Procurement 101: Lean Manufacturing – Applicable from mass production to HMLV
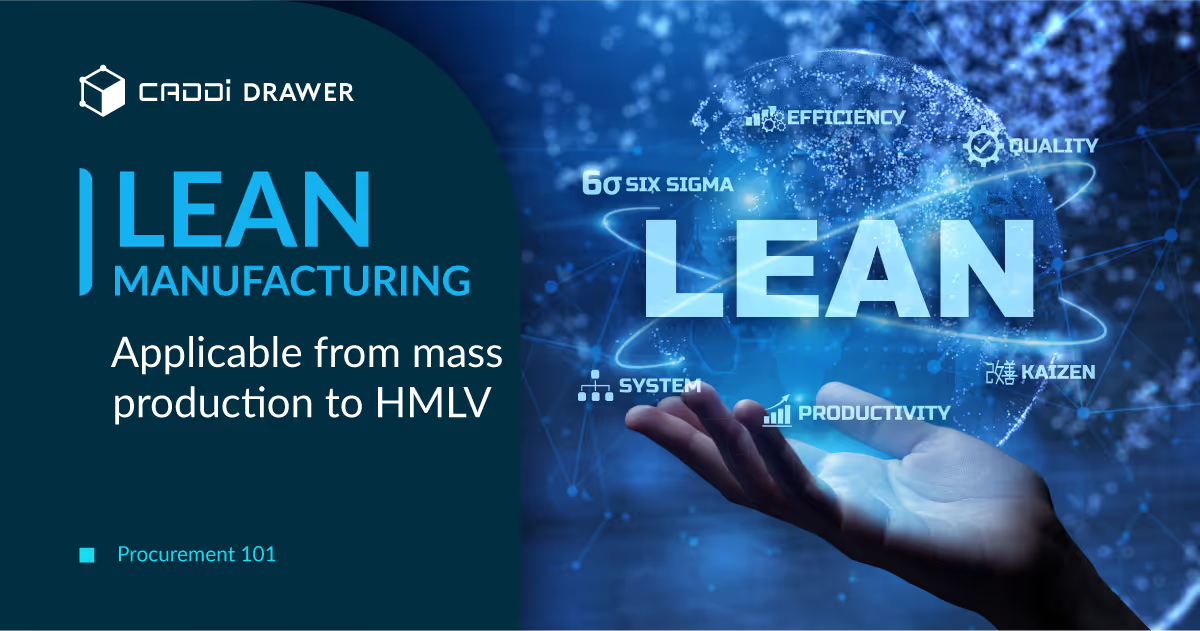
Table of Contents
Lean manufacturing, a philosophy rooted in maximizing value by minimizing waste, has revolutionized the way companies operate and compete on a global scale. Production based on the principles of Lean Manufacturing is often referred to as the Lean Production System (LPS). This transformative approach, born from necessity in post-war Japan, has evolved into a set of principles and practices adopted by leading organizations worldwide to achieve operational excellence.
As we delve into the essence and evolution of lean manufacturing, we’ll explore its foundational principles, notable case studies, and the profound impact it has on industries today. Additionally, the following section will also explain lean manufacturing for high-mix low-volume (HMLV) manufacturers.
Lean Manufacturing: Origins and Evolution
The inception of lean manufacturing can be traced back to Japan’s post-war economic environment, where challenges such as scarce resources, limited space, and a need for efficient production methods catalyzed the development of innovative manufacturing practices. The Toyota Production System (TPS), spearheaded by pioneers like Taiichi Ohno, emerged as a beacon of lean philosophy, focusing on just-in-time production to reduce waste and increase efficiency. This system’s global recognition was further solidified by studies and publications, notably “The Machine That Changed the World” by Womack, Jones, and Roos, which introduced the term “lean” to a broader audience.
American industrialists, aware of the looming threat posed by cheap offshore labor, had already begun to echo the sentiments of lean manufacturing as early as the 1910s. Frederick Winslow Taylor’s “Principles of Scientific Management” laid the groundwork for what would become lean manufacturing, emphasizing the importance of continuous improvement and efficiency to maintain competitiveness in global markets.
Lean Manufacturing: Core Principles
The journey toward streamlining production and minimizing waste takes its shape through the core principles of lean manufacturing. These principles are not mere guidelines but the foundation upon which companies like Toyota have built their global success. The essence of lean lies in understanding and applying five principles: value, the value stream, flow, pull, and perfection.
Value, from the perspective of the customer, dictates that a product or service must be designed to meet their needs at the right price point. This principle challenges manufacturers to scrutinize every aspect of production to ensure that it contributes to what the customer is willing to pay for. Companies that excel in this area not only meet but often exceed their customers’ expectations, leading to higher satisfaction and loyalty.
Mapping the value stream involves a detailed analysis of the product’s lifecycle, identifying every step from raw materials to the end customer, and eliminating anything that does not add value. This step is crucial for spotting inefficiencies and ensuring that the product flows smoothly towards completion. For instance, a study conducted by the Lean Enterprise Institute highlighted how value stream mapping helped a major electronics manufacturer reduce its product development cycle time by over 50%.
Creating a continuous flow and implementing a pull system ensures that products are made at the pace of customer demand, eliminating overproduction and reducing inventory costs. Toyota, a pioneer in this area, utilizes a kanban system to achieve a seamless flow in production, responding dynamically to customer demand while keeping inventory and waste to a minimum.
Pursuing perfection is the ongoing quest for improvement, where the lean journey never truly ends. Companies committed to this principle constantly seek ways to enhance efficiency, quality, and customer satisfaction. This relentless pursuit of perfection fosters a culture of continuous improvement and innovation.
Lean Manufacturing: Waste Elimination
The elimination of waste, or ‘muda,’ is at the heart of lean manufacturing. Taiichi Ohno, the father of the Toyota Production System, identified seven types of waste that companies should strive to eliminate: defects, overproduction, waiting, non-utilized talent, transportation, inventory, and motion. Recognizing these wastes and actively working to reduce them can significantly enhance operational efficiency and productivity.
For example, a study published in the Journal of Manufacturing Technology Management demonstrated how lean practices helped a textile company reduce its defect rate by 30%. By focusing on quality control and streamlining processes, the company not only reduced waste but also improved customer satisfaction and profitability.
Furthermore, adding an eighth waste – unused talent or ingenuity – acknowledges the importance of engaging employees in problem-solving and innovation. Encouraging employee participation in waste identification and process improvement has been shown to not only increase efficiency but also enhance job satisfaction and organizational commitment.
Lean Manufacturing: Advanced Practices
Advanced lean manufacturing practices, such as Heijunka (level production) and Just-In-Time (JIT) production, further refine the process of waste elimination and efficiency optimization. Heijunka, for instance, focuses on producing goods at a constant rate, smoothing out the peaks and troughs of demand. This approach not only reduces waste associated with overproduction and inventory but also stabilizes the workforce and production processes.
The JIT principle, demanding that production aligns closely with customer orders, drastically reduces the need for inventory, freeing up capital and space for other uses. Implementing JIT can be challenging, as it requires a high degree of coordination and flexibility within the production process. However, when successfully applied, it leads to significant cost savings and a more responsive production system.
A case in point is Dell Computers, which revolutionized the PC manufacturing industry by implementing a JIT system. By building computers to order, Dell was able to drastically reduce its inventory levels and lead times, offering customers faster delivery times and the ability to customize their computers. This strategic approach not only improved customer satisfaction but also gave Dell a significant competitive advantage in the market.
In conclusion, advanced lean practices offer strategic advantages to companies willing to embrace the challenges of implementation. Through continuous improvement and a focus on eliminating waste, companies can achieve greater efficiency, flexibility, and customer satisfaction, ultimately driving profitability and competitive advantage.
Lean Manufacturing for High-mix Low-volume manufacturers
Implementing lean manufacturing in high-mix, low-volume (HMLV) environments presents unique challenges compared to high-volume production settings. However, by adapting lean principles to their specific context, HMLV manufacturers can significantly enhance efficiency and flexibility, reduce waste, and improve customer satisfaction like Rockheed Martin’s case.
Here’s how HMLV manufacturers can apply lean manufacturing principles effectively:
1. Customized Value Stream Mapping
For HMLV manufacturers, each product or product family might require a distinct value stream map. This involves identifying and documenting all the steps involved in the production process, from raw material to delivery, for each product or family of products. The goal is to pinpoint waste and inefficiencies in each stream. For instance, a custom electronics manufacturer might use value stream mapping to reduce setup times and minimize work-in-process inventory, thereby improving lead times for their diverse product range.
2. Flexible Work Cells
Instead of traditional assembly lines, HMLV manufacturers can benefit from setting up flexible work cells capable of producing a variety of products. These cells are designed to quickly switch between different products with minimal downtime. By training workers to perform multiple tasks within these cells, companies can reduce waiting times and respond more swiftly to changing customer demands. A bespoke furniture company, for example, could reconfigure its work cells based on order flow to maintain continuous production.
3. Implementing Pull Systems
Pull systems, like Kanban, are highly effective in HMLV settings to control inventory and ensure that production is directly tied to customer demand. By only producing what is needed, when it’s needed, companies can drastically cut down on overproduction and excess inventory. A specialized medical device manufacturer might use a Kanban system to manage parts inventory more effectively, ensuring that critical components are always available without overstocking.
4. Focused Continuous Improvement (Kaizen)
Continuous improvement is vital in HMLV environments, where processes and products are often more complex. Regular kaizen events that involve cross-functional teams can help identify improvements in production flows, quality control, and waste reduction. These improvements are essential for staying competitive and meeting the varied needs of customers. An aerospace parts supplier could conduct kaizen events to streamline the production of custom components, enhancing quality and reducing cycle times.
5. Advanced Setup Reduction (SMED)
Single-Minute Exchange of Dies (SMED) techniques are crucial for reducing setup times in HMLV manufacturing. By analyzing and optimizing setup activities, companies can switch between product lines more efficiently, thus increasing machine utilization and reducing lead times. A precision machining company, for instance, might invest in training and tooling improvements to cut down setup times from hours to minutes, allowing for more flexible production scheduling.
Lean Manufacturing vs. Lean Enterprise
Distinguishing between lean manufacturing and lean enterprise clarifies the scope and impact of lean principles beyond the factory floor. While lean manufacturing focuses on eliminating waste and improving efficiency within the manufacturing processes, lean enterprise extends these principles across the entire value stream, including suppliers, customers, and all internal functions. This holistic approach ensures that improvements in one area are not offset by inefficiencies in another, leading to a truly optimized organization.
A compelling example of lean enterprise in action is seen in how Amazon applies lean principles not just in its distribution centers but across its entire operation, including its supply chain, customer service, and new product development. This integrated approach has enabled Amazon to achieve remarkable efficiency, rapid delivery times, and high levels of customer satisfaction, proving that the principles of lean manufacturing can be effectively applied on a much broader scale.
Lean Manufacturing: Process and System Optimization
Optimization in lean manufacturing is about continually seeking ways to improve and refine processes and systems. This continuous improvement cycle is captured in the concept of kaizen, which focuses on making small, incremental changes that collectively lead to significant improvements over time. By fostering a culture of continuous improvement, companies can remain agile, responsive to changes in the market, and ahead of the competition.
A striking case of process optimization comes from Intel, where kaizen principles were applied to their chip manufacturing process. By continuously analyzing and refining their processes, Intel achieved a dramatic reduction in manufacturing defects, leading to higher yields of usable chips per wafer and a significant decrease in production costs. This focus on optimization not only improved Intel’s bottom line but also reinforced its position as a leader in the highly competitive semiconductor industry.
How CADDi Drawer Can Help
CADDi Drawer is one of the solutions that contribute to Lean Manufacturing. These features significantly enhance the elimination of waste and visualization, which are indispensable for lean manufacturing.
Streamline activities in the procurement process
The following features enable you to streamline the time-consuming tasks of data collection and organization in procurement and manufacturing operations.
- Price data and supplier information can be automatically linked to each drawing and can also be exported together.
- By using keyword searches combined with similarity searches, the time spent searching for drawings and data in procurement tasks can be reduced.
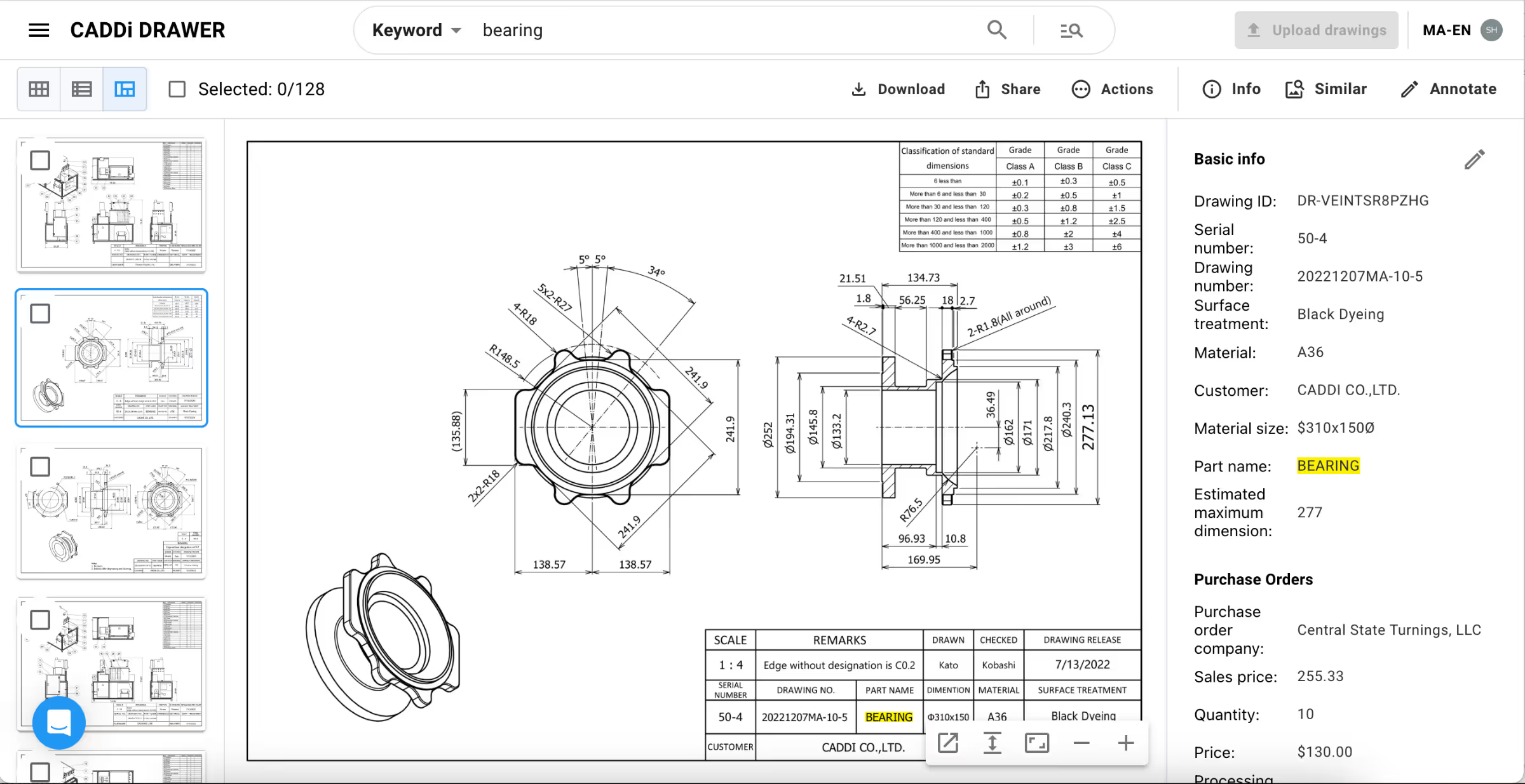
Similarity search of part drawings
The similarity search feature allows users to instantly identify which suppliers have previously been ordered similar items and under what pricing and conditions. This functionality makes supplier candidates selections and cost analysis much easier and more effective to execute.

Furthermore, by assetizing data and sharing tribal knowledge, it can also contribute to the development of personnel, which is one of the essential elements of lean manufacturing.
Lean manufacturing, a philosophy rooted in maximizing value by minimizing waste, has revolutionized the way companies operate and compete on a global scale. Production based on the principles of Lean Manufacturing is often referred to as the Lean Production System (LPS). This transformative approach, born from necessity in post-war Japan, has evolved into a set of principles and practices adopted by leading organizations worldwide to achieve operational excellence.
As we delve into the essence and evolution of lean manufacturing, we’ll explore its foundational principles, notable case studies, and the profound impact it has on industries today. Additionally, the following section will also explain lean manufacturing for high-mix low-volume (HMLV) manufacturers.
Lean Manufacturing: Origins and Evolution
The inception of lean manufacturing can be traced back to Japan’s post-war economic environment, where challenges such as scarce resources, limited space, and a need for efficient production methods catalyzed the development of innovative manufacturing practices. The Toyota Production System (TPS), spearheaded by pioneers like Taiichi Ohno, emerged as a beacon of lean philosophy, focusing on just-in-time production to reduce waste and increase efficiency. This system’s global recognition was further solidified by studies and publications, notably “The Machine That Changed the World” by Womack, Jones, and Roos, which introduced the term “lean” to a broader audience.
American industrialists, aware of the looming threat posed by cheap offshore labor, had already begun to echo the sentiments of lean manufacturing as early as the 1910s. Frederick Winslow Taylor’s “Principles of Scientific Management” laid the groundwork for what would become lean manufacturing, emphasizing the importance of continuous improvement and efficiency to maintain competitiveness in global markets.
Lean Manufacturing: Core Principles
The journey toward streamlining production and minimizing waste takes its shape through the core principles of lean manufacturing. These principles are not mere guidelines but the foundation upon which companies like Toyota have built their global success. The essence of lean lies in understanding and applying five principles: value, the value stream, flow, pull, and perfection.
Value, from the perspective of the customer, dictates that a product or service must be designed to meet their needs at the right price point. This principle challenges manufacturers to scrutinize every aspect of production to ensure that it contributes to what the customer is willing to pay for. Companies that excel in this area not only meet but often exceed their customers’ expectations, leading to higher satisfaction and loyalty.
Mapping the value stream involves a detailed analysis of the product’s lifecycle, identifying every step from raw materials to the end customer, and eliminating anything that does not add value. This step is crucial for spotting inefficiencies and ensuring that the product flows smoothly towards completion. For instance, a study conducted by the Lean Enterprise Institute highlighted how value stream mapping helped a major electronics manufacturer reduce its product development cycle time by over 50%.
Creating a continuous flow and implementing a pull system ensures that products are made at the pace of customer demand, eliminating overproduction and reducing inventory costs. Toyota, a pioneer in this area, utilizes a kanban system to achieve a seamless flow in production, responding dynamically to customer demand while keeping inventory and waste to a minimum.
Pursuing perfection is the ongoing quest for improvement, where the lean journey never truly ends. Companies committed to this principle constantly seek ways to enhance efficiency, quality, and customer satisfaction. This relentless pursuit of perfection fosters a culture of continuous improvement and innovation.
Lean Manufacturing: Waste Elimination
The elimination of waste, or ‘muda,’ is at the heart of lean manufacturing. Taiichi Ohno, the father of the Toyota Production System, identified seven types of waste that companies should strive to eliminate: defects, overproduction, waiting, non-utilized talent, transportation, inventory, and motion. Recognizing these wastes and actively working to reduce them can significantly enhance operational efficiency and productivity.
For example, a study published in the Journal of Manufacturing Technology Management demonstrated how lean practices helped a textile company reduce its defect rate by 30%. By focusing on quality control and streamlining processes, the company not only reduced waste but also improved customer satisfaction and profitability.
Furthermore, adding an eighth waste – unused talent or ingenuity – acknowledges the importance of engaging employees in problem-solving and innovation. Encouraging employee participation in waste identification and process improvement has been shown to not only increase efficiency but also enhance job satisfaction and organizational commitment.
Lean Manufacturing: Advanced Practices
Advanced lean manufacturing practices, such as Heijunka (level production) and Just-In-Time (JIT) production, further refine the process of waste elimination and efficiency optimization. Heijunka, for instance, focuses on producing goods at a constant rate, smoothing out the peaks and troughs of demand. This approach not only reduces waste associated with overproduction and inventory but also stabilizes the workforce and production processes.
The JIT principle, demanding that production aligns closely with customer orders, drastically reduces the need for inventory, freeing up capital and space for other uses. Implementing JIT can be challenging, as it requires a high degree of coordination and flexibility within the production process. However, when successfully applied, it leads to significant cost savings and a more responsive production system.
A case in point is Dell Computers, which revolutionized the PC manufacturing industry by implementing a JIT system. By building computers to order, Dell was able to drastically reduce its inventory levels and lead times, offering customers faster delivery times and the ability to customize their computers. This strategic approach not only improved customer satisfaction but also gave Dell a significant competitive advantage in the market.
In conclusion, advanced lean practices offer strategic advantages to companies willing to embrace the challenges of implementation. Through continuous improvement and a focus on eliminating waste, companies can achieve greater efficiency, flexibility, and customer satisfaction, ultimately driving profitability and competitive advantage.
Lean Manufacturing for High-mix Low-volume manufacturers
Implementing lean manufacturing in high-mix, low-volume (HMLV) environments presents unique challenges compared to high-volume production settings. However, by adapting lean principles to their specific context, HMLV manufacturers can significantly enhance efficiency and flexibility, reduce waste, and improve customer satisfaction like Rockheed Martin’s case.
Here’s how HMLV manufacturers can apply lean manufacturing principles effectively:
1. Customized Value Stream Mapping
For HMLV manufacturers, each product or product family might require a distinct value stream map. This involves identifying and documenting all the steps involved in the production process, from raw material to delivery, for each product or family of products. The goal is to pinpoint waste and inefficiencies in each stream. For instance, a custom electronics manufacturer might use value stream mapping to reduce setup times and minimize work-in-process inventory, thereby improving lead times for their diverse product range.
2. Flexible Work Cells
Instead of traditional assembly lines, HMLV manufacturers can benefit from setting up flexible work cells capable of producing a variety of products. These cells are designed to quickly switch between different products with minimal downtime. By training workers to perform multiple tasks within these cells, companies can reduce waiting times and respond more swiftly to changing customer demands. A bespoke furniture company, for example, could reconfigure its work cells based on order flow to maintain continuous production.
3. Implementing Pull Systems
Pull systems, like Kanban, are highly effective in HMLV settings to control inventory and ensure that production is directly tied to customer demand. By only producing what is needed, when it’s needed, companies can drastically cut down on overproduction and excess inventory. A specialized medical device manufacturer might use a Kanban system to manage parts inventory more effectively, ensuring that critical components are always available without overstocking.
4. Focused Continuous Improvement (Kaizen)
Continuous improvement is vital in HMLV environments, where processes and products are often more complex. Regular kaizen events that involve cross-functional teams can help identify improvements in production flows, quality control, and waste reduction. These improvements are essential for staying competitive and meeting the varied needs of customers. An aerospace parts supplier could conduct kaizen events to streamline the production of custom components, enhancing quality and reducing cycle times.
5. Advanced Setup Reduction (SMED)
Single-Minute Exchange of Dies (SMED) techniques are crucial for reducing setup times in HMLV manufacturing. By analyzing and optimizing setup activities, companies can switch between product lines more efficiently, thus increasing machine utilization and reducing lead times. A precision machining company, for instance, might invest in training and tooling improvements to cut down setup times from hours to minutes, allowing for more flexible production scheduling.
Lean Manufacturing vs. Lean Enterprise
Distinguishing between lean manufacturing and lean enterprise clarifies the scope and impact of lean principles beyond the factory floor. While lean manufacturing focuses on eliminating waste and improving efficiency within the manufacturing processes, lean enterprise extends these principles across the entire value stream, including suppliers, customers, and all internal functions. This holistic approach ensures that improvements in one area are not offset by inefficiencies in another, leading to a truly optimized organization.
A compelling example of lean enterprise in action is seen in how Amazon applies lean principles not just in its distribution centers but across its entire operation, including its supply chain, customer service, and new product development. This integrated approach has enabled Amazon to achieve remarkable efficiency, rapid delivery times, and high levels of customer satisfaction, proving that the principles of lean manufacturing can be effectively applied on a much broader scale.
Lean Manufacturing: Process and System Optimization
Optimization in lean manufacturing is about continually seeking ways to improve and refine processes and systems. This continuous improvement cycle is captured in the concept of kaizen, which focuses on making small, incremental changes that collectively lead to significant improvements over time. By fostering a culture of continuous improvement, companies can remain agile, responsive to changes in the market, and ahead of the competition.
A striking case of process optimization comes from Intel, where kaizen principles were applied to their chip manufacturing process. By continuously analyzing and refining their processes, Intel achieved a dramatic reduction in manufacturing defects, leading to higher yields of usable chips per wafer and a significant decrease in production costs. This focus on optimization not only improved Intel’s bottom line but also reinforced its position as a leader in the highly competitive semiconductor industry.
How CADDi Drawer Can Help
CADDi Drawer is one of the solutions that contribute to Lean Manufacturing. These features significantly enhance the elimination of waste and visualization, which are indispensable for lean manufacturing.
Streamline activities in the procurement process
The following features enable you to streamline the time-consuming tasks of data collection and organization in procurement and manufacturing operations.
- Price data and supplier information can be automatically linked to each drawing and can also be exported together.
- By using keyword searches combined with similarity searches, the time spent searching for drawings and data in procurement tasks can be reduced.
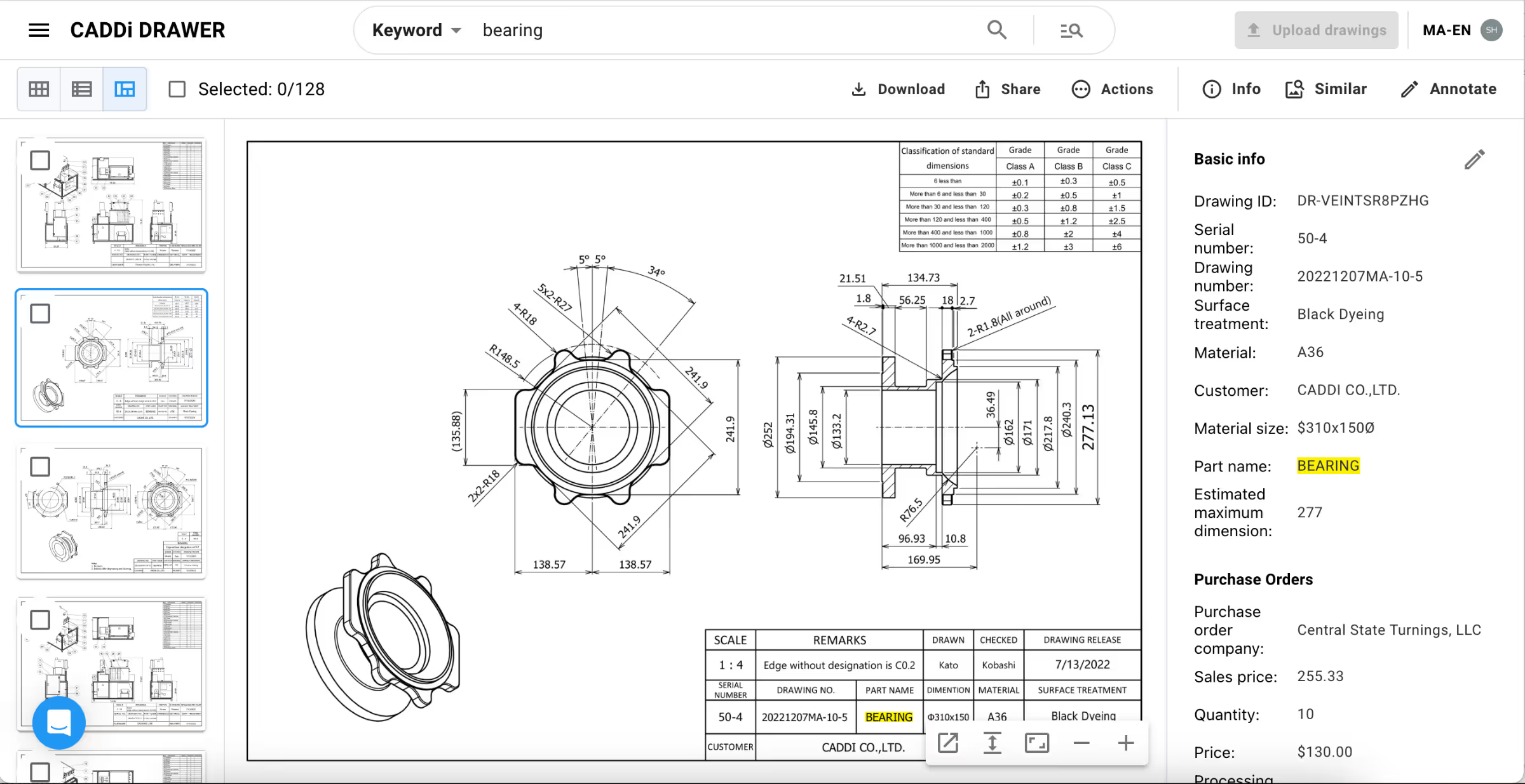
Similarity search of part drawings
The similarity search feature allows users to instantly identify which suppliers have previously been ordered similar items and under what pricing and conditions. This functionality makes supplier candidates selections and cost analysis much easier and more effective to execute.

Furthermore, by assetizing data and sharing tribal knowledge, it can also contribute to the development of personnel, which is one of the essential elements of lean manufacturing.
Ready to see CADDi Drawer in action? Get a personalized demo.
Subscribe to our Blog!
Related Resources
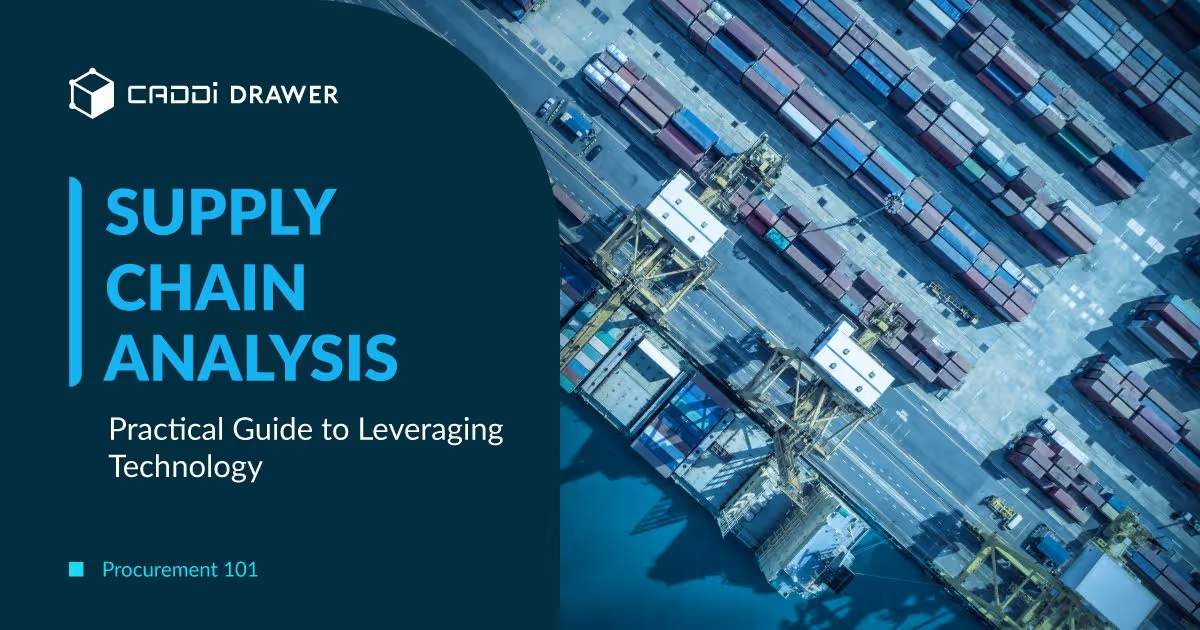
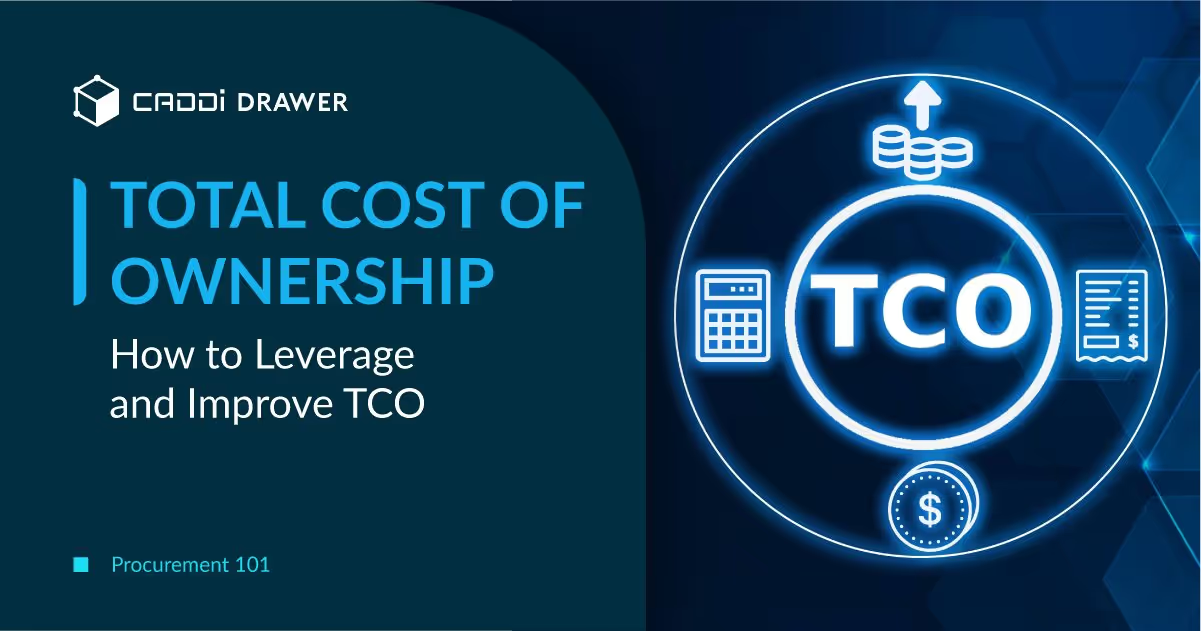
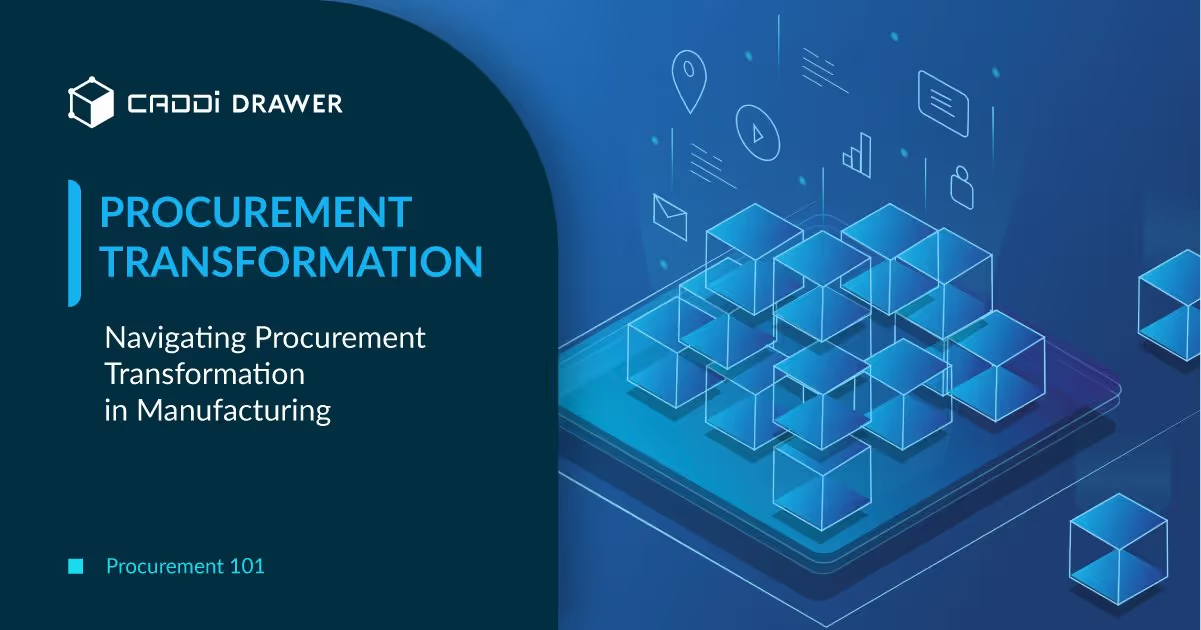

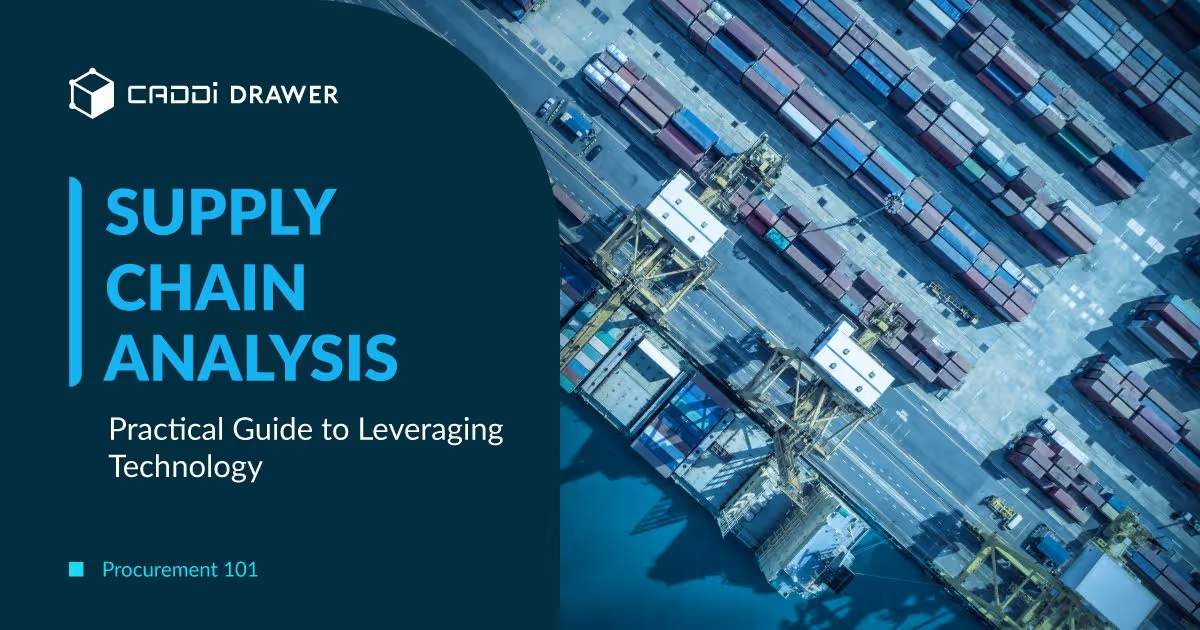
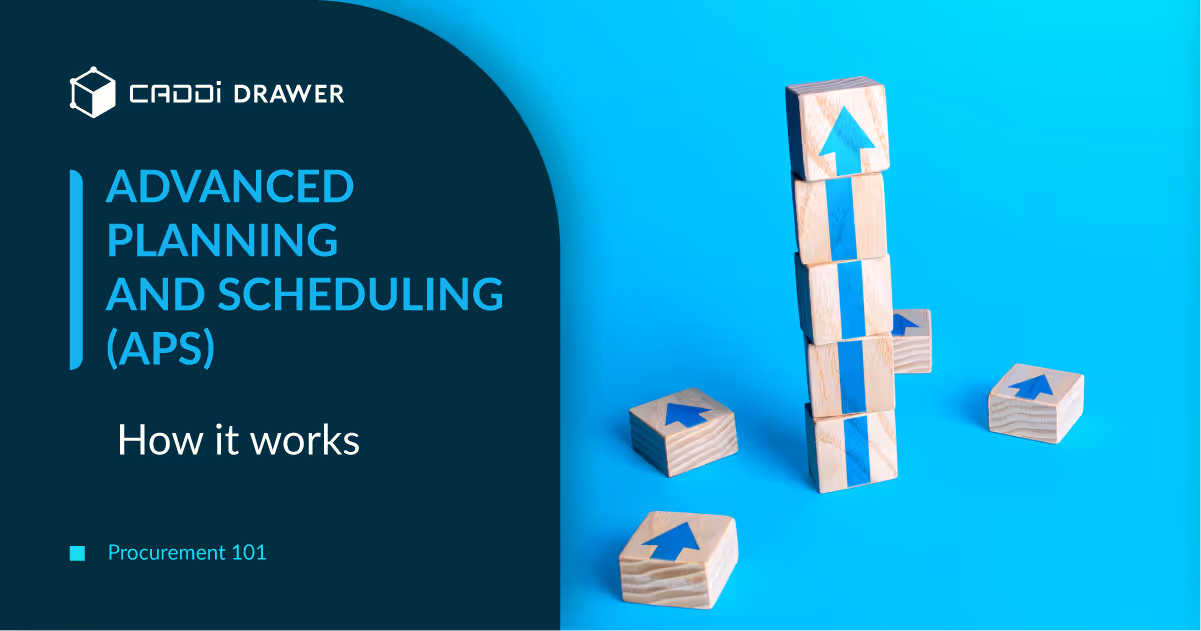