specific product, but that entire category of products. This can be very helpful for:
- Making new designs based on old products
- Negotiating with suppliers
- Consolidating suppliers
- Estimating defect rates
- Estimating costs
And much more.
With traditional ERP systems, you can track the overall productivity of systems, but not zoom in to particular actionable examples. CADDi puts the spotlight on the individual examples that make up the larger trends. In concert, these allow you to diagnose the most essential changes for your business, and then find all the categories of individual examples that need to change.
This dynamic categorization of example data allows you to diagnose enterprise-level problems more flexibly. The categories you decide on won’t be all-encompassing. You might eventually run into a situation where you want to categorize based on another quality of the product, or create a new subset of a category. This would require tedious manual effort with traditional systems.
CADDi allows for dynamic and flexible categorization of products. As you use the drawings themselves to search, you’ll be able to cast a broad net that will reliably gather every similar design. Then you can filter down with other metrics to arrive at the exact category of products you’re looking for. Once you do, all your data from your different systems will be connected and ready for analysis.
To see it all in action, sign up for a demo today or click through our interactive experience.
Enterprise Resource Planning (ERP) software is a product and set of processes that track data about your business, including human resources, accounting, and project management. In manufacturing, ERP includes and often focuses on data such as supply chain information, inventory, and procurement. Generally speaking, ERP operates on a more general level than PLM software, looking at the overall inputs and outputs of your processes as a whole, rather than tracking specific parts.
CADDi is a manufacturing intelligence software that functions as a data lake, combining data from multiple services, including ERP. It contextualizes specific product and part data by surfacing and connecting related information. Essentially, it lets you zoom in on your ERP data to see which specific parts are forming trends or are critical outliers. Or you can zoom out from a particular product, purchase, or drawing, finding how it connects to other data to build a big picture.
Before we discuss the details of what sets CADDi apart from ERP tools, let’s summarize the differences in a chart:
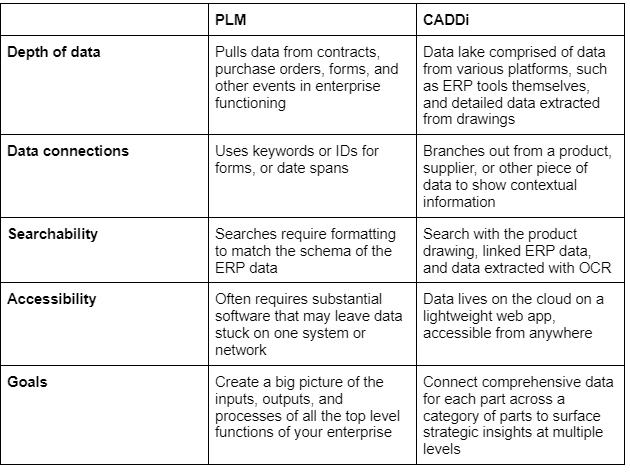
What does a manufacturing ERP tool do?
Manufacturing ERP tools are software platforms that help collect and manage the data that is generated by your enterprise as a whole as it operates. Here are some examples of types of data that these tools can organize and store for you, and some questions this data should be able to answer. Some of these are specific to manufacturing shops, whereas others apply to all companies.
- Human resources data – how many people work in each role? How long have they been there? What accreditation and training have they received? What roles have they worked in the past?
- Supply chain data – what components have been ordered from which suppliers? How long did they take to arrive? How much did they cost? What tariffs and import fees were they subject to? What countries do you order from?
- Sales data – how much does your company sell per month? What products are sold and for what price? How are they processed and shipped? What customers do you have and what have they purchased?
- Inventory data – what products do you have in inventory? Where are they stored and how are they accessed? How long have they been there? How frequently is new inventory added for each product? When will storage areas fill up based on current rates?
- Accounting data – what are the financials of your business? How much money is being spent on payroll vs procurement vs production, etc.? How much will you need to pay in taxes and other fees? What are all your sources of revenue and cost?
- Project management data – what initiatives is your business taking? How long have they been underway? What are the key milestones for each project? What resources have been assigned? What outcomes are you hoping to achieve?
A given ERP tool may only cover only a few of these data areas. Each one may require a different database schema to organize. They may also have their own methods for inputting data. However, your ERP system in totality should be able to track all of these business areas in a fairly automated and easy-to-read manner.
Modern ERP software should be able to gather significant parts of this data automatically. You should be able to do work in whatever program is most relevant and have the ERP collect the produced data. If you have a dedicated HR program, a program for creating procurement orders, and a program that tracks financials, your ERP program should be able to take in data from all of these and display it in a centralized location.
Modern ERP software also makes this data accessible on the cloud. This allows multiple sources to collaborate on it from multiple locations. It prevents data becoming desynchronized between different viewpoints, becoming a “single source of truth” about the state of your enterprise.
What does CADDi do differently from ERP software?
CADDi takes a different perspective on your enterprise data than ERP tools. ERP tools provide a “top down” big picture, summarizing the overall inputs and outputs of your systems. CADDi, on the other hand, builds a “bottom up” big picture, contextualizing data from individual parts and transactions to highlight larger trends.
CADDi is capable of making the leap between individual pieces of information to bigger strategic insights because of how it links data. Let’s say you’re trying to analyze all the data around a given product. It’ll have a very specific and arbitrary ID, something like HF5320328, and maybe a label that might be too generic, like “bearing with eight flanges”. Imagine there’s some data stored for this product under HF53203328, because someone made a typo, or “bearing with 8 flanges”, because someone forgot the formatting.
With CADDi, all of this data would be linked and would surface just by searching with the product drawing itself. No matter how it might get IDed or labelled in other systems, CADDi knows when two entries have the same or very similar drawings associated with them. This accounts for revised versions of the drawing that might differ slightly. This helps you make sure all of your data is accessible, even when human error would disconnect it. It also helps make sure you don’t have redundant versions of parts taking up space in your database.
This searching technology also allows you to find insights about types of products. This is a middle layer between the total perspective of ERP tools and the individual parts data of PLM tools. Often you’ll want to understand data not just about one specific product, but that entire category of products. This can be very helpful for:
- Making new designs based on old products
- Negotiating with suppliers
- Consolidating suppliers
- Estimating defect rates
- Estimating costs
And much more.
With traditional ERP systems, you can track the overall productivity of systems, but not zoom in to particular actionable examples. CADDi puts the spotlight on the individual examples that make up the larger trends. In concert, these allow you to diagnose the most essential changes for your business, and then find all the categories of individual examples that need to change.
This dynamic categorization of example data allows you to diagnose enterprise-level problems more flexibly. The categories you decide on won’t be all-encompassing. You might eventually run into a situation where you want to categorize based on another quality of the product, or create a new subset of a category. This would require tedious manual effort with traditional systems.
CADDi allows for dynamic and flexible categorization of products. As you use the drawings themselves to search, you’ll be able to cast a broad net that will reliably gather every similar design. Then you can filter down with other metrics to arrive at the exact category of products you’re looking for. Once you do, all your data from your different systems will be connected and ready for analysis.
To see it all in action, sign up for a demo today or click through our interactive experience.